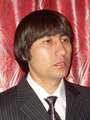 |
Saparov Fakxriddin Abdimitalibovich
|
Theme of master's degree work: “Improvement of quality of cylindrical gear wheels by applying the technological method of treating the sprockets”
Supervisor: Professor.
Polchenko Victor Vasilyevich
Summary of master's degree work
Chapter
Actuality of the work
      During the recently carried out a large number of study biases of various technological processes treatment because of the need to improve the accuracy of gear wheels. These studies summaries the wealth of industrial experience in manufacturing gears, and by the development of the theory in this field, contribute to the improvement of practice. Using the results of these studies should help to improve the accuracy of gears.
      Any manufacturing process of forming gears is periodic. It has a large number of sources of harmonic elementary mistakes, which, in his summation on the product creates periodic errors. Kinematic gear chain machine consists of a rotating gear wheels, shafts, propellers, worm tooth. Errors which are the source of a number of sinusoidal oscillations. The same phenomenon has occurred and to set the eccentricity of the work piece and the tool gear machine, tool manufacture their own biases. In addition, the error of form, arising out of products on previous technological operations, is the volatility of the efforts of cutting, and hence the deformation.
Finishing thermally enmesh teeth
Treated gear tooth
      active surfaces of teeth of cylindrical gears performed by removing thin shavings (0,001-0,005 mm thick) with a tooth wheel gearing with their teeth with the tool (Shivered) with grooves on the height of the tooth profile. During the rotation Treated gear tooth reported heavier elements Shivered pair of wheels at without clearance engaged their teeth or with one-engaged, performed with breaking slave element. In the latter case, you can rent the metal of different thickness at various tooth sites (selective Treated gear tooth).
Figure 1. shevingovaniya gear wheel and worm shaft
      The processing is done Shivered disk. In Grinding tooth tool and the wheel turns with angular velocity, respectively, ? 1 and ? 2 play with helical gearing to transfer the theoretical point contact, due to the presence layer of metal removed cuts grooves on the surfaces of teeth on each Shivered working during the (movement filing Ds) the actual contact area is kind of a narrow oval, major axis which is located approximately along the tooth.
Figure 2. Scheme Grinding tooth:
      Grinding tooth improves accuracy of gear wheels for smooth norms of their work and contact teeth. Declining as the radial pulse tooth crown on the real axis rotation with Treated gear tooth, but the kinematic error on this axis are not significantly altered.
Figure 3. Scheme Grinding tooth:
      Grinding tooth can be used to modify the teeth of the wheel as for the tooth (changed pitch) and profile of teeth (profile modification). The accuracy obtained with Grinding tooth of cylindrical gears Shivered disk, to a large extent depends on the errors of previous honing teeth and set the wheels in Grinding tooth machine. With accurate pre-treatment and the correct choice of instrument Grinding tooth provides high accuracy gears up to manufacture precision wheels.
Grinding tooth
      In contrast Treated gear tooth Grinding tooth and grinding of teeth is carried out on methods for copying or coercion oblate, therefore, pre-cut errors and distortions, educated thermal treatment, after Grinding tooth completely eliminated. This ability Grinding tooth is the only vehicle for obtaining high-precision gears with tempered to great hardness of teeth. In the manufacture of precision gears, subjected to chemical and thermal processing, Grinding tooth widely used for finishing and hardened case-hardened teeth with surface hardness of HRC 58-63. In the manufacture of gears with teeth nitride with hardness HR 15-N 91-92 (HRC 63-70), Grinding tooth used to eliminate the brittle upper layer of teeth and profile distortions arising from the increase in the surface layers of teeth. A major obstacle to the use of gear wheels with polish teeth in mass production are the big labor and the high cost of processing. Therefore, when choosing the best method of finishing teeth should take into account not only technical but also economic indicators.In grinding of teeth by copying Grinding wheel remains stationary,
Figure 4. Grinding tooth method copy: a-side surfaces of a tooth; b. lateral surfaces of the tooth surface and depressions;
      - receives a range of back and forth motion on the length of Grinding teeth and periodic filing to the depth of grinding for each double turn.When grinding the side surfaces of the tooth periphery of the circle can be sanded or not sanded the bottom of depressions toothed wheel. During the range is exposed to edit profile, it is made of diamonds, channeled through the copier diagram shows the pantograph mechanism, enabling users to edit the terms of grinding with high accuracy.
Figure. 5. Scheme of the filling mechanism.
      This mechanism consists of two interconnected by a pantograph, acting on a common hydraulic cylinder. Lower pantograph levers associated with copiers 2, at the ends of the upper levers secured holders diamond 1. When a lower growl with their pins 3 to slide copier 2, the tip of each diamond describes a curve similar to curve copier, but the reduced proportionately arm pantograph.
Figure. 6. Scheme Grinding tooth disk range.
      Grinding tooth in most cases is the final transaction processing gears. A serious defect Grinding tooth responsible gears are the Grinding tooth occur and Trenched. To prevent the marriage of expensive parts do not need all the previous grinding of teeth of the technological operation of mechanical and thermal processing to comply with the required precision. The tendency to occur metal and the crack formation in a large extent depends on the structure, formed during thermal processing.
Honing teeth
      The process of abrasive honing hardened gears is designed to improve the micro geometry of the lateral surfaces of teeth, removal of the working surfaces gabion, hangnail, and traces of scale, and corrected small errors of the parameters gear shrouds caused by thermal treatment. In honing teeth limpest lateral surfaces of teeth increases to a three-class, improving contact-noise characteristics of gears, reduced surface roughness of teeth Grinding tooth and polished gears, increasing the contact strength of teeth, tooth treatment increase productivity by improving the pre-treatment with subsequent honing teeth.
      Are two ways honing teeth unilateral and bilateral.When honing teeth first method of processing is done with the District (tangential) loading, the stress of one-Hon and wheels, with side clearance (usually 0.1-0.2 mm) between the parties discontinuous teeth. Processing each of the parties shall alternately teeth (with the reverse rotation of the wheels Hon) at a constant span.
New and special methods for finishing gears.
      Creation of finishing treatment of teeth to improve the quality of gears and transmissions, as well as processing performance. Of the new methods tooth treatment spread Grinding teeth line and worm community of elbow, covering honing teeth hone, as well as turning tooth hardened gears hard tool. The table shows the main technical characteristic machine on which the processing is performed by these methods.
Table. 1. Technical specifications of machine tools for new methods of gears.
      Sanding elbow range does not require interruption of treatment for the correction terms, guarantees the consistently high accuracy of the tooth profile of gear wheels and the structure of its surface. Using the small-diameter circles (up to 25 mm) makes it possible to polish the wheels with internal teeth and a configuration that used to grind, it was impossible.
Figure.7. Scheme gear grinding wheel profile elbow range
      Fastening the steel shell in terms of spindle machine with a minimum clearance for the hole and against the butt end of the spindle ensures high accuracy of the provisions of the working surface of the circle about its axis of rotation.
Figure.8. Scheme honing hone toothed wheel with internal teeth
      Machine D-250 can process one local and many local Gear in diameter and 250 mm and a width of tooth crown and 500 mm.
      Work VNII diamond and gas showed that the gear honey constructed by applying the diamond powder DIA 80/63 at precise metal base, providing up to 10 wheels with m \u003d 3,5 z \u003d 25, with thickness cut layer 0,02-0,03 mm on the thickness of the tooth and removing gabion depth of 0.1 mm.
Conclusion
      In the process performance was analyzed using the technological feasibility of finishing processing of teeth, particularly the development of recommendations for the application to achieve the highest quality teeth of wheels, depending on the degree of accuracy and working conditions.
Literature
      1. Тайца Б.А, КоганГ.И. «Производство зубчатых колес» справочник М.Машиностроение 1990 – 464 стр.
      2. Гинзбург Е.Г. «Производство зубчатых колес» Ленинград .Машиностроения выпуск-3, 1978 – 133стр.
      3.Тайца Б.А. «Точность и контроль зубчатых колес» Москва. Машиностроения 1972 – 361 стр.
      4. Калашников С.Н. «Шевингование зубчатых колес» Москва.Высшие школа, 1985- 224 стр.
      5. Калашников С.Н. «Изготовления зубчатых колес» Москва 1980-450 стр
      6. Бабичева А.П. «Физико-технологические основы методов обработки». Учебные пособия. ДГТУ 2003 – 424стр.
      7. Схирдладзе А.Г. «Технологические регламенте процессов механической обработки»; ООО «ТНТ», 2005 430 стр.
      8. Гусев А.А. «Технология машиностроения». ; М. Машиностроения 1986 – 480 стр
      9. Косиловой А.Г. «Справочник технология машиностроения» 2-томах., М. Машиностроения 1985 – 495 стр.
      10. Панова А.А. «Обработка металлов резанием» .; М. Машиностроения 1988 – 735 стр.