Реферат по теме выпускной работы
Содержание
- Введение
- Теоретическая модель траектории движения инструмент
- Этапы повышения эффективности процесса фрезерования
- Выводы
- Список источников
Введение
На сегодняшний момент фрезерование является одним из наиболее часто используемых методов получения поверхности резанием, так как позволяет получить деталь практически любой сложности. Основным достоинствами этого метода обработки являются высокая производительность, точность и качество обработанных поверхностей.
Фрезерование характеризуется сложной кинематикой и динамикой резания, связанных с переменностью срезаемого слоя и ударностью процесса резания. Вопрос о повышении качества обработанной поверхности фрезерной обработки в непростых современных экономических условиях стоит особенно остро.
Постоянное повышение требований к точности и качеству обработанной поверхности, а также к ресурсу изготовленной детали приводят к необходимости проведения исследований по всем параметрам качества поверхности и разработки на их основе новых технологических рекомендаций, позволяющей получать оптимальный комплекс свойств обработанной поверхности на данном этапе изготовления детали.
Теоретическая модель траектории движения инструмента
Существуют четыре принципа генерации траектории движения режущего инструмента, которым подчинены все подходы к созданию УП для высокоскоростной обработки [1]:
- Предпочтительны длинные траектории инструмента для резания с небольшой глубиной в осевом и радиальном направлениях.
- Резание образующей вместо торцового фрезерования. Окружная скорость прямо пропорциональна радиусу инструмента, и даже при высокой скорости вращения шпинделя она равна нулю в центре инструмента (на оси). Силы резания при высокоскоростной обработке существенно уменьшаются в направлении осей X и Y, а в направлении оси Z практически не изменяются. К тому же при торцовом фрезеровании удаление стружки затруднено, что негативно сказывается на процессе резания.
- Плавное изменение условий резания: условия отвода стружки, усилия резания в осевом и радиальном направлениях и так далее. Для инструмента из твердого сплава более благоприятна постоянная (пусть даже и высокая) температура в зоне резания, чем ее колебания.
Резкое изменение условий резания при врезании инструмента в материал приводит к увеличению количества выделяемой теплоты и механических напряжений, что отрицательно сказывается на стойкости инструмента. Если траектория инструмента рассчитана при условии плавного изменения условий резания, то это позволит значительно увеличить стойкость инструмента, получить лучшую точность и шероховатость обработанной поверхности.
- Плавные траектории инструмента. Применение функции предварительного анализа траектории с соответствующим регулированием рабочей подачи позволяет предотвратить резкие врезания в материал, так как рабочая подача будет соответствовать запрограммированному значению только на плавных (особенно на прямолинейных) участках траектории, а перед резкой сменой направления движения инструмента рабочая подача будет постепенно уменьшаться до некоторого значения. При плавном изменении нагрузки на инструмент на механические узлы станка будут действовать наименьшие силы. Практика показывает, что деталь невозможно изготовить без использования траектории, предполагающей резкую смену направления движения инструмента (рис. 1а), но такие случаи необходимо минимизировать.
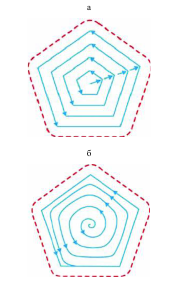
Рисунок 1. Схемы траекторий движения инструмента:
а– с резким изменением направления;
б – плавное движение
Плавная траектория (рис. 1б) более подходит для высокоскоростной обработки. Трохоидальная обработка – фреза движется по окружности (рис. 2).
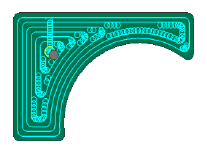
Рисунок 2. Схема трохоидальной траектории движения инструмента
Сила резания в направлении оси Z не уменьшается при увеличении скорости вращения шпинделя. Врезание в твердый материал с высокой рабочей подачей создаст напряжение в инструментальном патроне и шпинделе и приведет к повреждению инструмента. Необходимо избегать вертикального врезания инструмента (за исключением графита, алюминия и некоторых других мягких материалов). Перемещение режущего инструмента на величину прохода по оси Z рекомендуется производить в воздухе, а врезание в горизонтальном направлении – по дугообразной траектории. Желательно и выход инструмента осуществлять по дуге. Чем тверже материал, тем меньше должно быть значение угла врезания. Например, при обработке стали твердостью 62–65 HRC рекомендуется задавать угол врезания не более 0,5 градуса.
Резание параллельными слоями (фреза движется последовательно слоями по горизонтальным плоскостям) – наиболее распространенный метод формирования траектории для предварительной обработки (рис. 3). Преимущество этого подхода заключается в простоте программирования при сохранении глубины фрезерования. При обработке параллельными слоями генерируются проходы для окончательной обработки боковых стенок карманов или островов. Однако для обработки плоских поверхностей (низ кармана или верх острова) такая техника не совсем подходит, и тут лучше применять другие методы. Некоторые CAM-системы позволяют программировать траектории для обработки комбинированных поверхностей [2].

Рисунок 3. Модель обработки сложнопрофильной поверхности параллельными слоями
Одна из проблем обработки параллельными слоями – изменение шага по оси Z. Только часть САМ-систем автоматически определяют различные значения приращения по оси Z в зависимости от угла наклона стенок, большинство же – не может. Технолог-программист вынужден вручную разделять поверхность на области и указывать различные значения шага по оси Z, чтобы получить оптимальную шероховатость поверхности наклонных и вертикальных стенок.
Этапы повышения эффективности процесса фрезерования
Фрезерование боковыми лезвиями концевых фрез широко распространено в общем машиностроении и авиастроении. Приведем пример детали, изготавливаемой на ПАО «Роствертол» (рис. 4). Это вилка, с помощью которой крепится лонжерон к несущему винту вертолета. К внутренней поверхности вилки предъявляются высокие требования к качеству поверхности, так как параметры точности и качества поверхности влияют на долговечность узла крепления, и, следовательно, на ресурс вертолета. Данные по усталостным испытаниям узла крепления лонжерона с несущей системой вертолета с помощью вилки, выполненные в условиях ПАО «Роствертол» показывают, что снижение высоты волн с 12 до 6 мкм позволяет в 2 и более раза повысить усталостную долговечность. Это определяет требования к качеству поверхности аналогичных изделий. На усталостную долговечность оказывает влияние и шероховатость.
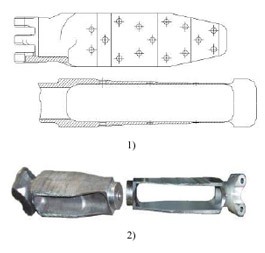
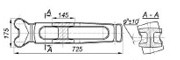
Рисунок 4. Пример детали:
1 – эскиз;
2 – фото заготовки;
3 – операционные эскизы обработки наконечника лопасти несущего винта(анимация 4 кадров, 3 повторения,25,3 кб)
Выполненные исследования позволили сформулировать эффективный алгоритм выбора и настройки процесса контурного фрезерования концевыми фрезами при обработке деталей, ширина обрабатываемой поверхности которых превышает диаметр фрезы. Этот случай относится к обработке большой номенклатуры деталей на предприятиях авиационной промышленности. Пример эскиза такой детали приведен на рис. 5, эскиз технологической наладки. Значения жесткости даны по средней линии детали. На рис. 5 представлены только диагональные элементы матрицы. Обеспечение качества деталей, имеющих тонкие и маложесткие стенки, есть многофакторная проблема. Ее решение включает несколько этапов [3, 4].
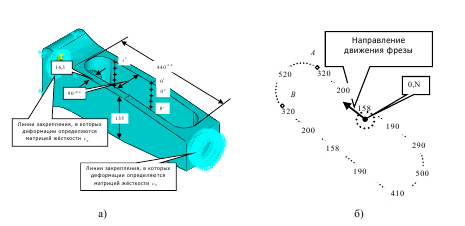
Рисунок 5. Эскиз заготовки при обработке внутренней поверхности (а) и пример распределения коэффициента жёсткости (кг/мм) в направлении, нормальном к образующей (б)(наконечник лопасти 8АТ-270-25)
Первый этап – выбор стратегии обработки. Здесь возможны два варианта. Первый вариант связан с последовательными проходами для обработки верхней части заготовки, затем последующей части, как показано на рис. 5. Это области 1, 2 и 3.
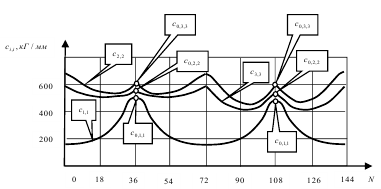
Рисунок 6. Изменения диагональных элементов матрицы жёсткости заготовки, материал 40ХН2МА
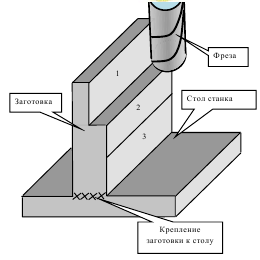
Рисунок 7. Схема первой стратегии обработки тонкостенной заготовки
В данном случае нижняя часть за счет повышенной жесткости заготовки уменьшает жесткость обрабатываемой части детали. Однако на линии сопряжения последовательных проходов (границы областей 1, 2, 3) всегда образуется неровность, которая приводит к погрешности формы. Кроме этого эффективность применения такой стратегии существенно снижается. Второй вариант связан с обработкой сразу всей поверхности. Он более производителен, но приводит к вышеуказанным погрешностям. По этой причине необходимо оставлять припуск для дополнительных чистовых проходов. Рассмотрим вторую стратегию, как более производительную, но сложную в анализе и синтезе [5].
Второй этап – выбор станка. Для фрезерования поверхности, ширина которой больше диаметра фрезы, желательно выбрать станок с пятикоординатным контурным управлением. Это обусловлено необходимостью компенсации погрешности изгибных деформаций фрезы. Кроме этого, для компенсации зависимости жесткости детали вдоль траектории движения по образующей формируемой поверхности необходимо обеспечивать неизменное отношение силы к суммарной приведенной жесткости в направлении, нормальном к образующей. Для этого, как возможная стратегия обработки, рассматривается программное управление скоростью движения стола по направлению формируемой образующей.
Третий этап – диагностирование кинематических возмущений станка в единстве оценивания амплитуды радиальных биений шпинделя и вариаций скоростей подачи движения стола. Для оценивания кинематических возмущений можно воспользоваться методикой, изложенной в работах [1, 2]. Она основана на обработке информации от датчиков обратной связи по положению стола, которыми снабжены практически все станки с ЧПУ с контурным управлением. Характеристики кинематических возмущений, представленные, например, автокорреляционными функциями, характеризуют предельно достижимую точность обработки на конкретном станке.
Четвертый этап – выбор инструмента. При выборе инструмента необходимо принимать во внимание следующие особенности.
- Число зубьев (шаг между зубьями фрезы), с учетом угла наклона режущих лезвий, должно обеспечивать непрерывность процесса без перекрытия контактов. Диаметр фрезы выбирается на основе компромисса между желанием его увеличить для обеспечения повышенной жесткости и необходимостью формирования поверхности на участках ее искривления (на участке
А-В
на рис. 2 б). - Необходимо обеспечить геометрическую точность режущих лезвий фрезы. В описываемом случае точность радиуса режущих лезвий должна быть в два-три раза выше требуемой точности поверхности. Необходимо учитывать, что при фрезеровании, в отличие от точения, формируемая поверхность непосредственно определяется всей геометрией каждого зуба по оси вращения инструмента.
- При заточке зубьев фрезы необходимо выбирать, по возможности, передний угол режущего клина не менее 12°-15°. В этом случае при движении инструмента ориентация силы имеет проекцию, практически совпадающую с направлением движения фрезы. Тогда на участках формообразования будет минимальное отклонение инструмента от идеальной траектории.
- Угол наклона зубьев фрезы необходимо выбирать таким, чтобы осевая составляющая силы, как отмечено ранее, имела направление в сторону стола, на котором закреплена обрабатываемая заготовка. В описанном случае – это фреза с правой ориентацией наклона зубьев.
- Рекомендуемые значения геометрических параметров фрезы при обработке материала.
Пятый этап – выбор технологических режимов и управления.
При обработке детали, у которой параметры жесткости остаются неизменными, величина подачи на зуб при обработке стали 40ХН2МА зависит от требований к качеству формируемой поверхности. Выше показано, что показатель шероховатости поверхности учитывает кинематическую характеристику, возрастающую при увеличении подачи; траекторию, зависящую от формируемых притягивающих множеств и самостоятельные процессы в зоне резания. По мере развития износа инструмента соотношение между ними изменяется. На начальном этапе основной вклад имеет кинематическая составляющая. Затем существенно возрастает влияние самостоятельных процессов в хоне резания. Образующая траектория зависит от параметров динамической системы и эволюционно изменяющихся параметров динамической связи. Кроме этого, необходимо учитывать, что при подаче на зуб меньшей, чем 0,01-0,02мм, может наблюдаться увеличение шероховатости за счет возможного перескока траектории движения инструмента. При этом волнистость может увеличиваться еще больше. Поэтому, строго говоря, для обеспечения неизменных значений высоты микронеровностей необходимо изменять величину подачи при обработке одного типоразмера деталей.
При обработке детали, у которой изменяются параметры жесткости вдоль траектории движения инструмента, желательно при построении программы установить промежуточные узловые точки для интерполяции траектории, обеспечивающей малые вариации отношения силы к значению жесткости в направлениях, нормальных к обрабатываемой поверхности.
При обработке участков поверхности, на которых изменяется направление движения стола (рис. 2б участок А-В
), дополнительно необходимо учитывать изменение угла контакта фрезы с заготовкой, который влияет на силы резания, и, следовательно, на упругие деформации и всю динамику системы.
Скорость резания выбирается из условий обеспечения устойчивости траекторий. Как известно [1], с одной стороны при увеличении скорости возрастает запас устойчивости, с другой – при увеличении частоты вращения инструмента, возможно параметрическое самовозбуждение системы. Теоретические и экспериментальные исследования [3, 5] показывают, что для потери устойчивости в системе достаточно незначительного увеличения частоты вращения шпинделя и скорости резания. Так как динамическая характеристика процесса резания зависит от износа инструмента и точности геометрии инструмента, значит, существует оптимальное значение скорости, при которой одновременно отсутствуют параметрические самовозбуждения и система устойчива.
На скорость резания накладываются ограничения, обусловленные отсутствием биений в деформационных смещениях инструмента на участках формообразования инструмента.
Учитывая вышеперечисленное, можно утверждать, что динамика процесса фрезерования определяется параметрами динамических подсистем, взаимодействующих с процессом обработки, технологическими режимами и геометрией инструмента. Принципиально возможно изменять все эти характеристики для обеспечения требуемых показателей качества формируемой поверхности.
Приведем пример эффективности управления процессом на примере обработки внутренней поверхности вилки крепления лонжерона к несущей системе вертолета. Исходные технологические параметры, положенные в основу построения программы ЧПУ на чистовых проходах, следующие: подача на зуб – 0,02 мм; скорость резания – 0,8 м/с; величина технологического припуска – 2, 5 мм. Использовалась четырехзубая фреза из Р6М5 диаметром 60,0 мм с углом наклона зуба 35°. После динамического анализа и экспериментальной проверки установлено, что частота вращения шпинделя, при которой отсутствует параметрическое самовозбуждение, лежит ниже 500 Гц. Кроме этого, согласно диаграмме устойчивости, система теряет устойчивость при скорости, меньшей 0,8 м/с. На основе этого установлено значение скорости безвибрационного фрезерования в пределах (0,8-1,4) м/с. При подаче на зуб меньше 0,01 мм, возрастает нестационарность формирования микрорельефа. В связи с этим определены следующие рациональные режимы: скорость резания 1,2 м/с (соответствует частоте вращения шпинделя 400 об/мин); величина подачи на зуб – 0,04 мм. Для уменьшения вариаций сил число зубьев увеличено до 6. При таком режиме после одного прохода улучшились характеристики качества формируемой поверхности. В результате, при чистовой обработке внутренней поверхности для получения требуемого качества, удалось уменьшить число проходов при обработке с трех до одного. Кроме этого для фиксирования наступления предельного состояния процесса фрезерования были апробированы системы диагностирования на основе измерения шума процесса с помощью измерительного микрофона.
Выводы
Предложенный алгоритм (этапы) обеспечивает повышение качества поверхности при фрезеровании концевыми фрезами. Он включает требования к инструменту, выбору его геометрии, технологическим режимами параметрам точности станка. В общем случае проблема улучшения микрорельефа формируемой поверхности решается с помощью метода, основанного на использовании сведений об акустическом шуме, измеренном микрофоном, с последующей обработкой информации. Предложенный метод позволяет в процессе резания оценивать предельные состояния процесса для получения информации о замене инструмента и его переналадки.
Разработанные рекомендации по выбору параметров инструмента и технологических режимов обработки, а также метод для контроля критического состояния процесса могут быть приняты к внедрению в реальных условиях на предприятиях авиационной промышленности.
Список источников
- Zelinski, P. Five sides and one zero: Shopfloor programming for five-side parts. Mod. Mach./P. Zelins-ki // Shop. – 2003. – 76. – № 7. – С. 54–55.
- Hans, B. Kief. CNC for Industry / Hans B. Kief. – 2000. – Р. 198.
- Заковоротный, В. Л. Определение оптимальных траекторий при обработке с учётом эволюции процесса резания / В. Л. Заковоротный, В. П. Лапшин, А. А. Губанова // Вестник Дон. гос. техн. ун-та. – 2014. – № 3 (78). – С.5–12.
- Заковоротный, В. Л. Синергетическая концепция при построении систем управления точностью изготовления деталей сложной геометрической формы/ В. Л. Заковоротный, А. А. Губанова // Инновационные технологии в машиностроении и металлургии : сб. трудов VI междунар. науч.-практ. конф. – 2014. – С.51–70.
- Заковоротный, В. Л. Определение оптимальных координат переключения циклов обработки в эволюционной динамической системе резания/ В. Л. Заковоротный, В. П. Лапшин, А. А. Губанова // Изв. вузов. Сев.-Кавк. регион. Техн. науки. – 2014. – № 4 (179). – С.59–63.
- Заковоротный, В. Л. Особенности формирования притягивающих многоообразий в окрестности стационарных траекторий попутного фрезерования концевыми фрезами/В. Л. Заковоротный, А. А. Губанова, А. Д. Лукьянов // Вестник Дон. гос. техн. ун-та. – 2016. – № 3 (86). – С.23–38.
- Губанова, А. А. Виброакустическая диагностика фрезерования концевыми фрезами / А. А. Губанова, Н. Н. Черненко// Юбилейная конференция студентов и молодых ученых, посвященная 85-летию ДГТУ [Электронный ресурс] : сб. трудов. науч.-техн. конф. – Ростов-на-Дону, 2015. – С.5089–5091.