Abstract
Содержание
- Introduction
- 1. Theme urgency
- 2. Goal and tasks of the research
- 3. The results of the scientific and theoretical approach of domestic and foreign scientists on the problem under study
- 4. Structural reliability and methods of increasing the resource of gas turbine engines based on the provision of functionally oriented properties
- Conclusion
- References
Introduction
In modern mechanical engineering in the context of intense competition on the world markets, the problem of producing competitive products is of particular relevance for engine-building enterprises. At the same time, it is necessary to take into account the quality of products, tight deadlines and the cost of the product. One of the most important tasks of improving aircraft engines is to increase their reliability and resource.
The reliability of gas turbine engines largely depends on the reliability of the compressor and turbine blades, since they are the most stressed parts. The blades are exposed to static, dynamic and cyclic loads, in addition, turbine blades experience cyclic, thermal stresses, they operate in an aggressive gas environment at high temperatures and are subject to gas corrosion. GTE blades have a complex spatial geometry and are made of difficult-to-deform materials: heat-resistant, titanium and aluminum alloys. Increased requirements are imposed on them, such as: for the structure of the metal, its chemical composition, mechanical properties, geometric dimensions, e xclusion of defects (locks, lumbago, burns, etc.).
1. Theme urgency
A helicopter gas turbine engine (GTE) consists of a large number of subsystems, modules and elements that operate in difficult operating conditions. At the same time, the main subsystems of this aircraft engine include a compressor, which has a plurality of blades for various purposes, located on the stage disks, forming groups of blades that perform specified operational functions. It can be noted that these groups of blades have a different nature of their operation, due to the peculiarities of the movement of the dust-air flow along the compressor path, the spatial shape of the blades, their location and the kinematics of movement. This leads to the occurrence of uneven and uneven abrasive-erosive wear of each blade, blades in a group and groups of blades relative to each other in the compressor. All this reduces the resource of the helicopter GTE as a whole, reduces the potential for the full use of all groups of compressor blades from the condition of equality of their resources, reduces the efficiency of its repair and restoration, and also limits the possibility of organizing various structural groups of blades into modular structures, which significantly reduces the parameters of their finishing - hardening treatment (OUO), restoration and repair.
To increase the service life of the compressor blades of helicopter GTEs, a whole range of different methods of OUO, t echnological processes and principles of rational processing are used. At the same time, functionally oriented coatings (FOP) are used to level out the wear of the working surfaces of the blades. These coatings provide the implementation of functionally oriented properties (FOS) of the working surfaces of the compressor blades, which significantly increases their resource.
The performed studies made it possible to establish that the compressor of a helicopter GTE is structured from different groups of blades. In this case, each group of blades is affected by its own specific operating effects, characterized by the occurrence of different types and intensity of wear of these groups of blades. Therefore, for each group of blades, it is necessary to provide its own specific technological process OUO of compressor blades with FOS. Moreover, the existing technological processes and applied methods do not allow equalizing the resource of compressor blades of various groups of blades in a single complex. The solution of these issues becomes possible on the basis of unified connections and the provision of the specified FOS parameters between different groups of GTE compressor blades. For this, it is necessary to improve the technological support and create a complex multi-connected technological process of the OUO of blades with FOS.
Based on this, increasing the resource of the blades of a helicopter GTE compressor by aligning it between the structural groups of blades on the basis of complex finishing and hardening multi-connected technological processes and providing FOS is an urgent task of great scientific and practical importance.
2. Goal and tasks of the research
Increasing the service life of the blades by providing functionally oriented technologies, by synthesizing a special technological process and developing technological support.
Main tasks of the research:
- To analyze the features of the compressor blades of a turboshaft GTE.
- Explore the basic principles and features of the operation of the blades.
- To develop a structural synthesis of technological processes to ensure the functional properties of GTE blades.
- Carry out experimental studies to improve the performance of compressor blades.
- To propose general recommendations for the synthesis of the structure of a complex multi-connected technological process of finishing and hardening treatment of groups of compressor blades based on FOP and the principle of equality of resources of their groups. Implement results in real production to save money and increase productivity.
Research object: the structure of a complex multi-connected technological process OUO of blades of a GTE compressor with FOP based on the equality of the resources of their groups.
Research subject: the set of relationships between the parameters of the properties of compressor blades between individual technological processes of processing their groups.
Within the framework of the master's work, it is planned to obtain relevant scientific results in the following areas:
- It has been established that the compressor blades are affected by uneven operational functions, which are implemented by groups of blades, while the abrasive-erosive wear of the compressor blades is characterized by irregularities of three ranks.
- A technological approach has been developed for the synthesis of a complex technological process of the OUO of compressor blades on the basis of multiply connected technological processes and the provision of FOS of structural groups of blades from 4 conditions of equality of their resource.
- A set of relationships between the parameters of the structure of individual technological processes has been determined to provide the necessary set of FOS to groups of compressor blades from the condition that their resource is equal by its greater value.
3. The results of the scientific and theoretical approach of domestic and foreign scientists on the problem under study
The work of a large number of scientists and specialists is devoted to the issues of improving the structural and technological support of finishing and hardening treatment of GTE compressor blades. The fundamental studies in this direction include the work of the following professors: Abraimov N.V., Bezyazychny V.F., Boguslaev V.A., Demin F.I., Zhemanuk P.D., Eliseev Y.S., Krylov V. I., Makarova V.F., Poletaeva V.A., Pronicheva N.D., Tamarina Yu.A., Shitareva I.L., Yatsenko V.K. and many other scientists. These works provide information on the creation of advanced technologies aimed at improving the quality of elements and blades of aircraft gas turbine engines. However, the studies presented in them do not allow improving the structural and technological support for the manufacture of compressor blades for helicopter GTEs, taking into account the connections of the technological processes of the OUO of groups of compressor blades and the equality of their resource. Also, the review of the current state of the research issue showed that on the basis of existing data it is impossible to solve the issues of increasing the resource of the compressor blades of helicopter gas turbine engines by aligning it between the structural groups of blades on the basis of existing technological processes and providing FOS. Therefore, for this it is necessary to improve the structural and technological support of the compressor blades on the basis of multiply connected technologies.
At the same time, it can be noted that the previously performed studies and the results obtained are a good basis for further increasing the resource of the compressor blades of helicopter GTEs by aligning it between the structural groups of blades on the basis of complex finishing-strengthening multi-connected technological processes and providing FOS.
4. Structural reliability and methods of increasing the resource of gas turbine engines based on the provision of functionally oriented properties
The engine is one of the main elements of an aircraft (AC), which determines its reliability and flight safety. One of the important areas of aircraft technical operation is the operation of gas turbine engines (GTE) in difficult climatic conditions (increased dustiness of the atmosphere) with the provision of the required resources.
Gas turbine engine (GTE) compressor blades are the main elements of modern aircraft engines, which determine the resource and reliability of their operation under conditions of combined action of gas corrosion and (high-temperature oxidation, various types of salt corrosion) and erosion phenomena, as well as phase and structural changes in material properties. This is due to the action of an aggressive gas environment at high temperature, humidity, liquid particles, dust, sand and other particles in the air flow, which leads to the occurrence of chemical-abrasive erosion of the blade elements and their failure.
At the same time, it can be noted that GTEs belong to complex technical systems, which consist of many structural elements connected to certain subsystems. Here, the main elements are blades, which are structured according to GTE devices. For example, in an engine of the TV3-117 series, there are the following devices with blades: inlet guide vanes (VNA), an axial compressor device, a device with compressor turbine blades, a device with free turbine blades. In particular, the axial compressor has 4 groups of different blades: rotary guide vanes (HA) on the stator, HA blades on the stator, straightener vanes (SA) on the stator, rotor blades (12 stages).
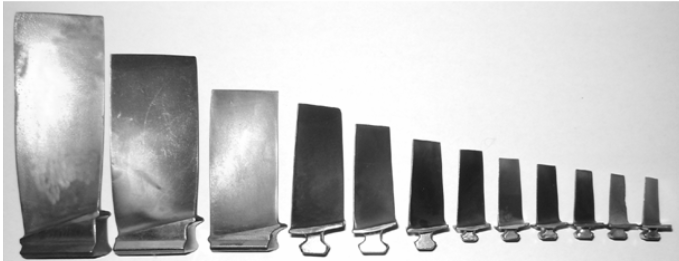
Figure 1 – General view of the blades of the compressor GTE model TV3–117
In general, the process of GTE operation can be characterized by the following main features:
- The presence of a complex structure of blade subsystems in a gas turbine engine.
- The complex structure of blade subsystems in a gas turbine engine is formed from a system of groups and subgroups of blades (stages).
- In the course of GTE operation, the complex structure of blade subsystems is affected by a system of irregular operating actions (a system of irregular functions), which occurs due to the following factors: design features of the blade, its location in the gas turbine engine, the kinematic structure of the blade, the peculiarities of the movement of the gas-air flow along the engine path, temperature environment in the corresponding engine subsystem, the structure of the abrasive dust environment and the like.
- As a result of the action of uneven operating influences (abrasive-erosion, corrosion, salt, alkaline, acid, temperature and others) on the GTE blades, uneven wear or destruction of the working surfaces of the blades occurs.
- The resulting irregularities in wear can be reduced to irregularities of 3 kinds, namely: 1st kind arising on the surface of the blade; 2nd kind - arising in the group of shoulder blades; 3rd kind - arising between the groups of the shoulder blades.
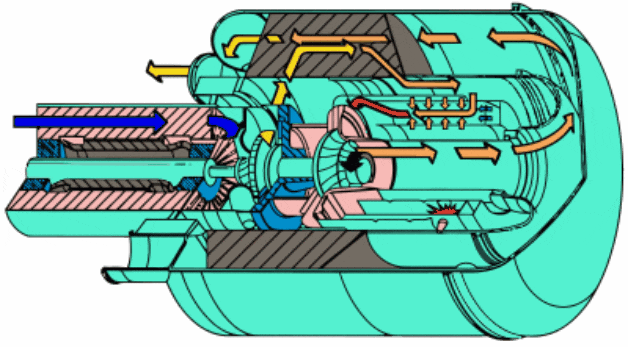
Figure 2 – General view of gas turbine engines
These features of the GTE operation reduce the resource of the blades of various groups and require further analysis of their operation, the creation of methods for increasing the resource of elements, subsystems and the entire GTE as a whole.
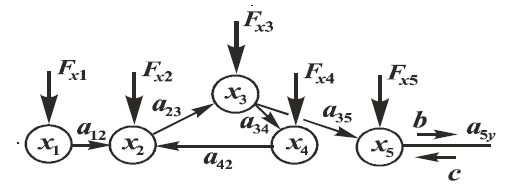
Figure 3 – A hypothetical scheme of the action of various operational functions on the subsystems of the gas turbine engine. Number of frames– 7
At present, to increase the resource of the element base of a gas turbine engine, many different methods have been developed to improve the performance of aircraft engines. However, in a number of cases, these methods do not provide a further increase in the service life of a gas turbine engine, especially under conditions of uneven operational influences. Therefore, this work is focused on further increasing the service life of GTE blades under conditions of uneven operating functions.
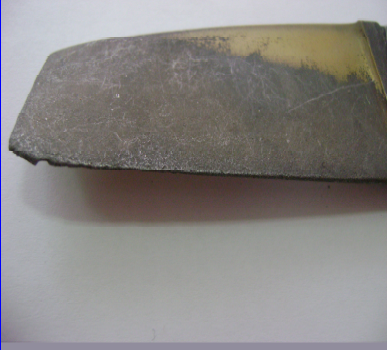
Figure 4 – General view of erosional destruction of the rotor blades
It should be noted that the working process of a helicopter turboshaft engine hypothetically corresponds to the ideal thermodynamic Brayton cycle with Q1 supply and Q2 heat removal at constant pressure and isentropic load (curve A–B) and expansion (curve C–D). Here, as a working medium, air with a specific heat Cp and an isentropic index k is proposed, the molecular composition of which does not change
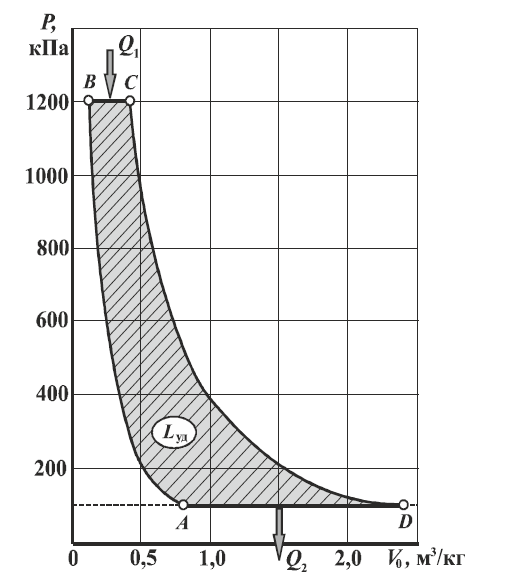
Figure 5 – Brighton ideal cycle diagram
Based on the diagram in Fig. 5, for an axial compressor the most important is to ensure the parameters of the compression of the gas-air flow of the flow path in accordance with the curve А – В. In practice, however, an ideal cycle is always different from a real thermodynamic cycle. This is influenced by a whole range of different parameters. The most important of these are the constantly increasing clearances between the rotor and stator blades, the rotor blades and the compressor casing, and the stator blades and the rotor.
With an increase in the clearances of the compressor flow path, all parameters of the thermodynamic cycle decrease. The increase in the clearances between the blades and the elements of the compressor flow path is mainly due to their erosion-abrasive wear and the action of a whole range of other operating influences. This is especially true under the conditions of the action of various types of operational irregularities in the structural elements and subsystems of the gas turbine engine, which further reduce its resource.
Conclusions
Of great importance in solving the problem of ensuring the resource and reliability of aviation gas turbine engines, as well as creating new generations of engines, is the development, improvement and creation of new technological processes, methods of processing parts and equipment, which increase not only productivity, but also the quality of manufacture.
The emergence of modern types and modifications of aircraft engines is continuously accompanied by new design solutions that entail technological difficulties. To overcome them in a timely manner and reduce the gap between "ideal", in terms of design, and "real", in terms of manufacturing technology of the part, it is necessary to actively introduce progressive methods of mechanical and finishing-hardening processing into production.
The analysis of the features of the operation of the structural elements and subsystems of the gas turbine engine made it possible to develop structural formulas for the reliability of the gas turbine engine for the stage of its design. Also, the work proposes a general approach to increasing the resource of a gas turbine engine based on the provision of a FOS of its elements and subsystems. This approach is based on a group of special principles for providing FOS element base. The paper shows the main ways to ensure a given, nominal or limit resource of a gas turbine engine based on FOS.
References
- Mikhailov A.N., Mikhailov V.A., Mikhailova E.A. Fundamentals of shaping and productivity increase in the deposition of vacuum ion-plasma coatings of mechanical engineering products / A. N. Mikhailov, V. A. Mikhailov, E. A. Mikhailova // Progressive technologies and systems of mechanical engineering: International collection. scientific papers. – Donetsk: DonNTU, 2004. - Issue. 28 .– S. 108 – 116.
- Mikhailov A.N. Basics of synthesis of functionally oriented technologies. – Donetsk: DonNTU, 2009 – 346 p.
- Mikhailov A.N. General features of functionally oriented technologies and the principles of orientation of their technological effects and properties of products. // Mechanical engineering and technosphere of the XXI century. Proceedings of the XIV International Scientific and Technical Conference in Sevastopol, September 17-22, 2007. In 5 volumes. - Donetsk: DonNTU, 2007. T. 3. S. 38–52.
- Boguslaev V.A., Yatsenko V.K., Zhemanyuk P.D., Pukhalskaya G.V., Pavlenko D.V., Ben V.P. Finishing and hardening treatment of GTE parts - Zaporozhye, ed. JSC "Motorsich", 2005 - 559 p. Demin F.I., Pronichev N.D., Shitarev I.L. Manufacturing technology of the main parts of gas turbine engines: Textbook. allowance. – M .: Mechanical engineering. 2002. – 328 p .; silt
- Sulima A.M., Shulov V.A., Yagodkin Yu.D. Surface layer and performance properties of machine parts. M .: MashinostroenieYu, 1988 240s.
- Mikhailov AN, Mikhailova E.A. General classification of vacuum ion-plasma coatings on the inner cylindrical surfaces of mechanical engineering products. // Hardening technologies and coatings. – M .: Mechanical engineering ,. No. 7. 2006.S. 3 – 6.
- Mikhailov A.N., Mikhailov V.A., Mikhailova E.A. Ionic-plasma vacuum coatings are the basis for a wide improvement in the quality of mechanical engineering products. // Progressive technologies and systems of mechanical engineering: International collection. scientific papers. – Donetsk: DonNTU, 2004. Issue 28.S. 108–116.
- Skubachevsky G.S. Aviation gas turbine engines: A textbook for students of aviation universities. Moscow: Mechanical Engineering, 1969–544 p. Matalin A. A. Technology of mechanical engineering: Textbook for university students. Moscow: Mechanical Engineering, 1985–512 p.
- Mikhailov A.N., Khavlin T.V. Features of the technological process of increasing the resource of turbine blades of an aircraft engine on the basis of functionally oriented technology // Progressive technologies and systems of mechanical engineering: Mezhdunar.sb. scientific. tr. – Donetsk: DonNTU, 2017. – Issue. 1 (56). - S. 101–114.