Реферат по теме выпускной работы
Содержание
- Введение
- 1. Прямые способы диагностики
- 2. Обратные методы
- 3. Комплексные модели
- Выводы
- Список источников
Введение
Нагревая стальные слитки в высокотемпературных печах перед термической обработкой или обработкой давлением (преимущественно при многократном нагреве) способствует существенным потерям металла в окалину. Пределы потерь составляют 0,5-2%, а в особых случаях могут доходить до 8%. Проблема высокотемпературного окисления и обезуглероживания стали исследуется уже более ста лет такими учеными как Бенар, Энгель, Казанцев и др. В их научных работах изучался процесс образования гетерогенной окалины на поверхности железа. Пласт окалины состоял из: вюстита, магнетита, гематита.
Осуществление вычислительной оценки потерь металла в окалину, которая зависит от конструктивных и технологических параметров нагрева, является важной научно-технической задачей. Её можно решить при помощи стандартных вычислений или воспользоваться методом диагностики. Целью моей работы является изучение ранее известных подходов к диагностике процесса образования окалины на поверхности металла, при его высокотемпературной обработке. Чтобы доказать важность использования предложенного метода диагностики и привести точные показатели о потерях металла в окалину, мы прибегнем к исследованию стандартных вычислительных подходов и проблем, которые могут возникнуть при их эксплуатации.
1. Прямые способы диагностики
Упрощенный способ диагностики обязан проверять изменение во времени характерных температур, которые определяют нынешнее значение константы окалинообразования. Для нахождения значений температур на наружной и внутренней поверхностях слоя окалины, а также распределения температуры по толщине окалины и металла, зачастую прибегают к решению дифференциального уравнения нестационарной теплопроводности. Зачастую, температурным сопротивление слоя окалины и температурным перепадом по ее толщине пренебрегают. Задача нахождения температурного состояния металла решается отдельно, а все значения температуры поверхности металла, которые были определены на каждом временном шаге, применяют для поиска значений констант окалинообразования. Проектируемый режиме тепловой обработки металла, изменение во времени температуры печи периодического действия или температурный профиль печи непрерывного действия задаются исследователем. При работе в режиме реального времени значения характерных температур печи измеряются соответствующими датчиками. Заданные или измеренные значения температур используются для формирования граничных условий теплообмена на поверхности заготовок.
Примером разработки, реализующей прямой метод диагностики, является прогнозная модель для изучения теплового состояния металла при его высокотемпературном нагреве, учитывающая динамику процессов окисления поверхности металла. Эта прогнозная модель создана на базе дифференциального уравнения нестационарной теплопроводности при задании граничных условий теплообмена с использованием основных закономерностей лучистого теплообмена и дифференциального уравнения первого порядка, описывающего темп нарастания окалины. Задача рассматривается в одномерной постановке. При этом слой окалины рассматривается как дополнительное внешнее термическое сопротивление при решении внешней задачи теплообмена. Скорость вычислений при помощи созданной модели значительно превышает темп реального времени, что делает возможным ее использование в качестве компонента систем прогнозного управления. Тестирование созданной модели для решения задач с учетом и без учета влияния слоя окалины, а также с учетом и без учета тепловыделения по реакции окисления железа позволили получить результаты, хорошо согласующиеся с логикой процесса и практическими данными. Уточнение информации о необходимом времени протекания процесса и температурном поле металла при учете влияния окалинообразования составляет порядка 5%.
Таким образом, данная модель сочетает в себе возможность учета всех аспектов окалинообразования без потери быстродействия и в связи с этим может быть нацелена на параллельное прогнозирование теплового состояния металла и его потерь с окалиной. Если же говорить только об исследовании теплового состояния металла, то подтверждена допустимость общепринятого подхода, согласно которому при создании математических моделей тепловой обработки металла, а в особенности быстродействующих моделей, предназначенных для интеграции в алгоритмы АСУ ТП, влияние слоя окалины исключается из рассмотрения. Показано, что в процессе окисления имеется два фактора, влияющих на параметры нагрева металла: дополнительное термическое сопротивление, удлиняющее нагрев, и тепловыделение при окислении металла, ускоряющее нагрев. Влияние первого фактора оказывается сильнее. В результате удлинение нагрева при прочих равных условиях составляет порядка 5%. Еще одним примером диагностики процесса окалинообразования по прямому методу является прогнозная математическая модель для исследования температурного состояния сляба при его нагреве в методической печи, учитывающая окалинообразование. Как и в предыдущем случае задача рассмотрена в одномерной постановке, математическая формулировка представлена уравнением нестационарной теплопроводности и дифференциальным уравнением, описывающем нарастание окалины по параболическому закону. Особенностью является то, что область, для которой решается конечно-разностная задача теплопроводности, представлена как металлом, так и окалиной. При этом учтены подвижные границы металл-окалина. Для двухстороннего нагрева сляба на каждом временном шаге задаются условия теплообмена на четырех границах: окалина-продукты сгорания (верх сляба), стык верхнего слоя окалины с металлом, стык нижнего слоя окалины с металлом, окалина – продукты сгорания (низ сляба).
2. Обратные методы
Примером системы диагностики процесса окалинообразования, реализующей обратный метод, является разработка, идея которой базируется на рассмотрении баланса кислорода в камере и газоходах печи. При этом учитываются следующие источники поступления кислорода в печную систему: вентиляторный воздух, подаваемый на горелочные устройства; атмосферный воздух, подсасываемый в камеру печи; атмосферный воздух, подсасываемый в газоходы. Принято, что кислород расходуется только лишь по реакциям горения и на окисление и обезуглероживание металла. Расход кислорода, и соответственно воздуха, на протекание процесса горения и остаточное содержание кислорода в продуктах сгорания определены при помощи стандартных подходов, используемых в теории горения топлива.
Схема расстановки чувствительных элементов для реализации создаваемого компонента диагностики процессов окисления металла на примере печи периодического действия приведена на рис.2. Для организации замеров концентрации кислорода необходимо на основании предварительной экспериментальной проработки в каждом конкретном случае так выбрать точки замера, чтобы результаты измерения в них соответствовали среднерасходным концентрациям кислорода.
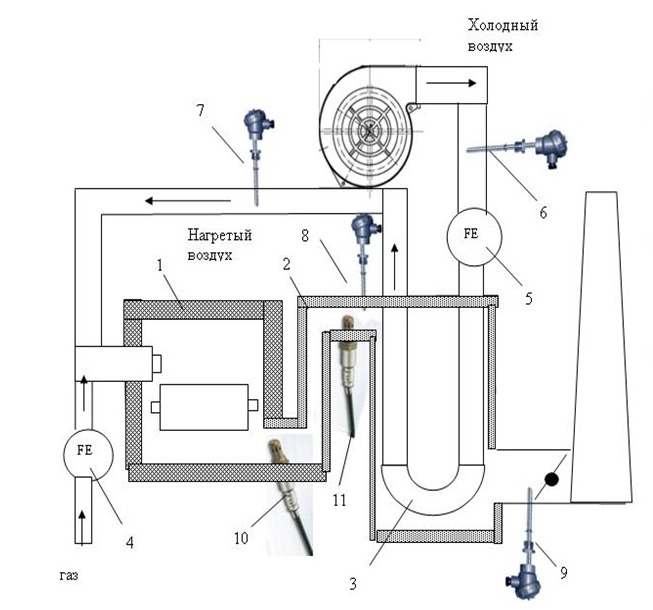
Рисунок 1 – Схема сбора информации от первичных датчиков для системы диагностики процессов окисления в печи периодического действия 1 - камера печи; 2 - участок газохода от камеры печи до рекуператора; 3 - рекуператор; 4 - расходомер по топливу; 5 - расходомер по воздуху; 6 - термопара для измерения температуры холодного воздуха; 7 - термопара для измерения температуры нагретого воздуха; 8 - термопара для измерения температуры продуктов сгорания до рекуператора; 9 - термопара для измерения температуры продуктов сгорания после рекуператора; 10 - датчик концентрации кислорода в районе пламенного окна; 11 - датчик концентрации кислорода перед рекуператором
Первое уравнение системы представляет собой выражение из теплового баланса идеализированного рекуператора, не имеющего потерь теплоты, а также перетоков воздуха и продуктов сгорания. Смысл этого уравнения заключается в том, что количество тепла, воспринятое воздухом, численно равно количеству тепла, отданному продуктами сгорания. Из данного теплового баланса определяется неизвестное значение полного расхода продуктов сгорания через рекуператор. Это значение формируется за счет соединения продуктов сгорания с воздухом, подсосанным в камеру печи и по газоходам до рекуператора и исключения объема кислорода, израсходованного на окисление металла. Второе уравнение получено из рассмотрения баланса кислорода в районе пламенного окна, а третье – из баланса кислорода перед рекуператором. Решение системы уравнений необходимо производить для исследуемого момента времени на основании текущих значений величин-аргументов. Для использования созданного компонента в отрыве от АСУ на ПК, находящейся под управлением обычной ОС, данная система элементарно решается при помощи стандартных вычислительных пакетов. Для режима работы в рамках АСУ составляется программный модуль, реализующий стандартные способы решения систем уравнений. Для рассматриваемой системы более удобными оказываются стандартные численные методы решения систем уравнений.
Важным элементом обратных способов диагностики является измерение концентрации кислорода на различных участках печной системы. Циркониевые анализаторы кислорода предназначены для непрерывного измерения концентрации кислорода в отработанных газах процессов горения в промышленных котельных или печах, и идеально подходят для мониторинга и управления этими процессами. Для рассматриваемых условий нагрева металла в высокотемпературных пламенных печах, по мнению авторов, подходит анализатор кислорода и несгоревших компонентов газа, а именно комплектация, поскольку данная модель анализатора является пламенезащищенной. Анализатор кислорода и несгоревших компонентов газа, с его прочной конструкцией, демонстрирующим стабильные характеристики сенсором, электронными компонентами и пакетом программного обеспечения, является одним из наиболее надёжных и адаптируемых датчиков кислорода/горючих материалов на рынке. Вся информация от анализатора постоянно обновляется и передается оператору или техническому специалисту. Данный прибор имеет высокую коррозионную стойкость и температуроустойчивость, а также повышенную чувствительность и минимизированную погрешность измерений.
3. Комплексные модели
Из сказанного выше очевидно, что целесообразным является использование в рамках одной системы диагностики приемов, относящихся как к прямым, там и обратным методам.
В качестве примера комплексной системы диагностики можно привести разработку, представленную в работе. В ней авторы при помощи системы диагностики исследуют возможность уменьшения окалинообразования путем применения системы управления режимом работы печи для воздействия на факторы, способствующие образованию окалины. С одной стороны есть все признаки прямого метода – для контроля используется система управления, реализованная по принципу наблюдатель-предсказатель, включающая в себя регистрацию фактического значения температуры печной атмосферы; моделирование технологического процесса, результатом которого является определение температуры нагреваемого изделия с учетом фактических значений технологических параметров; управление технологическим процессом, предполагающее достижение заданного теплового состояния металла при минимизации потерь с окалиной
С другой стоны, производится непрерывный замер концентрации кислорода и построение моментального баланса отходящих газов. С помощью текущих значений концентрации кислорода можно прогнозировать моментальные значения скорости реакций окисления. А построение баланса отходящих газов для всего печного пространства дает возможность определения количества окислившегося металла обратным способом.
Таким образом, в рамках разработки оператор получает сообщение в виде обратной связи о влиянии производственных условий на окалинообразование. В результате появляется возможность (например, в случае вынужденного простоя или изменения производительности прокатного стана) минимизировать образование окалины.
Выводы
Обоснована целесообразность использования методов диагностики процессов образования окалины при высокотемпературном нагреве стальных заготовок в пламенных печах, поскольку выполнение предварительных расчетов при помощи упрощенных уравнений окалинообразования не позволяет в полной мере учесть изменение значений параметров, оказывающих существенное влияние на окалинообразование. Применение соответствующих систем диагностики упрощает поиск параметров процесса, позволяющих уменьшить потери металла с окалиной. Показано, что система диагностики процессов окалинообразования может быть реализована на базе прямых, обратных или комплексных методов. Прямые методы представлены прогнозной математической моделью, выполняющей расчет теплового состояния металла и образования окалины в режиме реального времени, в зависимости от текущих результатов изменения характерных технологических параметров. В наиболее простом случае учитываются только параметры внешнего теплообмена. В наиболее полной постановке учитывается также парциальное давление кислорода.
Обратные методы основаны на рассмотрении баланса кислорода в камере и газоходах печи и определении текущих значений расхода кислорода, переходящего в окалину. Перспективными можно считать системы диагностики, одновременно прогнозирующие потери металла в окалину по прямому и обратному методам, поскольку они предоставляют более достоверные результаты, имеют резервы самоподстройки и позволяет уточнять значения констант скорости для реакций окалинообразования или практических констант окалинообразования.
Список источников
- Диагностика процесса окисления металла в пламенных печах/ А.Б. Бирюков, Е.В. Новикова, Т.Г. Олешкевич, Л.Н. Петренко// Металлургические печи. – 2014. – Вып.6 (21). – С.3-11.
- Диагностика процесса образования окалины при высокотемпературном нагреве стальной заготовки/ А.Б. Бирюков, Ю.Л. Курбатов, Е.В. Новикова, А.А. Заика // Черная металлургия. – 2017. – №11(1415). – С.65-72.
- Современные подходы к диагностике процессов тепловой обработки металла в печах/ А.Б. Бирюков, С.М. Сафьянц, А.А. Иванова, Е.Н. Андриенко Черная металлургия. Бюллетень научно-технической и экономической информации – 2015. – №1. – С.50-55.
- Математическое моделирование процессов тепловой обработки металла в печах с учетом окалинообразования/ А.Б. Бирюков, С.И. Гинкул, П.А. Гнитиев, Т.Г. Олешкевич// Сталь. – 2016. – №8. – С.85-90.
- Мастрюков, Б.С. Теплофизика металлургических процессов / Б.С. Мастрюков, Г.С. Сборщи-ков. – М.: Металлургия, 1996. – 268 с.