Актуальность темы
Поверхности проката подвергаются зачистке. В зависимости от группы поверхности заготовку подвергается выборочной или сплошной зачистке. Наружный слой снимают ровными бороздками вдоль цилиндрической части прутка в местах, имеющих дефекты. Обдирке подвергаются заготовки, поставка которых по техническим условиям и стандартам должна производится в ободранном состоянии, а также заготовки, требующие переточки на меньший диаметр из-за поверхностных дефектов. Обдирка проката производится на бесцентрово-токарных станках 9А340Ф1 и КЖ9340.
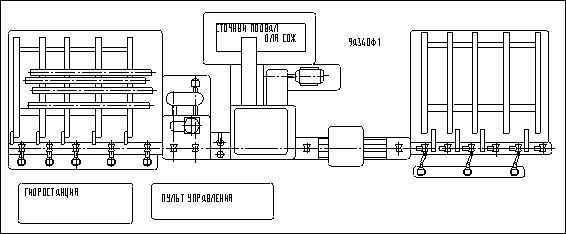
Рисунок 1 – Обдирочный станок 9А340Ф1
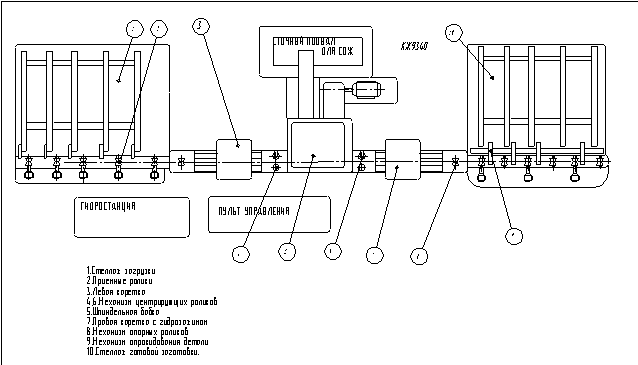
Рисунок 2 – Обдирочный станок КЖ9340
Бесцентрово-токарные обдирочные станки работают в сравнительно тяжелых условиях, в условиях больших динамических нагрузок. Поэтому часто происходят поломки, что приводит к простою.
Для успешной эксплуатации станков в условиях перестройки народного хозяйства нашей страны используются новые принципы и подходы для решения задач технического обслуживания и ремонтов. К таким новым подходам на современном этапе в первую очередь относится широкое использование стационарных средств технической диагностики, позволяющих сократить затраты труда на обслуживание и ремонт.

|
Цель и задачи
Цель работы заключается в поиске наиболее часто выходящих из строя узлов станков для установления на них датчиков. Для этого необходимо:
- произвести анализ отказов;
- выбрать метод диагностирования;
- определить точки установки датчиков;
- разработать стационарную систему диагностирования.

|
Научная новизна
Цель работы: разработать 32-канальную стационарную систему диагностирования для бесцентрово-токарных станков 9А340Ф1 и КЖ9340.До этого этим вопросом мало кто занимался. Именно поэтому она представляет научную новизну как для кафедры «МОЗЧМ», так и для персонала обслуживающего данное оборудование.
|
|
Практическая ценность
Планируемый практический результат: система диагностирования позволит следить за работоспособностью станков автоматически при помощи приборов и в случае критического состояния одного из узлов, даст знать оператору на пульт управления станком о неисправности.

|
Обзор существующих исследований
Проблемы:
Бесцентрово-токарные обдирочные станки работают в сравнительно тяжелых условиях, в условиях больших динамических нагрузок. Основными отказами таких станков являются :
- Неполадки подачи смазки в шпиндельный узел. Это приводит к досрочному изнашиванию уплотняющих манжет. Такая поломка чаще всего происходит из-за малой подачи масла, и подачи большого количества воздуха к подшипникам шпинделя (в этих станках применяют систему смазывания “Масло-воздух”).
- Заклинивание подшипников на подающих роликах. Заклинивание происходит от удара заготовки при попадании ее на ролики. Также одной из причин заклинивания может быть и нехватка смазки в подшипниках роликов.
- Прокручивание заготовки в тисах (центрирующем устройстве). Отказ происходит от малого усилия на прижимном гидроцилиндре. Причин поломок гидроцилиндра очень много: износ уплотнений, загрязнение подводящего трубопровода, неполадки в насосной установке и т.д. Тиса (ролики) имеют рифленую поверхность. Повреждение этой поверхности приводит к уменьшению силы трения между заготовкой и поверхностью. Этот фактор также влияет на прижимное усилие и даже при нормальном рабочем давлении гидроцилиндра заготовка может прокручиваться. Повреждение поверхности тисов может происходить и из-за малой твердости материала, что играет очень большую роль при эксплуатации механизма.
- Неравномерная подача заготовки. Одной из причин неисправности может быть проблемы с приводом, второй причиной может быть износившаяся поверхность направляющих станков. Направляющие имеют не идеально ровную форму, и именно из-за перепадов неровностей привод перемещается неравномерно.
- Перегрев маслостанции. Перегрев говорит о том что, неисправна система смазки, либо появились детали, между поверхностями которых повышенное трение [7,стр.56]. Если вовремя не обратить внимание, то это может привести к аварийной ситуации.
Все выше приведенные отказы могут привести к остановке оборудования, и поэтому требуют дополнительного внимания. Очень немаловажно за ними следить, так как даже заклинивание подшипников может привести к значительным материальным потерям для предприятия.
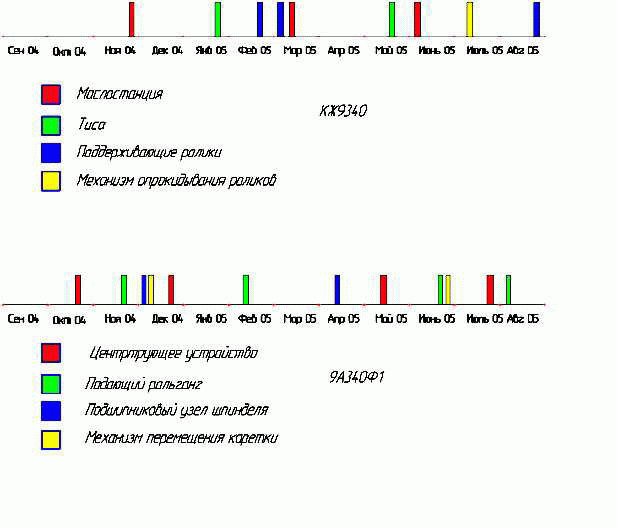
Рисунок 3 – Временный анализ отказов станков
Решение:
Для диагностики деталей, входящих в характерные узлы, выберем следующие диагностические параметры:
1. Уровень шума;
2. Уровень вибраций (виброскорость, виброускорение);
3. Температура;
4. Деформации.
Для фиксации и контроля вышеперечисленных параметров можно применить следующие виды средств диагностирования:
1. Ручной или электронный стетоскоп;
2. Виброметр ВШВ-003-1М;
3. Зубомер, индикаторный щуп Г112-5-0ММ11;
4. Температурные датчики;
В станках используются подшипники качения, зубчатые передачи, а так же возможны задевания и кавитация, то необходимо следить за высокочастотной составляющей вибрации. Подшипники качения удобно диагностировать по вибрации, сосредоточенной на частотах порядка килогерц (50-70 гармоники от оборотной частоты). Дефекты зубчатых передач локализуются на частотах «зацепления», равных произведению частоты вращения шестерни на число зубьев, находящихся на ней. Контролируемая полоса должна включать в себя частоту зацепления. При вероятности возникновения задеваний, вибрация, так же как и при дефектах подшипников качении имеет всплеск на нескольких килогерцах.
В системе мониторинга для измерения вибрации могут использоваться как автономные датчики, устанавливаемые в точки измерения с использованием магнита или винтовой шпильки или удерживаемые вручную при использовании измерительного щупа, так и стационарно установленные штатные датчики системы непрерывного контроля вибрации.
Пьезоэлектрические акселерометры - самые универсальные и наиболее часто используемые датчики на сегодняшний день. Акселерометр является преобразователем механических колебаний объекта в электрический сигнал пропорциональный виброускорению. В результате пьезоэлектрического эффекта на поверхности пьезоэлемента возникает электрический сигнал пропорциональный воздействующей силе и ускорению механических колебаний. Частотный диапазон от 0 до 1/3 резонансной частоты акселерометра (обычно 30 кГц). Акселерометры имеют в основном линейную амплитудную чувствительность, стабильно работают длительное время, нуждаются только в периодической калибровке.
Перегрев маслостанции можно контролировать термодатчиком, который бы передавал сигнал о перегреве на пульт программисту.
Эффективность:
Эффективность металлургических предприятий в значительной мере будет определяться надежностью оборудования.
Для успешной эксплуатации металлургических станков используются новые принципы и подходы для решения задач технического обслуживания и ремонтов. К таким новым подходам на современном этапе в первую очередь относится широкое использование вычислительной техники и средств технической диагностики, позволяющих сократить затраты труда на обслуживание и ремонт.
Относительно невысокая стоимость переносных систем (в 2-3 раза ниже стоимости систем ведущих западных производителей) и повышенная ремонтопригодность собственно стационарных систем диагностики, позволяющая быстро восстанавливать их после повреждений при проведении ремонтов диагностируемых машин, позволяют выигрывать конкурентную борьбу у западных производителей. Этому способствует и деятельность отечественных фирм по обучению и поддержке пользователей диагностических систем.
Как правило, многие предприятия начинают внедрение систем мониторинга и диагностики с переносных систем, не требующих длительной подготовки специалистов. Такие системы окупаются в 2-3 месяца, особенно на крупных производствах. И лишь на втором этапе, в процессе модернизации машин и оборудования, начинают монтироваться и вводиться в действие небольшие стационарные системы мониторинга и диагностики, рассчитанные на 50-100 точек контроля.

|
Основные результаты работы
1. Определение коэффициента запаса прочности колеса редуктора:
Для зубчатых колес коэффициент запаса прочности рассчитывают по двум показателям:
- По изгибу:
nизгибающее=(G изгиб.факт.*K напр)/[G]изгиб.допуск.
где Кнапр.-коэффициент учитывающий изменение напряжений изгиба (Кнапр=1,2 так как передача реверсивная),
[G]изгиба-допускаемое значение напряжения изгиба:
[G]изгиб.допуск.=(0,8...0,9)Gтеор.
где где Gтекучести-предел текучести (для Ст40Х = 700 МПа) [1,табл.2,4, стр 43-44]
[G]изгиб.допуск.=0,8*700=560 МПа
G изгиба фактическое –фактическое напряжение изгиба,
Gизгиба фактическое=10HRC+300=10*50+300=800 МПа
nизгиба=(800*1,2)/560=1,71
- По контактной прочности:
nконтактное=G конт.факт.*Zдолговечности)/[G]конт.допуск.
где Zдолговеч.-коэффициент долговечности (Zдолговечности=1,8) [1,рис. 2,6, стр. 40],,
[G]контакт допускаемоедопускаемое значение напряжения по контактной прочности:
[G]конт.допуск.=1,8Gтекуч.
где где Gтекучести-предел текучести (для Ст40Х = 700 МПа) [1,табл.2,4, стр 43-44]
[G]конт.допуск.=1,8*700=1260МПа
G конт.фактическое –фактическое напряжение по контактной прочности,
Gконт.фактическое=17HRC+200=17*50+200=1050 МПа
nконтакт.=(1050*1,8)/1200=1,5
2. Определение усилия резания:
P=CpTxSyVn
где Cp- постоянная, которая характеризует вид обработки (Cp=300).[2, табл.20, стр.429].
x, y, n –показатели степени,
x=1,y=0.75, n=-0,13 [2, табл.20, стр.429].
t –длина лезвия резца (t=15мм),
s –подача заготовки (s=1.3 мм/об),
v –скорость резания, определим по формуле:
V=3.14*n*D/60
где n –частота вращения шпинделя (n=2,33 об/сек),
D –диаметр обрабатываемой заготовки (D=200 мм),
V=3.14*2.33*0.2/60=0.0244 м/с
Усилие резания:
P=300*151*1,30,75*24,4-0,13=3624,2 Н
3.Нарушение уравновешенности валов - дисбаланс.
Вибрация неуравновешенного вала проявляется в виде синусоидальных колебаний с частотой вращения вала. В спектре колебаний при этом присутствует значительный пик на частоте вращения: fповр = fвp, где fповр - частота проявления повреждения; fвр - частота вращения вала. Так как дисбаланс приводит к увеличению нагрузок на опоры, в большей степень проявляются и другие повреждения на частотах кратных частоте вращения (гармониках).
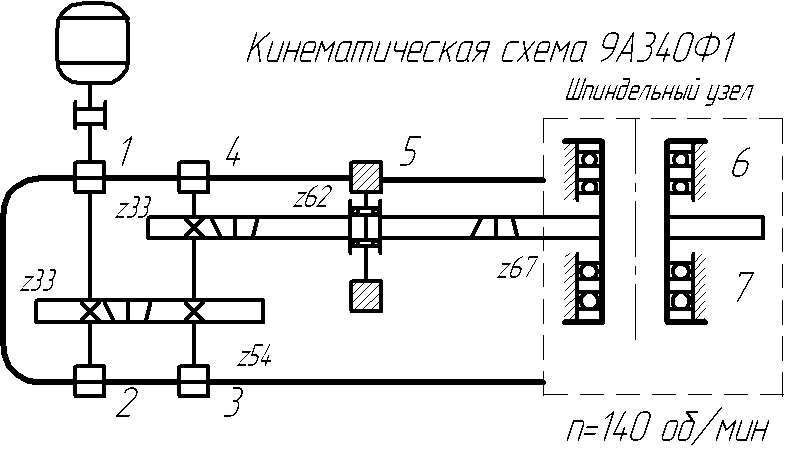
Рисунок 4 – Кинематическая схема 9А340Ф1
fповр1=n*(67/33)*(54/33)=140*(67/33)*(54/33)=465.12 ГЦ
fповр2=n*(67/33)=140*(67/33)=284,24 Гц
fповр4=n=140 Гц
4.Повреждения подшипников качения шпиндельного узла.
Появление большого количества составляющих в спектре виброускорения в районе собственных частот подшипников (1000...5000 Гц). В спектре огибающей высокочастотного сигнала либо в спектре колебаний возникают одиночные либо периодические пики с частотой возможных повреждений подшипника :
- повреждения наружного кольца:
fнк0.5*Z*fвр=(1-d*cosβ/D)=0.5*30*140*(1-(52/740))=1952.4 Гц
- повреждения внутреннего кольца:
fвк0.5*Z*fвр=(1+d*cosβ/D)=0.5*30*140*(1+(52/740))=2247.6 Гц
- повреждения тел качения:
fтк=(D*fвр/d)(1-(d*cosβ/D)2)=(740*140/52)(1-(52/740)2)=1982.5 Гц
- повреждения сепаратора:
fc=0.5*fвр*(1-d*cosβ/D)=0,5*140(1-(52/740))=65.1 Гц
где fBP - частота вращения вала; z - число тел качения; d - диаметр тел качения; β- угол контакта; D - диаметр окружности, проходящей через центры тел качения.
5.Повреждения зубчатых передач.
Появление в спектре одиночных либо периодических зубцовых частот: fповр = z fBp, где z - число зубьев колеса. Появление в спектре боковых составляющих с частотой вращения. Возможны гармонические составляющие данных повреждений:
fповр.Z67=Z67*fвр=67*140=9340 Гц
fповр.Z62=Z62*fвр=67*140=9340 Гц
fповр.Z33-2=Z33*fвр=33*(67/62)*(62/33)*140=9340 Гц
fповр.Z54=Z54*fвр=54*(67/62)*(62/33)*140=15349.1 Гц
fповр.Z33-1=Z33*fвр=33*(67/62)*(62/33)*(54/33)*140=15349.1 Гц

Выводы
Современные системы мониторинга и диагностики реально обеспечивают переход на обслуживание и ремонт машин по фактическому состоянию. В настоящее время ни одно крупное западное оборудование не поставляется без стационарных систем, и экономический эффект от ее использования учитывается при планировании эксплуатационных затрат.Наша промышленность отличается от западной тем, что большинство машин и оборудования давно выработали ресурс и требуют капитального ремонта или замены. Учитывая этот факт, системы мониторинга и диагностики российского производства стали приспосабливаться к работе с таким оборудованием, и основное внимание уделяют глубокой диагностике наиболее аварийноопасных узлов. Этот факт, а также относительно невысокая стоимость переносных систем (в 2-3 раза ниже стоимости систем ведущих западных производителей) и повышенная ремонтопригодность собственно стационарных систем диагностики, позволяющая быстро восстанавливать их после повреждений при проведении ремонтов диагностируемых машин, позволяют выигрывать конкурентную борьбу у западных производителей. Этому способствует и деятельность отечественных фирм по обучению и поддержке пользователей диагностических систем.
Как правило, многие предприятия начинают внедрение систем мониторинга и диагностики с переносных систем, не требующих длительной подготовки специалистов. Такие системы окупаются в 2-3 месяца, особенно на крупных производствах. И лишь на втором этапе, в процессе модернизации машин и оборудования, начинают монтироваться и вводиться в действие небольшие стационарные системы мониторинга и диагностики, рассчитанные на 50-100 точек контроля.

Литература
1.Методическое указание к самостоятельной работе над курсовым про-ектом по деталям машин», раздел 3 «Эскизный проект. Технический проект» /сост. В.С.Горелик и др.- Донецк: ДПИ, 1992, 84с.
2.Справочник технолога машиностроителя» том 2, А.Н.Малов.М.: «Машиностроение», 1972, 568с.
3.Предупреждение разрушения деталей забойного оборудования / Н. Б. Шубина, Б. П. Грязнов, И. М. Шахтин и др. – М., Недра, 1985. - 215 с.
4. Сидоров В.А., Серебров Л.М. «Основы работы с виброметрами-анализаторами» // Конспект лекций семинара-практикума – Донецк,2003. – 113 с.
5. Марутов В.А. и Павловский С.А. Гидроцилиндры. Конструкция и расчет. – М "Машиностроение", 1966. – 315 с.
6. Производство блюмов, слябов и заготовок из углеродистых и легированных сталей в обжимном цехе. Технологическая инструкция. ТИ – 234 – П.03.01 – 95. Донецкий металлургический завод.: – Донецк, 1995. – 225 с.
7. Целиков А.И., Полухин П.И., Гребеник В.М. и др. Машины и агрегаты металлургических заводов. Том 3. Машины и агрегаты для производства и отделки проката. – М.: Металлургия, 1988. – 576 с.
8. Королев А.А. Конструкция и расчет машин и механизмов прокатных станов. Учеб. пособие для вузов. – М.: "Металлургия". 1985. – 367 с.
9. Анурьев В.И. Справочник конструктора-машиностроителя: В 3-х т. Т.1. – М.: Машиностроение, 1982. – 736 с.
10. Раздаточный материал к выполнению расчетов крюковвывх пдвесок по диссцмплине: "Подъемно-транспортные машины". П.И. Пузырьков. Днепропетровск ., 1991, 28 с.

| |