Contents
- Introduction
- 1. Relevance of the topic
- 2. The goal and tasks of the study, the planned results
- 3. Analysis of the rectification process
- 4. Development of the concept of ACS
- 4.1. Analysis of the existing automatic control systems (ACS) of the object and the rationale for the need to improve the ACS
- 4.2. Description, assessment of the advantages and disadvantages of the developed alternative versions of the ACS concept
- 4.3. Justification of the choice and the expected results of the selected variant of the ACS concept
- 5. Synthesis of the mathematical model of the object
- 5.1. Synthesis of the structural diagram
- 5.2. Math model
- 6. Conclusion
- References
Introduction
Rectification is one of the most important processes in the chemical industry. Its purpose is to separate the mixture of components with different boiling points for individual fractions. The driving force of rectification is the difference between the actual concentration of components in the vapor phase from the equilibrium for a given composition of the liquid phase. The vapor-liquid system tends to achieve an equilibrium state. Upon contact with the liquid, the vapor is enriched in volatile components (low-boiling) and the liquid in volatile substances (high-boiling) components. The liquid and steam move countercurrent: steam – up, liquid – down. After a certain time from the top of the column continuously the liquid flows down as rich as possible with low-boiling component, and from the bottom – with high-boiling one.
The regulation of the distillation process is of interest for several reasons. From a scientific point of view, this is a complex multidimensional process, to the management of which various techniques can be applied. From the industrial point of view, better regulation will allow maximizing profits with more rational use of raw materials, higher energy efficiency, etc.
1. Relevance of the topic
At the moment, the problem of automation of the technological process is that the adjustment of regulators often occurs empirically, that in the conditions of a real object is associated with the loss of raw materials and a long time of commissioning the system.
The development of computing in recent years has made it possible to use a more advanced mathematical apparatus for describing processes occurring in distillation columns, with the aim of forming control actions that provide the best characteristics output product and maximum compensation of various disturbances.
The automatic control system will optimize the processes of maintaining the main technological parameters of the rectification process and increase the efficiency of the installation in quality and quantity of products.
2. The goal and tasks of the study, the planned results
Maintaining the concentration of distillate at a given level is the main task of the control system. This parameter is measured either directly (concentration sensor), or indirectly (temperature sensor), and affects the consumption of reflux fed to the column.
It is also necessary to control the flow of reflux returned to the column by irrigation. This is achieved by applying to the flow regulator. signal from either the temperature sensor at the top of the column, or from the concentration sensor, depending on the chosen scheme.
In addition, an alarm is required if the pressure in the column is exceeded from the specified limits (measured by a pressure sensor in the upper part column), the temperature of the top of the column, the flow rate of the initial mixture. With a pressure in the column above the allowable, as well as at the termination of the supply of the original mixtures into the column, automatic protection devices must be activated, disabling the installation. At the same time flows of distillate, residue and coolants overlap, and the flow of phlegm opens.
In order to control the process and analyze the performance of the system as completely as possible, it is necessary to ensure the collection, display and storage data from the temperature sensors of the top of the column, the flow rate of the feed mixture, the steam consumption in the boiler.
The expected economic and social effect of the introduction of the system – minimizing the consumption of steam and refrigerant, increasing the concentration of useful substances in the final product with the same volume of the initial mixture, as well as minimizing the influence of the human factor on the technological process.
3. Analysis of the rectification process
Rectification – separation of liquid mixtures into practically pure components, differing in boiling points, by repeated evaporation liquid and vapor condensation[1].
As a control object, there is a distillation unit for separation of a binary mixture, consisting of a plate distillation column, remote boiler, reflux condenser and condensate collector (fig. 1).
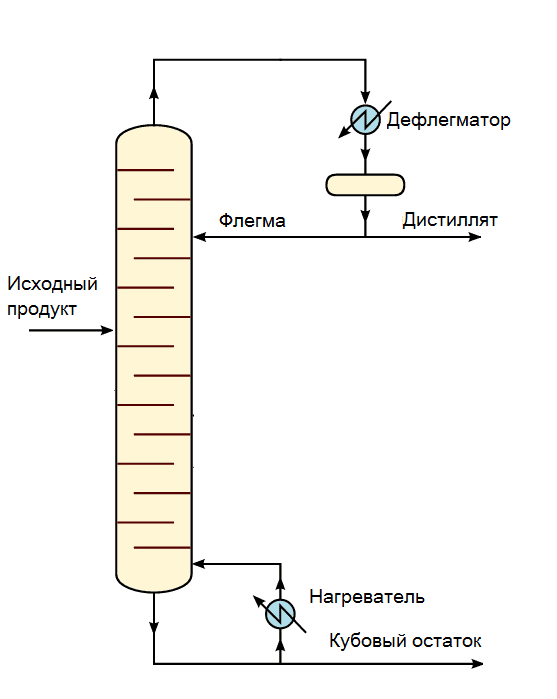
Figure 1 – Scheme of the distillation unit
From the physical point of view, rectification is possible, since initially the concentration of the individual components of the mixture in the vapor and liquid phases is different, but the system tends to equilibrium – the same pressure, temperature and concentration of all substances in each phase. Upon contact with liquid, steam enriches volatile (low-boiling) components, in turn, liquid – volatile (high-boiling) (fig. 2). Simultaneously with enrichment occurs heat exchange.
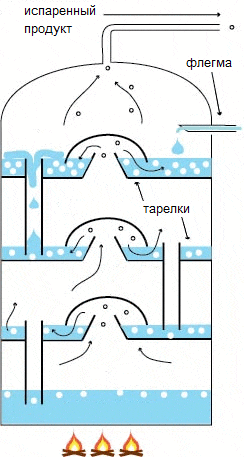
Figure 2 – Illustration of the processes inside the column (animation: 4 frames, 10 cycles of repetition, 134 kilobytes)
After switching on, the liquid in the cube is brought to a boil by the heater. The resulting steam rises up the column, then enters the reflux condenser, where it condenses (reflux appears) and returns in liquid form along the walls of the pipe to the lower part of the column, on the way back contacting the ascending steam on plates or nozzles. Under the action of the heater, the reflux becomes steam again, and the vapor above again condenses with a reflux condenser. Process becomes cyclical, both streams are continuously in contact with each other[1-3].
Indicators of the effectiveness of the process are the compositions of the output streams (bottom liquid, distillate) containing the target product. The purity of these target products is influenced by a number of disturbing effects of the process – composition, parameters of heat and coolants, pressure in the column and other quantities.
With respect to the rectification process, maintaining a given composition of the target stream is the goal of process control. The composition of the stream not containing target product, – the bottom residue – may change due to changes in the composition and feed rate of the original feed stream.
The main control actions are the reflux flow to the column and the coolant to the boiler. Moreover, a change in reflux consumption leads to relatively quick changes in the composition of the distillate and at the same time with a large delay and to a much lesser extent – to a change in the composition of the bottom residue. Change the same the consumption of heating steam leads mainly to a change in the composition of the bottom residue; the composition of phlegm at the same time changes much less[4].
Disturbing effects are changes in the flow rate of the initial mixture, the parameters of the initial mixture, the pressure in the column.
Summarizing all the above and presenting the object in the form of a “black box”, you can obtain the following analysis scheme of the rectification process from the point of view of the main material flows and their information variables (fig. 3).
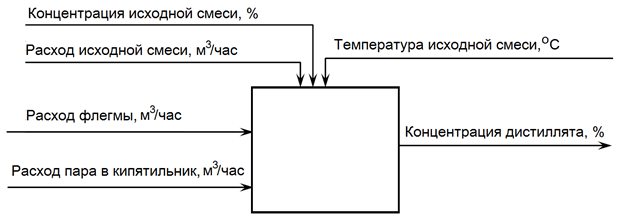
Figure 3 – Scheme of the analysis of rectification from the point of view of the main material flows and their information variables
4. Development of the concept of ACS
4.1. Analysis of the existing automatic control systems (ACS) of the object and the rationale for the need to improve the ACS
The simplest control system of a distillation unit is shown in fig. 4.
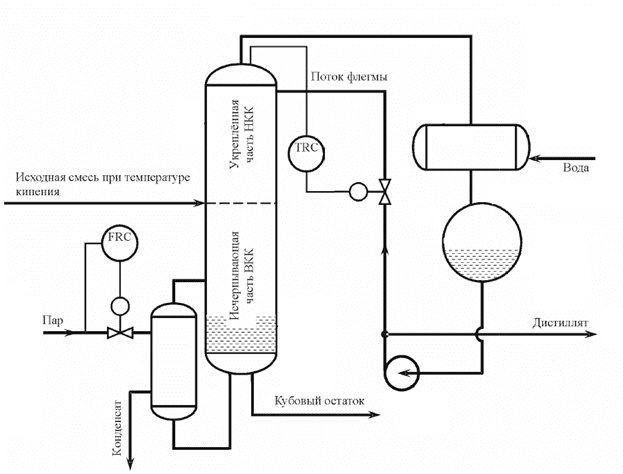
Figure 4 – Scheme of stabilization of the rectification process
In fig. 4, the temperature of the top of the column and the flow rate of steam supplied to the boiler are stabilized using local single-loop control systems. These systems are interconnected through the process and ensure compliance with the material and heat balances of the installation.[5].
The main parameter of the column is the vapor composition at the top of the column. The composition of the distillate is controlled by changing the reflux feed to the column. Regulator set on the supply line of phlegm in the column. According to the rules of phase separation in the separation of a binary mixture, if the pressure in the column is constant, the composition distillate and the temperature of the top of the column are uniquely related. Therefore, in the circuit, the source of information is the top temperature in the columns. If the number plates is large, then to improve the quality of regulation, the temperature is measured on a so-called control plate, where the temperature is more sensitive to filing reflux and where there is less delay when changing the composition of the initial mixture[6].
Such a scheme of several single-loop systems has a large delay and disturbing effects significantly change the mode of operation of the object[7]. These drawbacks of the base ACS necessitate the creation of a better system.
4.2. Description, assessment of the advantages and disadvantages of the developed alternative versions of the ACS concept
To improve the quality of the separation of the mixture in the ASR of the main quantities introduce corrective contours.
One of the possible implementation schemes is shown in fig.5. Here the flow of reflux into the column is regulated by a three-loop regulation system. Regulator composition 1b gives a correction signal to the temperature controller 1b, and this, in turn, corrects the task to the flow regulator 1a[1].

Figure 5 – Option cascade regulation of the composition of the distillate
If the residue is also a target product, then to ensure its purity, a system for regulating the steam consumption in the boiler is used (2a) with correction for temperature in the distant (exhaustive) part of the column (fig. 6)[8].
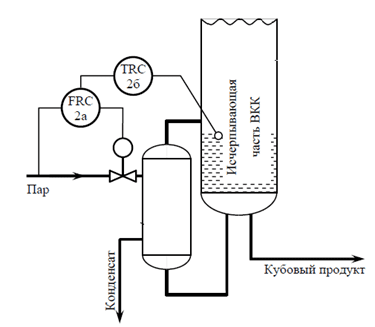
Figure 6 – Cascade control option for the temperature of the bottom residue
The above schemes improve the quality of work, but are not able to compensate for significant variations in the composition and consumption of the original mixture.
With a significant change in the composition of the initial mixture, additional control loops are introduced into the systems for regulating the composition of the distillate and the bottoms residue, usually a correction in the composition of the initial mixture (fig. 7).
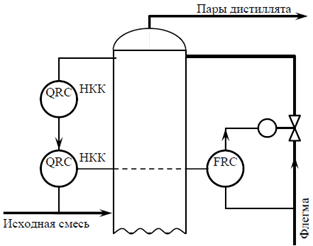
Figure 7 – Regulation of reflux consumption according to the composition of the initial mixture
In the absence of an analyzer of the composition of the initial mixture, variations in the composition can be compensated for by regulating the ratio of distillate and initial mixture consumption, which is a corrective for the reflux flow regulator (fig. 8). The ratio controller receives a correction signal from the distillate vapor composition controller[9-12].
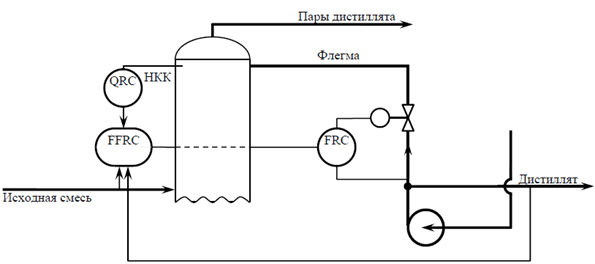
Figure 8 – Regulation taking into account changes in the composition of the initial mixture
4.3. Justification of the choice and the expected results of the selected variant of the ACS concept
All of the above options for the implementation of the regulation are not resistant to significant fluctuations in the flow rate of the original mixture, which are not a rarity in the conditions of a real object. To compensate for such disturbances will allow the introduction of a ratio controller, which corrects the flow of phlegm in depending on the temperature of the top of the column and the flow rate of the initial mixture, i.e. two-loop system (fig.9).
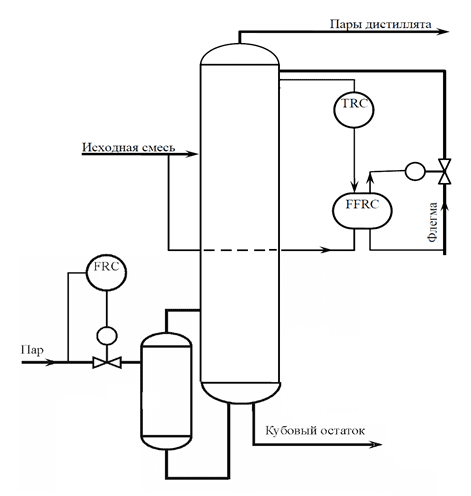
Figure 9 – Regulation using the ratio controller with temperature correction
The setting of the ratio controller is adjusted by the distillate temperature controller at the top of the column. With an increase in the flow rate of the initial mixture, the ratio controller increases phlegm consumption and vice versa. The cost ratio itself is adjusted by a temperature controller. The change in the flow rate of the steam supplied is not so a strong influence on the composition of the distillate and is generally necessary only to maintain the material balance in the column, therefore, to regulate the steam supply to boiler enough use single-loop control circuit.
For the conditions of the distillation plant, the phlegm feed control scheme is best suited using the ratio controller with correction by top temperature.
5. Synthesis of the mathematical model of the object
5.1. Synthesis of the structural diagram
The control scheme selected in the previous section corresponds to the following block diagram (fig. 10).
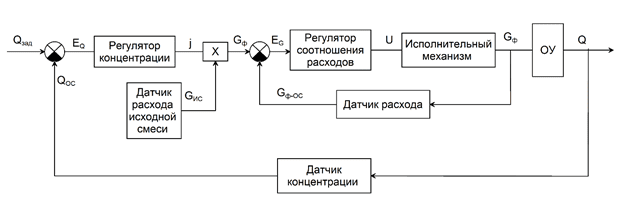
Figure 10 – Block diagram of the system
where Qзад – concentration target, %;
Qос – concentration value from the feedback sensor, %;
EQ – concentration mismatch, %;
j – consumption ratio;
GИС – initial mixture consumption, m3/h;
Gф – reflux consumption, m3/h;
EG – phlegm disagreement, m3/h;
Gф-ОС – reflux flow rate from the feedback sensor, m3/h;
U – control action (valve opening), %/s;
Q – output concentration of the product.
As can be seen from the diagram, the required concentration value is fed to the input, which must be maintained, then the mismatch between the specified the concentration value and the actual concentration measured by a special sensor, after which the mismatch goes to the concentration regulator, which calculates the ratio of costs phlegmy and the initial mixture, able to provide the desired concentration. After the necessary reflux consumption has been calculated, it is compared with the actual reflux consumption for the current moment, the mismatch of reflux consumption is calculated and fed to the flow ratio controller, which generates a control action on the actuator (valve).
5.2. Math model
To simulate the mass transfer processes inside the column, it is necessary to analyze the process on each of the plates of the column (fig.11). N – number of plates, f – number of feed tray, Vi – steam flow through i-th plate, Li – liquid flow through i-th plate, Gf, Gd, Gw – volumetric costs of the feed mixture, distillate and residue, respectively, xi and yi – the content of low-boiling fraction in the liquid and vapor phase, respectively. The distribution of the above parameters on the plates of the column is shown in fig. 11.
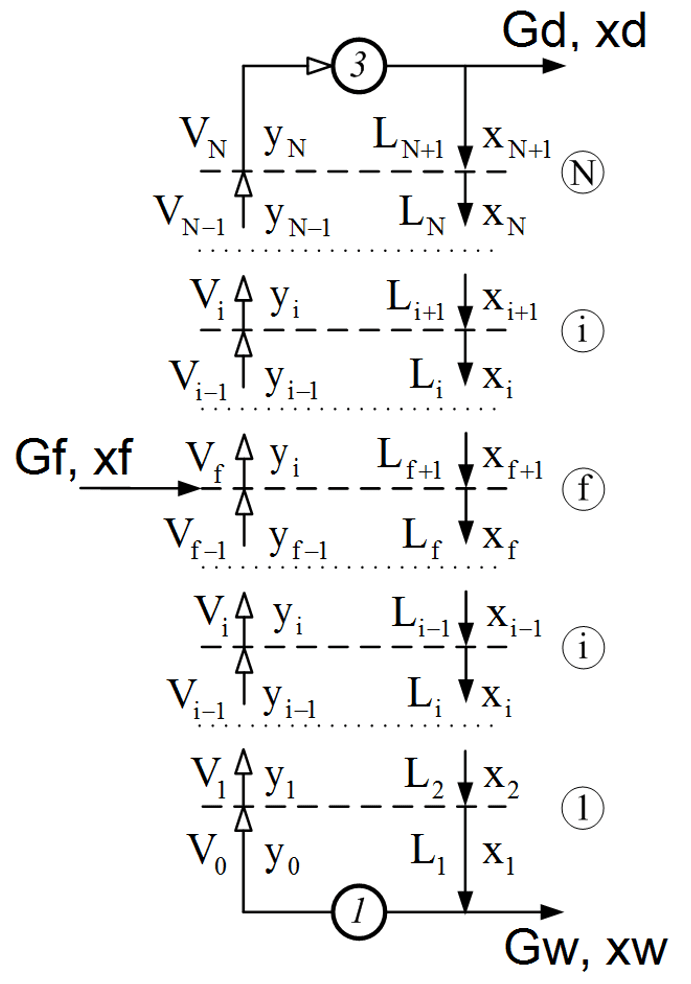
Figure 11 – The distribution of process parameters across the plates of the column
Basic equations of material balance in a column[10-14]:
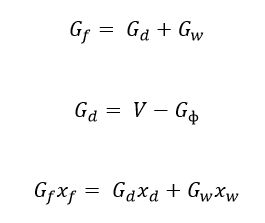
To build a mathematical model, we adopt the following assumptions:
- the steam flow in the strengthening part of the column (above the feed plate) is constant, i.e. Vi = V+Vf, i=(f+1)…N, where V is the steam flow supplied to the column from the boiler, and Vf is the vaporized portion of the mixture fed to the feed tray;
- the steam flow in the exhaustive part of the column (below the feed plate) is constant, i.e. Vi = V, i=1…f;
- the fluid flow in the strengthening part of the column (above the feed plate) is constant, i.e. Li = Gф, i=(f+1)…N;
- the fluid flow in the exhaustive part of the column (below the feed plate) is constant, i.e. Li = Gф + Lf, i=1…f, where Lf – the liquid part of the mixture supplied to the feed tray.
When making the above assumptions, the material balance equations are as follows:
- for the boiler (i=0):
where MB – amount of substance in the boiler, kmol.
- for an exhaustive part of the column (below the feed plate) (i=1...f):
where M is the layer of substance on the column plate, kmol.
- for feed tray (i=f):
- for the strengthening part of the column (above the feed plate) (i=f...N):
- for condenser (i=N+1):
where Md – amount of substance in the reflux condenser, kmol.
The concentration of a substance in a gaseous form on each plate can be found through the equilibrium equation[15]:
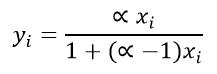
where α – relative volatility.
Thus, to simulate a column with 14 plates, you need to create a system of 16 differential equations of the first order (one equation for each of the plates and the equation for the condenser and the boiler).
To perform the calculations, it is supposed to use the Matlab application package, in particular, the Simulink graphical modeling environment.
6. Conclusion
The development of a rectification process control system is not only an engineering issue, but also a complex mathematical problem, the solution of which will allow significantly improve the quality of the output products of the process and ensure the independence of this quality from fluctuations in the input quantities, which, in turn, will raise the efficiency of the installation, reduce the financial costs of maintaining the process, and increase the cost of the target product due to its higher concentration.
To achieve these goals, the following tasks were solved:
- Technological process of rectification was analyzed. The control action was taken to change the flow of reflux supplied to the column by irrigation.
- The existing automation schemes with similar objects were analyzed, their advantages and disadvantages were identified in the context of the problem to be solved, and the study made the conclusion that the best choice for the given conditions will be the management concept through control of the ratio of reflux expenses to the initial mixture with correction for the temperature of the top of the column.
- A mathematical model of the control object was obtained, which is a system of 16 first-order differential equations.
Further research focused on the following aspects:
- Development of control based on the existing model.
- Подбор технических элементов для реализации системы управления реальным объектом.
When writing this essay master's work is not yet completed. Final Completion: May 2019. Full text of the work and materials on the topic can be obtained from the author or his manager after the specified date.
References
- Кузьменко Н. В. Учебное пособие для студентов заочной формы обучения по дисциплине «Автоматизация технологических процессов и производств» / Кузьменко Н. В. – Ангарск: АГТА, 2005. – 78 с.
- Дудникова Е. Г. Автоматическое управление в химической промышленности: учебник для вузов / Дудникова Е. Г. – Москва: Химия, 1987. – 111 с.
- Голубятников В. А. Автоматизация технологических процессов в химической промышленности. / Голубятников В. А., В. В. Шувалов – Москва. : Химия. 1985. – 212 с.
- Бондарь А.Г. Математическое моделирование в химической технологии / Бондарь А.Г. – Киев: «Вища школа», 1973. – 274 с.
- Исакович Р.Я. Aвтоматизация производственных процессов нефтяной и газовой промышленности. / Исакович Р.Я., Логинов В.И., Попадько В.Е. – Москва: Недра, 1983. – 324 с.
- Холоднов В.А. Математическое моделирование и оптимизация химико-технологических процессов : практ. руководство. / Холоднов В.А., Дьяконов В.П. – СПб.: Профессионал, 2003. – 312 с.
- Vu Trieu Minh Modeling and Control of Distillation Column in a Petroleum Process / Vu Trieu Minh, Ahmad Majdi Abdul Rani // Mathematical Problems in Engineering. – Tronoh, Malaysia – 2009. – P. 4-5.
- Денисенко В.В. Компьютерное управление технологическим процессом, експериментом, оборудованием. / Денисенко В.В. – М.: Горячая линия – Телеком, 2009. – 608 с.
- Филлипс Ч. Системы управления с обратной связью. / Филлипс Ч., Харбор Р. – М.: Лаборатория Базовых Знаний, 2001. – 616 с.
- Денисенко В. В. ПИД-регуляторы вопросы реализации часть 2/ Денисенко В. В. – СТА. – 2008. – № 1. – С. 86-99.
- Денисенко В. В. ПИД-регуляторы: принципы построения и модификации / Денисенко В. В. – СТА. – 2007. – № 1. – С. 77-88.
- Лукас В. А. Теория автоматического управления: Учебник для вузов – 2-е издание./ Лукас В. А. – М: Недра, 1990. – 416 с.
- Дорф Р. Современные системы управления / Р. Дорф, Р. Бишоп. Пер. с англ Б. И. Копылова. – М.:Лаборатория Базовых Знаний, 2002. – 832 с.
- Перельмутер В.М. Пакеты расширения MATLAB. Control System Toolbox & Robust Control Toolbox / Перельмутер В.М. – М.: СОЛОН-ПРЕСС, 2008. – 224 с.
- Дудников Е. Г. Автоматическое управление в химической промышленности / Дудников Е. Г. – М.: Химия, 1987. – 368 с.