Реферат за темою випускної роботи
Зміст
- Вступ
- 1. Актуальність теми
- 2. Мета і завдання дослідження
- 3. Моделювання процесу штампування колісних заготовок на пресах силою 20 МН, 50МН, 100МН
- Висновки
- Список джерел
Вступ
Актуальним для сучасної теорії колесопрокатного виробництва є створення методів проектування технології деформування точних по масі (відміну заготовок по масі до 1%) заготовок коліс, які б забезпечували високу точність прогнозу формозміни металу і силових параметрів процесів штампування і прокатки заготовок. Рішення даної проблеми вимагає зміни постановки відповідних крайових задач та способів їх реалізації відповідно до технічних і технологічними особливостями виробництва коліс на конкретній прессопрокатной лінії.
Постановка задачі моделювання. У даній роботі виконана постановка задачі моделювання багатоперехідних процесу деформування заготовок коліс з подальшою її реалізацією в системі DEFORM 3D.
1. Актуальність темы
Актуальним напрямом вдосконалення технології деформування заготовок коліс на прессопрокатной лінії є створення технологічних схем і режимів деформації металу, що дозволяють зменшити асиметрію штампованих колісних заготовок і, як наслідок, - знизити ексцентричність прокатанних коліс.
Обладнання прессопрокатной лінії, введене в експлуатацію понад 40 років тому з одного боку дозволяє забезпечувати високу продуктивність технологічного процесу, а, з іншого, - морально застаріло, наслідком чого є нестабільність розмірів штампованно-катаних коліс і підвищена ремонтне обточування.
2. Мета і завдання дослідження
Робота присвячена моделюванню процесу штампування заготовки по новому способу штампування з частково сформованими ободом і маточиною на заготівельному пресі.
Недоліком існуючої технології є незадовільна центрування заготовки перед її формуванням в штампах преса 100 МН. Існуючий на пресі центрователь вимагає постійного підстроювання в процесі роботи, що виконують далеко не завжди, тому що для цього необхідно зупиняти прокат. В результаті цього при високому темпі прокатки виходить велика кількість прокатаних коліс з нестабільними розмірами обода і, як наслідок, - підвищена ремонтна обточування.
Перевага нової технології: отримана заготівка буде самоцентроваться в нижньому штампі преса 100МН ще до початку деформації по сформованої посадкової поверхні в зоні маточини.
Застосування запропонованої технології дозволить стабілізувати розміри колісних заготовок і, відповідно, прокатанних з них коліс.
Для вивчення особливостей розглянутої технології необхідно виконати в системі DEFORM 3D кінечно-елементне моделювання процесу осадки-разгонки заготовок.
3. Моделювання процесу штампування колісних заготовок на пресах силою 20 МН, 50МН, 100МН
Попередня осадка на пресі силою 20 МН проводиться з метою зменшення висоти і збільшення площі поперечного перерізу заготовок. Осадку застосовують для поліпшення структури і механічних властивостей металу заготовок, а також для зменшення нерівномірності властивостей в осьовому і радіальному напрямках.
В процесі осадки видаляється окалина з бічних поверхонь заготовок, а також залишилася після гідрозбиву окалина з торцевих поверхонь. Прес силою 20 МН - гідравлічний вертикальний чотириколонний з архитравом і встановленої на фундаменті станиною. Між станиною і архитравом розташована траверса, яка переміщається по колонах преса. На станину преса і опору встановлена ??плита, по напрямних якої переміщується стіл преса. Плита з одного боку упирається в зуб станини, а з іншого підпирається двома гідроциліндрами, що знаходяться під постійним тиском.
Опускання траверси здійснюється плунжером робочого циліндра, підйом траверси - двома підйомними циліндрами, розміщеними в припливах архітрава. До траверсі і столу кріпляться осадові плити.
Робочий цикл преса складається з опускання траверси до зіткнення із заготівлею, робочого ходу - осадки заготовки і підйому траверси в початкове положення. Опускання траверси починається після подачі маніпулятором заготовки на стіл преса під час його повернення в початкове положення. Встановлена величина осадки забезпечується системою автоматичного управління траверсою. Для контролю висоти осаджені заготовки прес обладнаний покажчиком ходу траверси у вигляді дискового циферблату з стрілкою. Різнотовщинність осаджених заготовок не повинна перевищувати 2 мм.[1]
Перед подачею заготовки на стіл преса за допомогою дозаторів здійснюється нанесення технологічної підсипання на середину нижньої обжимной плити з метою попередження запрессовки окалини, невідокремив після гідрозбиву. Вона спрацьовує на верхню торцеву поверхню заготовки.
Після осадки заготівля забирається маніпулятором з робочої зони преса силою 20 МН. Для попередження розігріву і зменшення зносу обтискні плити після видалення заготовки охолоджуються водою. Окалина з нижньої плити також видаляється водою.
По рольгангу заготовка подається на кантувач, встановленому перед пресом силою 50 МН, і кантується на 180°. Для більш повного видалення вторинної окалини торцеві поверхні заготовки перед кантователем і після нього піддаються очищенню металевими щітками, після чого заготовка по рольгангу подається до пресу силою 50 МН. Заготовка на пресі 50МН перед розгоном - центрируется (шляхом підняття кільця). Операціі деформації на пресі силою 50 МН виробляються з метою регламентованого розподілу металу між периферійної і центральної частинами заготовки.[2]
Прес силою 50 МН - гідравлічний вертикальний чотириколонний складається з нерухомих поперечок - станини і архітрава, з'єднаних між собою колонами. З преса силою 50 МН заготовку прибирають і перекладивателем переміщається на відвідний рольганг і транспортується до формувальних пресу силою 100 МН. При цьому вона піддається очищення від окалини металевими щітками.
Деформація заготовки на пресі силою 100 МН проводиться з метою отримання отформованной заготовки з остаточними розмірами маточини і прилеглої до неї частини диска, а також підготовки обода і прилеглої до нього частини диска для подальшої прокатки на колесо-прокатному стані.
Прес силою 100 МН - гідравлічний вертикальний чотириколонним має дві нерухомі поперечки - станину і архітрав, з'єднані між собою чотирма колонами. У архітраві встановлений робочий циліндр преса, а також два підйомних диференціальних і два врівноважують циліндра. Плунжери цих циліндрів закріплені на рухомій траверсі. До траверсі кріпиться підштамповою плита, в якій встановлено верхню виштовхувач заготовки. Циліндр поршня працює спільно з підйомними циліндрами траверси.[2]
Технологічний цикл роботи преса силою 100 МН включає наступні операції: укладання заготовки на нижній формувальний штамп; центрування заготовку на штампі; опускання траверси до зіткнення верхнього штампа із заготівлею; робочий хід - формовку заготовку; підйом траверси в початкове положення; видалення отформованной заготовки за допомогою виштовхувачів з верхнього і нижнього штампа і видачу її на рольганг.
Результати моделювання. На першому етапі досліджень було виконано моделювання процесу охолодження заготовки на повітрі при її транспортуванні (час транспортування - 25с) по рольгангу від печі до осадового пресу силою 20 МН. Розподіл температур в заготівлі після її транспортування і витримки (час витримки 5С) на нижній плиті преса 20МН представлено на мал. 3.1. Середня температура металу на поверхні заготовки перед осадкою становить 1260 - 1270 °С. Вільну осадку заготовки виробляють до висоти 117-120 мм. Результати моделювання процесу осадки заготовки, представлені на мал. 3.2. Отримане значення сили опади (24,9МН) є для даного преса максимально можливим. Його досягають при тиску робочої рідини 31,4МН / м2.[3][4][5]
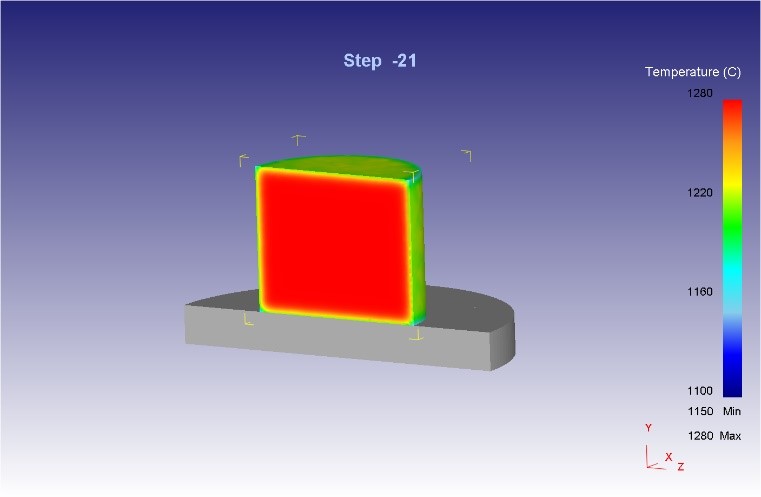
Малюнок 3.1 – Заготовка після її транспортування і витримки на нижній плиті
Після цього заготовка подається на прес силою 50 МН (час транспортування - 10 с) для осадки-разгонки в технологічному кільці. Перед пресом 50 МН заготовку кантуют на 180° для вирівнювання температури з її верхньої і нижньої сторін. На мал. 3.3 а, б представлено розподіл температури в заготівлі до і після її транспортування до пресу 50 МН, а також після витримки заготовки (час витримки - 5 с) на нижній обжимной плиті преса. Середня температура металу на поверхні заготовки перед розгоном становить 1250 - 1260°С.
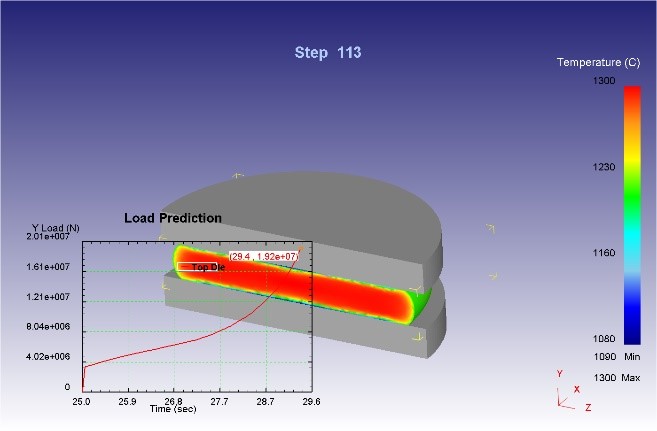
Малюнок 3.2 – Заготовка після її осадки на пресі силою 20 МН
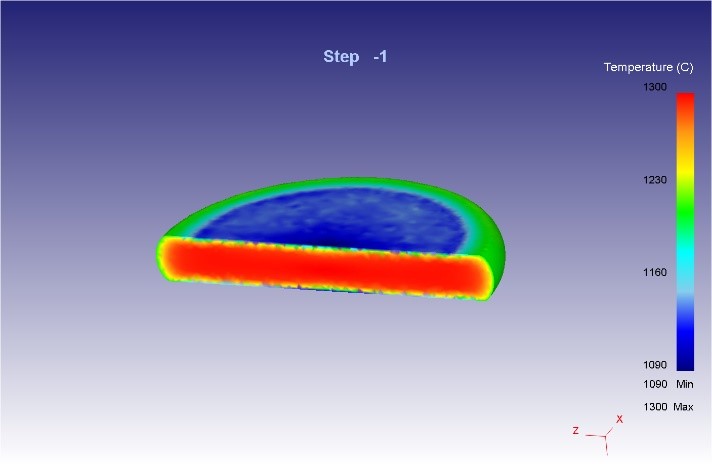
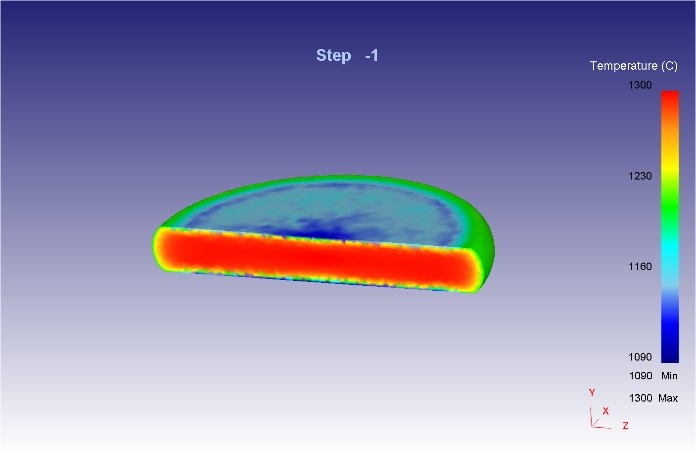
Малюнок 3.3 – Заготовка (а) до і (б) після її транспортування і витримки на нижній плиті
На наступному етапі виконують опускання траверси преса до виникнення контакту верхнього штампа із заготовкою. Результати моделювання процесу до і після розгону заготовки на пресі силою 50 МН представлені на мал. 3.4 а, б.
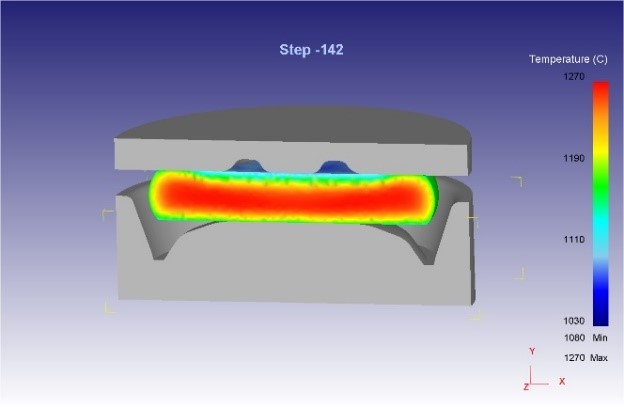
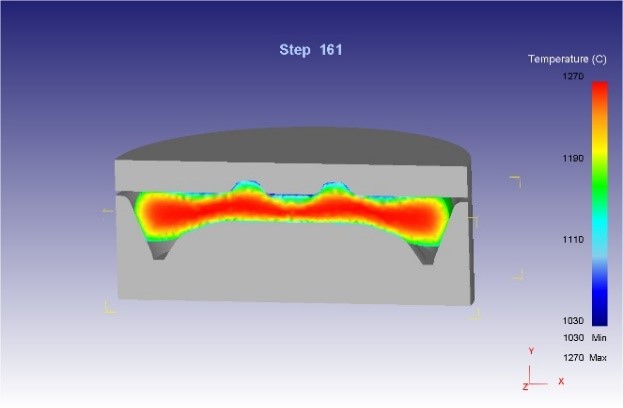
Малюнок 3.4 – Заготовка (а) до і (б) після її розгону на пресі силою 50 МН
Після розгону на пресі 50МН, заготовка передається на прес силою 100МН, де здійснюється формування. Така заготовка самоцентруется в нижньому штампі, що забезпечує стабільність процесу. На мал. 3.5 а, б, представлені результати до і після формування.
Висновки
Розроблено схему штампування колісних заготовок, що забезпечує підвищення точності і стабільності розмірів одержуваних заготовок під прокатку.
За рахунок сформованого калібру на заготівельних пресі 50МН, заготовка буде самоцентроваться в нижньому штампі формувального преса 100МН що забезпечить стабільність процесу.
Виконаний аналіз формозміни і силових параметрів процесів деформації заготовок на пресах 20МН, 50МН і 100МН показав раціональність розроблених режимів деформації.
Отримані при моделюванні значення сил штампування, температур заготовок і параметрів їх формозміни добре узгоджуються з експериментальними даними, отриманими в умовах промислового виробництва коліс діаметром 957 мм.
Список джерел
- Яковченко, А.В. Проектування профілів і калібрувань залізно-дорожніх коліс: монографія / А.В. Яковченко, Н.І. Івлєва, Р.А. Голишко. - Донецьк: ДонНТУ, 2008. - 491с.
- Яковченко А.В., Снитко С.А., Ивлева Н.И. Шляхи вдосконалення комп'ютерних програм проектування калібровок інструмента деформації для виробництва штампованнокатанихзалізничних коліс // Металл и литье Украины. - 2003. - № 6. - С. 30-35.
- Гун Г.Я. Теоретичні основи обробки металів тиском / Г.Я. Гун. - М .: Металургія, 1980. - 456 с .: іл.
- Снитко С.А. Аналіз силових і швидкісних параметрів прокатки коліс / С.А. Снитко // Наукові праці ДонНТУ. Металургія: Зб. наук. пр. – Донецьк, 2008. – Вип. 10 (141). – С. 163 – 172.
- Прогнозування і спосіб усунення освіти затискачів при формуванні колісних заготовок / Б.Г. Каплунов, В.Н. Крашевіч, М.І. Староселецкій, А.В. Белущенко // Изв. вузів Чорна підприєм-гія. - 1991. - № 1. - С. 55-56.
- Шифрін М.Ю. Резерви продуктивності і виходу придатного при прокатці коліс / М.Ю. Шифрін. - М .: Металургія, 1989. - 144 с .: іл.
- Шифрін М.Ю. Раціональний режим опади обода колісної заго-товки / М.Ю. Шифрін // Сталь. - 1993. - № 5. - С. 52-54.