Abstract
Contents
- Introduction
- 1. General characteristics of needle wire and needles made of it
- 2. Purpose and objectives of the study, planned results
- 3. Material, Methods and equipment for research
- 4. Study of the structure structure, microhardness and properties of wire products with thinned working part
- Conclusions
- References
Introduction
From 8 to 10% of the world's production of technical iron and steel is processed into wire. The range of products made from wire is very diverse, for example, ropes, springs, screws, nails, needles, lightning protection wire, fittings for rubber, fabrics and reinforced concrete. Every year, tens of millions of tons of wire are used. wire is a universal structural material. It is used in all branches of material production without exception, this causes a variety of properties and sizes, and mass consumption requires manufacturability and economically justified manufacturing schemes.[1].
One of the mass-consumption products made of wire are needles. Needles are divided into sewing and medical, made of high-carbon and stainless steel grades, respectively. Needles of both medical and sewing types are subject to high technological requirements. The production of needle wire of the required quality is possible under the condition of a stable and high-quality technological process at all stages of production. Domestic manufacturers of household and industrial sewing needles are forced to compete with foreign manufacturers, which produce higher-quality, but at the same time, more expensive products. In an attempt to reduce production costs, domestic manufacturers at the same time reduce the mechanical characteristics of the finished product made of needle wire [2].
Needles are used not only for sewing, with very special needles artists create etchings in the technique of "silver needle" - these are virtuoso drawings. Doctors darn the flesh of patients with needles and use the thinnest hollow tools to inject, and Eastern healers perform miracles of acupuncture. All professions can be counted [3]. But probably the most revered, needles are in Japan, where for about 1000 years, an annual festival dedicated to broken needles is held. Moreover, everyone can take part in it. During such a festival, all participants take down the broken needles and put them in a special box, at the same time, thank the needles for their good service. After that, the box is lowered into the sea forever. Thus, needles are used not only for sewing, doctors darn the flesh of patients with needles and use the thinnest hollow tools to inject, and Eastern healers perform miracles of acupuncture.
1. General characteristics of needle wire and needles made of it
Needle wire is used for the manufacture of needles for various purposes. The most famous are needles for sewing by hand. There are the following types of needle products: household needles, industrial needles, shoe needles, carpet and knitting needles. In addition, needles are divided into manual sewing (ordinary, darning, embroidery, for the blind, furrier, saddlery, etc.), machine (with a thickening at one end, which is called a flask) The range of large enterprises can include several thousand different names of needles of different thickness, shape of the tip and type of surface coating. According to the purpose of the needle is divided into:
- Sewing, which in turn are divided into manual and machine. Hand-made needles include standard needles with an eye for thread, embroidery and tailor's pins, and shoe needles. Machine needles are used in sewing machines. Sewing needles come in different sizes and shapes. When working, the size of the needle is selected, which corresponds to the structure of the material and the type of thread. The needle number is usually written in hundredths of a millimeter (70, 90, 120) — that is, the larger the number, the thicker the needle. There are needles with a smooth point — for spreading the threads of woven materials with minimal damage, and needles with sharp edges, for sewing leather, rubber, nonwovens, etc., and needles with a rounded end — for knitted fabrics, knitwear. Figure 1 shows the types of sewing needles [4].

Figure 1-machine needles (a) and household 1-rod, 2-eye, 3-tip (b)
- Medical (characteristic property — sterility):
* Injection, infusion, for the intake of biological fluids-hollow inside, designed for the introduction or intake of liquid substances from/to the object (s) of exposure. Often used with syringes and droppers [3]
* Surgical needles are classified into crosslinking for connecting biological tissues, (biopsy, puncture and ligature
o Crosslinking can be piercing, cutting, piercing-cutting, spatula-shaped, diamond-shaped, etc. Often used with a Mathieu or Hegar needle holder.
o Ligature needles have a special design with an eye at the end of the needle and a handle. They are intended for carrying out the thread in hard-to-reach places. The most common ligature needles are Reverden and Deschamps. Ligature needles are designed to bring ligatures under the vessel. Figure 1.2 shows the types of medical needles [4]
2. Purpose and objectives of the study, planned results
In our region, the range of sewing needles is quite limited. needle sizes range from 35-80 mm in length and 0.6-1.8 mm in diameter. domestic manufacturers of household and industrial sewing needles are forced to compete with the largest manufacturers. High-quality sewing needles are produced and imported to our country from europe (germany, great britain, france), japan, china. Most domestic companies prefer not to produce needles themselves, but to place orders for their manufacture in Chinese factories. they pack the finished products in their own packaging and sell them under their own brand name thus, the purpose of this work is to improve the production of machine sewing needles by improving the technological process of their manufacture[5]
3.Material, Methods and equipment for research
As a starting metal, a wire product made of low-carbon steel, presented by the Department of Physical Materials Science, was used.
Low-carbon steel is an alloy that does not contain alloyed elements, has impurities and a low carbon content, up to 0.25%. The composition of this alloy contains manganese and silicon, but due to the small percentage content (manganese-no more than 1%, silicon-no higher than 0.8%), they do not have a noticeable alloying effect on the material. Low-carbon steel is soft and low in manganese.
Table 1-Chemical composition of low-carbon steel % wt.

Figure 3 shows a general view of the wire from above.

Figure 3-general view of the wire with a diameter of 1.5 mm; 2-with a diameter of 1.1 mm
Before the test, two samples of different diameters were selected to study the microstructure and microhardness. The samples were placed in a container and filled with a solution of epoxy glue, and placed in the following sequence: 2 samples with a diameter of 1.1 and 1.5 mm in a longitudinal form, and 2 samples of the same diameter had a transverse form (Fig. 4)< / h3>
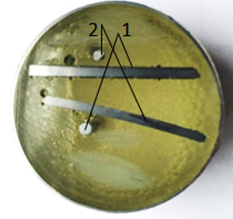
Figure 4-General view of the samples in the container: 1-samples with a diameter of 1.5 mm, longitudinal and transverse views; 2-samples with a diameter of 1.1 mm, longitudinal and transverse views.
4. Study of the structure structure, microhardness and properties of wire products with thinned working part
The microstructure was studied on the sections using a Neophot–21 microscope. The microhardness of the structural components was determined on the PMT-3 device at a load of 0.5 N. At least 3 measurements were made on each sample and the average value was calculated.
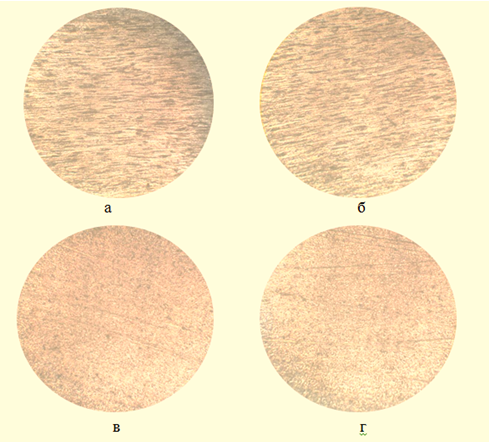
Figure 5-Initial structure of low-carbon steel wire: longitudinal section with a diameter of 1.5 mm and 1.1 mm (a, b); transverse section with a diameter of 1.5 mm and 1.1 mm (b, d), x600
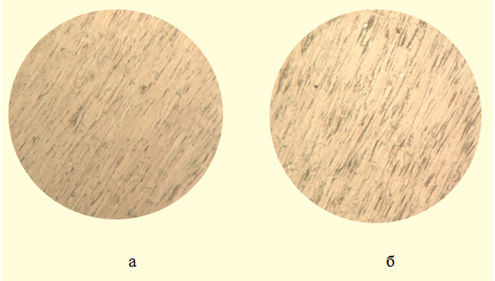
Figure 6-Initial structure of low-carbon steel wire of longitudinal sections, x1600
figures 4 to 6 show that the structure of low-carbon steel consists of a ferrite - perlite structure.
table 2-average hardness of the measured samples
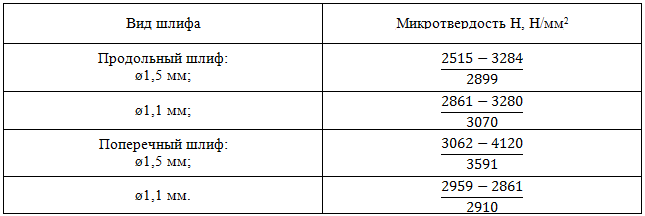
Note: ; min – minimum value; max – maximum value; average-average hardness value.
Conclusion
1. Established that one of the mass-consumption products made of wire are needles for various purposes used in the clothing and medical industries;
2. It is shown that for the production of sewing needles, tool carbon steel is mainly used, for medical needles, corrosion-resistant steels of martensitic, austenitic and austenitic-martensitic classes;
3. The optimal methods of steel smelting for needle wire are smelting in electric arc and induction vacuum furnaces. The wire billet must have increased technological plasticity. The presence of defects should be minimized;
4. To achieve the necessary mechanical characteristics of needle wire products made of high-carbon steel grades, they must have a sorbitol structure, high wear resistance and hardness. Based on the above, it is advisable to study in more depth this issue of wire products with a thinned working part, in order to increase and improve the mechanical characteristics of the wire, as well as extend the service life.
References
- Свой бизнес: производство швейных игл [Электронный ресурс] – Режим доступа: http://www.openbusiness.ru/html/dop11/shveinie-igli.htm - Загл. с экрана.
- Парусов, В.В. Усовершенствование технологии производства игольной проволоки / В.В. Парусов, В.Н. Прокофьев, И.И. Долженков, М.И. Сорокин,В.З Марченко, Н.П. Нестерова // Журн. «Сталь» - 1980. - № 12 – С. 1090 – 1092.
- Жоховский О.В. Основные направления развития машиностроения для швейной промышленности по странам-членам СЭВ «Швейная промышленность», 1975. № 4. С. 37-38.
- Сорокин В.Г. Марочник сталей и сплавов/В.Г.Сорокин, А.В. Волосникова, С.А. Вяткин и др.; под редакцией Сорокина В.Г. – М.: Машиностроение, 1989. – 640с.Гайнанов, Х.С. Почвообрабатывающее орудие / Х.С.
- Вальщиков Н.М., Зайцев Б.А., Вальщиков Ю.Н. Расчет и проектирование машин швейного производства. Л. «Машиностроение», 1973. 343 с.
- Русаков С.И., Сергевнин Н.В., Эппель С.С. Оборудование швейных фабрик. М. Гизлегпром, 1955. 464 с.
- Исаев В.В., Дремалин Н.А., Навасардян Г.С. Новые швейные машины. М. «Легкая индустрия», 1973. 126 с.
- Суховаров В.Ф., Сизова О.В., Хазанов А.А., Бухарин А.В., Царапкин А.В.,Рыжков Э.С. Авторское свидетельство SU 1293236 A1, 28.02.1987. Заявка № 3827940 от 20.12.1984.
- Алимов С.У. Исследования влияния двойной закалки на аустенитное зерно стали У8, Труды Ташкентского политехнического института, 1980. вьш. 297, с. 15-18, . Геллер Ю.А. Инструментальные стали. М.: Металлургия, 1983, с. 528.
- Алимов, В.И. Фазовые и структурные превращения при деформационно-термической обработке проволоки / В.И. Алимов, О.В. Пушкина. – Донецк: Донбасс, 2012. – 242 с.
- Маточкин, В.А. Особенности термической обработки и подготовки поверхности высокоуглеродистой катанки-проволоки при волочении / В.А. Маточкин // Журн. «Сталь» - 2007. - № 6 – С. 55 – 57.