Abstract
Content
- Introduction
- 1. ACTUALITY
- 2. PURPOSE AND TASKS OF RESEARCH.
- 3. TECHNOLOGICAL SCHEME OF PRODUCTION BY BANDAGE
- 4. DEVELOPMENT OF TECHNOLOGY IMPROVEMENT EVENTS
- 5. DETERMINING TOTAL REVIEWS TAKING INTO ACCOUNT EXTENSION
- Conclusions
Introduction
Currently, rolling is the main method of manufacturing ring products in technically highly developed countries. This situation is primarily associated with the complex advantages of this method. First of all, such advantages include the low cost of the resulting products, high manufacturability and flexibility of the process, versatility of technological equipment used. Products obtained in this way have a more homogeneous cross-sectional metal structure that is circumferentially oriented. The noted versatility and flexibility of the process allows to obtain products with a diameter from 100 to 8000 mm and a height from 10 to 1500 mm. Used as the initial billet ingots and rods of the same diameter are suitable for rolling a wide range of ring products. When rolling shaped products in cross-section, a minimum fleet of working rolls is used. There is a relatively low power consumption strain.
1. ACTUALITY OF WORK
Production of tires for rolling stock of railways, tires for trams and subways is carried out on the press-rolling line of the ring-dressing shop (CSC).
Master's work is aimed at creating new and improving existing technologies with the aim of energy and resource saving, as well as reducing marriage, having a rolling origin, in the production of bandages. The present determines the relevance of the research data.
2. THE GOAL AND TASKS OF THE RESEARCH
Improve the method of calculating calibrations and the technology of stamping and rolling locomotive tires taking into account the distribution of total radial and axial reductions in the rolling process, taking into account the broadening. To achieve this goal it is necessary to solve the following tasks: * to develop a new method of producing locomotive tires on one mill, normalizing the flow of metal to the ridge and ring parts of the bandage in the process of its rolling in order to improve the quality.
3. TECHNOLOGICAL SCHEME OF PRODUCTION BY BANDAGE
Technological scheme of production of ring products adopted according to the approved technological task of VNITI 1) No. TLZ -61-22-19-79 [2]. The technological process of production of tires on the press-rolling line is as follows (Figure 1):
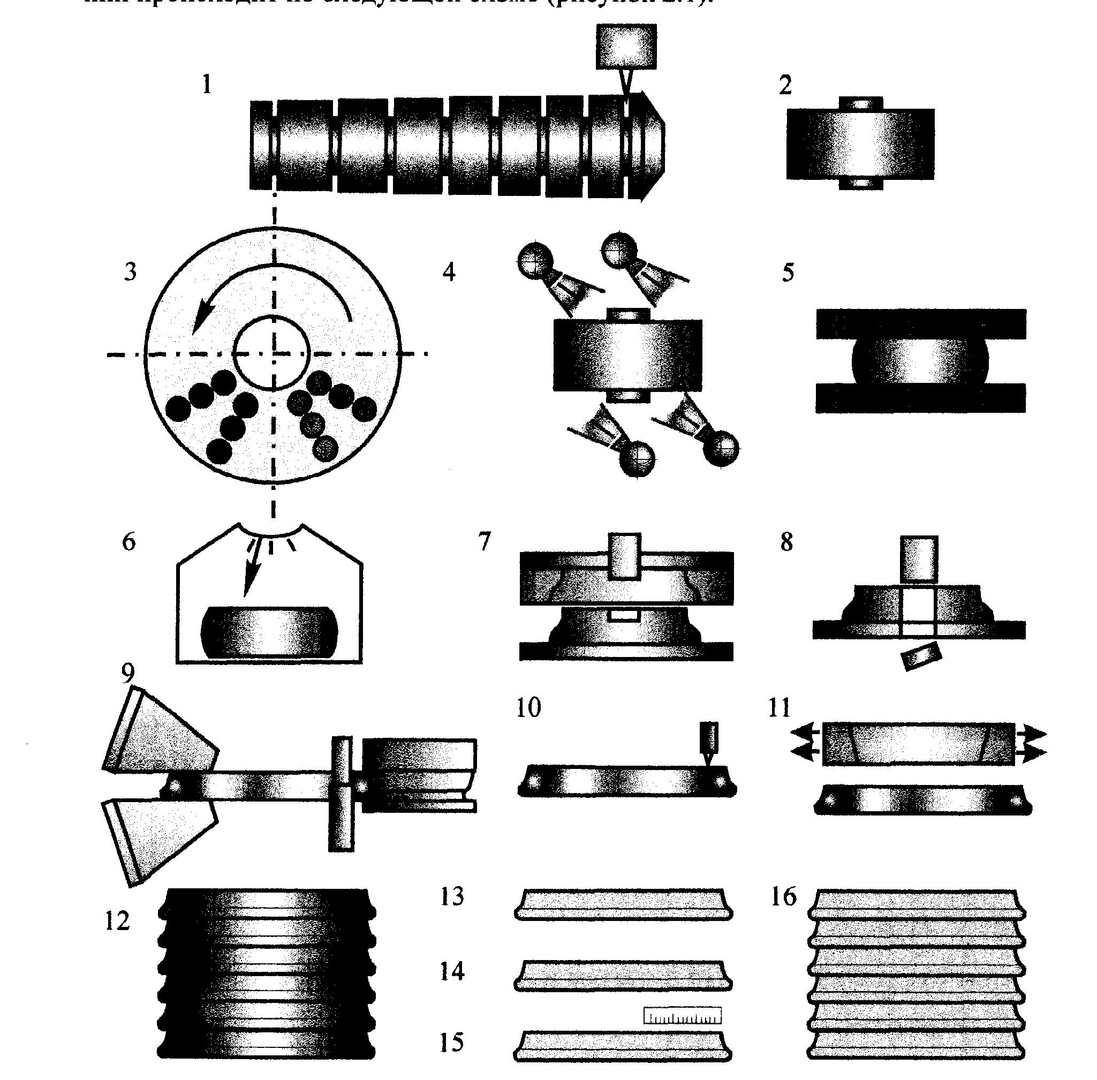
Figure 1 - Production scheme of bandages
1. The incision of ingots on the ingot-cutting mills, the breaking of notched ingots into blanks and the distribution of blanks by weight categories on an aggregate of breaking and sorting.
2. Inspection and repair of blanks.
3. Heating billets to 1250-1260 ° C in an annular heating furnace.
4. Knocking down the scale in the chamber gidroshbiva.
5. The precipitation of the workpiece on a sedimentary press force of 20MN.
6. Weighing on the scales in order to determine the mass of metal extruded during the firmware.
7. The deformation of the blanks on the billet press force 40 / 20MN and the implementation of the central recess.
8. Firmware central hole on the press force 8MN.
9. Rolling on one or two ring rolling mills.
10. Branding.
11. Press hot edit.
12. Heat treatment.
13. Unbrakable control.
14. Sampling for testing.
15. Inspection and measurements.
16. Warehousing.
4. DEVELOPMENT OF EVENTS TO IMPROVE TECHNOLOGY
The technological scheme of the production of bandages has a significant drawback - about 3-4% of the marriage of bandages due to defects in the profile at the box office. The method used to calibrate the deformation tool (mill rolls and dies) allows for the occurrence of such defects as crest failure, weighting, non-flatness, etc., which significantly increases the cost of production that is manufactured.
It is obvious that the solution of technological problems of the project should be to reduce the marriage.
To solve the problem of improving the quality of bandages proposed the following. First, the use of closed gauges on ring rolling mill (Fig. 1). The use of closed gauges creates a more favorable deformation pattern in the radial deformation zone, and contributes to rolling bandage with calculated hoods, because bandage height = caliber height, which improves the quality of bandages.
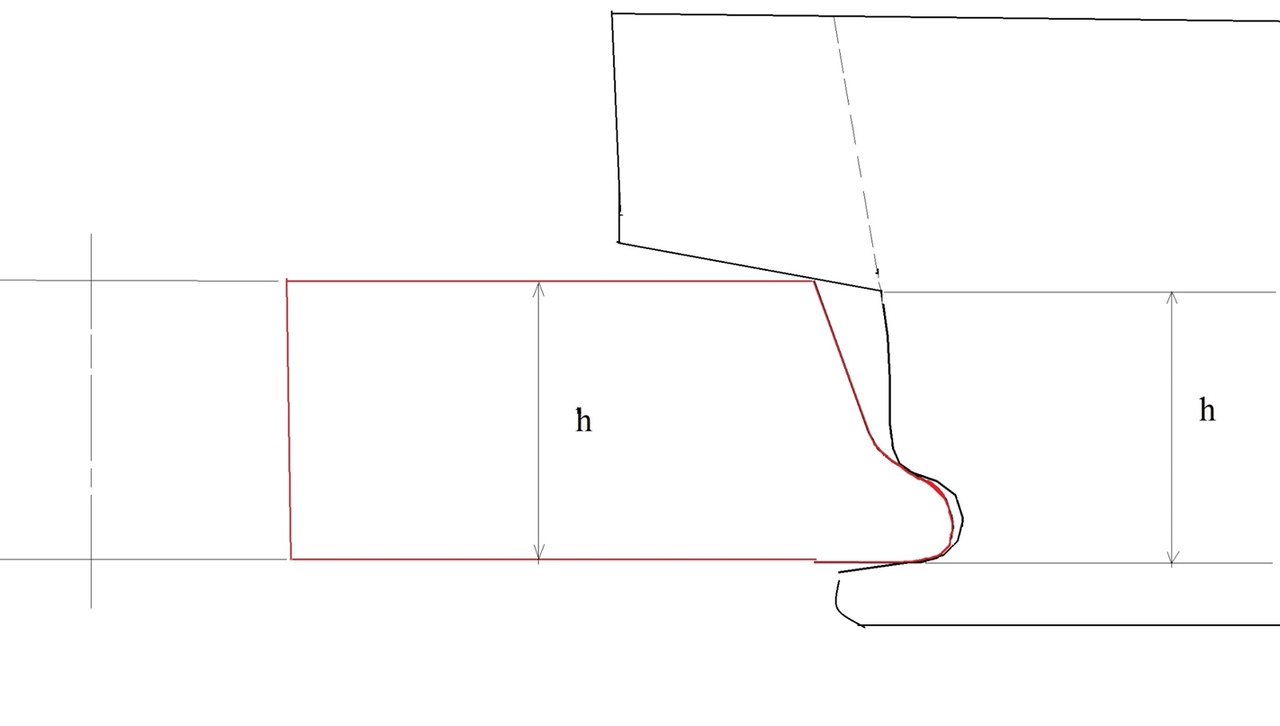
Figure 2 - Diagram of a closed caliber
Another is the use of modern methods for calculating calibration, which exclude, during rolling, the flow of metal from the ridge part to the ring part and, thus, allow you to avoid defects such as utyazhka and failure to comb.
At the first stage, the value of the total axial compression, which consists of compression of both the upper and lower inclined rolls, is determined. In practice, it is assigned within = (10? 30) mm for bandages with a mass of 100? 400 kg, respectively. Then the height of the workpiece L will be equal to L = (here s is the height of the band).
Then you need to find the dimensions of the ridge of the workpiece. They are determined from the condition of its entry into the ridge part of the caliber (Fig. 3). Sunset ridge should not lead to such a defect as sunset. In this case, the size of the ridge should be (taking into account this condition) as much as possible. Values ??a, b and h determined from the construction (Fig. 3). At the same time it is necessary to fulfill the following conditions. First, to avoid the formation of a sunset in the zone of transition of the ridge part of the bandage into the ring, it is necessary that the crest of the workpiece at the first moment of contact of the gauge did not reach the bottom of its crest part by an amount equal to 5 ? 10 mm (for bandages with a mass of 100–400 kg, respectively). Secondly, the arc at the base of the ridge of the tire formed by radius r (Fig. 3) should smoothly go into the arc at the base of the ridge of the workpiece formed by radius R. The contact point of the above contours in Figure 3 is denoted by the letter A.
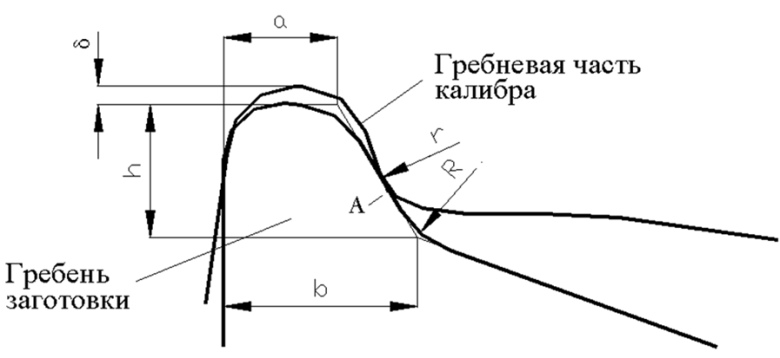
Figure 3 - Determining the size of the ridge of the workpiece
After that, the contour of the workpiece must be positioned relative to the contour of the bandage as shown in Fig.4. The skeleton points of the billet and band in the zone of the transition of the ridges to the ring parts should be on the same vertical line, separating ridge and ring parts of the bandage and blanks. p>
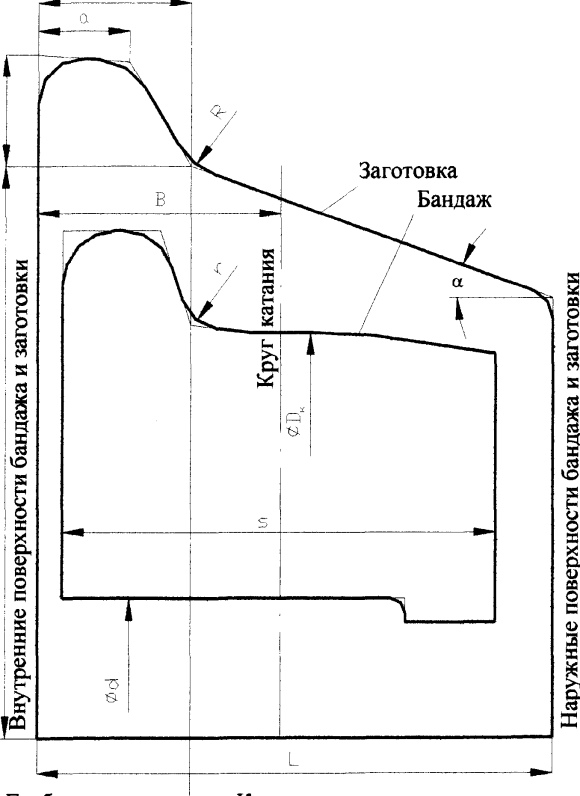
Figure 4 - Placement of the contours of the workpiece and bandage
The maximum thickness of the ring part of the workpiece H (see Fig. 3) is found from the condition of equality of masses of the ridge parts of the workpiece and the bandage.

where is the mass of the ridge part of the workpiece; m is the mass of the bandage; - mass of the annular part of the bandage; coefficient in brackets denote. Technological parameters of the process, which are normalized by this method, in particular, radial axial compression, we find from the condition of separate rolling of the ridge part of the band from the ridge part of the billet and, accordingly, the annular part of the band from the annular part of the billet. The physical essence of the coefficient k = (1.0? 1.03) in the expression (1.1), is precisely that that the mass of the ridge part of the workpiece, from which the ridge part of the bandage rolls should not be less than the last.
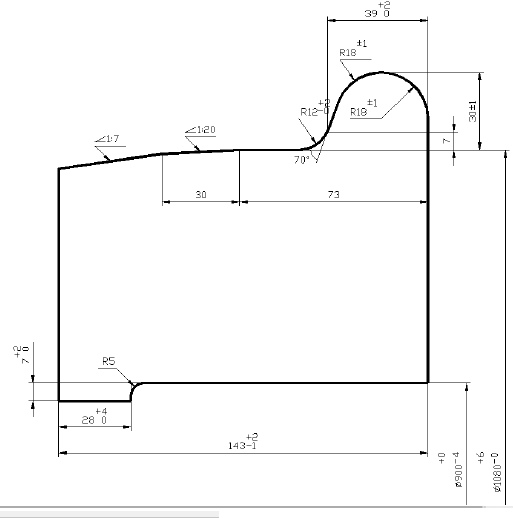
Figure 4 (a) - Drawing of a finished machined locomotive brace.
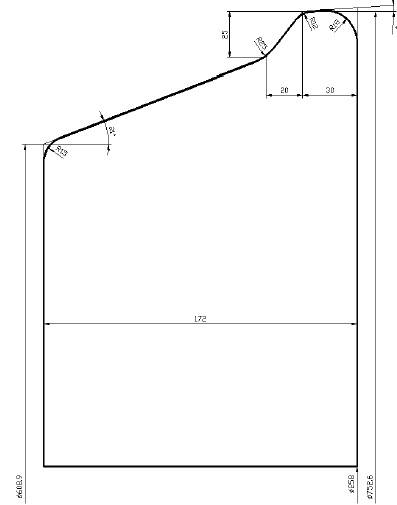
Figure 4 (b) - Drawing of the workpiece received by force on the press.
DETERMINATION OF TOTAL REJECTIONS TAKING INTO ACCOUNT EXTENSION
Incorrect determination of the height and thickness of the workpiece and, accordingly, total axial and radial reductions during rolling of ring products is the cause of the defects of the finished product and, first of all, utyazhka on the side and end surfaces of the annular product. Therefore it is important to determine the required ratio as between total radial and axial compresses, and this ratio on each turn of the ring product in the process of rolling ..
An important condition for defect-free rolling is the absence of braces. The weighting on the surfaces of the ring product is formed if the flow of metal into the hood (a, respectively, and to the growth of the diameter) along different parts of the profile occurs with unequal intensity. Therefore, the condition of defect-free rolling rings can be written in the form
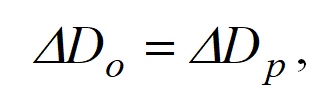
In fig. 3 shows an intermediate cross section of the annular article. Suppose that it is obtained as a result of crimping the workpiece only in the axial direction. At the same time, its diameter increased by an amount, and the thickness also increased by an amount of broadening. Determine the mass of the finished ring product and the mass of the ring billet obtained after the implementation of this axial compression
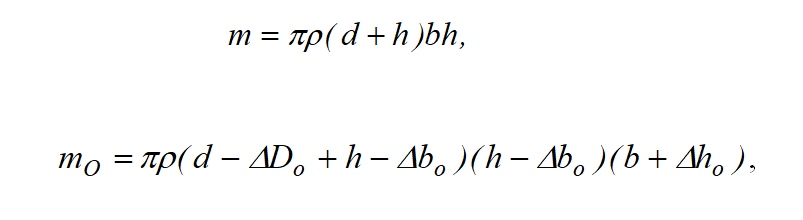
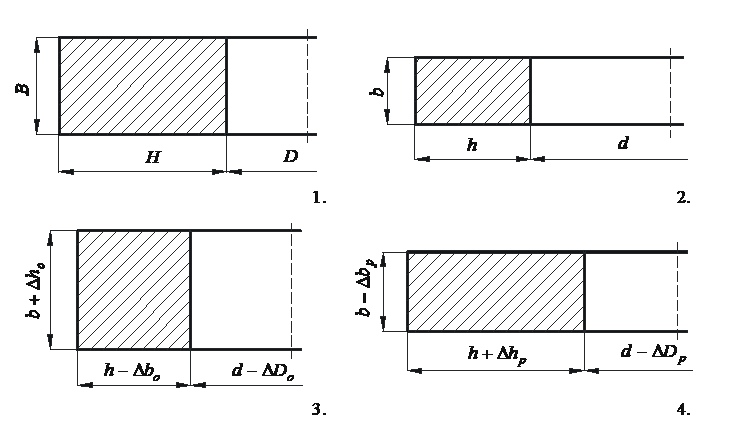
Figure 5- Dimensioning scheme
1, 2 - sections of the initial ring billet and the finished ring product;
3, 4 - cross sections of intermediate rolls.
Equating the mass of the finished ring product and the specified intermediate roll, we get

The increase in the diameter of the workpiece due to the realization of the axial compression is

Also presented is the second intermediate cross section of the ring article. Suppose it is the result crimping the workpiece only in the radial direction. At the same time, its diameter increased by an amount, and its height also increased by an amount of broadening. Equating the mass of the finished ring product and the specified intermediate roll, we get

The increase in the diameter of the workpiece due to radial compression is

Equating and in accordance with condition (1), we obtain the first relation for determining the size of the original piece

The broadening of the workpiece in the radial direction due to the compression of the metal in the axial deformation zone and the broadening billet in the axial direction due to compression of the metal in the radial deformation zone will be determined through the coefficients and axial and radial broadening, respectively p>

Here, the coefficients and are defined as functions of the section shape factor of the annular product of other parameters of the radial and axial deformation foci. The axial and radial reductions (see Fig. 5) are defined as follows

Considering the ratios, these values ??are equal

Substituting the functions in the condition, in the final form we get the first dependence for determining the parameters and the original ring billet p>
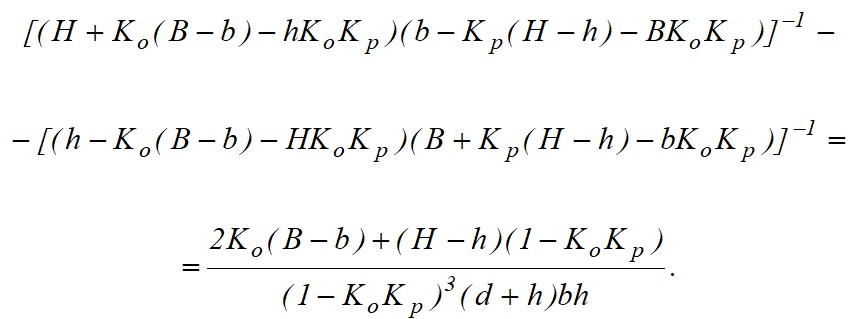
We will find the second dependence equating the masses of the initial ring billet and the finished ring product (2). The mass of the original ring billet is p>
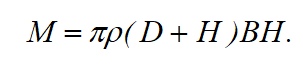
Solving the resulting equation for height, we finally get

The system of equations (12) and (14) determines the parameters of the workpiece and. The internal diameter of the original ring billet, as a rule, is determined by the existing technology on the press-rolling line and is equal to the diameter of the press punch on the firmware of the blanks. The system of equations (11) determines the ratio between the axial and radial reductions, ensuring the flow of metal into the hood and, accordingly, the diameter growth with the same intensity in the axial and radial directions, which is the decisive condition for rolling rings without the formation of tightening on its lateral and end surfaces. Obviously, system (11) determines the most rational total radial and axial compression. The task of determining the relationship between them at each turn of the ring product during its rolling should be considered separately. P>
CONCLUSIONS:
1. Based on the deficiencies found, measures have been developed to improve the technology: transition to rolling small diameter tires on one ring-rolling mill; development of a new calibration for the production of small and medium diameter tires 2. A calibration has been developed for rolling the tires on one mill, which prevents the metal from flowing from the ridge to the ring and prevents defects such as utyazhka and failure to comb.