ROBOTICS IN MANUFACTURE
Today it is difficult for us to imagine our life without robots and various automatic devices that have replaced people in various spheres of industry and everyday life. Despite the relatively short history of robotics, it has firmly entered our lives, replacing people in the most dangerous conditions of work.
This article summarizes the history of the development of automation and robotics.
1947 was the starting point for the development of industrial robotics. With the beginning of the nuclear era in the United States, a group of scientists from the Argonne National Laboratory, headed by R. Hertz, created the first of its kind automatic electromechanical manipulator with copy control. This mechanism could repeat human movements and work with hazardous radioactive materials. But he had significant flaws, for example, he did not have feedback on the strength. However, already in 1948, General Electric developed the Handy Man copying manipulator, in which such feedback existed and the operator could perceive the forces affecting the capture of the manipulator.
The first industrial robots appeared in the mid-50s of the twentieth century in the United States. It all started with J. Devol (Im. 1) of an engineer who developed a method for controlling a loading manipulator using punched cards and filed a patent application for a "programmable device for carrying objects" designed by him. Almost immediately, together with J. Engelberg, they created a company that for the first time in the world began to produce industrial robots. This company is called "Unimation".
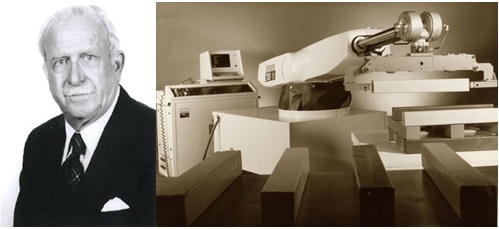
In 1959, the firm "Consolidated Corporation" (USA) published a description of the numerical control manipulator (CNC), and in 1960-1961. In the American press, the first reports appeared on the “Transferrobot” and “Eleximan” manipulators with program management for automation of assembly and other work.
An experimental copy of the Unimation robot was created in 1959, and in the spring of 1961 this industrial robot was put into operation at the foundry site of one of the factories of the General Motors automobile corporation in the city of Ewing - a suburb of Trenton. The robot captured the hot castings of door handles and other parts of the car, lowered them into the pool with coolant and set them on the conveyor, after which they came to the workers for trimming and polishing. Working 24 hours a day, the robot replaced three shifts of workers in a heavy, dirty and dangerous production.
This robot had 5 degrees of mobility, had a hydraulic drive and a two-finger gripping device with a pneumatic drive. Moving objects weighing up to 12 kg was carried out with an accuracy of 1.25 mm. A program carrier in the form of a cam drum with a stepper motor, designed for 200 control commands, and code position sensors were used as the control system. In the training mode, the operator specified a sequence of points through which the links of the manipulator must pass during the working cycle. The robot memorized the coordinates of points and could automatically move from one point to another in a given sequence, repeating the work cycle many times. In the unloading operation, the Unimation injection molding machine worked with a productivity of 135 parts per hour, the rejection rate was 2%, while the manual discharge capacity was 108 parts per hour with a marriage of up to 20%.
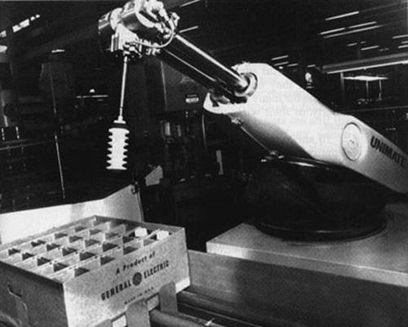
Unmate” in production.
Industrial robot "Versatran", which had three degrees of mobility, used magnetic tape as a program carrier. It was used in a kiln and could load and unload up to 1200 heated bricks per hour. At that time, the cost ratio of electronics and mechanics in the cost of the robot was 75% and 25%, so many control tasks were solved by mechanics. Now this ratio is 25% and 75% respectively. The massive use of industrial robots in Europe began in 1967. The first Unimate robot (Fig. 2) was installed at the Swedish metallurgical plant in Upplands-Vesby. In the same year, Japan entered the era of robotics, which acquired the Versatran robot.
Soon in Japan and Sweden, as well as in the UK, Germany, Italy and Norway, production of own-produced industrial robots began. In 1968, Kawasaki Heavy Industries acquired a license from Unimation for the production of industrial robots and in 1970 Japan became number one in the world, both in terms of the annual production of robots and in the number of industrial robots installed in enterprises in the country .
In the Soviet Union, industrial robots appeared in 1971, thanks to Nikolai Petrovich Belyanin and Boris Nikolaevich Surnin, who created the UM-1 and Universal-50 robots. From 1972 to 1975 in the USSR, a whole range of industrial robots appeared, such as the Universals series (Figure 3), PR-5, Brig-10, IES-690, MP-9C, TUR-10, and others.
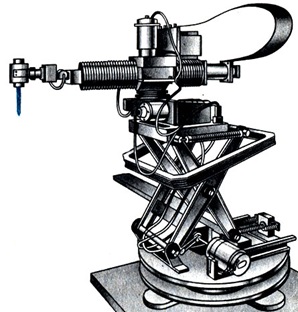
Since the 1960s, robots with feedback based control systems have been developed in the USA. Initially, the master devices in these systems were formed on the switchboard; In 1974, Cincinnati Milakron first used a computer in the robot control system, creating the industrial robot T3 (The Tomorrow Tool).
Today, engineering is the most robotic industry. The use of robots has led to a significant increase in productivity, obtaining high-quality products at a lower price. Robot, unlike humans, does not require good lighting, maintaining the optimum temperature in the field of robots. The production area is also reduced, because industrial robots can be installed both on the wall and on the ceiling. Labor safety is increased, manipulators can work without problems with radioactive or chemical hazardous materials, in rooms with high temperatures or excessive dust. The quality of products increases and the number of defective products decreases. The robot does not need weekends or breaks, it can safely work 24 hours a day, 7 days a week. With proper operation, the cost of acquiring and servicing the robot pays off within one year.
The design of the robot may contain one or several manipulators, while the manipulator itself may have different load capacity, positioning accuracy, and the number of degrees of freedom. It is worth noting that there are simple mechanisms with 2-3 degrees of freedom, and complex mechanisms - more than 6 degrees of freedom. Production processes in engineering are very diverse. They can be divided into procurement processes (forging, casting, stamping), the processing of workpieces (machining of cast, forged, stamped parts), assembly (assembly, welding) and final processing (painting, packaging).
The use of robots can significantly improve the performance of stamping production. This is due to the fact that the time of stamping the part is 1-6 seconds, while the auxiliary operations (submission and removal of the workpiece) take much longer. The use of robots significantly reduces the time for auxiliary operations. In this area, devices are used as with one or two working bodies, and two-capture robots are much more effective.
In machining, robots play a supporting role. Their purpose is to feed and install the workpiece on the machine, as well as remove the machined part from the machine. The effectiveness of robots in this area is obvious - it completely replaces the person when working with metal cutting machines, thereby reducing the likelihood of injury. An important role in mechanical engineering is played by assembly robots (Im.4). They are used to assemble various units and assemblies from individual elements and parts. Their purpose - installation and fixing parts.
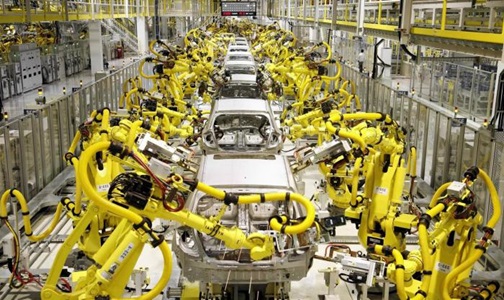
When assembling, the positioning accuracy of individual parts is very important. Modern robots provide accuracy up to 0.05 mm, which is many times greater than the capabilities of the human eye. On a typical assembly mechanism, several robots are installed, each of which performs its own operation - feeding, holding, and coupling parts. The process is controlled by an on-board computer according to a predetermined algorithm. The robot is equipped with feedback sensors, the main of which is a force sensor. Modern mechanisms can perform different types of assembly.
Currently, the industrial robotics market is actively developing. The demand for automation is constantly growing, even among small enterprises. The use of robotics has great potential. It allows you to minimize production time and increase productivity. There is also a reduction in production costs. The introduction of robots reduces the number of workers. In addition, the robot can be entrusted with the implementation of particularly important tasks, which will allow to avoid mistakes and eliminate the so-called "human factor".
Of course, production automation is beneficial to manufacturers. But the process of mass introduction of advanced technologies is not fast enough. The question arises: What slows down the massive introduction of automation? Indeed, the development of the robotic industry requires large investments. The main global companies today still attract more cheap labor than innovative automation solutions. Industrialized countries, such as France, Japan and Germany, locate their production in countries with a developing economy, for example, in India or Brazil. Nevertheless, forecasts for the future development of the industry are quite favorable. At the same time, the trend of production of individual technologies and automation systems is actively developing in the market of industrial robots.
In conclusion, it should also be noted that a large market for robotics can be not only industry. It would not be serious to consider modern robotics as a modern trend in industrial automation, which, after the peak of its popularity, will become just another tool in the hands of an engineer. There are potentially many non-industrial areas of robotization.
List of sources
- Êîðûçåâ Þ.Ã. «Ïðèìåíåíèå ïðîìûøëåííûé ðîáîòîâ» / Èçäàòåëüñòâî «Ìîñêâà» 2015 ãîä.
- Òechno guide www.techno-guide.ru.
- Wikipedia ru.wikiversity.org .