Abstract
CONTENTS
- INTRODUCTION
- 1 THEORETICAL PART
- 1.1 Polypropylene pipes: basic concepts, properties, application
- 1.2 Reinforcement of polypropylene: methods, types and influence on properties
- 1.2.1 Reinforcement of polypropylene with aluminum
- 1.2.2 Reinforcement of polypropylene with glass fiber
- 1.2.3 Reinforcement of polypropylene with basalt
- 1.3 Corrosion of polymers: concepts, mechanisms, factors
- 1.3.1 Scientific publications on the corrosion destruction of polypropylene
- 2 EXPERIMENTAL RESEARCH
- 2.1 Statement of the problem and purpose of the study
- 2.2 Materials, methods and equipment for research
- 2.3 Results of preliminary studies
- CONCLUSIONS
- REFERENCES
- 1.2 Reinforcement of polypropylene: methods, types and influence on properties
At the time of writing this abstract, the master’s work is not completed. Estimated completion date – May 2024. The full text of the work and materials on the research can be obtained from the author or his scientific adviser after the specified date.
INTRODUCTION
Polypropylene pipes are widely used in heating and water supply systems, replacing traditional metal pipes made of steel and cast iron. They have minimal susceptibility to stray currents and good physical and mechanical properties. However, when transporting liquids under pressure and at high temperatures, pipes can become deformed due to thermal expansion. To solve this problem, pipes are reinforced with materials with a low coefficient of expansion, which ensures the product has a long service life, reliability and an affordable price. Despite their high corrosion resistance, at elevated temperatures and aggressive environments, polypropylene pipes can lose their properties.
The purpose of the work is to study the effect of chemicals on the corrosion resistance of polypropylene reinforced pipes and their mechanical properties.
The relevance of the topic is due to the fact that polypropylene pipes are widely used in various industries and households, where they are exposed to aggressive environments and high temperatures, which can lead to deterioration of their properties and reduced service life.
The significance of the topic lies in the fact that increasing the corrosion resistance of polypropylene pipes will increase their durability, reliability and efficiency, as well as reduce environmental risks.
1 THEORETICAL PART
1.1 Polypropylene pipes: basic concepts, properties, applications
Polypropylene is a thermoplastic polymer made from propylene (alkene) with the formula CH2=CH-CH3, which is produced using catalysts at high pressure and temperature [1].
Polypropylene can be linear or branched, with different orientations of propylene units. This determines its tacticity: isotactic, syndiotactic or atactic (Fig. 1.1). Tacticity affects the crystallinity and properties of polypropylene. There are 4 types: homopolymer (PP-H), block copolymer (PP-B), random copolymer (PP-R) and random copolymer with increased heat resistance (PP-RCT).
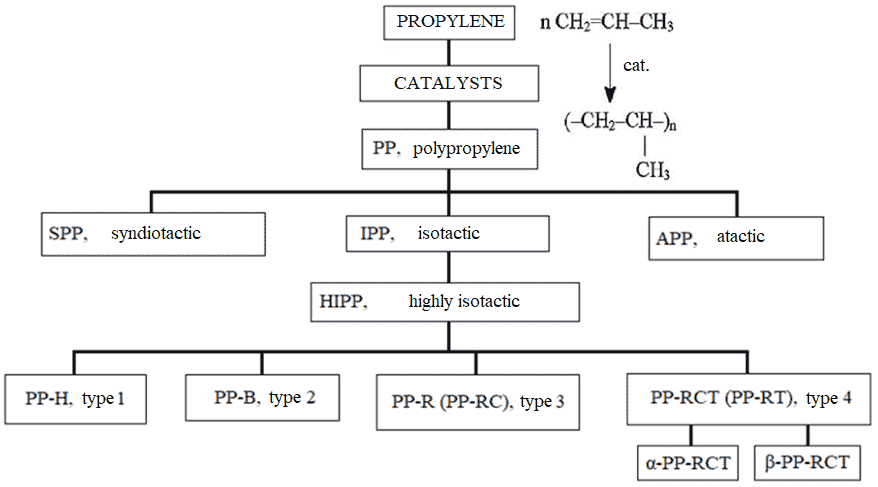
Figure 1.1 – Scheme for obtaining existing types of polypropylene
Polypropylene pipes are made by extrusion and come in different types depending on their characteristics and purpose. They are used in water supply, heating, sewerage, gas supply, compressor stations and the chemical industry. Polypropylene pipes have a number of advantages, but there are also some disadvantages. The main disadvantages are high linear expansion when heated and low mechanical strength at high pressures and temperatures [2-4].
1.2 Reinforcement of polypropylene: methods, types and influence on properties
Reinforcement technology is the application of reinforcing material to polypropylene pipes, which improves their quality and reliability. Reinforcement inhibits the linear expansion of polypropylene when heated. This makes it possible to reduce the coefficient of linear expansion to 0.03-0.05 mm/m•°C, which is comparable to metal or metal-plastic pipes. Thus, reinforced pipes can be used for hot water and heating without fear of deformation or damage [5].
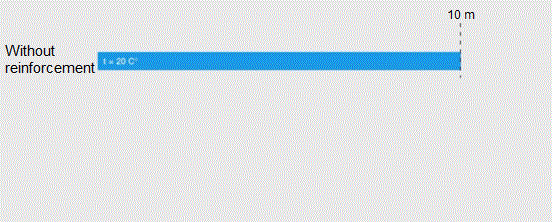
Figure 1.2 – Change in linear elongation of PP-R pipes depending on the type of reinforcement under the influence of elevated temperatures
The figure is animated (10 frames, 6 cycles, duration of 1 cycle = 10 sec., gif size 74 KB)
In the vast majority of cases, pipes for reinforcement are made of polypropylene type PP-R (random copolymer), which has high heat resistance, resistance to ultraviolet radiation and chlorine-containing substances, as well as good weldability. Polypropylene pipes correspond to service class 5 according to GOST 53630-2015, which means that they can be used at temperatures up to 95 °C and pressures up to 25 bar [6].
1.2.1 Reinforcement of polypropylene with aluminum
Reinforcement of polypropylene pipes comes in different types depending on the type of reinforcing material and its location relative to the polypropylene.
Aluminum reinforcement of PP-R pipes is made using aluminum foil or tape (the layer is connected ‘butt’ or ‘overlapping’), which can be located inside or outside the pipe (solid or perforated layer). Aluminum has high thermal conductivity and reduces the level of oxygen permeability of polypropylene pipes, but is still susceptible to corrosion upon contact with liquid if the integrity of the polypropylene layer enveloping it is damaged [7].
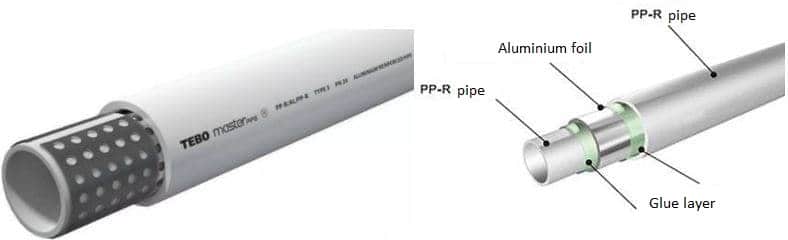
Figure 1.3 – PP-R polypropylene pipes reinforced with perforated aluminum foil (left) and a solid layer (right)
PP-R pipes with aluminum must be cleaned and trimmed before welding, otherwise there may be problems with the passage of gas or liquid. Aluminum can cause swelling in polypropylene, which does not affect performance, but spoils the appearance (Fig. 1.4). This is due to residual moisture during pipe production [7].
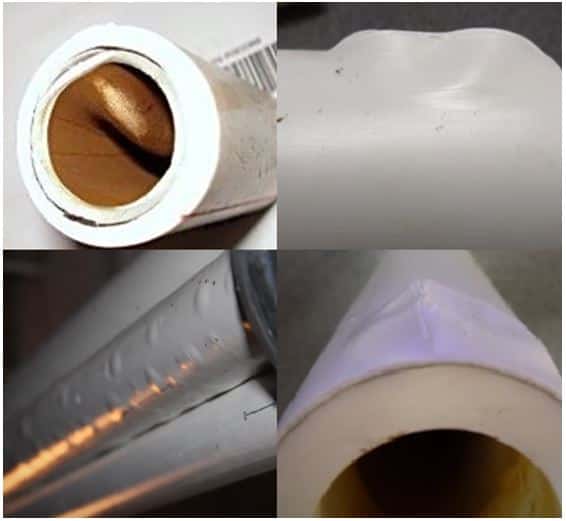
Figure 1.4 – Blistering of thin layers of polypropylene coating when reinforced with aluminum
Adhesion between the reinforcing layer and polypropylene affects the corrosion resistance of pipes. Good adhesion protects polypropylene from corrosion, but poor adhesion can increase corrosion or create microcracks in pipes.
1.2.2 Reinforcement of polypropylene with glass fiber
Fiberglass reinforces polypropylene pipes, making them stronger and reducing elongation. The pipes consist of three layers: an inner and outer layer of polypropylene type 3 (PP-R) and a middle layer of polypropylene type 3 (PP-R) with glass fiber (GF). Fiberglass is soldered into polypropylene and forms the frame of the pipe. Pipes are made using the coextrusion method, in which all layers are sintered together. Such pipes do not elongate at high temperatures and are easily welded without stripping the ends [8].
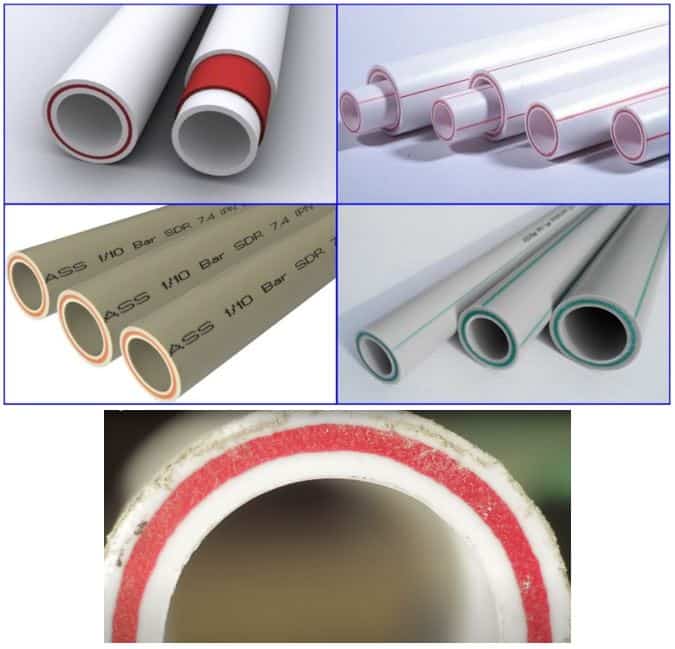
Figure 1.5 – Appearance of PP-R pipes reinforced with glass fiber
Glass fiber has high heat resistance, low hygroscopicity and good electrical insulating properties. The strength of the glass filament increases at temperatures of 60-160 °C due to the removal of moisture from the surface [9].
It is known that the strength of thin threads (fibers) is many times greater than the strength of bulk samples of some substances.
A-glass is called soda-lime glass, C-glass is sodium borosilicate, E-glass is aluminoborosilicate, S-glass is magnesium aluminosilicate [10].
According to GOST 32415-2013, pipes made from type 3 polypropylene PP-R, subject to the operating temperature range (70-75 °C), can last at least 50 years (Fig. 1.6).
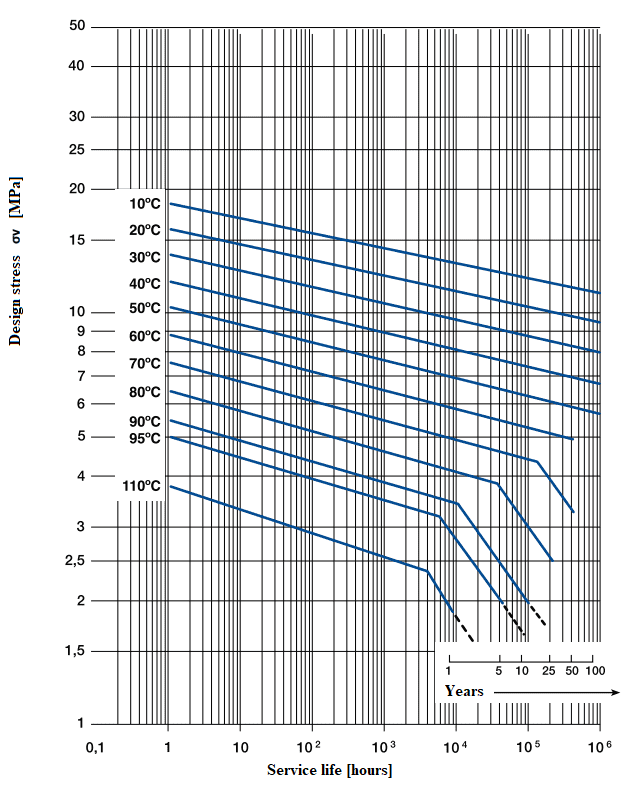
Figure 1.6 – Isotherms strength PP-R [11]
Pipes reinforced with glass fiber have the following advantages:
- expand less when heated (by 75%);
- do not require cleaning before welding;
- require less supports during installation;
- last longer in heating and cooling systems.
1.2.3 Reinforcement of polypropylene with basalt
Basalt reinforcement of polypropylene pipes is made using basalt fiber, which is a natural material obtained from molten basalt. The inner and outer layers are made of polypropylene type 4 (PP-RCT), the middle layer is made of polypropylene type 4 (PP-RCT) and reinforced with basalt fiber (BF). The composition of the layers can be schematically represented by the formula PP-RCT/ PP-RCT+BF/PP-RCT [12].
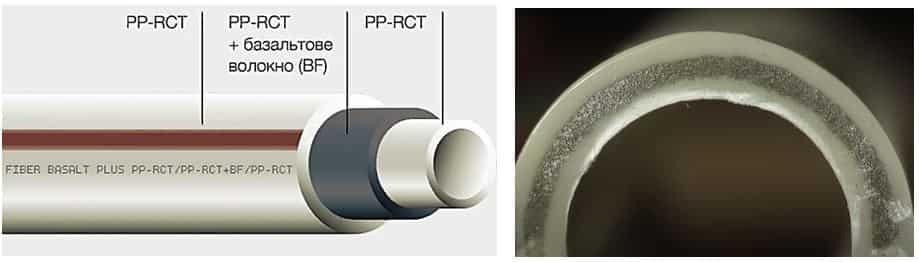
Figure 1.7 – Structure of a PP-RCT polypropylene pipe reinforced with basalt
The properties of PP-RCT polypropylene allow the use of a thinner pipe wall compared to pipes made from conventional polypropylene. With the same outer diameter, PP-RCT pipes provide greater system throughput.
Basalt fiber is very strong and flexible. Used in various industries that require materials of increased strength.
According to GOST 32415-2013, pipes made from type 4 polypropylene PP-RCT, subject to the operating temperature range (70-75 °C), can last at least 50 years (Fig. 1.8).
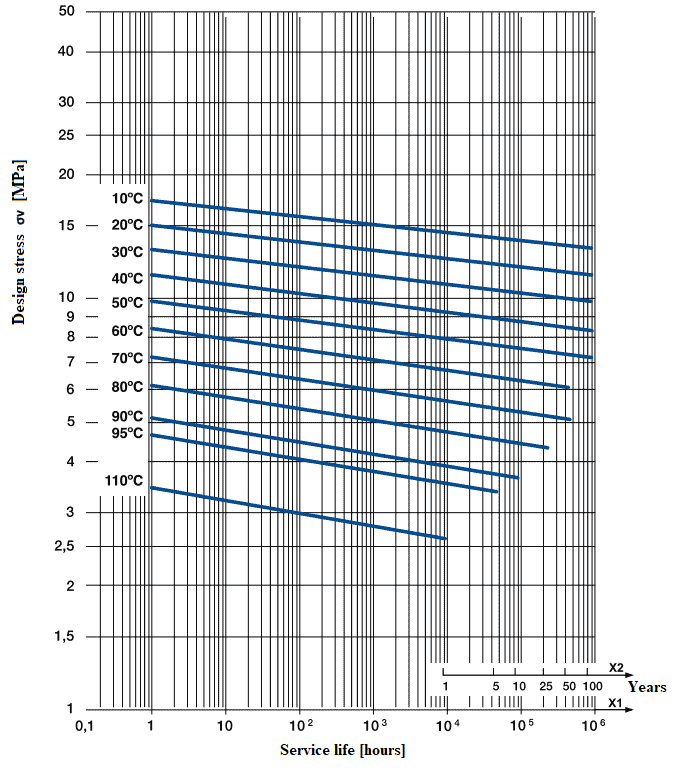
Figure 1.8 – Isotherms strength PP-RCT [11]
However, all reinforcing layers that are produced for polypropylene pipes in the form of finely chopped material fibers (glass, basalt) play a more key role in reducing the coefficient of linear thermal expansion than in increasing strength characteristics.
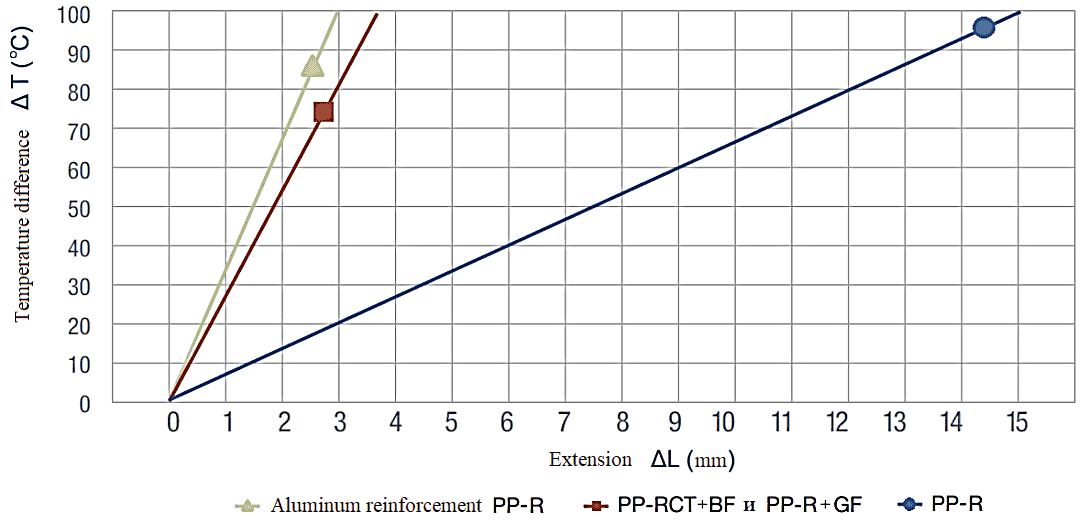
Figure 1.9 – Graph linear extensions pipes Pilsatherm [12]
Polypropylene pipes come in different types and diameters. Choose only high-quality material from trusted manufacturers. Poor-quality reinforced pipes can lead to system failure and high repair costs.
1.3 Corrosion of polymers: concepts, mechanisms, factors
Polymer corrosion is the process of chemical or physical destruction of polymer materials under the influence of various external factors, such as temperature, humidity, oxygen, light, solvents, acids, alkalis and salts. It degrades their properties, such as strength, rigidity and heat resistance.
The main mechanisms of destruction depend on the type of polymer, the corrosive environment and external factors (oxidation, hydrolysis, dissolution, diffusion, light aging, thermal aging and mechanical aging).
Signs of corrosion may include discoloration, cracking, peeling, formation of corrosion products, loss of weight, density or wall thickness, and changes in shape [13].
1.3.1 Scientific publications on the corrosion destruction of polypropylene
Polypropylenes are polyolefins that are resistant to aggressive chemicals. Their chemical resistance depends on solvation and chemical reaction. Bleach (hypochlorites) destroys polypropylene by oxidation, which leads to decomposition and failure of the pipeline (Fig. 1.10).
The article emphasizes that the chemical resistance of PP-R depends on many factors, such as temperature, concentration, stress and product geometry. Therefore, laboratory data may not always correspond to actual operating conditions [14].
The study showed that disinfectants in water corrode polyolefin (polypropylene) pipes. The diffusion corrosion process creates a brittle layer inside the pipes that can lead to rupture. Chlorine dioxide has a stronger destructive effect on plastic pipes than chlorine (in the form of hypochlorous acid) [15].
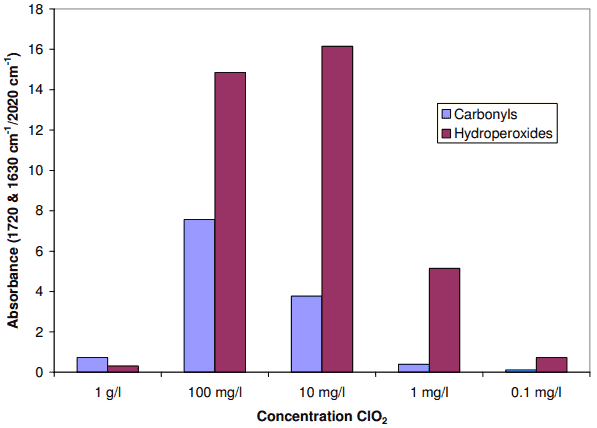
Figure 1.10 - Concentration of hydroperoxides and carbonyls in PP-R pipe after exposure to various concentrations of chlorine dioxide at 50°C for 24 hours [15] p>
Chlorine dioxide promotes the oxidative destruction of polypropylene. Destruction occurs due to a chain branching reaction during oxidation. The inner layer of the polypropylene pipe becomes brittle, as in Fig. 1.11.
When connecting PP pipes to aluminum and copper, electrolytic corrosion may occur, which damages the system. This occurs due to the potential difference between metals and water, which creates a galvanic cell. The anode corrodes faster than the cathode. To avoid corrosion, separate metals, use dielectric or insulating fittings, and ground the system [16].
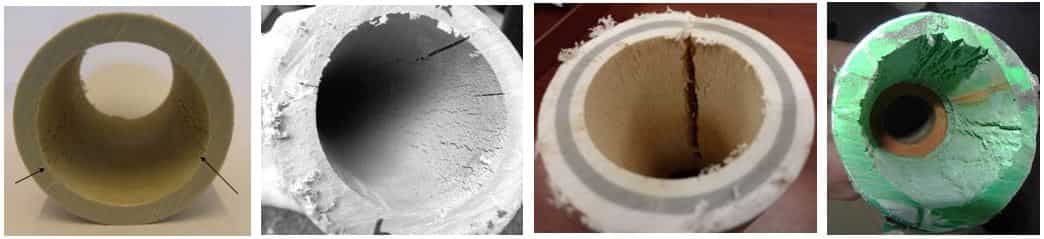
Figure 1.11 – A piece of pipe from a hot water supply in a hospital using chlorine dioxide disinfection. The arrows indicate stripes of cracks running in the direction of the pipe [15, 17]
Articles [18-20] talk about the destruction of polypropylene pipes by oxidation. It occurs due to exposure to water containing chlorine dioxide (ClO2) or hypochlorites, which remove antioxidants from the polymer. Oxidation leads to the appearance of cracks, cavities and other defects on the inner surface of the pipes. The rate and degree of destruction depend on the concentration of ClO2, exposure time and water temperature.
Consequently, corrosion of polypropylene pipes goes through five stages:
1. Reduction of antioxidants on the inner layer of the pipe due to oxidizing agents in the water.
2. Breakage of polymer chains, decreased elasticity and increased fragility of the inner surface of the pipe.
3. The appearance of microcracks on the inner surface of the pipe due to mechanical stress.
4. Leaching of antioxidants from the deep layers of the pipe, coalescence and propagation of cracks deep into the material.
5. Formation of a through crack due to ongoing mechanical loads.
In works [18, 20-22] these processes are described in more detail (Fig. 1.12).
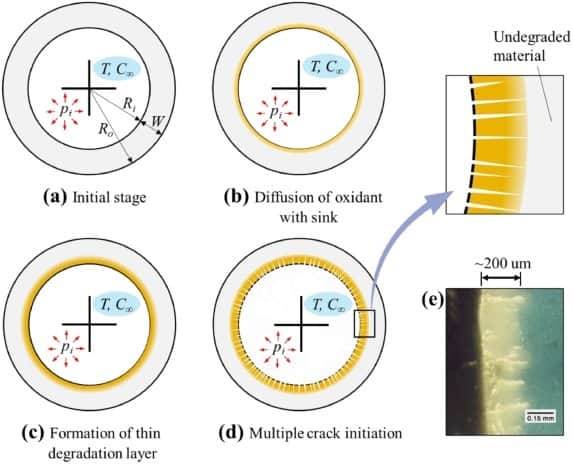
Figure 1.12 – Simplified diagram of the process of destruction of a polymer pipe [21]
PP pipes in houses with individual heating points (IHP) in hot water supply systems last longer than in high-rise buildings because there is no pressure drop. But chlorine and oxygen in water can speed up the oxidation of polypropylene and reduce its benefits.
2 EXPERIMENTAL RESEARCH
2.1 Statement of the problem and purpose of the study
The purpose of this work is to study the effect of chemicals on the durability of polypropylene reinforced pipes and preliminary studies of the effect of thermal cycling on the linear dimensions of polypropylene reinforced pipes and their mechanical properties.
Based on the task posed in the work, the following areas of research were identified:
- evaluate the relative elongation as a result of exposure to thermal cycles on samples of polypropylene pipes;
- determine the tensile strength as a result of tensile tests;
- examine the microstructure of samples after exposure to elevated temperatures;
- evaluate the corrosion resistance of samples in neutral, acidic and alkaline environments;
- examine the microstructure of samples after corrosion.
2.2 Materials, methods and equipment for research
Preliminary studies were carried out on samples of three types of polypropylene pipes with a diameter of 20 mm:
1) PP-R – polypropylene pipe without a reinforcing layer;
2) PP-R-AL – polypropylene pipe reinforced with aluminum;
3) PP-R-GF – glass fiber reinforced polypropylene pipe.
The general view is shown in Figure 2.1.
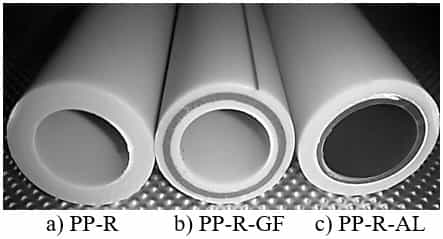
Figure 2.1 – General view of samples for research
To study the effect of periodic heating and cooling cycles on the elongation of pipe samples, sections of polypropylene pipes 100 mm long were taken: without a reinforcing layer, reinforced with aluminum, fiberglass and cut lengthwise, 10 mm wide in the amount of 3 samples per test.
Selected samples were placed in a Hotpoint Ariston electric oven with a thermostat, heated to 50, 75 and 95 °C (temperature deviation was ±5 °C), held for 10-15 minutes, cooled to room temperature and the process was repeated another 5 times, after which the length and warpage of the samples were assessed.
For mechanical tensile testing, sections of pipe samples 100 mm long and 10 mm wide were selected - not subjected to heating and samples after thermal cycling at temperatures of 50, 75 and 95 °C.
Before tensile tests, markings were made on all samples every 30 mm and the cross-section of each sample was measured (width and thickness) in order to determine the cross-sectional area F0.
Temporary resistance was determined by the formula:
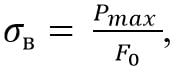
where:
Pmax – maximum load;
F0 – initial cross-sectional area of the sample.
The increase in sample length as a result of deformation is usually characterized by relative elongation, which we calculated using the formula:
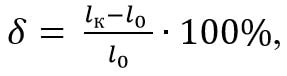
where:
l0 – initial length;
lê – final length.
The samples were installed in an FR-100 tensile testing machine and subjected to loading. After breaking the samples, the relative elongation and tensile strength were calculated.
2.3 Results of preliminary studies
The results of the influence of thermal cycling on the warping of pipe samples when heated to 95 °C are shown in Fig. 2.2.

Figure 2.2 – Appearance of samples after thermal cycling tests: a – without a reinforcing layer; b – reinforced with aluminum; c – with fiberglass filler
From Figure 2.2 it is clear that after all thermal cycles, the sample of a polypropylene pipe without a reinforcing layer was subject to warping the most, the deviation of which from the horizontal axis was 8-10 mm, the sample with aluminum reinforcement bent within 5-6 mm, while the sample with glass fiber filler retained relative straightness with a deviation of up to 1.5 mm.
Table 2.1 – Results of average elongation of samples after thermal cycles
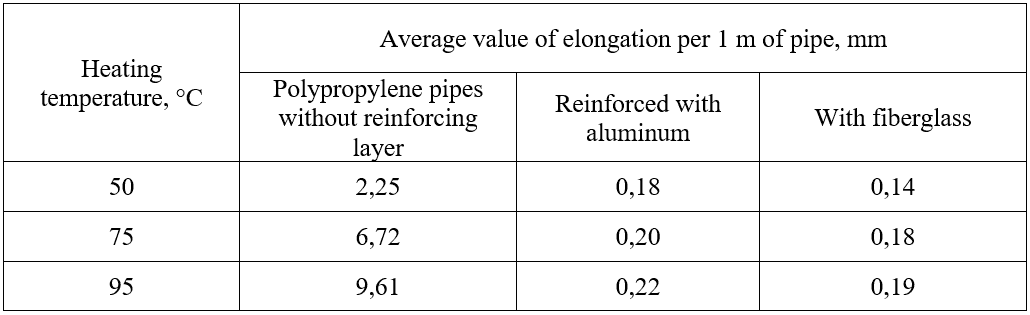
When analyzing the results of Table 2.1, it is clear that heating temperature has a significant effect on the elongation of polypropylene pipes without a reinforcing layer, which leads to warping of the pipeline. For pipes reinforced with glass fiber and aluminum, the values are similar, which has a negligible effect on the elongation of the pipes and is unlikely to lead to damage to the heating system.
Table 2.2 – Tensile test results for a polypropylene pipe sample without a reinforcing layer
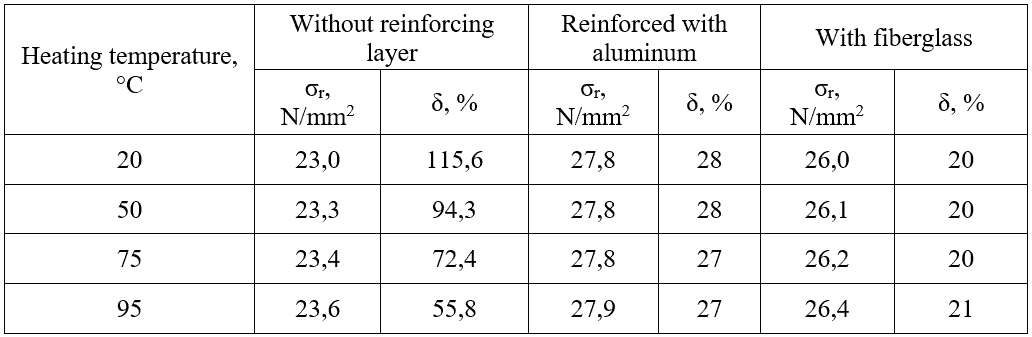
From Table 2.2 it is clear that heating temperature affects the plastic properties of polypropylene that does not have a reinforced layer. As the heating temperature increases, the ductility of polypropylene decreases, making it more brittle. Heating has little effect on polypropylene pipes reinforced with aluminum and fiberglass. Thermal cycling also does not have much effect on the strength properties. These characteristics remain almost at the same level, which can be seen on the samples during the tensile test.
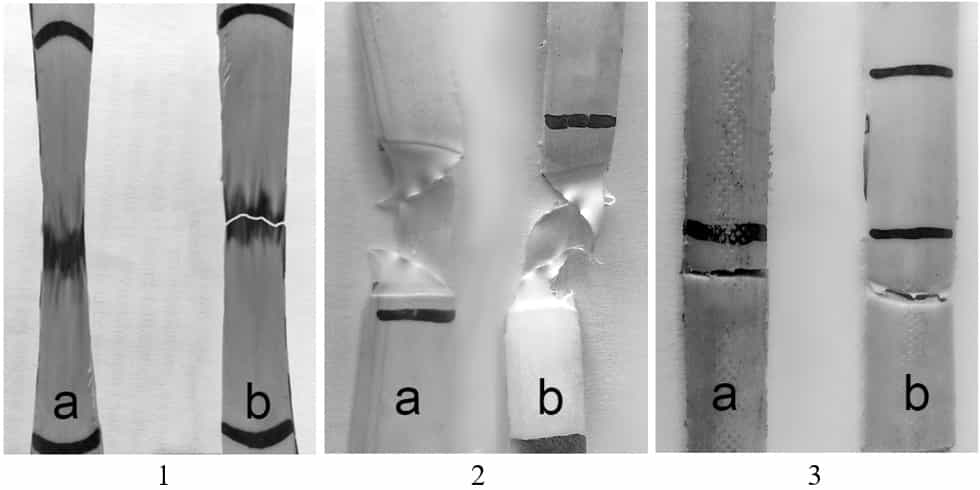
Figure 2.3 – Samples of polypropylene pipes after tensile tests: 1 – pipes without a reinforcing layer, 2 – aluminum reinforced, 3 – fiberglass reinforced;
a – sample without heating; b – sample after cyclic heating to 95 °C
As can be seen from Figure 2.3, the reinforcing layer has a significant effect on the properties of polypropylene pipes under the influence of temperatures. The main load is borne by the aluminum layer, which breaks first when stretched. Polypropylene continues to stretch until a certain point of rupture. Glass fiber reinforced samples do not elongate as long as polypropylene without a reinforcing layer and break, which indicates a strong connection between the layers.
Figure 2.4, a shows the solidity of polypropylene material without a reinforcing layer.
Figure 2.4, b shows the microstructure of a polypropylene pipe reinforced with aluminum. It is clearly visible that between aluminum and polypropylene, the connecting layer is an adhesive-based layer, which under thermal influence tends to lose its elastic and adhesive properties.
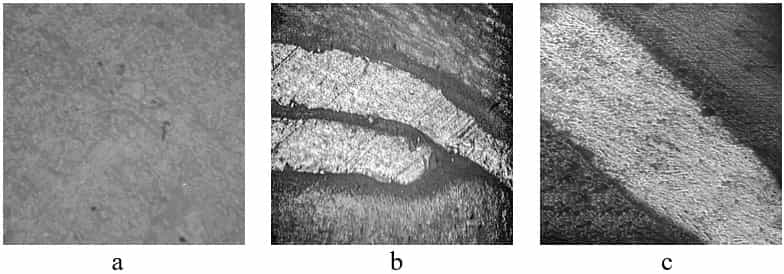
Figure 2.4 – Microstructures of polypropylene pipe samples:
a – without a reinforcing layer; b – reinforced with aluminum; c – with fiberglass filler, ?250
Polypropylene pipes with aluminum can delaminate and corrode if they are not cleaned before welding. This is due to moisture penetration between the foil and polypropylene. Figure 2.4, b shows the structure of the ‘overlapping’ pipe reinforcement.
Figure 2.4, c, shows the microstructure of a pipe sample with fiberglass filler, where it can be seen that the layers of polypropylene are reliably welded to the reinforcing layer, which allows maintaining the strength and integrity of the structure after thermal exposure.
CONCLUSIONS
During the research work, a literature analysis was carried out regarding the issue of the corrosion resistance of polypropylene pipes, their structure, properties and characteristics. The scope of application of these products was also considered.
It has been studied that polypropylene reinforced pipes used in hot water supply systems are susceptible to oxidative destruction of the internal surface due to the presence of dissolved disinfectants in the water (hypochlorites, chlorine dioxide, chloramines, oxygen).
As a result of preliminary studies, it was found that the reinforcing layer has a positive effect on polypropylene pipes:
- creates structural strength, which allows it to withstand pressure loads;
- reduces the coefficient of linear expansion, which allows the pipeline to be used in systems with high coolant temperatures with its cyclic effect.
It has been confirmed that thermal cycling leads to a significant elongation (from 2.25 to 9.61 mm per 1 m of pipe) of unreinforced polypropylene pipes, while reinforced ones elongate by 0.14-0.22 mm; their strength is 26-28 N/mm2.
When studying the microstructure of the samples, it was determined that polypropylene pipes with a fiberglass reinforcement layer have a monolithic structure, which makes it possible to improve the performance characteristics of the pipe. This pipeline structure allows it to be installed without additional processing of the edges, which speeds up the installation process.
However, despite many studies, the effect of various types of reinforcement on the corrosion resistance of polypropylene pipes remains insufficiently studied. This is due to the fact that polypropylene corrosion is a complex process that depends on many factors. Therefore, to fully understand the effect of different types of reinforcement on the corrosion resistance of pipes at elevated temperatures, additional research is necessary.
REFERENCES
- Ïîëèïðîïèëåíîâûå òðóáû [Ýëåêòðîííûé ðåñóðñ]. ñàéò. — Ýëåêòðîí. äàí. — Ìîñêâà, 2023. — Ðåæèì äîñòóïà: https://www. vseinstrumenti. ru/ — Çàãë. ñ ýêðàíà.
- Ïîëèïðîïèëåí — ÷òî ýòî çà ìàòåðèàë, åãî ñâîéñòâà è ïðèìåíåíèå [Ýëåêòðîííûé ðåñóðñ]. ñàéò. — Ýëåêòðîí. äàí. — Ìîñêâà, 2022. — Ðåæèì äîñòóïà: https://epolymer. ru/ — Çàãë. ñ ýêðàíà.
- Ïîëèïðîïèëåíîâûå òðóáû: îáçîð è âûáîð ëó÷øèõ òðóá [Ýëåêòðîííûé ðåñóðñ]. ñàéò. — Ýëåêòðîí. äàí. — Ìîñêâà, 2019. — Ðåæèì äîñòóïà: https://otrubah. com/ — Çàãë. ñ ýêðàíà.
- Ïîëèïðîïèëåíîâàÿ òðóáà, àðìèðîâàííàÿ àëþìèíèåì VALTEC PP-R/AL/PP-R PN25 [Ýëåêòðîííûé ðåñóðñ]. ñàéò. — Ýëåêòðîí. äàí. — Ìîñêâà, 2017. — Ðåæèì äîñòóïà: https://valtec. ru/ — Çàãë. ñ ýêðàíà.
- Ïîëèïðîïèëåí èëè ìåòàëëîïëàñòèê: êàêèå òðóáû âûáðàòü [Ýëåêòðîííûé ðåñóðñ]. ñàéò. — Ýëåêòðîí. äàí. — Óôà, 2021. — Ðåæèì äîñòóïà: https://www. gigas. su/ — Çàãë. ñ ýêðàíà.
- ÃÎÑÒ Ð 53630-2015. Òðóáû íàïîðíûå ìíîãîñëîéíûå äëÿ ñèñòåì âîäîñíàáæåíèÿ è îòîïëåíèÿ. Îáùèå òåõíè÷åñêèå óñëîâèÿ. — Ìîñêâà: Ñòàíäàðòèíôîðì, 2016. — 20 ñ.
- § 2. ÏÏ-Êóðñ. Âñ¸ îá àðìèðîâêå ïîëèïðîïèëåíîâûõ òðóá [Ýëåêòðîííûé ðåñóðñ]. ñàéò. — Ýëåêòðîí. äàí. — Ñàíêò-Ïåòåðáóðã, 2020. — Ðåæèì äîñòóïà: https://dretun. ru/ — Çàãë. ñ ýêðàíà.
- Òðóáû ïîëèïðîïèëåíîâûå àðìèðîâàííûå ñòåêëîâîëîêíîì [Ýëåêòðîííûé ðåñóðñ]. ñàéò. — Ýëåêòðîí. äàí. — Ìîñêâà: çàâîä FDplast, 2018. — Ðåæèì äîñòóïà: https://www. fdplast. ru/ — Çàãë. ñ ýêðàíà.
- Êîíîâàëîâ, Ï. Ã. Ïëàñòè÷åñêèå ìàññû, èõ ñâîéñòâà è ïðèìåíåíèå â ïðîìûøëåííîñòè: (ñïðàâî÷íîå ïîñîáèå) / Ï. Ã. Êîíîâàëîâ. — Ìîñêâà: Âûñøàÿ øêîëà, 1961. — 182 ñ.
- ÑÒÅÊËßÍÍÎÅ ÂÎËÎÊÍÎ [Ýëåêòðîííûé ðåñóðñ]. ñàéò. — Ýëåêòðîí. äàí. — Ìîñêâà, 2022. — Ðåæèì äîñòóïà: https://xumuk. ru/ — Çàãë. ñ ýêðàíà.
- ÃÎÑÒ 32415-2013. Òðóáû íàïîðíûå èç òåðìîïëàñòîâ è ñîåäèíèòåëüíûå äåòàëè ê íèì äëÿ ñèñòåì âîäîñíàáæåíèÿ è îòîïëåíèÿ. Îáùèå òåõíè÷åñêèå óñëîâèÿ. — Ìîñêâà: Ñòàíäàðòèíôîðì, 2014. — 83 ñ.
- Óíèêàëüíàÿ Êîìïîçèòíàÿ Òðóáà äëÿ Ñèñòåì Ãîðÿ÷åãî Âîäîñíàáæåíèÿ è Îòîïëåíèÿ [Ýëåêòðîííûé ðåñóðñ]. êàòàëîã. — Ýëåêòðîí. äàí. — Ìîñêâà: BASALTTHERM, 2019. — Ðåæèì äîñòóïà: https://ppr-plastek. ru/ — Çàãë. ñ ýêðàíà.
- Êàê âûáðàòü àðìèðîâàííûå ïîëèïðîïèëåíîâûå òðóáû äëÿ îòîïëåíèÿ [Ýëåêòðîííûé ðåñóðñ]. ñàéò. — Ýëåêòðîí. äàí. — Ìîñêâà, 2019. — Ðåæèì äîñòóïà: https://lammin. org/ — Çàãë. ñ ýêðàíà.
- Chemical Resistance of Polypropylene [Ýëåêòðîííûé ðåñóðñ]. òåõí. äàí. — Ýëåêòðîí. äàí. — Houston, 2023. — Ðåæèì äîñòóïà: https://www. lyondellbasell. com/ — Çàãë. ñ ýêðàíà.
- Corrosion of plastic pipes — the role of disinfectants / K. Jacobson. — Lucerne: CEOCOR, PhD Swerea KIMAB AB, Stockholm, Sweden, 2012. — 14 p.
- Proper Integration of Copper Tubing and Components with PP-R Piping Materials for Plumbing Applications [Ýëåêòðîííûé ðåñóðñ]. òåõí. äàí. — Ýëåêòðîí. äàí. — Plastics Pipe Institute, 2018. — Ðåæèì äîñòóïà: https://plasticpipe. org/ — Çàãë. ñ ýêðàíà.
- Âîçìîæíûå ïðîáëåìû èñïîëüçîâàíèÿ ïîëèïðîïèëåíîâûõ òðóá â çàêðûòûõ ñèñòåìàõ ÃÂÑ âûñîòíûõ ÌÊÄ [Ýëåêòðîííûé ðåñóðñ]. ñàéò. — Ýëåêòðîí. äàí. — Ìîñêâà: ÀÂÎÊ, 2020. — Ðåæèì äîñòóïà: https://www. abok. ru/ — Çàãë. ñ ýêðàíà.
- Oxidation resistance of polypropylene random copolymer pipe to chlorinated water / Duvall D. // Journal of Failure Analysis and Prevention. — 2014. — Vol. 14. — PP. 336–342.
- Chlorine dioxide degradation issues on metal and plastic water pipes tested in parallel in a semi-closed system / Vertova A. [et al.] // International Journal of Environmental Research and Public Health. — 2019. — Vol. 16(22). — P. 4582.
- Degradation of polymer & elastomer exposed to chlorinated water — a review / Samarth N. B., Mahanwar P. A. // Open Journal of Organic Polymer Materials. — 2021. — Vol. 11. — PP. 1–50.
- Modeling of multiple crack initiation in polymer pipes under oxidative environment / Jung-Wook Wee. [et al.] // International Journal of Engineering Science. — 2022. — Vol. 176. — P. 103686.
- Antioxidant consumption in squalane and polyethylene exposed to chlorinated aqueous media / Yu W. [et al.] // Polymer Degradation and Stability. — 2012. — Vol. 97(11). — PP. 2370–2377.