Abstract
- Content
- Introduction
- 1. Actuality of the topic
- 2. The purpose and objectives of the study, the planned results
- 3. Review of research on the topic
- Conclusion
Introduction
One of the most progressive methods of improving the working qualities of a cutting tool is the application on its surface of special wear-resistant coatings with the necessary properties. The coating informs the subject of its hardness or viscosity, chemical resistance or thermal conductivity, and also increases the safety margin. The use of coatings can significantly improve the quality and durability of the cutting tool, thereby confirming the high efficiency and availability of the technology of their application [1].
To improve the reliability of the cutting tool, more and more industrial applications, especially in cutting conditions without the use of cutting fluids, are finding methods for applying wear-resistant coatings. Such methods make it possible to create a fundamentally new instrumental material of a composite type with an optimal combination of the properties of the surface layer and properties that manifest themselves in the volume of the geometric body of the instrument [1].
1. Actuality of the topic.
Today, the rapid automation of production processes in the field of engineering is characterized by the use of high-performance, expensive automated machine equipment, which in turn requires the intensification of machining processes. To date, there is a fairly large amount of research in the field of manufacturing technology of cutting tools with wear-resistant coatings [2].
One of the most effective ways to improve the properties of a metalworking tool is to apply a wide range of monolayer, multilayer and composite wear-resistant coatings using vacuum ion plasma condensation technology based on nitrides, carbides and carbonitrides of refractory metals, which makes it possible to apply coatings of different composition on high-speed tools. steels and hard alloys [2].
The existing principles for constructing special coatings do not always take into account the type of processing and cutting conditions. Hence, it is often recommended to use the same coatings for different cutting conditions and, on the contrary, different coatings are recommended under the same processing conditions. All this is complicated by the insufficient knowledge of the influence of the technological parameters of the coating process, its composition, structure and functionality on the performance of the cutting tool, as well as the insufficient number of recommendations for various machining operations [2].
Coatings affect the contact processes in the cutting zone, the deformation, the force and temperature of cutting, the directivity of heat fluxes, the stress state of the cutting part of the tool, and a number of other parameters of the tool-to-work material system. It is known that the temperature decrease during the operation of such a tool is not due to the heat-shielding characteristics of the coating material, but due to other properties, for example, a change in the friction forces at the contact sites [3].
Vacuum spraying – the transfer of particles of the sprayed substance from the source (place of its transfer into the gas phase) to the surface of the part is carried out along straight paths with a vacuum of 102 Pa and below (vacuum evaporation) and by diffusion and convective transfer in plasma at pressures of 1 Pa (cathode sputtering) and 101-102 Pa (magnetron and ion-plasma sputtering). The fate of each of the particles of the sprayed substance in a collision with the surface of the part depends on its energy, surface temperature and chemical affinity of the film materials and parts. Atoms or molecules that have reached the surface can either be reflected from it, or adsorb and after some time leave it (desorption), or adsorb and form condensate on the surface (condensation). At high particle energies, high surface temperatures and low chemical affinities, the particle is reflected by the surface. The temperature of the surface of the part, above which all particles are reflected from it, and the film does not form, is called the critical vacuum deposition temperature; its value depends on the nature of the materials of the film and the surface of the part, and on the state of the surface. With very small streams of evaporated particles, even if these particles adsorb on the surface, but rarely meet with other similar particles, they are desorbed and cannot form nuclei, i.e. the film does not grow. The critical density of a stream of evaporated particles for a given surface temperature is the lowest density at which particles condense and form a film. The structure of the sprayed films depends on the properties of the material, the state and temperature of the surface, the deposition rate. Films can be amorphous (glassy, for example, oxides, Si), polycrystalline (metals, alloys, Si) or monocrystalline (for example, semiconductor films produced by molecular beam epitaxy). To rationalize the structure and reduce the internal mechanical stresses of the films, increase the stability of their properties and improve adhesion to the surface of products immediately after deposition, without breaking the vacuum, films are annealed at temperatures slightly above the surface temperature during deposition. Often, by vacuum deposition, multilayer film structures of various materials are created [3].
2. The purpose and objectives of the study, the planned results
The purpose of the study is: improving the quality and performance of turning through the use of precast turning tools with special wear-resistant coatings.
The main objectives of the study:
- Perform an analysis of progressive ways to improve the efficiency of carbide cutting tools by applying Wear resistant coatings.
- The rationale for the feasibility of applying wear resistant coatings with special properties depending on functional purpose and processing conditions.
- To establish the effect of wear of the tool blade on the formation The quality of the treated surface, evaluate the increase in durability Tool through the use of wear-resistant coatings.
- To perform an analysis of the temperature state of the cutting tool and yustify the reduction of cutting temperature due to coating.
- Develop recommendations for the selection of coverage that provides increased productivity depending on the type of treatment and cutting conditions.
3. Review of research on the topic
There are more methods for obtaining coatings on the working surfaces of cutting tools. The word coating
is understood to mean such formation on the surface of the instrumental material, which, significantly different in its crystal-chemical, physico-mechanical and thermal properties from the corresponding properties of the instrumental material (base), significantly improves the properties of the latter [4].
Taking into account the specifics of the processes of coating formation, the existing methods can be divided into three main groups. The first group includes methods in which the formation of coatings is carried out mainly due to diffusion reactions between the structures of the tool material that are saturable with elements. The second group includes methods for the formation of coatings by a complex mechanism. The coating is formed due to reactions between vapor-gas mixtures consisting of a compound of metal carrier, a carrier of the second component, which serves as a carrier gas and a reducing agent [4].
At the same time in the process of coating formation a large contribution is made by the substructure of the surface of the tool material and the interdiffusion reactions between the condensate and the tool material. The third group includes coating formation methods by chemical and plasma-chemical reactions of a particle flow simultaneously in volumes of space immediately adjacent to saturable surfaces of the tool material [4].
Chemical-thermal methods of formation of coatings (CTM), based on solid-phase, liquid and gas-phase saturation of the instrument surfaces. CTM includes such methods [5] as the saturation of the surface of tool steels with nitrogen and carbon in gozofazovyh and liquid media, ion nitriding cementation in glow discharge plasma, boronization, nitro-oxidation.
Methods of chemical deposition of coatings (OCPs) are widely used for the application of coatings based on carbides, nitrides, titanium carbionetrides, as well as aluminum oxide on multifaceted non-replaceable carbide plates. Based on OCP methods, technologies have been developed that are used by well-known manufacturers of carbide tools "SandvikComant" (Sweden), "Teledyne" (USA), "Plansee" (Australia), "Eugene Carbon" (France). In the USSR, a method was developed to apply carbide titanium coatings on non-refractory carbide inserts (VNIITS), which was called GT. A variety of OCP methods is the vacuum titanation method (TCC), developed by the Moscow Institute of Transport Engineers in cooperation with the Moscow Hard Alloys Combine [5].
Physical coating deposition (FOP) methods that are known worldwide as PVDs (Phisicalvapordeposition) usually include vacuum evaporation of a refractory metal that forms a coating compound, its partial or complete ionization, reaction gas supply, chemical and plasma chemical reactions, coating condensation on the working surfaces of the cutting tool [6].
Several better coatings are formed using the detonation method, when the coating is formed using the energy of the explosion of gas mixtures. Detonation coatings are characterized by high density and good adhesion with the base. However, this coating has the main drawbacks of the sprayed coatings, moreover, during detonation spraying, noise is generated that exceeds 140 dB. In addition, the very high cost of equipment [6].
Let us also consider the features of TiC coatings obtained by the high-temperature method of the first group, the method of thermal diffusion saturation (DT method). TiCDT coatings have a relatively coarse-grained structure with a high heterogeneity of crystals throughout the coating volume due to geometric distortions of the grains. In addition, it has a non-technometric composition and consists mainly of fused grains of TiC. A transition phase is also formed at the boundary between the coating and the hard alloy, the grains of which have a submicroscopic structure [7].
Vacuum Plasma Coating (CIB). The CIB method is based on the generation of a substance by a cathode spot of a vacuum arc of a high-current low-voltage discharge, which develops exclusively in pairs of electrode material. The supply of reacting gases (nitrogen, methane, etc.) to the vacuum space under conditions of ion bombardment [9] results in the condensation of the coating on the surface of the cutting tool due to the occurrence of plasma chemical reactions [11, 12, 13]. Figure 1 shows the basic diagrams of vacuum-plasma installations of the usual type (Fig. 1, a) and with a plasma-optical system (Fig. 1, b) control of the plasma flow (Hall accelerator).
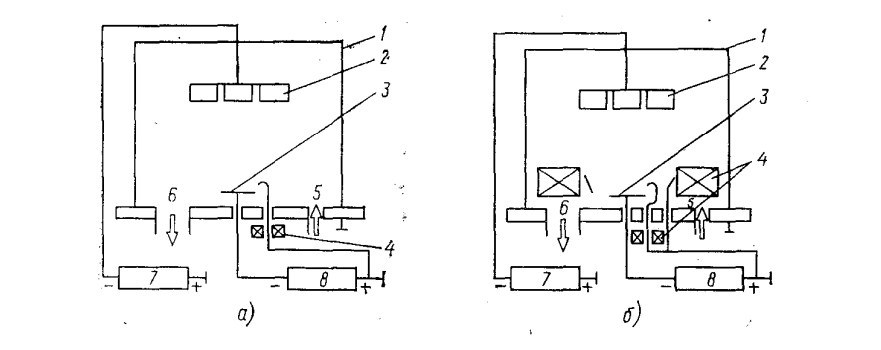
Fig. 1 – Schematic diagram of the vacuum-plasma installation (a) and installation with plasma-optical system (b): 1 – vacuum chamber housing (anode); 2 – cutting tools; 3 – cathode-evaporator metal IV – VI groups of the Periodic system of elements; 4 – electromagnets; 5 – supply of the reaction gas; 6 – to the vacuum pump; 7 – power supply for supplying negative potential to the cutting tool; 8 – arc power source [8].
Optimum properties of wear-resistant coatings can be obtained at a certain ratio between the fundamental characteristics of coating materials. These characteristics include:
- the nature of the relationship in specific materials;
- stoichiometry;
- phase relations;
- anisotropy;
- the nature of solubility in specific systems, which determines the formation of solid solutions, intermetallic compounds, etc. in the coating materials and the substrate [14].
More subtle criteria for optimizing coatings include taking into account the interaction of the surface of a wear-resistant coating with the material being processed, the hardness of the coating itself, its fatigue strength, fracture toughness and ability to accommodate mechanical stresses, and adhesion with the substrate material and the mismatch of their thermal coefficients [14].
From the above, it follows that the main directions of improving the performance of cutting tools with wear-resistant coatings are [15, 16]:
- structural hardening of the wear-resistant coating material;
- the bond strength of the
coating – tool material
border; - change of physico-chemical interaction at the boundary
coating - processed material.
A review of the literature showed that this issue, namely the modeling of the technological processes of applying ion-plasma coatings, was taken up by the department of metallurgy and the technology of materials at OSU. To study the process of deposition of ion-plasma coatings, the use of modeling for complex systems was used. Using simulation, you can reproduce changes in the state of the system, their optimization and forecasting. As a result, a matrix of ranks was developed, including thirteen factors, their dimensions and intervals of variation, which were ranked according to their influence on the wear resistance of coatings. According to the obtained regression equation, the approximate value of the wear resistance of ion-plasma coatings was calculated for the given technological parameters of condensation.
One of the ways to improve the performance and reliability of cutting tools is the application of thin-film wear-resistant coatings, which is what Ph.D., associate professor Tonkonogiy V.M. [2]. The results of studies of the nature of the destruction of coatings are confirmed by practical tests of cutting tools with a wear-resistant coating of titanium nitride applied by the CIB method. As a result, the tool life increased 2 times. Thus, the proposed model of the reliability of the technological system allows to quantify the increase in its level due to the application of wear-resistant coatings on the working surfaces of cutting tools.
Chromium steel has been widely used in mechanical engineering. Many parts of automobile, tractor, diesel engines, compressors, marine machinery and mechanisms are made of chromium steels. Therefore, the development of ways to improve the efficiency of machining of chromium steels is an important task. The scientist Moskalev AA [17], who carried out experimental studies on the wear and durability of the tool, dealt with this question; nitrido-titanium coatings were deposited on the Bulat-3T vacuum-plasma unit. Carbide plates before coating were subjected to polishing with diamond paste, mechanical, and noticeable by ultrasonic cleaning. Experimental studies of the topography of the cutting part of the instrument with and without coatings and also after wear with simultaneous determination of the qualitative and quantitative elemental composition by X-ray spectral analysis were performed using a scanning electron microscope microanalyzer REMMA-102-02. Current wear was determined on a small instrumentation microscope model "MMTS". Nitride coatings led to a sharp decrease in wear intensity and increased durability from 1.5 to 2.5 times in the entire range of experimental cutting conditions. There was a significant change in the nature of contact processes during cutting caused by a noticeable change in external friction conditions, which led to the formation of clearly visible plastic zones. and elastic contacts, reduced the length of the full contact of the chip with the front surface and, accordingly, the length of the plastic contact. The volume of the zone of plastic deformation of the metal being cut has decreased. Coating by 50…70°C reduces the temperature in the cutting zone depending on the cutting conditions and causes the isotherms of maximum temperatures to shift towards the leading cutting edge [17]. In modern production, increased requirements are imposed on wear-resistant coatings for cutting tools, due to a complex of factors. These factors are associated with the improvement of the properties of the coatings, the composition "coating - tool material" and the optimization of the working conditions of the cutting tool. Optimization of the conditions of use of the tool is associated with a decrease in the process of growth and the intensity of adhesion-fatigue processes, an increase in the rigidity of the design of the tool and machinery equipment [18].
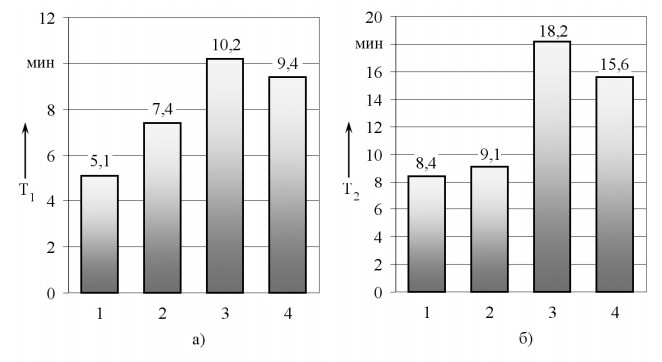
Fig. 2 – The influence of the coating composition on the tool operation time to the formation of cracks in the area of elastic T1 (a) and plastic T2 (b) chip contact when turning workpieces from steel 30HGSA: V =210 m/min, S=0,1 mm/rev; 1 – TiN; 2 – TiСN; 3 – TiZrN; 4 – TiZrCN [18].
In [19-23], principles for constructing multilayer coatings are considered. It is noted that the coating should consist of the following layers: the upper – solid, wear-resistant layer, possessing physical and chemical passivity in relation to the material being processed and high thermodynamic stability; bottom – possessing maximum crystal chemical compatibility with the base material and ensuring maximum adhesion with the tool surface; intermediate layers – having variable properties and providing an adhesive bond between the upper and lower layers, as well as having barrier functions.
In [24-28], the structural-energetic approach to the formation of a multilayer coating is substantiated. According to this position, the application of coatings must be based on a compromise between the inter-durability of adhesion of the coating to the material being processed and the instrumental basis, and the first should be much less.
When designing a multilayer coating, the upper layers should have a higher thermodynamic stability and energy consumption than the lower ones. The lower layers must have high adhesion with the tool material and the upper layers of the coating. Therefore, it is proposed to apply layered and composite multilayer coatings of refractory compounds with high thermodynamic stability, as well as introduce intermediate layers of pure metals (Ti, Zr, Mo) to enhance the adhesive bond and increase the crack resistance of the entire coating (due to the soft layer that fills the intergranular spaces and microcracks on the surface tool base). As noted in the above studies, complex multilayer coatings show a high thermal stability of the composition and properties, have a higher microhardness than the single-element ones. These coatings better resist destruction, which is due to their heterophase structure and change in properties over the cross section. Analyzing the known principles of the formation of a multi-layer coating, it can be noted that all of them are based on the general requirements for wear-resistant coatings. Accumulated experience and a number of studies [29] show that the effectiveness of the same coatings in various machining operations is not the same. Consequently, when designing a multilayer coating, first of all, it is necessary to take into account the conditions of the cutting process of one or another method of mechanical processing, which determines the pattern of wear of the cutting tool and the destruction of the coating on its contact pads.
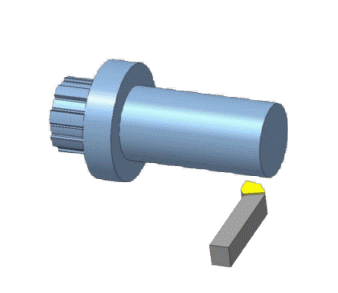
Fig. 3 – Carbide treatment.
Such an approach was used in [11, 30] to develop multilayer coatings designed for intermittent cutting. Based on the analysis of the thermal and stress state of the cutting wedge of the tool, the nature of the destruction of the coating and the wear of the tool, the authors formulated the requirements and the principle of constructing a multilayer coating for face mills. In accordance with the proposed principle, a multi-layer coating should have at least two layers. The top layer should provide the lowest level of contact temperatures and the amplitude of their oscillations at the tool working cycle, and the bottom layer should have high adhesive strength properties and have a high level of compressive stresses. Developed on the basis of this principle, multilayer coatings showed high efficiency when milling structural steels in comparison with single-layer coatings. In this case, the deviation of the proposed principle in the design of a multi-layer coating of bicycles to increase tool wear [11].
One of the ways to improve the performance of the cutting tool is to change the composition of the gas mixture in the process of condensation of the coating. In [7, 31, 32], the effect of acetylene in the gas mixture and the condensation of carbonitride coatings TiCN, TiZrCN, TiCrCN, TiMoCN on their properties and tool performance is considered. The optimum content of acetylene allows to increase the durability of the cutting tool with scarbonitride coatings compared with similar nitride coatings due to changes in mechanical properties. Thus, the period of durability of a cutting tool with a TiCN coating increased by 2.2 times compared with the coating of TiN when turning billets from steel 30HGSA. The maximum increase in the durability of the cutting tool with a coating corresponds to the content of acetylene in the gas mixture (25-40) %. The use of TiCN coatings applied by a CIB method on a high-speed tool allows one to increase its durability period as compared to TiN coating, according to the authors [33], by reducing friction and creating a thermal barrier when applying a carbonitride coating.
Conclusion
An analysis of the current state of the issue has shown the promise of using cutting tools with wear-resistant coatings, as well as further developing the development of advanced methods for coating deposition in order to improve the efficiency of cutting tools. Master's thesis is devoted to increasing the effectiveness of the use of precast turning cutters with special coatings. When writing this essay, the master's work has not yet been completed. The final completion: June 2018. The full text of the work and materials on the topic can be obtained from the author or his manager after the specified date.
References
- Верещака, А. С. Основные аспекты применения и совершенствования режущих инструментов с износостойкими покрытиями / А. С. Верещака //СТИН. – 2000. – №9. – С. 3 – 5.
- Тонконогий В. М. Работоспособность и надежность инструментов с износостойкими покрытиями // Труды Одесского политехнического университета, 1997. Вып. 1.
- Верещака, А. С. Основные аспекты применения и совершенствования режущих инструментов с износостойкими покрытиями / А. С. Верещака //СТИН. – 2000. – №9. – С. 6 – 8.
- Верещака, А. С. Основные аспекты применения и совершенствования режущих инструментов с износостойкими покрытиями / А. С. Верещака //СТИН. – 2000. – №9. – С.8 – 9.
- ХВерещака, А. С. Основные аспекты применения и совершенствованиярежущих инструментов с износостойкими покрытиями / А. С. Верещака //СТИН. – 2000. – №9. – С.9 –12.
- Верещака, А. С. Основные аспекты применения и совершенствования режущих инструментов с износостойкими покрытиями / А. С. Верещака //СТИН. – 2000. – №9. – С.13 – 14.
- Верещака, А. С. Основные аспекты применения и совершенствования режущих инструментов с износостойкими покрытиями / А. С. Верещака //СТИН. – 2000. – №9. – С. 18 – 19.
- Верещака, А. С. Основные аспекты применения и совершенствования режущих инструментов с износостойкими покрытиями / А. С. Верещака //СТИН. – 2000. – №9. – С.20.
- Лобанов, А. В. Влияние ионной бомбардировки на эксплуатационныесвойства инструмента с износостойким покрытием / А. В. Лобанов, В. В.Закураев // Техника машиностроения. – 2001. – №5. – С. 43 – 46.
- Верещака, А. С. Основные аспекты применения и совершенствования режущих инструментов с износостойкими покрытиями / А. С. Верещака //СТИН. – 2000. – №9. – С. 33 – 40.
- Андреев А. А. Применение стационарных эррозионных плазменных ускорителей для получения покрытий (методом КИБ) и результаты исследований материалов плазменных конденсаторов на основе тугоплавких металлов и углеродов. - Тезисы докладов на III Всесоюзной конфиренции по плазменным ускорителям. Минск: Знание 1976, с. 218 - 221.
- .Лунев В. М. Исследование характеристик плазмы вакуумных источников металлических дуг: Труды IVВсесоюзной конференции по физике низкотемпературной плазмы. Киев: институт физики АН УССР, 1975, с. 40 - 45.
- Покрытия из карбида молибдена, полученные методы осаждения плазменных потоков в вакууме КМБ. - Физика и химия обработки материалов, 1979, № 2, с. 169 - 170.
- Табаков, В. П. Износостойкие покрытия режущего инструмента, работающего в условиях непрерывного резания / В. П. Табаков, А. В. Чихранов. Ульяновск: УлГТУ,2007. c. 8 – 9.
- Табаков, В. П. Работоспособность режущего инструмента сизносостойкими покрытиями на основе сложных нитридов икарбонитридов титана / В. П. Табаков. – Ульяновск: УлГТУ, 1998. – 123 с.
- Верещака, А. С. Физические основы процесса резания и изнашиваниярежущего инструмента с износостойкими покрытиями: учебное пособие /А. С. Верещака, В. П. Табаков. – Ульяновск: УлГТУ, 1998. – 144 с.
- А. А. Москалев Статья: "Исследование износостойкости режущего инструмента с покрытием при обработке хромистых сталей" – 2009.
- Моисеев, В. Ф. Влияние азота на структуру и свойства упрочняющихповерхностных покрытий на основе титана / В. Ф. Моисеев, Г. С. ФуксРабинович, Г. К. Досбаева // Физика и химия обработки материалов –1991.– №2. – С. 118 – 121.
- Верещака, А. С. Работоспособность режущего инструмента сизносостойкими покрытиями / А. С. Верещака. – М.: Машиностроение,1993. – 336 с.
- .Табаков, В. П. Работоспособность торцовых фрез с многослойнымиизносостойкими покрытиями / В. П. Табаков, М. Ю. Смирнов, А. В.Циркин. – Ульяновск: УлГТУ, 2005. – 151 с.
- Кабалдин, Ю. Г. Структура, прочность и износостойкость композиционныхинструментальных материалов. – Владивосток: Дальнаука, 1996. – 183 с.
- Верещака, А. С. Основные аспекты применения и совершенствованиярежущих инструментов с износостойкими покрытиями / А. С. Верещака //СТИН. – 2000. – №9. – С. 33 – 40.
- Кабалдин, Ю. Г. Повышение работоспособности режущей частиинструмента из быстрорежущей стали / Ю. Г. Кабалдин // Вестникмашиностроения. – 1996. – №6. – С. 27 – 32.
- Верещака, А. С. Влияние структуры покрытий на работоспособностьтвердосплавных инструментов / А. С. Верещака, Ю. Г. Кабалдин // Вестникмашиностроения. – 1986. – №8. – С. 38 – 42.
- Кабалдин, Ю. Г. Повышение прочности и износостойкости режущегоинструмента термопластическим упрочнением / Ю. Г. Кабалдин. –Хабаровск: Изд-во ДГУ, 1986. – 53 с.
- ГКабалдин, Ю. Г. Механизмы разрушения режущей части инструмента ипути повышения производительности обработки / Ю. Г. Кабалдин //Технологические исследования и разработки при создании САПРтехнологических процессов: сб. научн. трудов. – Владивосток: Изд-во ДГУ,1984. – С. 72 – 82.
- МКабалдин, Ю. Г. Термодинамический анализ разрушенияинструментальных материалов / Ю. Г. Кабалдин, А. А. Бурков // Вопросы248 теории и технологии литейных процессов: сб. научн. трудов. – Хабаровск:ХабПИ, 1985. – С. 36 – 44.
- Кабалдин, Ю. Г. Структурно-энергетический подход к процессуизнашивания режущего инструмента / Ю. Г. Кабалдин // Вестникмашиностроения. – 1990. – №12. – С. 62 – 68.
- Табаков, В. П. Работоспособность режущего инструмента сизносостойкими покрытиями на основе сложных нитридов икарбонитридов титана / В. П. Табаков. – Ульяновск: УлГТУ, 1998. – 123 с.
- Табаков, В. П. Повышение работоспособности торцевых фрез путемсовершенствования структуры износостойких покрытий / В. П. Табаков, Н.А. Ширманов , М. Ю. Смирнов // СТИН. – 2002. – №2. – С. 6 – 10.
- Табаков, В. П. Влияние состава износостойкого покрытия на контактные итепловые процессы и на изнашивание режущего инструмента / В. П.Табаков // СТИН. – 1997. – №10. – С. 20 – 24.
- Табаков, В. П. Применение покрытий на основе карбонитридов титана дляповышения стойкости режущего инструмента / В. П. Табаков // СТИН. – 1991. – №11. – С.18 – 19.
- Внуков, Ю.Н. Нанесение износостойких покрытий на быстрорежущий инструмент. – Киев: Тэхника, 1992. – 143 с.