Abstract
Warning! This abstract refers to a work that has not been completed yet.
Estimated completion date: June 2021. Contant author after that date to obtain complete text.
Content
- Introduction
- 1. Relevance of work
- 2. The purpose and objectives of the study
- 3. Disposal methods of distillery stillage
- 4. The proposed technology for the disposal of distillery stillage
- 5. Laboratory results
- Conclusions
- List of sources
Introduction
Today in the alcohol industry there is a rather difficult ecological situation with the disposal of the main production waste – distillery stillage [1].
In the production of alcohol, after the stage of distillation / rectification, there are several products at the outlet: the main product is ethyl alcohol and a number of by-products products such as ether-aldehyde fraction (EAF), fusel oil and distillery stillage.
Stillage is a waste product from the production of ethyl alcohol, a liquid (suspension) of light brown color with a pleasant smell of grain. The dry matter content is 6-8%. Output – 12-13 liters for each liter of alcohol [1].
On the one hand, stillage is a waste that causes environmental pollution, therefore it is forbidden to dispose of stillage into water bodies or into the sewage system without preliminary processing (figure 1).
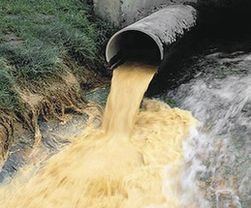
Figure 1 – Discharge of distillery stillage into water bodies
On the other hand, stillage, due to the content of fiber, carbohydrates, protein and microelements, is secondary material, it can serve as a raw material for the production of animal feed and other useful products. If fusel oil and EAF make up 1-3% of the total amount produced in modern rectification plants ethyl alcohol, then the amount of liquid distillery stillage is about 10-12 times greater than the amount of ethyl alcohol [2].
The main difficulty in the disposal of distillery stillage is the processing of soluble substances. In fact, on alcohol plant with a capacity of 3000 dal, up to 350 m3 / day of stillage is formed (figure 2), in the soluble part of which substances with chemical oxygen demand (COD) more than 50,000 mg O2 / l. Currently, there are several widespread areas for processing distillery stillage [2].
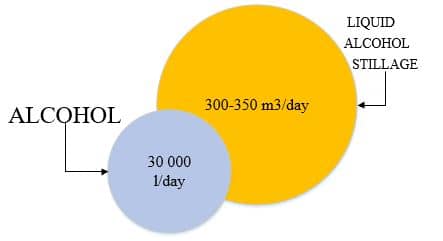
Figure 2 – Comparative diagram of the amount of produced ethyl alcohol to the amount of liquid distillery stillage
Recycling and disposal of distillery stillage, especially at high-capacity distilleries, has always been a big problem, since the discharge of distillery stillage, previously practiced by many factories, led to significant environmental pollution, and transportation of stillage in liquid form to livestock enterprises over long distances is not economically feasible [2].
1. Relevance of work
Fresh distillery stillage is an aqueous suspension with a small amount of dissolved and suspended solids: it contains 6-8% dry substances, of which 3-4% are solutes, and the rest is insoluble suspended particles. In the process of obtaining alcohol in vinasse almost everything remains, with the exception of starch and sugars, the nutrients present in the feedstock entering the alcohol production, as a result, stillage is a very valuable food and feed product, regardless of the type of raw materials used. According to monitoring data scientific literature, it is widely used in animal husbandry in many developed countries of the world. So, for example, in France and the USA 90-95% of liquid post-alcohol stillage is processed into a dry food product containing dry protein, easily digestible carbohydrates, vitamins, micro and macro elements. Nutritional the value of dry distillery is superior to standard compound feed and bran. 1 kg contains it (depending on moisture content and other components) from 1.08 up to 1.27 feed units. This product is either supplied to feed mills and introduced into complete feed, or is purchased by farmers and is mixed with feed grains directly on the farm. Thus, dry distillery stillage can be an additional source of high-value feed protein, easily digestible carbohydrates, vitamins, macro-microelements.
Its use in the diets of farm animals and poultry significantly increases productivity and reduces the consumption of grain fodder.
2. The purpose and objectives of the study
The main purpose of this work is to justify the choice of technology for the disposal of distillery stillage in the territory of the DPR. Scientific the novelty lies in the fact that this study is used for the first time to solve this problem on the territory of the DPR.
The main objectives of the study:
- Conduct an analysis in the field of the alcohol industry, assess the current environmental situation with the disposal of the main waste of alcohol production;
- To study the existing technologies for the disposal of alcohol stillage, consider the physicochemical foundations of the process of disposal of alcohol production;
- To analyze the content of the main indicators in the distillery stillage, in particular to control the content of heavy metals, dry substances, and control acidity;
- To form a general view of the technological scheme of the distillery stillage disposal process.
3. Disposal methods of distillery stillage.
Methods for processing distillery stillage can be conditionally divided into several types of schemes (figure 3.1):
- – using biotechnological operations;
- – based on physical methods.
They are based on already known methods, such as separation of the liquid and solid phases in centrifuges, growing fodder yeast on the substrate, product drying [3].
Schemes using biotechnology operations.
The essence of the scheme with the production of feed yeast is to ensure the utilization of most of the dissolved organic compounds stillage and their conversion into digestible feed protein in the form of feed yeast.
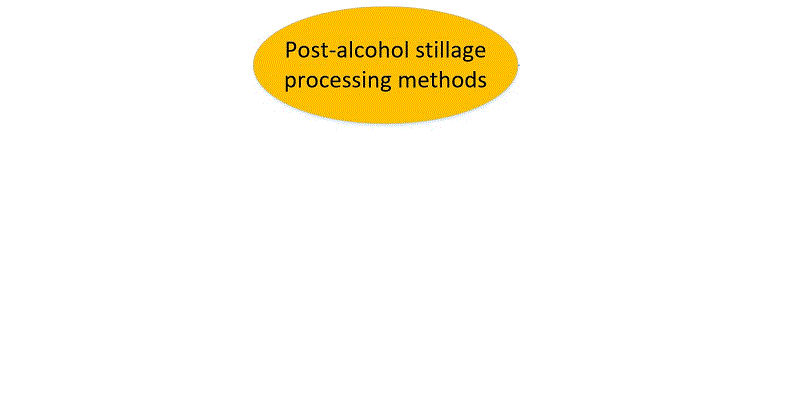
Figure 3.1 – Methods for processing distillery stillage
(Animation: Size: 103Kb; Frames: 8; Reps: 10; Delay: 1 sec.)
After growing yeast, the stage of separation of the solid phase (cake) and liquid (centrate) follows. The next stage is the most energy-intensive drying process. solid phase. The liquid phase at different enterprises can be processed in different ways: partially returned to production, sent to treatment facilities, evaporate [3].
The technology for processing vinasse into biogas is based on anaerobic fermentation (fermentation without oxygen).
Stillage is served in special containers, into which anaerobic bacteria are introduced. Bacteria Eating Nutrient Bard substances that produce biogas. Biogas can be used to generate electricity or heat by burning in factories boiler rooms, and the precipitated sediment can be used as a high-quality fertilizer. The advantage of this processing method is relative low operating costs and ease of use [3].
Physical method mased schemes.
The technological scheme for the processing of alcohol stillage with separation and filtration is as follows: distillery grain stillage from the silo is fed by a piston pump through a pipeline to a separator installed on the stillage press, where it is divided into two phases: centrate – low solids content, wet concentrate – solid enriched.
After the separator, the wet concentrate enters the press, where further moisture separation takes place. After the press, the bard is fed to the infrared drying unit, in which the product is dehydrated to 7-10% residual moisture. Further, the dried vinasse goes to a pellet press, where the final product is obtained – granules. The technology provides for the production of feed flour instead of granules, while the dry stillage is passed through mill installations. Finished products are packaged and packaged in containers that meet consumer requirements[4].
The technology of "concentrate evaporation" in evaporation plants is the most widespread. Whole stillage (after the stage of rectification) is separated into solid and liquid phase, after which the solid phase is dried[4].
Combined scheme for processing vinasse.
A relatively recently developed technology provides for the processing of distillery stillage into dry yeast feed concentrate (DCC). DCC – it is a mixture of the solid phase of vinasse, with fugate-based feed yeast. Introduction of yeast as a biologically active additive in the "cake" allows you to get a finished feed product that is significantly superior in biological value and digestibility to DDGS.
The proposed scheme allows you to significantly save energy resources in the process of processing vinasse. Energy savings are made mainly due to the "mechanical" separation of water from the centrate and the use of low-temperature belt conveyor dryers for drying, having energy consumption 4-6 times lower than spray dryers [4].
Ultimately, the choice of a particular technology for processing vinasse depends on the specifics of production..
4. The proposed technology for the disposal of distillery stillage
Many methods of disposal of waste distilleries are energy-intensive and do not provide the required level of safety for the environment. The most optimal economically and environmentally friendly scheme for processing distillery stillage with "concentrate evaporation" in evaporation plants [5].
The technological process for obtaining the DDGS product (figure 4.1) consists in the concentration of grain stillage, drying the resulting concentrate and granulating the latter [5].
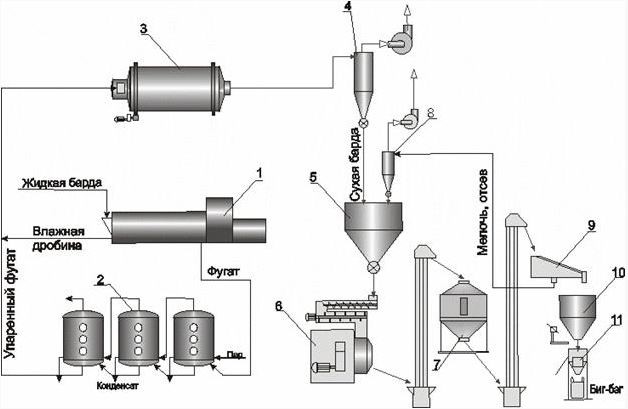
Figure 4.1 – Flow diagram of the DDGS product production process. 1 – decanter centrifuge; 2 – three-case evaporation plant; 3 – drying; 4 – cyclone; 5 – bunker; 6 – pellet press; 7 – cooler; 8 – aspiration system; 9 – vibrating sifter; 10 – weighing batcher; 11 – bag sewing machine
5. Laboratory results
When analyzing the content of the main indicators in distillery stillage, studies have shown that the sample contains distillery stillage (sample No. 1-5) the average content of indicators is: dry matter – 10.90-10.93%; moisture – 89.01-89.07%; ash – 0.40-0.56%; pH – 3.60-3.61; heavy metals (Pb) – 0.0044-0.0051%, which corresponds to the required standards of GOST 31809-2012. Stillage is fodder. Specifications, clause 3.4.
The average chemical composition of alcohol stillage (according to I.V. Petrukhin) is presented in table 5.1.
Table 5.1 – Chemical composition of alcohol stillage (according to I.V. Petrukhin)
Dry matter | Protein | Fat | Cellulose | NES | Ash | |
Molasses bard | 7,9 | 0,5 | 0,6 | - | 37,0 | 1,8 |
Potato stillage | 5,2 | 0,9 | 0,2 | 0,5 | 2,5 | 0,6 |
Wheat stillage | 11,5 | 1,7 | 0,6 | 0,7 | 5,7 | 0,6 |
Barda from corn | 7,3 | 1,4 | 0,6 | 0,7 | 3,3 | 0,4 |
Determination of the content of the main indicators is the basic way to control the quality of waste.
Conclusions
The work is devoted to the substantiation of the choice of technology for the disposal of the main waste of alcohol production – distillery stillage.
Within the framework of the research carried out:
- Considered the global environmental situation in the alcohol industry;
- Existing methods of disposal of distillery stillage have been studied;
- The physicochemical foundations of the process of utilization of distillery stillage are described;
- Quality control of the main waste of alcohol production, distillery stillage was carried out.
List of sources
- Леднев В.П. – Переработка барды: опыт, реальность, перспективы // Ликероводочное производство и виноделие. 2008, №7 (103) – с.8-11.
- Проблемы переработки отходов спиртового производства в Рсо-алания [Электронный ресурс]: Переработка мусора. – Режим доступа: https://ztbo.ru...
- Андросов А.Л. Промышленные технологии переработки послеспиртовой барды / А.Л. Андросов, И.А. Елизаров, А.А. Третьяков // Тамбовский государственный технический университет. – 2010. – 954 с.
- Переработка послеспиртовой барды: что это такое, описание методов [Электронный ресурс]: Утилизация и переработка мусора. – Режим доступа: https://bezotxodov.ru...
- Проблемы переработки отходов спиртового производства в Рсо-алания [Электронный ресурс]: Переработка мусора. – Режим доступа: https://ztbo.ru...
- ГОСТ 26713-85 Удобрения органические. Метод определения влаги и сухого остатка. Organic fertilizers. Method for determination of moisture and dry residue
- ГОСТ 26714-85 Удобрения органические. Метод определения золы. Organic fertilizers. Method for determination of ash content.
- ГОСТ 27979-88 Удобрения органические. Методы определения рН. Organic fertilizers. рН determination method.
- ГОСТ 30692-2000 Корма, комбикорма, комбикормовое сырье. Атомно-абсорбционный метод определения содержания меди, свинца, цинка и кадмия. Fodders, mixed fodders and animal raw foodstuff. Atomic absorption methodfor determination of copper, lead, zinc and cadmium.