Актуальность темы.
Одним из наиболее экономичных способов повышения качества проката является повышение надежности уравновешивающего устройства шпиндельных соединений, так как во время работы происходит интенсивный износ подшипников скольжения опор шпиндельного вала, что сказывается на возникновении динамических нагрузок в главной линии прокатного стана, влияющей на качество выпускаемой продукции, и, как следствие, технической надежности элементов шпиндельного соединения. Известная конструкция уравновешивающего устройства характеризуется жесткими опорными элементами в виде вкладышей, установленных в корпусах, прикрепленных к балкам, а также жестким соединением тяг уравновешивающего механизма с траверсой, связанной с верхними балками, что значительно снижает срок службы уравновешивающего устройства из-за невозможности обеспечить равномерное нагружение его элементов. В процессе эксплуатации происходит изнашивание вкладышей шпинделя и вкладышей опорных элементов, что приводит к смещению в пространстве
геометрической оси вала шпинделя относительного его оси вращения, в результате чего возникает центробежная сила, вызывающая поперечные колебания вала шпинделя и дополнительные ударные нагрузки, воздействующие на опорные элементы уравновешивающего устройства. Эти дополнительные нагрузки вызывают усталостное разрушение вкладышей опорных элементов и уменьшают срок службы уравновешивающего устройства. Кроме того в существующей конструкции происходят частые отказы резьбовых соединений, используемых для крепления тяг уравновешивающего механизма к траверсе, соединенной с верхними балками устройства, из-за действия дополнительных срезающих и изгибающих сил, возникающих вследствие непараллельности продольных осей гидроцилиндра и тяг уравновешивающего механизма, что вызывается неточностями изготовления отверстия для расположения гидроцилиндра. Так как крепление тяг выполнено жестким в виде резьбовых соединений, то у них нет возможности занять в пространстве положение, в котором срезающие и изгибающие силы отсутствуют, что приводит к разрушению резьбовых соединений и, следовательно, к аварии уравновешивающего устройства. В разработанной конструкции эти недостатки исключаются за счет того, что опорные элементы, поддерживающие вал шпинделя, представляют собой две пары роликов, каждая из которых установлена в коромысле, размещенных так, что оси, проходящие через центры роликов пары, расположены друг к другу под углом 60 градусов относительно вертикальной оси, проходящей через ось вращения вала шпинделя. В процессе эксплуатации происходит смещение в пространстве геометрической оси относительно оси вращения вала шпинделя из-за износа его вкладышей. При этом за счет обеспечения контакта вала шпинделя с роликами, происходит поворот каждой пары роликов вокруг оси коромысла на угол, при котором обеспечивается равенство сил, действующих на ролики. Крепление тяг уравновешивающего механизма к траверсе выполнены с помощью карданных шарниров и при непараллельности осей гидроцилиндра и тяг уравновешивающего механизма, под действием
горизонтальной силы, кронштейн карданного шарнира может провернуться вокруг крестовины, в результате чего тяга займет новое положение, в котором срезающие и изгибающие силы будут отсутствовать. Благодаря наличию карданных шарниров и роликовых опорных элементов обеспечивается равномерное распределение нагрузок на элементы устройства для уравновешивания шпинделей, что способствует повышению их долговечности.
|
Основные результаты работы.
Разработанная конструкция уравновешивания шпиндельного вала исключает общие недостатки уравновешивающих устройств, существующих на данный момент. Крепление тяг данного уравновешивающего механизма к траверсе выполнено с помощью карданных шарниров, а опорные элементы, поддерживающие вал шпинделя, представляют собой две пары роликов, каждая из которых установлена в коромысле, размещенных так, что оси, проходящие через центры роликов пары, расположены друг к другу под углом 60 градусов относительно вертикальной оси, проходящей через ось вращения вала шпинделя. Данная конструкция имеет небольшие габариты, обладает саморегулировкой и обеспечивает точность позиционирования шпиндельного вала.
Рисунок 1 дает более полное представление о месторасположении роликовых опор.
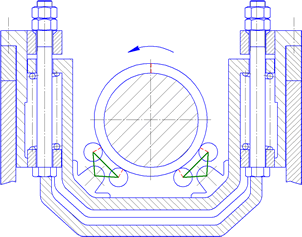
Рисунок 1 – Роликовый балансир
На рисунке 2 а) изображена кинематическая схема уравновешивающего устройства с предлагаемым креплением тяги гидроцилиндра к траверсе шпиндельного вала через карданный узел [рис. 2 б)], который дает дополнительно 2 степени свободы по сравнению с работающим на данный момент жестким креплением тяги, при использовании которого возникали аварийные отказы, что влекло в свою очередь простои стана.
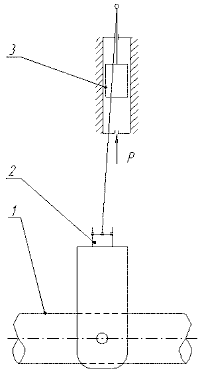
а) кинематическая схема уравновешивающего устройства: 1 – шпиндельный вал, 2 – карданный узел, 3 – гидроцилиндр;
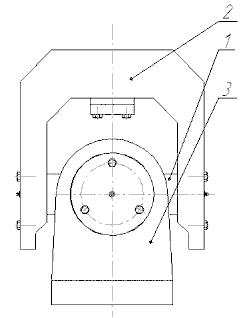
б) карданный узел: 1 – крестовина; 2 – верхний кронштейн; 3 – нижний кронштейн;
Рисунок 2 – Уравновешивающее устройство
1.Определение расчетной нагрузки, действующей на ролик.
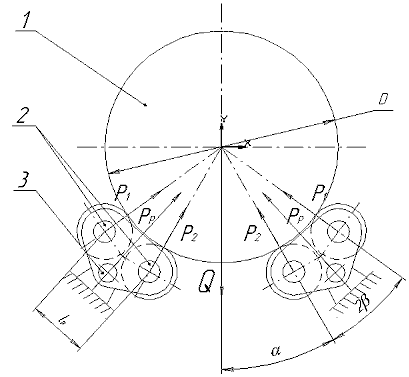
1 – шпиндельный вал; 2 – опорные ролики; 3 – ось.;
Рисунок 3 – Расчетная схема роликовой опоры.
где Q – нагрузка действующая на балансирную опору, Q=111,53кН;
α=30° – угол между вертикалью и осью ролика;
β=arctglp/D=arctg190/600=17,5°;
lp – межцентровое расстояние роликов;
D – диаметр вала;
Из рисунка 3 определяем численные значения реакций Р1и Р2:
P1=Q/[4*cos(α+2*β)]=111530/[4*cos(30°+2*17,5°)]=65975,6 H;
P2=Q/[4*cosα]=111530/[4*cos30°]=32196 H.
Дальнейшие расчеты будем вести по наибольшей силе Р1.
2.Определение изгибающего момента, действующего в опорном ролике.
Определим значение распределенной нагрузки, действующей со стороны вала на опорный ролик:
q=P1/0,245*2=65975,6/0,490=134644,1 H.
Определим значение реакций опор N1 и N2 для построения эпюры изгибающих моментов:
∑MA=0; N2*(2*a+2*b)-P1*(b+a)=0.
Откуда выражаем искомую силу N2 и получаем:
N1=N2=P1(b+a)/(2*b+2*a)=65975,6*(0,245+0,084)/(2*0,245+2*0,084)=32987,8 H.
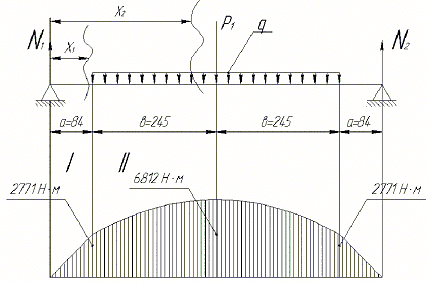
Рисунок 4 – Эпюра изгибающих моментов
В сечении 1 при х1=84мм, значение изгибающего момента будет равно:
M1-1=N1*x1=32987,8*0,084=2771 Н·м ,
а в сечении 11-11 при х2=329мм
M11-11=N1*x2-[q(x2-a)2]/2=32987,8*0,329-[134644,1*(0,329-0,084)2]/2=6812 Н·м.
Так как в сечении 11-11 значение изгибающего момента наибольшее, дальнейший расчет будем вести по этому значению.
3.Определение диаметра ролика.
Исходя из конструктивных соображений, принимаем диаметр ролика d=100мм.
Выполним проверку ролика на смятие.
Значение местных напряжений смятия при линейном контакте:
σсм=0,418√(Pв * Eпр/b * r) ≤ [σсм],
где [σсм]– допускаемое напряжение на смятие, [σсм]=8,5МПа;
b – толщина ролика, b=0,06м,
Pв – расчетная нагрузка на вал,
Pв=k * γ * Pр,
где k – коэффициент, учитывающий режим работы механизма, k=1,6,
γ – коэффициент, учитывающий переменность нагрузки, γ=0,8,
Pр – нагрузка на один ролик
Pр=(G + Q) / 8,
где (G + Q) – сила давления вала шпинделя,
8 – количество роликов.
Eпр – приведенный модуль упругости для стального ролика и стального вала, Eпр=2,1*109 Па,
r – радиус ролика, r=0,05м.
Расчитаем местное напряжение смятия при линейном контакте.
Так как результат расчета удовлетворяет заданному условию смятия, то диаметр ролика оставляем равным 100мм.
4.Расчет оси опорных роликов.
Определим изгибающий момент, действующий на ось балансира.
Ось не передает вращающего момента, а воспринимает только поперечные нагрузки.Вращающуюся ось расчитываем на изгиб как балку на шарнирных опорах. За центр шарнирных опор принимаем середины подшипников скольжения.
Расчетная схема определения диаметра сплошной цилиндрической оси представлена на рисунке 5.
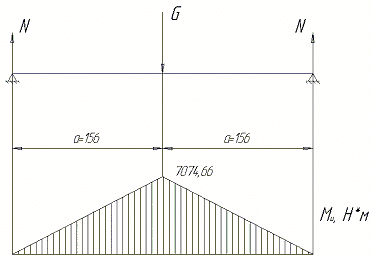
Рисунок 5 – Эпюра изгибающих моментов
Определим реакции опор RAиRB:
∑MA=0; RB*b-N4*(b+a)+N3*a=0;
откуда
RB=[N4*(b+a)-N3*a]/b,
где N3 и N4 – силы, действующие на ось.
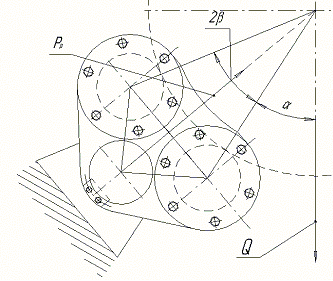
Рисунок 6 – Силы, действующие на роликовую опору
N3=N4=Pp/2=82542,6/2=41271,3 Н;
Pp – реакция со стороны опоры на вал, которая равна:
Pp=Q/2*cos(α+β)=111530/2*cos(30°+17,5°)=82542,6 H.
Подставив ранее найденное значение сил N3 и N4 в формулу для определения реакции RB,получим:
RА=RВ=[41271,3*(0,34+0,1615)-41271,3*0,1615]/0,34=41271,3 Н.
Определим изгибающий момент, действующий на данную ось при х=а=161,5:
Mи=N3*a=41271,3*0,161=6644,7 Н·м.
5.Расчет гидроцилиндра.
Произведен расчет гидроцилиндра уравновешивающего устройства, нагружение на который определялось из условия веса шпиндельного соединения и веса верхнего валка с подушками [4].
В гидроцилиндре могут быть следующие соединения: соединения головок с гильзой, болты фланцевого крепления крышек, стяжные болты, соединяющие головки, резьба штока. Все эти резьбовые соединения рассчитываются по методике, принятой в общей машиностроении [5].
6.Расчет крестовины.
Так как крестовина имеет не одинаковые пальцы (это было сделано исходя из конструктивных соображений), то последующий расчет будем вести по наибольшему пальцу.
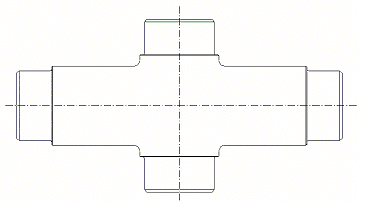
а) общий вид;
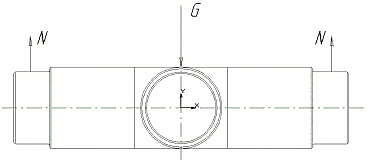
б) рабочее положение;
Рисунок 7 – Крестовина
Определим силы, действующие на крестовину.
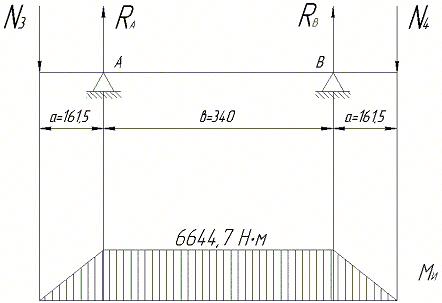
Рисунок 8 – Эпюра изгибающих моментов
Определим значение реакций N:
N=G/2,
где G – часть силы тяжести от шпиндельного вала, приходящаяся на одну тягу уравновешивающего устройства, G=90700,8 H.
N=90700,8/2=45350,4 H.
Момент изгибающий будет равен:
Mи=N*a=45350,4*0,156=7074,66 Н·м.
Диаметр оси, работающей на изгиб, определим из формулы:
σи=Mи/W≤[σв],
где Mи – изгибающий момент;
W – полярный момент, который равен:
W=π*d 3/32=0,1*d 3;
d – диаметр оси крестовины.
Подставив значение полярного момента сопротивления в формулу и выразив d, получим:
d=3√(Mи/0,1*[σи]),
где [σи] – допускаемое напряжение на изгибе, которое в свою очередь равно:
[σи]=σв/S,
где σв – временное сопротивление растяжению, σв=1370МПа для стали 40ХН (закалка 820° в масле, с последующим отпуском 400° на воздухе);
S – общий коэффициент запаса прочности, который определяется по формуле:
S=S1*S2*S3,
где коэффициент S1=1 … 1,5 – достоверность определения расчетных нагрузок и напряжений;
коэффициент S2=1,2 … 1,5 – однородность механических свойств материалов (для стальных деталей из поковок и проката);
коэффициент S3=1 … 1,5 – специфические требования безопасности.
Расчитаем диаметр крестовины.
Исходя из конструктивных соображений, принимаем диаметр крестовины d=75мм.
6.Определение напряженного состояния деталей уравновешивающего устройства.
С помощью программы ANSYS были выполнены расчеты напряженного состояния деталей уравновешивающего устройства.
На рисунке 9 представлена конструкция в исходном положении.
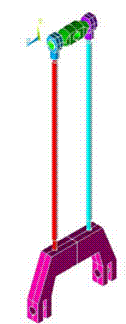
Рисунок 9 – Уравновешивающее устройство
Приложим силу F=299,6 кН и давление P=0,77 МПа (с учетом отклонения оси гидроцилиндра на 3° от вертикали) и, после расчетов, получим деформированную конструкцию, представленную на рисунке 10.
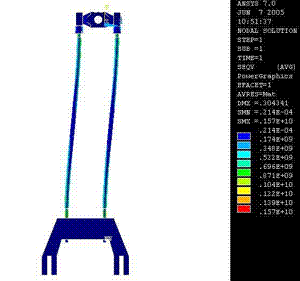
Рисунок 10 –Уравновешивающее устройство деформированное
При приближении (рисунок 11, рисунок 12) можно увидеть максимальные напряжения, возникающие в тягах, и места, где возможно разрушение материала (выделенны красным цветом).
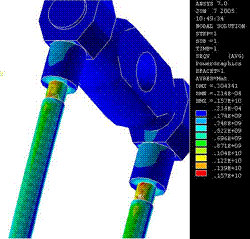
Рисунок 11 –Соединение тяги с проушиной
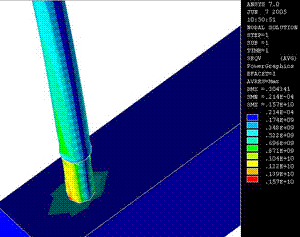
Рисунок 12 –Соединение тяги с траверсой
|