The use of organic additives for the production of coke from depleted mixtures
Content
- Introduction
- 1. Relevance of the topic
- 2. Purpose and objectives of the study, planned results
- 3. Analysis of trends in the change in the grade composition of industrial charges used at coke plants of Donbass
- 4. Laboratory coking of charges, including sulphurous coals
- 5. Influence of anthracene fraction on the yield of gas coal semicoking products
- Conclusion
- References
Introduction
Modern conditions for coal supply of coke plants in the DPR and other CIS countries are characterized by incomplete supplies and the presence of a shortage of high-quality, well-sintered charge components. This situation leads to the most negative consequences in the practice of coke production, first of all, to frequent re-charging, sharp fluctuations in the coking period. At small-scale enterprises, the most vulnerable due to the limited economic and technological capabilities, emergency shutdowns of production can occur, and then a complete cessation of coke production, as was the case, for example, at the Donetsk and Horlivka coke plants.
One of the possible ways to solve this problem is the coking of charges of unconventional composition with the addition of various substances that directly affect the course of the sintering process. At the same time, coals of the middle stage of metamorphism are characterized by a high yield of liquid products with high sintering properties, but they are scarce and expensive. In part, instead of these grades of coals, the literature suggests using such organic additives as solid polymers (polyethylene, polystyrene, polyethylene terephthalate), by-product coke waste (sour tar of the sulfate department, polymers of absorbing oil, sour tar from the benzene rectification shop, coal tar, fossils), fuel oil, coal tar pitch, oil industry waste, etc. Most of the investigated products did not find practical application due to increased thermosetting, which led to the formation of fragile amorphous structures [1-3].
1. Relevance of the topic
Of the numerous proposals, the most elaborated are methods of increasing sintering capacity by adding petroleum or coal tar pitch – mesogenic additives. Their role is mainly in the following: they supply the missing quantities of thermally stable liquid nonvolatile products necessary for sintering coal grains, as well as condensed aromatic structures that contribute to the formation of an anisotropic liquid crystalline phase – the mesophase. The addition of coal tar and pitch to the coal charge initiates the destruction of the coal substance, shifting the process to the region of lower temperatures. In addition, an increase in the fluidity and thermal stability of the plastic mass is, to a certain extent, due to the hydrogenating effect of organic additives.
In this work, when selecting an additive to improve the sintering ability of low-sintering gas coal, we proceeded from the idea that the properties of the plastic mass are determined by the forming mesophase structures. In addition, based on previously obtained comparative data, studies of the composition of extracts of fatty and gas coals [4]. According to these data, the content of anthracene and phenanthrene is about 5 times higher in the extract of well-caking grade Zh coal than in the extract of low-caking grade G coal.
2. Purpose and objectives of the study, planned results
One of the tasks of this work was the analysis of literature data and real industrial charges of the DPR coke plant to identify the most acute problems of the raw material base and ways to eliminate them.
Based on the above data, it can be concluded that the main problems of the raw material base are the shortage of coals of the middle stage of metamorphism and low-sulfur coals.
Hence the goal of this work follows:
- selection and research of organic additives for producing coke from depleted charge;
- analysis of the effect of sulfur on the sintering process.
To achieve this goal, two methods of thermal destruction were used, which made it possible to obtain and study liquid products formed during the formation of the plastic layer, i.e. responsible for the sintering process, namely: the standard char method and the thermofiltration method.
3. Analysis of trends in the change in the grade composition of industrial charges used at coke plants of Donbass
1. The leading tendency of the XXI century in the field of primary energy carriers is the further strengthening of the position of coal as an organic source of energy, on the one hand, and natural organic raw materials for the chemical and coke-chemical industry, on the other. At the operating mines of Donbass, coal reserves are estimated at 8.7 billion tons (6.5 billion tons of industrial) [5].
However, the quality characteristics of coal – ash content, moisture content, sulfur content, particle size distribution, etc., are constantly deteriorating due to a decrease in the share of highly scarce coking, low ash, low-sulfur coals and an increase in the production of low metamorphosed and brown coals [6]. Thus, domestic raw materials are characterized by high humidity ≈ 10.5%, ash content ≈ 18.3 – 25.5% and high sulfur content ≈ 0.5 – 9.3%. The yield of volatile substances is also overestimated and amounts to 31–32% [5].
2. A big problem in the DPR is the use of coals with a high sulfur content, since their amount in the total balance is about 70%. In the DPR and in Ukraine, formations of all categories are being developed: sulphurous – 35.2% of their total amount, 26.4% of formations are low-sulfur, 24% are medium-sulfur and 14.4% are high-sulfur. Of the 238 mines with coking coal, 113 (or 47.5%) have a sulfur content of up to 2.5%. The sulfur content in coals of different grades and within each varies greatly. On average, sulfur in DG, G, K and OS coals is ≈ 2.9%. They are used for coking. However, the coke obtained from such coals is considered uncompetitive on the European and world markets [7]. Accordingly, there is a problem of rational use of coking coal with a high sulfur content.
3. There are few coals from which coke of satisfactory quality can be obtained by self-coking. These include well caking coals of grades K and Zh. Coals of grades G and OS are also valuable for coking. If we consider the structure of the geological reserves of coal in the Donetsk basin [8], then with the existing technology of layered coking for these purposes only about 39% of the coal in the depths can be used. Their structure (by brands) is approximately as follows,%: G – 57, GZh – 9.5, F – 13.5, K – 8, OS – 9.5, T – 2.5. As you can see, the specific value of the most valuable for coking coals of grades K, Zh and OS in the reserves of this basin is small and amounts to about ⅓. Therefore, given the current scale of coke production, it is impractical to obtain it only from well-sintered coals, as this would lead to a rapid depletion of their reserves. At present, in the conditions of layer coking, it is practically impossible to ensure the quality of coke that meets modern requirements from even the most valuable coal grade.
Table 1 shows the change in the grade composition of coal charges at the Donbass factories over the years. As can be seen from the table, there is a clear tendency towards a reduction in the participation of highly sintered grades of domestic coals in the charge.
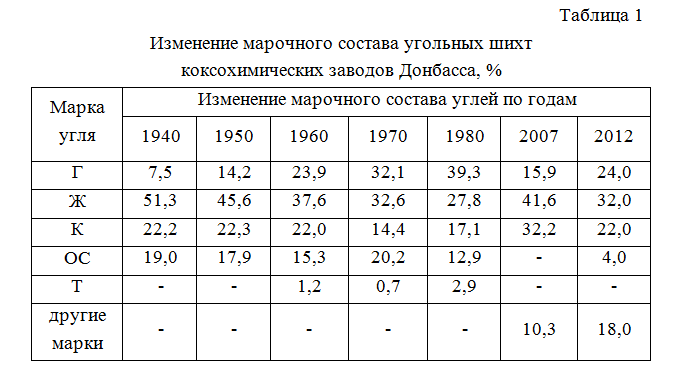
The growing role of imported coals indicates an irrational approach to the operation of the domestic coal complex (Table 2).
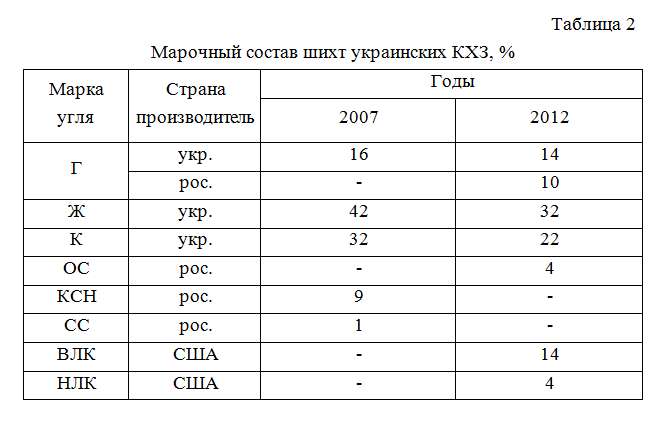
As shown by the studies of UHIN, an increase in the share of gas coals in the charge by 1% leads to a decrease in the gross yield of coke by 0.5 – 0.6%, i.e. to a decrease in the productivity of coke ovens.
It is believed that in order to obtain strong coke from Donetsk coals, the content of caking coals of grades Zh, K and OS in the charge should be at least 68%, and gas – no more than 32%. A further increase in the content of gas coals leads to a deterioration in the quality of coke.
Laboratory coking of charges, including sulphurous coals
In this work, for the preparation of the charge, we used coals of grade Zh and G, which are the basic irreplaceable components of the charge. Fatty coals are well caked, and gas coals are components with reduced caking. The ratio of different grades of coal in the mixtures (W: G = 70: 30) is selected by analogy with the classical
mixtures used in industry. A distinctive feature of the studied charges is the use of coals of different genetic types in terms of recovery. These are low-sulfur coals of type a
(Zha, Ha) and sulfurous type c
(Zhv).
The yield of liquid non-volatile products (LNP) and over-mesh residue (HO) of the residue for the charge from a pair of poorly reduced coals is 20.71% and 54.21%, respectively. Replacing poorly reduced fat coal with reduced coal dramatically increases the yield of liquid products responsible for the sintering capacity of coal.
Tables 3 and 4 show the comparative characteristics of the above-mentioned mixtures obtained from them by pyrolysis products and cokes.
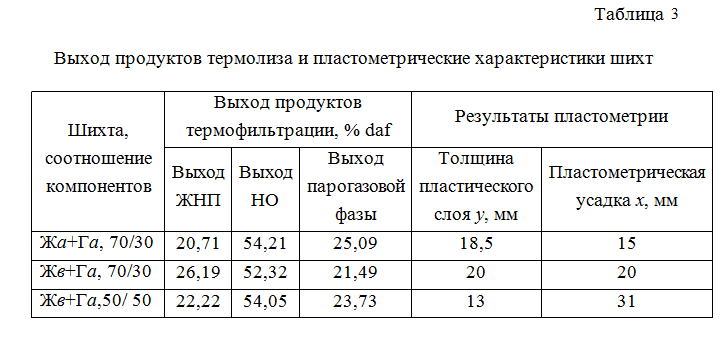

The use of recovered coal of grade Zh allows to increase the thickness of the plastic layer, yield and strength characteristics of coke; to increase the proportion of low-caking gas coal in the charge without reducing the coke yield, but leads to a slight decrease in the thickness of the plastic layer to 13 mm, with the value of y = 14 – 17 mm recommended for coking.
Influence of anthracene fraction on the yield of gas coal semicoking products
In theoretical terms, the study of the semi-coking process, as the most important stage in the coking process, makes it possible to make a scientifically grounded choice of sintering additives for coke mixtures with a high content of low-sintering components that form an insufficient amount of liquid products in a plastic state. In this case, the most important characteristic of the semicoking process is the yield of primary tar or tar
.
In the present work, the object of study was gaseous coals, which are one of the main components of the coke charge. An increase in their share in the charge leads to a decrease in the amount of liquid non-volatile products in the plastic mass. To compensate for this effect, it is recommended to use mesogenic sintering additives. During crystallization, it easily forms small crystals and sorbs a large amount of the liquid phase, separating from the oil with considerable difficulty.
The anthracene fraction is the last fraction obtained during the rectification of coal tar. It contains 1 – 3% high-boiling phenols, 3 – 5% naphthalene, 2 – 4% pyridine bases, 16 – 20% crude anthracene and 75 – 80% anthracene oil. A feature of the crystallization of anthracene oil is the very high viscosity of the product and the closeness of the structure and properties of the solid and liquid phases. Viscous products like anthracene oil have internal anisotropy, which leads to the formation of peculiar crystal-like fragments in the liquid phase [9].
A comparative analysis of the behavior of gaseous coal in the temperature range of semi-coking without and in the presence of various amounts of anthracene fraction addition has been carried out.
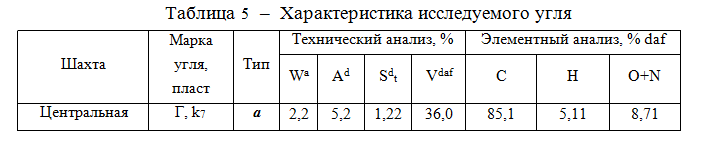
He following standard research methods were used in the work: technical and elemental analyzes according to GOST R 53357-2013 [10] and GOST R 53355-2009, respectively; determination of the yield of coking products according to GOST 3168-93 [11]; determination of the volume fraction of components in gases according to GOST 5439-76.
Table 6 shows comparative data on the yield of semi-coking products of the test coal with additions of the anthracene fraction. It follows from the table that with an increase in the percentage of anthracene additives in the mixture, the yield of resin increases sharply (≈ 3 times), the yield of pyrogenetic moisture, semi-coke and semi-coke gas decreases. An increase in the resin yield may indicate an increase in the sintering capacity of the mixture.
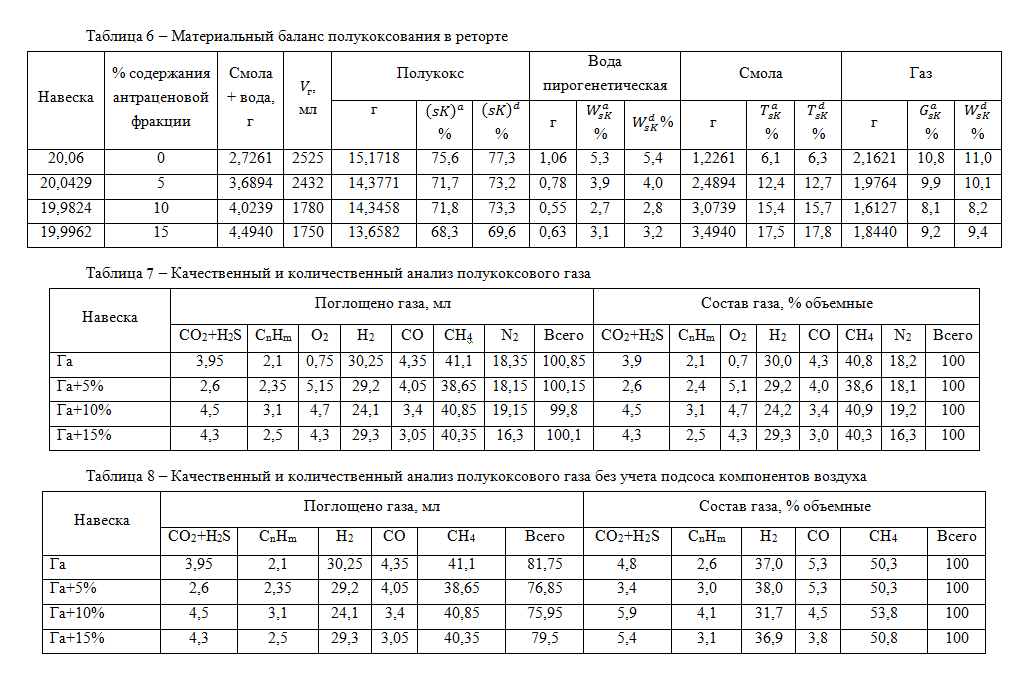
As can be seen from tables 7, 8, methane is the main component of semi-coke gas. Adding an anthracene additive to the gas increases the yield of hydrocarbons and the amount of acid gases – carbon dioxide and hydrogen sulfide. This fact indicates that the obtained semi-coke contains fewer oxygen and sulfur heteroatoms, i.e., it is more nutritious and less sulfurous.
A decrease in the content of carbon monoxide and hydrogen under the influence of the additive indicates the implementation of synthesis processes in the organic mass of coal and, as a consequence, should reflect an improvement in its sintering capacity.
The data obtained are consistent with the conclusions of Rusyanova [12] about improving the sintering ability of low-metamorphosed coals by breaking hydrogen bonds and removing oxygen. In experiments with long-flame and gaseous coals, it was possible to reduce the oxygen content by 2-3%, destroy some of the strong hydrogen bonds and, as a result, improve the thermoplastic properties of coals.
The laboratory studies carried out confirm the expediency of using the anthracene fraction to increase the yield of semi-coke tar and increase the proportion of low-sintering gas coals in the coke charge.
Conclusion
Analysis of the state of the coal industry in Donbass, current trends in the composition of charges at coke plants shows that the share of scarce well-caking fuels in the reserves is rapidly decreasing. This requires an increase in the proportion of low-caking, including gas coals and coals with a high sulfur content in the charge.
In this work, the effect of the addition of anthracene on the sintering capacity of coals included in the coke charge is studied. It was found that the addition of anthracene, as a component of anthracene oil, takes an active part in the process of coke formation, changing the nature of the reactions of thermochemical decomposition of coal and increasing the yield of LNP (or resin) responsible for sintering processes. The use of such additives in the charge will expand the raw material base of coking due to the use of a large amount of low-sintering gas coals in the charge. In this case, hazardous organic compounds are disposed of.
It is shown that during the transition to the plastic state, anthracene effectively affects the characteristic indicators of the resulting carbon plastic mass, which is due to its aromatic nature and the ability to participate in the formation of the mesophase. In addition, anthracene can act as an internal solvent, which also leads to an increase in the yield of liquid products.
When writing this abstract, the master's work has not yet been completed. Final completion: June 2021. The full text of the work and materials on the topic can be obtained from the author or his manager after that date.
References
- Сысков К.И., Громова О.Б. О механизме действия добавок – отходов коксохимического производства в процессе спекания //Кокс и химия. – 1984. – №3. – С. 18 – 19.
- Васючков Е.И., Музычук В.Д., Журавлева Л.А., Глущенко И.М., Панченко Н.И., Ивченко А.Ю. Исследование возможности использования отходов коксохимического производства в шихте для коксования //Кокс и химия. – 1985. – №11. – С. 16 – 18.
- Глущенко И.М., Цвениашвили В.Ж., Ольферт А.И., Наумов Л.С. Улучшение качества кокса путем использования в шихте мезогенных спекающих добавок //Кокс и химия. – 1987. – №11. – С. 39 – 41.
- Ольферт А.И., Тайц Е.М., Фесенко Ю.А. Мезофаза, спекание углей и формирование структуры кокса//Кокс и химия. – 1987. № 1. – С. 9-13.
- Огаренко Ю. Проблеми вугільної промисловості України та викиди парникових газів від видобутку й споживання вугілля. – Київ: Національний екологічний центр України. – 2006. – с. 24.
- Дроздник И.Д. Потребление коксующихся углей Украины. Проблемы и перспективы//Сб. трудов третьей ежегодной конференции «Уголь СНГ–2007. – Алушта, 2007. – С. 91–95.
- Долгий В.Я., Кривченко А.А., Шамало М.Д., Долгая В.А. Содержание общей серы в угольных пластах на шахтах Украины // Уголь Украины. – 2000. – № 1. – с. 44-46.
- Геология месторождений угля и горючих сланцев СССР. / Под ред. И.И. Аммосова и др. – М.: Госуд. научно-технич. изд.-во литературы по геологии и охране недр, 1963. – Т.1. – 1210 с.
- Печень В.А., Оксак Н.М., Бутузова, Л.Ф. Влияние добавки антрацена на спекаемость газовых углей / Охрана окружающей среды и рациональное использование природных ресурсов: сборник докладов ХIII Международной конференции аспирантов и студентов / ДОННТУ, ДонНТУ. – Донецк: ГОУ ВПУ «ДОННТУ, 2019. – с. 221-224.
- ГОСТ 53357-2013 Топливо твердое минеральное. Технический анализ.
- ГОСТ 3168-93 Топливо твердое минеральное. Методы определения выхода продуктов полукоксования.
- Русьянова Н.Д. Углехимия. – М.:Наука, – 2000. – 316 с.