Реферат за темою випускної роботи
Зміст
- Вступ
- 1. Актуальність теми
- 2. Мета і задачі дослідження та заплановані результати
- 3. Огляд досліджень та розробок
- Висновки
- Перелік посилань
Вступ
Одним з найбільш прогресивних методів підвищення робочих якостей ріжучого інструменту є нанесення на його поверхню спеціальнихізносостойкіх покриттів, що володіють необхідними властивостями. Покриття повідомляє предмету свою твердість або в’язкість, хімічну стійкість або теплопровідність, а також збільшує запас міцності. Використання покриттів дозволяє істотно підвищити якість і стійкість різального інструменту, тим самим, підтверджуючи високу ефективність і перспективність технології їх нанесення [1].
Для підвищення надійності різального інструменту все більше промислове застосування, особливо в умовах різання без застосування мастильно-охолоджуючих технологічних середовищ, знаходять методи нанесення зносостійких покриттів. Такі методи дозволяють створити принципово новий інструментальний матеріал композиційного типу з оптимальним поєднанням властивостей поверхневого шару і властивостей, що виявляються в обсязі геометричного тіла інструменту [1].
1. Актуальність теми
На сьогоднішній день стрімке автоматизація виробничих процесів в галузі машинобудування характеризується застосуванням високопродуктивного, дорогого автоматизованого верстатного обладнання, що в свою чергу вимагає інтенсифікації процесів обробки різанням. На цей час існують досить велика кількість наукових досліджень в області технології виготовлення ріжучого інструменту зі зносостійкими покриттями [2].
Одним з найбільш ефективних шляхів підвищення властивостей металообробного інструменту є нанесення на робочі поверхні широкої гами моношарових, багатошарових і композиційних зносостійких покриттів за технологією вакуумного іонно-плазмового конденсацііна основі нітридів, карбідів і карбонитридов тугоплавких металів, яка дає можливість наносити покриття різного складу на інструмент з швидкорізальних сталей і твердих сплавів [2].
Існуючі принципи побудови спеціальних покриттів не завжди враховують вид обробки і умови різання. Звідси часто одні й ті ж покриття рекомендують використовувати для різних умов різання і, навпаки, – в однакових умовах обробки рекомендуються різні покриття. Все це ускладнюється недостатньою вивченістю впливу технологічних параметрів процесу нанесення покриття, його складу, будови та функціонального призначення на працездатність ріжучого інструменту, а також недостатньою кількістю рекомендацій для різних операцій механічної обробки [2].
Покриття впливають на контактні процеси в зоні різання, деформації, сили і температури різання, спрямованості теплових потоків, напруженого стану ріжучої частини інструменту і на ряд інших параметрів системи інструмент – опрацьований матеріал
. Відомо, що зниження температури в процесі роботи такого інструменту відбувається не за рахунок теплозахисних характеристик матеріалу покриття, а за рахунок інших властивостей, наприклад, зміни сил тертя на майданчиках контактах [3].
Вакуумне напилення – перенесення частинок напилюваного речовини від джерела (місця його перекладу в газову фазу) до поверхні деталі здійснюється по прямолінійних траєкторіях при вакуумі 102 Па і нижче (вакуумне випаровування) і шляхом дифузійного і конвективного переносу в плазмі при тисках 1 Па (катодного розпилення) і 101-102 Па (магнетрон і іонно-плазмове розпилення). Доля кожної з частинок напилюваного речовини при зіткненні з поверхнею деталі залежить від її енергії, температури поверхні і хімічної спорідненості матеріалів плівки і деталі. Атоми або молекули, які досягли поверхні, можуть або відбитися від неї, або адсорбуватися і через деякий час покинути її (десорбція), або адсорбуватися і утворювати на поверхні конденсат (конденсація). При високих енергіях частинок, великій температурі поверхні і малому хімічну спорідненість частка відбивається поверхнею. Температура поверхні деталі, вище якої всі частинки відбиваються від неї, і плівка не утворюється, називається критичною температурою напилення вакуумного; її значення залежить від природи матеріалів плівки і поверхні деталі, і від стану поверхні. При дуже малих потоках випаровуваних частинок, навіть якщо ці частинки на поверхні адсорбуються, але рідко зустрічаються з іншими такими ж частками, вони десорбируются і не можуть утворювати зародків, тобто плівка не росте. Критичною щільністю потоку випаровуваних частинок для даної температури поверхні називається найменша щільність, при якій частинки конденсуються і формують плівку. Структура напилюються плівок залежить від властивостей матеріалу, стану і температури поверхні, швидкості напилення. Плівки можуть бути аморфними (стеклообразнимі, наприклад, оксиди, Si), полікристалічний (метали, сплави, Si) або монокристаллическими (наприклад, напівпровідникові плівки, отримані молекулярно-променевої епітаксії). Для упорядкування структури та зменшення внутрішніх механічних напружень плівок, підвищення стабільності їх властивостей і поліпшення адгезії до поверхні виробів відразу ж після напилення без порушення вакууму виробляють відпал плівок при температурах, кілька перевищують температуру поверхні при покритті. Часто за допомогою вакуумного напилення створюють багатошарові плівкові структури з різних матеріалів [3].
2. Мета і задачі дослідження та заплановані результати
Метою дослідження є підвищення якості та продуктивності токарної обробки за рахунок застосування збірних токарних різців зі спеціальними зносостійкими покриттями
Основні задачі дослідження:
- Виконати аналіз прогресивних засобів підвищення ефективності твердосплавного ріжучого інструменту за рахунок нанесення ізносостійких покриттів.
- Обґрунтування техніко-економічної доцільності нанесення зносостійких покриттів зі спеціальними властивостями в залежності від функціонального призначення та умов обробки.
- Встановити вплив зношування леза інструменту на формування кості обробленої поверхні, оцінити підвищення стійкості iнструменту за рахунок застосування зносостійких покриттів.
- Виконати ааліз температурного стану ріжучого інструменту ібґрунтувати зниження температури різання за рахунок нанесення покриття.
- Розробити рекомендації щодо вибору покриття, що забезпечує підвищення продуктивності в залежності від виду обробки і мов різання.
3. Огляд досліджень та розробок
Існує більше число методів отримання покриттів на робочих поверхнях ріжучих інструментів. Під словом покриття
будемо розуміти таку освіту на поверхні інструментального матеріалу, яке, істотно відрізняється за своїми Крісталлохимічеськая, фізико-механічних і теплофізичних властивостей від відповідних властивостей інструментального матеріалу (основи), значно покращує властивості останнього [4].
З урахуванням специфіки протікання процесів формування покриттів існуючі методи можна розділити на три основні групи. До першої групи належать методи, при яких формування покриттів здійснюється переважно за рахунок дифузійних реакцій між насичується елементами структурами інструментального матеріалу. До другої групи належать методи формування покриттів з комплексного механізму. Покриття утворюється за рахунок реакцій між парогазовими сумішами, що складаються із з’єднання метало носія, носія другого компонента, службовця як газом-транспортером, так і відновником [4].
При цьому одночасно в процесі формування покриття великий внесок вносять субструктура поверхні матеріалу інструменту і інтердіффузіонние реакції між конденсатом і матеріалом інструменту. До третьої групи можна віднести методи формування покриттів за рахунок хімічних і плазмохімічних реакцій потоку частинок одночасно в обсягах простору, що безпосередньо примикає до насичується поверхнях інструментального матеріалу [4].Хіміко-термічні методи освіти покриттів (ХТМ), засновані на твердофазових, рідинному ігазофазовом насиченні поверхонь інструменту. ХТМ включає такі методи [5], як насичення поверхні інструментальних сталей азотом і вуглецем в гозофазових і рідких середовищах, іонну Азотування цементація в плазмі тліючого розряду, борирование, нітро оксидування.Методи хімічного осадження покриттів (ХОП) набули широкого поширення для нанесення покриттів на основі карбідів, нітридів, карбіонетрідов титану, а також оксиду алюмінію на багатогранні непереточувані твердосплавні пластинки. На підставі методів ХОП розроблені технології, застосування відомими фірмами-виробниками твердосплавних інструментів СандвікКоромант
(Швеція), Теледайн
(США), Планзее
(Австралія), Юджин карбон
(Франція). В СРСР розроблений метод нанесення карбідотітанових покриттів на непереточувані твердосплавні пластинки (ВНІІТС), який отримав найменування ГТ. Різновидом методів ХОП є метод вакуумного Тітанірованіє (КВТК), розроблений Московським інститутом інженерів транспорту спільно з Московським комбінатом твердих сплавів [5]. Методи фізичного осадження покриття (ФОП) отримали назву в світовій практиці PVD (Phisicalvapordeposition) зазвичай включають вакуумне випаровування тугоплавкого металу-просвітників з’єднання покриття, його часткову або повну іонізацію, подачу реакційного газу, хімічні і плазмохімічні реакції, конденсацію покриття на робочих поверхнях різального інструменту [6].
Кілька більш якісні покриття формуються при використанні детонаційного методу, коли покриття утворюється за допомогою енергії вибуху газових сумішей. Детонаційні покриття характеризуються високою щільністю і гарну адгезію з основою. Однак цим покриттям притаманні головні недоліки напилюються покриттів, до того ж при детонаційному напиленні створюється шум, що перевищує 140 дБ. Комі того, дуже висока вартість обладнання [6].
Розглянемо також особливості покриттів TiC, одержуваних високотемпературним методом першої групи-методом термодиффузионного насичення (метод ДТ). Покриття TiCДТ має відносно грубозернисту будову з високою неоднорідністю кристалів за обсягом покриття геометричними спотвореннями зерен. Крім того, воно має не технометріческій склад і складається в основному з зрощених зерен TiC. На кордоні покриття і твердого сплаву також формується перехідна фаза, зерна якої мають субмікроскопічна будова [7].
Вакуумно-полум’яне покриття (КІБ). Метод КІБ заснований генерації речовини катодних плямою вакуумної дуги потужнострумового низьковольтного розряду, що розвивається виключно в парах матеріалу електрода. Подача в вакуумний простір реагують газів (азот, метан та ін.) В умовах іонного бомбардування [9] призводять до конденсації покриття на поверхні ріжучого інструменту завдяки протіканню плазмохимических реакцій [11,12,13. На рис.1 показані принципові схеми вакуумно-плазмових установок звичайного типу (рис. 1, а) і з плазмооптіческой системою (рис. 1, б) управління плазмовим потоком (холлівських прискорювач).
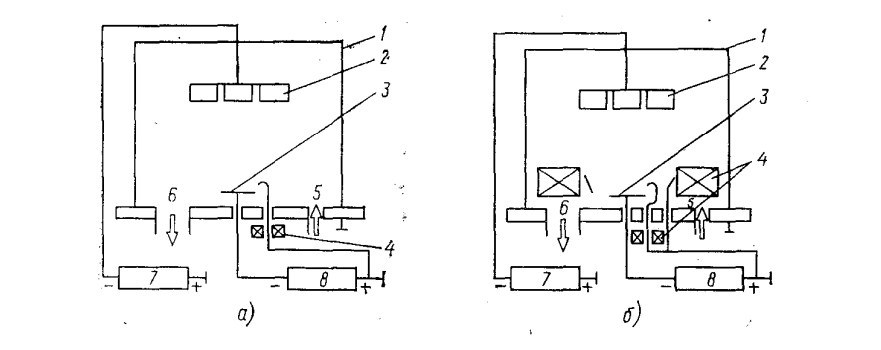
Малюнок 1 – Принципова схема вакуумно-плазмового установки (а) і установки з плазмооптіческой системою (б): 1 – корпус вакуум-камери (анод); 2 – ріжучі інструменти; 3 – катод-випарник метала IV – VI груп Періодичної системи елементів; 4 – електромагніти; 5 – подача реакційного газу; 6 – до вакуумного насоса; 7 – джерело живлення для подачі негативного потенціалу до ріжучого інструменту; 8 – джерело живлення дуги [8].
Оптимальні властивості зносостійких покриттів можна отримати привизначенні співвідношенні між фундаментальними характерістіками іматеріалов покриттів. До таких характеристик відносяться:
- Характер зв’язку вконкретних матеріалах;
- Стехіометрії;
- Фазові співвідношення;
- Анізотропія;
- Характер розчинності в конкретних системах, що визначає освіту в матеріалах покриття і в підкладці твердих растворов, интерметаллидов i т.п. [14].
Більш тонкі критерії оптимізації покриттів включають учетвзаімодействія поверхні зносостійкого покриття з обрабативаеми мматеріалом, твердість самого покриття, його міцність від утоми, вязкостьразрушенія і здатність до акомодації механічної напруги, а также адгезію з матеріалом підкладки та невідповідність їх коеффіціентiв термічного [14].
З вищесказаного випливає, що основними напрямками повишення работоспособності ріжучого інструменту зі зносостійкими покритіямі являются [15, 16]:
- Структурне зміцнення матеріалу зносостійкого покриття;
- Підвищення міцності зв’язку кордону покриття;
- Iнструментальний матеріал;
- Зміна фізико-хімічної взаємодії на кордоні
покриття – опрацьований матеріал
.
На сьогоднішній день стрімке автоматизація виробничих процесів в галузі машинобудування характеризується застосуванням високопродуктивного, дорогого автоматизованого верстатного обладнання, що в свою чергу вимагає інтенсифікації процесів обробки різанням. Це посилює умови експлуатації ріжучого інструменту, підвищує вимоги до якості і зносостійкості різального інструменту.
Огляд літератури показав, що цим питанням, а саме моделюванням технологічних процесів нанесення іонно-плазмових покриттів занімались на кафедрі металознавства і технології матеріалів ОДУ. Для вивчення технологічного процесу нанесення іонно-плазмових покриттів було застосовано використання моделювання для складних систем. За допомогою моделювання можна відтворити зміни в стані системи, їх оптимізацію і прогнозування. У слідстві чого була розроблена матриця рангів, що включає тринадцять факторів, їх розмірність і інтервали варіювання, які ранжувались відповідно до їх впливом на зносостійкість покриттів. За отриманим рівнянням регресії було розраховано орієнтовне значення зносостійкості іонно-плазмових покриттів при заданих технологічних параметрах конденсації.
Одним із шляхів підвищення працездатності та надійності ріжучих інструментів є нанесення тонкоплівкових зносостійких покриттів, чим і займався кандидат технічних наук, доцент Тонконогий В.М. [2]. Результати досліджень характеру руйнування покриттів підтверджені практичними випробуваннями ріжучих інструментів з зносостійким покриттям з нітриду титану, нанесеним методом КІБ. В результаті чого стійкість інструменту підвищилася в 2 рази. Таким чином, запропонована модель надійності технологічної системи дозволяє кількісно оцінити підвищення її рівня за рахунок нанесення зносостійких покриттів на робочі поверхні ріжучих інструментів.
Хромисті стали набули широкого застосування в машинобудуванні. Багато деталей автомобільних, тракторних, дизельних двигунів, компресорів, суднових машин і механізмів виготовляють з хромистих сталей. Отже, розробка шляхів підвищення ефективності механічної обробки хромистих сталей є актуальним завданням. Даним питанням займався вчений Москальов А.А. [17] який виконував експериментальні дослідження зносу і стійкості інструменту, нітрідотітановие покриття наносилися на вакуумно-плазмового установці Булат-3Т
. Твердосплавні пластини перед нанесенням покриттів піддавали поліруванню алмазною пастою, механічної, а замет ультразвукової очищенням. Експериментальні дослідження топографі і поверхностей ріжучої частини інструменту з покриттями і без покриттів, а також після зносу з одночасним визначенням якісного іколічественного елементного складу методом рентгеноспектрального аналізавиполнялі за допомогою растрового електронного мікроскопа-мікроаналізатора РЕММА-102-02. Поточний знос визначали на малому інструментальноммікроскопе моделі ММЦ
.
Нітрідотітановие покриття зумовили різке зниження інтенсивності зносу і підвищення стійкості від 1,5 до 2,5 разів у всьому інтервалі експериментальних режимів резанія. Відбулося суттєва зміна характеру контактних процесів взоне різання, пов язаного з помітною зміною умов зовнішнього тертя, що зумовило формування чітко помітних зон пластичного і упругого контактів, зменшилася довжина повного контакту стружки з переднейповерхностью і відповідно довжина пластичного контакту. Знизився обсяг зони пластичної деформації зрізаного металу. Покриття на 50…70°C в залежності від режимів різання сніжаеттемпературу в зоні різання і обумовлює зсув ізотерм максімальних температур в напрямку головної різальної крайки
У сучасному виробництві до зносостійким покриттям ріжучого інструменту пред’являються підвищені вимоги, обусловленние комплексом факторів. Ці фактори пов’язані з удосконаленням властивостей покриттів, композиції покриття – інструментальний матеріал
і оптимізацією умов роботи ріжучого інструменту. Оптимізація умов використання інструменту пов’язана зі зниженням процессанаростообразованія і інтенсивності адгезионно-втомних процесів, підвищенням жорсткості конструкції інструменту і верстатного обладнання [18].
Велике різноманіття типів покриттів, що наносяться на режущій інструмент, можна класифікувати за певним набором властивостей і функцій, що визначають їх службове призначення: за складом покриття і егостроенію.
Час початку утворення тріщин залежить як від складу покриття, так і режиму різання. Так при різанні на швидкості V=210 м/хв і подачі S=0,1 мм/об (мал. 2) час до утворення тріщин на ділянці пружного контакту склало для інструменту з покриттям TiN 5,1 хв. При використанні 36 покриттів TiCN, TiZrN і TiZrCN воно збільшується в 1,5, 2,0 і 1,9 разів відповідно. Зниження швидкості різання V і подачі S веде до підвищення часу до утворення тріщин і зменшення різниці в даному показнику для інструментів з різними покриттями.
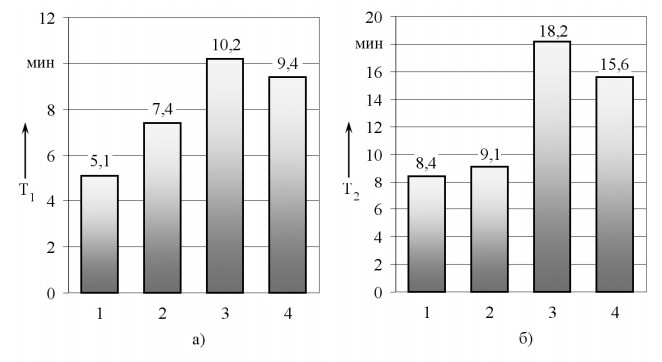
Мал. 2. – Вплив складу покриття на час роботи інструменту до утворення тріщин на ділянці пружного Т1 (а) і пластичного Т2 (б) контакту стружки при точінні заготовок із сталі 30ХГСА: V=210 м/хв, S=0,1 мм/об; 1 – TiN; 2 – TiСN; 3 – TiZrN; 4 – TiZrCN [18]
В роботах [19-23] розглядаються принципи построеніямногослойних покриттів. Відзначається, що покриття повинне складатися знаступних шарів: верхнього – твердого, зносостійкого шару, обладающегофізіко-хімічної пасивністю по відношенню до обрабативаемомуматеріалу і високою термодинамічною стійкістю; нижнього – володіє максимальної крісталлохимічеськой сумісністю сматеріалом основи і забезпечує максимальну адгезію зповерхні інструменту; проміжних шарів – мають переменниесвойства і забезпечують адгезионную зв’язок між верхнім і ніжнімслоямі, а також володіють бар’єрними функціями.
В роботах [24-29] доводиться структурно-енергетичний підхід к формірованію багатошарового покриття. Згідно з цим положенням прінанесеніі покриттів необхідно грунтуватися на компромісі междупрочностью зчеплення покриття з оброблюваним матеріалом і сінструментальной основою, причому, перше має бути значно менше. При конструюванні багатошарового покриття верхні шари повинні обладать более високою термодинамічною стійкістю і енергоємністю, чем ніжніе. Нижні шари повинні мати високу адгезію з інструментальнимматеріалом і верхніми шарами покриття. Тому пропонується наносітьслоістие і композиційні багатошарові покриття з тугоплавкіх соедіненій, що володіють високою термодинамічною стійкістю, а также вводіть проміжні шари з чистих металів (Ti, Zr, Mo) для повишенія адгезіонной зв’язку і збільшення тріщиностійкості всього покриття (за счетмягкого шару, який заповнює межзеренного простору і мікротріщини на поверхні інструментальної основи). Як наголошується в рассмотреннихвише роботах, складні багатошарові покриття показують високуютермостабільность складу і властивостей, володіють більш високоймікротвердостью, ніж одноелементні. Дані покриття лучше сопротівляются руйнування, що обумовлюється їх гетерофазних будовою і зміною властивостей по перетину.
Аналізуючи відомі принципи формування многослойногопокритія можна відзначити, що всі вони побудовані на основі загальних вимог, що пред'являються до зносостійким покриттям. Накопичений досвід і рядісследованій [29] показують, що ефективність одних і тих же покриттів нарізних операціях механічної обробки не однакова. Отже, при конструюванні багатошарового покриття, в першу чергу, необхідновраховувати умови процесу різання того або іншого методу механіческойобработкі, що визначає характер зносу ріжучого інструменту іразрушенія покриття на його контактних майданчиках.
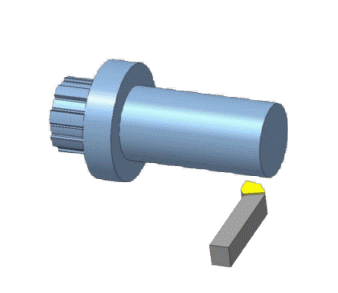
Рисунок 3 – Обрабка твердосплавними пластинами
Такий підхід биліспользован в роботах [11, 30] для розробки багатошарових покриттів, призначених для умов переривчастого різання. На основі аналізатеплового і напруженого стану ріжучого клина інструмента, характераразрушенія покриття і зношування інструменту авторами билісформуліровани вимоги і принцип побудови багатошарового покритіядля торцевих фрез. Відповідно до запропонованого принципом многослойноепокритіе повинно мати мінімум два шари. Верхній шар повинен обеспечіватьнаіменьшій рівень контактних температур і амплітуду їх коливань зарабочій цикл інструменту, а нижній – володіти високими адгезіоннопрочностнимісвойствамі і мати високий рівень стискають напруг.
Розроблені на основі даного принципу багатошарові покриття показалівисокую ефективність при фрезеруванні конструкційних сталей посравнению з одношаровими покриттями. При цьому відступ отпредложенного принципу при конструюванні багатошарового покриття ВелоКиїв підвищення зносу інструменту [11].
Одним із шляхів підвищення працездатності різального інструментаявляется зміна складу газової суміші в процесі конденсації покриття. У роботах [7, 31, 32] розглядається вплив ацетилену в складі газової смесіпрі конденсації карбонітридним покриттів TiCN, TiZrCN, TiCrCN, TiMoCNна їх властивості та працездатність інструменту. Оптимальне содержаніеацетілена дозволяє підвищити період стійкості різального інструменту скарбонітріднимі покриттями в порівнянні з аналогічними нітрідниміпокритіямі за рахунок зміни механічних властивостей. Так, період стойкостірежущего інструменту з покриттям TiCN підвищився в 2,2 рази в порівнянні спокритіем TiN при точінні заготовок із сталі 30ХГСА. Максімальноеувеліченіе періоду стійкості різального інструменту з покритіемсоответствует змістом ацетилену в газовій суміші (25 – 40) %. Прімененіепокритій TiCN, нанесених методом КІБ на швидкорізальний інструментпозволяет збільшити його період стійкості в порівнянні з покриттям TiN Помнению авторів [33] за рахунок зниження тертя і створення теплового барьерапрі нанесенні карбонітридним покриття TiCN, TiZrN і TiZrCN воно збільшується в 1,5, 2,0 і 1,9 разів відповідно. Зниження швидкості різання V і подачі S веде до подвищення часу до утворення тріщин і зменшення різниці в даному показнику інструментів з різними покриттями.
Висновки
Аналіз сучасного стану питання показав перспективність застосування ріжучого інструменту зі зносостійкими покриттями, а також подальшого розвитку питань розробки прогресивних методовнанесенія покриттів з метою підвищення ефективності роботи ріжучого інструменту. Магістерська робота присвячена підвищенню ефективності застосування збірних токарних різців зі спеціальними покриттями. При написанні даного реферату магістерська робота ще не завершена.Окончательное завершення: червень 2018 року. Повний текст роботи та матеріали по темі можуть бути отримані у автора або його керівника після зазначеної дати.
Перелік посилань
- Верещака, А. С. Основные аспекты применения и совершенствования режущих инструментов с износостойкими покрытиями / А. С. Верещака //СТИН. – 2000. – №9. – С. 3 – 5.
- Тонконогий В. М. Работоспособность и надежность инструментов с износостойкими покрытиями // Труды Одесского политехнического университета, 1997. Вып. 1.
- Верещака, А. С. Основные аспекты применения и совершенствования режущих инструментов с износостойкими покрытиями / А. С. Верещака //СТИН. – 2000. – №9. – С. 6 – 8.
- Верещака, А. С. Основные аспекты применения и совершенствования режущих инструментов с износостойкими покрытиями / А. С. Верещака //СТИН. – 2000. – №9. – С.8 – 9.
- ХВерещака, А. С. Основные аспекты применения и совершенствованиярежущих инструментов с износостойкими покрытиями / А. С. Верещака //СТИН. – 2000. – №9. – С.9 –12.
- Верещака, А. С. Основные аспекты применения и совершенствования режущих инструментов с износостойкими покрытиями / А. С. Верещака //СТИН. – 2000. – №9. – С.13 – 14.
- Верещака, А. С. Основные аспекты применения и совершенствования режущих инструментов с износостойкими покрытиями / А. С. Верещака //СТИН. – 2000. – №9. – С. 18 – 19.
- Верещака, А. С. Основные аспекты применения и совершенствования режущих инструментов с износостойкими покрытиями / А. С. Верещака //СТИН. – 2000. – №9. – С.20.
- Лобанов, А. В. Влияние ионной бомбардировки на эксплуатационныесвойства инструмента с износостойким покрытием / А. В. Лобанов, В. В.Закураев // Техника машиностроения. – 2001. – №5. – С. 43 – 46.
- Верещака, А. С. Основные аспекты применения и совершенствования режущих инструментов с износостойкими покрытиями / А. С. Верещака //СТИН. – 2000. – №9. – С. 33 – 40.
- Андреев А. А. Применение стационарных эррозионных плазменных ускорителей для получения покрытий (методом КИБ) и результаты исследований материалов плазменных конденсаторов на основе тугоплавких металлов и углеродов. - Тезисы докладов на III Всесоюзной конфиренции по плазменным ускорителям. Минск: Знание 1976, с. 218 - 221.
- .Лунев В. М. Исследование характеристик плазмы вакуумных источников металлических дуг: Труды IVВсесоюзной конференции по физике низкотемпературной плазмы. Киев: институт физики АН УССР, 1975, с. 40 - 45.
- Покрытия из карбида молибдена, полученные методы осаждения плазменных потоков в вакууме КМБ. - Физика и химия обработки материалов, 1979, № 2, с. 169 - 170.
- Табаков, В. П. Износостойкие покрытия режущего инструмента, работающего в условиях непрерывного резания / В. П. Табаков, А. В. Чихранов. Ульяновск: УлГТУ,2007. c. 8 – 9.
- Табаков, В. П. Работоспособность режущего инструмента сизносостойкими покрытиями на основе сложных нитридов икарбонитридов титана / В. П. Табаков. – Ульяновск: УлГТУ, 1998. – 123 с.
- Верещака, А. С. Физические основы процесса резания и изнашиваниярежущего инструмента с износостойкими покрытиями: учебное пособие /А. С. Верещака, В. П. Табаков. – Ульяновск: УлГТУ, 1998. – 144 с.
- А. А. Москалев Статья: "Исследование износостойкости режущего инструмента с покрытием при обработке хромистых сталей" – 2009.
- Моисеев, В. Ф. Влияние азота на структуру и свойства упрочняющихповерхностных покрытий на основе титана / В. Ф. Моисеев, Г. С. ФуксРабинович, Г. К. Досбаева // Физика и химия обработки материалов –1991.– №2. – С. 118 – 121.
- Верещака, А. С. Работоспособность режущего инструмента сизносостойкими покрытиями / А. С. Верещака. – М.: Машиностроение,1993. – 336 с.
- .Табаков, В. П. Работоспособность торцовых фрез с многослойнымиизносостойкими покрытиями / В. П. Табаков, М. Ю. Смирнов, А. В.Циркин. – Ульяновск: УлГТУ, 2005. – 151 с.
- Кабалдин, Ю. Г. Структура, прочность и износостойкость композиционныхинструментальных материалов. – Владивосток: Дальнаука, 1996. – 183 с.
- Верещака, А. С. Основные аспекты применения и совершенствованиярежущих инструментов с износостойкими покрытиями / А. С. Верещака //СТИН. – 2000. – №9. – С. 33 – 40.
- Кабалдин, Ю. Г. Повышение работоспособности режущей частиинструмента из быстрорежущей стали / Ю. Г. Кабалдин // Вестникмашиностроения. – 1996. – №6. – С. 27 – 32.
- Верещака, А. С. Влияние структуры покрытий на работоспособностьтвердосплавных инструментов / А. С. Верещака, Ю. Г. Кабалдин // Вестникмашиностроения. – 1986. – №8. – С. 38 – 42.
- Кабалдин, Ю. Г. Повышение прочности и износостойкости режущегоинструмента термопластическим упрочнением / Ю. Г. Кабалдин. –Хабаровск: Изд-во ДГУ, 1986. – 53 с.
- ГКабалдин, Ю. Г. Механизмы разрушения режущей части инструмента ипути повышения производительности обработки / Ю. Г. Кабалдин //Технологические исследования и разработки при создании САПРтехнологических процессов: сб. научн. трудов. – Владивосток: Изд-во ДГУ,1984. – С. 72 – 82.
- МКабалдин, Ю. Г. Термодинамический анализ разрушенияинструментальных материалов / Ю. Г. Кабалдин, А. А. Бурков // Вопросы248 теории и технологии литейных процессов: сб. научн. трудов. – Хабаровск:ХабПИ, 1985. – С. 36 – 44.
- Кабалдин, Ю. Г. Структурно-энергетический подход к процессуизнашивания режущего инструмента / Ю. Г. Кабалдин // Вестникмашиностроения. – 1990. – №12. – С. 62 – 68.
- Табаков, В. П. Работоспособность режущего инструмента сизносостойкими покрытиями на основе сложных нитридов икарбонитридов титана / В. П. Табаков. – Ульяновск: УлГТУ, 1998. – 123 с.
- Табаков, В. П. Повышение работоспособности торцевых фрез путемсовершенствования структуры износостойких покрытий / В. П. Табаков, Н.А. Ширманов , М. Ю. Смирнов // СТИН. – 2002. – №2. – С. 6 – 10.
- Табаков, В. П. Влияние состава износостойкого покрытия на контактные итепловые процессы и на изнашивание режущего инструмента / В. П.Табаков // СТИН. – 1997. – №10. – С. 20 – 24.
- Табаков, В. П. Применение покрытий на основе карбонитридов титана дляповышения стойкости режущего инструмента / В. П. Табаков // СТИН. – 1991. – №11. – С.18 – 19.
- Внуков, Ю.Н. Нанесение износостойких покрытий на быстрорежущий инструмент. – Киев: Тэхника, 1992. – 143 с.