Abstract
Содержание
- Introduction
- 1. Theme urgency
- 2. Goal and tasks of the research
- 3. Analysis of sump as an object of automation
- 3.1 Technological process of water pumping
- Improvement of automation equipment
- Conclusion
- References
Introduction
Recently in the coal industry there is a tendency to development of deeper horizons, giving an impetus to the creation of new and improvement of existing mechanisms of extraction, transportation of minerals, as well as drainage and ventilation.
Mine drainage is one of the most important technological processes in the mine, from the smooth operation of which depends on work safety in mines. Also, water-drainage installations are large energy consumers.
To the mine pumping units and especially working in the conditions of mining, hazardous gas and dust are increased requirements in relation to safe operation and environmental protection. These requirements are taken into account in the construction of modern new and upgraded pumps [1].
1. Theme urgency
Operation of permanent mine dewatering plants include: management of pump-motor units – start and stop control over the main parameters (pressure in pipes, the flow of the pump, the voltage and current supplying the electric motor, the bearing temperature, the water flow through the discharge device) maintenance, inspection, and ensuring the normal condition of joints, gate valves, check valves, starting and controlling apparatus of the organization and conduct of ongoing preventive maintenance and establishment period pumps to factories for overhaul.
Cavitation, negatively affects the pumps and the process of sump as a whole. Therefore, the fight against it is an important aspect in the process of operation of drain mechanisms.
2. Goal and tasks of the research
The purpose of the research and development is to increase the efficiency of pumps through the use of automation system that monitors and control operation of pumps.
Requirements for the automation system of the main dewatering mechanism:
- the casting of the water pump and the suction pipe, and automatic starting of the pump unit depending on the water level in the sump;
- automatic stop of the pump unit depending on the water level in the sump;
- automatic inclusion of additional pump when reaching the alarm level of water or failure of the working pump;
- automatic combination of technological breaks in the drainage with established periods of maximum electric loads in the power system;
- automatic control over the magnitude of active power which is consumed by the drive motor of the pump;
- automatic control over the magnitude of the coefficient of performance water-drainage installations;
- automatic control of the casting process and the supply pump;
- automatic temperature control bearing assemblies pumps;
- the possibility of transmission of information and alarms to the mine Manager about the status and operation of the pumping unit and the water level in the sump sump station;
3. Analysis of sump as an object of automation
The main functions of the control system are the starting, stopping and automatic regulation of the electric pump units depending on the water level in the collector, which determine the efficiency of pumping water from the mine.
The given top level is an impulse for preparation and start of the unit in work, the bottom-for a stop.
At work on an influx the rational level of water in a collector is supported by constant automatic regulation of pump supply, equal to a tide.
3. Technological process of water pumping
The technological process of pumping water to the surface of the mine is characterized by such modes of operation of the main sump plant [2]:
- start-up;
- working mode;
- emergency mode;
- stop.
Start-up mode starts with constant control of water level in the collector. When water reaches the upper permissible level, it is necessary to prepare the sump installation to work. For this purpose it is necessary to fill the suction pipe and the pump with water before switching on the pump unit. If the start is normal, the pump takes a load, the pressure pipe 6 is set to the nominal press, the pump works with the specified performance, and the start mode is completed.
In working mode, you need control over the process of pumping water by controlling the various parameters of the sump installation: Hydraulic and electrical. Including: water level in the collector; siltation of the preliminary sump; pressure and pump supply; the active power consumed by the drive motor; power consumption; coefficient of useful action of the sump plant.
A number of circumstances can lead to emergency mode: overheating of the pump bearings or drive motor, decrease of pump performance, reduction of pressure in the pipeline, reaching the water of emergency level in the collector. In these cases, except the last, the pump unit is switched off and the backup comes to work.
If the pumping process is normal, the water level decreases to the controlled lower level. At its achievement it is necessary to close a latch and to turn off a pump unit.
Improvement of automation equipment
The selected basic equipment of the ВАВ.1М fulfills all the basic requirements for the automation of the sump plant. However, its functionality does not include the protection of the pumping plant from cavitation. Therefore, one of the directions of improvement of the system of automation of the sump is to equip it with an additional device that performs this function.
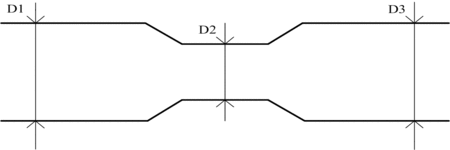
Figure 1 – The occurrence of cavitation in the pipeline
(animation: 17 frames, infinite repetition cycle, 106 kilobytes)
This problem can be solved in case of application of fundamentally new technical means and solutions in the scheme of automation equipment-discrete integral circuitry.
Figure 2 – Technological schemes at the location of the pump above the water level in the collector
Thus, the device БЗК in the equipment of the ВАВ.1М will be given the function of working out of control influences depending on occurrence of emergency situations in flumes pipeline.
Conclusion
Cavitation is the main enemy for the pump, which is fought for many years. The damage caused by this phenomenon affects the efficiency of the pump unit, additional maintenance costs and downtime of the process.
At the moment, the used equipment for the automation of the sump has no absolute protection against cavitation, but constantly conducted research and proposed new technical solutions.
Thus, at the subsequent work on the given theme the device which will allow to receive the information on possibility of occurrence of cavitation, to predict emergency situations and to save consumed electric energy by Reduce the number of launches.
At the time of writing this essay master's work is not yet completed. Final completion: June 2018. The full text of the work and materials on the subject can be obtained from the author or his manager after the specified date.
References
- Попов В.М. Шахтные насосы (теория, расчет и эксплуатация): Справочное пособие – М.: Недра, 1993.– 224 с.
- Тимошенко Г.М. Научные основы проектирования и эксплуатации насосных установок в переходных режимах. Киев; Донецк: Вища шк. Головное изд–во, 1986. – 127 с.
- Попов В.М. Водоотливные установки: Справочное пособие. - М: Недра, 1990.–294 с.
- Груба В.И. Технические средства автоматизации в горной промышленности: Учебное пособие/ В.И. Груба, Э.К. Никулин, А.С. Оголобченко. Под общей редакцией докт. техн. наук, проф. В.И. Грубы. – Киев: ИСМО, 1998. – 373 с.
- Толпежников Л.И. Автоматическое управление процессами шахт и рудников, – М.: Недра, 1985. – 352 с.
- Карелин В.Я. Насосы и насосные станции – М.: Недра, 1979. – 376 с.
- Гейер В.Г., Тимошенко Г.М. Шахтные вентиляторные и водоотливные установки – М.: Недра , 1987.–229 с.