Зміст
- Вступ
- 1. Актуальність теми
- 2. Мета і завдання дослідження, плановані результати
- 3. Аналіз процесу ректифікації
- 4. Розробка концепції системи автоматичного керування
- 4.1. Аналіз існуючих систем автоматичного керування об'єктом і обгрунтування необхідності удосконалення системи
- 4.2. Опис, оцінка переваг і недоліків розроблених альтернативних вариантів концепції системи керування
- 4.3. Обгрунтування вибору та очікувані результати вибраного варіанту концепції системи керування
- 5. Синтез математичної моделі об'єкта
- 5.1. Розробка структурної схеми
- 5.2. Математична модель об'єкта
- 6. Висновки
- Список джерел
Вступ
Ректифікація є одним з найважливіших процесів в хімичній промисловості. Її мета полягає в розділенні суміші компонентів з різніми температурами кипіння на окремі фракції. Рушійна сила ректифікації – відмінність фактичної концентрації компонентів в паровій фазі від рівноважної для даного складу рідкої фази. Парожідкостна система прагне до досягнення рівноважного стану. При контакті з рідиною пар збагачується легколетючими (низькокиплячими) компонентами, а рідина – важколетючими(висококиплячими) компонентами. Рідина і пар рухаються протитечією: пар – вгору, рідина – вниз. Через певний час з верху колони безперервно стікає рідина, максимально багата легкозакипаючої компонентом, а з низу – висококиплячих.
Регулювання процесу дистиляції представляє інтерес з кількох причин. З наукової точки зору це складний багатовимірний процес, до управління яким можна застосовувати різні техніки. З промислової ж точки зору більш якісне регулювання дозволить максимізувати прибутки при більш раціональному витрачанні сировини, більш високій енергоефективності тощо.
1. Актуальність теми
На даний момент проблема автоматизації технологічного процесу полягає в тому, що настройка регуляторів часто відбувається емпіричним шляхом, що в умовах реального об'єкта пов'язане з втратами сировини і великим часом введення системи в експлуатацію.
Розвиток обчислювальної техніки останніх років зробив можливим застосування більш досконалого математичного апарату для опису процесів, що протікають в ректифікаційних колонах, з метою формування керуючих впливів, які забезпечують найкращі характеристики вихідного продукту і максимальну компенсацію різних збурень.
Система автоматичного управління дозволить оптимізувати процеси підтримки основних технологічних параметрів процесу ректифікації і збільшити ефективність установки в якості і кількості продукції.
2. Мета і завдання дослідження, плановані результати
Підтримка концентрації дистиляту на заданому рівні – головне завдання системи управління. Даний параметр вимірюється або безпосередньо (датчиком концентрації), або опосередковано (датчиком температури), і впливає на витрату флегми, що подається в колону.
Також необхідно забезпечити управління потоком флегми, що повертається в колону. Це досягається подачею на регулятор витрати сигналу або з датчика температури верху колони, або з датчика концентрації, в залежності від обраної схеми.
Крім того, потрібна сигналізація в разі виходу із заданих меж тиску в колоні (вимірюється датчиком тиску у верхній частині колони), температури верху колони, витрати вихідної суміші. При тиску в колоні вище допустимого, а також у разі припинення подачі вихідної суміші в колону, повинні спрацювати автоматичні пристрої захисту, які відключають установку. При цьому потоки дистиляту, залишку і теплоносіїв перекриваються, а потік флегми відкривається.
З метою якомога повнішого контролю процесу і аналізу продуктивності системи необхідно забезпечити збір, відображення і зберігання даних з датчиків температури верху колони, витрати живильної суміші, витрати пари в кип'ятильник.
Очікуваний економічний і соціальний ефект від введення системи – мінімізація витрати пари і холодоагенту, підвищення концентрації корисної речовини в вихідному продукті при тому ж обсязі вихідної суміші, а також зведення до мінімуму впливу людського фактора на технологічний процес.
3. Аналіз процесу ректифікації
Ректифікація – розділення рідких сумішей на практично чисті компоненти, що відрізняються температурами кипіння, шляхом багаторазових випарів рідини і конденсації пари[1].
Як об'єкт управління є ректифікаційна установка для поділу бінарної суміші, що складається з тарельчатої ректифікаційної колони, виносного кип'ятильника, дефлегматора і збірки конденсату (рис.1).
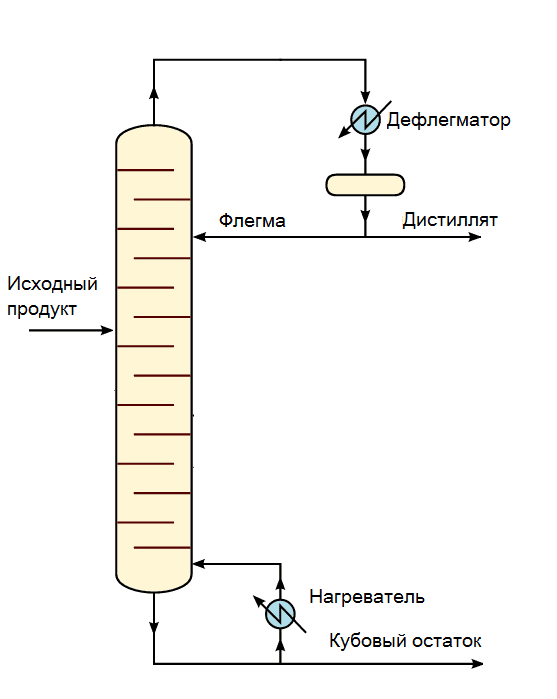
Рисунок 1 – Схема ректифікаційної установки
С физической точки зрения ректификация возможна, поскольку изначально концентрация отдельных компонентов смеси в паровой и жидкой фазах отличается, но система стремится к равновесию – одинаковому давлению, температуре и концентрации всех веществ в каждой фазе. При контакте с жидкостью пар обогащается легколетучими (низкокипящими) компонентами, в свою очередь, жидкость – труднолетучими (высококипящими) (рис.2). Одновременно с обогащением происходит обмен теплом.
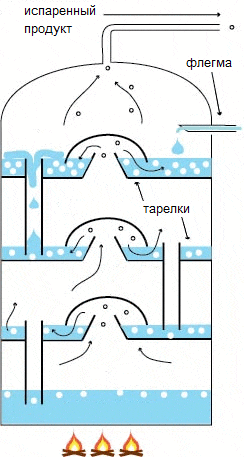
Рисунок 2 – Ілюстрація процесів всередині колони (анимація: 4 кадру, 10 циклів півтерення, 134 килобайт)
З фізичної точки зору ректифікація можлива, оскільки спочатку концентрація окремих компонентів суміші в паровій і рідкій фазах відрізняється, але система прагне до рівноваги – однаковому тиску, температури і концентрації всіх речовин в кожній фазі. При контакті з рідиною пар збагачується легколетючим (низькокиплячим) компонентом, в свою чергу, рідина – труднолетючем (висококиплячим) (рис.2). Одночасно із збагаченням відбувається обмін теплом[1-3].
Показниками ефективності процесу є склади вихідних потоків (кубова рідина, дистилят), що містять цільовий продукт. На чистоту цих цільових продуктів впливає ряд збурюючих впливів процесу – склад, параметри тепло- і холодоагентів, тиск в колоні і інші величини.
Стосовно до процесу ректифікації підтримання заданого складу цільового потоку є метою управління процесом. Склад потоку, що не містить цільового продукту, – кубового залишку – може змінюватися внаслідок зміни складу і швидкості подачі вихідного напруги потоку.
Основні керуючі впливи – витрати флегми в колону і теплоносія в кип'ятильник. Причому зміна витрати флегми відносно швидко призводить до зміни складу дистиляту і одночасно з великим запізненням і в значно меншій мірі – до зміни складу кубового залишку. Зміна ж витрати пари, що гріє, призводить в основному до зміни складу кубового залишку; склад флегми при цьому змінюється набагато слабкіше[4].
Збурюючими впливами є зміни витрати вихідної суміші, параметри вихідної суміші, тиск в колоні.
Підсумувавши все вищесказане і представивши об'єкт у вигляді «чорного ящика», можна отримати наступну схему аналізу ТП ректифікації з точки зору основних матеріальних потоків і їх інформаційних змінних (рис. 3).
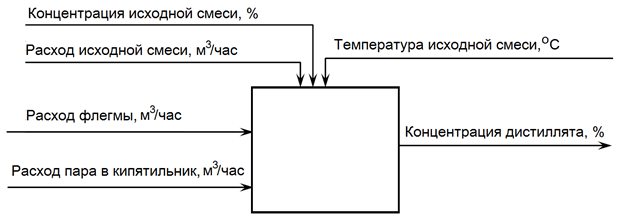
Рисунок 3 – Схема аналізу ТП ректифікації з точки зору основних матеріальних потоків і їх інформаційних змінних
4. Розробка концепції системи автоматичного керування
4.1. Аналіз існуючих систем автоматичного керування об'єктом і обгрунтування необхідності удосконалення системи
Найбільш проста система управління ректифікаційної установкою зображена на рис. 4.
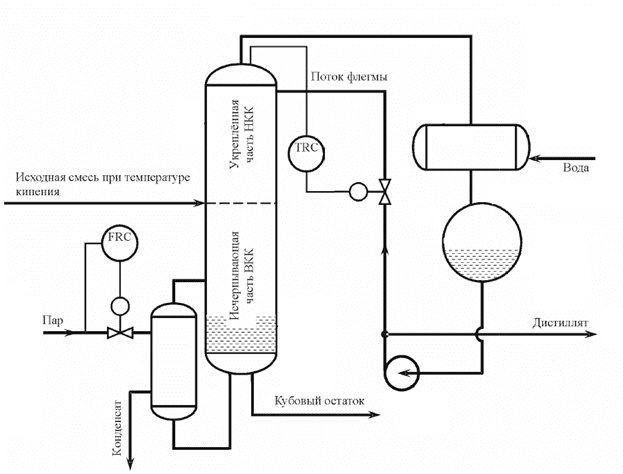
Рисунок 4 – Схема стабілізації процесу ректифікації
На рис. 4 здійснюється стабілізація температури верху колони і витрати подаваного в кип'ятильник пара за допомогою локальних одноконтурних систем регулювання. Ці системи пов'язані між собою через процес і забезпечують дотримання матеріального і теплового балансів установки[5].
Основний параметр колони – склад парів вгорі колони. Склад дистиляту регулюють зміною подачі флегми в колону. Регулюючий орган встановлюють на лінії подачі флегми в колону. Згідно правил розділу фаз при поділі бінарної суміші, якщо тиск в колоні постійний, склад дистиляту і температура верху колони однозначно пов'язані. Тому в контурі джерелом інформації є температура верху в колони. Якщо число тарілок велике, то для поліпшення якості регулювання температуру вимірюють на так званій контрольній тарілці, де температура більш чутлива до подачі флегми і де забезпечується менше запізнювання при зміні складу вихідної суміші[6].
Подібна схема з декількох одноконтурних систем має велике запізнення і впливи значно змінюють режим роботи об'єкта[7]. Ці недоліки базової системи обумовлюють необхідність створення більш досконалої системи.
4.2. Опис, оцінка переваг і недоліків розроблених альтернативних вариантів концепції системи керування
Для підвищення якості поділу суміші вводять коригувальні контури.
Одна з можливих схем реалізації показана на рис.5. Тут подача флегми в колону регулюється трехконтурною системою регулювання. Регулятор складу 1в дає сигнал корекції на регулятор температури 1б, а цей, в свою чергу, коригує завдання регулятору витрати 1а[1].

Рисунок 5 – Варіант каскадного регулювання за складом дистиляту
Якщо кубовий залишок теж є цільовим продуктом, то для забезпечення його чистоти застосовують систему регулювання витрати пари в кип'ятильник (2а) з корекцією по температурі в отгонній (вичерпної) частини колони(рис.6)[8].
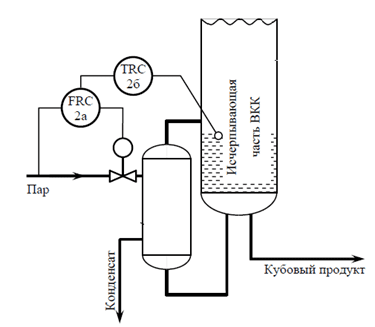
Рисунок 6 – Варіант каскадного регулювання по температурі кубового залишку
Наведені вище схеми покращують якість роботи, але не здатні компенсувати значні коливання складу та витрати вихідної суміші.
При значній зміні складу вихідної суміші в систему регулювання складу дистиляту і кубового залишку вводять додаткові контура регулювання, зазвичай корекцію за складом вихідної суміші (рис.7).
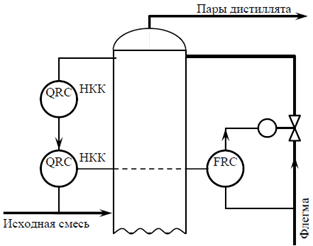
Рисунок 7 – Регулювання витрати флегми по складу вихідної суміші
При відсутності аналізатора складу вихідної суміші коливання складу можна компенсувати регулятором співвідношення витрат дистиляту і вихідної суміші, який є коригувальним для регулятора витрати флегми (рис.8). Регулятор співвідношення отримує сигнал корекції від регулятора складу парів дистиляту[9-12].
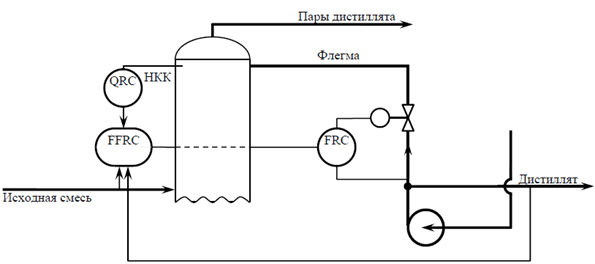
Рисунок 8 – Регулювання з урахуванням зміни складу вихідної суміші
4.3. Обгрунтування вибору та очікувані результати вибраного варіанту концепції системи керування
Всі наведені вище варіанти реалізації регулювання не є стійкими до значних коливань витрати вихідної суміші, які не є рідкістю в умовах реального об'єкта. Компенсувати подібні збурення дозволить введення регулятора співвідношення, коригуючого потік флегми залежно від температури верху колони і витрати вихідної суміші, тобто двухконтурной системи (рис.9).
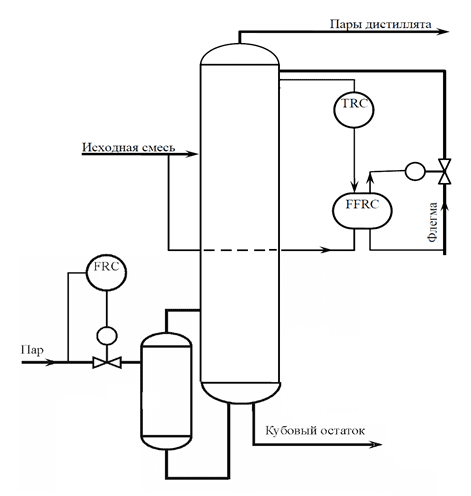
Рисунок 9 – Регулювання з використанням регулятора співвідношення з корекцією по температурі
Завдання регулятору співвідношення коригують регулятором температури дистиляту вгорі колони. При збільшенні витрати вихідної суміші регулятор співвідношення збільшує витрату флегми і навпаки. Саме співвідношення витрат коригується регулятором температури. Зміна ж витрати подаваного пара надає не настільки сильний вплив на склад дистиляту і в цілому необхідна лише для підтримки матеріального балансу в колоні, отже, для регулювання подачі пари в кип'ятильник досить використання одноконтурной схеми управління.
Для умов ректифікованого цеху найкращим чином підходить схема регулювання подачі флегми з застосуванням регулятора співвідношення з корекцією по температурі верху.
5. Синтез математичної моделі об'єкта
5.1. Розробка структурної схеми
Обрана в попередньому розділі схема управління відповідає наступній структурній схемі (рис.10).
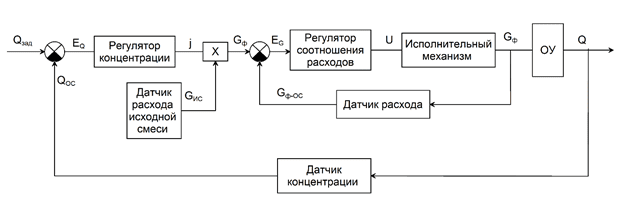
Рисунок 10 – Структурна схема системи
где Qзад – задане значення концентрації, %;
Qос – значення концентрації з датчика зворотного зв'язку, %;
EQ – неузгодженість концентрацій, %;
j – коефіцієнт співвідношення витрат;
GИС – витрата вихідної суміші, м3/ч;
Gф – витрата флегми, м3/ч;
EG – неузгодженість витрат флегми, м3/ч;
Gф-ОС – значення витрати флегми з датчика зворотного зв'язку, м3/ч;
U – керуючий вплив (відкриття клапана), %/с;
Q – вихідне значення концентрації продукту.
Як видно зі схеми, на вхід подається необхідне значення концентрації, яку необхідно підтримувати, потім обчислюється неузгодженість між заданим значенням концентрації і фактичною концентрацією, яка вимірюється спеціальним датчиком, після чого неузгодженість надходить на регулятор концентрації, який обчислює співвідношення витрат флегми і вихідної суміші, здатне забезпечити необхідну концентрацію. Після того як була обчислена необхідна витрата флегми, він порівнюється з фактичними витратами флегми на поточний момент, обчислюється неузгодженість витрати флегми і подається на регулятор співвідношення витрат, який генерує керуючий вплив на виконавчий механізм (клапан).
5.2. Математична модель об'єкта
Щоб змоделювати массообменниє процеси всередині колони, необхідно проаналізувати процес на кожній з тарілок колони (рис.11). N – кількість тарілок, f – номер тарілки живлення, Vi – потік пари через i-ту тарілку, Li – потік рідини, що стікає через i-ту тарілку, Gf, Gd, Gw – об'ємні витрати живильної суміші, дистиляту і кубового залишку відповідно, xi и yi – зміст низкокиплячої фракції в рідкій і паровій фазі відповідно. Розподіл перерахованих вище параметрів по тарілках колони зображено на рис. 11.
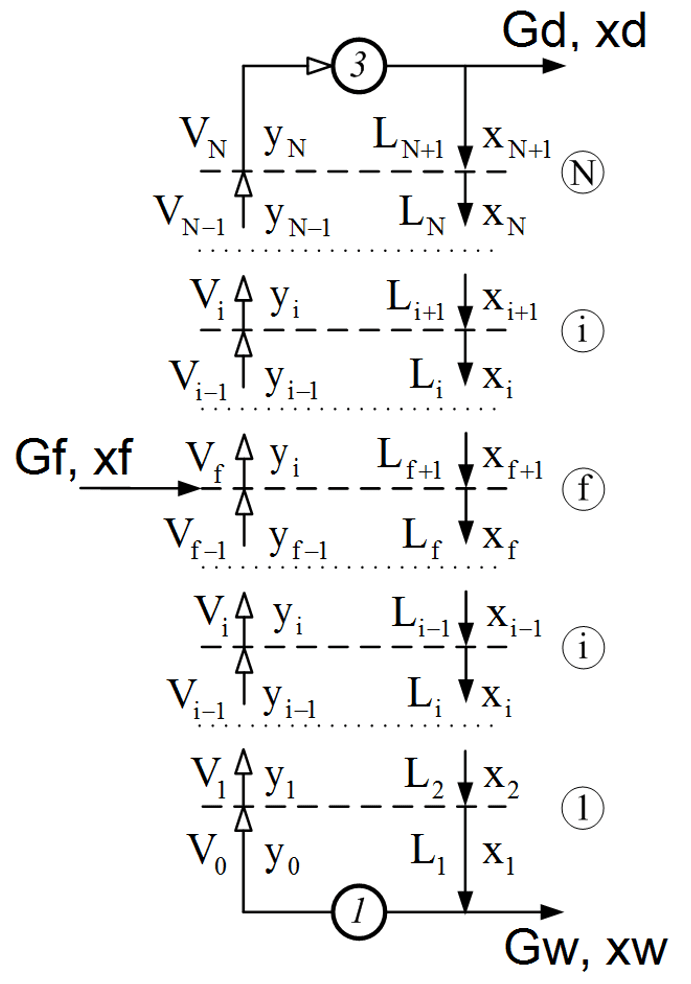
Рисунок 11 – Розподіл параметрів процесу по тарілках колони
Основні рівняння матеріального балансу в колоні[10-14]:
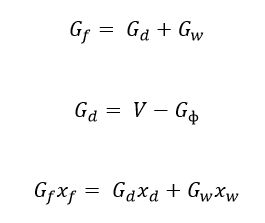
Для побудови математичної моделі приймемо такі припущення:
- потік пара в зміцнює частини колони (вище тарілки живлення) постійний, тобто Vi = V+Vf, i=(f+1)…N, де V – потік пари, що подається в колону з кип'ятильника, а Vf – випаровуванна частина суміші, яка подається на тарілку живлення;
- потік пара в вичерпній частині колони (нижче тарілки живлення) постійний, тобто Vi = V, i=1…f;
- потік рідини в зміцнюючій частині колони (вище тарілки живлення) постійний, тобто Li = Gф, i=(f+1)…N;
- потік рідини в вичерпній частини колони (нижче тарілки живлення) постійний, тобто Li = Gф + Lf, i=1…f, де Lf – рідка частина суміші, яка подається на тарілку живлення.
При прийнятті вищевикладених припущень рівняння матеріального балансу мають такий вигляд:
- для куба колони(i=0):
де MB – кількість речовини в кубі колони, кмоль.
- для вичерпної частини колони (нижче тарілки живлення) (i=1...f):
де M – шар речовини на тарілці колони, кмоль.
- для тарілки живлення (i=f):
- для зміцнюючій частини колони (вище тарілки живлення) (i=f...N):
- для дефлегматора (i=N+1):
де Md – кількість речовини в дефлегматорі, кмоль.
Концентрація речовини в газоподібному вигляді на кожній тарілці може бути знайдена через рівняння рівноваги[15]:
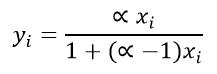
де α – відносна летючість.
Таким чином, для моделювання колони з 14 тарілками необхідно скласти систему з 16 диференціальних рівнянь першого порядку (по одному рівнянню для кожної з тарілок і за рівнянням для дефлегматора і куба колони).
Для виконання обчислень передбачається використовувати пакет прикладних програм Matlab, зокрема графічне середовище моделювання Simulink.
6. Висновки
Розробка системи управління технологічним процесом ректифікації є не тільки інженерним питанням, але і складною математичною задачею, рішення якої дозволить значно поліпшити якість вихідних продуктів процесу і забезпечити незалежність цієї якості від коливань вхідних величин, що, в свою чергу, підніме ефективність установки, зменшить фінансові витрати на підтримку процесу, і збільшить вартість цільового продукту за рахунок більш високої його концентрації.
Для досягнення поставлених цілей були вирішені наступні завдання:
- Був проаналізований технологічний процес ректифікації. Керуючим впливом було прийнято зміна витрати флегми, що подається в колону збільшити обсяги виробництва.
- Були проаналізовані існуючі схеми автоматизації подібними об'єктами, виявлені їх переваги та недоліки в контексті розв'язуваної задачі і за підсумками дослідження був зроблений висновок, що найкращим вибором для заданих умов буде концепція управління через контроль співвідношення витрат флегми і вихідної суміші з корекцією по температурі верху колони.
- Була отримана математична модель об'єкта управління, що є системою з 16 диференціальних рівнянь першого порядку.
Подальші дослідження спрямовані на наступні аспекти:
- Розробка закону управління на основі наявної моделі.
- Підбір технічних елементів для реалізації системи управління реальним об'єктом.
При написанні даного реферату магістерська робота ще не завершена. Остаточне завершення: травень 2019 року. Повний текст роботи і матеріали по темі можуть бути отримані у автора або його керівника після зазначеної дати.
Список джерел
- Кузьменко Н. В. Учебное пособие для студентов заочной формы обучения по дисциплине «Автоматизация технологических процессов и производств» / Кузьменко Н. В. – Ангарск: АГТА, 2005. – 78 с.
- Дудникова Е. Г. Автоматическое управление в химической промышленности: учебник для вузов / Дудникова Е. Г. – Москва: Химия, 1987. – 111 с.
- Голубятников В. А. Автоматизация технологических процессов в химической промышленности. / Голубятников В. А., В. В. Шувалов – Москва. : Химия. 1985. – 212 с.
- Бондарь А.Г. Математическое моделирование в химической технологии / Бондарь А.Г. – Киев: «Вища школа», 1973. – 274 с.
- Исакович Р.Я. Aвтоматизация производственных процессов нефтяной и газовой промышленности. / Исакович Р.Я., Логинов В.И., Попадько В.Е. – Москва: Недра, 1983. – 324 с.
- Холоднов В.А. Математическое моделирование и оптимизация химико-технологических процессов : практ. руководство. / Холоднов В.А., Дьяконов В.П. – СПб.: Профессионал, 2003. – 312 с.
- Vu Trieu Minh Modeling and Control of Distillation Column in a Petroleum Process / Vu Trieu Minh, Ahmad Majdi Abdul Rani // Mathematical Problems in Engineering. – Tronoh, Malaysia – 2009. – P. 4-5.
- Денисенко В.В. Компьютерное управление технологическим процессом, експериментом, оборудованием. / Денисенко В.В. – М.: Горячая линия – Телеком, 2009. – 608 с.
- Филлипс Ч. Системы управления с обратной связью. / Филлипс Ч., Харбор Р. – М.: Лаборатория Базовых Знаний, 2001. – 616 с.
- Денисенко В. В. ПИД-регуляторы вопросы реализации часть 2/ Денисенко В. В. – СТА. – 2008. – № 1. – С. 86-99.
- Денисенко В. В. ПИД-регуляторы: принципы построения и модификации / Денисенко В. В. – СТА. – 2007. – № 1. – С. 77-88.
- Лукас В. А. Теория автоматического управления: Учебник для вузов – 2-е издание./ Лукас В. А. – М: Недра, 1990. – 416 с.
- Дорф Р. Современные системы управления / Р. Дорф, Р. Бишоп. Пер. с англ Б. И. Копылова. – М.:Лаборатория Базовых Знаний, 2002. – 832 с.
- Перельмутер В.М. Пакеты расширения MATLAB. Control System Toolbox & Robust Control Toolbox / Перельмутер В.М. – М.: СОЛОН-ПРЕСС, 2008. – 224 с.
- Дудников Е. Г. Автоматическое управление в химической промышленности / Дудников Е. Г. – М.: Химия, 1987. – 368 с.