Abstract
Содержание
- Introduction
- Goals and objectives of the study
- The relevance of research
- Efficiency of the rationing system
- Labor standardization system at the enterprise
- Organization of labor standards at the enterprise
- Conclusions
- List of used literature
Introduction
In the modern Russian economy, increasing production efficiency is becoming an increasingly important task. One of the main factors influencing the success of production is the reasonable use of labor. Therefore, the labor standardization system becomes of great importance, since it allows one to determine the optimal performance indicators and efficiency of the enterprise’s employees.
However, the existing system of labor standards in many organizations does not always correspond to modern requirements and production realities. As a result, problems arise related to the discrepancy between objective indicators of the work results of labor subjects and the requirements they make, insufficient motivation and labor efficiency, as well as distrust on the part of employees in the standardization system.[1]
The purpose of this master's thesis is to develop recommendations for improving the labor standardization system at the enterprise, which will increase production efficiency and improve working conditions for employees. In the process of work, existing methods and approaches to labor standardization will be reviewed, their advantages and disadvantages will be identified, and factors influencing the success of the implementation of a standardization system at a particular enterprise will be identified.
The methodological basis of the study is the theoretical foundations of labor regulation, as well as the results of previous studies in this area. To achieve this goal, a survey and analysis of the current labor standardization system at the selected enterprise will be carried out, as well as a comparison with best practices and international standards.[2]
The results of the study can be used to optimize the work of employees and increase the productivity of the enterprise as a whole. In addition, they can contribute to the development and improvement of the labor standardization system in the broad practice of Russian enterprises.
Thus, this master's thesis has practical significance and will contribute to the development of recommendations for optimizing the labor standardization system in enterprise conditions.
Goals and objectives of the study
Target: Research and develop recommendations for improving the labor standardization system at the enterprise in order to increase production efficiency and improve working conditions for employees.
Tasks:
- Analyze the existing labor standardization system at the enterprise, identify its advantages and disadvantages.
- Study the experience of best practices and international standards in the field of labor standards.
- Study the theoretical foundations of labor regulation and existing methods and approaches to its organization.
- Determine the factors influencing the success of the implementation of the labor standardization system at the enterprise.
- Conduct a survey and analysis of the current labor standardization system at the selected enterprise in order to identify problems and potential areas for improvement.
- Develop recommendations for optimizing the labor standardization system, taking into account the specifics and needs of the enterprise.
- Conduct an assessment and the expected effect of implementing the proposed recommendations.
- Develop practical recommendations for the implementation and monitoring of a labor standardization system at an enterprise.
In carrying out these tasks, an integrated approach will be used, including analysis of theoretical materials, analysis of practical experience, collection and analysis of data, as well as the use of methods of economic and sociological analysis.[3]
The results of the study and developed recommendations will optimize the work of employees and increase the productivity of the enterprise, as well as improve the working conditions of employees and reduce the level of tension and stress in the workplace.
The relevance of research
The relevance of the study is due to a number of factors:
- Economic efficiency: Effective use of working time and increased productivity are key factors for the competitiveness of an enterprise. Increasing the efficiency of labor standards can lead to a reduction in work completion time, improved quality of products or services, and an increase in labor productivity.
- Improving working conditions: The labor standardization system can have an impact on the comfort and safety of the working environment. Optimizing time standards for completing tasks helps reduce tension, fatigue and stress among workers, which in turn leads to an increase in their performance, satisfaction and a reduction in the risk of work-related diseases.
- Increasing employee motivation: A clear system of labor standards allows you to establish transparent and objective criteria for evaluating work. This helps to reward and stimulate high performance and develop the individual potential of employees. As a result, their motivation and level of performance increases.
- Optimization of personnel management: Modern labor standards systems provide the collection and analysis of a large amount of data on work processes, allowing management to effectively plan resources, distribute tasks and optimize work processes. This improves personnel management and informed decision-making.
- Holistic approach to improving production processes: Improving the labor standards system is part of a broader process of improving the production processes of the enterprise. Systematic study and optimization of labor standards contribute to the creation of a more efficient and flexible management system that is able to adapt to changing conditions and market requirements.
All these factors make the study relevant and practically significant for various industries and organizations. The results of the study will help improve the efficiency of the work process, improve working conditions and increase the competitiveness of the enterprise.[4, 5]
Efficiency of the rationing system
The effectiveness of an improved labor standardization system in an enterprise can be expressed in the following aspects:
- Increased labor productivity: Optimally established time standards for completing tasks allow workers to more effectively distribute their efforts and reduce the time spent on certain types of work. This leads to an increase in labor productivity and, as a consequence, an increase in production or services.
- Cost reduction: More accurate and objective labor rationing helps eliminate unnecessary time and energy spent on tasks, as well as avoid overexpenditure of resources. This allows you to reduce production costs and improve the financial performance of the enterprise.
- Improving the quality of products or services: An improved labor standardization system helps to reduce errors and defects, which, in turn, improves the quality of the final products or services provided by the enterprise.
- Reducing the time for training new employees: An optimal labor standardization system allows the enterprise to systematize and formalize work requirements and processes. This facilitates the training process for new employees and helps them quickly master the basic skills and requirements of the position.
- Improving working conditions: Rational regulation of labor helps improve working conditions for employees. Optimal time standards allow you to avoid excessive workload and fatigue, as well as reduce physical and psychological stress in the workplace.
- Increasing employee motivation and satisfaction: The clarity and objectivity of the labor standardization system creates transparent criteria for assessing employee performance. This motivates employees to achieve optimal results and rewards high performance. Improved working conditions and fair remuneration also contribute to increased employee motivation and job satisfaction.
All these factors together contribute to increasing the efficiency of the enterprise, improving production results and creating conditions for the sustainable development of the organization.[6-8]
Labor standardization system at the enterprise
The labor standardization system at an enterprise is a system of rules and procedures that determines the standards and time norms required to perform certain types of work. It includes the following elements:
- Establishment of standards: One of the main aspects of the labor standardization system is the establishment of time standards for performing certain types of work. This occurs based on the analysis of production processes and labor operations, taking into account the optimal use of resources and the quality of the final product or service.
- Calculation of working hours: A labor rationing system determines how much time should be spent on each operation or task. This includes taking into account time spent on preparation, breaks, training and other factors that affect job performance. Calculation of working hours: A labor rationing system determines how much time should be spent on each operation or task. This includes taking into account time spent on preparation, breaks, training and other factors that affect job performance.
- Consideration of productivity standards: The labor standards system takes into account productivity standards that determine not only the quantity of work, but also the quality and efficiency of its performance. They can be established based on the performance of past employees or through the analysis of expert knowledge.
- Control and reporting: The labor standardization system provides for monitoring the implementation of time norms and productivity standards. This can be done through various methods such as observation, measurement or automated monitoring systems. The results of monitoring and reporting allow you to evaluate performance and identify potential areas for improvement.
- Adaptation and updating: The labor standardization system must be flexible and able to adapt to the changing conditions of the enterprise. It must be periodically updated and revised in accordance with production requirements, technological changes, and changes in the workforce and labor market.
All these elements of the labor standardization system are aimed at optimizing work processes, increasing productivity, improving working conditions for employees and achieving optimal results for the enterprise.[9-11]
Organization of labor standards at the enterprise
Savings today force companies to manage all available resources more flexibly and reduce costs. In an unstable economic situation, managers need to understand the principles of forming these funds.
When planning the optimal number of enterprises, they use the labor standardization method. It is based on scientific and technical calculations that allow companies to minimize costs while ensuring production plans are met and all quality standards are met.
The organization of labor standardization at an enterprise is the process of analyzing the work activity of workers and establishing working time standards established for each specific area or workplace.
The object of labor regulation is labor actions, movements and operations of workers (in seconds or hours), which are measured in a unit of time. The purpose of the measurement is to calculate the optimal duration of the work shift for a given working period. The inversely proportional value of the production rate is the planned number of products, semi-finished products or products per hour (per shift).[12]
The organization of labor standardization at an enterprise solves the following problems:
- Planning the maximum possible production volumes for the current staff size.
- Issuing tasks to workers in accordance with the production plan (during the norm).
- Optimization of the production process, based on the results of the analysis of workers’ work activities (in normalization time).[13]
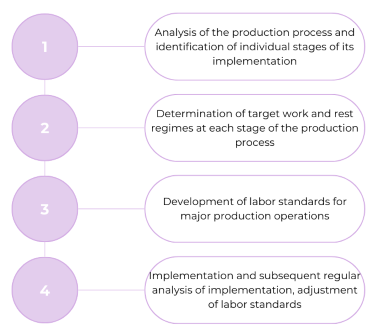
Figure 1 – Stages of organizing labor standards at an enterprise
The purpose of organizing labor standards at an enterprise is as follows:
- Establishing target working hours for carrying out a particular work operation.
- Justification of the amount of material remuneration.
- Organization of production planning (for the available number), analysis and control of the implementation of production plans.
- Rational organization of work allows the most effective use of the physical and psychological abilities of employees during the work shift.
Depending on the method of developing labor standards, various methods of regulating labor in an organization or enterprise are distinguished
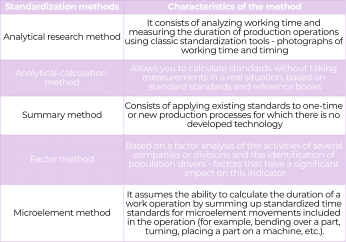
Figure 2 – Methods of labor standardization at the enterprise
To calculate labor standards, it is necessary to determine the typical structure of working time. The structure shows how much time the work itself takes and what part of it is spent preparing for it (percentages are indicated for reference): what is the proportion of working time in preparing the work. [14-16]
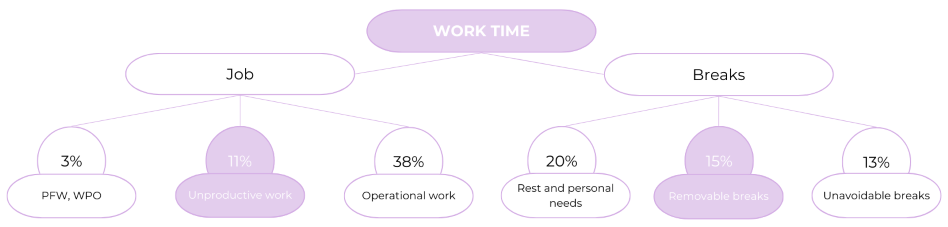
Figure 3 – Working hours at the enterprise
Working hours consist of the following categories:
Organization of the workplace, in contrast to the preparatory - last operation, here we are talking about equipment maintenance (lubrication, cleaning). Operational work is the time to complete a production task, the main job of an employee.
Unproductive work is an optional type of labor time expenditure, which is allocated when there are losses in production (in the terminology of lean manufacturing) and products made from defective materials.
Organization of the workplace, in contrast to the preparatory - last operation, here we are talking about equipment maintenance (lubrication, cleaning). Operational work is the time to complete a production task, the main job of an employee.
Break time structure:
Time for rest and personal needs is the time of breaks in work necessary for an employee to maintain his ability to work. In the office, this is usually 15 - 20% of the time from the working day to the end of the shift; under particularly difficult climatic working conditions, 50 percent or even more: these periods are regulated by labor legislation.
Unavoidable interruptions are forced downtimes during which the employee waits for the receipt of materials or the completion of the equipment operation cycle. The percentage of unresolved outages must be continuously reduced using lean manufacturing methods.
As a result of interruptions in working time lost due to the fault of the employee himself (being late for work or leaving work early), the employee loses working time. To eliminate these cases, it is necessary to organize labor standardization and establish the optimal number of workers. [17-19]
In order to automate the processes of personnel planning, special calculators are being developed at the enterprise. Based on labor standards, results-oriented material reward systems are created:
- Salary-bonus system of remuneration - when a bonus is paid for fulfilling a time standard.
- Piecework - if wages were calculated based on piecework rates for each unit of production (for example, unit cost).
To organize labor standards at an enterprise, it is always important to obtain an economic effect from:
- Planning the optimal number of personnel.
- Creating modern results-oriented motivation systems.
- Increasing productivity and quality of labor operations.
The costs of a project to implement a labor standardization system usually pay off within a few months after the implementation of technically and scientifically sound standards. The practice of applying the methodology created in the production process allows it to be adapted for administrative personnel and sales teams.[20]
Conclusions
- Improving the labor standardization system is an urgent and necessary task for enterprises in modern conditions. Optimal use of labor resources and increased production efficiency become the basis for increasing the competitiveness and sustainable development of the enterprise.
- The study showed that the existing labor standardization system at the selected enterprise has some disadvantages, such as insufficient objectivity, lack of connection with real requirements and production features, as well as insufficient adaptation to changing conditions. These shortcomings lead to decreased productivity, failure to meet targets, insufficient motivation of employees and negative consequences for the enterprise.
- Based on an analysis of best practices and theoretical foundations of labor regulation, recommendations were developed to improve the labor regulation system at the enterprise. These recommendations include: taking into account the characteristics of production and technological processes, developing more objective criteria for evaluating work, establishing realistic time standards, taking into account factors affecting productivity, and improving the information base and control.
- The practical implementation of the proposed recommendations will allow the enterprise to significantly increase operational efficiency, improve working conditions for employees and achieve better production results. This will help reduce costs, increase productivity, improve the quality of products and services, and increase employee motivation and satisfaction.
- Important conditions for the successful implementation of the proposed recommendations are the active participation and support of the enterprise management, as well as the provision of the necessary resources and employee training. The implementation of changes in the labor standardization system requires joint efforts and interaction between various structural divisions of the enterprise.
In general, the research results and developed recommendations confirm the feasibility of improving the labor standardization system at the enterprise. This will improve the efficiency of using labor resources, optimize production processes and achieve better results in a modern economy.
List of used literature
- Адамович А.Н. Системы нормирования и оплаты труда: учебное пособие / А.Н. Адамович. — М.: ЮНИТИ, 2009.
- Гончаров А.В. Основы нормирования труда и управление производительностью труда: учебник / А.В. Гончаров, А.В. Лебедев. — М.: Флинта, 2017.
- Кочеткова А.А. Управление трудовыми процессами на предприятии: учебное пособие / А.А. Кочеткова, Е.Л. Третьякова. — М.: ИТДГ «Мэн», 2010.
- Зубковская О.В. Труд и заработная плата: нормирование, организация и оплата труда: учебное пособие / О.В. Зубковская. — М.: Издательский дом «Территория науки», 2017.
- Collaboration, Communication and Coordination in Work — Interdisciplinary Perspectives / edited by Heikki Rainio, Samuli Pekkola, Paivi Timonen. — Springer, 2019.
- Матяш Н.Ф. Управление трудовыми ресурсами предприятия: учебное пособие / Н.Ф. Матяш, С.А. Крапивка. — Минск: Полицейская академия, 2017.
- Олейникова Н.М. Технологии конкурентоспособности в условиях индустриализации и техногенного общества / Н.М. Олейникова. — Ростов-на-Дону: Южный научный центр РАН, 2019.
- Абрамченков М.А. Организация и нормирование труда: учебное пособие / М.А. Абрамченков, И.И. Абрамченкова. — М.: Юрайт, 2010.
- Очерки теории труда и нормирования / под редакцией А.В. Гончарова, Б.Е. Брауде. — М.: Госэргиз, 1949.
- Ремль Б.М. Управление эффективностью предприятия: учебное пособие / Б.М. Ремль. — М.: ФОРУМ: Инфра-М, 2016.
- Беженцева Т.В. Анализ производственно-хозяйственной деятельности предприятия: учебное пособие / Беженцева Т.В. — Тюмень: Тюменский индустриальный университет, 2019. — 118 c. — ISBN 978-5-9961-1828-1. — Текст: электронный // URL: https://www.iprbookshop.ru/101407.html
- Земцова Л.В. Экономический анализ: учебное пособие / Земцова Л.В. — Томск: Томский государственный университет систем управления и радиоэлектроники, Эль Контент, 2013. — 234 c. — ISBN 978-5-4332-0089-0. — Текст: электронный // URL: https://www.iprbookshop.ru/72226.html
- Кондаурова, И.А. «Стратегическое управление человеческими ресурсами» Электронный ресурс: для обучающихся по направлению подготовки 38.04.03 «Управление персоналом» / ГОСУДАРСТВЕННОЕ ОБРАЗОВАТЕЛЬНОЕ УЧРЕЖДЕНИЕ ВЫСШЕГО ПРОФЕССИОНАЛЬНОГО ОБРАЗОВАНИЯ «ДОНЕЦКИЙ НАЦИОНАЛЬНЫЙ ТЕХНИЧЕСКИЙ УНИВЕРСИТЕТ», Кафедра управления бизнесом и персоналом; ГОУВПО «ДОННТУ», Каф. упр. бизнесом и персоналом; сост. И. А. Кондаурова. — 246 Кб. — Донецк: ГОУВПО «ДОННТУ», 2021. — 1 файл. — Систем. требования: Acrobat Reader.
- Кондаурова, И.А. Управление персоналом: учебно-методическое пособие / И. А. Кондаурова, О. А. Штагер; И.А. Кондаурова, О.А. Штагер; ГОУВПО «ДОННТУ». — 1 Мб. — Донецк: ГОУВПО «ДОННТУ», 2021. — 1 файл. — Систем. требования: Acrobat Reader. — URL: http://ed.donntu.org/books/21/cd10286.pdf
- Кондаурова, И.А. «Управление человеческим капиталом в экономике знаний»: для обучающихся по направлению подготовки 38.04.03 «Управление персоналом» / ГОСУДАРСТВЕННОЕ ОБРАЗОВАТЕЛЬНОЕ УЧРЕЖДЕНИЕ ВЫСШЕГО ПРОФЕССИОНАЛЬНОГО ОБРАЗОВАНИЯ «ДОНЕЦКИЙ НАЦИОНАЛЬНЫЙ ТЕХНИЧЕСКИЙ УНИВЕРСИТЕТ», Кафедра управления бизнесом и персоналом; ГОУВПО «ДОННТУ», Каф. упр. бизнесом и персоналом; сост. И. А. Кондаурова. — 246 Кб. — Донецк: ГОУВПО «ДОННТУ», 2021. — 1 файл. — Систем. требования: Acrobat Reader.
- Кондаурова, И. А. Экономический анализ: учебное пособие / И. А. Кондаурова, С. Н. Карельская, В. Л. Карлинский, Т.В. Коваленко и др. — Нижний Новгород: НОО «Профессиональная наука», 2018. — URL: http://scipro.ru/conf/economic_analysis.pdf
- Кондаурова, И. А. Эффективность использования человеческих ресурсов как фактор повышения конкурентоспособности предприятия / И. А. Кондаурова И.А., В. А. Геммерлинг // Экономика и управление: теория и практика. — 2018. — Т. 4. — № 2. — С. 13-18.
- Мизя М.С. Анализ и моделирование трудовых показателей: учебное пособие / Мизя М.С., Телятникова Т.В. — Омск : Омский государственный технический университет, 2020. — 120 c. — ISBN 978-5-8149-3033-0. — Текст: электронный // URL: https://www.iprbookshop.ru/115398.html
- Экономический анализ деятельности предприятия: учебное пособие. — Самара: Самарский государственный технический университет, ЭБС АСВ, 2020. — 84 c. — Текст: электронный // URL: https://www.iprbookshop.ru/105093.html
- HR-Академия: Рост производительности труда — главный показатель эффективности управления персоналом. — URL: https://hr-academy.ru/hrarticle/rost-proizvoditelnosti-truda---glavnyiy-pokazatel-effektivnosti-upravleniya-personalom.html