Реферат по теме выпускной работы
Содержание
- Введение
- 1. Актуальность, цели и задачи исследования
- 2. Технологические особенности мартеновского производства стали
- 3. Технологические особенности электросталеплавильного производства
- 4. Сравнительный анализ удельных выбросов загрязняющих веществ мартеновского и электросталеплавильного производства
- 5. Оценка количественного и качественного состава выбросов загрязняющих веществ при различных режимах работы электросталеплавильных печей
- 6. Анализ возможных методов очистки отходящих газов электросталеплавильного производства
- 7. Расчет рассеивания выбросов загрязняющих веществ в атмосферном воздухе для мартеновского цеха ПрАО
Донецксталь
-МЗ - 8. Исследование уровня загрязнения атмосферного воздуха в районе расположения мартеновского сталеплавильного цеха по данным наблюдения близлежащих стационарных постов контроля
- Выводы
- Список источников
Введение
К числу наиболее актуальных проблем города Донецка относится загрязнение атмосферного воздуха, которое является причиной возникновения множества различных заболеваний у жителей города.
Негативное влияние на состояние атмосферного воздуха оказывают промышленные предприятия, в число которых входят предприятия металлургии.
Одним из ведущих предприятий, специализирующихся на выпуске высококачественной стали, является ПрАО Донецксталь
– металлургический завод. Выпуск стали на данном предприятии осуществляется в физически и морально устаревших мартеновских печах, которые не оборудованы системами газоочистки. Вследствие этого при работе мартеновских печей в атмосферный воздух поступает большое количество загрязняющих веществ. По величине валовых выбросов ПрАО Донецксталь
– МЗ долгие годы занимает одно из первых мест среди предприятий города Донецка. На рисунке 1 приведена диаграмма выбросов загрязняющих веществ в целом по г. Донецку и мартеновским цехом ПрАО Донецксталь-МЗ
[1].
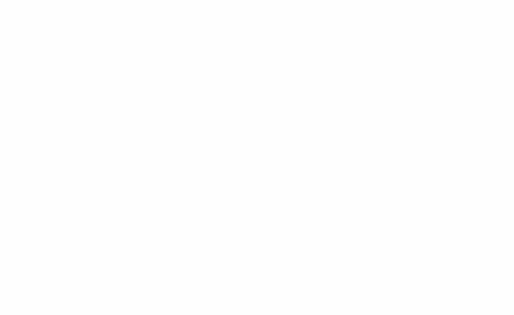
Рисунок 1 – Мощность выбросов загрязняющих веществ
Анализ данных диаграммы показывает, что мартеновский цех ПрАО Донецксталь
-МЗ вносит существенный вклад в загрязнение атмосферного воздуха пылью (мощность выбросов составляет 33 % от общегородского показателя) и оксидами азота (мощность выбросов составляет 40 %).
Следует отметить, что данные вещества являются приоритетными загрязнителями для г. Донецка, в частности, по величине экологического риска оксиды азота занимают второе место среди загрязняющих веществ, а пыль – четвертое.
Таким образом, производство стали в устаревших мартеновских печах, работающих без пылегазоочистных установок, оказывают очень сильное негативное влияние на состояние атмосферного воздуха, и тем самым способствует росту уровня заболеваемости населения. Одним из возможных способов снижения техногенной нагрузки на атмосферный воздух города является замена мартеновского способа производства стали на электросталеплавильный, что позволит существенно уменьшить выбросы загрязняющих веществ.
1. Актуальность, цели и задачи исследования
В настоящее время в г. Донецке на предприятии ПрАО Донецксталь
-металлургический завод реализуется программа по замене мартеновского производства стали на электросталеплавильный. Выплавка стали на данном предприятии будет производиться в современной электросталеплавильной печи.
Вследствие изменения типа печи и технологии выплавки стали произойдет значительное количественное и качественное изменение состава выбросов загрязняющих веществ предприятия. В частности, существенно снизятся выбросы пыли и оксидов азота, которые являются приоритетными загрязнителями для города. В то же время, при работе электросталеплавильных печей в атмосферный воздух поступают такие загрязняющие вещества, как цианиды, фториды, диоксины и фураны. Таким образом, влияние мартеновского и электросталеплавильного производства на состояние атмосферного воздуха существенно отличается.
Целью магистерской работы является сравнительный анализ влияния мартеновского и электросталеплавильного производства на состояние атмосферного воздуха.
Задачи исследования:
- анализ технологических особенностей мартеновского и электросталеплавильного производств;
- оценка количественного и качественного состава выбросов загрязняющих веществ при различных режимах работы мартеновских и электросталеплавильных печей;
- анализ возможных методов очистки отходящих газов для данных производств;
- расчет рассеивания выбросов загрязняющих веществ в атмосферном воздухе и определение зоны влияния сталеплавильных цехов;
- исследование уровня загрязнения атмосферного воздуха в районе расположения мартеновского сталеплавильного цеха по данным наблюдения близлежащих стационарных постов контроля;
- расчет вклада мартеновского производства в формирование фоновых концентраций загрязняющих веществ в атмосферном воздухе;
- определение зависимости концентраций загрязняющих веществ в атмосферном воздухе в зоне влияния мартеновского цеха от его мощности выбросов;
- расчет мощности выбросов загрязняющих веществ от электросталеплавильного цеха;
- расчет экологических рисков.
2. Технологические особенности мартеновского производства стали
Мартеновская печь представляет собой пламенную регенеративную печь для переработки чугуна и стального лома в сталь заданного химического состава и качества.
Мартеновская печь состоит из следующих основных частей (рисунок 2.1): рабочего пространства (под, передняя и задняя стенки, свод), где осуществляется плавка; головок (правой и левой), состоящих из собственно головок и вертикальных каналов для подачи топлива и воздуха в рабочее пространство и отвода из него продуктов сгорания; шлаковиков (воздушных и газовых) – для осаждения и накопления пыли и частиц шлака, выпадающих из проходящих через них продуктов сгорания; регенераторов (воздушных и газовых) – для подогрева поступающих в печь газа и воздуха теплом выходящих из рабочего пространства продуктов сгорания; боровов (каналов) для воздуха, газа и продуктов сгорания; системы перекидных клапанов, предназначенных для изменения направления подачи в печь топлива и воздуха и отвода из рабочего пространства продуктов сгорания; котла-утилизатора; дымовой трубы. Рабочее пространство и головки печи расположены выше рабочей площадки цеха и условно называются верхним строением печи. Остальные части находятся под рабочей площадкой и называются нижним строением [2].
Мартеновская печь имеет симметричное строение: правая и левая её стороны относительно вертикальной оси одинаковы по устройству.
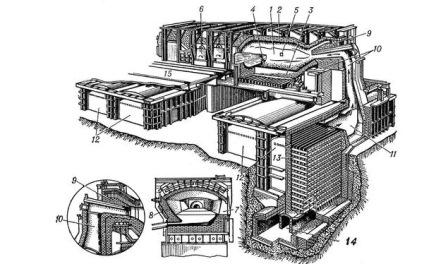
1 – рабочее пространство; 2 – свод; 3 – подина; 4 – сталевыпускное отверстие; 5 – отверстие для спуска шлака; 6 – завалочные окна; 7 – передняя стенка; 8 – задняя стенка; 9 – головки; 10 – вертикальные каналы; 11 – шлаковик; 12 – регенераторы: 13 – насадка регенераторов; 14 – борова; 15 – рабочая площадка
Рисунок 2.1 – Устройство мартеновской печи
В мартеновском процессе выплавки стали различают следующие периоды: заправка печи, завалка и прогрев шихты, заливка жидкого или завалка твёрдого чугуна, плавление, кипение, раскисление и легирование, выпуск.
Заправка печи необходима для поддержания в рабочем состоянии всех элементов кладки плавильного пространства. Заправка печи заключается в том, что после выпуска из печи металла и шлака подину тщательно осматривают и, если нужно, исправляют замеченные неровности.
Завалка шихты осуществляется завалочной машиной. Все твёрдые шихтовые материалы подаются к печи в специальных коробах – мульдах). Для дополнительного подогрева всего стального лома перед заливкой в печь чугуна производятся прогрев шихты, после чего происходит заливка жидкого или завалка твердого чугуна.
Период плавления начинается сразу после окончания заливки (завалки) чугуна и продолжается 1-5 ч. В печь в этот период подаётся максимальное количество топлива, ванна продувается кислородом. В процессе заливки чугуна и в первый момент плавления происходит интенсивное образование шлака, в состав которого входят оксиды железа, кальция, кремния, марганца, фосфора, а также разрушающиеся огнеупоры кладки печи, флюсы и примеси, вносимые шихтой. Толстый слой образовавшегося шлака затрудняет передачу тепла от факела к металлу. В связи с этим в первой половине плавления из печи удаляют (путём спуска в шлаковые чаши) некоторое количество шлака [3].
Химический состав металлической ванны в момент полного расплавления заметно отличается от состава, который сталь должна иметь перед выпуском плавки; температура металла относительно невысока. Поэтому главное назначение следующих периодов плавки, называемых доводкой, состоит в том, чтобы обеспечить необходимый нагрев металла, доведение его до заданного химического состава.
В связи с этим период кипения – наиболее ответственный период мартеновской плавки. Главной реакцией этого периода является реакция окисления растворённого в жидком металле углерода. Образующиеся в результате этой реакции пузырьки оксида углерода вырываются на поверхность металла, пробивают слой шлака и, выходя на его поверхность, создают впечатление кипения ванны.
Период кипения условно разделяют на 2 части – период рудного кипения, когда в печь вводят добавки руды (кислород), извести, флюсов, и период чистого кипения, когда окисление растворенного в металле углерода продолжается без каких-либо добавок, за счёт растворённого в шлаке и металле кислорода. В период чистого кипения происходит окончательное доведение металла до требуемых температуры и химического состава.
Раскисление и легирование – завершающий период плавки, основное назначение которого состоит в снижении содержания кислорода в металле и доведении состава металла до заданного по содержанию всех элементов, включая легирующие. Раскисляющие и легирующие добавки в зависимости от выплавляемой марки стали вводят или в печь, или в сталеплавильный ковш во время выпуска металла [4].
Для выпуска металла из печи со стороны задней стенки пробивают или прожигают струей газообразного кислорода сталевыпускное отверстие; металл по жёлобу стекает в установленный под ним сталеразливочный ковш. Из ковша металл разливают в изложницы или на установках непрерывной разливки стали.
Главным достоинством мартеновского процесса является возможность его проведения при любом расходе чугуна, а также возможность переработки как жидкого, так и твердого чугуна. Другим преимуществом мартеновских печей является высокий выход стали, который составляет 90-96 % металлической завалки. К преимуществам мартеновского производства стали также относится использование первичной энергии (тепла газообразного и жидкого топлив).
Недостатками мартеновского производства являются:
- низкая производительность;
- большие трудности в синхронизации плавки стали в мартеновской печи и разливки стали на машины непрерывного литья заготовок;
- большой расход огнеупорных материалов и топлива;
- необходимость ручного труда при ремонтах печей;
- тяжелые условия труда;
- большая длительность процесса плавки.
По этим причинам мартеновский процесс неуклонно вытесняют кислородно-конвертерный и электросталеплавильный.
3. Технологические особенности электросталеплавильного производства
Электросталеплавильное производство – производство стали в электрических (главным образом дуговых) печах. Позволяет получать стали широкого сортамента (от рядовых до высококачественных) при массе плавки от нескольких десятков килограмм до 200 т и выше. Электросталеплавильное производство имеет существенные преимущества перед другими способами получения стали, и его удельный вес в мировом производстве стали непрерывно возрастает.
Выплавку стали данным способом осуществляют в дуговой сталеплавильной печи (рисунок 3.1). Различают сталеплавильные печи постоянного и переменного тока [5].
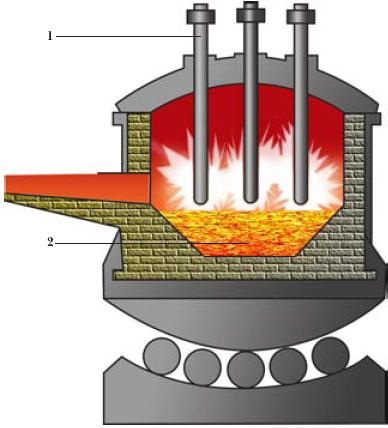
1 – электроды, 2 – металл
Рисунок 3.1 – Дуговая электросталеплавильная печь
Дуговая печь состоит из рабочего пространства (фактически печи) с электродами и токоподводами и устройств, обеспечивающих наклон печи, удержание и перемещение электродов и загрузку шихты.
Плавку стали ведут в рабочем пространстве, ограниченном сверху куполообразным сводом, снизу сферическим подом и с боков стенами.
Плавка стали в дуговых сталеплавильных печах, после осмотра печи и ремонта пострадавших участков футеровки (заправка), начинается с завалки шихты. Шихту в печи загружают сверху при помощи загрузочной бадьи (корзины). Для предохранения подины от ударов крупными кусками шихты на дно бадьи загружают мелкий лом. Для раннего шлакообразования в завалку вводят известь 2-3 % от массы металлической шихты.
После окончания завалки в печь опускают электроды, включают высоковольтный выключатель и начинают период плавления. Под действием высокой температуры дуг шихта под электродами плавится, жидкий металл стекает вниз, накапливаясь в центральной части подины. По мере увеличения количества жидкого металла электроды поднимаются. Плавление ведут при максимальной мощности печного трансформатора. Во время плавления происходит окисление составляющих шихты, формируется шлак, происходит частичное удаление в шлак фосфора и серы. Окисление примесей осуществляется за счет кислорода воздуха, окалины и ржавчины, внесенных металлической шихтой [6].
За время плавления полностью окисляется кремний, 40-60 % марганца, частично окисляется углерод и железо. Шлак к концу периода плавления имеет примерно следующий состав, %: 35-40 CaO; 15-25 SiO2; 8-15 FeO; 5-10 MnO; 3-7 Al2O3; 0,2 P2O5. Продолжительность периода плавки определяется мощностью трансформатора и составляет от 1 часа.
Окислительный период начинается с того, что из печи сливают 65-75 % шлака, образовавшегося в период плавления. Слив шлака производят для того, чтобы удалить из печи перешедший в шлак фосфор.
Присадку руды в течение окислительного периода осуществляют для интенсивного кипения ванны – окисляется углерод, реагируя с оксидами железа руды с выделением большого количества пузырьков СО. При этом происходит дегазация металла и его перемешивание, что ускоряет процессы дефосфорации и нагрева. При кипении вместе с пузырьками СО из металла также удаляются водород и азот.
После формирования жидкоподвижного шлака в ванне в течение всего окислительного периода ведут продувку кислородом. Печь для слива шлака в течение данного периода наклонена в сторону рабочего окна. Под воздействием газов шлак вспенивается, уровень его повышается, и он стекает в шлаковую чашу через порог рабочего окна.
Шлак в конце окислительного периода имеет примерно следующий состав, %: 35-50 CaO; 10-20 SiO2; 4-12 MnO; 6-15 MgO; 3-7 Al2O3; 6-30 FeO; 2-6 Fe2O3; 0,5 P2O5.
Окислительный период заканчивается тогда, когда углерод окисляется до нижнего предела его содержания в выплавляемой марке стали, а содержание фосфора снижено до 0,015 %. Полное скачивание окислительного шлака необходимо, чтобы содержащийся в нем фосфор не перешел обратно в металл во время восстановительного периода [7].
4. Сравнительный анализ удельных выбросов загрязняющих веществ мартеновского и электросталеплавильного производства
Количественный и качественный состав выбросов загрязняющих веществ при проведении процесса выплавки стали зависит от технологии выплавки стали и от емкости печи. В таблице 1 приведена сравнительная характеристика удельных выбросов загрязняющих веществ для мартеновских печей, действующих на ПрАО Донецксталь
-МЗ (однованные печи емкостью 100 т, в которых не применяется продувка кислородом), и для электросталеплавильной печи емкостью 150 т, которая будет установлена взамен мартеновских [8].
Таблица 4.1 – Мощность выбросов загрязняющих веществ при проведении мартеновского и электросталеплавильного процесса
Название загрязняющего вещества | Удельные выбросы загрязняющих веществ, кг/т стали | |
Мартеновское производство | Электросталеплавильное производство | |
1 Организованные выбросы | ||
Пыль | 11,33 | 9,40 |
Оксиды азота | – | 0,27 |
Оксид углерода | – | 1,35 |
Диоксид серы | – | 0,0016 |
Цианиды | – | 0,0284 |
Фториды | – | 0,00056 |
2 Неорганизованные выбросы | ||
Пыль | 6,516-7,575 | 0,68-1,38 |
Оксиды азота | 0,5 | – |
Оксид углерода | 4,084-0,499 | – |
Диоксид серы | 0,0204 | – |
3 Выбросы тяжелых металлов, г/т сталиы | ||
Кадмий | 0,80 | 0,52 |
Свинец | 35,30 | 12,90 |
Медь | 1,53 | 2,70 |
Ртуть | – | 0,012 |
Никель | 0,33 | 0,48 |
Цинк | 52,10 | 176,50 |
Анализ данных таблицы показывает, что удельные выбросы пыли, оксидов азота, диоксида серы, кадмия и свинца имеют большие значения для мартеновского производства, а удельные выбросы меди, никеля и цинка больше при электросталеплавильном производстве. Также следует отметить, что в выбросах электросталеплавильного производства присутствуют такие токсиканты, как ртуть, цианиды и фториды, нехарактерные для мартеновского производства.
5. Оценка количественного и качественного состава выбросов загрязняющих веществ при различных режимах работы электросталеплавильных печей
В связи с происходящими сложными физико-химическими процессами выплавка стали сопровождается интенсивным образованием газов, в которых содержатся оксиды углерода, оксиды азота, оксид серы, пыль, а также небольшое количество цианидов, сернистого ангидрида и фторидов. Концентрация данных загрязняющих веществ в отходящих газах зависит от периода плавки, способа ее интенсификации и резко изменяется в пределах одной плавки.
На рисунке 4 приведены данные о содержании цианистых соединений (кривая 1), оксидов азота (кривая 2) и углерода (ІІ) (кривая 3), а также пыли (кривая 4) в отходящих газах при нормальных условиях для работы печи ДСП-100. Общее время цикла такой печи составляет 2 часа 15 минут, а средний объем отходящих газов – 8000 м3/ч [9].
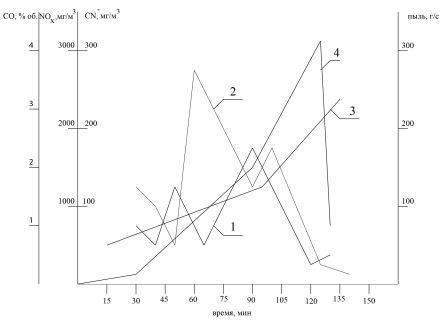
Рисунок 5.1 – Зависимость выбросов загрязняющих веществ от времени работы электропечи для одного цикла
На основании представленных данных в программе ЭОЛ+ был проведен расчет рассеивания выбросов загрязняющих веществ для печи ДСП-100 в 4 точках: 50 мин, 60 мин (максимум для концентрации диоксида азота), 90 мин (максимум для концентрации цианистых соединений), 125 мин (максимум пылевыделения).
В результате проведения данного расчета были определены концентрации рассматриваемых загрязняющих веществ в атмосферном воздухе и их концентрации на границе санитарно-защитной зоны, которая составляет 1000 м.
Как показали расчеты, максимальные значения для всех рассмотренных веществ наблюдаются на расстоянии 1100 м от источника и поэтому практически совпадают со значениями концентраций на границе СЗЗ.
Анализ результатов расчета показал, что концентрации NO2 и HCN достигают наибольших значений (0,430 и 0,023 ПДК соответственно) при рассеивании выбросов, которые образуются во время плавления, когда температура максимальна. Для оксида углерода и пыли наблюдается возрастание концентрации загрязняющих веществ в течение процесса. При этом, если для СО в конце процесса концентрация на СЗЗ составляет 0,12 ПДК, то для пыли превышает нормативные в 3,62 раза.
Таким образом, при определении концентрации загрязняющих веществ в атмосферном воздухе более целесообразно использовать не средние значения мощности выбросов, а их пиковые значения.
6 Анализ возможных методов очистки отходящих газов электросталеплавильного производства
Газ, выделяющийся из электросталеплавильной печи, имеет следующий химический состав, % (объемн.): СО < 68; СО2 < 30; О2 < 21; N2 30-79. Концентрация пыли составляет 50-60 г/м3, она состоит из оксидов железа, кремния, алюминия, марганца, кальция. Температура газа на выходе из печи составляет около 1600 °С.
Вследствие наличия в газе взрывоопасного оксида углерода (СО), перед направлением на очистку оксид углерода дожигают в специальном устройстве.
Отходящие газы очищают в сухом пластинчатом электрофильтре или в тканевом рукавном фильтре, поскольку среди распространенных сухих способов очистки промышленных газов от пыли наибольшая эффективность улавливания тонкодисперсных частиц (до 5 мкм) достигается практически только при использовании рукавных фильтров и электрофильтров.
Ведущее положение в настоящее время занимают рукавные фильтры. При увеличении коэффициента пылеулавливания от 98 до 99 % стоимость электрофильтров значительно возрастает (приблизительно на 20 %), в то время как стоимость рукавных фильтров и объём потребляемой ими энергии с увеличением эффективности пылеулавливания не меняются, что делает их наиболее привлекательными с точки зрения эксплуатации.
Установки пылеулавливания с применением электрофильтров характеризуются меньшим энергопотреблением, но для их сооружения требуются значительные капитальные затраты. При этом, электрофильтры чувствительные к параметрам очищаемых газов, при их колебании может снижаться эффективность аппаратов.
Электрофильтры применяются при температурах газов до 300400 градусов и являются наиболее экономичными при объемах газов более 500 тыс. м3/ч. В то же время, специалисты не рекомендуют применять электрофильтры при необходимости получения запыленности газа на выходе менее 500-100 мг/м3. Степень очистки газов в электрофильтрах достигает 98%. При использовании электрофильтров предъявляются достаточно высокие требования безопасности, поскольку велика вероятность поражения работников электротоком в случае несоблюдения требований охраны труда при их эксплуатации. Поэтому рукавные фильтры здесь имеют определенное преимущество перед электрофильтрами.
При использовании рукавных фильтров обеспечивается остаточная запыленность ниже 5-10 мг/м3 независимо от свойств улавливаемой пыли; работа проводится в широком диапазоне очищаемого газа. Степень очистки составляет 99 % и более, особенно пыли с высоким электрическим сопротивлением, улавливание которой в электрофильтрах происходит недостаточно полно. Расход энергии составляет 2-2,5 кВт/ч на 1000 м3 очищаемых газов. Низкие капитальные затраты и умеренные эксплуатационные расходы – еще одно преимущество таких устройств. Применение синтетических тканей в качестве фильтровальных материалов для фильтров позволяет использовать их при температурах выше 140 градусов. При этом, такие ткани более долговечны по сравнению с натуральными шерстяными и хлопчатобумажными тканями.
Особый интерес представляют рукавные фильтры с импульсной продувкой. Они применяются для очистки газов объемом 500 тыс. м3 и более и температурах около 150 градусов с использованием синтетических фильтровальных материалов, что обеспечивает высокую степень очистки при значительных удельных нагрузках (46 м3/кВ•м•мин). Другими преимуществами таких фильтров являются отсутствие подвижных частей, простота обслуживания, надежность действия и длительный срок службы рукавов (до 20-24 месяцев) [10].
7 Расчет рассеивания выбросов загрязняющих веществ в атмосферном воздухе для мартеновского цеха ПрАО Донецксталь
-МЗ
На основе данных инвентаризации источников выбросов ПрАО Донецксталь
-МЗ в программе ЭОЛ + был проведен расчет рассеивания выбросов загрязняющих веществ мартеновского цеха предприятия. Полученные результаты показали, что на границе санитарно-защитной зоны предприятия наблюдаются следующие концентрации загрязняющих веществ, в долях ПДК:
- оксид железа (в пересчете на железо) – 0,15;
- оксид кадмия (в пересчете на кадмий) – 0,025;
- марганец и его соединения (в пересчете на диоксид марганца) – 1,03;
- оксид меди (в пересчете на медь) – 0,0058;
- никель металлический – 0,0041;
- свинец и его соединения (в пересчете на свинец) – 3,34;
- хром шестивалентный (в пересчете на триоксид хрома) – 0,039;
- цинк и его соединения (в пересчете на цинк) – 0,0099;
- диоксид азота – 3,33;
- диоксид серы – 0,12;
- оксид углерода – 0,41;
- пыль неорганическая – 0,22.
Таким образом, можно сделать вывод о том, что на границе СЗЗ предприятия нарушаются нормативы ПДК для марганца и его соединений (в пересчете на диоксид марганца), свинца и его соединений (в пересчете на свинец), а также для диоксида азота.
8 Исследование уровня загрязнения атмосферного воздуха в районе расположения мартеновского сталеплавильного цеха по данным наблюдения близлежащих стационарных постов контроля
В зоне влияния ПрАО Донецксталь
-МЗ расположен пост наблюдения и контроля атмосферного воздуха № 4. На данном посте анализируется концентрация таких загрязняющих веществ как пыль, диоксид серы, оксид углерода, диоксид азота. На рисунке 8.1 представлена динамика уровня загрязнения атмосферного воздуха за последние 11 лет по данным наблюдения поста № 4.
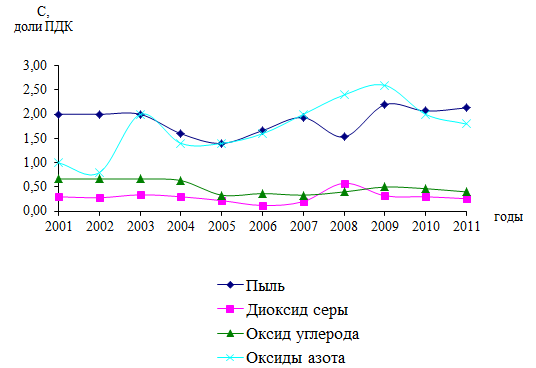
Рисунок 8.1 – Динамика изменения концентраций загрязняющих веществ на посте наблюдения № 4
Анализ графика позволяет сделать вывод о том, что в течение всего рассматриваемого периода на данном посте наблюдения концентрация оксида углерода и диоксида серы в атмосферном воздухе не превышала нормативов ПДК, в то время как по пыли и диоксиду азота наблюдались значительные превышения ПДК. Концентрации данных веществ достигла максимума в 2009 году и составила 2,2 ПДК для пыли и 2,6 ПДК для диоксида азота.
Выводы
Мартеновский цех ПрАО Донецксталь
-МЗ оказывает существенное влияние на состояние атмосферного воздуха города, в частности, выбросы пыли данного цеха составляют 33 % от общегородского показателя, а диоксида азота – 40 %. Именно по этим веществам наблюдается значительное превышение нормативов ПДК на посте наблюдения и контроля атмосферного воздуха, расположенного в зоне влияния предприятия.
Значительные объемы выбросов загрязняющих веществ данным цехом обусловлены тем, что выплавка стали в нем производится в физически и морально устаревших мартеновских печах, которые не оборудованы пылегазоочистными установками.
Но в настоящее время на предприятии реализуется программа по замене мартеновского производства стали на электросталеплавильный. Для электросталеплавильного производства характерны значительно меньшие удельные выбросы таких загрязняющих веществ, как пыль, диоксид азота, диоксид серы, кадмий и свинец. Также следует отметить, что электросталеплавильный цех будет оборудован современными пылеочистными установками – рукавными фильтрами, эффективность очистки которых составляет 99 %.
Но в настоящее время на предприятии реализуется программа по замене мартеновского производства стали на электросталеплавильный. Для электросталеплавильного производства характерны значительно меньшие удельные выбросы таких загрязняющих веществ, как пыль, диоксид азота, диоксид серы, кадмий и свинец. Также следует отметить, что электросталеплавильный цех будет оборудован современными пылеочистными установками – рукавными фильтрами, эффективность очистки которых составляет 99 %.
Список источников
- Звіт про стан навколишнього природного середовища в м. Донецьк у 2006 році. – Донецьк, 2003. – 152 с.
- Доклад о состоянии окружающей природной среды города Донецка в 2004 – 2005 годах. – Донецк, 2006. – 72 с.
- Брыгинец Н.Г., Батманов А. И. Защита воздушного и водного бассейнов от выбросов металлургических заводов. – М.: Металлургия, 1980. – 48 с.
- Газоочистные установки и аппараты в металлургическом производстве. Ученик для вузов. – М.: Металургія, 1990. – 400 с.
- Збірник показників емісії (питомих викидів) забруднюючих речовин в атмосферне повітря різними виробництвами, т.1. – Донецьк: Український науковий центр технічної екології, 2004. – 184 с.
- Программа охраны и оздоровления атмосферного воздуха города Донецка. [Электронный ресурс] – Режим доступа: http://doneco.org.ua.
- ОНД-86. Госкомгидромет. Методика расчёта концентраций в атмосферном воздухе вредных веществ, содержащихся в выбросах предприятий. – М., 1987. – 82 с.
- Науково-технічний розвиток Донецької області у сфері охорони навколишнього середовища, екологічної безпеки та відтворення природних ресурсів на період до 2020 року [Електронний ресурс] / Донецьк. – Режим доступу: http://doneco.org.ua.
- Пылегазовые выбросы предприятий черной металлургии. Андоньев С.М., Зайцев Ю.С., Филипьев О.В. – Харьков: Металлургия, 1998. – 247 с.
- Бирман Ю.А, Вурдова Н.Г. Инженерная защита окружающей среды. – М.: АСВ, 2002. – 296 с.