Abstract
When writing this abstract, the master's work is not yet completed. Final completion: May-June 2024. The full text of the work and materials on the topic can be obtained from the author or his manager after the specified date.
Contents
- Introduction
- 1. Theme urgency
- 2. Goal and tasks of the research
- 3. Scientific novelty and significance of the study
- Research and Development Overview
- 4.1 Overview of national sources
- 4.2 Local Sources Overview
- 5. Requirements for raw materials
- 6. The need for coal enrichment
- 7. Purpose and classification of processes
- Conclusion
- List of used literature
Introduction
Coal mined in mines contains many impurities that reduce the quality of the mineral. Therefore, it must be separated from unnecessary mineral components.
The separation process is called enrichment - it takes place in several stages and in a wide variety of ways, including mechanical, physical and chemical methods. They make it possible to separate groups of various products from coal, such as coke, gases and liquid hydrocarbons, thereby improving the quality of coal by removing impurities and waste from it. This procedure is quite important, since the "interfering" components available in black gold give a low combustion temperature. It follows from this that it will be necessary to burn more coal, which will give a low combustion temperature.
When enriching coals, several goals are achieved: firstly, minerals and impurities are removed, and secondly, mined coal is divided into fractions in terms of grain size and grade. Only after passing these procedures and checking the quality of the final product does the coal arrive at the consumer.
1. Theme urgency
The shortage of well-coking and light-rich coals of the Donetsk People's Republic, as well as studies of the qualitative characteristics of the charge, give relevance to the topic of master's work.
2. Goal and tasks of the research
The expediency is aimed at the possibility of replacing the dry method of preparing machine classes with wet with the help of hydrotreating on stationary sieving surfaces.
In accordance with the purpose of the study, the following tasks are set:
- determine the requirements for raw materials;
- compare and analyze the methods of enrichment of the dry method of preparing machine classes and wet, using hydrography;
- establish the composition of the coal charge and factors that make it possible to obtain a better product with appropriate preparation;
- identify the reasons for insufficient quality of coal preparation at the enterprises of the Donetsk region;
- confirm the effectiveness of the selected technology.
The object of the study is the charge supplied for coking.
The subject of the study is theoretical and practical possibilities, means of improving and developing measures to improve the quality of coal preparation before coking.
3. Scientific novelty and significance of the study
Scientific novelty is theoretically justified by the choice of technology that allows to ensure high quality of coal product for coking at DPR enterprises.
The scientific significance lies in the fact that the considered technological solution, with appropriate refinement, can be based on the methods of coal enterprises.
4. Research and Development Overview
On this topic, most of the discussions and developments are carried out in the national space than in the world. Since Russia is the leading country in the world and has a dominant position in the coal industry.
4.1 Overview of national sources
СAmong national sources, there are many publications on the quality of the charge going to coking. For example, in the article "Coal Processing," published in the scientific, technical and production and economic journal "Coal," the directions of improving the quality of coking coal at the stage of the project of coal processing plants are considered. The authors propose fluidized bed technology for the production of semi-coke [1].
In the studies of Shmelzer E.O., Lyalyuk V.P. and Sokolova V.P., it was established that the strength of coke is influenced by the high moisture content of the coal charge, and the quality of preparation and its correctly selected degree of crushing is also of great importance [2].
D.A. Polulyakh in his book "Rattling Coal" notes that the most important place among the preparatory processes is rattling in the coal industry and, especially, in the enrichment of coal. He considers the basics of the theory of wet vibration, hydromechanical and hydraulic screening, and also describes the structures, technical characteristics and performance indicators of equipment used in preparatory screening [3].
4.2 Local Sources Overview
In the paper "Use of Organic Additives to Coal Charge Affecting the Quality of Metallurgical Coke," Oksak N.M. gave a characteristic of fatty and gas coals and made a comparative analysis of the effect of additives on low-sintering gas and well-sintering fatty coals, which showed that high speckability of fatty coals is associated with the accumulation of a critical amount of polycyclic aromatic hydrocarbons capable of binding into stacks that form mesophase.
Semkovsky S.V. The purpose of his work "Opportunities for improving the composition of charges for coking in modern conditions of Donbass" is to improve the composition of charges and reduce the amount of sulfur in the semi-oxide using preliminary chemical treatment.
5. Requirements for raw materials
The basis of the metallurgical process consists of two types of raw materials: ore and coal.
However, in recent years, there has been an acute shortage of coking coals in the Donbas - raw materials for coke plants producing coke for blast furnaces and iron foundries.
At the same time, well-sintered high-sulfur coals of the DNR are used only as fuel for thermal power plants, despite the huge chemical and technological potential.
Currently, coking of coal charges is carried out, which in a certain ratio include various brands and technological groups of coking coals.
The raw materials for the production of coke are hard coals and their mixtures, which are subjected to a certain thermal effect [4].
Coal is the only type of coal from which coke is obtained, which is necessary in the metallurgical industry. Accordingly, the charge for coking, according to its physico-mechanical properties, must provide the required properties of the final product - coke.
The main parameters of the technological classification of coking coals are: the yield of volatile substances (1 / g, %) and the thickness of the plastic layer (Y, mm).
6. The need for coal enrichment
Since ash is a non-combustible ballast, it is necessary to strive to obtain a smaller amount of ash coke. To do this, the extracted coal must undergo an enrichment procedure, which allows obtaining coke with minimal ash content and improving the operation of blast furnaces and foundry wagons.
Coal enrichment is a process consisting of several technological operations, as a result of which the content of harmful mineral impurities in the final product decreases, reducing the strength of coke.
The enriched product is called a concentrate, and mineral impurities having other physical constants (coefficient of thermal expansion, thermal conductivity, etc.) than coal are removed from the concentrate in the form of waste rock or in the form of coal fillers (industrial product). This is necessary so that the uniformity of the coke structure is not disturbed during the coking process, since mineral impurities become a focus of crack development [5].
Finally, the enrichment of coals contributes to the expansion of the raw material base of coking, since many coals after their enrichment significantly improve the coking ability, and they can be used for coking without compromising the quality of coke.
7. Purpose and classification of processes
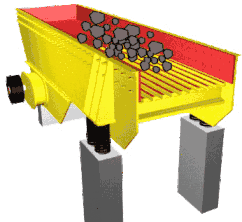
Figure 1 – Vibrating screen
(Animation. File size - 178 KB; number of frames – 8; the number of playback cycles is limited to 10.)
Screening of bulk materials can be dry, wet or in an aqueous environment.
Dry screening is carried out without adding water and is used for preliminary and preparatory screening of coal, as well as for separating dry screenings with a particle size of 0 - 6 mm from raw coal.
Wet sifting is carried out with the addition of water. During coal preparation, it is used for preliminary and fine sorting of coal and coal slurry, respectively [3].
Difficulties that arise when sifting wet coal are caused by the manifestations of capillary adhesion between individual coal grains covered with a film of water (Fig. 2)[6, 7, 8].
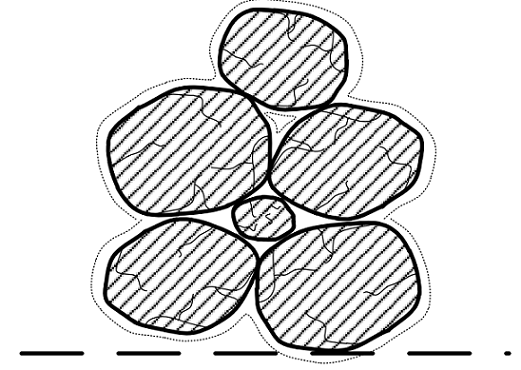
Figure 2 – Adhesion between coal grains covered with a film of water
Under the action of surface tension forces between the films of water, the wet material clumps, and as a result of the action of the same forces between the coal particles and the moistened surface of the sieve, the sieves stick.
As shown by studies [9], presented in Fig. 3, the influence of surface tension forces can be eliminated either by removing moisture during drying, or by filling intermediate volumes with liquid (wet sieving).
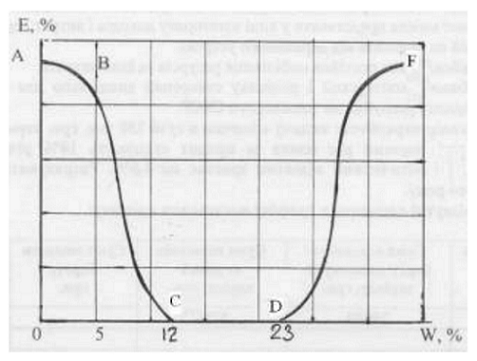
Figure 3 – Dependence of coal screening efficiency (E) on their moisture content (W): AB – dry screening; BС – sorting of wet coal; CD – no verification; DF – wet sieving.
When dry sorting wet coals, an increase in separation forks is achieved through the selection of optimal dynamic operating modes of the sieve and special materials of working surfaces, the installation of string, cantilever-cascade and other sieves, the use of centrifugal forces, and the creation of special devices for loosening sieves. material. For the same purpose, various devices and mechanisms are used to clean the working surface in the form of brushes, self-cleaning grates, rubber balls, etc. [9]. However, the problem of dry screening of wet coals at modern coal processing plants remains unresolved. This is largely due to the fact that when using electric heating of sieves and means of intensifying separation modes on a sieve operating in dry sifting mode, the forces that intensify separation act predominantly on the scattering surface of the sieve, and not on the sifted material, as a result the phenomenon of clumping is not eliminated .
Due to the fact that gas and electric heating methods, as well as aerodynamic impact on the endangered material have not yet given satisfactory results, the most acceptable method is to improve the classification of coals for production conditions with wet enrichment methods and a depth of up to 0 mm, the use of the method has been proven wet sifting [10].
The effectiveness of this screening method is explained by the fact that the elimination of capillary adhesion forces between particles and the screening surface of the screen is carried out using external impulses in the form of jets of water, simultaneously acting on both the screened material and the surface of the screen.
An important reason for the introduction of wet screening at coal processing enterprises was the need to allocate a class of 0-0.5 or 0-1 mm. The ingress of gravitational enrichment of a significant amount of grains with a size less than the lower limit of fineness (class <0.5 mm) inevitably worsens the performance of machines.
The passage of grains of class <0.5 mm through the desliming operation determines the further path of their circulation in the operations of fine category, flotation, dewatering and thickening. At the same time, this class is ground during pumping and transportation, coal grains and rocks are soaked, as a result of which its ability for further processing is lost, the physicochemical properties of water deteriorate, and coal is lost. group with an increase in enrichment waste [11].
As a result of the complete wetting of raw coal when dividing it into machine classes, conditions arose for the joint separation of fine classes with water and the direct sending of primary sludge to flotation.
Conclusion
The advantage of the wet classification method is:
– greater efficiency;
– reduction of circulation loads;
– reducing the number of technological operations without deteriorating the quality of enrichment products;
– a significant increase in the productivity of individual units.
List of used literature
- Ежемесячный научно-технический и производственно-экономический журнал «Уголь» № 12-2018 /1113/. [Электронный ресурс]. – Режим доступа:http://www.ugolinfo.ru....
- Журнал «Вестник Приазовского государственного технического университета." Научная статья: «Исследование влияния подготовки угольных шихт на качество металлургического кокса». [Электронный ресурс]. – Режим доступа:https://elibrary.ru....
- Полулях Д.А., Полулях А.Д. - «Грохочение угля»/2017г.-630 с. [Электронный ресурс]. – Режим доступа:https://fictionbook.ru....
- Филоненко Ю.Я., Кауфман А.А., Филоненко В.Ю. Теоретические основы технологии коксования каменных углей. Липецк: ЛГТУ, 2015. - 192с.
- Лекции - Коксохимическое производство – 2002г. / Лекция № 07- Обогащение углей Цель обогащения углей и размещение углеобогатительных фабрик. [Электронный ресурс]. – Режим доступа:https://studfile.net....
- Сидоренко Н.И. Интенсификация процесса грохочения влажных углей. – М.: ЦНИИУголь, 1971.
- Навроцки Е. Зависимости между силами грохочения и прилипания во влажных углях // Przeglad Gorniczy. – 1965. – № 10.
- Батель В. Новые понятия в процессах грохочения // Глюкауф. – 1955. – №14.
- Жовтюк Г.В. Исследование процесса мокрого грохочения на неподвижных колосниковых поверхностях. Дис. … канд. техн. наук. – Д., 1969.
- Neavel R.C., Larsen J.W., Wender J.//Coal Sciences. N.Y.: Acad. Press, 1982. P.1
- Митронов Д.В. Введение в химию и технологию переработки угля учебное пособие для студентов химического отделения биолого-географического факультета, электронная версия. - Якутск: ЯГУ, 2011. - 172 с.