Abstract on the topic of the final work
Content
- Introduction
- 1. Relevance of the topic
- 2. The purpose and objectives of the study, the planned results
- 3. Critical analysis of existing technical solutions for automation of a mine boiler plant
- 4. Justification of the direction of automation of the mine boiler plant
- 5. Development of the algorithm of operation and circuit solutions of the boiler plant automation device
- Conclusions
- List of sources
Introduction
Automation of technological processes is one of the key links in the overall system of functioning and development of any modern coal enterprise. The replacement of human intellectual labor with machine labor in this area, the scientifically based distribution of functions between a person and a computer in the process of technology management leads to an increase in the efficiency and quality of technological decisions.
The temperature inside the furnace is one of the most important technological parameters of a mine boiler plant. Its current values must be constantly monitored during the combustion process and, if it goes beyond the normal limits, adjustments and appropriate alarms must be carried out. Gorenje This control can be carried out most effectively by automating the process.
Therefore, the purpose of this thesis project is to develop a system for automating the operation of a mine boiler plant with low–temperature fluidized bed furnaces.
1. The relevance of the topic
Due to the difficult state of the fuel and energy sector, which is caused by a shortage of all types of fuel, a decrease in coal production and a decrease in its quality (coal ash content, in some places, reaches 50%), it is extremely important to solve this problem. In this situation, it is important to use boiler installations with a low-temperature fluidized bed capable of using this type of fuel.
The object of the study is a mine boiler installation with a low-temperature fluidized bed furnace. Low-temperature fluidized bed (NTCS) is successfully used for burning lean coals. The NTKS furnace is designed to create conditions for the existence of a fluidized bed and forced combustion of solid fuels with an ash content of no more than 60% and a calorific value of at least 1800 kcal / kg, with a lump size of 0-35 mm and a content of fines up to 1 mm of no more than 30%. In general, the boiler plant with the NTKS furnace is shown in Figure 1.
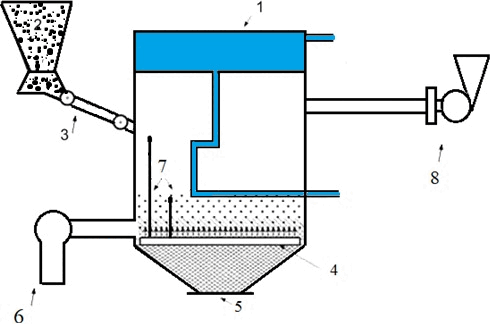
Figure 1. Technological scheme of the NTKS furnace (animation: 5 frames, delay 1250 ms, 143 kilobytes)
The following designations are accepted in the diagram:
1 - NTKS furnace;
2 - solid fuel bunker;
3 - plate feeder;
4 - air distribution grid;
5 - ash removal device;
6 - blast fan;
7 - temperature sensors;
8 - smoke exhaust.
Compared with traditional layered combustion of solid fuels, the NTCS technology has a number of advantages:
- it is possible to use low-reaction and high-ash coals with an ash content of up to 75-80%, which is unattainable with other combustion methods. This is due to the stabilization of the fuel combustion process due to the presence in the layer of a large number of heated solid particles with a high specific heat capacity;
gorenje- the thermal capacity of boilers in operation increases and the metal consumption of newly created ones decreases due to the intensification of heat and mass transfer processes in the fluidized bed;
- provides combustion of fuel with a wide range of ash content in one furnace device;
- the reliability of the furnace devices of boilers increases due to the absence of moving grates, and the design is simplified.
2. The purpose and objectives of the study
During operation of the NTCS furnace, the most important parameter to be measured is the temperature of the fluidized bed of the TCS, which, depending on the properties of the fuel, lies within 600-1000 ° C with a range of 200 ° C. Currently, thermoelectric converters are used to measure the value of TCS, which have a significant disadvantage – high inertia (the thermal inertia constant is 120-180 seconds).
The most important economic indicator of the functioning of a mine boiler plant is temperature, since maintaining a set temperature regime allows increasing the energy efficiency of the boiler plant, it is advisable to take constant operational control of this parameter as the final goal of the development.
Thus, the purpose of this work is to increase the efficiency of the mine boiler plant by developing an automation system for the mine boiler plant. The efficiency of the mine boiler plant is meant to ensure continuous stable combustion in the furnace, according to the specified technological parameters. Gorenje
The main tasks of the work are as follows:
1. Analysis of existing technical solutions in the field of automation of mine boiler installations with NTKS furnaces;
2. Investigation of technological features of a mine boiler plant;
3. Development of a mathematical model of the process of production and distribution of thermal energy;
4. Improvement of the control system of the mine boiler plant with the NTKS furnace;
5. Development of technical solutions for the implementation of the system of automatic control of heat production in the heat supply system of the mine.
3. Critical analysis of existing technical solutions for automation of a mine boiler plant
Consider the existing industrial temperature controls. The choice of a particular measurement method is determined by a number of factors, namely: the range of measured temperatures, the aggressiveness of the medium, mechanical loads on the primary converter, the dynamic properties of the process under study, as well as the necessary sensitivity and measurement accuracy. These factors are often in conflict, which makes it difficult to choose a method. The determining factor is primarily the range of measured temperatures and the required accuracy.
With the contact method, the measured temperature is judged by the temperature of the sensor element of the primary transducer. The heat sink according to the design elements of the thermal converter, radiation heat transfer, thermal inertia lead to methodological errors in converting the temperature of the medium into the temperature of the sensing element.
To reduce the methodological error, it is necessary to choose the right type and design of the primary converter and install it correctly at the research object.
In the dynamic mode, contact temperature measuring devices have dynamic errors due to the thermal inertia of the thermal converter. They are determined by the design, thermal characteristics of the converter and the medium, as well as the rate of temperature change. The contactless method does not require the placement of the primary transducer in the medium whose temperature is being measured, which eliminates distortion of the object's temperature field and makes it possible to measure the temperature of small objects, mobile objects and such environments in which long-term stable operation of primary transducers is impossible. Due to the low inertia of the primary converters, contactless methods are characterized by high performance.
Contact temperature measurement methods are based mainly on the use of thermoresistive converters, called thermal resistance converters (TC), or thermoelectric converters (TP).
Millivoltmeters or automatic DC potentiometers are used as secondary devices with TP. A distinctive feature of temperature measurement using TP is the need to stabilize the temperature of the free ends or compensate for the influence of changes in this temperature.
In many cases, the temperature of the TP head, and consequently its free ends, varies widely and its value is unknown. To reduce the impact of these changes, extension (compensation) wires are used. Since these wires are not affected by the test medium, they are made of cheaper materials than the electrodes of a thermal converter. The essence of the thermoelectric method is the occurrence of EMF in a conductor whose ends have different temperatures. In order to measure the EMF that has arisen, it is compared with the EMF of another conductor forming a thermoelectric pair AB with the first one (Fig. 2), in the circuit of which current will flow.
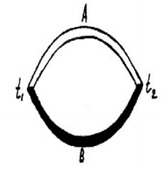
Figure 2. Thermoelectric steam
To increase the sensitivity of the thermoelectric temperature measurement method, in some cases, a thermal battery is used: several series-connected thermocouples, the working ends of which are at temperature t2, free at a known and constant temperature t1. Metran has developed a thermoelectric converter CCI. Type and design of CCI - 0192 sensors. Measured media: gaseous, oxidizing and neutral media that do not interact with the material of thermoelectrodes and do not destroy the material of protective fittings. The measured temperature ranges are from 0 to 1300 °C. The margin of error is 0.004 t(*), where t(*) is the value of the measured temperature.
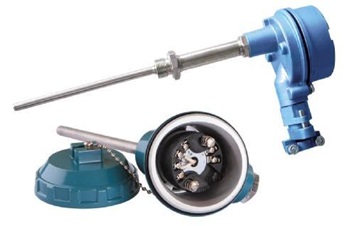
Figure 3. Thermoelectric converter "Metran"
«Elemer» has developed platinum (copper) resistance thermometers.Thermometers are designed to measure the temperature of liquid and gaseous media in explosive zones, which may contain ammonia, a nitrogen-hydrogen mixture, natural or convertible gas and its components. The nominal pressure of the measured medium is 0.4 - 16 MPa. The operating temperature range is from -50 to 500 °C.
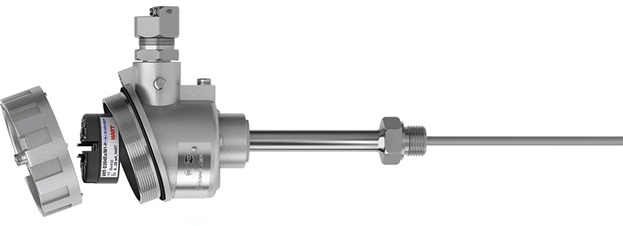
Figure 4 "Elemer" resistance thermometer
Resistance thermometers are not suitable for measuring the working area of a methodical furnace, because the range of measured temperatures is too small. Devices designed for non-contact temperature measurement, the principle of operation of which is based on the use of radiation energy from heated bodies, are called radiation pyrometers. The basic law determining the relationship between absolute temperature and spectral density, i.e. the amount of energy emitted per unit of time from a unit of body surface area and per unit of wavelength range, is Planck's law.
Pyrometers are divided into energy and spectral ratio pyrometers. Energy pyrometers include partial and full radiation pyrometers.
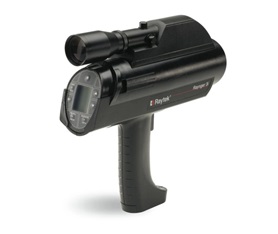
Figure 5. Portable pyrometer of the RAYNGER series of models 3i "Metran"
RAYNGER 3i is a non-contact infrared pistol-type thermometer with precise sight, having wide measurement ranges, various optical and spectral characteristics, and a wide variety of functions. 2M and 1M - for foundry and metallurgical production.
Of all the listed temperature measuring instruments, for measuring the fluidized bed temperature due to the range of variation of the measured parameter, accuracy, required measurement efficiency, as well as the cost of the sensor, the most suitable measuring instrument is a thermocouple. Namely, a platinum-rhodium thermocouple.
Let's review modern technical solutions for automation of thermal engineering facilities - the most common regulators of technological parameters.
The ML310 controller from MICROLOG SYSTEMS allows you to implement a proportional-integral-differential law for regulating a controlled parameter - temperature, pressure, air flow, natural gas, gas-air ratio, and also allows you to multiparametrically regulate process parameters, for example, temperature and pressure as a function of time. The ARIES two-channel 2TRM1 meter-regulator is designed to measure, register or regulate the temperature of heat carriers and various media in refrigeration equipment, drying cabinets, furnaces for various purposes and other technological equipment, as well as to measure other physical parameters (weight, pressure, humidity, etc.).
The PID controller with a universal input ARIES TRM101 is designed to measure and regulate temperature or other physical quantity. An additional advantage of this regulator is the presence of a universal input for connecting a wide range of primary converters.
The relay controller with timer TRM501 is designed to regulate temperature or other physical quantities in technological processes in which precise observance of time modes is required. The PID meter controller with an additional relay TRM10 is designed to measure the input parameter, pulse or analog load control according to proportional integral differential (PID) laws, as well as to generate an additional signal that can be used to signal that the parameter exceeds the set limits or two-position regulation. It is recommended to use it for controlling objects with increased inertia, where conventional two-position control does not provide the necessary accuracy.
The PID-regulator meter for controlling valves and three-way valves TRM12 is designed to automate the supply of coolant in a hot water system, gas or steam heating, to heat exchangers of pasteurizers, to control gas burners, control the position of the spool in cooling machines, as well as in other technological equipment where shut-off and control valves or three-way valves and electric gate valves. It consists of a single-channel three-position PID controller with one input for connecting a sensor and a microprocessor data processing unit, generates control signals for two output devices.
The universal eight-channel meter-regulator TRM-138 is designed for measuring, registering and regulating a physical parameter, simultaneously controlling several (up to 8) actuators, as well as for registering measured parameters on a computer.
Based on the technological features of the NTCS furnaces, the number of adjustable circuits (depending on the number of furnaces up to eight - four for regulating the vacuum pressure above the furnace and four for regulating the height of the CS) and the cost of the devices finally for use in the system under development to maintain at a given level the values of the height of the NTCS and the pressure of the vacuum universal meter-regulator TRM138.
Thus, taking into account modern technical solutions for the control of thermal parameters, we will carry out further design.
4. Justification of the direction of automation of the mine boiler plant
The object of the study of this work is the heat supply system of a mine with a boiler plant with several NTCS furnaces operating on a single collector under conditions of variable coolant flow. For furnaces of this type, hot water boilers of the DKVS or DKVR type are used. As it was determined, the purpose of the work is to develop an automated control system for NTCS furnaces in accordance with the current needs of mine consumers.
The main technological parameters of NTCS furnaces include solid fuel consumption and blast air velocity. By changing these parameters, it is possible to adjust the thermal power of the furnaces and prevent the occurrence of emergency modes - slagging or sintering of the layer. It is necessary to determine the dependence of the thermal power of the furnaces on the speed of the blast air.
Thus, the dependence between the heat generated by the furnace and its technological parameters - the consumption of solid fuel, and the speed of the blast air is derived. Therefore, by changing these parameters, we can adjust the heat output of the furnace depending on the required parameters.
From a technological point of view, it is much easier to control the operation of the furnace by changing the speed of the blast air. This indicator, as noted above, varies depending on the angle of rotation of the blades of the guide unit of the blast fan.
When adjusting the furnace capacity for solid fuel consumption, the main problem is measuring the actual values of this indicator, due to a number of factors, but this method gives a much greater economic effect, since it allows you to save solid fuel.
Thus, the following requirements must be put forward for the automation device being developed:
- temperature control of the CS;
- control of solid fuel consumption;
- control of blast air flow;
- regulating the furnace performance (CS temperature) through the solid fuel channel is the first priority;
- control of the furnace performance through the blast air channel;
- temperature control of heated rooms and forecast of the dynamics of their thermal needs;
- constructive development of a microprocessor-based device;
- availability of a remote communication interface;
- indication of the technological state of the CS furnaces.
5. Development of the algorithm of operation and circuit solutions of the boiler plant automation device
The algorithm includes several programs for the operation of individual firebox regulators.
Figure 6 shows a generalized algorithm for controlling the entire complex of the mine's heat supply system. Block 5 contains a subroutine for regulating the operation of each individual NTCS furnace in accordance with a certain capacity.
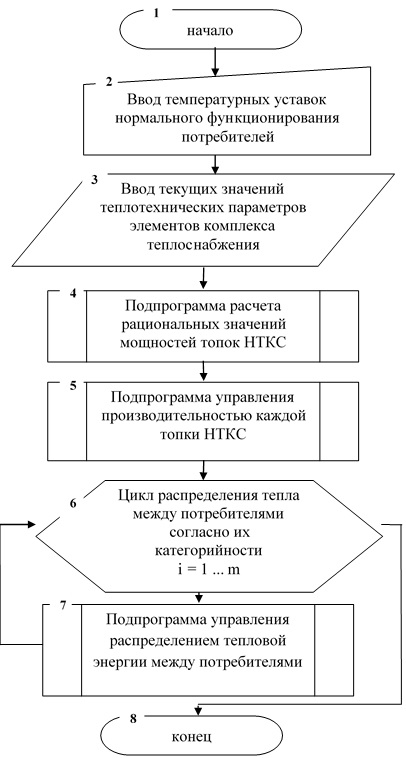
Figure 6. Algorithm for managing heat production and distribution
The number of such regulators is equal to the number of NTCS furnaces m, and a similar program is loaded into the memory of each of them, working on the basis of data received from sensors of technological parameters and from a computer. This program is similar for each regulator. Its main goal is to achieve the required capacity of the NTCS furnace, which was applied to this furnace by a computer, or by an operator based on data on the current heat consumption in the system (the amount of heat consumed), as well as data on the previous operation of the furnace (values of technological parameters for a certain period of time, was the furnace in working condition or in "reserve" etc.).
The value of the power with which the furnace should operate is loaded into the memory of the controller in the form of the setpoint of the temperature of the NTCS Tust, which the controller maintains in the furnace. This approach is justified, since there is a direct relationship between the performance of the furnace and its NTCS temperature, and therefore the ability to indirectly control the performance of each furnace, which is very important, given the difficult technological conditions of the NTCS furnaces. The functions of this program are reduced to ensuring that the required temperature of the NTCS is reached by regulating the power of the NTCS furnace by solid fuel consumption in and, after exhausting the reserve of regulation for this parameter, by adjusting the blast air velocity in V.
The priority of regulating the furnace performance is given first to regulating the consumption of solid fuel, since this is much more economical. And we switch to regulating the speed of the blast air only when the first means cannot provide the necessary control depth. In addition, the tasks of this program include the monitoring function, which ensures that the temperature of the NTCS does not exceed the limit values and, thus, prevents the occurrence of an emergency situation, as well as the issuance of information on the computer about the exhaustion of reserves of means of regulating the power of the furnace if the set capacity values are not reached. This serves as a signal to the computer about the need to recalculate the power values for each furnace, taking into account the data received from all regulators.
This program contains two subprograms - a subprogram for regulating the furnace power by solid fuel consumption and a subprogram for regulating the furnace power by blowing air velocity.
Their appearance is the same, except that when regulating the consumption of solid fuel, it is necessary to increase fuel consumption in order to increase the temperature of the NTCS, And when adjusting the speed of the blast air to increase the temperature of the NTCS, it is necessary to reduce the speed of the blast air, And vice versa.
So, the automatic control system for the operation of a mine boiler house with NTCS furnaces performs the following functions in parallel:
- determining the temperature of the NTCS of each furnace, which corresponds to the applied thermal power;
- maintaining a certain temperature of the NTCS of each furnace at a constant level by regulating the consumption of solid fuel and the speed of the blast air;
- preventing the creation of an emergency situation by preventing the release of the temperature values of the NTCS limit values.
According to the requirements for the control system, its block diagram has been developed, shown in Figure 7. As you can see, the developed automatic control system (ACS) is multilevel and consists of several lower-level subsystems, each of which is an independent element and can be developed separately from others.
Further developments will be carried out in the direction of creating a management system for the rational distribution of thermal energy between NTCS boilers.
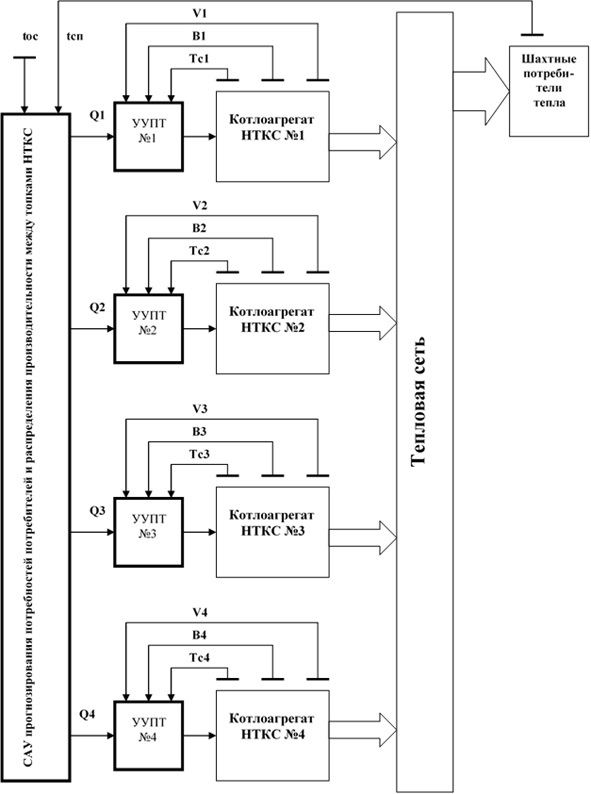
Figure 7. Block diagram of the mine heat supply management system
Conclusions
During the project, criteria were developed for controlling the operation of a mine heat supply system with several NTCS furnaces in conditions of variable coolant flow, according to which its optimal operation is achieved. At the same time, the boundary conditions of trouble-free operation of the furnaces were also taken into account.
Taking these control criteria as a basis, an automatic control system for NTCS furnaces was developed, which meets the requirements stated for it. That is, the synthesized system allows you to regulate the operation of the NTCS in accordance with the task of optimal functioning of the boiler room.
An algorithm for the operation of the control system has been developed, which allows you to adjust the temperature of the NTCS and other technological indicators based on the condition of the highest overall efficiency, provided that the specified performance is met, reduces energy losses to a minimum. Thus, the assigned task of energy saving is fulfilled.
And, as a result of the work carried out, an NTKS furnace automation device will be developed, which will be used as part of a synthesized automatic control system for the operation of a mine boiler house with NTKS furnaces, which will technically implement the management of the facility according to the developed management laws.
When writing this essay, the master's thesis has not yet been completed. Final completion: June 2024. The full text of the work and materials on the topic can be obtained from the author or his supervisor after the specified date.
List of sources
- Borodulya, V.A. Mathematical models of chemical reactors with a fluidized bed. V.A. Borodulya, Yu.P. Gupalo. - Mn.: Science and Technology, 1976, 208 p.
- Kravtsov, V. V. Economic use of coal in thermal power engineering / V. V. Kravtsov, A. G. Makhmudov, A.V. Kharchenko. – Donetsk: DonGTU, 1999. – 320 p.
- Makhorin, K. E. Combustion of fuel in a fluidized bed / K. E. Makhorin, P. A. Khinkis. – K.: Naukova dumka, 1989. – 204 p.
- Viskin, J. V. Burning coal in a fluidized bed and recycling its waste / J. V. Viskin, V. I. Sheludchenko. – Donetsk: Printing house
New World
, 1997. – 284 p. - Bednyak, G.I. Automation of production at coal mines / G.I. Bednyak, V.A., Ulshin, V.P. Dovzhenko. - K.: Technika, 1989. – 272 p.
- Gavrilenko, B. V. Criteria of the keruvannya mine heat transfer system with NTKSH furnaces.//The sciences of the Donetsk National Technical University. Series:
Girnic-mechanical
. Vipusk 83. B. V. Gavrilenko., G. E. Tkachenko. Donetsk: DonNTU, 2004, pp. 58-63. - Neezhmakov, S. V. Investigation of the mathematical model of the fluidized bed furnace of a mine autonomous air heater / S. V. Neezhmakov. // The practice of the Tavriysk state Agrotechnological University. – Vip. 8. Vol. 10. – Melitopol: TDATU, 2008. pp. 173-180.
- Borodulya, V.A. Combustion of solid fuel in a fluidized bed. V.A. Borodulya, L.M. Vinogradov. - Mn.: Science and Technology, 1980. – 192 p.
- Shafranovsky, V. A. Handbook of the adjuster of automation of boiler installations / V. A. Shafranovsky. – Simferopol: Tavria, 1987. – 176 p.
- Tolpezhnikov, L.I. Automatic control of the processes of mines and mines. L.I. Tolpezhnikov. - M.: Nedra, 1985. – 352 p.