Theoretical basis for the application of the provisions of ISO 10012–2003 Measurement management system
in a machine-building enterprise
Attention! While working on the essay the master`s dissertation is still being written. Expectable date of completing the dissertation is July, 2019. The complete text of the dissertation and materials on the research topic can be received from the author or his scientific adviser after the specified date.
Content
- Introduction
- 1. Formulation of the problem
- 2. Relevance of the work
- 3. Main part
- Conclusion
- References
Introduction
Measurement – finding a physical quantity experimentally with the help of special technical means (sleeve diameter using a micrometer caliper). In the technique, along with the concept of dimension
, the concept of control
is widely used, by which is meant a concept that includes the definition of both quantitative and qualitative characteristics. For example, the control of defects in the outer surface.
Unity of measurements – such a state of measurements, in which their results are expressed in legal units and measurement errors are known with a given probability. Without the uniformity of measurements, it is impossible to compare the results of measurements performed in different places at different times using different methods and measuring instruments [4].
Accuracy of measurements – measurement quality, reflecting the proximity of their results to the true value of the measured value. Under the method of measurement refers to the set of used measuring tools and conditions for their use.
1. Formulation of the problem
In the process of functioning of a machine-building enterprise, various measuring instruments are used. Business units working with measuring instruments can be grouped into a number of groups determined by the nature of the tasks being performed. To a large extent, such a grouping is influenced by the ISO 10012–2003
Measurement Management System
(media). It is necessary to group the subdivisions of a machine-building enterprise by the nature of the tasks solved in relation to the means of measurement.
2. Relevance of the work
It consists in the absence of a formalized approach to the formation of media components at a machine-building enterprise. The solution to this problem will provide the construction of a rational and effective measurement system of a machine-building enterprise. The purpose of the media in ISO 10012–2003 is to ensure the suitability of measuring equipment and measurement processes for their intended use. The use of the process approach in the consideration of media tasks allowed the development of a media model shown in Figure 1. [1]
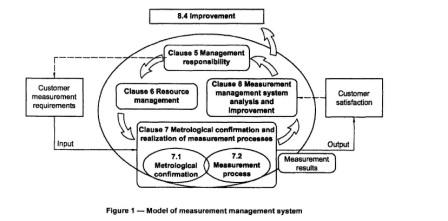
Figure 1 – Model of a measurement management system
The correct construction of the media is of great importance for the achievement of goals in the field of product quality by reducing the likelihood of inaccurate measurement results [3]. As part of the media, the management of measuring equipment and measurement processes is implemented, which makes it possible to control the reliability of measurement results of characteristics affecting product quality. The tasks of the measurement management system include the verification of measuring equipment and the application of statistical methods for managing the measurement process. The term measurement process
as used in the standard refers to physical activities associated with performing measurements (for example, when designing, testing, manufacturing, or controlling a product).
Approaches to building media at a machine-building enterprise are determined by the purpose of its existence – manufacturing, assembling parts into products. The objects of the main production in mechanical engineering are machines and mechanisms for various purposes. The technological process of manufacturing machines involves the production of parts, prefabricated units (nodes) of products with specified dimensions. Improving the quality, expanding the range and increasing the production of products that are in market demand, as a rule, require an increase in the accuracy of parts manufacturing and the use of more advanced media MMS [3]. The organization of the process of material and technical supply of the enterprise involves the expansion of input control and the nomenclature used by the MS. The modern direction of development of the listed and other and other tasks of the engineering enterprise is the construction of a rational media.
3. Main part
The stability of the technological process for the production of products involves the widespread use of measurement tools in various departments of the engineering enterprise. These units can be divided into two groups with respect to measuring instruments:
1. Using measuring instruments in the process of production: manufacturing technologists; normocontrollers detecting and screening defective parts, components and products; testing laboratories that provide an assessment of the conformity of finished products to consumer requirements [6].
2. Providing reliability of measurement results – metrological service. In its activities can be identified the main tasks: ensuring the calibration of measurement tools; development of measurement methods and procedures; repair of measuring instruments; monitoring and internal audit of the media, etc.
The technological process of manufacturing and assembling parts at a machine-building enterprise involves the wide use of measuring tools of casting dimensions. Manual measuring tools include: a caliper, a ruler, a micrometer, a caliber-plug and a caliber a bracket. Automatic tools involve setting up measuring tools performed by specialized personnel-service engineers. Technological processes of modern industrial facilities require monitoring a large number of parameters. In this regard, in the design and operation of industrial installations, exceptional importance is attached to the issues of ensuring reliable control over the process. Reliability and reliability of process control are largely determined by the quality of the adjustment of measuring instruments. Adjustment of measuring instruments provides for a complex of works on their verification (verification) and adjustment, ensuring obtaining reliable information about the values. Works are carried out by the Metrological Service personnel [6].
Normocontrol is aimed at identifying defective products. The type of tools used by normontrollers imposes requirements on their level of qualification. Low-skilled personnel will detect defective parts using gauges. Highly qualified and competent staff-uses measurement tools and performs analysis of measurement results to identify defects [5]. Within the MMS, this staff must continually improve their skills.
Normocontrol is the final stage of development of project, design and technological documentation. It is recommended to entrust the delivery of the original documents to the technical documentation department or the substitute unit thereof.
The test laboratory must be equipped with measuring, testing and monitoring equipment, as well as consumables for proper measurement. Calibration, verification of measuring and testing equipment, if necessary, is carried out before putting it into operation and further in accordance with the established program [2].The general equipment calibration program should ensure traceability of measurements carried out by the laboratory for compliance with national and international exemplary measuring instruments. Exemplary measuring instruments available in the laboratory should be used only for calibrating work equipment and should not be used for other purposes. Exemplary measuring instruments should be calibrated by a competent authority that can ensure that their compliance with national or international standards is monitored [3].
The metrological service solves problems in the enterprise as a whole in close connection with its units using measurement tools.
Among the tasks to be solved are:
– ensuring the operational status of funds;
– metrological confirmation of the suitability of measuring instruments and measuring equipment (calibration and verification) – to ensure that the metrological characteristics of measuring equipment comply with the metrological requirements for the measuring process (Figure 2);
– analysis of the state of measurements at the enterprise and the development of measures to improve the metrological support;
– verification and metrological certification of measuring instruments used at the enterprise; certification of measurement procedures;
– metrological examination of projects and existing design, technological and other regulatory-technical documentation;
– control over the manufacture, condition, use and repair of measuring instruments and the observance of metrological rules, requirements and norms.
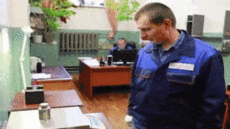
Figure 2 – The process of calibration of measuring instruments
(animation: 8 frames, cycles of repeating – 8, 184 kilobytes)
Records formed within the media are carried out in accordance with the requirements specified in the ISO 10012 standard Measurement Management Systems. Requirements for measuring processes and measuring equipment
[1]. Each of them must have a date approved by an authorized person as confirmation of the correctness of the results obtained. These records must be kept and made available. Record keeping time depends on: requirements of the SI supplier, mandatory and legal requirements, manufacturer's responsibility (approximately 3-5 years). Records relating to measurement standards may be held indefinitely. The calibration results must be recorded so that the traceability of the measurements can be demonstrated, and so that these results can be reproduced in conditions close to the original. Records can be handwritten, printed or stored in electronic or magnetic memory, or some other storage medium. The metrology service should ensure that only authorized personnel can make, modify, issue or withdraw records [4].
Conclusion
The divisions of a machine-building enterprise can solve the tasks of a measurement management system into four types: technologists, controllers, test laboratories (perform measurements) and the metrological service (ensures the accuracy of measurements.) Measurement and analysis methods, monitoring the use of measurement performance and operation management systems metrological service.
References
- Азгальдов Г. Г. Количественная оценка качества. Библиография. – М.: Изд-во стандартов, 1971 г. – 176 c.
- Маругина В. М., Азгальдова Г. Г. Квалиметрическая экспертиза. Руководство по организации экспертизы и выполнению квалиметрических расчетов. Книга третья. Расчётные модели качества. – М.: Русский Регистр, 2002 г.
- Гличев А. В. Качество, эффективность, нравственность: Учебное пособие. – М: Премиум Инжиниринг, 2009 г. – 358 с.
- Абдувалиев А. А. Основы обеспечения единства измерений. – 2005 г.
- Захаров В. И. Взаимозаменяемость, качество продукции и контроль в машиностроении – Л.: Лениздат, 1990 г.
- Клюев В. В. Машиностроение. Измерения, контроль, испытания и диагностика. –
Машиностроение
, 1996 г. - Ершова И. Г., Дмитриев С. И. Метрологическое обеспечение производства. Псков ППИ.: 2010 г.
- Мишина В. М. Метрология, стандартизация, сертификация. M.: 2009 г. – 10 с.
- Ершова И. Г., Дмитриев С. И. Метрологическое обеспечение производства. Учебное пособие. Псков ППИ 2010 г.
- Путкова А. В. Метрологическое обеспечение в машиностроении. Журнал экономических исследований. – 2016 г. – 44 с.
- Прохорова В. Т. Метрологическое обеспечение и контроль качества материалов и изделий. Шахты: ЮРГУЭС, 2009 г. – 159 с.
- Новицкий П. В. Оценка погрешностей результатов измерений, 1991 г.
- Безруков А. И. Метрология программного обеспечения. Экономические и правовые основы разработки программного обеспечения. – Саратовский Гос. Технич. Ун-т., 2003 г.
- Евстропов Н. А. Оценка технического уровня и качества промышленной продукции – М.: АСМС, 2004 г.
- Назаров В. Н., Карабегов М. А., Мамедов Р. К. Основы метрологии и технического регулирования: Учебное пособие – СПб: СПбГУ ИТМО, 2008 г.