Abstract
At the time of writing this abstract, the master’s work is not completed. Estimated completion date – May 2024. The full text of the work and materials on the research can be obtained from the author or his scientific adviser after the specified date.
Content
- Introduction
- 1. Corrosion test methods
- 2. Corrosion resistance of borated steel
- 3. Experimental study of corrosion resistance of borated steel
- 3.1 Goal and objectives of the study
- 3.2 Material and methodology
- 3.3 Study of corrosion resistance of borated samples
- Conclusion
- References
Introduction
Metal corrosion is one of the most important scientific, technical and economic problems in the modern world. Economic losses from metal corrosion are enormous in scale. Damage from corrosion and the costs of combating it amounted to 1.3% of US GDP, 2.8% of German GDP. Damage from corrosion annually amounts to 2 to 4% of GNP in other developed countries. Annual metal losses from corrosion (taking into account failed metal structures, equipment, etc.) range from 10 to 20% of annual steel production.
There are many ways to combat corrosion by influencing the corrosive environment, the composition of the corroding metal, etc. The most widely used methods of protection are the application of protective metal coatings, in particular chrome plating. Such coatings provide long-term protection of products from corrosion, but require additional costs for special equipment and expensive corrosion-resistant materials.
Chemical-thermal treatment is an effective, but not often used method of protecting products from corrosion.
The purpose of the research work is to study the corrosion resistance of boride coatings in various environments to assess the possibility of their use as protective during corrosion processes.
1. Corrosion test methods
The purpose of corrosion tests is to determine the durability of steel products under operating conditions. The following tasks are solved during corrosion studies:
- disclosure of the mechanism of the corrosion process, which can be chemical, electrochemical or mixed chemical-electrochemical;
- identification of the most aggressive component of the external environment (chlorine, fluorine, sulfuric, hydrochloric acids or their acid residues, О2, СО2, пары` Н2О vapors, etc.);
- determination of control of the corrosion process (kinetic, diffusion or mixed in the case of chemical corrosion) or one of the main practical cases of control of electrochemical corrosion processes (cathode with the main role of overvoltage during the discharge of the depolarizer or its diffusion, anodic or ohmic, etc.);
- establishing the influence of the main internal (material, structure, surface condition, etc.) and external (composition of the corrosive medium, temperature, pressure, speed of movement of the medium, etc.) factors on the corrosion resistance of a metal or alloy;
- checking corrosion protection methods (determining the effectiveness of anti-corrosion alloying, the use of corrosion inhibitors or electrochemical protection, checking the reliability of protective coatings, etc.);
- checking the quality of manufactured products in terms of corrosion resistance (monitoring stainless steel for lack of susceptibility to intergranular corrosion, checking welded joints for contact corrosion, checking the quality of protective coatings, etc.) [1].
Corrosion studies are divided by nature into:
- laboratory research – study of the corrosion behavior of metal samples in artificially created conditions;
- non-laboratory studies – corrosion studies of samples under natural operating conditions;
- operational research – testing of machines, apparatus, structures and corrosion protection means under operating conditions.
Typically, laboratory tests are carried out first, then non-laboratory tests are carried out, and operational tests are carried out last. Different types of research complement each other.
Corrosion studies can be accelerated, i.e. carried out under artificial conditions, accelerating corrosion processes occurring under natural conditions. Acceleration of testing is achieved by facilitating the flow of control processes, but without changing the nature of the corrosion process. In some cases, long-term tests are carried out, corresponding to the duration of operation. Accelerated and long-term research methods complement and control each other. Comparison of the results of these studies allows us to obtain conversion factors, which eliminates the need for lengthy tests.
The corrosion resistance of metals is assessed using a ten-point scale.

Figure 1.2 – Ten-point scale of corrosion resistance of metals and alloys [2]
The figure is animated. The number of frames is 7, the number of repetitions is 7, the duration of one is 3.5 seconds.
2. Corrosion resistance of borated steel
Work [3] presents studies of the weight loss of borated and non-borated C35 steel samples in low-concentrated aqueous solutions of acids, salts and alkalis. The weight loss of borated samples as a result of experiments in 5% HCl, HNO3 и NaCl, NaOH media is negligible compared to non-borated samples. The corrosion potentials of C35 borated steel in a 5% H2SO4 solution are more electropositive than in untreated steel, as determined using electrochemical polarization curves. The authors claim that the corrosion resistance of C35 borated steel increased by 4 to 16 times compared to untreated steel.
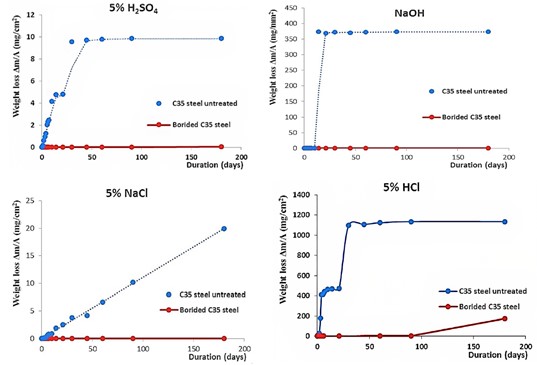
Figure 2.1 – Comparison of the rate of corrosion processes for borated and non-borated steel in acidic, neutral and alkaline solutions [3]
According to [4], borated steels are highly resistant to atmospheric corrosion. An experiment was carried out on aging samples of borated (liquid) and non-borated steel in atmospheric conditions under the influence of natural factors for one year. Control samples of unborated steel underwent significant oxidation to the point of destruction, while borated samples proved their resistance (no oxidation sites were detected when examining their surface using a microscope with х50 magnification).
The corrosion resistance of coatings based on boron nitride was studied in [5].Pulsed laser deposition of hexagonal boron nitride (hBN) films has been studied as protective coatings directly on steel to slow down corrosion processes. The microstructural, mechanical, wetting and corrosion properties of the resulting materials were studied at different application temperatures (25–800°C) and different thicknesses (35–115 nm). Corrosion studies have shown that 115 nm thick hBN coatings deposited at 600°C result in reduced corrosion rates in 3.5 wt% NaCl solution and have ~6 times greater corrosion resistance than untreated steel.
The corrosion-resistant properties of multicomponent boron-based coatings were studied in [6]. The mechanical and tribological properties of Ni–P–TiN coatings on steel are quite high. Tin particles were incorporated into a Ni–B coating matrix, and the morphology, structure, mechanical, tribological properties and corrosion resistance of the resulting composite coating were investigated as an alternative to current surface treatment coatings. According to the experimental results, the composite coating has excellent mechanical, tribological and anti-corrosion properties obtained by ensuring a compact, smooth and uniform distribution of tin particles in the Ni–B alloy matrix.
The study [7] is devoted to the analysis of the simultaneous use of homogenization and boridation to increase the hardness and corrosion resistance of stainless steel. The processes take place simultaneously at 1000°C for 1 hour; the effect of the applied heat treatment on the microstructure, phase components, hardness and wear resistance was investigated. The results showed that during the boriding process, a boride layer 30 nm thick is formed, consisting of FeB, Fe2B, Cr5B3. The wear resistance of the treated steel increased by 31.84 and 8.06 times, respectively, at room temperature and 500°C.
The use of borated steels in oil production is quite interesting. Oil production conditions are quite complex and, from a corrosion point of view, are a storehouse of corrosive factors. Well pipes, for example, are characterized by the influence of high pressures and temperatures, contact with aggressive media, both on the internal and external surfaces, wear of the internal surface under the influence of high-speed oil flows, abrasive wear of the internal surface under the influence of sand contained in crude oil, etc. The combined influence of these and many other factors leads to the appearance of local defects (cracks), in which corrosion processes develop more intensively, subsequently forming centers of corrosion damage.[8, 9]
Most protective coatings are quickly destroyed under such conditions, and according to [10], even alloys with a high content of chromium, titanium and nickel are powerless. Therefore, materials and coatings must have high corrosion resistance and wear resistance at the same time. The study [10] describes several tests, from static to dynamic, describing the behavior of borated steels in conditions and environments simulating oil production. The authors have proven the effectiveness of boriding as a protective treatment for oil production and transportation equipment, and provide information on the use of borated pipes in one of the oil wells in West Texas.
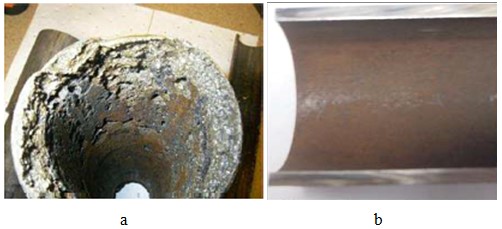
Figure 2.2 – Worn section of a pipeline for oil transportation (a) and borated section after 6 months of operation in real conditions (b) [10]
Thus, borated coatings are promising for use as protection against corrosion processes.
3. Experimental study of corrosion resistance of borated steel
3.1 Goal and objectives of the study
The purpose of the work is to study the corrosion resistance of steel subjected to boridation in acidic and neutral environments. Based on the goal, the research objectives were determined:
- study the microstructure and microhardness and some physical properties of borated samples;
- evaluate the corrosion resistance of samples in neutral and acidic environments;
- study the microstructure of samples after corrosion.
3.2 Material and methodology
Borated samples of low-carbon steel with a carbon content of 0.09–0.11% were used as the material for the study.
After cleaning the surface, plates 0.65 mm thick were packed into a container with a boron-containing mixture. Boriding was performed in a mixture of boron carbide and 2% sodium fluoride. A container with dimensions 200×250×100 mm was heated in a production furnace of the SNO/SNZ type. The thermal regime consisted of heating to 920–940° for 6 hours, followed by cooling with a furnace to 600–650° and then in air.
The density of the obtained samples was determined by the hydrostatic method. Electrical resistivity was determined using a double Thomson bridge.
The microstructure and microhardness were studied on transverse sections, which were made using a clamp. Microhardness was measured using a PMT-3 device at a load of 50 g.
Corrosion tests were carried out in acidic (1% H2SO4 solution) and neutral environments (3% NaCl solution).
The samples were immersed in solutions so that the outer surface was wetted by the liquid. The samples were turned over every day.
Corrosion resistance was assessed by mass index:

where Δm – loss in sample mass over the test period, g; S – sample surface area, м2; τ – test duration, h.
Transverse sections were made on the samples to assess corrosion damage after exposure to corrosive environments. To make sections, the plates under study were clamped into a clamp and ground using sandpaper with a gradual increase in grain size and polished on a polishing wheel using a chromium oxide suspension. Etching of thin sections was carried out in a 4% solution of nitric acid in ethyl alcohol.
3.3 Study of corrosion resistance of borated samples
The results of changes in the mass of borated samples during the corrosion test are presented in Figure 3.1.
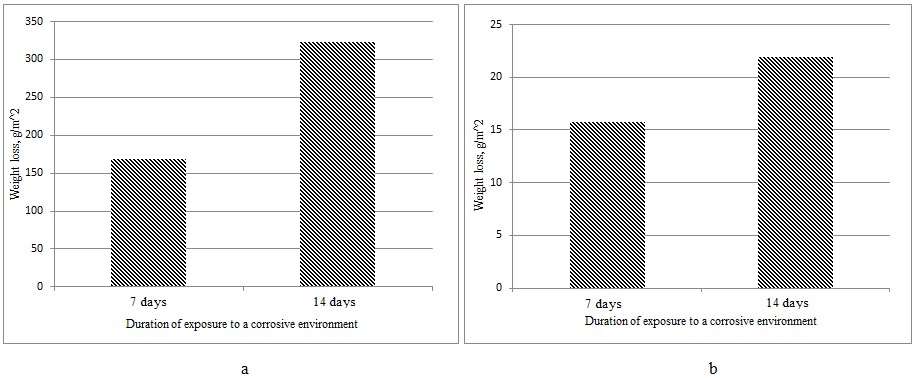
Figure 3.1 – Changes in the mass of borated samples when tested in an acidic (a) and neutral (b) environment
Thus, weight loss occurs quite actively during corrosion in an acidic environment (≈ 0.29 g and 0.19 g for samples No. 1 and 3, respectively), while losses from corrosion are quite small in a neutral environment (≈ 0.03 g and 0.01 g for samples No. 2 and 4, respectively).
Corrosion damage was assessed on transverse sections. The microstructures are shown in Figures 3.2 and 3.3. Corrosion damage in the form of elongated pores is clearly visible on samples tested in an acidic environment.
The location of the pores suggests that the destruction began with the dissolution of sections of the layer between the boride needles. Large pear-shaped pores were formed as a result of chipping of borides from the matrix during the preparation of a thin section. The heterogeneity of corrosion damage on different sides of the sample is caused by different corrosion conditions for the bottom and top sides of the sample. The corrosive activity of the environment changes over time, so the constancy of the test conditions is quite difficult to maintain.
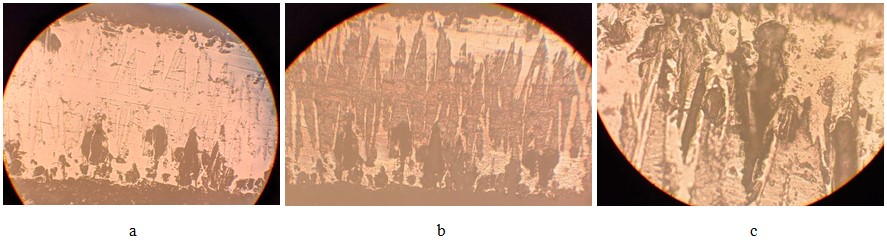
Figure 3.2 – Microstructure of a borated sample after corrosion in an acidic environment without etching (a) and after etching with nital (b, c) (a, b – x270; c – x600)
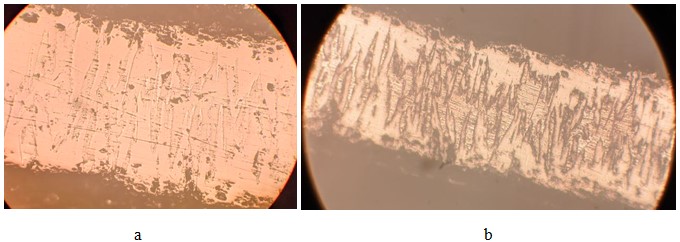
Figure 3.3 – Microstructure of a borated sample after corrosion in a neutral environment without etching (a) and after etching with nital (b), x270
The depth of corrosion damage exceeds the depth of the borated layer. On one of the samples, delamination was observed due to partial dissolution of the steel base of the sample.
Corrosion damage to samples in a neutral environment is much less, the depth of damage does not exceed 40–50 microns. Accordingly, weight loss during corrosion is much lower.
Thus, boriding makes it possible to increase the corrosion resistance of steel by 15.1 times in neutral and 5.9 times in acidic environments. The corrosion resistance of borated samples in an acidic environment is 14.8 times lower than in a neutral environment. Predominant destruction of the steel matrix with subsequent spalling of borides occurs in an acidic environment.
Conclusion
Metal corrosion is one of the most pressing problems of our time. It causes irreparable damage to all industries, disabling equipment, thereby deteriorating productivity and, in some cases, the quality of enterprise products. Metallurgy and mechanical engineering enterprises suffer the most, since they are faced with the task of restoring and updating products and mechanisms damaged by corrosion.
Boron-based coatings are known for their particularly high wear resistance due to their high surface hardness. Despite the greater interest in wear resistance, boride coatings have proven their corrosion resistance through testing in corrosive environments of various compositions and aggressiveness, which allows them to be considered as protective coatings to withstand corrosive influences.
As a result of experimental studies, a higher corrosion resistance of boride coatings in neutral environments compared to acidic ones was revealed, and increased corrosion resistance of borated steel compared to untreated steel was established (15.1 times in neutral and 5.9 times in acidic environments).
The corrosion process develops between boride needles on the substrate material; this was revealed as a result of analysis of the microstructure of borated steel after exposure to corrosive environments. Presumably, this development of corrosion processes causes external mechanical damage to the boride layer.
References
- Россина, Н. Г. Коррозия и защита металлов. В 2 ч. Ч. 1. Методы исследований коррозионных процессов / Н. Г. Россина, Н. А. Попов, М.А. Жилякова, – Екатеринбург : Изд-во Урал. ун-та, 2019. – 108 с.
- Луканина, Т. Л. Химическое сопротивление материалов и защита от коррозии / Т. Л. Луканина, И. С. Михайлова, М. А. Радин – Санкт-Петербург : Изд-во СПбГТУРП, 2014. – 85 с.
- Effect of Boriding Treatment on the Corrosion Behavior of Steels / Y. Ergun [et al] // Journal of Nanoscience and Nanotechnology. – 2017. – Vol. 17. – Р. 8946–8951.
- Шилякин, Л. В. Метод модификации жидкостным борированием стальных изделий с целью повышения их эксплуатационных свойств / Л. В. Шилякин, Д. Н. Веропаха, Н. В. Веропаха // Известия высших учебных заведений. Северо-Кавказский регион. Технические науки. – 2014. – № 1. – С.48–51
- Synthesis of hexagonal boron nitride nanocoatings for corrosion prevention of iron substrates / V. Kandadai [et al] // Surface and Coatings Technology. – 2023. – Vol. 468. – Р. 129736
- How the duty cycle affects wear and corrosion: A parametric study in the Ni–B–TiN composite coatings / F. Dogan [et al] // Results in Surfaces and Interfaces. – 2023. – Vol. 11. – Р. 100212
- A new approach to improve some properties of wire arc additively manufactured stainless steel components: Simultaneous homogenization and boriding / A. Gunen [et al] // Surface and Coatings Technology. – 2023. – Vol. 460. – Р. 129395
- Tribological effects of boriding treatment on a low carbon steel repaired by wire and arc additive manufacturing / L. Farfan-Cabrera [et al] // Surface and Coatings Technology. – 2023. – Vol. 465. – Р. 129574
- Advanced iron boride coatings to enhance corrosion resistance of steels in geothermal power generation / Е. Medvedovski // Advances in Applied Ceramics. – 2020. – Vol. 119. – Р. 462–481.
- Formation of Corrosion-Resistant Thermal Diffusion Boride Coatings / Е. Medvedovski // Advanced Engineering Materials. – 2016. – Vol. 18. – №. 1. – Р. 11–33.