Реферат по теме выпускной работы
Содержание
- Введение
- 1. Актуальность темы
- 2. Цель и задачи исследования, планируемые результаты
- 3. Обзор исследований и разработок
- 4. Анализ выбора твердосплавного резца с целью повышения эффективности
- Выводы
- Список источников
Введение
Детали сложной формы, имеющие фасонные поверхности получили широкое распространение, поэтому технологические процессы их изготовления, имеющие некоторые особенности, требуют пристального рассмотрения и усовершенствования с учетом современных тенденций. Существующие традиционные технологические процессы обработки фасонных поверхностей [1-6] сводятся к применению одного из двух основных методов: 1) фасонным режущим инструментом (резец, протяжка, фреза, зенкер, шлифовальный круг), форма режущей кромки которого соответствует форме обрабатываемой фасонной поверхности и копирует ее; 2) простым режущим инструментом (резец, фреза, шлифовальный круг), режущее лезвие которого находится в точечном или линейчатом контакте с обрабатываемой фасонной поверхностью.
Очевидно, что первый способ обработки более производителен, однако менее экономичен по причине необходимости проектирования и изготовления специального режущего инструмента. К тому же возможность применения фасонного режущего инструмента непосредственно зависит от размеров и формы обрабатываемой поверхности. Во-втором случае образование фасонной поверхности обеспечивается кинематикой процесса обработки, которая сообщает инструменту соответствующее криволинейное движение относительно обрабатываемой заготовки, что обеспечивается применением копировальных систем или станков с числовым программным управлением (ЧПУ). Увеличение номенклатуры изготавливаемых фасонных деталей, а также сложности их геометрических форм ставило новые задачи формообразования, что привело к усовершенствованию компьютерных систем станков с ЧПУ, обеспечивая широкие возможности управления процессом механообработки [7, 8].
1. Актуальность темы
Создание эфективной модели процесса обработки криволинейной поверхности является довольно сложной задачей ввиду сложности и переменного характера процессов, протекающих в зоне обработки. Но несмотря на такие факторы, акутуальность темы не поменяла своё направление в изучении данного вопроса.
Механическая обработка фасонных поверхностей довольно затруднительна и обеспечивается сложной кинематикой движения режущего инструмента относительно обрабатываемой заготовки, а также характеризуется переменными значениями технологических факторов, определяющих условия обработки.
Магистерская работа посвящена актуальной научной задаче по повышению эффективности обработки фасонных поверхностей твердосплавными резцами за счет выбора рационаьных условий процесса резания. Таким образом, установление связей и взаимного влияния всех составляющих процесса обработки фасонной поверхности целесообразно выполнять комплексно с учетом изменяющихся параметров для управления процессом резания и, как следствие – получения заданных параметров качества обработанной поверхности.
2. Цель и задачи исследования, планируемые результаты
Целью научной работы выступает достижение прироста эффктивности обработки фасонных поверхностей твердосплавными резцами за счет выбора рациональных условий процесса резания.
Основные задачи исследования:
- Анализ двух основных методов обаботки фасонных поверхностей.
- Обработка деталей сложной формы на станках с ЧПУ.
- Анализ точности обработки фасонных поверхностей в зависимости от погрешности настройки инструментов на программную операцию.
- Поиск и выявление характеристик физико-механических свойств поверхностного слоя (шероховатость, характер и величина остаточных напряжений, структурные преобразования).
- Управление режимами резания с целью повышения производительности и снижения себестоимости обработки.
- Увеличение периодов стойкости инструмента, а как следствие, сокращение количества их замен и связанных с этим простоев оборудования.
- Расширение технических ограничений процесса обработки (например, увеличение максимальной силы резания).
- Обеспечение заданных параметров качества обработанной поверхности.
Объект исследования: является процесс изучения и детализации особенностей обработки фасонных поверхностей.
Предмет исследования: методологические, теоретические и практические аспекты процесса обработки фасонных поверхностей.
В рамках магистерской работы планируется получение актуальных научных результатов по следующим направлениям:
- Управление процессом обработки фасонной поверхности детали (изменением ее геометрических характеристик со снятием припуска).
- Комплексная оценка возможностей повышения эффективности обработки с учетом переменности условий процесса резания.
- Установление зависимости отклонений взаимного расположения поверхностей от точности наладки токарного станка на операцию программной обработки
Для экспериментальной оценки полученных теоретических результатов и формирования фундамента последующих исследований, в качестве практических результатов планируется разработка точности взаимного расположения сопрягаемых поверхностей с радиусной образующей, в зависимости от значения погрешности размерной настройки резцов станка с ЧПУ, левого и правого, на операцию программной обработки :
- Зависимость позволит при заданной погрешности сопряжения поверхностей с радиусными образующими, получить числовые значения границ допустимой ошибки размерной привязки инструментов.
- Выбраные два угловых параметра – ошибки сопряжения и численные значения, позволят рассчитать для конкретной фасонной поверхности погрешность размерной привязки и зазор при контроле шаблонами на прилегание.
3. Обзор исследований и разработок
Поскольку детали сложной формы, имеющие фасонные поверхности, требуют пристального рассмотрения и усовершенствования с учетом современных тенденций, рассмотрим обзор исследований и разработок. Современные компьютерные системы высокопроизводительного оборудования исключают возможность автоматического назначения режимов резания самой системой. Система учитывает текущее состояние заготовки, что позволяет создавать оптимизацию управляющей программы по режимам обработки в целях ускорения процесса, повышения эффективности использования оборудования и повышения качества обработки. При этом траектория инструмента делится на элементарные участки с заданным шагом.
Сравнивая объем снимаемого материала на каждом участке, с рекомендованными заданными условиями резания, система назначает оптимальную подачу на каждом участке. Хотя система и рассчитывает оптимальные значения подач автоматически, все-таки начальные параметры для определенных условий обработки задает технолог исходя из собственного опыта или по таблицам режимов резания, которые предоставлены поставщиком инструмента.[14-15-16-17]
Однако эти сравнения определения оптимальных режимов резания не учитывают переменности параметров обработки фасонных поверхностей, что требует дальнейшего их развития.
Обзор литературных источников [7-9-10] показал, что далеко не все системы автоматического управления строятся по оптимизационному алгоритму, а системы проектирования управляющих программ для станков с ЧПУ не способны проектировать оптимальную технологию или учитывают только геометрические условия формообразования поверхности детали. К тому же современные тенденции развития программных продуктов показывают, что их усовершенствование происходит в направлении оптимизации процесса резания и всей технологической обрабатывающей системы при проектировании управляющих программ для станков с ЧПУ.
Известно, что для любого процесса резания, геометрические параметры слоя припуска определяют процесс в целом. Эти параметры зависят от формы заготовки, фактической формы инструментальной поверхности и фактической траектории формообразующего движения, которая определяет взаимное расположение инструмента и заготовки при обработке. В результате геометрического взаимодействия с удалением припуска формируется обработанная поверхность, а также ее макро и микрогеометрия. Наиболее сложные процессы происходят при формировании физико-механических свойств поверхностного слоя (шероховатость, характер и величина остаточных напряжений, структурные преобразования). При этом процесс обработки фасонной поверхности характеризуется постоянным изменением параметров процесса резания, что обуславливает необходимость детального исследования их взаимного влияния, установления связей и закономерностей их влияния на процессы в зоне резания. [2-11-20]
Комплексный учет и аналитическое определение переменных параметров, положенные в основу исследования, позволит наиболее точно смоделировать процессы в зоне резания при обработке фасонной поверхности (рис. 1). Поскольку использование упрощенных аналитических зависимостей в данном случае приведет к снижению достоверности определения действующих ограничений при расчете оптимальных режимов обработки.
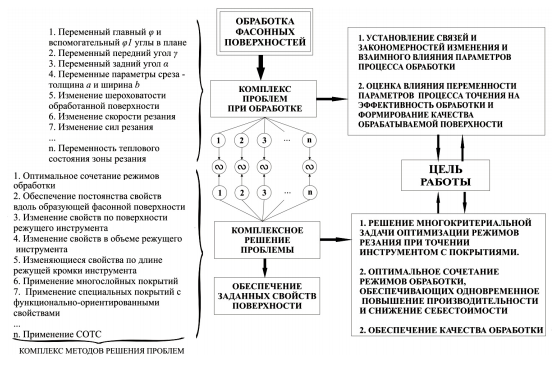
Рисунок 1 – Взаимосвязь процессов в зоне резания при обработке фасонной поверхности.
Современные исследования, отраженные в работе профессора Хейфеца М.Л. [21] показали, что комбинированные способы обработки являются наиболее эффективными. В силу тех или иных причин сфера использования многих эффективных процессов существенно ограничивается, в таких случаях сочетание их с другим способом можно достигнуть заданного состояния поверхностного слоя и расширить технологические возможности.
Детали сложной формы, имеющие фасонные поверхности получили широкое распространение, поэтому технологические процессы их изготовления, имеющие некоторые особенности, требуют пристального рассмотрения и усовершенствования с учетом современных тенденций. Существующие традиционные технологические процессы обработки фасонных поверхностей, рассмотренные в работах Грановского Э.Г., Дальского А.М., Дружинского И.А, Фираго В.П., Ящерицына П.И. [5-12] и др. сводятся к применению одного из двух основных методов:
- Фасонным режущим инструментом (резец, протяжка, фреза, зенкер, шлифовальный круг), форма режущей кромки которого соответствует форме обрабатываемой фасонной поверхности и копирует ее;
- Простым режущим инструментом (резец, фреза, шлифовальный круг), режущее лезвие которого находится в точечном или линейчатом контакте с обрабатываемой фасонной поверхностью.
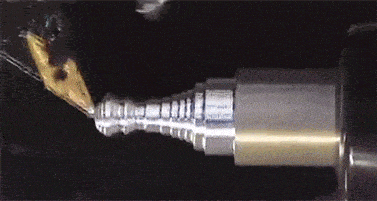
Рисунок 2 – Обработка вала с фасонными поверхностями
(анимация: 16 кадров, 4 циклов повторения, 215 килобайт)
Очевидно, что первый способ обработки более производителен, однако менее экономичен по причине необходимости проектирования и изготовления специального режущего инструмента. К тому же возможность применения фасонного режущего инструмента непосредственно зависит от размеров и формы обрабатываемой поверхности. Во втором случае образование фасонной поверхности обеспечивается кинематикой процесса обработки, которая сообщает инструменту соответствующее криволинейное движение относительно обрабатываемой заготовки, что обеспечивается применением копировальных систем или станков с числовым программным управлением (ЧПУ), что уже вышеупомянуто.
Вопросам повышения эффективности обработки фасонных поверхностей резцами посвящено большое количество научных трудов ученых (среди которых стоит отметить работы Базрова Б.М., Безъязычного В.Ф., Братана С.М., Бутенко В.И., Витренко В.А., Гильмана А.М., Гусева В.В., Гордиенко Б.И., Дальского А.М., Ермакова Ю.М., Лукичева А.В., Макарова А.Д., Маталина А.А., Михайлова А.Н., Рыжова Э.В., Старкова В.К., Хандожко А.В. и др.). Выполненные исследования позволили установить, что в настоящее время практически отсутствует информация по обоснованию выбора рациональных параметров процесса резания с учетом особенностей обработки фасонных поверхностей.
В настоящее время достаточно хорошо разработаны методы оптимизации процессов резания по критериям максимальной производительности или минимальной себестоимости, однако эти методики определения оптимальных режимов резания не учитывают переменности параметров обработки фасонных поверхностей, что требует дальнейшего их развития.
Вопросам технологического обеспечения эксплуатационных свойств деталей машин в процессе изготовления посвящено большое количество исследований известных ученых: Базрова Б.М., Безъязычного В.Ф., Дьяченко П.Е., Маталина А.А., Петрешина Д.И., Рыжова Э.В., Суслова А.Г., Шнейдера Ю.Г. Эксплуатационные свойства деталей и их соединений (износостойкость, жесткость и прочность, герметичность соединений, прочностью посадок) определяют основной показатель качества машин – надежность.
В Донецком национальном техническом университете (кафедра технологии машиностроения) широко разрабатываются методы повышения эффективности фасонных поверхностей, расширения материальной базы по данному вопросу, а так же, повышение эксплуатационных характеристик деталей машин и режущего инструмента за счёт ионно-плазменного упрочнения поверхностного слоя, разработка технологии нанесения функционально-ориентированных покрытий, разработка прогрессивных конструкций зубчатых муфт, повышение эффективности работы роторных линий и многое другое.
Обзор литературных источников показал, что в настоящее время основное внимание при обработке фасонных поверхностей уделяется вопросам управления процессом обработки с целью обеспечения точности.
Анализ литературных источников показал, что вопросы обеспечения высокой точности обработки деталей в целом, и фасонных деталей (когда показатели качества являются переменными вдоль профиля) достаточно хорошо изучены [12-17]. Обеспечение точности в рассмотренных работах достигается путем управления процессами проектирования и изготовления формообразующего инструмента, разработки технологических процессов обработки деталей с учетом явлений технологической наследственности и взаимного влияния показателей качества поверхности, применения оборудования с программным управлением и стабилизации кинематических параметров инструмента.
Однако следует отметить, что для решения задачи обеспечения точности обработки авторами выполнены исследования для цилиндрических поверхностей и не учитывают особенностей обработки деталей с фасонным профилем. В работах, посвященных обработке фасонных поверхностей решение этой задачи определяется назначением переменных режимных условий обработки с использованием методик, учитывающих только один или несколько переменных параметров. Для эффективного управления процессом обработки в этом случае целесообразно выполнять на основе методик, учитывающих весь комплекс переменных параметров процесса и их взаимосвязь.
Под качеством продукции понимают совокупность свойств в мере полезности продукции, удовлетворяющих определенным общественным и личным потребностям в соответствии с её назначением. Улучшение качества – важное условие повышения эффективности производства [18-20].
Информация по обоснованию выбора оптимальных режимов резания с учетом характера обработки фасонных поверхностей в современной литературе достаточно ограничена. Постоянные режимы обработки при точении поверхности со сложной криволинейной образующей не могут обеспечить высокую эффективность процесса по следующим причинам: изменение кинематических геометрических параметров инструмента; изменение параметров среза – ширины и толщины; изменение траектории движения инструмента и непрерывно изменяющееся направление подачи; переменность тепловых процессов в зоне обработки.
Поэтому, представляет интерес к работе по повышению эффективности обработки таких поверхностей непосредственно твёрдосплавными резцами, а так же и другими инструментами в целом.
4. Анализ выбора твердосплавного резца с целью повышения эффективности
За последние десятилетия объем различных типов инструментальных материалов для лезвийного инструмента, потребляемых металообрабатывающими производствами технологически развитых стран, сильно изменился. Практически не используются для лезвийного инструмента углеродистые и легированные инструментальные стали. Заметно снизилось потребление быстрорежущих сталей с 65…70% до 35…40%, в то время как, объёмы использования твёрдых сплавов увеличились с 30% до 55%, а режущей керамики и сверхтвёрдых инструментальных материалов с 1% до 10%.
Из твёрдых сплавов наилучшие показатели как по прочности, так и по износостойкости имеют материалы, изготовленные методами порошковой металлургии, которые также позволяют сформировать заготовку, максимально близкую по форме к окончательной форме режущего инструмента.
Существенно увеличивается доля использования относительно недорогих керметов (безвольфрамовых твердых сплавов), которые в ряде случаев не уступают, а иногда и превосходят по эксплуатационным характеристикам традиционные вольфрамсодержащие твердые сплавы. В Японии доля использования керметов доходит до 40% от объема твердосплавного инструмента. Несомненно следует ожидать существенного роста использования керметов и в российской промышленности.
Появился принципиально новый тип ультрамелкозернистых твердых сплавов с уникальной изгибной прочностью, соизмеримой с прочностью быстрорежущих сталей. Выпуск заготовок таких твердых сплавов в виде стержней различного диаметра приводит к тенденции изготовления необходимого концевого инструмента непосредственно на самих предприятиях при использовании многокоординатных шлифовальных станков с ЧПУ.
Твердосплавные пластины для токарных резцов являются одной из самых удобных разновидностей режущих инструментов. Дело в том, что резцы выпускаются как с цельной конструкцией, когда весь инструмент является цельным и режущая часть неразрывно соединена со всем остальным, так и со съемными деталями, что намного более удобно в процессе работы, когда можно снять и заменить одну пластину на другую. Это же удобно и при замене в случае поломки или износа. Пластины для отрезных резцов могут быть выполнены из различных материалов и сплавов, так что их можно иметь несколько в наборе для одного типа инструмента, что пригодится для взаимодействия с различными типами заготовок.
Покупать сменные пластины для токарных резцов выходит намного дешевле, чем сами резцы. Главным достоинством этих изделий является то, что они помогают увеличивать производительность, поэтому, в производстве они будут являться незаменимыми. С учетом роста номенклатуры изделий в мелкосерийном и среднесерийном производстве возникает необходимость в автоматизации многих процессов. Твердосплавные пластины обладают следующими преимуществами:
- Низкая стоимость, в сравнении с цельными резцами;
- Возможность быстрой смены;
- Надежно проявляют себя даже в интенсивных режимах работы;
- Возможность переналадки пластин;
- Управление режимами резания с целью повышения производительности и снижения себестоимости обработки;
- Большая унификация агрегатов и инструментов.
Твердосплавные пластины для токарных резцов классифицируются по следующим параметрам:
- Тип, или для каких инструментов они применяются, так как для отрезных, канавочных, подрезных, фасонных, расточных и прочих разновидностей требуется своя форма режущего профиля, которая создается согласно тем особенностям, с которыми придется встречаться в работе.
- Материал, из которого делаются изделия, может иметь различный состав. Несмотря на то, что все они относятся к твердосплавному типу, все равно, соотношение вольфрама, титана и других металлов может отличаться, в зависимости от требуемых условий работы.
- Размеры – в зависимости от тех деталей, с которыми будет идти работа, пластины могут иметь различные размеры. Когда идет обработка относительно небольших заготовок с мелкими диаметрами, то крупный резец с большой пластиной может попросту не пройти в нее. Для этого создаются идентичные по типу и материалу, на различные по размеру, изделия для токарных резцов по металлу.
- Величина заднего угла – данный параметр обозначается в марке изделия. От него зависит шероховатость обрабатываемой поверхности, чем он выше, тем более гладкой становится поверхность. Для мягких металлов используют пластины с большим задним углом.
- Класс точности – существует пять классов точности этих изделий, которые обеспечивают различную степень жесткости в плане допусков по размерам.
Маркировка отображает состав, который входит в изделия. Сменные твердосплавные пластины для резцов встречаются с маркировкой Т5К10 и Т15К6. На примере Т15К6 можно понять, что они относятся к изделиям титановольфрамовой группы. Содержание карбида титана в нем 15%, кобальта – 6%.
Для каждого типа этих типов инструментов имеется свой ГОСТ, по который попадают пластины с определенными параметрами:
- ГОСТ 19086-80 – сюда относятся твердосплавные материалы для механических резцов режущего и опорного типа, а также стружколомы;
- ГОСТ 19042-80 – относится к сменным многогранным изделиям;
- ГОСТ 25490-90 – твердосплавные материалы типов 61, 62, 01, 02. Это могут быть револьверные, проходные и расточные инструменты.
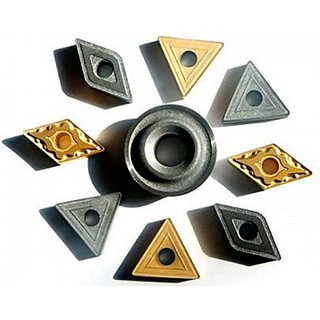
Рисунок 3 – Твёрдосплавные пластины
Из режущих керамик наиболее перспективными являются керамики, упрочненные нитевидными кристаллами нитрида кремния и сиалоны.
Из сверхтвердых материалов следует отметить появление поликристаллических алмазных лезвийных инструментов нового типа, изготавливаемых по технологии химического парофазного осаждения (CVD-diamond). В ближайшее время следует ожидать появления на рынке инструмента из монокристаллического алмаза, полученного по аналогичной технологии, что позволит в несколько раз снизить цены на монокристаллический лезвийный инструмент по сравнению с инструментом на основе природных алмазов и алмазами, получаемыми по традиционным технологиям синтеза.
В данном анализе следует отметить перспективность применения износостойких покрытий на лезвийном инструменте, существенно повышающих стойкость инструмента или производительность обработки, однако, создание новых типов покрытий и расширение их использования является однозначной мировой тенденцией улучшения эффективности обработки резанием, в том числе для фасонных поверхностей.
Выводы
Магистерская работа посвящена актуальной научной задаче создание эфективной модели процесса обработки криволинейной поверхности. В рамках проведенных исследований выполнено:
- Проведен анализ двух основных методов обаботки фасонных поверхностей.
- Выполнен анализ современного состояния вопросов обеспечения точности и качества обработки деталей с фасонным профилем.
- Проведен анализ влияния переменности процесса обработки фасонных поверхностей на обеспечение рациональных режимов резания.
- Представлены результаты известных исследований в области эффективности применения прогрессивного режущего инструмента.
- Расширено техническое ограничение процесса обработки.
- Обеспечена задание параметров качества обработанной поверхности.
Дальнейшие исследования направлены на следующие аспекты:
- Разработка соответствующих аналитических методик, позволяющих определять весь комплекс особенностей обработки фасонной поверхности расчетным путем без проведения дополнительных экспериментальных исследований.
- Управление процессом обработки фасонной поверхности детали (изменением ее геометрических характеристик со снятием припуска).
- Комплексная оценка возможностей повышения эффективности обработки с учетом переменности условий процесса резания.
- Развитие решения задач оптимизации процессов резания фасонных поверхностей.
- Обеспечение повышения эффективности обработки фасонных поверхностей за счет обоснованного сочетания оптимальных режимов обработки, управления процессом резания и применения твердосплавного инструмента в условиях переменности параметров процесса резания.
При написании данного реферата магистерская работа еще не завершена. Окончательное завершение: апрель 2019 года. Полный текст работы и материалы по теме могут быть получены у автора или его руководителя после указанной даты.
Список источников
- Дружинский, И.А. Сложные поверхности: Математическое описание и технологическое обеспечение: Справочник. – Л.: Машиностроение,Ленингр. Отделение, 1985. – 263 с
- Способ обработки фасонных поверхностей точением.[Электронный ресурс]. – Режим доступа: Findpatent.ru
- Основы технологии машиностроения / Под ред. А.М. Дальского. – М.: Изд-во МГТУ им. Н.Э. Баумана, 1999. – 426 c.
- Обработка фасонных поверхностей тел вращения. [Электронный ресурс] Режим доступа:Findpatent.ru
- Фираго, В.П. Основы проектирования технологических процессов и приспособлений. Методы обработки поверхностей. - М.: Машиностроение, 1973. - 468 с.
- Якухин, В.Г. Высокотехнологичные методы металлообработки: Учебник / Под ред. д.т.н. проф. О.В. Таратынова. – М.: МГИУ, 2011. – 362 с
- Некрасов, Р.Ю. Формообразование фасонных поверхностей при точении жаропрочных сталей и сплавов на станках с ЧПУ с использованием оперативных коррекций. - Тюмень, 2008. - 16 с.
- Лещенко, А.И. Анализ точности обработки фасонных поверхностей в зависимости от погрешности настройки инструментов на программную операцию. // Вісник Приазовського державного технічного університету. - 2008 р. - Вип. 18. - С 129-133.
- Петраков, Ю.В. Управление процессом обработки сложных поверхностей на станках с ЧПУ // Вестник НТУУ «КПИ». 2000. - № 39 – С. 37 – 44
- Радзевич, С.П. Формообразование поверхностей деталей. Основы теории: Монография. – К.: Растан, 2001. – 592с
- Учет переменности параметров процесса точения фасонных поверхностей при определении оптимальных режимов резания / И.А. Петряева, А.Н. Михайлов, Т.Г. Ивченко // Наукоемкие технологии в машиностроении: ежемесячный научнотехнический и производственный журнал. – М: Машиностроение. - 2014. - №. 9 – С.11-17. (Разработка методики определения оптимальных режимов резания с учетом переменности параметров процесса обработки фасонных поверхностей)
- Грановский, Э.Г. Точность обработки сложноконтурных поверхностей деталей. / Э.Г. Грановский, М.С. Камсюк // Основные направления развития технологии машиностроения: Труды МВТУ. – 1981. – № 348. – С.110 – 127.
- Дружинский, И.А. Сложные поверхности: Математическое описание и технологическое обеспечение: Справочник. – Л.: Машиностроение, Ленингр. Отделение, 1985. – 263 с.
- Лещенко, А.И. Анализ точности обработки фасонных поверхностей в зависимости от погрешности настройки инструментов на программную операцию. // Вісник Приазовського державного технічного університету. - 2008 р. - Вип. 18. - С 129-133.
- Марков, Н.Н. Нормирование точности в машиностроении. - М.: Издательство «Станкин», 1993. – 320 с.
- Нормирование отклонений формы, расположения и шероховатости поверхностей деталей машин: Учебное пособие. / Ю.М. Правиков, Г.Р. Муслина. - Ульяновск: УлГТУ, 2002. - 100с.
- Нормирование точности и технические измерения: учеб. Пособие / В.Л. Соломахо, Б.В. Цитович, С.С. Соколовский. – Минск: Изд-во Гревцова, 2011. – 360 с.
- Михайлов, А.Н. Общий подход к созданию композиционных технологий машиностроения / Наукоемкие технологии в машиностроении, 2012.- №6. - С. 24-29.
- Михайлов, А.Н. Основы синтеза функционально-ориентированных технологий машиностроения / Донецк: ДонНТУ, 2009. – 346 с.
- Управление качеством продукции машиностроения: учебное пособие / М.М. Кане, А.Г. Суслов, О.А. Горленко, Б.В. Иванов, В.Н. Корешков, А.И. Медведев, В.В. Мирошников; под общ. ред. д_ра техн. наук М.М. Кане. - М.: Машиностроение, 2010. - 416 с.
- Стружкообразование и формирование поверхностного слоя изделий при лезвийной обработке / М. Л. Хейфец, Л. Г. Полонский // Процеси механічної обробки в машинобудуванні. - 2015. - Вип. 15. - С. 178-185 .