Abstract
Contents
- Introduction
- 1. Theme urgency
- 2. The purpose and objectives of the study, the planned results
- 3. Review of research and development
- 3.1 Existing ways to regulate hydrotransport facilities
- 4. Main results of research and development
- Conclusion
- References
Introduction
To ensure the efficiency of the enterprise requires a comprehensive introduction of a comprehensive system of automation of technological processes with the use of modern automation devices. In addition, the automation of production has not only a technical and economic, but also a great social value, because nature changes the nature of labor, creates the conditions for eliminating the differences between physical and mental labor.
Increasing the productivity of coal mining makes increased demands on all technological processes of the mining enterprise. The process of pressure hydrotransport with the help of hydrotransport facilities is one of the most important technological processes of hydraulic seamen.
On the level of automation, hydraulic transport takes one of the leading places among other branches of mine automation.
ТThe technological process of hydrotransport is characterized by the continuity of the processes occurring in it. Operation of hydrotransport facilities should ensure reliable and efficient transport of required parameters, as well as safe working conditions for personnel working with these facilities.
1. Theme urgency
The operation of automated hydrotransport facilities should provide hydrotransport with coal or other minerals with the greatest economic effect, which is achieved precisely by ensuring safe labor and the continuity of the technological process.
The existing means of automation of hydrotransport facilities do not fully solve the problems of operation of the facilities. The issues of regulating the facility for supplying, monitoring the level of the slurry in the pulp container, power consumption of the coal-fired plant, and others have not been resolved. Also, the existing automation equipment is made on a technically obsolete element base, which does not allow the implementation of functions such as communication with the controller's computer, data storage, analysis, automatic control of the delivery of hydro transport facilities. Therefore, the development and research of the automatic control system of the coal-fueling unit of the technological process of hydrotransport is an actual topic.
2. The purpose and objectives of the study, the planned results
The aim of the master's work is to increase the efficiency of the technological process of hydrotransport by developing and researching an automatic control system of the coal-fueling unit.
Based on the analysis of the technological process of hydrotransport as an automation object, the following requirements are imposed on the automatic control system of the coal-fueling unit:
- provision of automatic starting and stopping of coal-fueling unit;
- automatic feed control of coal-fueling unit;
- automatic control of the following parameters: the current level of the slurry in the pulp container, the supply of the coal-fueling unit, the pressure of the slurry in the pulpwood, the electric power consumption of the hydro transport object, the temperature of the bearing units of the coal-fueling unit, operating time of the hydrotransport facility in the modes of regulation and deregulation;
- automatic protection of coal-fueling unit: with the development of cavitation in the object, with a decrease in the pump supply, with blockage of the suction device;
- automatic control: dithering mode (nominal mode of operation for the slurry) and the mode of regulation (minimum feed);
- continuous collection, processing, storage and presentation of information on the work hydrotransport object and automatic control system of the coal-fueling unit;
- providing information exchange between adjacent automation systems using a high-speed intrinsically safe industrial computer network;
- the design and the circuit solution of the technical means of the automatic control system must comply with the requirements of the "Rules for the manufacture of explosion-proof and mine electrical equipment" - have the form of explosion protection "flameproof enclosure" and "intrinsically safe electrical circuit", and be installed and operated in accordance with the "Rules for the Technical Operation of Coal and Shale mines "[1] .
Object of study: process pressure hydrotransport.
Subject of study: automatic control system of the coal-fueling unit.
3. Review of research and development
3.1 Existing ways to regulate hydrotransport facilities
All currently known methods of regulating the supply of coal-fueling unit by technical essence can be divided into two groups:
- regulation without preliminary transfer of the object to the water regime;
- regulation with a preliminary transfer.
The first group includes the following methods. Regulation by: changing the speed of the pump impeller; intake of air into the suction line of the pump; changes in the consistency of the slurry; throttling pulp conduit pressure pipeline.
All the listed methods of this group have a general significant drawback: all of them, in order to ensure a given depth of regulation, require an increase in the initial flow rate by the same amount, which leads to a sharp increase in friction losses and a substantial reduction in the length of transportation. Therefore, the noted methods do not meet the modern requirements imposed on them by the condition for efficient operation of the coal-fueling unit.
To a greater extent, the requirements of the second group meet the requirements set. These include the method developed at the Donetsk National Technical University. This method is based on the use of the suction device UV-5 and consists in the preliminary transfer of the hydrotransport object to the water mode of operation, the complete washing of the transport pipeline with a standard valve. This method has been successfully used for several years in hydraulic seamstresses, and has shown sufficient efficiency, compared to the previously used way of switching-off pumps in the level of the slurry in the sump. However, experience has shown that the effectiveness of this method decreases with the increase in the length of transportation due to the operation of a complete washing of the transport pipeline, consuming about 50 percent of all unproductive water costs in transport. Moreover, the time for complete flushing of the pulpwood, in a number of cases, is commensurate with the time of turning on the water supply in the face, as a result of which the maximum flow of water, which in one case is necessary for hydrotransport of solid material, and in the other for flushing the pipelines, can be continuously pumped through the hydraulic system.[5]
In the master's work, a method is applied to regulate the supply of coal-fueling unit by changing the speed of the impeller of the pump, with the preliminary transfer of the object from the slurry to water. Application of this method of regulation requires the use of a high-voltage electric drive speed converter in a special mine version.
4. Main results of research and development
Structural scheme of an automatic control system of the coal-fueling unit using an industrial network
The exchange of information between devices that are part of the automatic control system takes place through an industrial network, which is the basis for the design of any automated process system.
The communication technology for building a single information network, combining smart controllers, sensors and actuators, is defined by one term fieldbus (field bus, or industrial network).
An industrial network is, firstly, a physical way of combining devices (for example, RS 485) and, secondly, a program-logical protocol of their interaction.
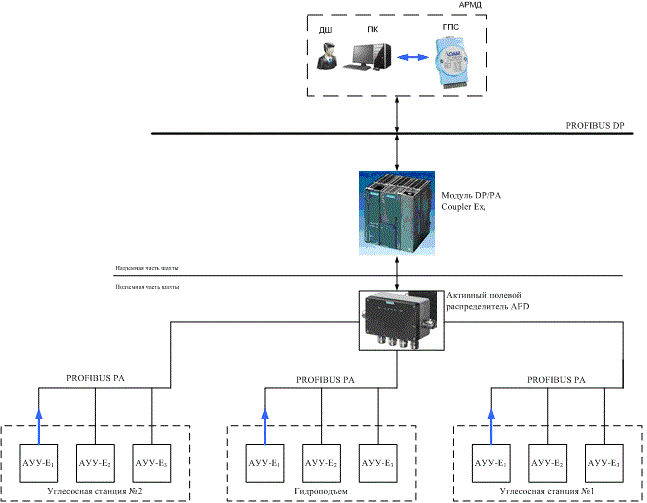
Figure 1 – Structural scheme of an automatic control system of the coal-fueling unit using an industrial network
(animation: 8 frames, infinite repetition cycle, 97 kilobytes)
(AUU-Ei – automatic control devices of the coal-fueling unit, which are located at the facility)
Figure 3 shows:
- АУУ–Е – automatic control device of the coal-fueling unit;
- ДШ – mine manager;
- АРМД – automated dispatcher workplace;
- ПК – industrial computer;
- ГПС – galvanically isolated RS-232 to RS-485 signal converter;
The software-logical protocol for constructing an industrial network for the technological process of pressure hydrotransport of a mine can be realized using RS-485 interface modules, which are provided by the automatic control devices of the coal-fueling unit AUU-E.[11]
Devices AUU-E have chips MAX489CPD. The MAX489CPD is a full-duplex RS-485 / RS-422 transceiver with low power consumption and speed limitation. Each chip contains one transmitter and one receiver.[8]
The unified PROFIBUS-DP and PROFIBUS-PA protocol allows both networks to communicate and thus a combination of time characteristics and intrinsically safe transmission techniques.
PROFIBUS-PA protocol operates on the lower automation level. The PROFIBUS-PA protocol is a field-level network oriented to use in systems automation of continuous and periodic processes. Normalized communication services guarantee the organization of reliable data exchange between automation systems and field level intelligent devices of various manufacturers.
The PROFIBUS-PA network uses electrical communication channels made with shielded twisted pairs. The use of trunk, tree-like and star-shaped topologies up to 1.9 km in length is allowed. At the ends of each PROFIBUS-PA segment, passive terminal elements (SplitConnect Terminator) are installed. The PROFIBUS-PA is connected to the PROFIBUS-DP network via blocks or DP / PA communication modules.
The advantages of a distributed automation system using the PROFIBUS-PA network are: less equipment, efficient design, high reliability of the system operation, ease of maintenance.
Conclusion
The master's work deals with the issue of the development and research of the automatic control system of the coal-fueling unit in order to ensure the continuity of the work, the lower the energy consumption of the technological process of pressure hydrotransport.
The analysis of the operation of the coal-fueling installation of the technological process of hydrotransport as an automation object was performed, and then requirements were formulated for the investigation of the automatic control system of the coal-fueling unit
During the development of the automatic control system, the environmental conditions for the system were taken into account. For example, automatic control device of the coal-fueling unit АУУ-Е is executed under all norms of intrinsic safety, which ensures safe current flow at the moment of transient processes, switching of contacts. The device is designed for operation in mines, including hazardous gas or dust, under conditions of moderate, cold climate at ambient air temperature from minus 10 to 35 ° C and relative humidity up to 100% at a temperature of 35 ° C.
The main advantages of the automatic control system of the coal-fueling unit are the solution of a number of technical problems that can not be solved without automated control: the reduction of working personnel and the increase in labor productivity, monitoring the operation of hydrotransport facilities with the help of automation equipment, visualization system and AUU-E device, reducing the energy consumption of the facility and reducing costs that go to preventing or eliminating various emergencies.
At the time of writing this abstract, the master's thesis is not completed yet. Final completion: June 2018. Full text of the thesis and related materials can be obtained from author or his scientific adviser after the specified date.
References
- НПАОП 10.0-1.01-10. Правила безпеки у вугільних шахтах. Наказ Державного комітету України з промислової безпеки, охорони праці та гірничого нагляду №62 від 23.03.2010. – 150с.
- Маренич К.Н. Электрооборудования технологических установок горных предприятий: [учеб. для студентов высших учеб. заведений] / Маренич К.М., Калинин В.В., Товстик Ю.В., Лизан И.Я., Коломиец В.В. - Донецк: ДонНТУ, Харьков: УИПА, 2009. – 372с.
- Коденцов А.Я. Гидротехнология на шахтаx/ А. Коденцов. – М.: Недра, 1984. – 320 с.
- Технические средства автоматизации в горной промышленности: Учебное пособие / В.И. Груба, Э.К. Никулин, А.С.Оголобченко. – К.:ИСМО, 1998. – 373 с.
- Основы управления гидроэнерготранспортными системами угольных шахт / В.И. Груба, Э.К. Никулин, А.С. Оголобченко; Под ред. В.И. Грубы, – Донецк: Донбасс, 1993. – 225 с.
- Методология расчётов гидродинамических параметров шахтных автоматизированных стационарных установок с центробежными нагнетателями: монография / Э.К. Никулин, И.В. Ковалёва, К.Н. Маренич. – Донецк: ООО "Технопарк ДонГТУ "Унитех", 2015. – 134 с.
- Центробежные насосы и трубопроводные сети в горной промышленности : справочное пособие / Ф.А. Папаяни, Н.Б. Трейнер, В.И. Никитин и др. ; под общ. ред. Ф.А. Папаяни, Н.Б. Трейнера. – Донецк : Восточный издательский дом, 2011. – 334 с.
- Рюмик С.М. 1000 и одна микроконтроллерная схема. Вып. 1. – М.: Додэка – XXI, 2010. – 356 с.
- Единая система конструкторской документации: Справочное пособие / С.С. Борушек, А.А. Волков, М.М. Ефимова и др.–2–е изд., перераб. И доп.– М. : Издательство стандартов, 1989. – 352 с.
- Груба В. И. Технические средства автоматизации в горной промышленности. – В. И. Груба, Э. К. Никулин, А. С. Оголобченко – К.: ИСМО, 1998. – 373 с.
- Ермолинский А.А., Оголобченко А. С. Автоматизированная система управления комплексом углесосных установок гидрошахты / Автоматизация технологических объектов и процессов. Поиск молодых. Сборник научных работ ХVII международной научно – технической конференции аспирантов и студентов в г. Донецке 24 – 25 мая 2017. – c.101 – 107.
- Ермолинский А.А., Оголобченко А. С. Компьютеризированная система автоматического управления шахтной гидротранспортной установкой / Автоматизация технологических объектов и процессов. Поиск молодых. Сборник научных работ ХVI международной научно – технической конференции аспирантов и студентов в г. Донецке 24 – 26 мая 2016. – c.111 – 115.
- Овсянников Ю.А., Кораблев А.А., Топорков А.А., Автоматизация подземного оборудования: Справочник рабочего. – М.: Недра, 1990.– 287 с.
- Баранов В.Н. Применение микроконтроллеров AVR: схемы, алгоритмы, программы. – М.: Издательский дом «Додэка–XXI», 2004. – 288 с.