Реферат за темою випускної роботи
Зміст
- Вступ
- 1. Актуальність теми
- 2. Мета і задачі дослідження та заплановані результати
- 3. Огляд досліджень та розробок
- 4. Аналіз вибору твердосплавного різця з метою підвищення ефективності
- Висновки
- Перелік посилань
Вступ
Деталі складної форми, що мають фасонні поверхні набули широкого поширення, тому технологічні процеси їх виготовлення, які мають деякі особливості, вимагають пильної розгляду та удосконалення з урахуванням сучасних тенденцій. Існуючі традиційні технологічні процеси обробки фасонних поверхонь [1-6] зводяться до застосування одного з двох основних методів: 1) фасонним ріжучим інструментом (різець, протяжка, фреза, зенкер, шліфувальний круг), форма ріжучої кромки якого відповідає формі оброблюваної фасонної поверхні і копіює її; 2) простим ріжучим інструментом (різець, фреза, шліфувальний круг), ріжуче лезо якого знаходиться в точковому або лінійчатому контакті з оброблюваної фасонної поверхнею.
Очевидно, що перший спосіб обробки більш продуктивний, проте менш економічний через необхідність проектування і виготовлення спеціального ріжучого інструменту. До того ж можливість застосування фасонного ріжучого інструменту безпосередньо залежить від розмірів і форми оброблюваної поверхні. По-другому випадку утворення фасонної поверхні забезпечується кінематикою процесу обробки, яка повідомляє інструменту відповідне криволінійний рух щодо оброблюваної заготовки, що забезпечується застосуванням копіювальних систем або верстатів з числовим програмним управлінням (ЧПУ). Збільшення номенклатури виготовляються фасонних деталей, а також складності їх геометричних форм ставило нові завдання формоутворення, що дала змогу вдосконалити комп'ютерних систем верстатів з ЧПУ, забезпечуючи широкі можливості управління процесом механічної обробки [7, 8].
1. Актуальність теми
Створення ефективної моделі процесу обробки криволінійної поверхні є досить складним завданням через складність і змінного характеру процесів, що протікають в зоні обробки. Але незважаючи на такі фактори, акутуальность теми не поміняла свій напрямок у вивченні даного питання.
Механічна обробка фасонних поверхонь досить скрутна і забезпечується складною кінематикою руху ріжучого інструменту щодо оброблюваної заготовки, а також характеризується змінними значеннями технологічних факторів, що визначають умови обробки.
Магістерська робота присвячена актуальній науковій задачі по підвищенню ефективності обробки фасонних поверхонь твердосплавними різцями за рахунок вибору раціонаьних умов процесу різання. Таким чином, встановлення зв’язків і взаємовпливу всіх складових процесу обробки фасонної поверхні доцільно виконувати комплексно з урахуванням мінливих параметрів для управління процесом різання і, як наслідок – отримання заданих параметрів якості обробленої поверхні.
2. Мета і задачі дослідження та заплановані результати
Метою наукової роботи виступає досягнення приросту еффктівності обробки фасонних поверхонь твердосплавними різцями за рахунок вибору раціональних умов процесу різання.
Основні задачі дослідження:
- Аналіз двох основних методів обаботкі фасонних поверхонь.
- Обробка деталей складної форми на верстатах з ЧПУ.
- Аналіз точності обробки фасонних поверхонь в залежності від похибки настроювання інструментів на програмну операцію.
- Пошук і виявлення характеристик фізико-механічних властивостей поверхневого шару (шорсткість, характер і величина залишкових напруг, структурні перетворення).
- Управління режимами різання з метою підвищення продуктивності і зниження собівартості обробки.
- Збільшення періодів стійкості інструменту, а як наслідок, скорочення кількості їх замін і пов’язаних з цим простоїв обладнання.
- Розширення технічних обмежень процесу обробки (наприклад, збільшення максимальної сили різання).
- Забезпечення заданих параметрів якості обробленої поверхні.
Об’єкт дослідження: є процес вивчення і деталізації особливостей обробки фасонних поверхонь.
Предмет дослідження: методологічні, теоретичні та практичні аспекти процесу обробки фасонних поверхонь.
В рамках магістерської роботи планується отримання актуальних наукових результатів по наступним напрямкам:
- Управління процесом обробки фасонної поверхні деталі (зміною її геометричних характеристик зі зняттям припуску).
- Комплексна оцінка можливостей підвищення ефективності обробки з урахуванням змінності умов процесу різання.
- Встановлення залежності відхилень взаємного розташування поверхонь від точності налагодження токарного верстата на операцію програмної обробки
Для експериментальної оцінки отриманих теоретичних результатів і формування фундаменту наступних досліджень, як практичних результатів планується розробка точності взаємного розташування поверхонь, що сполучаються з радіусної утворює, в залежності від значення похибки розмірної настройки різців верстата з ЧПУ, лівого і правого, на операцію програмної обробки:
- Залежність дозволить при заданої похибки сполучення поверхонь з радісних утворюють, отримати числові значення кордонів допустимої помилки розмірної прив’язки інструментів.
- Вибраний два кутових параметра – помилки сполучення і чисельні значення, дозволять розрахувати для конкретної фасонної поверхні похибка розмірної прив’язки і зазор при контролі шаблонами на прилягання.
3. Огляд досліджень та розробок
Оскільки деталі складної форми, що мають фасонні поверхні, вимагають пильної розгляду та удосконалення з урахуванням сучасних тенденцій, розглянемо огляд досліджень і разработок. Современние комп’ютерні системи високопродуктивного обладнання виключають можливість автоматичного призначення режимів різання самою системою. Система враховує поточний стан заготовки, що дозволяє створювати оптимізацію керуючої програми по режимам обробки з метою прискорення процесу, підвищення ефективності використання обладнання і підвищення якості обробки. При цьому траєкторія інструменту ділиться на елементарні ділянки з заданим кроком.
Порівнюючи обсяг матеріалу, що знімається на кожній дільниці, з рекомендованими заданими умовами різання, система призначає оптимальну подачу на кожній дільниці. Хоча система і розраховує оптимальні значення подач автоматично, все-таки початкові параметри для певних умов обробки задає технолог виходячи з власного досвіду або за таблицями режимів різання, які надані постачальником інструменту. [14-15-16-17]
Однак ці порівняння визначення оптимальних режимів різання не враховують змінності параметрів обробки фасонних поверхонь, що вимагає подальшого їх розвитку.
Огляд літературних джерел [7-9-10] показав, що далеко не всі системи автоматичного управління будуються по оптимізаційних алгоритму, а системи проектування керуючих програм для верстатів з ЧПУ не здатні проектувати оптимальну технологію або враховують лише геометричні умови формоутворення поверхні деталі. До того ж сучасні тенденції розвитку програмних продуктів показують, що їх удосконалення відбувається в напрямку оптимізації процесу різання і всьому технологічному обробної системи при проектуванні керуючих програм для верстатів з ЧПУ.
Відомо, що для будь-якого процесу різання, геометричні параметри шару припуску визначають процес в цілому. Ці параметри залежать від форми заготовки, фактичної форми інструментальної поверхні і фактичної траєкторії формотворного руху, яка визначає взаємне розташування інструменту та заготовки при обробці. В результаті геометричного взаємодії з видаленням припуску формується оброблена поверхня, а також її макро і геометрія. Найбільш складні процеси відбуваються при формуванні фізико-механічних властивостей поверхневого шару (шорсткість, характер і величина залишкових напруг, структурні перетворення). При цьому процес обробки фасонної поверхні характеризується постійною зміною параметрів процесу різання, що обумовлює необхідність детального дослідження їх взаємного впливу, встановлення зв’язків і закономірностей їх впливу на процеси в зоні різання.[2-11-20]
Комплексний облік і аналітичне визначення змінних параметрів, покладені в основу дослідження, дозволить найбільш точно змоделювати процеси в зоні різання при обробці фасонної поверхні (мал. 1). Оскільки використання спрощених аналітичних залежностей в даному випадку призведе до зниження вірогідності визначення діючих обмежень при розрахунку оптимальних режимів обробки.
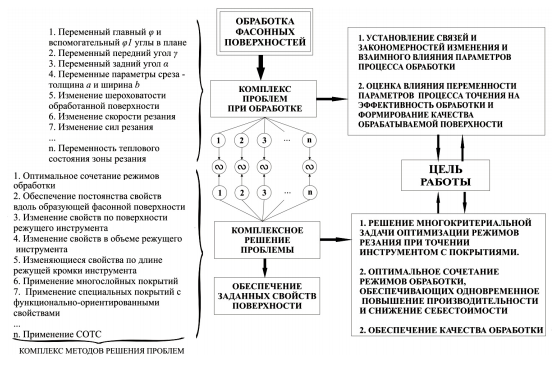
Малюнок 1 – Взаємозв’язок процесів в зоні різання при обробці фасонної поверхні.
Сучасні дослідження, відображені в роботі професора Хейфеца М.Л. [21] показали, що комбіновані способи обробки є найбільш ефективними. В силу тих чи інших причин сфера використання багатьох ефективних процесів істотно обмежується, в таких випадках поєднання їх з іншим способом можна досягти заданого стану поверхневого шару і розширити технологічні можливості.
Деталі складної форми, що мають фасонні поверхні набули широкого поширення, тому технологічні процеси їх виготовлення, які мають деякі особливості, вимагають пильної розгляду та удосконалення з урахуванням сучасних тенденцій. Існуючі традиційні технологічні процеси обробки фасонних поверхонь, розглянуті в роботах Грановського Є.Г., Дальського А.М., Дружинський І.А, Фіраго В.П., Ящеріцина П.І. [5-12] та ін. зводяться до застосування одного з двох основних методів:
- Фасонним ріжучим інструментом (різець, протяжка, фреза, зенкер, шліфувальний круг), форма ріжучої кромки якого відповідає формі оброблюваної фасонної поверхні і копіює її;
- Простим ріжучим інструментом (різець, фреза, шліфувальний круг), ріжуче лезо якого знаходиться в точковому або лінійчатому контакті з оброблюваної фасонної поверхнею.
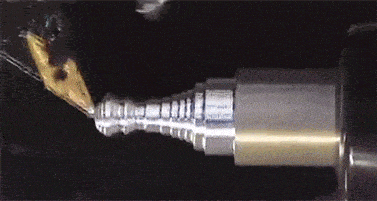
Малюнок 2 – Обробка вала з фасонними поверхнями
(анімація: 16 кадрів, 4 циклів повторення, 215 кілобайт)
Очевидно, що перший спосіб обробки більш продуктивний, проте менш економічний через необхідність проектування і виготовлення спеціального ріжучого інструменту. До того ж можливість застосування фасонного ріжучого інструменту безпосередньо залежить від розмірів і форми оброблюваної поверхні. У другому випадку утворення фасонної поверхні забезпечується кінематикою процесу обробки, яка повідомляє інструменту відповідне криволінійний рух щодо оброблюваної заготовки, що забезпечується застосуванням копіювальних систем або верстатів з числовим програмним управлінням (ЧПУ), що вже вищезгаданий.
Питанням підвищення ефективності обробки фасонних поверхонь різцями присвячена велика кількість наукових праць вчених (серед яких варто відзначити роботи Базрова Б.М., Без’язичного В.Ф., Братана С.М., Бутенко В.І., Вітренко В.А., Гільмана А.М., Гусєва В.В., Гордієнко Б.І., Дальського А.М., Єрмакова Ю.М., Лукичева А.В., Макарова А.Д., Маталін А.А., Михайлова О.М., Рижова Е.В., Старкова В.К., Хандожко А.В. та ін.). Виконані дослідження дозволили встановити, що в даний час практично відсутня інформація щодо обґрунтування вибору раціональних параметрів процесу різання з урахуванням особливостей обробки фасонних поверхонь.
В даний час досить добре розроблені методи оптимізації процесів різання за критеріями максимальної продуктивності або мінімальної собівартості, однак ці методики визначення оптимальних режимів різання не враховують змінності параметрів обробки фасонних поверхонь, що вимагає подальшого їх розвитку.
Питанням технологічного забезпечення експлуатаційних властивостей деталей машин в процесі виготовлення присвячена велика кількість досліджень відомих вчених: Базрова Б.М., Без’язичного В.Ф., Дьяченко П.Е., Маталін А.А., Петрешіна Д.И., Рижова Е.В., Суслова А.Г., Шнейдера Ю.Г. Експлуатаційні властивості деталей і їх з’єднань (зносостійкість, жорсткість і міцність, герметичність з’єднань, міцністю посадок) визначають основний показник якості машин – надійність.
У Донецькому національному технічному університеті (кафедра технології машинобудування) широко розробляються методи підвищення ефективності фасонних поверхонь, розширення матеріальної бази з даного питання, а так само, підвищення експлуатаційних характеристик деталей машин і ріжучого інструменту за рахунок іонно-плазмового зміцнення поверхневого шару, розробка технології нанесення функціонально-орієнтуватися покриттів, розробка прогресивних конструкцій зубчастих муфт, підвищення ефективності роботи роторних ліній і багато інше.
Аналіз літературних джерел показав, що питання забезпечення високої точності обробки деталей в цілому, і фасонних деталей (коли показники якості є змінними вздовж профілю) досить добре вивчені [12-17]. Забезпечення точності в розглянутих роботах досягається шляхом управління процесами проектування і виготовлення формотворного інструменту, розробки технологічних процесів обробки деталей з урахуванням явищ технологічної спадковості і взаємовпливу показників якості поверхні, застосування обладнання з програмним управлінням і стабілізації кінематичних параметрів інструменту.
Однак слід зазначити, що для вирішення завдання забезпечення точності обробки авторами виконані дослідження для циліндричних поверхонь і не враховують особливостей обробки деталей з фасонним профілем. У роботах, присвячених обробці фасонних поверхонь рішення цього завдання визначається призначенням змінних режимних умов обробки з використанням методик, що враховують тільки один або кілька змінних параметрів. Для ефективного управління процесом обробки в цьому випадку доцільно виконувати на основі методик, що враховують весь комплекс змінних параметрів процесу і їх взаємозв’язок.
Під якістю продукції розуміють сукупність властивостей в міру корисності продукції, які відповідають певним громадським і особистим потребам відповідно до її призначення. Поліпшення якості – важлива умова підвищення ефективності виробництва [18-20].
Інформація щодо обґрунтування вибору оптимальних режимів різання з урахуванням характеру обробки фасонних поверхонь в сучасній літературі досить обмежена. Постійні режими обробки при точінні поверхні зі складною криволінійною твірною не можуть забезпечити високу ефективність процесу з наступних причин: зміна кінематичних геометричних параметрів інструменту; зміна параметрів зрізу – ширини і товщини; зміна траєкторії руху інструменту і безперервно змінюється напрямок подачі; змінність теплових процесів в зоні обробки.
Тому, представляє інтерес до роботи з підвищення ефективності обробки таких поверхонь безпосередньо твердосплавними різцями, а так само і іншими інструментами в цілому.
4. Аналіз вибору твердосплавного різця з метою підвищення ефективності
За останні десятиліття обсяг різних типів інструментальних матеріалів для лезвийного інструменту, споживаних металооброблювального виробництвами технологічно розвинених країн, сильно змінився. Практично не використовуються для лезвийного інструменту вуглецеві і леговані інструментальні сталі. Помітно знизилося споживання швидкорізальних сталей з 65 … 70% до 35 … 40%, в той час як, обсяги використання твердих сплавів збільшилися з 30% до 55%, а ріжучої кераміки і надтвердих інструментальних матеріалів з 1% до 10%.
З твердих сплавів найкращі показники як по міцності, так і по зносостійкості мають матеріали, виготовлені методами порошкової металургії, які також дозволяють сформувати заготовку, максимально близьку за формою до остаточної формі ріжучого інструменту.
Істотно збільшується частка використання відносно недорогих керметів (безвольфрамових твердих сплавів), які в ряді випадків не поступаються, а іноді і перевершують за експлуатаційними характеристиками традиційні вольфрамсодержащіе тверді сплави. В Японії частка використання керметів доходить до 40% від обсягу твердосплавного інструменту. Безсумнівно слід очікувати істотного зростання використання керметів і в російській промисловості.
З’явився принципово новий тип ультрадрібнозернистих твердих сплавів з унікальною згинальної міцністю, сумірною з міцністю швидкорізальних сталей. Випуск заготовок таких твердих сплавів у вигляді стрижнів різного діаметра призводить до тенденції виготовлення необхідного кінцевого інструмента безпосередньо на самих підприємствах при використанні багатокоординатних шліфувальних верстатів з ЧПУ.
Твердосплавні пластини для токарних різців є однією з найбільш зручних різновидів ріжучих інструментів. Справа в тому, що різці випускаються як з цільної конструкцією, коли весь інструмент є цілісним і ріже частина нерозривно поєднана з усім іншим, так і зі знімними деталями, що набагато зручніше в процесі роботи, коли можна зняти і замінити одну пластину на іншу. Це ж зручно і при заміні в разі поломки або зносу. Пластини для відрізних різців можуть бути виконані з різних матеріалів і сплавів, так що їх можна мати кілька в наборі для одного типу інструменту, що стане в нагоді для взаємодії з різними типами заготовок.
Купувати змінні пластини для токарних різців виходить набагато дешевше, ніж самі різці. Головним достоїнством цих виробів є те, що вони допомагають збільшувати продуктивність, тому, у виробництві вони будуть незамінними. З урахуванням зростання номенклатури виробів в дрібносерійному і среднесерийном виробництві виникає необхідність в автоматизації багатьох процесів. Твердосплавні пластини мають наступні переваги:
- Низька вартість, в порівнянні з цільними різцями;
- Можливість швидкої зміни;
- Надійно проявляють себе навіть в інтенсивних режимах роботи;
- Можливість переналагодження пластин;
- Управління режимами різання з метою підвищення продуктивності і зниження собівартості обробки;
- Велика уніфікація агрегатів і інструментів.
Твердосплавні пластини для токарних різців класифікуються за такими параметрами:
- Тип, або для яких інструментів вони застосовуються, так як для відрізних, канавкових, підрізних, фасонних, розточувальних та інших різновидів потрібно своя форма ріжучого профілю, яка створюється відповідно до тих особливостей, з якими доведеться зустрічатися в роботі.
- Матеріал, з якого робляться вироби, може мати різний склад. Незважаючи на те, що всі вони відносяться до твердосплавних типу, все одно, співвідношення вольфраму, титану та інших металів може відрізнятися, в залежності від необхідних умов роботи.
- Розміри – в залежності від тих деталей, з якими буде йти робота, пластини можуть мати різні розміри. Коли йде обробка відносно невеликих заготовок з дрібними діаметрами, то великий різець з великою пластиною може просто не пройти в неї. Для цього створюються ідентичні за типом і матеріалом, на різні за розміром, вироби для токарних різців по металу.
- Величина заднього кута – даний параметр позначається в марці вироби. Від нього залежить шорсткість оброблюваної поверхні, чим він вищий, тим більш гладкою стає поверхню. Для м’яких металів використовують пластини з великим заднім кутом.
- Клас точності – існує п’ять класів точності цих виробів, які забезпечують різну ступінь жорсткості в плані допусків за розмірами.
Маркування відображає склад, який входить в вироби. Змінні твердосплавні пластини для різців зустрічаються з маркуванням Т5К10 і Т15К6. На прикладі Т15К6 можна зрозуміти, що вони відносяться до виробів Тітановольфрамовие групи. Зміст карбіду титану в ньому 15%, кобальту – 6%.
Для кожного типу цих типів інструментів є свій ГОСТ, по який потрапляють пластини з певними параметрами:
- ГОСТ 19086-80 – сюди відносяться твердосплавні матеріали для механічних різців ріжучого і опорного типу, а також стружколомом;
- ГОСТ 19042-80 – відноситься до змінних багатогранним виробам;
- ГОСТ 25490-90 – твердосплавні матеріали типів 61, 62, 01, 02. Це можуть бути револьверні, прохідні й розточувальні інструменти.
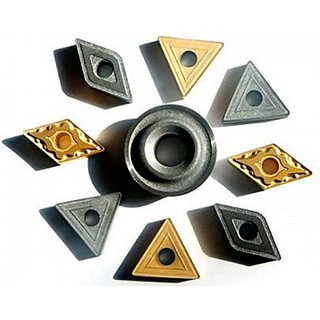
Малюнок 3 – Твердосплавні пластини
З ріжучих керамік найбільш перспективними є кераміки, зміцнені ниткоподібними кристалами нітриду кремнію і сіалони.
З надтвердих матеріалів слід відзначити появу полікристалічних алмазних лезових інструментів нового типу, що виготовляються за технологією хімічного парофазного осадження (CVD-diamond). Найближчим часом слід очікувати появи на ринку інструменту з монокристалічного алмазу, отриманого за аналогічною технологією, що дозволить в кілька разів знизити ціни на монокристалічний лезовий інструмент в порівнянні з інструментом на основі природних алмазів і алмазами, які отримуються за традиційними технологіями синтезу.
В даному аналізі слід зазначити перспективність застосування зносостійких покриттів на лезового інструменту, істотно підвищують стійкість інструменту або продуктивність обробки, проте, створення нових типів покриттів і розширення їх використання є однозначною світовою тенденцією поліпшення ефективності обробки різанням, в тому числі для фасонних поверхонь.
Висновки
Магістерська робота присвячена актуальній науковій задачі створення ефективної моделі процесу обробки криволінійної поверхні. В рамках проведених досліджень виконано:
- Проведено аналіз двох основних методів обаботкі фасонних поверхонь.
- Виконано аналіз сучасного стану питань забезпечення точності і якості обробки деталей з фасонним профілем.
- Проведено аналіз впливу змінності процесу обробки фасонних поверхонь на забезпечення раціональних режимів різання.
- Представлені результати відомих досліджень в області ефективності застосування прогресивного ріжучого інструменту.
- Розширено технічне обмеження процесу обробки.
- Забезпечено завдання параметрів якості обробленої поверхні.
Подальші дослідження спрямовані на наступні аспекти:
- Розробка відповідних аналітичних методик, що дозволяють визначати весь комплекс особливостей обробки фасонної поверхні розрахунковим шляхом без проведення додаткових експериментальних досліджень.
- Управління процесом обробки фасонної поверхні деталі (зміною її геометричних характеристик зі зняттям припуску).
- Комплексна оцінка можливостей підвищення ефективності обробки з урахуванням змінності умов процесу різання.
- Розвиток вирішення завдань оптимізації процесів різання фасонних поверхонь.
- Забезпечення підвищення ефективності обробки фасонних поверхонь за рахунок обґрунтованого поєднання оптимальних режимів обробки, управління процесом різання і застосування твердосплавного інструменту в умовах змінності параметрів процесу різання.
При написанні даного реферату магістерська робота ще не завершена. Остаточне завершення: квітень 2019 року. Повний текст роботи і матеріали по темі можуть бути отримані у автора або його керівника після зазначеної дати.
Перелік посилань
- Дружинский, И.А. Сложные поверхности: Математическое описание и технологическое обеспечение: Справочник. – Л.: Машиностроение,Ленингр. Отделение, 1985. – 263 с
- Способ обработки фасонных поверхностей точением.[Электронный ресурс]. – Режим доступа: Findpatent.ru
- Основы технологии машиностроения / Под ред. А.М. Дальского. – М.: Изд-во МГТУ им. Н.Э. Баумана, 1999. – 426 c.
- Обработка фасонных поверхностей тел вращения. [Электронный ресурс] Режим доступа:Findpatent.ru
- Фираго, В.П. Основы проектирования технологических процессов и приспособлений. Методы обработки поверхностей. - М.: Машиностроение, 1973. - 468 с.
- Якухин, В.Г. Высокотехнологичные методы металлообработки: Учебник / Под ред. д.т.н. проф. О.В. Таратынова. – М.: МГИУ, 2011. – 362 с
- Некрасов, Р.Ю. Формообразование фасонных поверхностей при точении жаропрочных сталей и сплавов на станках с ЧПУ с использованием оперативных коррекций. - Тюмень, 2008. - 16 с.
- Лещенко, А.И. Анализ точности обработки фасонных поверхностей в зависимости от погрешности настройки инструментов на программную операцию. // Вісник Приазовського державного технічного університету. - 2008 р. - Вип. 18. - С 129-133.
- Петраков, Ю.В. Управление процессом обработки сложных поверхностей на станках с ЧПУ // Вестник НТУУ «КПИ». 2000. - № 39 – С. 37 – 44
- Радзевич, С.П. Формообразование поверхностей деталей. Основы теории: Монография. – К.: Растан, 2001. – 592с
- Учет переменности параметров процесса точения фасонных поверхностей при определении оптимальных режимов резания / И.А. Петряева, А.Н. Михайлов, Т.Г. Ивченко // Наукоемкие технологии в машиностроении: ежемесячный научнотехнический и производственный журнал. – М: Машиностроение. - 2014. - №. 9 – С.11-17. (Разработка методики определения оптимальных режимов резания с учетом переменности параметров процесса обработки фасонных поверхностей)
- Грановский, Э.Г. Точность обработки сложноконтурных поверхностей деталей. / Э.Г. Грановский, М.С. Камсюк // Основные направления развития технологии машиностроения: Труды МВТУ. – 1981. – № 348. – С.110 – 127.
- Дружинский, И.А. Сложные поверхности: Математическое описание и технологическое обеспечение: Справочник. – Л.: Машиностроение, Ленингр. Отделение, 1985. – 263 с.
- Лещенко, А.И. Анализ точности обработки фасонных поверхностей в зависимости от погрешности настройки инструментов на программную операцию. // Вісник Приазовського державного технічного університету. - 2008 р. - Вип. 18. - С 129-133.
- Марков, Н.Н. Нормирование точности в машиностроении. - М.: Издательство «Станкин», 1993. – 320 с.
- Нормирование отклонений формы, расположения и шероховатости поверхностей деталей машин: Учебное пособие. / Ю.М. Правиков, Г.Р. Муслина. - Ульяновск: УлГТУ, 2002. - 100с.
- Нормирование точности и технические измерения: учеб. Пособие / В.Л. Соломахо, Б.В. Цитович, С.С. Соколовский. – Минск: Изд-во Гревцова, 2011. – 360 с.
- Михайлов, А.Н. Общий подход к созданию композиционных технологий машиностроения / Наукоемкие технологии в машиностроении, 2012.- №6. - С. 24-29.
- Михайлов, А.Н. Основы синтеза функционально-ориентированных технологий машиностроения / Донецк: ДонНТУ, 2009. – 346 с.
- Управление качеством продукции машиностроения: учебное пособие / М.М. Кане, А.Г. Суслов, О.А. Горленко, Б.В. Иванов, В.Н. Корешков, А.И. Медведев, В.В. Мирошников; под общ. ред. д_ра техн. наук М.М. Кане. - М.: Машиностроение, 2010. - 416 с.
- Стружкообразование и формирование поверхностного слоя изделий при лезвийной обработке / М. Л. Хейфец, Л. Г. Полонский // Процеси механічної обробки в машинобудуванні. - 2015. - Вип. 15. - С. 178-185 .