ЭЛЕКТРОННАЯ БИБЛИОТЕКА
Тихоновича Дениса Юрьевича
Д.Н. Браун, Й.Ц. Йэргенсен Брюль и Къер
Экструдер
На предприятии имеется 7 экструдеров, каждый из которых приводится электродвигателем через редуктор, имеющий 5 валов, включая два шестеренчатых вала самого экструдера (рис. 1 показывает систему шестерен). Состояние экструдеров не контролируется постоянной системой мониторизации, а контроль их состояния входит в программу периодических измерений и анализа.
Изготовитель экструдеров рекомендует разборку механизмов после 25 000 часов работы для ремонта шестеренчатых колес и подшипников с вращающимися элементами. Однако, после введения программы мониторизации механических колебаний со сравнением спектров состояние шестерен и подшипников экструдеров может контролироваться с большей точностью и максимально увеличить сроки межремонтной эксплуатации соответствующего оборудования. Это позволило оптимизировать межремонтные периоды, а в некоторых случаях и удвоить их до 50000 часов. Имеются основания предполагать дальнейшее увеличение межремонтного периода по мере накопления данных о характеристиках механических колебаний данного оборудования.
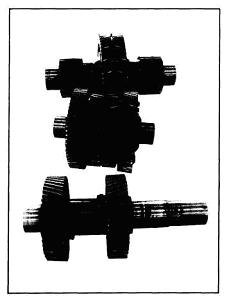
Рисунок 1 – Шестеренчатые валы экструдера
Дефекты игольчатых подшипников
По видимому, механические колебания экструдеров, имеющих небольшие повреждения малых игольчатых подшипников червячных валов (дефекты, в общих случаях трудно диа-гнозируемые), увеличиваются в области самых низких частот (см. рис. 2).
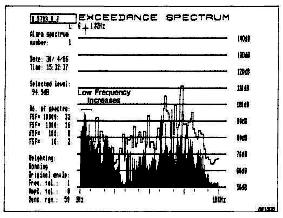
Рисунок 2 – Результаты сравнения спектров механических колебаний экструдера указывают на увеличение уровней составляющих в области низких частот
Частоты этих составляющих меньше соответствующей рабочей скорости вращения валов частоты и в них преобладают субгармоники скорости вращения червяков и приводного вала редуктора, т.е. 1/2, 1/3 и т.д. данных скоростей вращения. Такой эффект часто встречается в случае ослабления крепления целостности машины, предположительно, что повреждение игольчатых подшипников происходит в результате излишнего биения червячного вала.
Дефекты зубов шестерен
Дефекты шестерен, такие как нарушение соосности, рассогласование и местные повреждения зубов, в общих случаях отражаются в спектрах механических колебаний как боковые полосы, присущие частотам зубозацепления. Расстояние между этими боковыми полосами равно соответствующей скорости вала частоте. Рис. 3 показывает расширенный участок спектра механических колебаний редуктора экструдера. Этот участок расположен вокруг частоты зубозацепления 696,25 Гц. Разнос боковых полос в 11,3 Гц четко виден и равен частоте вращения промежуточного вала. При инспекции редукторов во время техобслуживания шестеренчатое колесо на смежной оси имело местные дефекты на части окружности венца.
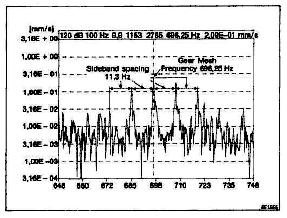
Рисунок 3 – Расширенный участок узкополосного спектра механических колебаний редуктора экструдера четко показывает боковые полосы частот, расположенные вокруг частоты зубозацепления
Мониторизация механических колебаний данного оборудования до сих пор производилась автономно. Однако, ввиду убедительных результатов автономной мониторизации в настоящее время рассматривается возможность расширить систему непрерывной мониторизации в реальном времени и включить в соответствующую программу и непрерывный контроль состояния экструдеров.
Заключение
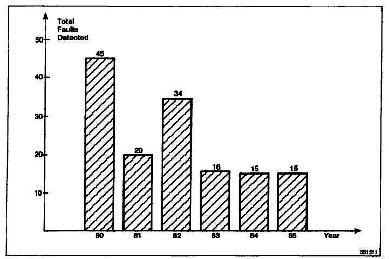
Рисунок 4 – Количество дефектов, определенное с использованием мониторизации механических колебаний с начала эксплуатации предприятия на полную мощность в 1980 году
Описанная выше система зарекомендовала себя способной для выявления и осуществления диагностики быстро и медленно развивающихся неисправностей. Она не только обеспечивает уверенность в эксплуатации благодаря знанию, что внешапное ухудшение состояния машинного оборудования будет обнаружено вовремя для принятия соответствующих мер, но также позволяет точное определение и поставку диагноза со значительным упреждением до аварии. Во многих случаях была заблаговременно выдана индикация ухудшения состояния машинного оборудования. Таким образом, состояние машинного оборудования непрерывно контролировалось в процессе его эксплуатации. Это дало возможность увеличения срока бесперебойной эксплуатации и оптимального выбора даты для технического обслуживания.
Некоторые из главных преимуществ системы описываются ниже:
Постоянная мониторизация
Постоянная мониторизация обеспечивает уверенность эксплуатации благодаря знанию, что состояние машинного оборудования непрерывно контролируется.
Мониторизация в широких полосах частот
Постоянная мониторизация в широких полосах частот выдает предупреждение в случае внезапного ухуд-щения состояния машинного оборудования, позволяя избежать серьезную аварию.
Сравнение спектров
Сравнение спектров механических колебаний способствует раннему обнаружению изменений состояния оборудования и выявлению причин диагностируемых неисправностей. Последующий анализ тенденций позволяет наблюдение за такими изменениями и эксплуатацию машинного оборудования максимально длительное время.
Системы на базе ЭВМ
Системы на базе ЭВМ предлагают преимущества автоматического управления процессом мониторизации и обеспечивают возможность эффективной обработки информации и хранения большого объема данных.
Рис. 4 показывает количество дефектов, обнаруженных за время использования программы мониторизации механических колебаний. Интересно отметить, что график следует началу «лавинной» кривой аварий - количество дефектов было большим вначале, когда машинный парк был новым и требовал приработки, а затем снизилось до устойчивой величины.
Конечно же невозможно утверждать, что каждый дефект, обнаруженный системой мониторизации, привел бы к неожиданной аварии. Однако, стоимость аварии даже одной мешалки была бы достаточной для оплаты комплектной системы мониторизаци. В исходном предложении на поставку системы мониторизации стоимость окупаемости по смете отдела техобслуживания фирмы Статойл составляла 18 месяцев. Реальный срок окупаемости, даже по самым консервативным подсчетам, был значительно короче.