Реферат
Содержание
- Введение
- 1. Конечно-элементное моделирование схем штамповок колесных заготовок
- 2. Результаты исследования
- Выводы
- Список литературы
Введение
Многие задачи, с которыми приходится в настоящее время сталкиваться исследователям и инженерам, не поддаются аналитическому решению либо требуют огромных затрат на экспериментальную реализацию. Зачастую единственной возможностью экспресс-анализа инженерной проблемы является компьютерное математическое моделирование. Прогресс в разработке численных методов позволил существенно расширить круг задач, доступных анализу. Полученные на основе этих методов результаты используются практически во всех областях науки и техники.
Современный технологический процесс, в том числе металлургический, не может обойтись без активного использования, как компьютерной техники, так и соответствующего программного обеспечения, необходимого, для разработки и освоения новых технологий и, конечно, для удовлетворения нужд текущего производства (разработка чертежей, конструкторской документации, выполнение проверочных расчетов и т.д.).
1. Конечно-элементное моделирование схем штамповок колесных заготовок
На сегодняшний день актуальной научно-технической задачей в сфере производства железнодорожных колес является совершенствование схем штамповки в части применения рациональных силовых режимов работы прессов и высокой стойкости инструмента деформации.
В настоящей работе будет рассмотрено 3 схемы штамповки железнодорожных колес: разработанная специалистами SMS Eumuco, специалистами ОАО «Евраз НТМК» и работниками АО «Выксунский металлургический завод» (далее АО «ВМЗ»), которые реализованы на предприятиях ОАО «Евраз НТМК» и АО «ВМЗ».
Наряду с получением требуемых параметров по геометрии, макро- и микроструктуре, а также механических свойств изделий, одним из важных критериев оценки эффективности применяемых схем деформирования заготовки является их влияние на силовой режим прессопрокатного оборудования и стойкость деформирующих штампов.
В колесопрокатном производстве повышение стойкости инструмента деформации является актуальной задачей, так как именно этот параметр влияет на затраты, связанные с выбором марки стали для штампов, схемой их производства и применяемой технологической смазкой.
Целью данной работы является изучение влияние вышеупомянутых схем штамповки на силовые параметры формовочного пресса R9000 и пресса силой 100 МН и величину износа инструмента деформации (штампов данных прессов).
Анализ формоизменения металла, температурных и силовых параметров, а также износ штампов на формовочных прессах R9000 и 100 МН был выполнен на основе результатов конечно-элементного моделирования процесса штамповки в среде DEFORM-3D.
Для колесной заготовки была выбрана пластическая модель материала, кривые течения металла были рассчитаны для стали марки Т (ГОСТ 10791-2011) для технологий SMS Eumuco, ОАО «Евраз НТМК» и АО «ВМЗ».
Заготовка имела неравномерное температурное поле в диапазоне 1100-1280°С, полученное путем конечно-элементного моделирования процессов транспортировки заготовки к прессу R5000, деформации заготовки на данном прессе и транспортировки к прессу R9000 для технологий SMS Eumuco и ОАО «Евраз НТМК». Для технологии АО «ВМЗ» температура заготовки составляла 1080-1260°С, которая была достигнута путем моделирования процессов транспортировки заготовки к осадочному прессу 20 МН, деформации на прессе 20 МН, транспортировки к прессу 50 МН, деформация на данном прессе и транспортировки к прессу 100 МН.
Получить реальные значения величины износа инструмента деформации не представляется возможным ввиду нехватки информации для расчета данного параметра при помощи заложенных в программу DEFORM-3D инструментов, то возможен лишь сравнительный анализ величины износа штампов относительно нескольких технологий.
При сравнительной оценке различных схем штамповки колесных заготовок учитывали только абразивный износ. Для расчета величины износа использовали модель Арчарда.
Напряжение контактного трения определили, как долю от величины напряжения течения металла на сдвиг.
Результаты исследования
Выполнен анализ трех схем штамповки колесной заготовки (рисунок 1-3) для колес диаметром 957 мм с плоскоконическим диском по ГОСТ 10791-2011:
- Схема штамповки с предварительной осадкой гладкими плитами колесной заготовки в верхнем плавающем калибровочном кольце (данная технология в настоящее время применяется на прессопрокатной линии ОАО «Евраз НТМК»;
- Схема штамповки с предварительной формовкой заготовки на прессе R5000 (данная технология была разработана фирмой SMS Eumuco и внедрена на предприятии ОАО «Евраз НТМК»);
- Схема штамповки с предварительной осадкой заготовки на гладких плитах пресса силой 20 МН и «разгонкой» в нижнем технологическом кольце на последующем прессе усилием 50 МН (технология используется на предприятии АО «Выксунский металлургический завод»).
Результаты моделирования показали, что при штамповке колесных заготовок по всем трем схемам температура штампов в последний момент штамповки не превышает 300 °С.
В результате анализа было установлено, что при штамповке колесной заготовки по схеме 1, штампы в зоне ступицы заполняются задолго до окончания процесса формовки (рисунок 1б), что предполагает работу пресса в экстремальных условиях при максимально допустимой силе формовки. В результате этого, в ряде случаев, имеет место недоштамповка колесной заготовки в связи с тем, что необходимая для продолжения деформирования металла сила, даже с учетом работы пресса в режиме выдержки под нагрузкой превышает допустимую величину (90 МН). Кроме этого, доштамповка колесной заготовки в режиме выдержки, максимально развиваемой прессом силы в течение 2 - 4 с, приводит к увеличению длительности контакта деформируемого металла с инструментом и, следовательно, к его дополнительному разогреву, что уменьшает срок службы деформирующих штампов.
При штамповке колесных заготовок по схемам 2 и 3 силовой режим работы пресса является более рациональным, т.к. величина средней силы для условий формовки в этом случае меньше более чем на 25% от величины соответствующей средней силы при штамповке по схеме 1) и характеризуется постепенным нарастанием необходимой для реализации процесса формовки силы, что видно на графиках (рисунок 2б; 3б). Ее максимальная величина нужна лишь в последний, кратковременный момент штамповки (рисунок 2в; 3в). При этом работа пресса R9000 и пресса силой 100 МН в режиме выдержки под нагрузкой, как при штамповке по схеме 1, не требуется.
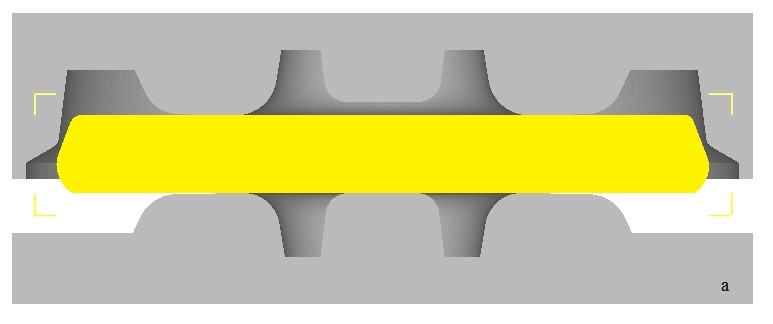
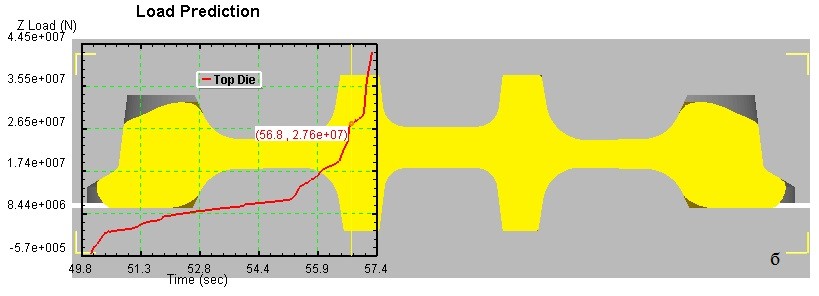
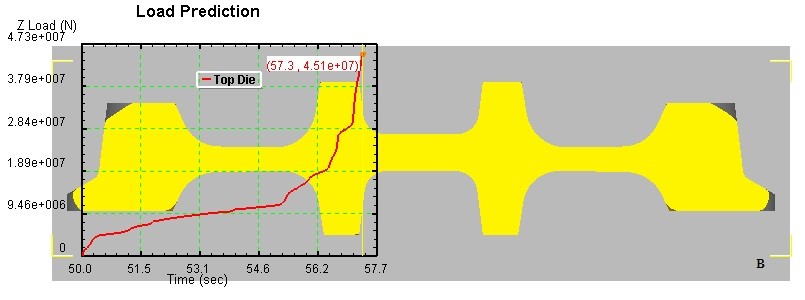
Рисунок 1 – Штамповка колесной заготовки по схеме 1: а – первый момент времени; б – промежуточный момент штамповки; в – последний момент штамповки.
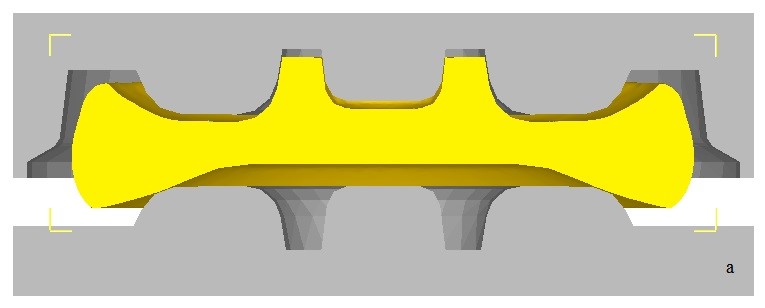
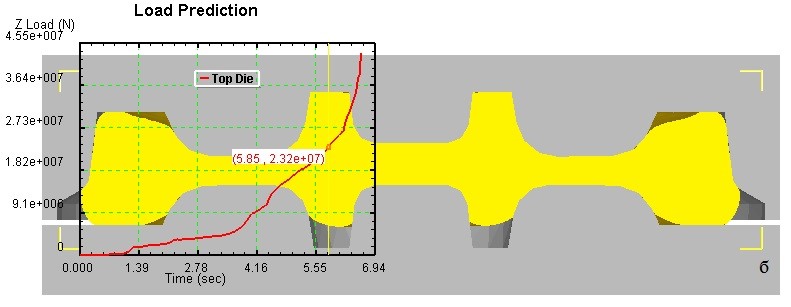
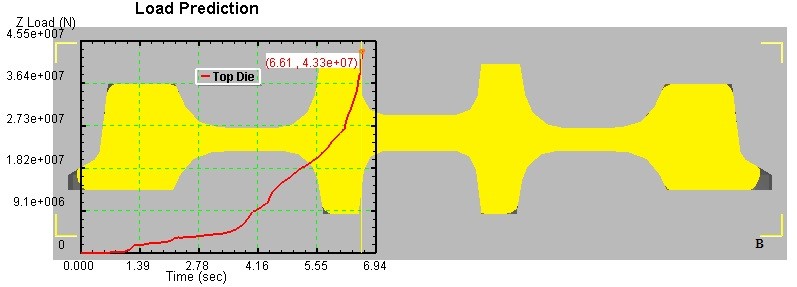
Рисунок 2 – Штамповка колесной заготовки по схеме 2: а – первый момент времени; б – промежуточный момент штамповки; в – последний момент штамповки.
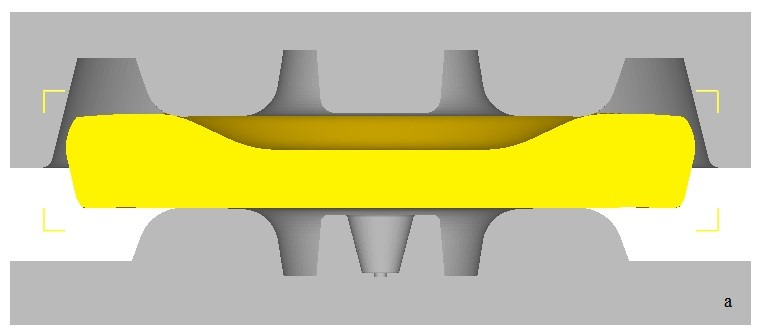
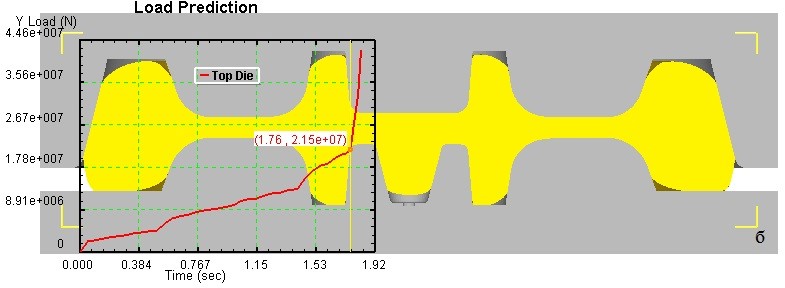
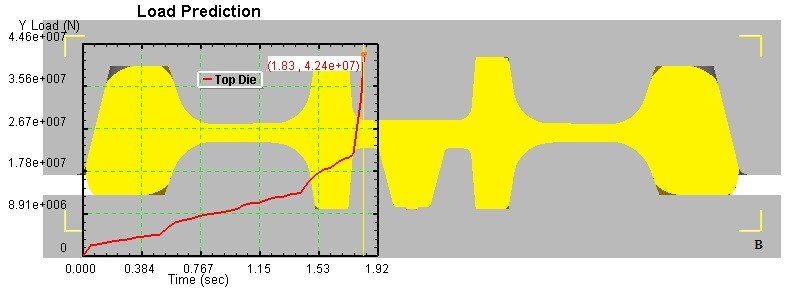
Рисунок 3 – Штамповка колесной заготовки по схеме 3: а – первый момент времени; б – промежуточный момент штамповки; в – последний момент штамповки.
На основе результатов моделирования процесса износа инструмента деформации (рисунок 4-6) можно сформулировать следующие выводы: преждевременное заполнение ступицы (схема 1) и реализация схемы одностороннего течения металла на заключительной стадии формовки приводит к повышению величины износа формовочных штампов более чем на 30% (относительно других схем) на участке формирования диска колесной заготовки, т.к. именно в этой части и происходит основная деформация металла; реализация схемы формовки заготовки с предварительной «разгонкой» (схема 3), помимо уменьшения величины износа (относительно схемы 1) приводит к локализации износа штампов с участка формовки диска в участок перехода от диска к ступице и участок перехода от диска к ободу, причем во втором случае данная величина в 2 раза больше, чем в первом; реализация схемы формовки заготовки с предварительной формовкой верхней части заготовки (схема 2) в еще большей степени уменьшает величину износа инструмента деформации, относительно двух предыдущих схем, и при этом основной износ приходится на участок перехода от диска в ободу. Износ деформирующих штампов вследствие преждевременного контакта краев заготовки с формовочным кольцом хоть и присутствует и практически равен для всех трех схем, однако является незначительным по сравнению с основной величиной износа.
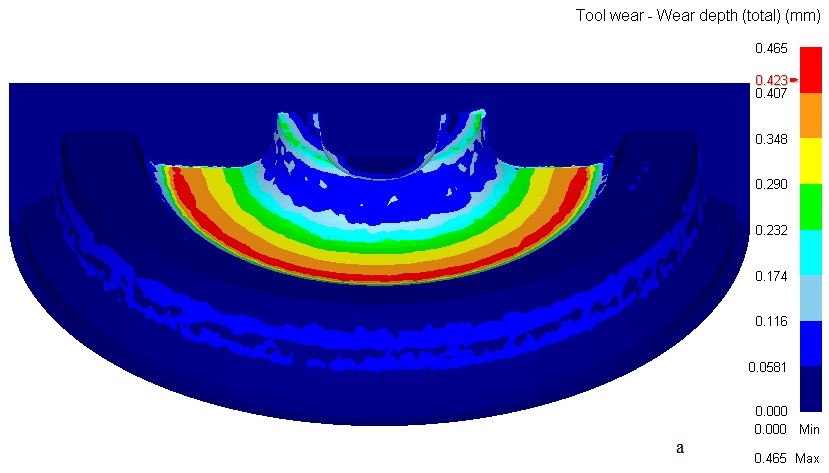
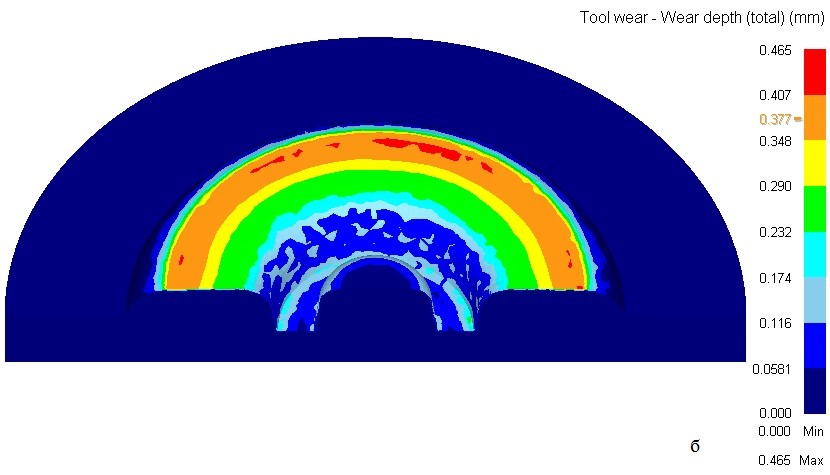
Рисунок 4 – Результаты моделирования износа штампов при штамповке колесной заготовки по схеме 1: а – верхний штамп; б – нижний штамп
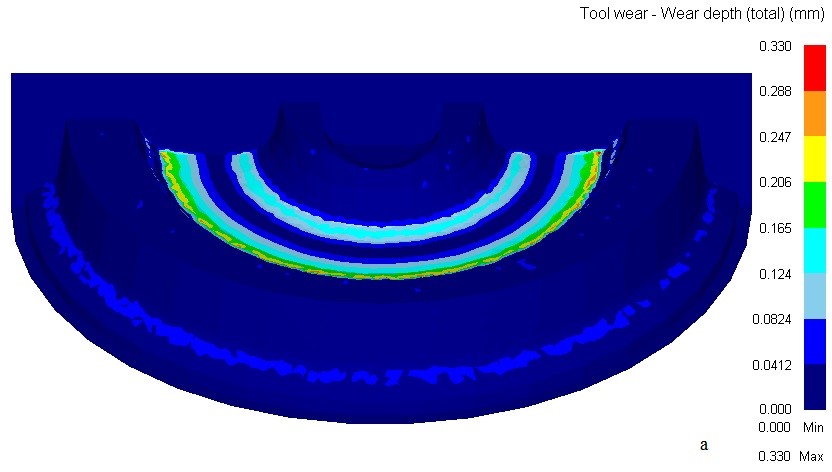
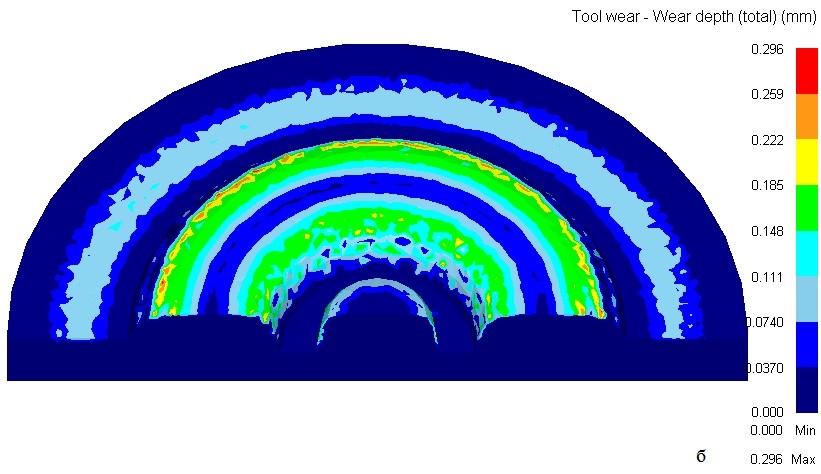
Рисунок 5 – Результаты моделирования износа штампов при штамповке колесной заготовки по схеме 2: а – верхний штамп; б – нижний штамп
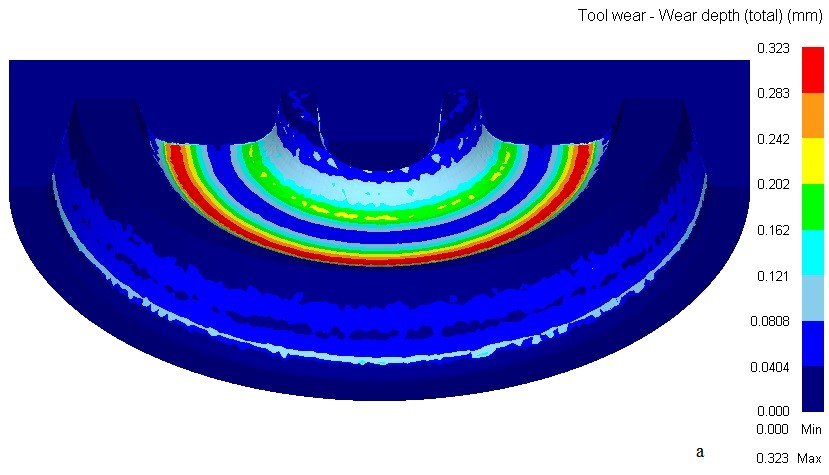
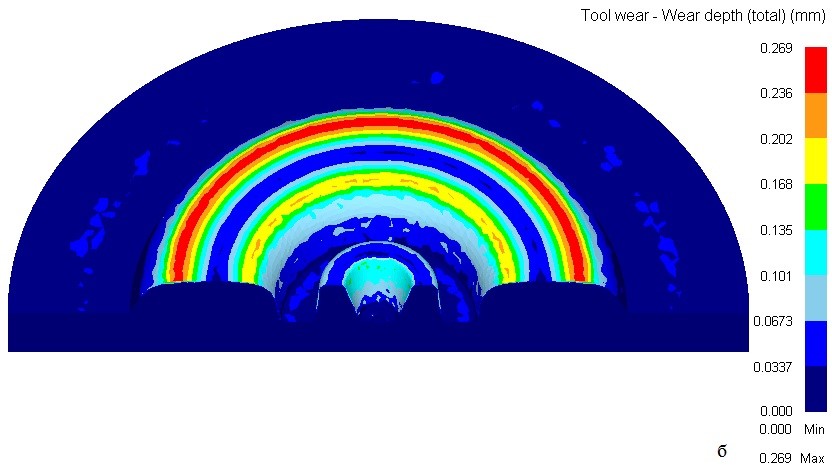
Рисунок 6 – Результаты моделирования износа штампов при штамповке колесной заготовки по схеме 3: а – верхний штамп; б – нижний штамп
Выводы
Таким образом, на основе результатов конечно-элементного моделирования выполнен анализ влияния схем штамповки колесных заготовок на силовые режимы работы формовочного пресса и износ инструмента деформации.
Показано, что использование схем штамповки, которые предусматривают регламентированное распре¬деление металла между ее центральной и периферийной частями, характеризуется рациональным силовым режимом. Во-первых, величина средней силы в этом случае снижается на 25% от величины средней силы при штамповке по схеме 1. Во-вторых, в этом случае имеет место постепенное нарастание необходимой для реализации процесса формовки силы, причем ее максимальная величина необходима лишь в последний, кратковременный момент штамповки.
Исключение преждевременного заполнения ступицы и, соответственно, одностороннего течения металла на заключительной стадии штамповки способствует уменьшению средней величины износа формовочных штампов более чем на 30%. Установлено, что в процессе обжатия металла в области диска, чем раньше образуется подпор течению металла со стороны формовочного кольца, тем меньше величина проскальзывания деформируемого металла относительно поверхности формовочных штампов в зонах их наиболее интенсивного износа (перехода от диска к ободу) и, как следствие, меньше величина износа.
Список источников
- Снитко С.А., Дужуржи А.А. Влияние параметров конечно-элементных моделей на точность расчета формоизменения металла и сил при штамповке и прокатке заготовок железнодорожных колес / С.А. Снитко С.А. [Электронный ресурс] // Обработка материалов давлением: сб. науч. тр., Краматорск: ДГМА, 2010. - Вып.1(22) - С. 44 – 48.
- Снитко С.А., Конечно-элементное моделирование многопереходного процесса деформирования заготовок при производстве железнодорожных колес / С.А. Снитко, В.Л. Калюжный [Электронный ресурс] // Вісник Національного технічного університету України “Київський політехнічний інститут”. Серія: Машинобудування / Київ: КПІ, 2010. – Вип. 62. – С. 53 – 62.
- Снитко С.А., Яковченко А.В., Ивлева Н.И. Компьютерное проектирование прессового инструмента деформации для штамповки колесных заготовок [Электронный ресурс] // Вестник ДонНТУ. – 2016. – №5(5)’2016. – С. 22 – 30.