Abstract on the topic of the final work
Content
- Introduction
- 1. Analysis of the technological process of heating workpieces in a methodical three-zone furnace as an automation object.
- 2. The purpose and objectives of the study, the planned results
- 3. A critical review of known technical solutions for automating the technological process of heating workpieces in a three-zone methodical furnace
- 4. Justification of the direction of automation of the technological process of heating workpieces in a methodical three-zone furnace
- 5. Algorithmization and circuit design solutions of the automation system
- Conclusions
- List of sources
Introduction
The technical and economic performance of methodical furnaces depends both on the technical capabilities of the furnaces and on the quality of their thermal management. The technical capabilities of a methodical furnace are determined by the totality of its design and thermal characteristics. During the operation of furnaces, these characteristics are predetermined, since they are formed during the calculation, design and construction of furnaces. Therefore, improving the performance of existing methodical furnaces can be achieved mainly by improving the process of managing their thermal regime. In terms of the functions performed, widely used thermal automation systems are similar and differ mainly only in details. With the help of existing automation systems, automatic control of the temperature of the furnace working space by zones, fuel consumption and air supplied to the burners of individual zones, and gas pressure in the zone adjacent to the outlet window, as well as automatic temperature control by zones by changing fuel consumption, automatic maintenance of a predetermined fuel-air ratio and automatic stabilization of gas pressure under the arch in the area of the window for issuing heated workpieces from the furnace. As the processes of rolling production intensified and the requirements for the quality of metal heating increased, the need for modification and expansion of the functions assigned to the automation systems of the thermal regime of methodical furnaces was revealed.
1. Analysis of the technological process of heating workpieces in a methodical three-zone furnace as an automation object.
Methodical furnaces used to heat workpieces in front of sheet rolling mills are the most common in metallurgical production.
In furnaces of this type, workpieces with a thickness of 60-400 mm, a width of 60-1850 mm and a length of 1000 to 12000 mm are usually heated, the weight of which ranges from 50 to 40,000 kg.
One of the main features of methodical furnaces is the countercurrent movement of gases and metal in them.
The heating metal is moved by a pusher through water-cooled pipes. The fuel is burned using burners located above and below the metal surface. The combustion products in two streams – upper and lower - move along the working space of the furnace in the direction opposite to the movement of the metal, i.e. counterflow. Through the smoke channels, the combustion products are removed into and out of the hog through the heat exchanger and the chimney into the atmosphere. The heated metal gets through the delivery window onto the roller and along it to the mill.
The thermal and temperature modes of operation of methodical furnaces are unchanged over time. At the same time, the temperature in the methodical furnaces varies significantly along the length of the furnace. The nature of the temperature change, depending on the required metal heating schedule, determines both the number and purpose of the furnace zones and the heat exchange mode in each of them. The cold metal enters the zone of the lowest temperatures and, moving towards the flue gases, the temperature of which is constantly rising, gradually (methodically) heats up.
The first (along the course of the metal) zone has a temperature varying in length and is called the methodical zone. No fuel is burned in this area. In it, the metal is gradually heated until it enters a heated high temperature zone (welding zone).
In order to avoid the occurrence of excessive thermal stresses, slow heating of massive bodies is necessary, in the temperature range from 0 to 500 ° C. Gradual heating of the metal in the methodical zone ensures such a heating rate at which there is no unacceptable temperature difference along the section of the workpiece.
The second (along the course of the metal) zone is called the high temperature zone or welding zone. The purpose of this zone is to quickly heat the surface of the workpiece to the final temperature of 1150 – 1250 ° C. For intensive heating of the metal surface to these temperatures in the welding zone, it is necessary to provide a temperature 150-250 ° C higher.
The third (along the course of the metal) languishing zone (holding zone) is used to equalize the temperature along the metal section and eliminate cold spots on the lower surface of the workpieces. In the welding zone, only the metal surface is heated to high temperatures; the temperature of the middle layers of the metal, of course, is much lower than the surface temperature, i.e. a temperature difference is created along the metal section, which is unacceptable according to technological requirements. The metal enters the melting zone with this temperature difference in thickness. The temperature in the melting zone is maintained only 50-70 ° C above the required final heating temperature of the metal. Therefore, the temperature of the metal surface in the melting zone practically does not change and is maintained at the level reached in the welding zone; only the temperature equalizes along the thickness of the metal under conditions of a uniformly distributed radiation regime of external heat exchange.
When regulating the thermal regime of a methodical furnace, the temperature of the workpieces at the outlet of the furnace is chosen taking into account its effect on the heating conditions of the metal, on rolling and the quality of rolled products: the higher the temperature at the outlet of the furnace, the more ductility of the metal, the less effort and energy consumption spent on its deformation during rolling, there is less wear and risk of damage to the rolling equipment, i.e. with an increase in temperature at the outlet of the furnace, the rolling conditions become more favorable. The outlet temperature required by the rolling conditions is higher, the lower the drive power of the rolling mill stands, the greater the distance from the methodical furnace to the mill and the greater the required compression.
It is usually desirable that the temperature of the rear end of the workpiece exceeds the temperature of the front end, since the rear end is in rolling for a longer time and, therefore, is cooled to a greater extent before the end of rolling. The required temperature distribution along the length of the workpiece depends on the rolling speed. So, for rolling mills of the old design, it was desirable that the temperature of the rear end of the slab should exceed the temperature of the front end by 30 C. In modern mills operating at higher rolling speeds, a smaller drop is sufficient.
The thermal mode of the furnace depends on the productivity, the speed of metal movement along the furnace, since the methodical furnace operates in the same production line with the rolling mill and the speed of metal movement depends on the rolling rate, which for short periods of time can vary widely until the mill stops, when the speed of metal movement becomes zero.
Fluctuations in the speed of metal movement lead to a change in the time during which the workpieces pass through one or another section of the furnace, and consequently, to a change in the amount of heat they receive in this section, if the temperature in the zone remains constant. When the rolling rate slows down and especially when the mill stops, this leads to overheating of the metal up to welding of the workpieces, to an increase in carbon monoxide and fuel consumption, and when the rate increases, to underheating of the metal, to stops of the mill due to the absence of heated metal.
Thus, with variable productivity of the methodical furnace, automatic temperature stabilization in the zones does not provide the required heating of the metal. In this case, the control system must determine the speed of metal movement and, when it changes, automatically change the temperature regime of the furnace in such a way as to ensure the required heating of the metal in each zone. The systems implementing such control are relatively simple, and it is advisable to use them on all methodical furnaces.
The required temperature regime in a methodical furnace depends on the rate of metal advance. In this regard, cascade systems for automatic control of the temperature regime of methodical furnaces were created. Each such system includes local temperature control systems in the heating zone and a control device that determines the speed of metal movement and, when it changes, automatically changes (corrects) the tasks for local temperature controllers in such a way as to ensure the required heating of the metal in each zone. These systems differ mainly in what parameter is used in them as a measure of the speed of metal advance or the rolling rate.
Initially, the temperature in the methodical zone of the furnace or the temperature of the exhaust gases were chosen as such a parameter, since an increase in the rate of metal movement leads to a decrease in these temperatures, and a decrease in speed leads to their increase. However, this information signal had to be abandoned, since this dependence occurs only at constant temperature conditions in heating zones. If the temperatures in the zones change, for example, due to a change in the rolling rate, then this dependence becomes ambiguous and significantly different under transient and steady-state conditions.
A more controlled parameter is the metal surface temperature, measured by a radiation pyrometer approximately in the middle of the methodical zone. There is also an inverse relationship between this temperature and the metal's rate of advance, which is more stable. In these systems, the signal of the output sensor of the potentiometer, which works in conjunction with the radiation pyrometer, is converted and supplied to the input of the temperature regulators of the welding zones, changing the setting to the required value.
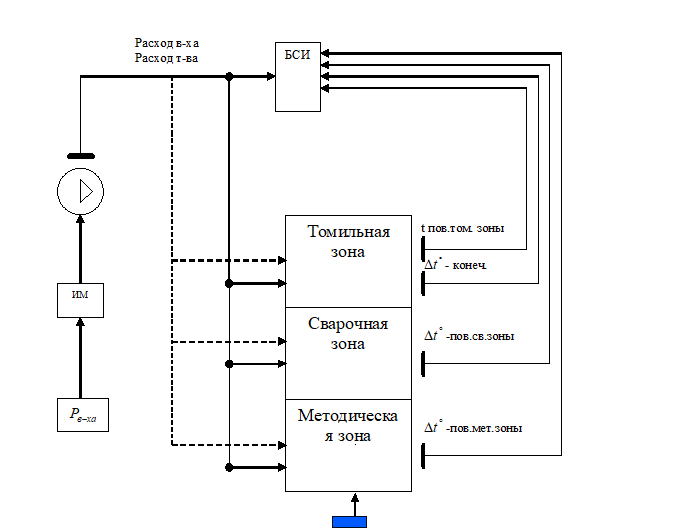
Figure 1. Technological scheme of a methodical three-zone furnace (animation: 5 frames, delay 1500 ms, 60 kilobytes)
2. The purpose and objectives of the study
The main task is to obtain a metal with a given surface temperature and a permissible temperature difference over the section under rolling conditions. It is not difficult to do this with constant furnace performance and the same parameters of the loaded metal. To do this, it is enough to stabilize the temperature in the zones. However, methodical furnaces operate in conditions far from the established ones: the furnace performance is changing, determined by the operation of the rolling mill and neighboring furnaces, the temperature, size, and grade of the loaded metal are changing. Therefore, the main task of controlling the heating process is to develop such a temperature regime of the furnace in order to constantly obtain the desired heating quality in conditions of variable unit performance, taking into account other disturbances. The controlling effect is the fuel consumption per zone, which determines the temperature in it. Additional tasks are to ensure low metal oxidation and full use of fuel in the furnace. The controlling influences are air flow and thrust, determined by the position of the gate or the guide device of the smoke pump.
Purpose of the work: development of an automatic control device for heating workpieces in a methodical three-zone furnace.
Requirements for the automation system: the need to determine the speed of metal movement and, when it changes, automatically change the temperature regime of the furnace in such a way as to ensure the necessary heating of the metal in each zone.
Device requirements: maintaining the temperature in the furnace areas; displaying information on a digital display; forecasting the heating temperature of workpieces.
3. A critical review of known technical solutions for automating the technological process of heating workpieces in a three-zone methodical furnace
The applied automation systems of the thermal regime of methodical furnaces, according to the functions performed, belong to partial automation systems. The quality and efficiency of these systems cannot be considered satisfactory. One of the main reasons is that the used systems actually lack elements of automatic control and regulation of parameters that determine the quality of metal heating: the surface temperature of the workpieces and the temperature difference along their cross section. The existing automation systems also do not have elements for automatic distribution of heat power between individual zones of the furnace.
These circumstances, however, do not indicate that the applied automation systems of the thermal regime of methodical furnaces are ineffective. Despite certain disadvantages, these systems still facilitate and improve the process of managing methodical furnaces.
The following is a description of some of the most common systems for automatic control and regulation of the thermal regime of methodical furnaces.
The system of control and automatic regulation of a three-zone furnace heated by gas with constant heat of combustion. The schematic diagram of this system is shown in Fig. 2. The scheme provides for the control and regulation of the following parameters:
1. temperatures in the working space of the languishing, upper welding zone and lower heating zone;
2. fuel–air ratio in the same zones;
3. pressure in the languishing zone, as well as control:
1. smoke temperatures after the heat exchanger;
2. Hot air temperatures after the extractor;
3. temperatures of the furnace tail section; 4. Gas and air consumption for each zone.
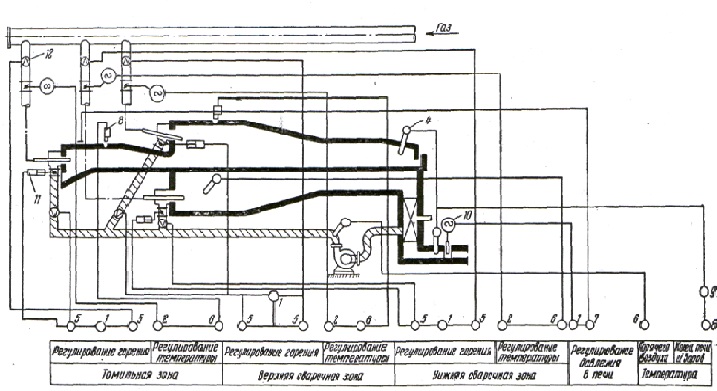
Figure 2. Schematic diagram of the automation of the thermal regime of a furnace heated with constant calorific value gas
In addition to these parameters, a number of others can be controlled (gas and air pressure, gas flow rate for the entire furnace, smoke temperature to the heat exchanger, etc.).
Automatic temperature control and regulation of the furnace zones. The schemes of automatic temperature control and regulation of all zones are of the same type. The temperature of the zones is measured by platinum–rhodium-platinum thermocouples in porcelain cases or by radiation pyrometers, which are sighted to the bottom of carbofrax glasses. Readings and recording of the zone temperature are carried out using an electronic potentiometer with an integrated rheostatic sensor. The potentiometer usually works in combination with an isodromic regulator, which uses an electric actuator to control a throttle valve located in a pipeline supplying gas to the furnace area.
When the measured temperature deviates from the set value, the regulator, acting on the valve actuator, changes the fuel consumption, trying to maintain the temperature in the zone at a set level.
Setting the temperature controller for each zone is set manually by the welder, depending on the temperature of the metal being discharged from the furnace. In the vast majority of cases, the latter is determined by eye.
Regulation of the fuel–air ratio. The schemes of automatic regulation of the fuel–air ratio are also of the same type for all zones.
The gas and air consumption for each zone is determined using measuring diaphragms. Pulse lines from the diaphragms are connected to secondary display and recording devices, as well as to the jet ratio regulator. The jet controller controls a hydraulic servo motor articulated with a throttle located in the air duct of the corresponding zone.
If the fuel–air ratio deviates from the set value, which may occur when fuel consumption changes or the task changes, the jet regulator acts on the flap in the air duct in such a way as to set the set fuel–air ratio.
Pressure regulation in the working space of the furnace. Pressure regulation is carried out by a pulse selected under the vault of the languishing zone.
An electric astatic regulator is used to regulate the pressure, which acts on the electric motor of the smoke gate winch.
The control scheme provides for the possibility of remote control of the gate position by push-button activation of the winch electric motor. The pressure control system has a manual setting of the task to the regulator.
Temperature control of the furnace zones. The temperature of the zones is measured by platinum–rhodium -platinum thermocouples connected to electric potentiometers with built-in rheostat sensors. To regulate the temperature of the zones, an isodromic regulator is used, acting through an electric actuator on the articulated control valves of the fuel oil flow and the atomizer. When the temperature deviates from the set value, the control system changes the consumption of fuel oil and the atomizer in such a way as to eliminate the deviation that has arisen.
Regulation of the fuel–air ratio. The ratio of fuel oil and air consumption is regulated by means of an electric regulator acting by means of an electric actuator on the throttle valve in the air duct of the corresponding zone.
The measuring circuit of the ratio regulator includes induction sensors from fuel oil and air flow meters, as well as a panel setpoint for the fuel–air ratio, graduated in the value of the excess air coefficient.
A constant differential flow meter is used to measure fuel oil flow, and a secondary display device with a built–in induction sensor is used for air flow.
Pressure control in the working space of the furnace. The pressure pulse is selected under the arch of the upper welding zone and transmitted to an electric astatic bell-type regulator. When the measured pressure deviates from the set value, the regulator acts on the smoke gate through an electric actuator, changing its position in such a way as to eliminate the deviation that has arisen.
The system of automatic regulation of the thermal regime of the methodical furnace.
The system of automatic control of the thermal regime of the methodical furnace (Fig. 3) includes the following automatic control units: temperature in zone 1, the ratio of fuel and air consumption per zone 2, optimization of fuel combustion in zone 3, pressure in the working space 4. Gorenje
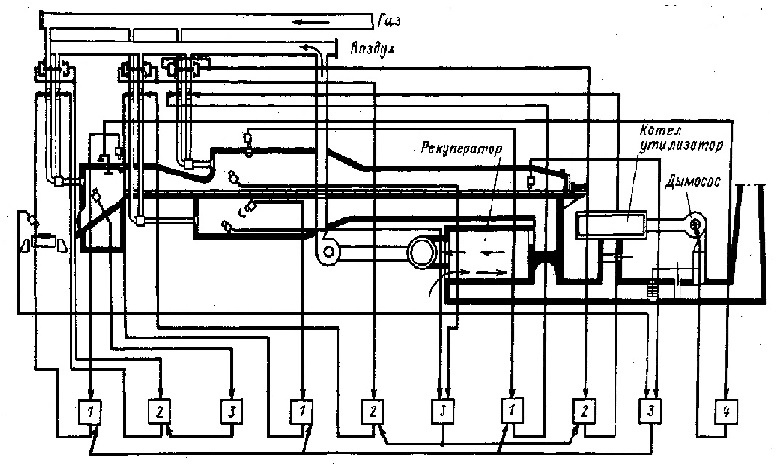
Figure 3. Diagram of the system of automatic regulation of the thermal regime of the methodical furnace
To ensure high-quality operation of the system in conditions of varying furnace performance, a node 5 is provided for correcting tasks for zonal temperature controllers.
Temperature control in the furnace area is carried out by a standard set of devices based on a signal from a thermocouple or pyrometer. By changing the fuel consumption per zone, the P- or PI-regulator adjusts the actual temperature in the furnace to the set temperature set by the welder, depending on the furnace performance, metal grade, planting temperature and heating quality. The latter parameter is estimated by the temperature of the workpiece during the rolling process on the mill, which is measured by a photoelectric pyrometer, usually installed behind the roughing cage.
When changing productivity, heating quality, and planting temperature, it is necessary to change the tasks of the zonal temperature controllers. The correction system makes adjustments to the tasks depending on the temperature of the heated metal in the methodical zone, the rate of delivery of blanks from the furnace and during furnace downtime.
The temperature of the metal in the methodical furnace during cold planting characterizes the furnace performance. Temperature measurement is carried out by a pyrometer, which is aimed at the end of the workpieces through the side wall of the furnace.
The rate of delivery of workpieces is estimated using a photorail, the sensitive head of which is aimed at the workpiece at the place of its passage at the end of the furnace.
When the furnace is stopped, the temperature in the zones and the temperature of the metal increase, which can lead to burnout and melting of the metal. The correction system on the relay elements has a circuit that gradually reduces the thermal load in the furnace in the event of a mill stop: the motor time relay turns on this circuit if a signal from the photorail does not arrive at its input within a certain interval, signaling the issuance of another workpiece.
In some circuits, instead of the temperature of the metal in the methodical zone of the furnace, a signal is sent to the correction circuit from a device measuring the temperature of the roll.
Optimal combustion mode – maintenance of the set value of the air flow coefficient is provided by a two-circuit control system. Gorenje The optimizer changes the setting of the I-regulator of the ratio for the temperature of the torch: the optimal ratio corresponds to the maximum temperature. The temperature is measured by a radiation pyrometer, which is aimed directly at the torch.
The pressure control unit in the furnace must provide a small positive pressure at the level of the workpieces, which eliminates the suction of cold air and knocking out combustion products through the working windows. Due to the operation of the burner devices and the profile of the working space, the static pressure is in the cooling zone, the highest is at the end of the loading.
A typical set of devices maintains pressure in the languishing zone – the zone of metal preparation, a small positive pressure on the hearth to exclude the cooling of heated workpieces. Pressure extraction is carried out through an opening in the roof of the furnace. The I-regulator controls the gate in front of the flue or chimney and changes the thrust in the furnace to maintain the set pressure.
On methodical furnaces equipped with metal recuperators for heating air or gas, a system of automatic protection of the recuperator or temperature control of the heated component is provided. At the signal of a thermocouple measuring the temperature of the smoke in front of the recuperator, or the temperature of the wall of its pipe, or the temperature of air and gas before being fed into the furnace, the PI controller using a control valve either reduces the temperature of the smoke by adding cold atmospheric air to it, or passes part of the combustion products through the bypass, bypassing the recuperator.
To notify personnel of violations in operation and automatic shutdown of the furnace in case of emergency situations, a sound and light alarm system is provided and the furnace is turned off in case of emergency situations, a sound and light alarm system is provided and gas and air are turned off to the furnace. The gas and air supply to the burners is cut off when the pressure of one of gorenje components drops and the power supply of the instrumentation and control equipment is turned off.
The system of automatic regulation of the thermal regime of the methodical furnace considered above has the following advantages: for better operation of the system in conditions of varying furnace performance, a task correction unit for zonal temperature controllers is provided; a sound and light alarm system is provided in case of emergency situations.
But the system also has disadvantages: outdated automation equipment, there is no information output on a digital scoreboard. The listed disadvantages in this course work will be eliminated by updating automation equipment, expanding the functions of automatic control of system parameters, a light indication unit will be developed to visualize the changing parameters of the automatic control system for heating workpieces.
4. Justification of the direction of automation of the technological process of heating workpieces in a methodical three-zone furnace
The main directionally variable parameter for controlling metal heating is the temperature of the working space. It primarily determines the heat transfer of metal, the temperature distribution in its mass, the intensity of scale formation, wear of furnace structures and other important parameters characterizing the process of heat treatment of metal and the operation of the unit. The measured temperature is the main source of information about the thermal condition of individual zones and the entire furnace as a whole. Based on this information, heating instructions are compiled, thermal calculation of zones is performed, metal heating is calculated, the temperature profile of the furnace is set, thermal and temperature conditions are controlled. The reliability of the results of solving these tasks primarily depends on what value is accepted as the temperature of the workspace, where and how it is measured.
Automatic temperature control is, as a rule, the main task of the metallurgical furnace automation system. The temperature regime, the temperature level in the furnace determine the heat transfer to the metal and, consequently, the rate of its heating, the temperature distribution in the mass of the metal, the intensity of scale formation, the wear of the furnace masonry and other important parameters characterizing the process of heat treatment of the material and the operation of the unit itself.
The existing automation systems of the thermal regime of methodical furnaces, according to the functions performed, belong to partial automation systems. The quality and efficiency of these systems cannot be considered satisfactory. One of the main reasons is that the used systems actually lack elements of automatic control and regulation of parameters that determine the quality of metal heating: the surface temperature of the workpieces and the temperature difference along their cross section. Therefore, it is necessary to strive for full automation of the control system by heating workpieces, improvement of the automation system, and improvement of work safety.
5. Algorithmization and circuit design solutions of the automation system
For a better understanding of the work of the automation system being developed, it is necessary to provide a block diagram of the algorithm of its operation. At the same time, in order to process the analog signals at the input of the device into logical signals that enter the display unit, it is necessary to identify the input and output signals.
The system of automatic control of heating of workpieces in a three-zone methodical furnace includes the following automatic control units:
- temperature in the zone;
- the ratio of fuel and air consumption per zone;
- the speed of movement of the workpieces;
- pressure in the working space.
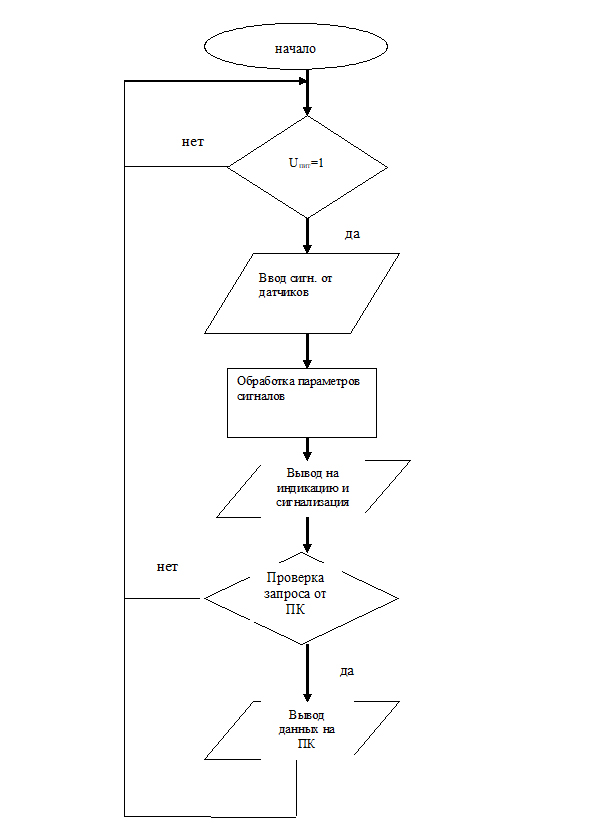
Figure 4. Block diagram of the algorithm of generalized operation of the control system
Based on the tasks assigned to the developed control and signaling unit of technological parameters, we will develop a block diagram of this device. At the same time, it should be borne in mind that there is already a power supply unit that provides the necessary levels and quality of the supply voltage.
The block diagram is shown in Fig. 5.
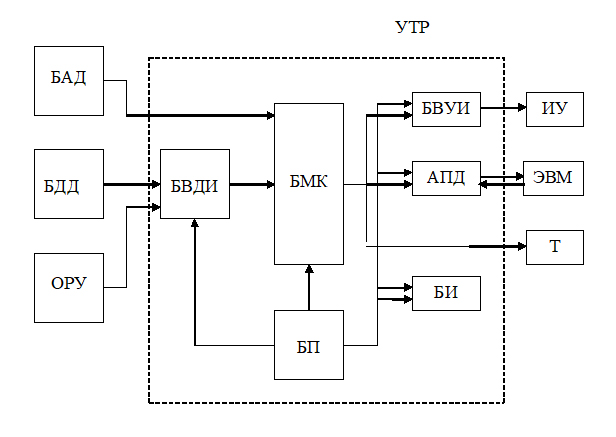
Figure 5. Block diagram of the automation system of a methodical three-zone furnace
The following designations are accepted in the scheme:
UTR – temperature control device;
PSU – power supply unit;
Dietary supplement – block of analog sensors;
BDD is a block of discrete sensors;
BMK – microcontroller;
BVDI is a discrete information input unit;
BVUI – control command output unit;
APD – data transfer adapter;
BI – display unit of the device;
IU is an executive device;
T is the display board for the furnace operator.
The automation system includes two types of sensors: analog and discrete. Analog sensors include: temperature, pressure and flow. Discrete sensors include speed. From the discrete sensor, information is sent to the BDI discrete information input unit. Next to the microcontroller. From BMK to BVUI and to the IU executive device. From the ADF data transfer adapter to the computer. From the display unit of the UTR device on the display board to the indication of the furnace operator.
Conclusions
During the project, criteria were developed for controlling the operating mode of a methodical heating furnace, according to which its optimal operation is achieved. At the same time, the boundary conditions of trouble-free operation of the furnace were also taken into account.
Taking these control criteria as a basis, a system for automatic control of the operating mode of a methodical heating furnace was developed, which meets the requirements stated for it. That is, the synthesized system allows you to regulate the operation of a methodical heating furnace in accordance with the task of optimal functioning.
An algorithm has been developed for the operation of the control system, which allows you to adjust the temperature of the heating furnace and other technological indicators based on the condition of the highest overall efficiency, provided that the specified performance is met, reduces energy losses to a minimum. Thus, the assigned task of energy saving is fulfilled. And, as a result of the work carried out, a system of automatic control of the operating mode of the methodical heating furnace will be developed, which will technically implement the management of the facility according to the developed control laws.
When writing this essay, the master's thesis has not yet been completed. Final completion: June 2024. The full text of the work and materials on the topic can be obtained from the author or his supervisor after the specified date.
List of sources
- Kazantsev E.I. Industrial furnaces. Reference guide for calculations and design – M. Metallurgy, 1975. – 368 p.
- Kaplan V. G. Commissioning and operation of furnaces for heating metal – M.: Metallurgy, 1990. – 398s.
- Butkovsky A.G.Optimal control of metal heating. M., "Metallurgy", 1972
- Revun M.P. Automatic control of metal heating. K., "Technika", 1973.
- Makovsky V.A. Control algorithms for heating furnaces. M., "Metallurgy", 1977
- M.D. Klimovitsky Automation of methodical furnaces. Moscow: Metallurgy, 1981. - 196c.
- Belenky A.M.Automatic control of metallurgical processes/ Belenky A.M., Berdyshev V.F., Blinov O.M. – M.:Metallurgy, 1989. – 384 p.
- Technical thermodynamics: Studies. For mechanical engineering. special universities/V.I. Krutov, S.I. Isaev and others; edited by V.I. Krutov.- 3rd ed., reprint. and additional- M.: Higher School, 1991. – 384 p.: ill.
- A.S. USSR "System of automatic regulation of the thermal regime of the heating furnace" 1723157 IPC C21D11/00 publ. 30.03.92, BI No.12.
- Gubinsky V.I. Metallurgical furnaces: Textbook. - Dnepropetrovsk: NMetAU, 2006. – 85 p.