|
по теме выпускной работы «Обоснование
и разработка структурной схемы прибора контроля и управления процессом
сжигания газового топлива»
Введение
Обзор
исследований по теме
Решение поставленной задачи
Выводы
Введение. В экономике Украины энергосбережение и
энергосберегающие технологии являются приоритетными при внедрении их в
производство. В связи с этим важное место занимает всестороннее
комплексное обследование теплоэнергетических систем и ресурсов. Тепловая
энергия – необходимое условие жизнедеятельности человека,
совершенствования общества, в котором он живет, и создания благоприятных
факторов его быта. Оптимизация систем производства и распределения
тепловой энергии, корректировка энергетических и водных балансов,
энергосбережение и энергоаудит позволяют улучшить перспективы развития
теплоэнергетики, повысить технико-экономические показатели
теплоэнергетического оборудования.
Эффективность, безопасность, надежность и экономичность работы
теплоэнергетического оборудования котельных во многом определяются
методом сжигания топлива, совершенством и правильностью выбора
оборудования и приборов. Повышение надежности и экономичности систем
теплоснабжения зависит от работы котельных агрегатов, рационально
спроектированной тепловой схемы котельной, широкого внедрения
энергосберегающих технологий, экономии топлива, тепловой и электрической
энергии.
В настоящее время проблема газовой экономии заставляет пересматривать процесс
сжигания топлива, улучшать технологии для увеличения КПД котельной
установки при уменьшении затрат на топливные ресурсы. Современные
научные и производственные технологии предполагают использование
высокотемпературных реакций для обеспечения источником энергии и
отопительной системой [4]. Эффективность использования применяемых для
этих целей источников энергии (в частности использование газовой смеси в
горелках) должна обеспечивать максимальные температуры и полноту
сгорания топлива.
Обзор исследований по теме. Этой проблеме посвящено несколько работ,
связанных с теплотехническими процессами. Например, в работе [3] учтены
зависимость нагрева воды от количества подаваемого топлива. Проведены
исследования оптимальных параметров факела для нагрева воды. Основываясь
на полученной математической модели теплообмена нагретого воздуха внутри
топочной камеры с конвекционными поверхностями нагрева [2] получены
теоретические данные температуры факела в различных точках среды. В этих
работах показано, что достижение максимальной температуры для
данной горелки возможно при оптимальном соотношении для нее подачи
окислителя и горючего. Смешивание компонентов происходит в рабочем теле
горелки, чтобы в сопло поступала приготовленная смесь исходных
компонентов. Получаемое пламя на протяжении значительного удаления от
сопла стабильно и осесимметрично. Это разрешает нам применять
термоэлектрические методы определения температур. Однако эти
исследования не касаются измерительной части и не делают акцента на
выборе первичных преобразователей, которые можно использовать в
агрессивной высокотемпературной среде с наименьшими погрешностями.
Постановка задачи. Построить
математическую модель нагрева воды от подаваемого на вход системы
топлива, обеспечивая тем самым экономичность процесса за счет увеличения
КПД работы котельной установки. Для этого необходимо провести
исследования оптимальных параметров факела в различных точках среды
внутри топочной камеры с конвекционными поверхностями нагрева. Учесть,
что факел равномерно распределяется по топочной камере, так как тип
горелки диффузионный, то есть топливо смешивается до поступления в
горелку.
Научная значимость выполняемых в данной работе исследований заключается в том, что для оптимальной организации
процесса горения и, следовательно, эффективного использования газа
необходимо исследование структуры факела пламени
используемой горелки. [2]
Решение поставленной задачи.
Топочная камера представляет собой замкнутое пространство, с одним
входом и выходом, в которое через горелку подается тепло, а дымосос
убирает продукты сгорания топлива.
Рисунок 1 - Структурная схема парового котла
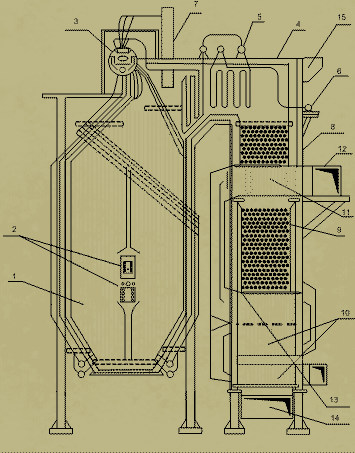
Схема парового котла имеет вид, представленный на
рисунке 1, на котором обозначено:
1 - топочная камера;
2 - горелочное устройство;
4 - пароперегреватель;
5 - пароохладитель;
6 – выходная камера пароперегревателя;
7 - циклон выносной
8,9 – водяные экономайзеры;
10,11–воздухоподо-греватели;
12 – выход горячего воздуха на горелки
13 – вход воздуха после дутьевого вентилятора
14 – выход продуктов сгорания на дымосос.
Температура горения может колебаться в диапазоне от 100
в нижней правой области факела до 700 в верхней центральной области факела. Управление системой можно
осуществлять двумя способами: за счет контроля расхода
топлива или контроля температуры. Существующая система контролирует
расхода топлива, контроль температуры является второстепенным
параметром. Разрабатываемый прибор контроллирует температуру тем самым
обеспечивая экономичность процесса.
В настоящее время система контроля
и управления процессом сжигания газового топлива имеет вид, структурно
представленный на рисунке 2. Было доказано, что оптимизация организации
процесса горения и, следовательно, эффективноcть
использования газа возможна за счет разработки дополнительных элементов
контроля (прибора), при помощи которых, управляя количеством подаваемого
топлива на горелку можно управлять структурой факела, следовательно,
изменять нагрев конвекционных поверхностей.
Проанализируем состав сухой массы газообразного топлива:
CH4+C2H6+C3H8+C4H10+C5H12+N2
=100%,
если рассмотреть поэлементно, то процентное содержание веществ
составляет CH4=94,1%, C2H6=3,1%, C3H8=0,6%, C4H10=0,2%,
C5H12=0,8%, N2=1,2%
для плотности газа при 0ordm;С и 760 мм.рт.ст ρ=0,786кг/м3.
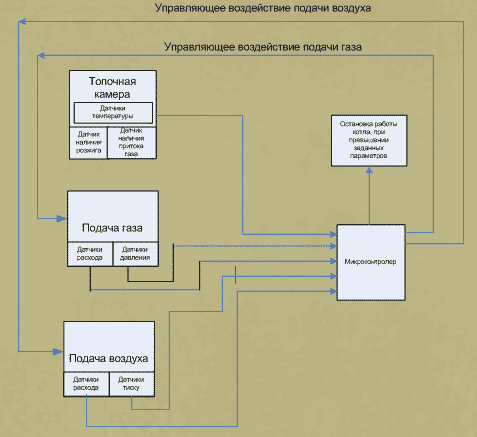
(4)
Рисунок 2 - Структурная система контроля и
управления процессом сжигания газового топлива
Низшая теплота сгорания сухого газообразного топлива [4]
QHP=358·CH4+637·C2H6+912·C3H8+1186·C4H10+1460·C5H12,
QHP=358·94,1+637·3,1+912·0,6+1186·0,2+1460·0,8=37614,9
кДж/ч,
Расход топлива, м3/с, подаваемого в камеру
сгорания, определяется по формуле
(1)
D(iПП-iПВ)+DПР(i'-iПВ)
В=
∙100,
QHP∙ηПГ
____________________
D=2,78
кг/с–паропроизводительность парогенератора ДЕ-10-14ГМ
iпп=2928,4
кДж/кг–энтальпия перегретого пара, определяется по [4],
табл.П.10.
i’=855 кДж/кг–энтальпия воды при температуре кипения,
по [4] ,табл.П.9.
iпв=4,19·tпв=4,19·100=419
кДж/кг–энтальпия питательной воды
tпв=100ºС–температура питательной воды
DПР=
=
=0.0278 кг/с - расход продувочной воды
100
100
_____ ______
Разрабатываемая
математическая модель должна учитывать зависимость выходных
параметров от входных. Существующая измерительная система,
настроенная на контроль топлива, не учитывает распределение
температуры по среде топочной камеры. Предлагается учесть в
модель этот факт, и тем самым обеспечить такой же нагрев
поверхностей, но при сжигании меньшего количества топлива, т.е.
целевой функцией разрабатываемого прибора можно определить как
Эф=g(TФАКЕЛА,НФАКЕЛА)àmax.
(2)
НФАКЕЛА - висота факела TФАКЕЛА-
температура факела в определенной точке факела
Зная количество выделяемой теплоты и
дифференциальное уравнение теплообмена для бесконечного стержня круглого
сечения можно построить зависимость нагрева воды от подаваемого топлива
ТФАКЕЛА=f(RГАЗА,RВОЗДУХА),
НФАКЕЛА=f(RГАЗА,RВОЗДУХА),
где RГАЗА,RВОЗДУХА-расход газа, воздуха
соответсвтенно
Если учесть что расход топлива B (м3/с), есть не что иное как
функция от расхода газа и воздуха, то математическая модель примет вид
ТФАКЕЛА, НФАКЕЛА=f(B),
ТВ.ВЫХ=φ(НФАКЕЛА,ТВ.ВХ),
(3)
где ТВ.ВХ,ТВ.ВЫХ - температура воды
на выходе и на входе соответственно.
Важно разработать
прибор контроля факела при различных подачах топлива, составить
характеристическую таблицу максимальной температуры факела от
подаваемого топлива, в идеальном случае – все сжигаемое топливо
сгорает и тепло идет на нагрев поверхности. Исходя из полученных
условий нужно выдавать регулирующие воздействие на подачу
топлива, если это не поможет учитывать потери при недожоге.
В связи с этим, важно
представить механизм горения. Метод, с помощью которого это возможно -
распределение температуры в факеле и ее измерение [4]. Обычно измеряемые
температуры лежат в достаточно широком интервале от -273 ºС до 3000 ºС и
более.
Для реализации прибора
необходимо определить количество точек контроля пламени в разных
температурных сечениях. Измерение температуры может осуществляться за
счет контактного или бесконтактного измерения. Контактные методы
измерения температуры предполагают непосредственный контакт с измеряемым
объектом. Однако использование контактного термометра может приводить к
нарушению структуры пламени. Возникающие в результате этого погрешности
измерения и запаздывания показаний зависят от физических свойств и
скорости течения измеряемой среды около термометра, а также от
конструкции термометра. Такие погрешности могут быть больше методических
погрешностей. При выборе контактного термометра следует, кроме того,
учитывать, что термометр должен выдерживать механические, химические и
термические нагрузки, которым он подвержен на данном объекте
исследования.
В случае больших
температур и быстропротекающих процессов, используются оптические методы
измерения температуры, обладающие высоким пространственным и временным
разрешением.
Рассчитать действительную температуру пламени по результатам измерений
можно одним термометром по формуле (4). Получили также развитые способы
измерения температуры, основанные на зависимости между показаниями
термометра и диаметра термоэлектродной проволоки: в определенное место
пламени один за другим вводят два (или более) термометра с разной
толщиной термоэлектродов и исходя из результатов измерений рассчитывают
действительную температуру факел
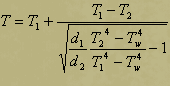
где d — диаметр термоэлектродной проволоки; индекс «1» относится
к тонкому термоэлектроду, индекс «2» — к толстому, индекс w — к
стенке. Этот, а
также и большинство других методов с использованием двух
термометров не учитывают обмена излучением между термометром и
пламенем. Пренебрежение этим обменом в случае несветящегося
пламени не приводит к большой погрешности измерения. В случае
светящегося оптически толстого пламени обменом излучением между
термоэлектродной проволокой и стенкой можно пренебречь по
сравнению с обменом между термоэлектродной проволокой и
пламенем. Вследствие сильной абсорбции пламени термометр «не
видит» стенку. В этом случае применение уравнения (4) не
приводит к полезным результатам. Естественно, что влияние
излучения стенки или пламени зависит также и от места измерения.
При практическом
применении метода двух термометров часто возникают погрешности измерения
того же порядка, что и рассчитанные. Поэтому предложено измерять
температуру лишь одним возможно более тонким термоэлектрическим
термометром. Последовательность расчетов следующая.
Фk=α∙FTh∙(T-T1)≈σ∙ε∙FTh∙(T14-Tw4)=ФStr,
(5)
ε - излучательная способность;
FTh - поверхность термометра.
После несложных преобразований получим
T≈T1+KSo∙(T14-Tw4).
(6)
Коэффициент
KSo рассчитывается при
температуре Тw=300 К. Действительная температура приблизительно
дается уравнением (6), в которое вводятся измеренные значения Т1 и
Тw и значения
KSo, определенные для данной температуры Т1 и
диаметра проволоки d. Вследствие своей массы термоэлектрические
термометры при высокочастотных турбулентных колебаниях температуры
пламени не могут точно за ними следовать и дают средние значения
температуры, полученные интегрированием первой степени температуры
во времени. При измерении температуры контактными
термопреобразователями могут возникнуть значительные погрешности,
обусловленные отводом теплоты от чувствительного элемента за счет
теплоотдачи по чехлу и теплоотвода излучением.
Погрешность Δt измерения температуры газа, вызванная лучистым
теплообменом между чехлом термопреобразователя и стенкой трубы,
определяется из выражения:
(7)
Δt=TT-TC=-
[( ) - (
)]
____ ____ ____
αК 100
100
C0εПР ТТ4
ТТ4
где ТС, ТТ, ТСТ – соответственно температура
измеряемой среды, термопреобразователя и стенки, К; αК -
коэффициент теплоотдачи конвекцией между термопреобразователем и
измеряемой средой,
Вт/(м2∙К); С0=5,67eВт/(м2∙К)-
коэффициент излучения абсолютно черного тела;εПР
- приведенный коэффициент теплового излучения, характеризующий
теплообмен между термопреобразователем и стенкой.
Когда поверхность
стенки значительно больше поверхности термопреобразователя (FСТ>>FТ),
можно считать, что приведенный коэффициент теплового излучения
практически равен коэффициенту теплового излучения
термопреобразователя (εПР=εТ).
Погрешность Δt измерения температуры за счет теплоотвода по
чехлу определяется по формуле
(8)
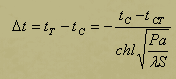
где
α - коэффициент теплоотдачи между термопреобразователем и измеряемой
средой,
Вт/(м2∙К); Р и S – периметр, м, и площадь, м 2,
поперечного сечения чехла термопреобразователя;
λ- коэффициент теплопроводности материала термопреобразователя,
Вт/(м∙К);
l - глубина погружения чехла в измеряемую среду, м.
Проведенный анализ показывает, что для выбора контрольных точек
необходимо исследовать структуру факела для дальнейшего контроля
температуры пламени в нем. Геометрически факел представляет собой
сужающуюся вверх осесимметричную структуру (см.рис.3). Сечения
выбирались следующим образом: 1-е сечение – у сопла горелки, 2-е сечение
– на расстоянии 1/3 от общей длины малого конуса, 3-е сечение - на
расстоянии 2/3 от общей длины малого конуса, 4-е сечение – у вершины
малого конуса.нутри большого конуса светло-синего цвета наблюдается
малый конус насыщенного голубого цвета. У вершины малого (внутреннего)
конуса располагается зона желтого свечения.
Факел стабилен приблизительно до зоны желтого свечения,
располагающейся на расстоянии ¾ длины факела начиная от
торца сопла. Данная нестабильность обусловила невозможность
получения точных значений температур верхней четверти
факела.
По оси факела температура возрастает по мере удаления от
торца сопла и достигает максимума у нижнего края зоны желтого
свечения. Далее измерения регистрируют падение температуры
пламени.
Таким образом механизм горения у торца сопла носит диффузионный
характер. По мере продвижения по факелу, перемешивание
окислителя и горючего улучшается и определенную роль начинает
играть кинетическая составляющая, что и обуславливает повышение
температуры у края зоны желтого свечения. Что касается
постоянства температуры внешнего края большого конуса, то она
определяется диффузией окислителя из внешнего воздуха в зону
реакции [5].
Рисунок 3 - Сечения факела
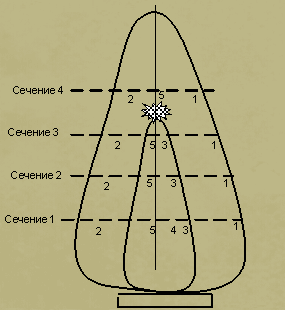
Таким образом полученная структура факела обусловлена режимом
диффузионного горения горючего (пропан-бутановая смесь применяемая в
бытовой технике и окислителя воздуха) с постепенным увеличением
кинетической составляющей (и температуры), которая достигает
максимального значения у нижнего края зоны желтого свечения. При
проведение этой работы были обнаружено параллельные исследование
в теплотехническом направлении [2], в которой были получены
экспериментальные данные для топочного газового устройства,
представленные в таблице 1.
Из результатов эксперимента, полученных работе [2], видно, что измерение
температуры необходимо проводить в разных точках сечения, для
определения распространения пламени в среде топочной камеры. Измерение в
центре факела теоретическое подтверждается экспериментальными данными,
температура по высоте должна быть максимальной в каждом сечение. Данные
в крайних точках видимой области факела ближе находятся к конвекционным
поверхностям поэтому имеют важное значение.Подача воздуха регулируется
увеличением зазора диффузора горелки, обеспечивая подсос воздуха в
рабочий объем горелки. Возможность регулирования таким образом
достаточно ограничено и осуществляется в основном изменением подачи
горючего (газ) в рабочий объем.
Таблица 1 – экспериментальные данные полученные в сечениях факела
Сечение 1 |
r, мм |
Т, ºС |
Сечение 2 |
r, мм |
Т, ºС |
5 |
0 |
170 |
5 |
0 |
560 |
4 |
2.75 |
440 |
3 |
4,63 |
640 |
3 |
6.13 |
530 |
2 |
5,69 |
600 |
2 |
6,81 |
485 |
1 |
6,81 |
420 |
1 |
7,5 |
420 |
|
|
|
Сечение 3 |
|
|
Сечение 4 |
|
|
5 |
0 |
650 |
5 |
0 |
700 |
3 |
2,38 |
640 |
2 |
2,31 |
600 |
2 |
4,02 |
630 |
1 |
4,36 |
420 |
1 |
5,59 |
420 |
|
|
|
В качестве термоэлектрического датчика можно
использовать хромель-алюмеливую дифференциальную термопару. Рабочий
спай термопары, помещаемый в пламя крепится на электроизолирующей
тефлоновой подставке, закрепленной на препаратоводителе, конструкция
которого позволяет перемещение в горизонтальном и вертикальном
направлениях, что дает возможность измерить температуру в любой точке
факела [2].
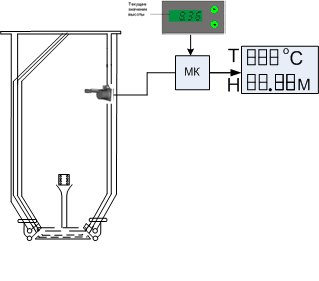
Рисунок 4 - Принцип работы системы
контроля
На данное время работа находится в стадии завершения, ожидаемые
результаты:
1. Построена обобщенная математическая модель нагрева воды от
подаваемого на вход системы топлива отличающейся от существующей тем что
обеспечивает управление не по расходу а по температуре внутри топки. Это
позволяет обеспечить увеличение экономичности процесса (1) за счет
уменьшения затрат топлива (3).
2. Определено, что гипотетические данные подобны экспериментальным, т.е.
имеют такую же тенденцию распространения температур в факеле и
аргументируют возможность модификации существующей системы контроля и
управления
3. Проведены исследования оптимальных параметров факела в различных точках
внутри топочной камеры – в центральных и крайних точках факела. Определено
что элементами модификации существующей системы контроля и управления будет
установка термопреобразователей в центральных и крайних точках пламени, причем
необходим переход от контактных датчиков температуры к безконтактным, которые
обеспечат возможность исследования высокодинамического распространения
температуры пламени в среде.
Литература
1. Киселев Н. А. – Котельные установки. Учеб. пособие для техн.
училищ. М., «Высш. школа», 1975, 277 с.
2. Трофименко М.Ю. Особенности структуры факела
пламени твердых смесевых систем на основе перхлората аммония.
Диссертация на соискание степени канд. физ.-мат. наук, Одесса, 1999.
3. Тепловой расчет котельных агрегатов (нормативный метод). Кузнецов
Н.В., Митор В.В., Дубовский И.В., Карасина Э.С. -М.: Энергия, 1973
4. Тепловой расчет котельных агрегатов [ Учебное пособие] А. С.
Попов, И. Л. Дунин; Рост. инж.-строит. ин-т 119 с., [2] л. табл. ил. 20
с.
5. Гейдон А.Г., Вольфгард Х.Г. Пламя, его структура, излучение и
температура. Пер. с англ. –М: Металлург, 1959. -333 с.
6. Евдокимов Н. И. Методы и средства исследований. Ч. 1 Температура.
Российский гос. университет нефти и газа им. И. М. Губкина.
7. Двойнишников В. А.,,Деев Л. В. Конструкция и расчет котельных
установок: Уч. для техникумов по специальности
«Котлостроение». М.:
Машиностроение, 1988. - 264 с. ил.
8. В. С. Мухин, И. А. Саков Приборы контроля и средства автоматики
тепловых процессов. М: Высшая школа 1988 - 256 с.
9. Качан А. Д. - Режимы работы и эксплуатации ТЭЦ, Минск: Вышэйшая
школа
10. М. М. Щеголев Топливо, топки и котельные установки М.: Литературы
по строительству и архитектуре. 1953
К содержанию
Оптимальный просмотр сайта -
avant browser
В=
∙100=0.2 м3/с
37614,9∙91,95
2,78∙(2928,4-419)+0,0278∙(855-419)
________________________________
|
|