Реферат за темою випускної
роботи
Зміст
- Вступ
- 1. Актуальність теми
- 2. Мета і задачі дослідження та заплановані результати
- 3. Огляд досліджень по темі
- 4. Основна частина
- Висновок
- Список використаних джерел
Вступ
Алмазне шліфування великогабаритних сложнопрофільних тонкостінних оболонок з крихких неметалічних матеріалів є невід'ємною частиною технологічного процесу створення елементів конструкцій виробів авіаційної і ракетної техніки, ефективність якого визначає трудомісткість, собівартість і якість виробів. Вимоги до якості, що пред'являються до досліджуваних деталей, визначаються умовами їх експлуатації. Основними вимогами є забезпечення аеродинамічним конструкції, високою механічною міцністю, здатної зберігатися при експлуатаційних температурах, а також селективне пропускання електроенергії в заданому інтервалі частот і відносно мала маса вироби. Аеродинамічні вимоги забезпечуються формою розглянутих деталей-оболонок. Вимоги до міцності, радіопрозорості і невеликій масі забезпечуються фізико-механічними властивостями матеріалу (ситала АС–418), з яких виготовляють розглядаються вироби. Забезпечення необхідних радіотехнічних властивостей вироби можливо при дотриманні високих вимог по точності форми, відхилення від заданої товщини стінки не більше ± 0,1 мм і шорсткості обробленої поверхні Ra≤2,5 мкм. Міцність виробу в основному забезпечується відсутністю дефектності в при поверхневому шарі [1].
Ситали (склокристалічні матеріали), неорганічні матеріали, які здобуваються спрямованою кристалізацією разліних скла при їх термічній обробці. Складаються з однієї або декількох кристалічних фаз. У ситалів дрібнодисперсні кристали (до 2000 нм) рівномірно розподілені в склоподібної матриці. Вперше ситали були виготовлені в 50–х рр. 20 ст. Матеріали, подібні ситалам, за кордоном називають пірокерамом, девітрокерамом, стеклокерамом [2].
1. Актуальність теми
Темою магістерської роботи є: Розробити
і дослідити систему управління точність обробки тонкостінних деталей з
ситалів
.
В даний час в світі спостерігається тенденція виробництва виробів з неметалічних і композиційних матеріалів, які все ширше замінюють метали в багатьох галузях промисловості. Ця тенденція пов'язана зі зниженням собівартості продукції при одночасному підвищенні їх терміну служби, надійності та екологічної чистоти. Особливе місце серед неметалічних матеріалів займає кераміка. Фізико–механічні властивості конструкційної кераміки (в тому числі і ситалів) в порівнянні з усіма видами металів, які в теперешній час застосовуються в якості головних матеріалів для виготовлення деталей машин, мають такі відмітні характеристики, як високу температуру плавлення, твердість, високу зносостійкість, корозійну стійкість, стійкість до впливу хімікатів і т.д.
Ці фактори і зумовили широкий інтерес до вивчення властивостей ситалів, їх спостереження і в кінцевому підсумку розробці методів впливу на властивості під час механічної обробки.
2. Мета і завдання дослідження, планованірезультати
Метою дослідження є розробка та дослідження системи управління точність обробки тонкостінних деталей з ситалів.
Основні завдання дослідження:
- Аналіз факторів, що впливають на формування точності механічної обробки виробу.
- Аналіз варіантів і вибір методу управління точністю обробки ситалового обтікача.
- Вибір параметрів САУ обробки.
- Розробка керуючої програми в параметричному вигляді.
Об'єкт дослідження: Процес алмазного шліфування ситалового обтікача.
Предмет дослідження: Процес формування точності зовнішнього контуру при алмазному шліфуванні.
3. Огляд досліджень по темі
Технологічний процес обробки виробів включає багатоопераційної обробку шліфуванням як зовнішнього, так і внутрішнього їх контурів на верстатах типу РТ 66202, обладнаних агрегатної шліфувальної головкою і системою прямого копіювання. Наведено результати досліджень динамічних характеристик системи ВПІД при шліфуванні зовнішньої поверхні деталі, схема якої зображена на мал. 1.
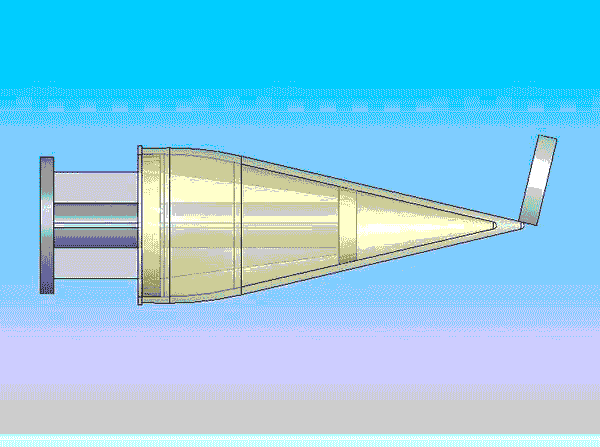
Малюнок 1 – Зовнішня обробка виробу (анімація: 10 кадрів, 10 повторів, 132 кілобайт)
Особливості обробки виробів розглянутого класу з ситалів в значній мірі обумовлені наступними факторами. Основні розміри вироби: довжина до 1,0 м; максимальний діаметр 450 ... 500 мм; товщина стінки заготовки 20 мм при товщині готового виробу 5 мм. На обробку внутрішнього контуру вироби витрачається приблизно 18–20 годин машинного часу; обробка зовнішнього контуру займає 6–10 годин значною мірою ручної праці, що застосовується на операції чистової обробки зовнішнього профілю. Експлуатаційні характеристики виробів припускають дотримання підвищених вимог по точності і якості обробки, зокрема, забезпечення мінімальної глибини дефектності поверхневого шару, яка визначає тривалість наступних операцій хімічного травлення і зміцнення механічно оброблених поверхонь [3].
Для підвищення точності механічної обробки ситаловогообтікача необхідно нівелювати фактори впливають на неї.
Основною причиною утворення похибки на шліфованої поверхні виробу є зміна положення в просторі оброблюваної поверхні щодо траєкторії, заданою формою і профілем деталі. Причинами, що викликають зміну відстані між заданою і реальної траєкторіями формоутворення, є вібрації в технологічній системі обробки, а також неточності геометричної форми шліфувального круга і похибка його установки [4].
Розглянемо фактори, що впливають на точність обробки.
Відомо, що при шліфуванні
тонкостінних оболонок обертання (схема установки заготовки на верстаті
представлена на малюнку 2) в зоні контакту заготовки з шліфувальним
кругом виникають коливання згибу на двох частотах 60 ± 5 Гц
і 123 ± 10 Гц, близьких до власних частот підсистеми шпиндельний
вузол верстата – пристосування – заготовка
[5].
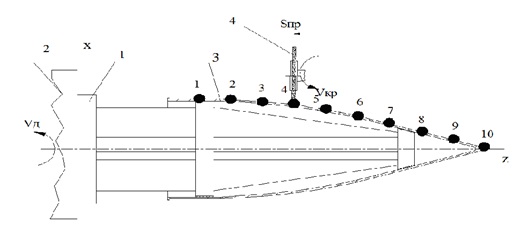
Малюнок 2 – Схема технологічної системи при зовнішньому круглому шліфуванні заготовки – тонкостінної оболонки обертання з ситалу: 1 – оправка; 2 – шпиндель верстата; 3 – оброблювана заготовка; 4 – шліфувальний круг IАI 200х10х3х76 А 315 / 250–4–М2–01, встановлений в агрегатній голівці. Крапки 1 ... 10 – крапки, що обмежують області зміни параметрів даної технологічної системи
Також передбачається, що в зоні контакту шліфувального круга з заготовкою виникають параметричні коливання деталі – тонкостінної оболонки обертання, під впливом сили різання, що переміщається. На підставі даних, наведених у роботі [6], проведено аналіз стійкості системи на параметричні коливання, який показав, що найбільшою нестійкістю володіють області заготовки в районі крапок 1 – 5 (див. мал. 1). Області, обмежені крапками 6 – 10, знаходяться в зоні стійкості до параметричних коливань. Схема алмазно–абразивної обробки оболонки, представлена на мал. 3.
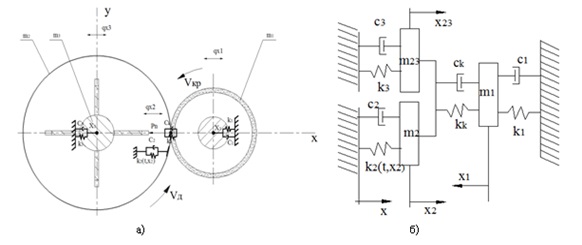
Малюнок 3 – Схема шліфування (а) і розрахункова схема (б) алмазно-абразивної обробки тонкостінної оболонки обертання з ситалa
Оброблювана заготовка являє собою тонкостінну оболонку обертання, динаміку якої неможливо описати за допомогою системи з зосередженої масою, до якої наводиться розглянута технологічна система. Тому аналіз динамічної поведінки оболонки необхідно провести відповідно до законів теорії оболонок. Для кожної області, обмеженою крапками, зазначеними на малюнку 2, за допомогою моделі, розробленої в програмі Simulink, були визначені частота і амплітуда коливань. Динамічна поведінка технологічної системи при обробці даної заготовки – тонкостінної оболонки обертання з ситалу при переміщенні інструменту від вершини виробу до фланця не постійне, що позначається на якості обробленої поверхні. Характер коливань, їх амплітуда, частота, форма змінюються в залежності від ділянки щодо осі заготовки, який проходить інструмент [4].
Дослідження особливостей
вимушених коливань підсистеми пристосування–заготовка
[7]
також показали змінну інтенсивність рівня вібрацій по довжині
заготовки, подібну до експериментальної кривої амплітуди коливань. На
мал. 4 по довжині заготовки щодо осі Z наведені динамічні і пружні
показники підсистеми шпиндельный
узел–пристосування–заготовка
.
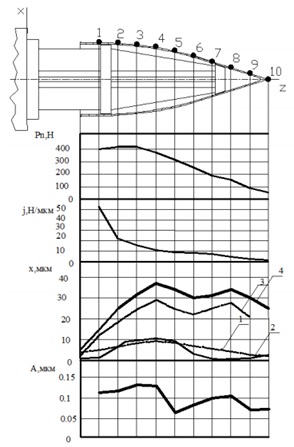
Малюнок
4 – Порівняльні діаграми зміни динамічних і пружних
характеристик підсистеми шпиндельний
вузол – оправка – заготовка
уздовж осі деталі: Pn – нормальної складової сили різання, Н;
j – згинальної жорсткості, H/мкм; x – статичних
прогинів, мкм (1 – сумарні радіальні переміщення шпиндельного
вузла, 2 – радіальні переміщення оброблюваної заготовки, 3
– радіальні переміщення підсистеми пристосування–заготовка
,
4 – сумарні радіальні переміщення підсистеми шпиндельний
вузол – пристосування–заготовка
);
А – амплітуди вібрацій, мкм. 18
Однак отримані теоретичні дані мали деякі розбіжності з їх експериментальними значеннями. Це можна пояснити наступним. При моделюванні не були враховані ряд властивостей оброблюваної заготовки як замкнутої тонкостінної оболонки, а також фактори, пов'язані з механічною обробкою деталі на спеціальному верстаті, що вимагає рішення задачі моделювання поведінки системи при шліфуванні на більш високому рівні [8].
4. Основна частина
Аналіз процесу утворення похибки контурної обробки на верстатах з ЧПУ і її складових показує, що автоматичне керування можна проводити за рахунок корекції еквідистанта або управлінням режимами різання з метою стабілізації або компенсації збурень. Застосовують також комбіновані методи, які поєднують управління режимами обробки з корекцією еквідистанта. За характером застосовуваної інформації методи автоматичного управління можна розділити на методи, що використовують апріорну, поточну і апостеріорну інформацію.
Управління режимами різання по апріорної інформації. Цей метод доцільно застосовувати при вагомому впливі нестабільності режимів різання на якість обробленої поверхні, наприклад, при шліфуванні. Метод базується на встановленому зв'язку між збуреннями, які керують діями і параметрами якості обробки, тобто на заздалегідь детермінованих передавальних функціях Wnpx та Wencx.
В цьому випадку процес різання повинен бути представлений як мінімум з двома входами: по вектору відносного формотворного руху хт, заданим без всякої корекції і по керуючим впливом S (мал. 5). Отже, силовий фактор, який спроектований на координату х, визначається залежністю:

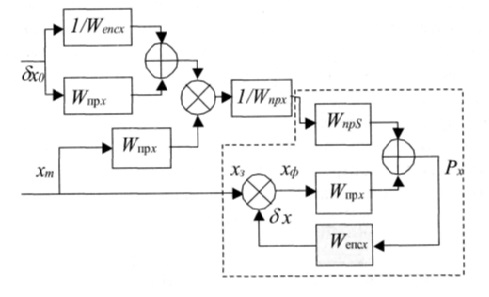
Малюнок 5 – Схема управління для стабілізації умов обробки
Управління режимами різання по
поточною інформацією. Метод передбачає створення САУ, замкнутої через
процес різання і працює за принципом зведення
балансу
, тобто за помилкою.
Незважаючи на загальний принцип управління, цей метод відрізняється від
розглянутого вище методу управління траєкторією формотворного руху за
поточною інформацією. Згідно зі схемою методу (мал. 6) впливають на
вихідні характеристики процесу, зокрема, точність обробки, через режими
різання. При цьому за безпосереднє мета управління вибирають будь-який
параметр процесу різання, контролюється і інтегрує в собі максимум
інформації. Таким параметром є, як правило, силовий фактор, зазвичай
вимірюється через пружні деформації системи.
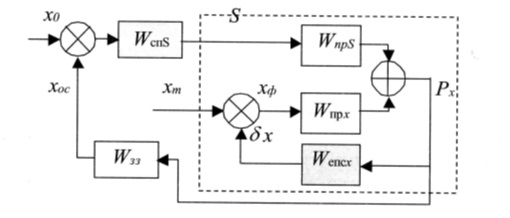
Малюнок 6 – Схема управління режимами обробки за поточною інформацією
Метод доцільно застосовувати не тільки для стабілізації, але і для програмного управління будь-якими параметрами процесу в циклі обробки. Наприклад, при різному шліфовці система може забезпечити алгоритм управління поперечної виразний подачею, що потрібно, в функції координати залишеного припуску. Для цього в САУ має бути забезпечене безперервне вимірювання фактичної координати в напрямку врізки і застосований додатковий програмний блок, яким заданий алгоритм управління.
Відповідно до одного з представлених методів проводиться розробка і дослідження системи управління точність обробки тонкостінних деталей з ситалів.
Висновок
Магістерська робота присвячена розробці та дослідженню системи управління точність обробки тонкостінних деталей з ситалів. При написанні даного реферату магістерська робота ще не завершена. Остаточне завершення: червень 2018 року. Повний текст роботи та матеріали по темі можуть бути отримані у автора або його керівника після зазначеної дати.
Список источников
- Гусев В.В., Калафатова Л.П. Повышение виброустойчивости технологической системы во время алмазного шлифования тонкостенных оболочек вращения из ситаллов //ISSN 2078–7405. Резание и инструмент в технологических системах, 2013, выпуск 83. Харьков: КПИ..
- ХИМИК. Сайт о химии. Ситаллы // [Электронный ресурс] – Режим доступа: http://www.xumuk.ru/encyklopedia/2/4086.html
- Калафатова
Л.П. Прогнозирование качества поверхностного слоя при обработке изделий
из технических ситаллов // Приложение №9 к журналу
Инженерный журнал. Справочник
Инженерия поверхности. – М.: Машиностроение. – 2002. – №9. – С.5–8. - Калафатова Л.П., Гусев В.В., Олейник С.Ю. Исследование динамического состояния технологической системы алмазно–абразивной обработки тонкостенных оболочек из ситаллов // Вісник СевНТУ: зб. наук. пр. Вип. 128/2012. Серія: Машиноприладобудування та транспорт. – Севастополь, 2012 с.60–67
- Гусев В.В. Исследование динамических характеристик элементов системы СПИД при шлифовании деталей сложной пространственной формы из ситаллов / В.В. Гусев, Л.П. Калафатова, И.С. Каракуц // Надійність інструменту та оптимізація технологічних систем. Збірник наукових праць. – Краматорск, 2007. – Вип. №21. – С. 148 – 155.
- Якушев Н.З. Коническая оболочка под действием подвижных нагрузок / Якушев Н. З., Якушев Р. С. // Исследования по теории пластин и оболочек. – Казань: Изд–во Казанского ун–та, 1975. – С. 303 – 316
- Гусев В.В. Повышение качества алмазного шлифования тонкостенных оболочек из ситалла путем снижения вибраций в технологической системе / Гусев В.В., Калафатова Л.П., Олейник С.Ю. // Наукові праці ДонНТУ– Донецк, 2010. – Вип. № 7(166).– С. 156–167.
- Петраков Ю.В.Драчев О.И. Теория автоматического управления технологическими системами / М.: Машиностроение, 2008. – C. 158 – 162