Abstract of master's diploma
Content
Introduction
Purposes and tasks
Relevance of the topic
Scientific novelty
Practical significance of the paper results
Review of research on the topic
Key results
Conclusion
Литература
Introduction
Under the conditions of transition to market economy, production prime cost is the most important
indicator of production and commercial operations of an organization. High energy consumption per unit of production is complicated by
significant dynamics of production and, consequently, the instability of positions portfolio.
This leads to the fact that calculations of the cost mechanism for planning and production program that does not match actual results are
traditionally carried out. This factor is dominant in the formation of business profits, from whence, instead of some planned profit by the end
of the plan period, the company comes to losses. These features complicate the task of forming raw material base with the corresponding
variations in pricing for the purchase of raw materials, because contractors — suppliers of raw materials have no guarantees on the
amount of purchased raw materials. All this is complicated by the fact that in these conditions, the period of planning the production does
not exceed one month, i.e. availability of contracts with suppliers and customers concluded for an annual period or more is monthly accompanied
by production. This leads to an unstable financial state of enterprises, lack of strategic policies of enterprises to introduce new technology
and modernize the equipment, which determines the mechanism of reduction of energy and labor costs for production.
The calculation of this index is necessary:
- to assess the implementation plan for this indicator and its dynamics;
- to determine the profitability of production and certain types of products;
- the implementation of intercompany cost accounting;
- identification of reserves to reduce cost and pricing of the product;
- inform decisions about the production of new types of products and phasing out old ones.
Development of market relations increases the responsibility and autonomy of enterprises in
the development and managerial decision-making to ensure their effectiveness. The results of industrial, commercial, financial and other
economic activities depend on a variety of factors that are in varying degrees of communication between themselves and summary indicators.
Their actions and interactions vary in their strength, nature and time. Reasons or conditions that produce these factors are also different.
Without disclosing and evaluating direction, activity and time of their actions, it is impossible to provide effective management. Performing this
difficult task qualitatively is possible only through a comprehensive analysis of economic activity that meets modern requirements of a
market economy. With its help, strategies and tactics of the company are formulated, production efficiency increase reserves are determined,
business results are evaluated.
Production costs forming is the key and the most difficult element of the formation and development
of industrial and economic mechanism of an enterprise. Cost of production and costing of products (works, services) occupies a dominant
place in the general accounting system. Under the conditions of independent planning of the range of products and free (market) prices by
enterprises themselves, uses of current system of taxation increase the importance of methodologically grounded cost accounting and
calculation of the cost per unit of the product produced by the company. [3] Underestimation of these parameters leads to decrease in growth
of production efficiency and, above all, affects the amount of profit and profitability.
Purposes and tasks
Under the modern conditions of initial phase of capitalism, domestic production faces the problem of low competitiveness of the products
produced by certain enterprise due to the high indicators of cost mechanism and, consequently, low wages and loss of a material interest
in the outcome of labor. Reduction of production costs allows the company to exploit the economic advantage to change the infrastructure of companies,
the range of manufactured goods, new technology acquisition and upgrading of basic equipment.
It also gives an opportunity to increase the payroll to improve the skills of production staff and its interest in the outcome of labor.
In accordance with this, the purpose of planning the prime cost of production is the possibility of its reduction, and on that basis, achieving
the lowest possible level of production costs and increasing savings. In line with this purpose, the following statement of purposes of this work
is formulated: to develop a dynamic deterministic economics mathematical model that allows us to determine the options of the cost mechanism
at any desired period.
The purpose of this study is to define the structure and view of the model of dynamic forecast
of the prime cost of the enterprise. To develop a model, it is required to:
- carry out the classification of variables;
- create the logical and formal model of the prime cost calculation indicators relationship.
Logical and formal model is intended to determine the structure of sections and subsections
of the data containing the economic and industrial performance enterprise planned and actual character. To determine the mechanism of
cost of production of the chain:
raw materials — technology — costs — finished products
In addition, the logical and formal model allows determining relationship between input and output variables in the preparation of decisions of DSS, implementation of tasks of planning, accounting and control, operational control.
Relevance of the topic
Under the current circumstances, activity of an enterprise is characterized by the lack of payments
and mandatory state orders, reduction of the number of customers and the contracts at the same time. Consequently, the planned cost accounting
made by economists is significantly different from the actual one. This leads to the loss-making business activities. Situations occurring randomly
throughout the plan period lead to disruption of the planned target. This entails making decisions to adjust target indicaors. Therefore, in order
to improve the efficiency of enterprise, it is required to do a dynamic forecast of the production prime costs.
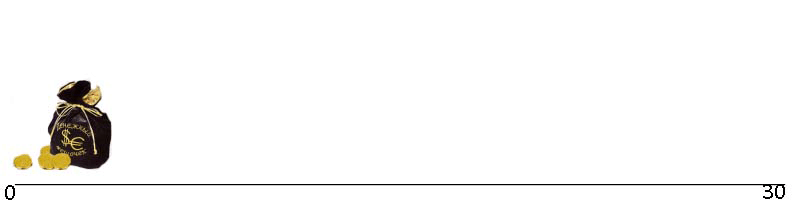
Рис. 1 - The difference between the targets of the actual cost of production (gif-animation, 12 frames,
6 cycles, size 92 Кб, software MP GIF Animator)
Scientific novelty
Under the modern conditions, issues of forecasting and cost control are crucial in solving a variety
of production problems in the industrial enterprise. Transients in the countries economics that have emerged in the former Soviet Union,
accompanied by a significant drop in production volumes, energy resources price hike and price instability in domestic markets, resulted in the
fact that the existing static model does not provide sufficiently accurate and reliable prediction of the prime cost. [11] At the same time, the development
of dynamic forecast models of the prime cost requires highly skilled specialists in the field of modeling and time-consuming.
Dynamical model prediction of the prime cost in an enterprise will be developed for the first time.
Practical significance of the paper results
This paper is a brief description of the methods for solving the problem of dynamic forecasting of production prime costs for industrial enterprises and the possibility of its application. Using this model, the operational management provides an opportunity to make management decisions in rhythm with the process.
Review of research on the topic in Ukraine
The problem of forecasting engaged and involved several domestic and foreign scholars. Bilousova I. deals
with methods of accounting of production prime costs and production prime cost calculation.
Together with M. Chumachenko, they consider the problems of accounting of production prime costs. [1, 2]
Moreover, methods of production prime cost accounting and product costing are addressed by Marenich T. [7] Chuhlib A.A. published several
well-known articles on financial accounting. [11]
Review of research on the topic in the world
We can distinguish such foreign scholars as Mubarakzyanova G.M., who has developed a
mathematical model of the production prime cost. [8] Arzhanova T.D. is also involved in forecasting prime cost in energetics through adaptive
exponential smoothing. Zhivoga Ya.V. and Charuyskaya L.A. published an article on forecasting the level of the prime cost of gas. [4] Urusova E.A. is
developing economic and mathematical models in forecasting prime cost in the construction of ships. [10] Problems of forecasting of production prime
costs of new technology in a small sample are addressed by Kudyankin N.N. [6] In the 80's, Sakantsev M.G. and Sakantsev G.G. published their
work on the forecasting the prime cost indicators on the basis of multifactorial statistical models. [9] Firman B.I. created the mathematical model of the cost forming in complex processing of raw materials.
[12] There is a huge number of scientists who deal with the problems of forecasting and planning costs of production, their work still being published, new models appear.
Key results
The method of dynamic forecasting of prime cost includes:
- mathematical models of the enterprise and the prime cost forecast;
- method of identification of these models for a particular company;
- algorithm for dynamic prime cost forecast.
The basis of the method of prime costs dynamic forecast is a multiple logical-conceptual model of the enterprise and dynamic model for the costing and prime cost calculation.
Multiple logical-conceptual model is a description of the qualitative level of the formation and calculation of production prime costs for industrial companies as a multilevel production system using the apparatus of set theory. It includes the formalization of the structure of the enterprise as a set of industrial units with the task characteristics of material transformation and calculation of the cost for each of the units.
On the basis of multiple logical-conceptual model, prime costs forecasting dynamic model has been developed, which allows to forecast in a given time period the number of manufactured products and the prime cost of facilities for the calculation of any production unit of the set A. This model includes submodels of the prime costs forecast for final and intermediate divisions. Each submodel is a parametric nonlinear system of ordinary differential equations with given initial conditions.
Conclusion
Application of these models allows us to provide enterprise management for guidelines with the purpose of management of its activities at different levels of hierarchy, which make it possible to organize the production process with minimum costs, increase management flexibility, which leads to saving material and money and increases profit.
Literature
- Білоусова І. Методи обліку виробничих витрат і калькулювання собівартості продукції. //
Бухгалтерський облік і аудит. — 2006, №9. — с.3-5.
- Білоусова І., Чумаченко М. Проблеми обліку виробничих витрат і калькулювання собівартості продукції в промисловості.
// Бухгалтерський облік і аудит. — 2009, №4. — с.3-11.
- Волков А.В., Саранчин А.В., Чечиков С.Д. Управление себестоимостью
выпускаемой продукции
с применением информационных технологий нового поколения // САПР и графика,№4, 2010 г. [Электронный ресурс] / Сервер журнала САПР и графика, — http://www.sapr.ru/Article.aspx?id=14865
- Живога Я. В., Чаруйская Л.А. Прогнозирование уровня себестоимости добычи газа.// Проблемы совершенствования отраслевого
планирования и методов управления в газовой промышленности. — М., 1982. — с.113-120.
- Криводубский О.А., Шушура А.Н. Динамический прогноз
себестоимости продукции предприятия в режимах online и offline
с использованием глобальной сети Internet // Вторая Международная научно-методическая конференция «Интернет — образование — наука — 2000», 10-12 октября 2000 г.,
Винницкий государственный технический университет. [Электронный ресурс] / Сайт Винницкого государственного технического университета, — http://www.vstu.vinnica.ua/ies2000/doclad/d/285.htm
- Кудянкин Н.Н. Прогнозирование затрат на производство новой техники в условиях малой выборки. // Вопросы повышения эффективности
разработки производства и эксплуатации РЭА. — Рязань, 1982. — с.23-28.
- Маренич Т. Методи обліку витрат і калькулювання собівартості продукції. // Бухгалтерський облік і аудит. — 2006, №12. — с.19-25.
- Мубаракзянов Г.М. Математическая модель себестоимости продукции. // Труды НИИ управляющих машин и систем. — М., 1974, №12. — с.145-155.
- Саканцев М.Г., Саканцев Г.Г. Прогнозирование стоимостных показателей на основе многофакторных статистических моделей. //
Эффективность разработки месторождений руд цветных металлов и схем их переработки. — Свердловск, 1982. — с.3-10.
- Урусова Е.А. Экономико-математические модели в прогнозировании затрат при постройке судов. // Экономика и
организация производства в судостроении. — Николаев, 1990. — с.54-58.
- Чухліб О.А. Управлінське рішення щодо витрат у собівартості продукції. // Фінанси підприємства. — 2006, №2. — с. 129-137.
- Фирман Б.И. Математическая модель формирования затрат пи комплексной переработке сырья. // Повышение комплексности
использования сырья в свинцово-цинковой подотрасли. — Усть-Каменогорск, 1981. — с.12-18.
- Харевич Г.Л. Проблемы стабильности планирования себестоимости //
«Планово-экономический отдел» № 3, 2003 г. [Электронный ресурс] / Специализированный журнал для экономистов, — http://peomag.by/number/2003/3/17/
- Шишкин М.В. Разработка системы прогнозирования затрат // EUP.RU —
Экономика и управление на предприятиях. [Электронный ресурс] / Электронная библиотека «Экономика и управление на предприятиях», —
http://eup.ru/Documents/2003-01-13/1487E.asp
During writing this abstract the master work was not finished yet. Final completion: December 2010.
Full text can be obtained from the author or her teacher аfter that date
|