Увага! На момент написання даного реферату магістерська робота ще не завершена. Передбачувана дата завершення: липень 2019 р. Повний текст роботи, а також матеріали по темі можуть бути отримані у автора після зазначеної дати. З усіх питань звертатися за адресою stepa.sergey.nov@mail.com
Зміст
- Вступ
- 1. Актуальність теми
- 2. Мета і завдання дослідження
- 3. Дослідження умов роботи ліній фасування сипучих матеріалів
- 3.1 Види дозаторів
- 3.2 Види пакувальних машин
- 3.3 Дозування сипучих матеріалів у виробничих умовах
- Список посилань
Вступ
Обсяг операцій з сипучими матеріалами на підприємствах хімічної, харчової промисловості, в сільському господарстві і будівництві на території всього пострадянського простору обчислюється мільярдами тон. Значна частина цих матеріалів піддається процесам дозування, з подальшою упаковкою і транспортуванням. Інтенсифікація технологічних процесів з впровадженням безперервних технологічних операцій визначає підвищені вимоги до бункерних установок, пристроїв для автоматизованої подачі сипучого матеріалу в дозатор, а також до дозуючих пристроїв.
Автоматизація це один із напрямів науково-технічного прогресу, що використовує саморегулюючі технічні засоби і математичні методи з метою звільнення людини від участі в процесах отримання, перетворення, передачі і використання енергії, матеріалів, виробів або інформації, або істотного зменшення ступеня цієї участі або трудомісткості виконуваних операцій. Автоматизація дозволяє підвищити продуктивність праці, поліпшити якість продукції, оптимізувати процеси управління, відсторонити людину від виробництв, небезпечних для здоров'я; вимагає комплексного, системного підходу до вирішення завдання. До складу систем автоматизації входять датчики (сенсори), пристрої введення, пристрої керування (контролери), виконавчі пристрої, пристрої виведення, комп'ютери[7].
Основна тенденція розвитку систем автоматизації йде в напрямку створення автоматичних систем, які здатні виконувати задані функції або процедури без участі людини. Роль людини полягає в підготовці вихідних даних, вибір алгоритму (методу рішення) і аналізі отриманих результатів. Також в подібних системах передбачається поступово нарощувана захист від нестандартних подій (аварій) або способи їх обходу [7].
1. Актуальність теми
Сучасний ринок заснований на конкуренції виробників, успіх яких оцінюється не за обсягами виробленої продукції, а за рівнем ефективності виробництва. Цей рівень визначається ступенем задоволення споживача з найменшими витратами. В даний час процеси автоматизації з дозування, упаковці і транспортуванні сипучих матеріалів є одним із перших місць в галузях харчової, хімічної, металургійної промисловості, в будівництві і сільському господарстві.
Важливим етапом в транспортно-технологічних схемах доставки сипучих матеріалів від виробника до споживача є процес їх розфасовки в різні види тари. Так як дозування матеріалів на виробництві невід'ємно пов'язане з їх розфасовкою і транспортуванням, в багатьох випадках за рахунок фізичної сили людини, що в свою чергу супроводжується сильним виділенням пилу і несе певну небезпеку для здоров'я людини, виникає необхідність застосування автоматичних дозуючих і пакувальних ліній. Зважаючи на відсутність єдиної моделі сипучого середовища виникає необхідність в проведенні більш ретельного вивчення властивостей сипучих матеріалів при їх розфасовці і упаковці [12].
2. Мета і завдання дослідження
Метою роботи є підвищення ефективності напівавтоматичних ліній розфасовки сипучих матеріалів
Для досягнення поставленої мети необхідно вирішити такі завдання:
- Дослідити умови роботи ліній фасування сипучих матеріалів;
- Визначити реологічні характеристики характерних сипучих матеріалів;
- Впорядкувати вантажі по плинності і об'ємною вагою;
- Вибрати відповідні захватні пристрої для подачі тари до завантажувального пристрою і видачі завантаженої тари на транспортуючий пристрій;
- Розробити алгоритм і провести аналіз пневмогідравлічної системи для роботи маніпулятора, в тому числі з керуванням від програмованого контролера;
- Проаналізувати динамічні властивості виконавчих механізмів;
- Виконати фізичне моделювання і уточнити параметри системи фасування сипучих матеріалів.
3. Дослідження умов роботи ліній фасування сипучих матеріалів
3.1 Види дозаторів
На сьогоднішній день розрізняють три основних способи дозування сипких речовин: масовий, ваговій і об'ємний.
Ваговий спосіб дозування заснований на вимірюванні ваги продукту і відмірювання його за даним критерієм з використанням стандартних мір ваги – кілограм і грам. Ваговий метод можна застосовувати практично до будь-яких видів продукту (речовин) і є найбільш поширеним. Єдиним винятком є рідини і пасти, які більш звично вимірювати в літрах або см 3 і дозувати об'ємним або масовим способом [8].
Масовий спосіб дозування використовує принцип вимірювання кількості продукту, що пройшов (подається) через певний простір і застосовується, переважно, для дозування рідин, паст і газів. Вимірювання доз в масовому способі відбувається за допомогою см 3 або літрів. Найбільш класичним застосуванням масового способу дозування є термінали зливу/наливу нафтопродуктів [8].
Об'ємний спосіб дозування заснований на принципі заповнення продуктом певного вільного простору і використовує для вимірювання стандартні одиниці вимірювання – см 3 або літри. В основному, застосовується для дозування рідин, паст і газів, але може також використовуватися для дозування різних сипучих матеріалів. При цьому, об'ємне дозування сипких продуктів передбачає подальший перерахунок об'ємних заходів в більш звичні вагові [8].
Найбільш застосовними і поширеними дозаторами для сипучих речовин є: шнекові, об'ємні і вагові дозатори.
Шнековий дозатор – застосовується для дозування сипких продуктів, порошків, зернистих матеріалів (що не піддаються подрібненню), гранул, паст, а також при дозуванні суспензій, радіоактивних та інших середовищ, в яких неприпустимо здавлювання середовища, для забезпечення постійної витрати. Зазвичай мають порівняно невисоку точність, прості і надійні, але не здатні створити значний напір рідини, а також не відповідають вимогам до компактності і герметичності. Являють собою, в основному, шнек, укладений в кожух; робочий інструмент даного типу може розташовуватися вертикально, горизонтально або під нахилом, зустрічаються дозатори з декількома шнеками [8].
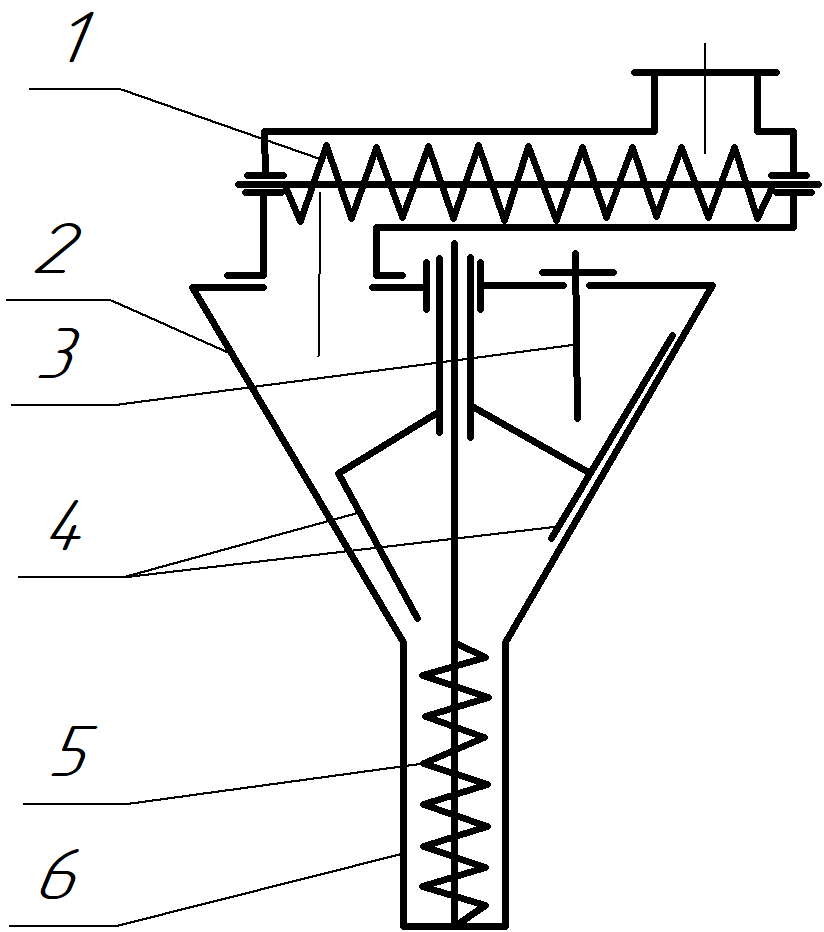
Принципова схема шнекового дозатора з двома шнеками
- Живлячий шнек;
- Конічний бункер;
- Датчик рівня продукту;
- Лопаті мішалки;
- Дозуючий шнек;
- Корпус дозуючого шнека (кожух).
Об'ємний дозатор – за допомогою даного виду дозаторів дозують гази, рідини, пасти, а також тверді сипучі матеріали; такі дозатори прості за конструкцією і цілком надійні, широко застосовуються в харчовій і інших галузях промисловості при подачі рідких і сухих дисперсних матеріалів. Відрізняються довговічністю і зручністю в експлуатації. Їх продуктивність регулюють за допомогою зміни швидкості наповнення, часу циклу або об'єму; мають невисоку похибка.
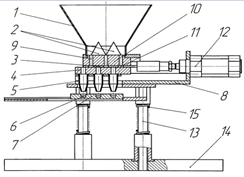
Пристрій для об'ємного дозування сипких матеріалів
- Завантажувальний бункер;
- Ворошитель;
- Шиберна заслінка;
- Живильник;
- Тічки;
- Співвісна матриця;
- Знімна палет;
- Підпружинений інструментальний стіл;
- Відвідні канали;
- Промислова решітка;
- Мірні ємності;
- Пневмоцилиндр;
- Вертикальні колонки;
- Станина;
- Пружини.
Використання об'ємного дозатора накладає певні обмеження на процес дозування:
- Для сипучих продуктів об'ємні міри вичислювання доводиться перераховувати в більш звичні вагові. При цьому такий перерахунок необхідний для
кожного виду продукту, що дозується, оскільки продукти з різною щільністю, при одному і тому ж обсязі
склянки
, матимуть різні вагові показники. - Межі дозування обмежені розмірами
склянки
. І хоч виробники дозаторів і намагаються робитисклянки
з регульованим внутрішнім об'ємом, все одно існують певні межі, в прив'язці до початкового розмірусклянки
, вийти за які дозатор не в силах. - Не кожен сипучий продукт здатний швидко просипатися і якісно заповнювати обсяг
склянки
, особливо в високому темпі автоматичного режиму. Липкі, маслянисті або легкі продукти, такі як родзинки, інжир, курага, кукурудзяні палички, практично неможливо дозувати даними дозатором, оскільки їхважкосипкість
призводить до суттєвих відхилень в розмірах і вазі доз.
Ваговий дозатор призначений для дозування ваговим способом будь-яких сипучих продуктів за винятком порошкоподібних, що пилять.
Проблема пилять продуктів, що пилять, та ж, що і у об'ємного дозатора – виникнення пилу заважає нормальній роботі обладнання і забруднює
пакувальний матеріал. В іншому ваговий дозатор здатний дозувати навіть важкосипучі
продукти. Сучасні вагові дозатори для
сипучих продуктів мають унікальну здатність – вони адаптуються під певні продукти. Також серед переваг відзначається компактність
датчиків тиску, універсальність (процеси зважування і дозування повністю автоматизовані, управління вагами зводиться до управління
приладом завантаження), оптимальна точність і велика продуктивність. Вагові дозатори конструюються таким чином, щоб висота падіння
сипучих речовин була мінімальною. Крім того, комбінаційні дозатори оснащуються спеціальними трасами, за якими і рухаються продукти.
Завдяки цьому практично повністю виключається можливість пошкодження навіть самих крихких продуктів при їх фасування. До недоліків можна
віднести необхідність попереднього визначення гідростатичного тиску від ваги продукту в ємності, низька швидкість роботи. У порівнянні з
об'ємними складні, тому мають малу експлуатаційну надійність і високу вартість.
Даний тип дозатора складається з вібролотка, ковша, що зважує,який підвішений на тензодатчику і блоку управління. Дозування відбувається шляхом засипання продукту вібролотком у ваговий ківш до досягнення вагового показника, виставленого оператором на блоці управління. Коли необхідна вага досягнута, вібролоток зупиняється, а ківш висивает свій вміст в тубус або лійку.
3.2 Види пакувальних машин
Використання механічних пристроїв для пакування сипучих продуктів у кілька разів підвищує швидкість і ефективність процесу в порівнянні з ручним фасуванням. Орієнтуючись на бюджет, можна вибрати агрегат наступних видів:
- Напівавтоматичний або автоматичний верстат. Забезпечує повний технологічний цикл від зважування (дозування) до запечатування пачок. Автоматичні самостійно склеюють упаковки. Необхідно тільки заправити апарат плівкою;
- Верстати з об'ємним або ваговим дозатором. Перші відміряють продукт за обсягом, другі – по масі. Вагові дозатори користуються великим попитом на ринку, додатково вони комплектуються мультиголовками, що дозволяють дуже точно зважувати навіть малі кількості сипучих продуктів, наприклад, спеції;
- Горизонтальні або вертикальні механізми для упаковки сипучих товарів. Вертикальні верстати більш компактні і продуктивні. Продукт в них надходить в дозатор самопливом, тоді як в горизонтальному його підвозять транспортером.
Напівавтомати для розфасовки сипучої продукції – працюють з цукром, крупами, макаронами. Продукція фасується в м'які пакети, шви заварюються. Напівавтоматичні верстати працюють з похибкою до 3%. Автомати для розфасовки забезпечують точність зважування до 2%. Автоматичні лінії використовуються для фасування будь-яких сипучих товарів, в тому числі гранулятов і нехарчових (прального порошку, цементу, піску). Продуктивність 15-100 пакетів в хвилину. Устаткування для кускових товарів – принципова відмінність їх у великому обсязі ковша. Стандартний – восьмилітровий, спеціального виконання – до 15 літрів. Програма управління передбачає роботу з шматками різних розмірів і властивостей. Похибка дозування становить два шматки.
Устаткування з шнековим дозатором – група устаткування, оснащена об'ємним дозатором шнекового типу. Використовується для акуратного фасування порошків – борошна, пральних, пудри. Точність розфасовки залежить від механічних властивостей товару і дозування і становить від 4 до 10%.
Верстати з мультиголівковиv дозатором по вазі – обладнання для упаковки заморожених ягід і овочів, пельменів та інших
нестандартних
продуктів. Похибка ваговій дозування становить до 4%.
3.3 Дозування сипучих матеріалів у виробничих умовах
Розглянемо процес фасування сипучих матеріалів у виробничих умовах на прикладі борошна.
Сьогодні машинобудівні заводи виробляють для борошна пакувальне обладнання, автоматизоване і яке легко обслуговується. Таке обладнання вимагає мінімальних витрат, як трудових, так і тимчасових, а, відповідно, і енергетичних витрат. Зазвичай воно представлено у вигляді пакувальної лінії вертикальної конструкції, призначеної для формування паперового пакета або пакета з іншого матеріалу. Пакувальну лінію укомплектована дозаторами, передбаченими для автоматичної процедури дозування борошна. Дозатор борошна конструктивно виконується:
- або з вертикальним шнеком, працюючи на основі шнекового дозування,
- або з телескопічними чашками, працюючи як об'ємний дозатор.
Якщо лінія забезпечена дозатором зі шнеком, то після дозування, на одному з етапів, встановлюється система контрольного визначення маси борошна. Це зважувальний пристрій, якщо є відхилення маси продукту з перевищенням заданої межі, необхідно виштовхнути забракований пакет. Якщо ж має місце одностороннє відхилення маси борошна у трьох або чотирьох пакетів поспіль, то по зворотному зв'язку на дозатор подається сигнал з метою зміни числа обертів шнека, і величина дози коригується. Сучасні дозатори для борошна виготовляють із сортів нержавіючої сталі, дозатори комплектуються системою контролю оборотів за допомогою енкодера, його швидкість регулюється за допомогою інвертера (перетворювача). Дозатори оснащуються засувками з пневмоприводом, які перекривають подачу борошна. На розвантажувальній горловині розміщується аспіраційний патрубок. Дозуючий шнек може швидко замінюватися (мається патрон для швидкої заміни).
Дозатори можуть також встановлюватися автономно. Автоматична лінія для фасування і упаковки борошна зазвичай складається з системи подачі порожніх пакетів, яку називають інакше магазином порожніх пакетів, бункера для завантаження борошна, оснащеного системою дозування за допомогою шнекового дозатора, станції наповнення (карусельного типу або іншого виконання) і пристрої утряски пакета, наповненого борошном (для зменшення його обсягу). Далі йде лінія закриття пакета. Пакет з борошном з паперу (1-2 кг) зазвичай проклеюють гарячим клеєм, роблячи попередньо подвійний подворот. Для упаковки борошна вагою по 5-25 кг в пакети, що мають ручку, використовують зашиття нитками, а внутрішній поліетиленовий шар мішка попередньо запаюється. При великих пакувальних форматах передбачають можливість використання великого плетеного мішка, що має поліетиленову вставку і вшивну ручку (як при фасуванні великих обсягів цукру). У комплект лінії упаковки може входити пристрій наповнення і система утряски пакетів (карусельного виконання, наприклад), розраховане на 4-14 позицій з дозуванням і наповненням одночасно до 3 пакетів. Магазин порожніх пакетів вміщує 300-1200 штук. Магазин може поповнюватися під час режиму експлуатації лінії. Пристрій утряски може виглядати на деяких лініях у вигляді вібротранспортера. Для успішної роботи пакувального обладнання муки м ного значить наявність системи аспірації, так як борошно відноситься все ж до продуктів, що порошать. Деяке обладнання вже оснащено такою системою. При її відсутності про це слід подбати підприємству-споживачеві. Система управління і регулювання процесами лінії розфасовки і упаковки борошна реалізується на сучасних моделях через контролер PLC і віддалений доступ, маючи можливість дистанційного контролю, який здійснюється по локальній мережі. Деяке обладнання виконується на базі кулачкового механізму, система не має вакуумних насосів, це значно збільшує експлуатаційну надійність обладнання. Встановлена електрична потужність сучасної лінії упаковки борошна становить в середньому 35 кВт.
Пакети, що виходять з фасувальною машини, надходять на конвеєр, де здійснюється групова упаковка. Операція групового пакування
це обгортання брикетів з пакетів з борошном термоусадочної плівкою або плівкою, що розтягується. При використанні полімерної плівки брикет
краще по всьому периметру не обертатися, так як борошні буде важко дихати
. Найчастіше обладнання групового пакування вже входить в
склад пакувальної машини, утворюючи тим самим лінію упаковки або просто лінію борошна. Тому фасувальна машина і автомат групового пакування
борошна закуповуються одночасно і стикуються в єдину технологічну схему. Блок з окремих упаковок зазвичай складається з 6-8 пакетів. Групове пакування,
змінивши дерев'яні та пластикові ящики (багатооборотну тару), в які раніше укладалися пакети, будучи одноразовими, насправді
дуже зручна, економічна, компактна, не потребує ремонту, запобігає від спроби підміни продукції або несанкціонованого розкриття.
На пакувальних лініях борошна застосовуються групові упаковки з пакетів по 1 кг або 2 кг, що формують по 5-6 пакетів з борошном в кілька рядів.
Для упаковки брикетів в плівку їх подають в термоусадочний тунель, де по контуру брикетів відрізається плівка і проводиться автоматична
усадка, яка полягає в стисненні плівки під дією високої температури і щільному охопленні нею брикету з усіх боків.
Принцип роботи всієї лінії упаковки для муки можна описати таким чином: на лінії упаковки роботом (маніпулятором) відбувається автоматичний забір з магазину порожніх пакетів для наповнення борошном, пакет розкривається і відправляється в секцію заповнення борошном. Устаткування пакувальних ліній борошна, яке передбачає використання готових пакетів для наповнення, займає меншу площу. У лінії відсутня в цьому випадку ціла операційна ділянка, яка виготовляє пакет, і тому таке обладнання коштує дешевше. Дешевизна ця, правда, з часом нівелюється, тому що папір в рулоні обходиться дешевше, ніж готові пакети. Всі операції на пакувальному конвеєрі залишаються тими ж. Однак, чим більше місць дозування в лінії, тим точніше буде доза наповнення і, відповідно, вище продуктивність машини та всієї лінії в цілому. Чим сильніше операція утряски, тим краще сформується пакет. Габарити автомата це також збільшує.
Після фасування борошна в паперові пакети до їх закриття не зайвою виявляється процедура утряски борошна в пакеті. Суть цієї утряски в тому, що наповнений борошном пакет піддається з боку денця зовнішньому впливу, ударному або коливального. В результаті процеса утряски відбувається деаерація і ущільнення борошна, верхній рівень борошна в пакеті зменшується, і верхній край пакета легше загортається. Досягти гарного наповнення пакета і отримати красиво сформований пакет без процесу утряски досить важко. При утрусці борошно і борошняний пил, які осідають на стінках пакета під час засипання туди борошна, зсипаються в пакет. Залежно від вибору конструкції обладнання, утруска може здійснюватися за допомогою частих ударів або за допомогою коливань. Пакет в процесі подальшого руху закривається автоматично, гребінець на верхньому шві складається, а потім приклеюється до верхньої частини пакета. Після цього упаковані пакети направляються на конвеєр групової упаковки, де формуються брикети з декількох пакетів в кілька рядів. Сформований брикет накривається термозбіжною плівкою і направляється в термоусадочний тунель. У термотунелі, де встановлена ??необхідна температура і потрібний час витримки, брикети рухаються по конвеєру. За рахунок температурного впливу відбувається обтягування брикетів термоусадочною плівкою, і тепловий температурний удар при цьому доводиться тільки на полотно пакувального матеріалу, а не передається продукту.
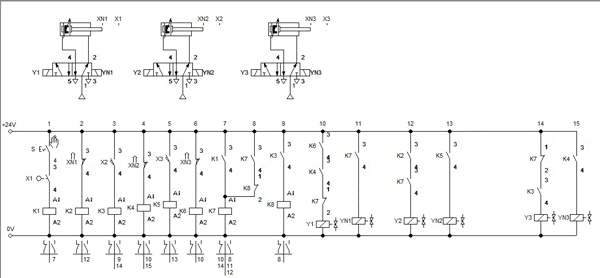
Демострація роботи пневмоелектричної схеми для дозування сипких матеріалів масою 1 кг
(анімація: 5 повторів, 19 кадрів, 199 кілобайт)
Список посилань
- Донской А. С. Математическое моделирование процессов в пневматических приводах: учебное пособие / А.С. Донской. – СПб.: Изд-во Политехн. ун-та, 2009. – 122с.
- Пневмопривод: метод. указ. к выполнению курсового проектирования для студентов спец. 151001
Технология машиностроения
всех форм обучения / Л. В. Ручкин, А. В. Скрипка, В. А. Будьков ; Сиб. гос. аэрокосмич. ун-т. – Красноярск, 2010. – 96 с. - Промышленные мехатронные системы на основе пневмопривода: Учеб. пособие /Е.В. Пашков, Ю.А. Осинский. – Севастополь: Изд-во СевНТУ 2007. – 401 с, ил
- Электропневмоавтоматика 1998 by Festo Didactic GmbH & Co., RechbergstraBe 3, D-73770 Denkendorf. Авторы: Г. Преде, Д. Шольц; Перевод: С.В. Сулига.
Свободно программируемые контроллеры
Festo Didactic GmbH & Co., D-73770 Denkendorf 2004. Авторы: Р. Близинер,Ф. Эбель, К. Лёфтер, Б. Плагеманн, Х. Регбер, Э. Фон Терци, А. Винтер.- Электропневмоавтоматика в производственных процессах: Учебное пособие / Е.В. Пашков, Ю.А. Осинский, А.А. Червякин; Под ред. Е.В. Пашкова. – 2-е изд., перераб. и доп. – Севастополь: Изд-во СевНТУ, 2003 – 496 с., ил.
- Автоматизация [Электронный ресурс]. Режим доступа: https://ru.wikipedia.org/wiki/Автоматизация
- Дозатор [Электронный ресурс]. Режим доступа: https://ru.wikipedia.org/wiki/Дозатор
- Каталог продукции FESTO [Электронный ресурс]. – Режим доступа: https://www.festo.com/cms/ru-uk_ua/index.htm
- Юшин Е.С. Гидро- и пневмопривод машин в нефтегазовой отрасли [Текст] : метод. указания / Е. С. Юшин. – Ухта : УГТУ, 2016. – 27 с.
- Герц Е.В., Крейнин Г.В. Расчет пневмоприводов. Справочное пособие. М.,
Машиностроение
, 1975. – 272 с. с ил. - Рогинский Г.А. Дозирование сыпучих материалов. М.,
Химия
, 1978. – 176 с.