Essay on the topic of final work
Contents
- Introduction
- 1. Purpose and objectives of the study
- 2. Research and Development Overview
- 2.1 Analysis of a boiler plant as an automation object
- 2.2 Critical review of known technical solutions for boiler plant automation
- 2.3 Development of an operating algorithm and circuit solutions for a boiler installation automation device
- 3. Development of operational requirements for an automatic control device for a boiler installation
- Conclusions
- List of sources
Introduction
Thermal power engineering occupies one of the leading positions among industrial sectors in terms of automation level. Thermal power plants are characterized by the continuity of the processes occurring in them. At the same time, the production of thermal and electrical energy at any given time must correspond to consumption (load).
Automation of steam generators includes:
1. Automatic regulation, which ensures the progress of continuously occurring processes in the steam generator (water supply, combustion, steam superheating, etc.)
2. Remote control allows the personnel on duty to start and stop the steam generator unit, switch and regulate its mechanisms at a distance, from the console where the control devices are located.
3. Technological protection.
4. Thermal control, which monitors the operation of the steam generator and equipment using indicating and recording instruments that operate automatically. The devices continuously monitor the processes occurring in the steam generator plant, or are connected to the measurement object by service personnel or an information computer. Thermal control devices are placed on panels and control panels, as convenient as possible for observation and maintenance.
5. Technological interlocks, which perform a number of operations in a given sequence when starting and stopping the mechanisms of a steam generator plant, as well as in cases where technological protection is triggered. Interlocks eliminate incorrect operations when servicing a steam generator unit and ensure that equipment is switched off in the required sequence in the event of an emergency.
6. Alarm - process alarm devices inform the personnel on duty about the state of the equipment (in operation, stopped, etc.), warn that a parameter is approaching a dangerous value, and report the occurrence of an emergency condition of the steam generator and its equipment. Sound and light alarms are used.
The operation of boilers must ensure reliable and efficient production of steam of the required parameters and safe working conditions for personnel. To meet these requirements, operation must be carried out in strict accordance with laws, rules, norms and guidelines, in particular, in accordance with the “Rules for the design and safe operation of steam boilers” of Gosgortekhnadzor, “Rules for the technical operation of power plants and networks”, “Rules for technical operation of heat-using installations and heating networks”, etc.
1. Purpose and objectives of the study
The goal of the project is to increase the efficiency of the technological process of controlling the mine boiler installation by developing an automation system for the mine boiler.
Main objectives of the study:
- Analysis of boiler installation.
- Critical review of known technical solutions.
- Justification of the direction of automation of the boiler plant.
- Development of a work algorithm.
- Development of operational requirements for an automatic control device for a boiler installation.
2. Research and Development Overview
2.1 Analysis of a boiler plant as an automation object
The work examines a gas boiler house, which consists of hot water boilers of the KVG-2.5-95 type. The boiler room is designed to feed the local heating system with a load of up to 17.4 MW.
In the water heating boiler KVG-2.5-95, as a result of combustion of gaseous fuel, water is heated to the temperature required for the vehicle of 95 ° C, which can be used in heating and ventilation systems, as well as hot water supply at industrial facilities.
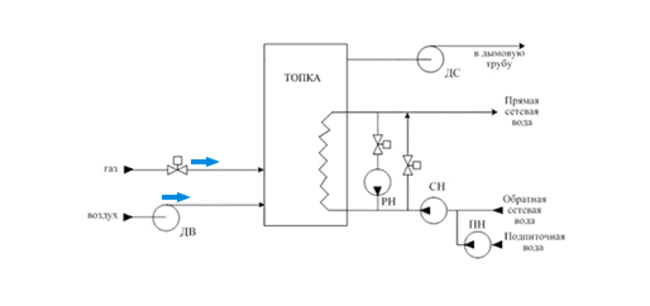
Figure 1 – General view of the principle of operation of the conveyor line
When choosing automation devices, not only factors such as functionality, performance, compatibility, scalability, resource, reliability, cost, but also compliance with the requirements of technical, fire and environmental safety of enterprise facilities should be taken into account.
The boiler room automated control system must control the facility at the time of the technological process and in the development and implementation of control solutions with the participation of modern microprocessor technology and the operator.
The KV-G-2.5-95 water heating boiler must be controlled in two modes: “local” (in case of an emergency the controller is turned off) or “remote” (the “remote” mode is set from the operator’s workstation).
The existing automated control system for the KVG-2.5-95 boiler is implemented under the control of the domestic controller AGAVA 6432.10, and the operator interface is organized using a graphic panel with touch control.
Figure 2 shows a flow diagram of the boiler room automation system.
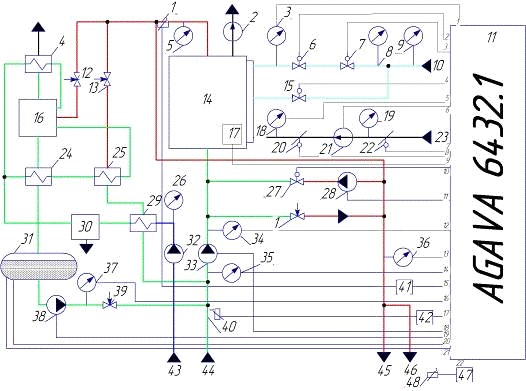
Figure 2 – Boiler room automation flow diagram
1 - exhaust gas temperature sensor; 2 - smoke exhauster; 3 - gas pressure sensor in front of the burner; 4 - vapor cooler; 5 - water supply pressure sensor; 6 - high combustion valve; 7 - low combustion valve; 8 - gas pressure sensor at the inlet; - gas pressure sensor at the inlet of the pipeline; 10 - gas supply line; 11 - microprocessor control device AGAVA 6432.1; 12 - deaerator heating valve; 13 - valve for heating the make-up heat exchangers; 14 - hot water boiler KVGM-0.5; 15 - burner pilot valve; 16 - deaerator; 17 - burner flame photosensor; 18 - vacuum sensor; 19 - air pressure sensor; 20 - MEO of air cone; 21 - discharge fan; 22 - MEO "air-2"; 23 - air supply pipeline; 24 - deaerated water cooler; 25 - heater of chemically purified water; 26 - cold water pressure sensor; 27 - controlled valve of the recirculation pump; 28 - recirculation pump; 29 - raw water heater; 30 - water treatment plant; 31 - tank - accumulator of deaerated water; 32 - deep pump; 33 - network pump; 34 - pressure sensor of the network pump; 35 - heat supply return pressure sensor; 36 - supply pressure sensor to the heating main; 37 - make-up pressure sensor; 38 - make-up pump; 39 - make-up valve; 40 - return temperature sensor; 41, 42, 47 - matching device for temperature sensors; 43 - well; 44 - return line; 45, 46 - street supply lines; 48 - external air temperature sensor.
2.2 Critical review of well-known technical solutions for boiler plant automation
Automated control system KONTUR-M for boilers of the DKVR type.
The automated control system KONTUR-M is designed to control the operation of a steam boiler of the DKVR type, transferred to the water heating mode of operation in full accordance with the boiler regime map in automatic mode.
The automatic control system for the combustion process is equipped with devices of the “Contour” system, which provide regulation of the supply of solid fuel to the furnace depending on the boiler load with adjustment for temperature in the fluidized bed, maintaining an optimal ratio of fuel and air, maintaining the required stable vacuum in the furnace. Let's take a closer look at his work below. The “Fuel” control loop contains a sensor, a regulator and starting equipment for controlling the single-turn electric motor of the fuel supply control mechanism.
Automatic adjustment of the fuel supply to the furnace is carried out according to signals from the steam pressure sensor (in the case of a steam boiler), which is an electric pressure gauge with remote transmission of the signal (readings) to the Regulator. The pressure gauge converts the steam pressure supplied from the steam boiler drum into an alternating current electrical signal. The “Air” control loop consists of a sensor, a regulator, and starting equipment for controlling a single-turn electric motor of the guide vane rotation mechanism in the pipe supplying the blower fan.
The correction signal to the regulators and the twenty-first comes from the correction device, which, in turn, receives a signal from the sensor (thermocouple). The corrective link acts as feedback. The “Vacuum” regulator ensures maintaining a constant vacuum with high accuracy. The vacuum pulse is taken in the upper part of the furnace by a sensor (draft meters), which converts the vacuum into an electrical signal sent to the regulator. From the regulator, the signal is sent to the starting equipment for controlling the single-turn electric motor of the actuator for turning the guide vane, installed in the pipe supplying the smoke exhauster. When the vacuum in the furnace changes by an amount exceeding the insensitivity of the regulator amplifier, the electric motor of the actuator moves the guide vane of the smoke exhauster until it restores the specified vacuum.
Disadvantages of the existing local regulation system: 1. Allows you to implement only simple control algorithms. 2. Allows the implementation of only panel control systems. 3. It has a low level of automation and a large number of control, measuring and converting devices, which is economically and technically impractical. 4. The system is physically and morally outdated due to wear and tear of its components. In this regard, the economic parameters and productivity of the boiler decrease, its load has to be reduced, and the reliability of the system decreases.
Automated control system for the PTVM-30 boiler
To control and protect the PTVM-30 boiler, automation panels were developed based on devices from two manufacturing companies: OWEN and MZTA. Based on MZTA devices, the following functions can be implemented in boiler automation: - gas/air ratio regulator; - vacuum regulator in the furnace; - gas pressure regulator; - burner flame control.
The main control of the system is organized using OWEN equipment. Based on devices from the OWEN company, namely using a programmable logic controller PLC100, the following functions can be implemented: 1. Automatic execution of a strictly defined boiler ignition sequence (furnace ventilation, launching a program for monitoring the tightness of gas valves, purge of the gas pipeline, checking the serviceability of protections, ignition of the igniter and the first burner of the ignition group at the operator’s command, ignition of the igniter and the second burner of the ignition group at the operator’s command, ignition subsequent burners as necessary, boiler heating, boiler operation). 2. Connection in stages of the required set of protections. 3. Diagnostics of the serviceability of the security automation. 4. Remembering the root cause of the boiler failure. 5. Diagnostics of the health of regulators, input/output modules and the PLC programmable logic controller that controls the boiler automation. 6. Control of the required number of burners turned on for the current boiler load. 7. Electronic recorder of the required boiler parameters on the operator’s PC.
The two-channel meter-regulator 2ÒÐÌ1 from OVEN is designed for measuring, recording or regulating the temperature of coolants and various media in refrigeration equipment, drying cabinets, ovens for various purposes and other technological equipment, as well as for measuring other physical parameters (weight, pressure, humidity and etc.). PID controller with universal input ARIES TRM101 is designed for measuring and regulating temperature or other physical quantities. An additional advantage of this regulator is the presence of a universal input for connecting a wide range of primary converters.
Disadvantages of the existing local regulation system: 1. They are not able to determine the rational efficiency of each NTKS firebox when they work together, taking into account the current needs of consumers. 2. They do not have the ability to forecast consumer demand for thermal energy in accordance with changing external conditions. 3. They do not allow for related regulation of the performance of the NTKS furnace according to several technological parameters. 4. They do not have the ability to rationally distribute the coolant, taking into account the current needs of each consumer.
Automated control system for water heating boiler KV-G-2.5-95
The KV-G-2.5-95 water heating boiler is designed to produce hot water with an outlet temperature of 950C, which can be used in heating and ventilation systems, as well as hot water supply at industrial facilities, housing and communal services and in agriculture sector. The KV-G-2.5-95 boiler can be used for boiler installations or in existing boiler houses when replacing exhausted steam or hot water boilers. KVG boilers have a horizontal layout and differ only in the depth of the convective shaft and combustion chamber. This affects the final performance.
Design features and diagrams:
The two main parts of the boiler are the combustion chamber and the convective flue. The heating surface consists of several U-shaped pipe structures. It consists of two sections. On the side surfaces of the flue there are coils that simultaneously serve as collectors. The combustion chamber is covered with pipes that go into the collectors. The device works as follows: 1. Water from the heating network enters the input collectors. It flows to the right and to the left, in two streams. 2. Moving along the coils, the liquid heats up and enters the output collectors. 3. The streams are then mixed and enter the rear of the combustion chamber. 4. After this, hot water flows into the heating network. You can connect any gas burners to the boilers - domestic or foreign. The only condition: they must have appropriate performance. The KV-G-2.5-95 boiler automation kit is based on the AGAVA 6432.10 microprocessor controller and belongs to the class of automated burner control systems (AAUG) in accordance with document SO 34.35.677-2003 “Technical requirements for an automated control system for burners of a gas-oil boiler , which helps to increase explosion safety when igniting burners."
Technological protection and blocking of the AGAVA 6432 controller when operating on gas fuel: 1. Automatic leak testing of gas valves. 2. Protective shutdown of burners in the event of emergency events. 3. Automatic ignition of the boiler burners. 4. Post-emergency ventilation of the furnace (at least 10 minutes). An important goal of automation is the implementation of energy-efficient control algorithms, namely, optimization of the technological parameters of the boiler according to economic, environmental, ergonomic and other indicators.
Functions for implementing energy-efficient control algorithms: 1. Automatic or remote connection of the required number of burners. 2. Automatic control of boiler power based on the water temperature at the boiler outlet or gas flow to the boiler. 3. Automatic smooth regulation of: fuel/air ratio by controlling actuators, fan guide vanes or VFDs of fan motors; vacuum in the boiler furnace by controlling the actuators of the guide vanes of smoke exhausters or VFDs of smoke exhauster engines; temperature of the water entering the boiler inlet. 4. Control and protection of the boiler when operating on reserve liquid fuel. 5. Remote or automatic control of electrified water valves at the boiler inlet/outlet, gas valves at the boiler inlet. 6. Correction of the fuel/air ratio table based on oxygen content.
Sensors used1) Pressure meters ADN, ADR are intended for: – continuous measurement of excess pressure and vacuum values air, natural and other gases that are non-aggressive to the materials of contacting parts; – generation of a current output signal of 4 – 20 mA, proportional measured parameter.
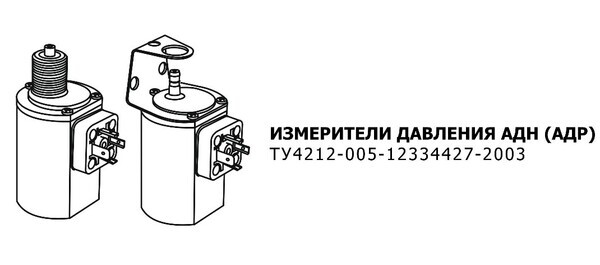
Figure 3 – Pressure sensors
2) ADP flame control sensor-relay: - works with all types of gas and liquid fuel burner boilers, furnaces and dryers; - controls the burner flame by the presence of torch pulsations; - controls the igniter torch of the control electrode.
Advantages of this boiler: - simple maintenance; - environmental friendliness (due to the use of a burner with low emissions of harmful substances); - safety; - reliability of the design; - The optimum ratio of price and quality; - quick access to the combustion chamber.
Constantly updated boiler automation "AGAVA" can be recommended for widespread implementation in the field of heat power engineering, including the reconstruction and modernization of high-power boilers. This device under development complements the basic equipment. Since all currently used mine automation equipment is morally and technically outdated, the diploma project uses a modern specialized control system based on the AGAVA PLC.
2.3 Development of an operating algorithm and circuit solutions for a boiler installation automation device
The KV-G-2.5-95 boiler automation kit is based on the AGAVA 6432.10 microprocessor controller.
The block being developed functionally complements the AGAVA PLC.
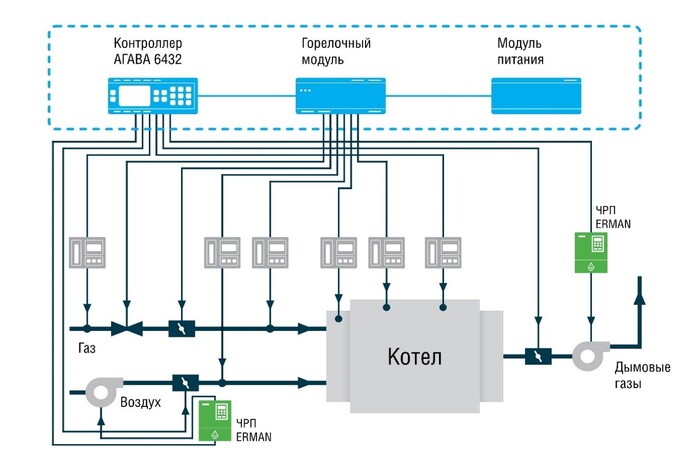
Figure 4 – Functional diagram of water heating boiler automation
An automated boiler room is developed using the latest advances in the field of automation and is an intelligent device that reduces the cost of boiler room maintenance, operation and troubleshooting. The use of duplication and automatic switching to a backup boiler allows you to operate the boiler room without interruptions in heat and water supply. The automation scheme (Fig. 4) is built on a microprocessor device AGAVA 6432.1, the control object is two water-heating, fire-tube, combination boilers KVG with universal burners RGMG-1p on natural gas or liquid fuel, with a total power of 1000 kW.
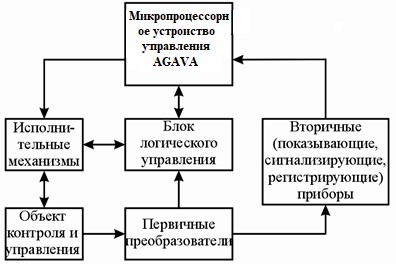
Figure 5 – Functional block diagram of the automation subsystem of the boiler installation temperature control circuit
The operating algorithm of the automated control system is shown in Figure 6. The operation of the system begins with the initialization of the initial parameters. At the next stage, the correct operation of the system and checking of emergency conditions are carried out. Then the burners are diagnosed. After heating, zone-by-zone temperature control is carried out. It is also necessary to control the pressure. To do this, the sensor is polled. The sensor readings are compared with the set parameter, and after that the pressure in the furnace is regulated. When the set value is reached, the air supply is checked and the air damper control is diagnosed. After which the sensor is interrogated again. If the pressure is greater than the target pressure - an accident, if less - control is transferred further. Water heating is controlled by polling the temperature sensor. According to the comparison condition with the specified parameters, either the damper opens or heating continues.
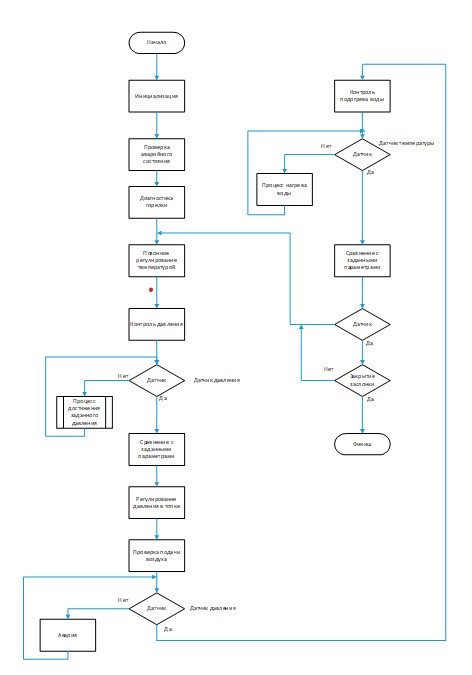
Figure 6 – Block diagram of the operation algorithm of a water heating boiler
Design of an automated boiler room control system AGAVA 6432.1
The AGAVA 6432.1 system is designed to control processes: - ignition; - power control; - protection and inspection of equipment, steam and hot water boilers and furnaces operating on gaseous and liquid fuels.
Purpose and features of the AGAVA 6432.1 controller: - hot water boiler control; - ignition – automatic; - regulation along all circuits is positional.
Resistance to impacts. Ambient temperature from +5 to +50°C. In terms of protection against the ingress of solids and water into the shell, AGAVA 6432.1 is made with a degree of protection IP41 according to GOST 14254-80. In terms of resistance to mechanical stress, the device complies with version L3 according to GOST 12997-84.
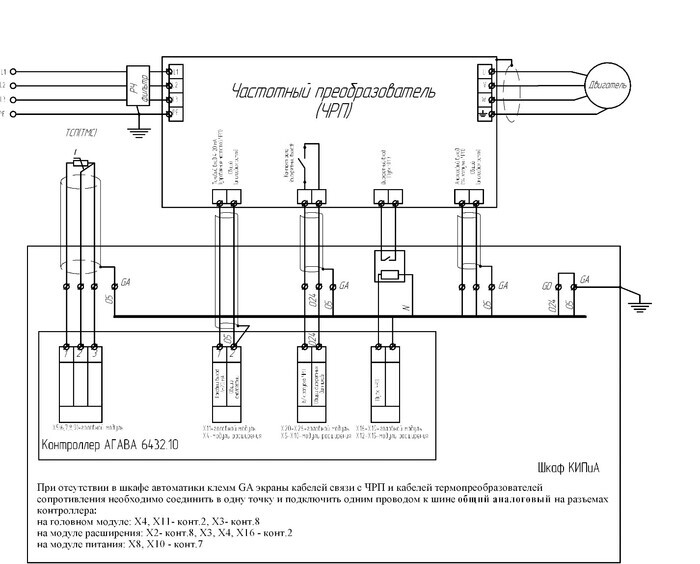
Figure 7 – Connection diagram of the VFD to the AGAVA 6432.10 controller
3. Development of operational requirements for an automatic control device for a boiler installation
The technical means of the system must be placed in places that allow servicing in accordance with the requirements of the operating instructions for these means.
Power supply to the complex of technical means of the automated control system must be provided: 1) main - from an alternating current network with a voltage of 220V + 10-15%, frequency 50 + 1 Hz; 2) backup - from an uninterruptible power supply 220V +10%. - When operating the system, you must be guided by the following directive documents: 1) “Rules for the operation of consumer electrical installations”; 2) “Safety and fire safety rules”; 3) "Rules for electrical installations" 4) “Rules for the operation of boiler installations.”
Operation of the system must be carried out in strict accordance with the requirements set forth in the documentation for the automated control system and operating instructions for individual system components.
The system being developed must satisfy the requirement of minimal maintenance.
Maintenance of system facilities must ensure round-the-clock operation and include: 1) carrying out preventive work; 2) repair and adjustment of technical equipment.
The schedule of preventive maintenance must comply with the requirements of the operational documentation for the system.
Conclusions
In the process of completing the diploma project, an analysis was carried out of the principles of constructing automation systems and the comparative characteristics of hardware produced by various manufacturers. As a result of the comparison and based on the requirements of unification and cost requirements, the choice of technical support was made in favor of the KVG 2.5-95 boiler controlled by the domestic controller AGAVA 6432.10..
When developing boiler installation automation software, all technological requirements for such systems were taken into account, as well as the requirements and wishes of the operating personnel who operate the system being developed.
Based on the results of the development of the functional structure and information model of the object, outdated measurement and automation tools were replaced with a new controller and visualization system. These changes are necessary both to achieve the goal of economical fuel consumption and ease of monitoring and control of automation processes, and to ensure the goal of increasing the productivity of the boiler house as a whole.
When writing this abstract, the master's thesis has not yet been completed. Final completion: June 2024. The full text of the work and materials on the topic can be obtained from the author or his supervisor after the specified date.
List of sources
- Sidelkovsky L.N., Yurenev V.N. Boiler installations of industrial enterprises: Textbook for universities. – 3rd ed., revised. – M.: Energoatomizdat, 1998. – 528 p.: ill.
- Batitsky V. A., Kuroyedov V. I., Ryzhkov A. A. Automation of production processes and automated process control systems in the mining industry; Textbook for technical schools. – M.: Nedra, 1991.
- Rules for electrical installations. St. Petersburg - DEAN Publishing House. – 2003. – 928 p.
- Automation of complex electromechanical objects of energy-intensive industries: a textbook for universities / K. N. Marenich [etc.]. - Donetsk: LLC "Technopark DonGTU "UNITECH", 2015. - 237 p.
- Automation of technological processes of underground mining = Automation of technological processes of underground mining robots: a textbook for universities / A. V. Bublikov [etc.] ; under general ed. V.V. Tkachev. - Dnepropetrovsk: NSU, 2012. - 304 p.
- Demchenko N.P. Technical means of information transmission in coal mine control systems. / N.P. Demchenko. - M.: Nedra, 1990. - 206 p.
- Technical requirements for mine explosion-proof electric drives with power semiconductor devices with voltage up to 1140 V: regulatory document / Kemerovo: VostNII. 1988.-17 p.
- Handbook of coal mine power engineer / [Dzyuban V.S., Shirnin I.G., Vaneev B.N., Gostishchev V.M.]; under general ed. Vaneeva B.N. – [2nd ed.] – Donetsk, Yugo-Vostok Ltd., 2001 – T1, - 447 p., T2, - 440 p.
- Gavrilov P.D. Automation of production processes: a textbook [for university students]. / [Gavrilov P.D., Gimelshein L.Ya., Medvedev A.E.] M., Nedra: 1985 - 215 p.
- Safety rules in coal mines [Electronic resource]: approved. by order of the State Mining and Technical Committee supervision of the DPR and the Ministry of Coal and Energy of the DPR 04/18/2016 No. 36/208: entry into force 05/17/2016. - Donetsk, 2016. - Access mode: https://doc.minsvyazdnr.ru/docs/2476. - Cap. from the screen.