Abstract
- Relevance of the topic
- Research and modeling of physical processes in smelting plants
- Features of processes for obtaining a liquid phase inside a cylindrical workpiece
- Simulation of melting processes of titanium alloys
- List of sources
Relevance of the topic
The topic of modeling physical processes for obtaining the liquid phase of a titanium alloy inside a cylindrical billet during induction melting is relevant and important for the production technology of titanium alloys. Titanium alloys are widely used in aviation, space, medical and other industries due to their unique properties such as strength, lightness and corrosion resistance.
Modeling physical processes during the induction melting of titanium alloy allows you to optimize the process and increase production efficiency. This allows you to reduce energy costs, reduce material losses and improve the quality of the finished product.
In addition, simulation allows us to predict the behavior of the titanium alloy inside the cylindrical billet under various melting conditions, such as temperature, induction frequency, time, etc. This helps improve the quality control process and ensure uniformity of structure and properties of the finished alloy [1].
Thus, the relevance of the topic of modeling physical processes for obtaining the liquid phase of a titanium alloy during induction melting is emphasized by its significance for modern industry and its potential impact on the economy and technological progress.
Induction melting of titanium alloys is a technology based on which an electromagnetic field is used to heat a metal material to the melting point. The process takes place in an induction melting furnace, where titanium alloys are exposed to a high-frequency alternating electromagnetic field, causing an induction heating effect.
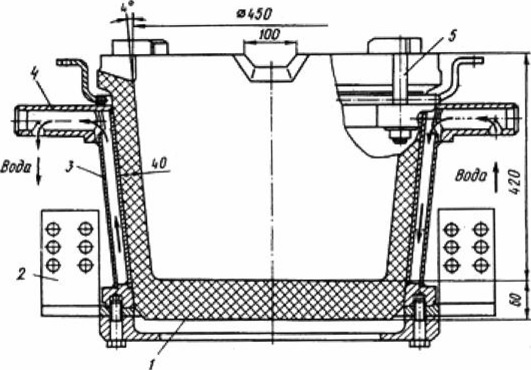
Figure 1 – Features of melting titanium alloys
The advantages of induction melting of titanium alloys include more uniform heating and higher temperatures than traditional melting methods such as fuel-fired or electric furnaces. This makes it possible to achieve higher purity and quality of fused titanium alloys.
Another advantage of induction melting is energy efficiency and faster melting times, which reduces production costs and increases productivity. It also allows for more precise control of the melting process and improved working conditions for operators.
Induction melting of titanium alloys also has the potential to reduce harmful emissions and pollution because it does not require the use of fuel or other energy sources that could release toxic substances.
Research and modeling of physical processes in smelting plants
Research and modeling of physical processes in smelting plants play an important role in the production of metallurgical materials. These processes can be complex and involve heat exchange, convection, thermodynamics, and chemical reactions. Modeling such processes allows you to optimize production processes, increase efficiency and product quality, and reduce energy intensity.
One of the main aspects of research and modeling of physical processes in smelting plants is the analysis of heat transfer and heat transfer in various parts of the plants. This includes studies of the interaction of heat with molten metals, induction heating, convection and thermodynamic processes.
Also an important aspect of research is the modeling of chemical reactions occurring in smelting plants. This includes studying the processes of oxidation and degassing of metals, the formation of alloys, and monitoring the content of volatile elements.
Research and modeling of physical processes in smelting plants are carried out using various methods, including mathematical models, computer simulations, physical experiments and technological tests [2].
In general, these studies are of great importance for the development and improvement of the metallurgical industry, as well as for increasing the efficiency and energy efficiency of production processes.
Features of processes for obtaining a liquid phase inside a cylindrical workpiece
The process of obtaining a liquid phase inside a cylindrical workpiece can be carried out in various ways, depending on specific conditions and requirements. However, there are basic features of this process that may be common to most cases:
- Use of heat. The liquid phase is usually produced by heating solid materials inside a cylindrical blank. This can be done using heating equipment such as an oven or an electric heater.
- Temperature control. An important feature of the process of obtaining the liquid phase is temperature control. This is necessary to ensure optimal conditions for the transformation of solid materials into the liquid phase and to prevent overheating or overcooling.
- Applying pressure. In some cases, pressure may be required to obtain a liquid phase. This may be necessary, for example, to increase the rate of transformation of materials into a liquid state or to ensure uniformity of the composition of the resulting liquid phase [3-5].
- Use of chemical reactions. In some cases, chemical reactions may be used to produce a liquid phase. For example, this may be the oxidation of a substance or other chemical transformations that lead to the formation of a liquid phase.
These features of the process of obtaining a liquid phase inside a cylindrical workpiece can be realized using various technologies and methods, including heat treatment, chemical processes, the use of pressure and others.
Simulation of titanium alloy melting processes
Modeling the melting processes of titanium alloys is an important part of their production. This process includes a number of technological steps that must be carefully thought out and planned to obtain a high-quality product.
Modeling of titanium alloy melting processes often includes the following main steps:
- Selection and preparation of raw materials - determining the composition of the alloy and preparing raw materials for smelting.
- Alloy smelting - the use of special melting furnaces to heat and melt a titanium alloy.
- Refining is the removal of impurities and other undesirable elements from an alloy.
- Casting is the formation of an alloy into the desired shape, for example, in the form of blanks or ingots.
Modeling of titanium alloy melting processes can be carried out using specialized software that allows you to analyze various process parameters, such as temperature, time, energy consumption and others. This helps to optimize the melting process and obtain the required product quality.
In addition, modeling the melting processes of titanium alloys allows you to explore various options for technological solutions and predict their effectiveness, which allows you to reduce risks and production costs [7].
Description of analytical methods for modeling processes
Analytical methods for modeling processes are methods of describing and analyzing a system using mathematical models. These methods make it possible to predict the behavior of a system, optimize its performance, and also study various aspects of its functioning.
Some of the main analytical methods for process modeling include:
- Analytical solution of differential equations. This method allows one to describe the dynamics of a process using mathematical equations that can be solved analytically.
- Optimization methods. They are used to determine optimal system parameters that maximize performance or minimize costs.
- Analytical modeling of queuing systems. This method is suitable for describing the behavior of systems with a large number of inputs and outputs, such as customer service systems.
- Methods of probabilistic modeling. They are used to assess the likelihood of various events and their impact on processes.
Analytical methods for process modeling allow you to explore various aspects of a system, optimize its operation and make informed decisions based on mathematical models.
o Use of software for numerical modelingNumerical modeling software is used to create mathematical models of various systems and processes and calculate them using numerical methods. Such programs are often used in engineering, physics, biology, economics and other fields of science [6].
Numerical modeling software can be used to solve a variety of problems, including analysis of structural performance, forecastingweather study, modeling of physical processes, research of biological systems, optimization of production processes and many others.
Such programs allow you to create and analyze complex mathematical models that may be difficult or impossible to solve analytically. They are usually based on numerical methods such as the finite element method, finite difference method, Monte Carlo method, etc.
Numerical simulation software can include capabilities to visualize results, automatically determine boundary conditions and material properties, and support parallelization of calculations to speed up the simulation process.
Such programs are often used for research, analysis and optimization of various systems and are an important tool for scientific work and engineering practice.
Parameters for experimental research can be defined as established and measured variables that are used to evaluate the influence of certain factors on the process or phenomenon under study. They may include various characteristics such as time, temperature, concentration, pressure, speed, mass, etc.
Defining the parameters for an experimental study usually begins with the formulation of a hypothesis and objectives of the study. The researcher then selects appropriate parameters that can be changed and controlled during the experiment. These parameters can be either independent (manipulated and changed by the researcher) or dependent (measured and recorded outcome variables).
It is also important to determine methods for measuring and manipulating parameters, as well as decide which values will serve as control values in the experiment. Correct determination of parameters for an experimental study ensures the accuracy and reliability of the results and allows one to draw correct conclusions about the influence of the factors being studied [8].
Parameters for obtaining a liquid phase inside a cylindrical workpiece:
- Pressure. To obtain a liquid phase inside a cylindrical workpiece, it is necessary to establish a certain pressure that will be sufficient for the liquid to pass into this phase.
- Temperature. It is also necessary to control the temperature inside the workpiece, since it also affects the state of the liquid. For example, an increase in temperature can cause a liquid to change into a gaseous state.
- Blank material. The material from which the cylindrical blank is made also plays an important role in obtaining the liquid phase. For example, some materials may be more suitable for maintaining a liquid phase under certain conditions.
- Shape and dimensions. The geometry of the workpiece can also influence the process of obtaining the liquid phase. For example, changing the shape or size of the workpiece can change the conditions for the formation of a liquid phase inside it.
- Processing process. Features of the process for obtaining the liquid phase, such as the effects of pressure, temperature, type of material and other processing parameters, must also be taken into account to achieve the desired result.
Carrying out smelting processes in real conditions includes several stages that must be performed taking into account all technological requirements and safety measures.
The first stage is the preparation of raw materials that will be used for smelting. This could be scrap metal, ore, or other materials, depending on the type of metal that will be obtained.
Then the melting furnace is prepared in which the smelting process will take place. This includes delivering raw materials to the kiln, diluting the fuel, maintaining optimal temperature and other preparatory work.
The next stage is the melting process itself. Metal raw materials are melted at high temperature in a smelting furnace using fuel or electricity. During this process, the metal is purified from impurities and the desired chemical component is created.
After this, the molten metal is cast into molds that correspond to the required type and size. This can be done using special equipment such as a foundry machine.
Finally, the quality of the resulting metal is controlled, it is cooled and subsequently processed in accordance with the customer's requirements.
It is important to note that during the smelting process in real conditions, it is necessary to strictly comply with all technological standards and safety rules in order to avoid possible accidents and fires.
References
- Технологии электромагнитного получения литых изделий из титана и титановых сплавов / В.Б. Демидович, П.А. Масликов, Д.А. Баранов, А.А. Ковинька // Индукционный нагрев. - 2012. - № 2(20). - С. 14-18.
- Analysis of transient heat and mass transfer processes in the melt of induction channel furnaces using LES / E. Baake, M. Langejuergen, M. Kirpo, A. Jakovics // Magnetohydrodynamics. - 2009. - Vol. 3. - P. 385-392.
- Bojarevics V., Roy A., Pericleous K. Magnetic levitation of large liquid volume // Magnetohydrodynamics. - 2010. - № 4. - Р. 317-329
- Демидович В.Б., Комракова Г.Д., Стефанов Б.В. Сравнение индукционного нагрева крупногабаритных титановых заготовок на промышленной и низкой частотах / Технология легких сплавов. – 1992. № 11-12. – С. 46-48.
- Mathematical modeling of casting processes in electromagnetic field / M. Khatsayuk, A. Minakov, V. Demidovich, M. Pervukhin // Magnetohydrodynamics. - 2015. - № 1. - Р. 57-65.
- Numerical modelling of free surface dynamics of conductive melt in the induction crucible furnace / S. Spitans, A. Jakovics, E. Baake, B. Nacke // Magnetohydrodynamics. - 2010. - № 4. - Р. 425-436.
- Pesteanu O., Baake E. The Multicell volume of fluid (MC-VOF) method for the free surface simulation of MFD flows. Part II. Experimental verifications and results // ISIJ International. - 2011. - № 5. - Р. 714-721.
- Демидович В.Б., Масликов П.А., Григорьев Е.А., Оленин В.А. Инновационные технологии обработки титановых сплавов с применением индукционного нагрева // Индукционный нагрев. – 2012. № 3 (21). – С. 26-28.