Главная страница ДонНТУ
Сайт магистров ДонНТУ
Поисковая система ДонНТУ
Главная страница
Автореферат магистерской работы
Электронная библиотека
Аннотированные ссылки
Результаты поиска
Индивидуальное задание
Анализ временных реализаций вибрационного сигнала
Сидоров В.А., Куватов А.В., Куришева Е.П.
(Донецкий национальный технический университет, ЗАО "ММЗ "Истил (Украина)", г. Донецк, Украина)
Предложены методы анализа временных реализаций вибрационного сигнала для оценки технического состояния механического оборудования.
1. Проблема и ее связь с научными и практическими задачами. Основным средством получения информации о техническом состоянии механических систем является измерение вибрации. Определение наиболее эффективных методов анализа временных реализаций вибрационного сигнала позволит оценивать техническое состояние механизмов, работающих в кратковременном режиме.
2. Анализ исследований и публикаций. В работах [1 — 4] наиболее полно исследовались измерение общего уровня вибрации, измерение параметров вибрационного сигнала, спектральный анализ вибрационного сигнала. Переходные процессы, являющиеся характерной особенностью металлургического оборудования, требуют анализа временного сигнала для контроля быстропротекающих процессов. Существующие технические решения не позволяют эффективно использовать диагностическую информацию о временных реализациях.
3. Постановка задачи. Необходимо разработать методы анализа временного сигнала параметров вибрации, которые позволят наиболее эффективно получать и использовать информацию о техническом состоянии механического оборудования, работающего в кратковременном режиме.
4. Изложение материала и результаты. Наиболее информативным методом получения информации о техническом состоянии механического оборудования в настоящее время является анализ параметров вибрационного сигнала. Для решения различного уровня практических и исследовательских задач используется: анализ шумов механизмов, измерение общего уровня вибрации, измерение параметров вибрации, анализ спектра вибрационного сигнала и анализ временных реализаций.
Развитие методов виброметрии начиналось с анализа форм полигармонических сигналов [5]. Реализация практических задач распознавания технического состояния оборудования потребовало измерения среднеквадратичных параметров вибрации, что и подтвердилось соответственным уровнем развития приборного обеспечения. Различение неисправностей на ранней стадии развития в наибольшей степени отвечает возможностям спектрального анализа вибрации, решаемого на базе компьютерных технологий. Расширение объектов диагностирования, необходимость распознавания фактического состояния механизмов, работающих в кратковременном режиме, требует разработки методологии анализа временных реализаций вибрационного сигнала на новом современном уровне требований решения практических задач.
Измерение общего уровня вибрации позволяет определить категорию технического состояния оборудования, используя методы взаимного, относительного или абсолютного сравнения. Измерение параметров вибрационного сигнала (ударный импульс, пик-фактор, огибающая виброускорения) используется для оценки технического состояния подшипниковых узлов оборудования. Спектральный анализ вибрационного сигнала обеспечивает выявление, идентификацию повреждений и возможность анализа тенденций их развития начиная с самой ранней стадии. Анализ временных реализаций используется относительно редко, позволяя судить о стабильности протекающих процессов в механизме.
Решение задач распознавания повреждений с использованием аппарата спектрального анализа параметров вибрации для механизмов длительного режима работы рассматривается во многих работах [1 — 4]. Практическая реализация рекомендуемых подходов позволяет с достаточной точностью диагностировать механизмы роторного типа. В то же время существует целый ряд машин, имеющих кратковременный и повторно кратковременный режим нагружения. К данному классу оборудования следует отнести металлургические машины, отличающиеся значительными габаритами, большой мощностью привода, наличием значительных, часто нестабильных динамических нагрузок, а также подъемные машины горных предприятий, имеющие аналогичные характеристики. Определение технического состояния в данном случае затрудняется в виду непредсказуемости воздействия рабочих нагрузок. В первую очередь это механизмы привода рабочих валков заготовочных и обжимных станов, ножницы горячей резки, механизмы металлургических кранов, скиповые лебедки, подъемные машины.
Кратковременность работы механизма в режиме стационарного нагружения, изменения нагруженности узлов на протяжении цикла работы приводят к неоднозначному прочтению данных спектрального анализа. Данный режим вынуждает работать без усреднения либо с минимальным количеством усреднений. Это безусловно влияет на повторяемость получаемых результатов (привести примеры спектров и описать). При сравнении спектров вибрационных сигналов (рис. 1,2,3,4) отмечаем значительные различия в полученных спектрах и совпадение пиковых значений на частоте 2,03 Гц в то же время имеющих различные амплитудные значения (соответственно: 0,89 мм/с, 1,39 мм/с, 0,95 мм/с, 0,85 мм/с). Также на спектрограммах можно увидеть повышение виброактивности в полосе 20…50 Гц., имеющих разные СКЗ в этой полосе. Неоднозначность результатов анализа не позволяет давать оценку технического состояния агрегата.
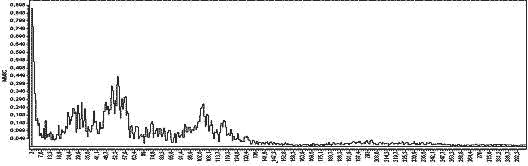
Рисунок 1 — Спектр вибросигнала, снятый с корпуса шестеренной клети 900 во время проката. Количество усреднений — 4 (СКЗ V в полосе 2…400 Гц — 2.7 мм/с)
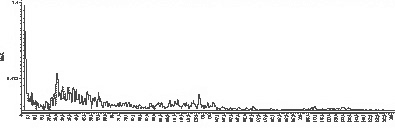
Рисунок 2 — Спектр вибросигнала, снятый с корпуса шестеренной клети 900 во время проката. Количество усреднений — 4 (СКЗ V в полосе 2…400 Гц — 2.8 мм/с)
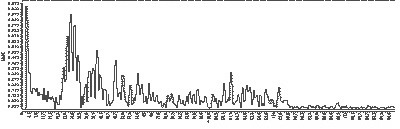
Рисунок 3 — Спектр вибросигнала, снятый с корпуса шестеренной клети 900 во время проката без усреднений (СКЗ V в полосе 2…400 Гц — 3.6 мм/с)
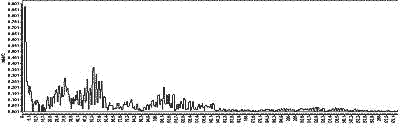
Рисунок 4 — Спектр вибросигнала, снятый с корпуса шестеренной клети 900 во время проката без усреднений (СКЗ V в полосе 2…400 Гц — 2.1 мм/с)
Использование тестового режима диагностирования (определение технического состояния механизма в режиме холостого хода) не позволяет судить о характере восприятия механизмом рабочих нагрузок. Обычно отмечается увеличение токовых характеристик в 2…3 раза электродвигателей машин во время рабочего процесса. Аналогично, значительно возрастают и механические нагрузки. Следовательно, отсутствие контроля технического состояния машины во время рабочего хода может привести к существенным ошибкам при определении фактического состояния и способности механизма выполнять заданные функции.
Известным фактом при диагностировании механических систем является высокая информативность переходных процессов (разгон, торможение, изменение нагрузки). Именно в этом периоде происходит закрытие зазоров, первые проявления повреждений. Сложность решения в данном случае усугубляется изменением частоты колебаний из-за увеличения или уменьшения скорости процесса, нестабильностью нагрузок (различия прокатываемых профилей, изменение температуры металла) и субъективностью процесса управления. Оптимальным решением является анализ временных реализаций вибрационного сигнала.
Предварительно рассмотрим природу возникновения механических колебаний на примере одномассовой системы (рис. 5). Параметрами данной системы являются: масса — m, жесткость — c, коэффициент демпфирования — h. Колебания системы возможны при воздействии силы — F, переменной относительно направления колебаний. Сила F может быть и постоянной, однако параметры контактирующих поверхностей могут служить причиной ее периодического изменения. Например, сила тяжести при взаимодействии с изношенной поверхностью подшипника при вращении вала служит источником колебаний. Частотная характеристика в данном случае укажет на характер повреждения.
Параметры колебательного процесса определяются следующим уравнением, в котором k — частота собственных колебаний системы, ε — параметр, определяющий демпфирующие свойства системы:
ε = h / 2m
Наличие повреждений в механической системе могут приводить к изменению жесткости (например, износ деталей, ослабление резьбовых соединений), изменению коэффициента демпфирования (в случае появления трещин), изменения воздействующих сил (при изменении шероховатости контактирующих поверхностей). Различение технического состояния при стационарном процессе колебаний возможно при изменении одного из указанных параметров, либо при введении дополнительных проверок. Например, изменение жесткости системы одновременно приводит к изменению частоты собственных колебаний системы. Изменение параметров демпфирования приведет к изменению времени затухания колебаний в механической системе
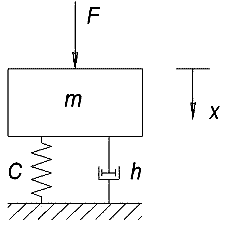
Рисунок 5 — Одномассовая система
В то же время колебания механической системы носят случайный характер при каждом конкретном цикле колебаний, определяемом целым рядом факторов: значением воздействующих сил, контактом взаимодействующих поверхностей, реализующим проявление повреждений. Предполагается следующая зависимость — большие повреждения приводят к увеличению разброса параметров колебательного процесса. Это создает предпосылки для распознавания состояния механической системы исходя из анализа временных реализаций вибрационного сигнала.
Временная реализация вибрационного сигнала механизма кратковременного режима работы может быть охарактеризована двумя факторами — текущими положительными и отрицательными значениями амплитуды колебаний Ai, -Ai и соответствующими периодами колебаний Ti (рис.6).
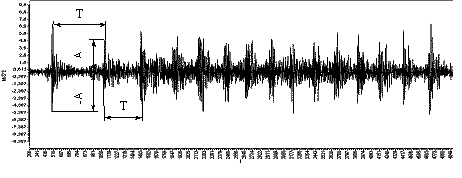
Рисунок 6 — Временная реализация вибрационного сигнала
В результате имеем двухмерное диагностическое пространство, для которого можем определить координаты исследуемой выборки (конкретной совокупности реализаций временного сигнала):
где Ak и Тk — математическое ожидание соответствующих координат, n — количество наблюдений. Дисперсия k-той двухмерной выборки характеризуется также двумя значениями S2k(A) и S2k(Т):
Обнаружение неслучайных отклонений может быть выполнено по методу средних [1]. Различие между выборками k и l оценивается с помощью критерия Стьюдента по одной из выбранных координат, например:
Различие в техническом состоянии объекта признается существенным (неслучайным), если выполняется условие: |t| >= tc(n, p), где tc(n, p) — коэффициент Стьюдента для числа степеней свободы n = nk + nl - 2 и доверительной вероятности p.
Сравнение результатов измерений может быть проведено путем оценки неслучайных отклонений по контрольным уровням [1]. Для этого используется гистограмма зависимости: Ni = f(νi), где Ni — количество наблюдений в i-м единичном диапазоне; νi — диапазон регистрируемых значений. Граница интервала определяется выражением νср + 2σ, где νср — среднее значение, σ — среднеквадратичное отклонение; включающее более 95% реализаций, может служить предельно допустимым значением параметра состояния для данного механизма (привести пример гистограммы: измеряемый параметр — количество реализаций). На рис.7 приведена гистограмма, при построении которой в качестве измеряемого параметра выступает виброускорение.
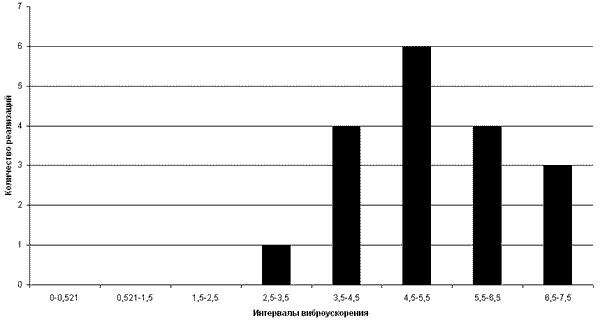
Рисунок 7 — Гистограмма
Для определения границ различения технических состояний была высказана гипотеза о соответствии изменения технического состояния характеру физических процессов, протекающих в механизме — изменение характера контакта в подшипнике скольжения от жидкостного к полужидкостному режиму смазывания неизбежно вызовет изменение технического состояния. Предположительно, граничные переходы должны быть связаны с искажениями непрерывности функций диагностической меры расстояния Nν, Nν2 в виде ступенчатых переходов. Это объясняется работой механизма в зоне неустойчивого равновесия при вибрации, соответствующей границам технических состояний.
Изменение технического состояния приведет к отклонению функции Ni = f(νi) от нормального распределения.
В общем случае в колебательной системе одновременно имеют место потери энергии, обусловленные различными причинами [6]: скоростью деформаций, жесткостью системы, сухим трением, способностью к демпфированию колебаний. Оценить стабильность демпфирующих свойств механической системы возможно при определении декремента колебаний δ как натурального логарифма отношения двух последующих амплитуд:
δ = ln (Ai / Ai+1)
При реализации временного сигнала вибрации появляется возможность измерения данного показателя (рис.8).
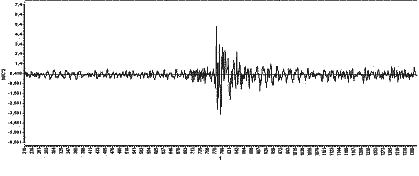
Рисунок 8 — Временные реализации вибрационного сигнала, измеренные в промышленных условиях
5. Выводы и направление дальнейших исследований. Определена возможность оценки технического состояния при помощи анализа временных реализаций вибрационного сигнала для машин кратковременного режима работы. Рассмотрены причины возникновения механических колебаний на примере одномассовой системы. Рассмотрены методы анализа временного сигнала и получения границ распознавания в пространстве диагностических признаков.
Список источников:
1. Биргер И. А. Техническая диагностика. — М.: Машиностроение, 1978. — 240с.
2. Виброакустическая диагностика зарождающихся дефектов/Ф. Я. Балицкий, М. А. Иванова, А. Г. Соколова, Е. И. Хомяков. — М.: Наука, 1984.
3. Коллакот Р. А. Диагностирование механического оборудования: Пер с англ. — Л.: Судостроение, 1980. — 296с.
4. Коллакот Р. А. Диагностика повреждений: Пер с англ. — М.: Мир, 1989. — 512с.
5. Иориш Ю. И. Виброметрия. Измерение вибрации и ударов. Общая теория, методы и приборы. — М.: Машгиз, 1963.
6. Обобщенная нелинейная модель учета рассеяния энергии при колебаниях/Писаренко Г.С. — Киев: Наук.думка. 1985. — 240 с.
Главная страница
Автореферат магистерской работы
Электронная библиотека
Аннотированные ссылки
Результаты поиска