Abstract
Content
- Introduction
- 1. Theme urgency
- 2. Goal and tasks of the research
- 3. An approach to the unification of synthesis of Moore FSM on FPGA
- Conclusion
- References
Introduction
Rolling thick sheets is characterized by the highest consumption of metal per tonne of good. The expenditure ratio is up to 1.25. The consumption of metal goes mainly to the side and end trimmings, which is determined by the inaccuracy of the shape of the sheet rolls in the plan. Reducing the consumption of metal during the pro-skating rink of thick sheets is an urgent problem.
Also, technological progress and competition pose difficult tasks for the manufacturer in terms of ensuring the quality of products for specific operating conditions.
The market for thick sheets with rolled edges is rather free due to the complexity of the process, but it is also promising and effective for its development.
1. Theme urgency
Metal consumption is mainly on the side and end trim, which is determined by the inaccuracy of the shape of the sheet rolls in the plan. Reducing the consumption of metal during the rolling of thick sheets is an urgent problem.
The greatest reduction in lateral cutting by reducing the width of the bulge and the average raznosherinnost in the batch of sheets is obtained when they are pro- duced with compressed edges along the entire length. Also, rolling sheets with pressed edges, allows to obtain a finished sheet without internal stresses on the edges and the associated defects. In addition, an important parameter is the weldability, the quality of which significantly increases when using this technology.
2. Goal and tasks of the research
When analyzing ways to control the shape of rolls in the plan, it was found that the most effective way to maintain the rectangular shape of the roll is to use vertical rolls. The known technologies of rolling sheets with crimped edges do not allow rolling sheets with a thickness of less than 20-25 mm.
The task of the research is the development of the technology of rolling thick sheets with a thickness of less than 25 mm with crimped edges. It is proposed to use a variable thickness reduction method along the length of the roll (Fig. 1), which provides parallel side edges of the finished roll, therefore, compression in the vertical stand installed before the finishing stand.
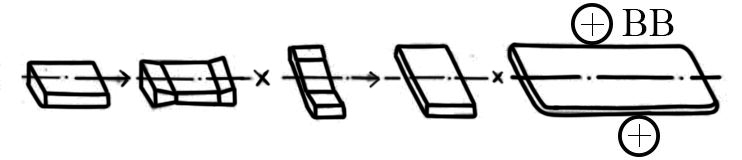
Figure 1 - Formation of parallel side edges of the roll
3. An approach to the unification of synthesis of Moore FSM on FPGA
There is a method of rolling thick sheets of ingots, according to which the breakdown of width is produced in stages. The number of stages is chosen from the value of the total stretching ratio for the breakdown of width μΣ.
The exhaust ratio at each stage does not exceed 1.4 - 1.6. Between the stages, the roll is turned over by 90 ° and rolled into cages with vertical rolls and in cages with horizontal rolls < p>
The disadvantage of this method is that the coefficients of the hood when splitting the width of the stages chosen without taking into account the size of the convexity of the width and the possibility of its compression along the entire length of the roll in vertical rolls.
One of the methods for rolling thick sheets with crimped edges is the method proposed by the Volgograd Metallurgical Plant "Red October" in 1994.
This method includes a phased breakdown of the width and longitudinal rolling in vertical rolls, characterized in that the drawing ratios at the stages of breaking the width, except for the last, are set depending on the total drawing ratio and the ratio of width to slab thickness.
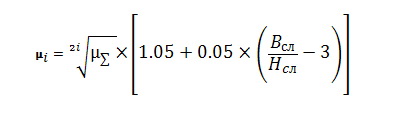
Where: μi, μΣ - step-by-step and total drawing ratios with breakdown of width;
B, H - is the width and thickness of the slab;
i - is the stage number.
Between the stages produce two longitudinal reversing passages in the vertical rolls with the maximum allowable reductions and a longitudinal curving passage in the horizontal rolls.
This technology of rolling thick sheets with crimped edges with a phased breakdown of the width provides an increase in the accuracy and stability of the width of 1.3 - 2 times, and consequently, reduces the consumption of metal per tonne suitable. Also, this technology does not allow to roll long and wide sheets, less than 50 mm thick, due to the unstable gripping and bending of the expanded ends.
In the line of the plate mill 5500 of the Kawasaki Seitetsu plant in Mizushima, Japan, a stand with vertical rolls, barrels of which have calibrated and smooth sections, was installed to produce thick sheets with uncut edges. The plate rolling technology provides for rolling according to the following scheme: ВВ-ГВ-ГВ-ВВ-ГВ-ГВ, where ВВ is rolling in vertical rolls with compression in width and ГВ - rolling in horizontal rolls with compression in thickness. Finishing pass in the explosive is performed with the clamping of the side edges of the upper and lower special rollers.
A distinctive feature of the vertical stand design is the presence of a roll displacement device, with which a roll set can be chamfering and usual in width on one set of rolls having calibrated and smooth barrel sections.
With the finishing passes in the vertical stand, the center of the roll is held by the central roller, and the side edges - by the pressure rollers. Thus, a three-point metal clamping is obtained, which makes it possible to eliminate the loss of stability when rolling wide and relatively thin sheets.
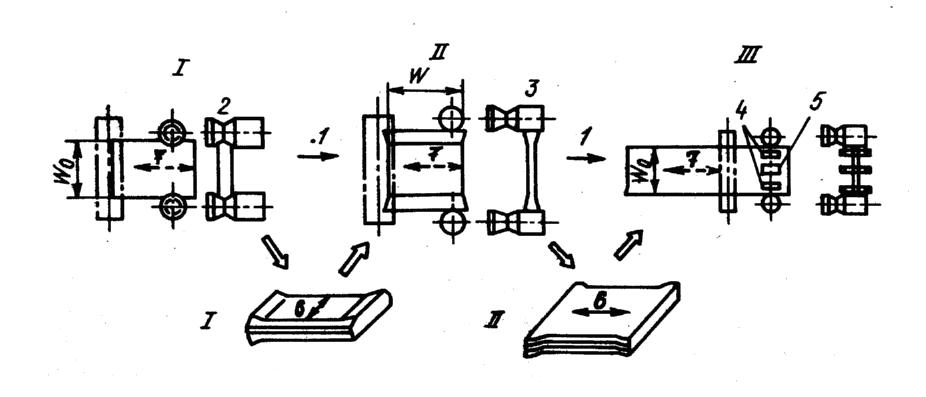
Figure 2 - Scheme of rolling sheets using a vertical stand: Ⅰ – roughing pass in calibrated vertical rolls and quart stand; Ⅱ – breakdown of width by width in smooth sections of explosives and rolling in a quarto stand; Ⅲ – finishing pass smooth areas with clamping the side edges and rolling in the quarto stand; 1 – turning; 2 – calibrated roll part; 3 – smooth roll; 4 – pinch rollers at the edges; 5 – central roller; 6,7 – the direction of rolling in explosives and gv respectively.
The size error in width over the entire length of the sheet reaches 10 mm. In addition, for a significant part of the assortment, the cutting operation of the side edges of the sheet is excluded. All of these benefits have allowed to reduce waste in the side trim to 16% of the previous value and increase the yield.
Conclusion
1. In the analysis of the loss of roll rectangular shape in the plan when rolling thick sheets, many reasons were identified. The consumption of metal goes mainly to the side and end trimmings, which is determined by the inaccuracy of the shape of the sheet rolls in the plan. Reducing the consumption of metal when rolling thick sheets is an actual problem.
2. When analyzing ways to control the shape of rolls in the plan, it was found that the most effective way to preserve the rectangular shape of roll is the use of vertical rolls.
3. Known technologies for rolling sheets with crimped edges do not allow rolling sheets with a thickness of less than 20-25 mm. On the basis of this, the research task was chosen, namely the development of the technology of rolling thick sheets with crimped edges, ensuring the expansion of the range of sheets in thickness.
References
- Коновалов, Ю.В. Металлургия: в 3 кн./ Ю.В.Коновалов, А.А.Минаев - М.: Донецк: ГВУЗ «ДонНТУ», 2012.
Кн.3: Теоретические основы обработки металлов давлением. Сорта-мент прокатной продукции. Производство заготовок, листопрокатное производство. – 496 стр..
- Коновалов, Ю.В. Повышение точности прокатки листов и полос / Ю.В. Ко-новалов, Е.А. Руденко, П.C. Гринчук и др. - М.: Металлургия, 1987. - 144с.
- Артманова, Е.А. Производство толстых листов высокого качества / Е.А. Артманова // Министерство черной металлургии СССР. - 1987. - №3. - С. 1-24.
- Усачева, А.Н. Обработка металла давлением и термическая обработка / А.Н. Усачева // Министерство черной металлургии СССР. - 1988. - №9. - С. 1-4.
- Пат. 2019324 Россия, МКИ В 21 В 1/38. Способ прокатки толстых листов с обжатыми кромками / Н.Ш. Орджоникидзе, А.Н. Рыбкин, Е.А, Руденко и др.; Волгоградский металлургический завод «Красный Октябрь» -т.- №5034739; заявл.03.03.92; опубл.15.09.94, Бюл.№17.
- Повышение качества толстых листов / Ф.Е.Долженков, Ю.В. Коновалов, В.Г.Носов и др. - М.: Металлургия, 1984. - 247 с.
- Повышение точности листового проката / И.М.Меерович, А.И.Герцев, B.C.Горелик, Э.Я.Классен. - М.: Металлургия, 1969.-264с