Реферат
Зміст
1. Аналіз існуючих конструкцій штовхувачів заготовок.
За способом передачі штовхає зусилля розрізняють такі конструкції Штовхувачі: рейкові, гвинтові, важільні, ланцюгові, фрикційні. Для приводу Штовхувачі переважно використовують електромеханічний привід, але іноді застосовуються гідравлічний або пневматичний приводи.
Рейковий штовхач (рис. 1) призначений для переміщення окремих блюмов і слябів з рольганга в нагрівальну піч і просування через неї всього ряду заготовок.
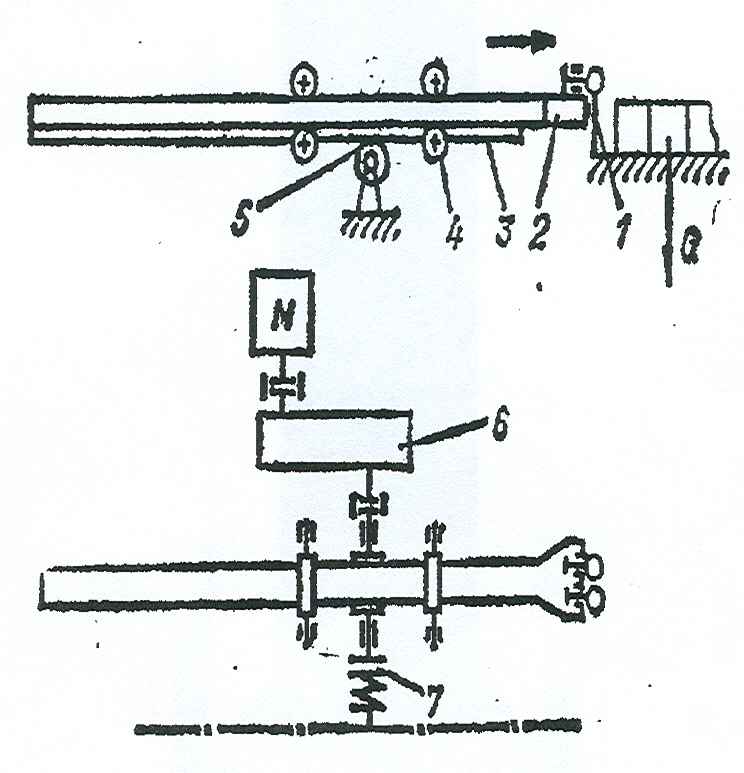
1–що штовхає елемент;
2,3–зубчасті рейки;
4–напрямні ролики;
5–шестерня;
6–редуктор;
7–сполучна муфта
Штовхає штага забезпечена штовхають пальцями з пружинними амортизаторами. При русі штанги вперед в опорних ковзанках пальці впираються в торець штанги і штовхають перед собою блюм. При русі штанги назад і наявності на рольганге наступного блюма, пальці відхиляються вгору, і головка штанги безперешкодно відхиляється у вихідне положення, після чого замикає пружина притискає штовхають пальці до торця штанги. З нижнього боку штанги закріплена зубчаста рейка, за допомогою якої на штангу передається штовхає зусилля від приводу через приводний шестерню. Швидкість руху заготовки, рухомої рейковим штовхачем, 0,2 - 0,25 м / с.
Гвинтовий штовхач (рис.2) подає заготовки в піч, просуває їх по ходу печі і вивантажує через вікно видачі; застосовується для подолання зусиль до 700 кН при ході лінійки до 2,5 м.
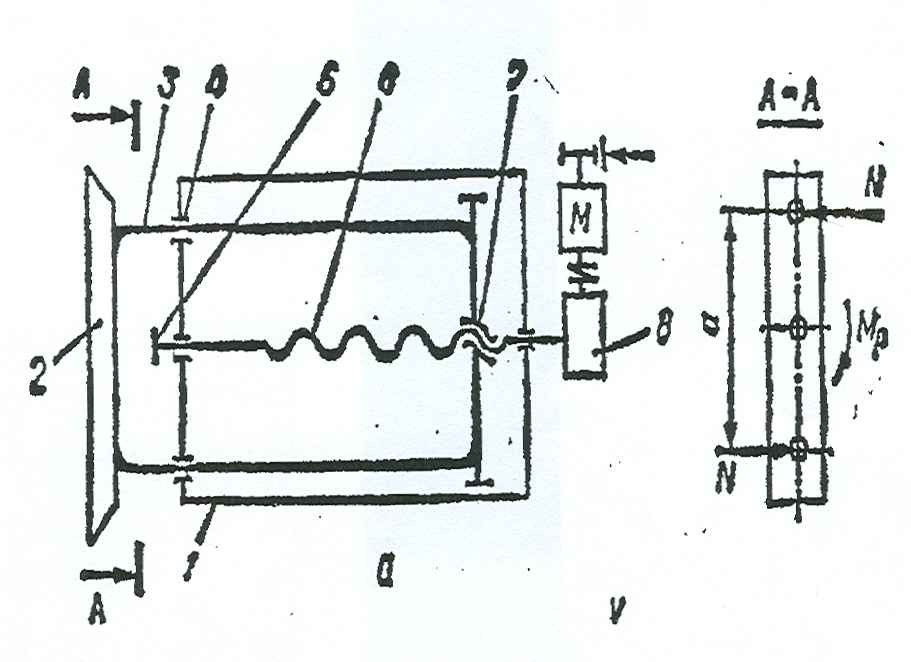
1–станина;
2–лінійка;
3–штанга;
4–напрямна;
5–підшипник;
6–гвинт;
7–гайка;
8–редуктор
Гвинтовий штовхач складається з нерухомої рами, на якій встановлені передня і задня стійки. До передньої сойці прикріплені напрямні втулки для штанг, радіальний і завзятий підшипники для переднього кінця гвинта. При обертанні гвинта переміщуються гайка і пов'язана з нею траверса. Траверса в свою чергу жорстко пов'язана з задніми кінцями штанг, які проходять через напрямні втулки передньої стійки, і їх передні кінці приєднані до загальної штовхає голівці. Така конструкція забезпечує роботу гвинта тільки на стиск. Гвинт обертається від приводу, що складається з електродвигуна, редуктора, сполучної муфти і гальма.
Недоліками гвинтових сталківаетелей є: швидкий знос гайки (термін служби не більше 2-х років), низький коефіцієнт корисної дії самої пари гвинт-гайка. Перевагою гвинтових штовхувачів в порівнянні з рейковими є менші габарити і металоємність.
Штанги Штовхувачі виконують кованими, звареними і, для штовхачів розрахованих на мале зусилля, з катаних заготовок круглого перетину. Ковані і зварні штанги більш складні у виготовленні, складніше виходить і конструкція направляючих. Однак застосування штанг прямокутного перетину, для рейкових штовхувачів, дозволяє виконати зубчасті рейки у вигляді окремих деталей, виготовляючи їх з більш міцною і зносостійкого сталі (40Х, 40ХН), і у разі спрацювання зубів замінювати, зберігаючи важкі і дорогі штанги. Штанги штовхачів круглого перетину простіше у виготовленні, але в цьому випадку зуби доводиться нарізати на них. В цьому випадку у разі спрацювання зубів штанги повинні замінюватися цілком.
На відміну від конструкцій штовхачів, у яких штанга з великим ходом і рухається зворотно-поступально в результаті реверсивного руху електродвигуна, у важеля штовхача (рис.3) зворотно-поступальний рух штовхає пристрої відбувається при безперервному обертанні електродвигуна в одному напрямку. Зазвичай важільні штовхачі розраховані на малі і середні штовхають зусилля зі швидкостями руху 2 ... 3 м / хв і ходом штовхача в межах 200 ... 600 мм. Перетворення обертального руху двигуна в зворотно-поступальний рух штовхає пристрої в важільному штовхачі відбувається наступним чином. Електродвигун обертає вхідний вал редуктора, на вихідному валу якого розташований кривошип. Кривошип з'єднаний шатуном з важелем, закріпленим на валу.
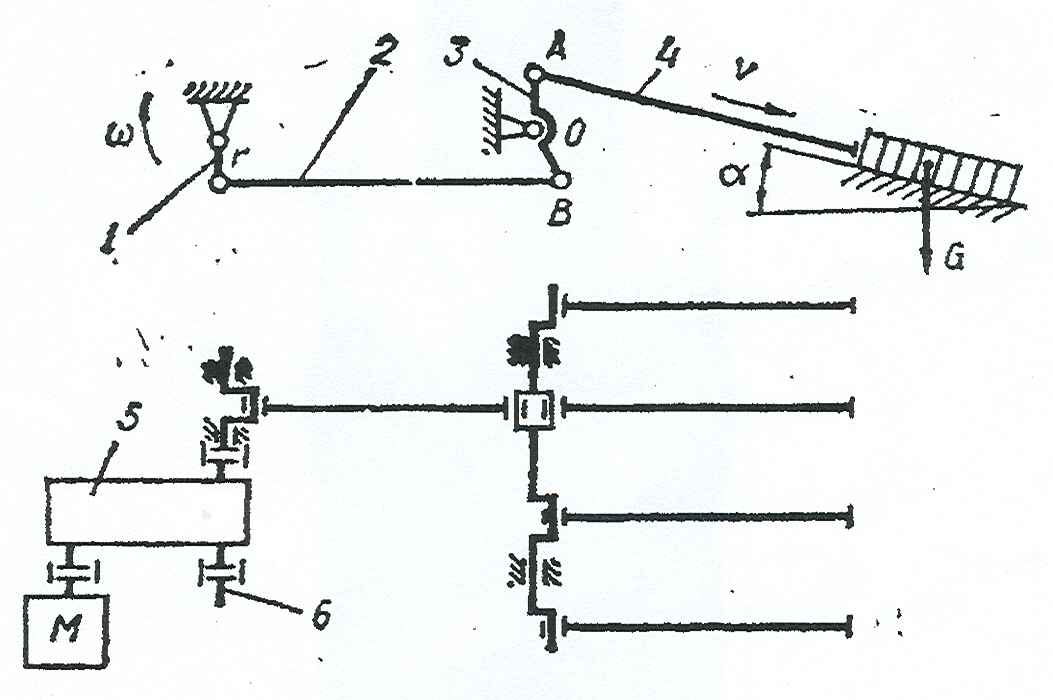
1–вал;
2–шатун;
3–важіль;
4–штанга;
5–редуктор;
6–вихідний вал редуктора
На цей же вал насаджені кілька коротких важелів, до яких одним кінцем шарнірно приєднані штовхають штанги. Штанги проходять через вікна печі і іншим кінцем ковзають по направляючої плиті всередині печі. При русі вперед штанги проштовхують через піч весь ряд довгих заготовок на величину ходу. При зворотному русі штанг між ними і кінцем ряду заготовок подається наступна заготівля, після чого цикл повторюється. Штанга розташована під кутом, який приблизно дорівнює куту нахилу печі. Хід штанги становить 500–550 мм. Тривалість робочого і холостого ходу 10 с.
На даний момент часу на стані 390 Макіївської філії ПАТ ЄМЗ
встановлено важільний штовхувач
заготовок,
конструкція якого показана на малюнку 4. За конструкцією цей штовхувач аналогічний конструкції вище
описаного типу важеля сталкивателя. Відмінності полягають у тому, що штовхувач стану 390 має
гідравлічний привід замість електромеханічного, і що штовхає штанга 1 (рис.5) рухається в напрямних
роликах 5, закріплених на рамі 4. Цей штовхувач проштовхує в піч одну заготовку, яка надходить на
крокуючі водоохолоджувані балки печі .
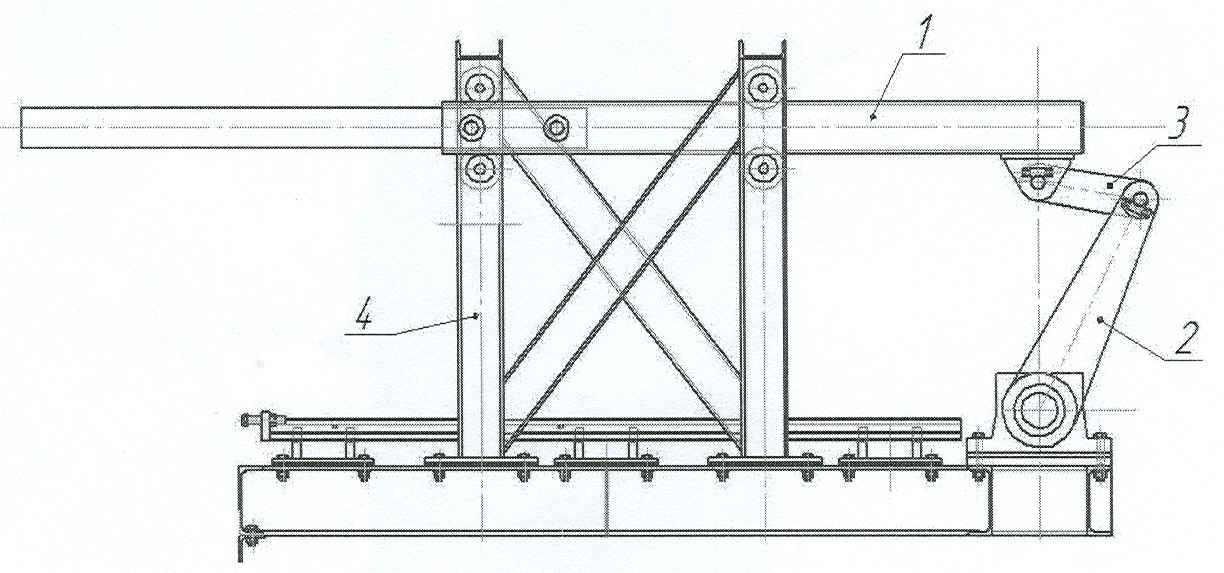
1–що штовхає штанга;
2–важіль;
3–тяга;
4–рама;
5–напрямні ролики;
6–вал
В процесі експлуатації цього сталкивателя був виявлений наступний недолік: при проштовхуванні заготовки в піч штовхають штанги 1 неодночасно вступають в роботу. Це викликано похибками при виготовленні елементів сталкивателя. В результаті цього, навантаження від зусилля зіштовхування заготовки не перерозподіляється рівномірно між штовхають штангами і, відповідно, валами 6. Це призводить до скручування валів і зрізу пальців тяг 6.
Для усунення даного недоліку пропонується жорсткі тяги 3 замінити на регульовані (рис.5). Це рішення дозволить шляхом зміни довжини тяг відрегулювати положення штовхають штанг, щоб останні одночасно вступали в роботу.
Регульована тяга складається з двох вушок, з'єднаних між собою різьбовим стрижнем. На одній стороні стрижня нарізана права різьба, на другий–ліва. Відповідно, одна проушина має праву різьбу, інша ліву. При обертанні нарізного стрижня він буде або укручуватися, або викручуватися з вушок. Таким чином, буде змінюватися довжина тяги. Для запобігання мимовільного вкручування або викручування нарізного стрижня в процесі роботи, передбачені дві стопорні гайки.
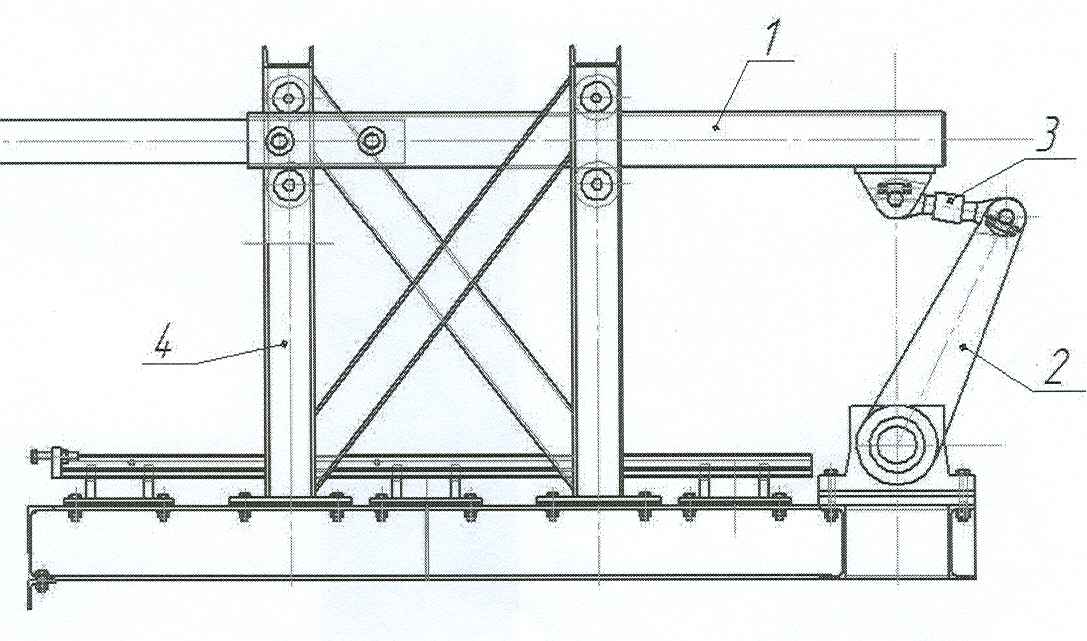
1–що штовхає штанга;
2–важіль;
3–регульована тяга;
4–рама;
5 - напрямні
ролики; 6–вал
Технічна характеристика сталкивателя стану 390:
- перетин стикаються заготовки, мм 150 × 150
- довжина стикаються заготовки, м 12
- маса стикаються заготовки m з , кг 2120
Привід сталкивателя гідравлічний
- хід h, мм 650
Цикл зіштовхування t ц , з 6
- хід вперед t в , з 3
- хід назад t н , с 3
2. Види зносу валів
В процесі експлуатації устаткування підприємств металургійної промисловості зустрічаються різні види фізичного зносу: пластичні деформації і злами; ерозійно-кавитационні, корозійні, корозійно-механічні та механічні пошкодження [2] .
Механічним зносом називають процес поступового руйнування поверхні деталей при їх відносному русі. Класифікацію механічних видів зносу розробили М.М. Хрущов [3] , І.В. Каргельскій і Е.М. Швецова [4] , Б.І. Костецький [5] та ін.
Контактіруемие поверхні деталей машин характеризуються мікрорельєфом і хвилястістю, якими в початковий момент роботи вузлів тертя визначаються площа фактичного контакту, тиск і час підробітки. В процесі експлуатації під дією робочих навантажень і деформацій утворюється робочий рельєф, що складається з западин і виступів. Їх розміри залежать від внутрішньої будови матеріалів деталей і процесів пластичної деформації. В період відносного руху в поверхневих шарах контактируемих деталей виникають упругопластические деформації, які, в свою чергу, викликають появу вторинних (фізичних, хімічних, механічних) процесів.
Професор Б.І. Костецький виділяє п'ять основних видів механічного зносу: знос схоплюванням I і II роду, окислювальний, осповідного і абразивний.
Знос схоплюванням I роду спостерігається при терті ковзання. Умови його виникнення: мала швидкість відносного руху (до 1 м / с для вузла тертя, що складається з двох сталевих деталей), високий тиск, що перевищує межу текучості на майданчиках фактичних контактів, відсутність мастила або захисної плівки оксидів і низька температура нагріву поверхневих шарів (до 100 º).
Механізм руйнування поверхонь тертя полягає в наступному. Взаємодія робочих рельєфів при тисках, що перевищують межу текучості, супроводжується інтенсивними пластичними деформаціями, в результаті яких руйнуються плівки оксидів і розкриваються хімічно чисті металеві поверхні. Крім того, пластичні деформації сприяють максимальному зближенню деталей і утворенню в поверхневих шарах текстур з гранично деформованих кристалів, розташованих у напрямку відносної швидкості. Якщо відстані гранично малі й порівнянні з розмірами атомних решіток, то між орієнтованими кристалами двох деталей з'являються металеві зв'язку (схоплювання), показані на рис. 6, а точками і лінією 1.
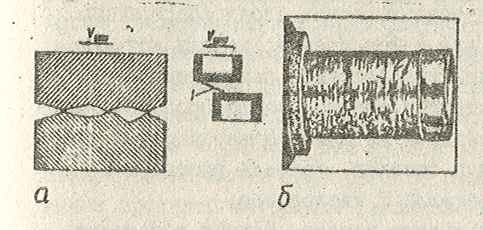
При граничних значеннях твердості і крихкості металеві зв'язки розриваються. На контактної поверхні деталі з менш міцного металу утворюються хаотично розташовані вириви, а на деталі з міцного металу - налипання. Налиплі частки високої твердості сприяють розвитку вторинних процесів місцевої пластичної деформації і мікрорізання поверхонь тертя. Зовнішній вигляд поверхні деталі, що працює в умовах зносу схоплюванням 1-го роду, показаний на рис. 6, б, де чітко видно хаотично розташовані вириви.
Швидкість зношування деталей становить 10 ... 15 мкм / год. Сили тертя визначаються геометричними характеристиками робочих рельєфів, площею контактних поверхонь і міцністю металевих зв'язків. Коефіцієнт тертя досягає 4 ... 6 од.
Окислювальний знос розвивається в умовах тертя кочення і тертя ковзання зі швидкостями відносного руху деталей 1,5 ... 7 м / с (без змащення). При граничної мастилі інтервал відносних швидкостей збільшується до 20 м / с.
Механізм руйнування поверхонь визначається складними взаємодіями матеріалів деталей з киснем навколишнього середовища: насиченням металів киснем за рахунок хімічних реакцій (хемосорбция), проникненням кисню в поверхневі шари деталей (дифузія) і розчиненням кисню в поверхневих шарах (адсорбція). Ці процеси найбільш характерні для вузлів тертя, деталі яких виготовлені з матеріалів з високою твердістю і підвищеним межею плинності. Залежно від характеру і інтенсивності процесів дифузії, адсорбції і хемосорбції основний метал в поверхневих шарах деталей може перетворюватися в плівки оксидів, тверді розчини і різні хімічні сполуки металу з киснем.
Розрізняють три форми окисного зносу. Перша характеризується безперервним освітою і руйнуванням ультрамікроскопічних плівок адсорбційних оксидів. Помітних пластичних деформацій і дифузійних явищ не відзначається. Друга форма окисного зносу проявляється при виникненні в поверхневих шарах деталей невпорядкованих твердих розчинів і евтектики хімічних сполук металу з киснем. Третя форма–суцільні плівки хімічних з'єднань металу з киснем. Зношування поверхонь полягає в періодичному появі і сколюванні твердих і тендітних хімічних сполук. Зовнішній вигляд деталі, що працює в умовах окисного зносу, показаний на рис. 7. У центрі видно матова смуга, що складається з оксидів, твердих розчинів і хімічних сполук металу з киснем.
Швидкість зношування мінімальна в порівнянні з іншими видами механічного зносу і становить 0,1 ... 0,5 мкм / год. Коефіцієнт тертя залежить від форми і коливається в межах 0,3 ... 0,7.
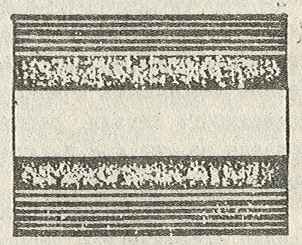
Знос схоплюванням 2-го роду. Умови його освіти: тертя ковзання, високі тиску і швидкість відносного переміщення (υ отн > 4 м / с), поєднання яких обумовлює великі втрати енергії на тертя, високий градієнт і інтенсивне зростання температури в поверхневих шарах (до 1600ºС). Механізм руйнування поверхонь залежить від інтенсивності зовнішніх механічних впливів і властивостей матеріалів деталей.
Розрізняють три стадії зносу схоплюванням 2-го роду. Перша стадія відповідає інтервалу температур, мало знижують механічні властивості матеріалів (для сталей до 600ºС). З підвищенням температури механічні властивості стали знижуються, і може наступити момент, коли тиску стануть вище фактичної межі плинності. У цьому випадку взаємодія робочих рельєфів, що супроводжується інтенсивними пластичними деформаціями, призводять до руйнування плівок оксидів і утворення металевих зв'язків. Подальший хід механізму руйнування такої ж, як і при зносі схоплюванням 1-го роду, але зовнішній вигляд поверхонь має істотну відмінність: виривання частинок на деталі з менш міцного матеріалу розташовані не хаотично, а чергуються приблизно через однакові проміжки (рис. 8, а) .
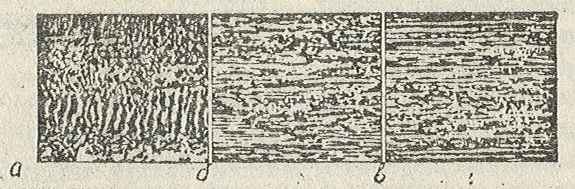
Друга стадія зносу розвивається в інтервалі температур 600 ... 1400ºС. Така температура помітно знижує механічні властивості сталей, і метал розм'якшується. Руйнування деталей характеризується контактним схоплюванням і пластичним розривом металевих зв'язків. На контактної поверхні більш міцної деталі видно налипання і розмазування металу (рис. 8, б), а на поверхні менш міцної деталі–виривання.
Третій стадії зносу відповідає температура плавлення. Розплавлені шари металу несуться зі змазкою, і на поверхнях тертя з'являються оплавлені борозенки (рис. 8, в).
Швидкість зношування деталей становить 1 ... 5 мкм / год. Коефіцієнт тертя коливається в межах 0,1 ... 0,5.
Осповідного знос виникає при терті кочення, змінних або знакозмінних навантаженнях і високому тиску, що досягають межі витривалості.
Механізм руйнування поверхонь з теорії А.К. Динника, Н.М. Бєляєва та ін. Полягає в наступному. Взаємодія двох пружних тіл з просторово-криволінійними поверхнями в обсязі металу, розташованого під точкою контакту А (рис. 9), викликає нормальні σ і дотичні τ напруження. Максимальні нормальні напруги відповідають координаті х = 0, а максимальні дотичні–координаті у = 0,7 А, тобто з'являються не на поверхнях тертя, а всередині деталей. Майданчики сумарних максимальних напружень розташовані під деяким кутом β (β <45º) до площини контакту. Багаторазові навантаження викликають втому матеріалу, і, як наслідок, на площинах максимальних напружень всередині деталі зароджуються тріщини. Їх розвиток призводить до розриву контактної поверхні, що принципово змінює характер взаємодії деталей. Рух кулі через розрив поверхні супроводжується динамічними явищами. Якщо куля рухається вліво, то ударні навантаження викликають наклеп і сколювання I ділянки по стрілці с. При русі кулі вправо спостерігається сколювання II ділянки. У місцях утворення відколів на контактних поверхнях з'являються осповідного поглиблення. Інтенсивність утворення мікротріщин залежить від напружень, що виникають в деталях в період механічної обробки, і різних концентраторів. У місцях утворення відколів на контактних поверхнях з'являються осповідного поглиблення. Інтенсивність утворення мікротріщин залежить від напружень, що виникають в деталях в період механічної обробки, і різних концентраторів. У місцях утворення відколів на контактних поверхнях з'являються осповідного поглиблення. Інтенсивність утворення мікротріщин залежить від напружень, що виникають в деталях в період механічної обробки, і різних концентраторів.
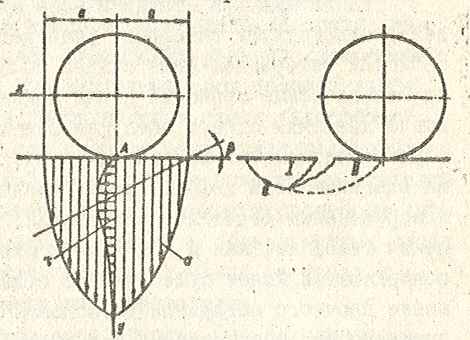
Абразивний знос розвивається при терті ковзання. Умови його виникнення: наявність на поверхнях тертя абразивних частинок, що деформують мікрооб'ємах поверхневих шарів і викликають процеси мікрорізання. Інтенсивність зношування залежить від розмірів, форми, властивостей абразивів і матеріалів деталей, від відносних швидкостей і тисків. Швидкість зношування деталей коливається в межах 0,5 ... 5 мкм / год.
Злам–руйнування деталі, що викликається низькою якістю матеріалу, дефектами виготовлення, порушеннями правил експлуатації, випадковими механічними пошкодженнями і іншими факторами. За характером навантаження деталей розрізняють статичні і втомні злами. Статичні злами виникають під дією надмірних короткочасних навантажень. Ці злами в залежності від швидкості навантаження і вихідної структури матеріалу можуть бути в'язкими і крихкими.
Втомні злами, що виникають під дією циклічних навантажень, різні за зовнішнім виглядом, проте всі вони виникають з невеликих тріщин, які, збільшуючись, повністю руйнують вал. Класифікація втомних зламів (рис. 10) запропонована проф. В.М. Гребенников [3] . Стрілками на малюнку показано напрямок поширення фронту тріщини; помірні номінальні напруги відповідають нижній половині кривої втоми, а високі–верхній половині. Така класифікація дозволяє оцінити вигляд і значення робочих навантажень, конструктивні особливості деталей, які сприятимуть розвитку втомних зламів. Вона наочно ілюструє умови зародження та розвитку тріщин і може бути використана для розробки заходів, спрямованих на зменшення поломок обладнання.
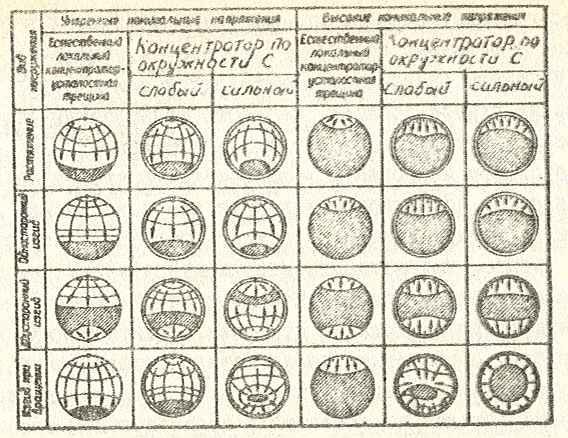
Корозійні пошкодження являють собою процес руйнування деталей внаслідок хімічного або електрохімічного взаємодії з навколишнім середовищем.
Хімічні пошкодження виникають в електрично нейтральних середовищах при реакціях між матеріалом валів і активними складовими зовнішнього середовища (наприклад, киснем, сірчистим газом). В результаті утворюються нестійкі плівки оксидів, руйнування яких під дією робочих зусиль змінює геометричні розміри деталей. Корозійні пошкодження, викликані електрохімічним впливом, спостерігається в тих випадках, коли на поверхні вала з'являються точки або ділянки з різними електричними потенціалами. Наприклад, межа і серцевина зерна, напружений і ненапружених ділянки металу, чистий метал і оксиди. Анодні ділянки мають більш високий електронний потенціал і тому піддаються руйнуванню.
Залежно від властивостей зовнішнього середовища розрізняють корозію в електролітах, атмосферну і газову. Атмосферна корозія розвивається при нормальному тиску і температурі не перевищує 80ºС. В навколишньому середовищу металургійних цехів міститься волога, різні солі, луги та кислоти, водні розчини яких є електроліт. Він осідає на деталях і сприяє утворенню мікрогальваніческіх елементів. Руйнування поверхонь валів в початковий момент має точковий характер, а в подальшому–суцільний. Зовнішнім середовищем при газовій корозії є гази, гаряче повітря і пар. Такому зносу піддаються багато деталей металургійних машин через взаємодію контактируемих поверхонь з киснем повітря.
Ерозійно-кавитационні пошкодження утворюються в період контакту деталей з потоками рідини і газу, що рухаються з великою швидкістю. Механізм руйнування поверхонь полягає в безперервній освіті плівок оксидів. Швидкість зношування деталей збільшується, якщо в потоці є тверді частинки.
Під дією корозії і механічних факторів на поверхні деталей з'являються корозійно-механічні пошкодження (корозійні втому і розтріскування, фреттинг-корозія). Корозійна втома–процес інтенсивного руйнування деталей при одночасній дії корозії і циклічних напружень. Корозійне розтріскування виникає під дією корозії і статичних напружень. Фреттинг-корозія утворюється, коли деталі, з'єднані пресової або гарячої посадкою, здійснюють малі відносні руху. Механізм руйнування деталей полягає в періодичному освіту захисних плівок оксидів на кордоні контактуючих поверхонь [2] .
Висновки. Проаналізувавши ознаки і умови виникнення видів зносу валів, а також те, що головний вал працює на кручення і вигин при змінних навантаженнях, то можна зробити висновок про втомному характері зламу головного валу в результаті виникнення і розвитку втомної тріщини. Опорні шийки головного валу схильні, перш за все, абразивного зносу через неякісні ущільнень і неправильного режиму змащування.
Список літератури
-
Радчик И., Рябков В., Сушко А. Комплексный подход к вопросам повышения надёжности работы основного и вспомогательного оборудования современного металлургического производства. Журнал
Национальная металлургия
, №1, 2006, с.24-29. -
Седуш В.Я. Надежность, ремонт и монтаж металлургических машин. – К.: НМК ВО, 1992.– 368 с.
-
Гребенник В.М. Усталостная прочность и долговечность металлургического оборудования. – М.: Машиностроение, 1969. – 256 с.
-
Хрущов М.М. Классификация условий и видов изнашивания деталей машин// Трение и износ в машинах. Сб. VIII. – М.: Изд-во АН СССР, 1953. – С. 5 – 17.
-
Швецова И.Е., Крагельский И.В. Классификация видов разрушения поверхностей деталей машин в условиях сухого и граничного трения // Трение и износ в машинах. Сб. VIII. – М.: Изд-во АН СССР, 1953. – С. 18 – 38.
-
Костецкий Б.И. Сопротивление изнашиванию деталей машин. – К.: Машгиз, 1959. – 478 с.
-
Іванченко Ф.К., Гребеник В.М., Ширяєв В.І. Розрахунок машин і механізмів прокатних цехів. – Київ: Вища школа, 1995. – 455 с.