Реферат по теме выпускной работы
Содержание
- Introduction
- 1. Relevance and objectives
- 2. Technological features an open-hearth steel production
- 3. Technological features of the production of electric
- 4. Calculation of the dispersion of pollutants in the air for the open-hearth shop PrJSC
Donetsk stall
-MZ - 5. Investigation of the level of air pollution in the area of the open-hearth steel plant according to the observations of nearby stationary control posts
- Findings
- List of sources
Introduction
Among the most pressing problems of the city of Donetsk is air pollution, which is the cause of many different diseases among residents of the city.
Negative impact on air quality have industrial enterprises, which include metallurgical enterprises.
One of the leading companies specializing in the production of stainless steel, is Press Donetsk stall
– Iron and Steel Works. "Steel production in the enterprise is in a physically and morally obsolete open-hearth furnaces, which are not equipped with gas cleaning systems. Consequently, when operating open-hearth furnaces in the air, large amounts of pollutants. The magnitude of total emissions Press Donetsk stall
– MZ "for many years is one of the first places among the enterprises of the city of Donetsk [1].
The analysis of the chart shows that the open-hearth shop PrJSC Donetsk stall
-MZ "contributes significantly to air pollution due to dust (the power emission is 33% of the citywide rate) and nitrogen oxides (the power emission is 40%).
It should be noted that these substances are priority pollutants for the city of Donetsk, in particular, the magnitude of the environmental risk of nitrogen oxides in second place among the pollutants, and dust – the fourth (the ecological risks of these substances are, respectively, 3,96*10-3 and 2,28*10-4).
Thus, the production of steel in the old open-hearth furnaces working without dust filters installations, have a very strong negative impact on air quality, and thus contributes to the morbidity of the population. One possible way to reduce development pressure on the air of the city is to replace the open-hearth method of steel production by electric arc, which will significantly reduce emissions of pollutants.
1. Relevance and objectives
Currently, the city of Donetsk in the enterprise Press Donetsk stall
Metallurgical Plant "implementing a program to replace the open-hearth steel production by electric arc. Steel production at this plant will be manufactured in a modern electric steel furnace.
Due to changes in the type of furnace and steelmaking technology will significantly change the quantitative and qualitative composition of the emissions of the enterprise. In particular, significantly reducing the emissions of dust and nitrogen oxides, which are priority pollutants for the city. At the same time, the electric-furnace operation in ambient air to pollutants such as cyanide, fluoride, dioxins and furans. Thus, the effect of open-hearth and electric steel production in the state of the air is very different.
The purpose of master's thesis is a comparative analysis of the impact of open-hearth and electric steel production in the state of the atmosphere.
Research objectives:
- an analysis of the technological features of open-hearth and electric industries;
- evaluation of quantitative and qualitative composition of pollutant emissions under various operating conditions of open-hearth and electric furnaces;
- analysis of the possible methods of purification of exhaust gases for these industries;
- calculation of the dispersion of pollutants in the air and the definition of zones of influence steelworks;
- study of the air pollution level in the vicinity of the open-hearth steel plant were observed surrounding fixed positions of control;
- the calculation of the contribution of open-hearth production in the formation of background concentrations of pollutants in the air;
- determination of the concentration of pollutants in the air in the zone of open-hearth shop of his power of emissions;
- calculation of emissions from the electric department;
- calculation of environmental risks.
2. Technological features an open-hearth steel production
Open-hearth furnace is a regenerative fiery furnace for recycling iron and steel scrap to steel given chemical composition and quality.
Open-hearth furnace consists of the following parts (Figure 2): the working space (for front and rear walls, vault), where the smelting; heads (right and left), consisting of actual heads and vertical channels for the fuel and air in the workplace space and the removal of a product of combustion, slag (air and gas) – for the deposition and accumulation of dust and slag particles falling from passing through them, the combustion products; regenerators (air and gas) – for heating entering the furnace gas and air heat emanating from the working space of the combustion products, hogs (channels) for air, gas and products of combustion system changeover valves for changing the direction of feed to the furnace fuel and air and removal of the working space of the combustion products, the recovery boiler, the chimney. Workspace and the furnace head located above the working platform of shop and conditionally called topside oven. The remaining parts are under the working area and called the lower structure. Open-hearth furnace has a symmetrical structure: the right and left sides of the vertical axis are the same on the device [2].
Мартеновская печь имеет симметричное строение: правая и левая её стороны относительно вертикальной оси одинаковы по устройству.
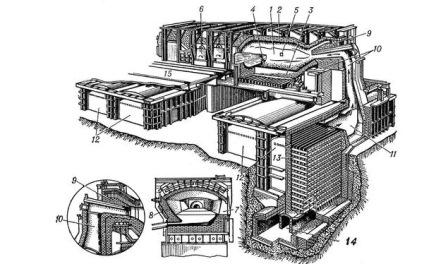
1 – work space, 2 – set of 3 – hearth, 4 – stalevypusknoe hole, 5 – hole for lowering the slag 6 – zavalochnye Windows 7 – the front wall, 8 – back wall, 9 – Head, 10 – vertical channels, 11 – slag, 12 – regenerators: 13 – nozzle regenerators, 14 – hog, 15 – working platform
Figure 2.1 – Installation of open hearth furnace
In the open-hearth steelmaking process distinguish the following periods: charging the furnace, filling and heating of the charge, pouring a liquid or solid cast filling, melting, boiling, deoxidation and alloying, issue.
Filling the furnace is necessary to maintain the clutch all the elements of the melting space. Filling the furnace is in the fact that after the release of the metal and slag furnace hearth carefully inspected and, if necessary, correct the irregularities were noticed.
The filling mixture is charging machine. All solid charge materials are fed to the furnace in the special boxes – charging boxes). For additional heating of steel scrap before casting into the furnace are made of cast iron heating of the charge, and then fill a liquid or solid iron filling.
Melting period begins immediately after the end of filling (filling), iron and lasts 1 – 5 pm in the oven during this period served the maximum amount of fuel, a bath is blown with oxygen. In the process of casting iron and the first moment of fusion is an intensive formation of slag, which consists of oxides of iron, calcium, silicon, manganese, phosphorus, and crumbling masonry furnace refractoriness, fluxes and impurities introduced by the charge. A thick layer of slag formed impedes the transfer of heat from the torch to the metal. In this regard, in the first half of the melting furnace is removed (by descent in the slag bowl), a certain amount of slag [3].
The chemical composition of the metal bath at the time of complete melting is markedly different from the composition of which steel shall be before the release of heat, the temperature of the metal is relatively low. Therefore, the main purpose of the following periods of heat, called fine-tuning, is to provide the necessary heating of the metal, bringing it up to a given chemical composition.
In this regard, during the boil – the most crucial period of open-hearth melting. The main reaction of this period is the oxidation of dissolved carbon in liquid metal. Resulting from the reaction of carbon dioxide bubbles erupt to the surface of the metal, the slag layer and the punch, leaving on the surface, creating the impression of boiling baths.
The period of boiling is conventionally divided into two parts – the period of ore boiling point when the additive is introduced into the furnace ore (oxygen), lime, fluxes, and the period of pure boiling, when the oxidation of dissolved carbon in the metal continues without any additives, due to dissolved in the slag and metal oxygen. During the boiling point of pure metal is finally bringing to the required temperature and chemical composition.
Deoxidation and alloying – the final period of melting, the main purpose of which is to reduce the oxygen content in the metal and bring to a given composition of the metal content of all elements, including the alloying. Deoxidizing and alloying additives, depending on the grade of cast steel, or injected into the furnace or steelmaking ladle during tapping [4].
For the production of metal from the furnace from the back of the punch or burn a jet of oxygen gas stalevypusknoe hole, the metal flows into the chute mounted beneath casting ladle. From the ladle metal is poured into molds or continuous casting of steel.
The main advantage of open-hearth process is its ability to conduct with any consumption of pig iron, as well as the ability to process both liquid and solid iron. Another advantage of the open-hearth furnace is a high yield steel, which is 90-96% metal filling. The advantages of open-hearth steel production also includes the use of primary energy (heat of gaseous and liquid fuels).
3. Technological features of the production of electric
Electric steelmaking – production of steel in electric (mainly arc) furnace. Allows you to receive a wide assortment steel (from ordinary to high) at a mass fusion of several tens of kilograms to 200 tons and above. Electric steelmaking has significant advantages over other methods of steel production, and its share in world steel production is continuously increasing. Steel production in this way is carried out in electric arc furnace (Figure 3.1). There are steel-smelting furnace of direct and alternating current. [5].
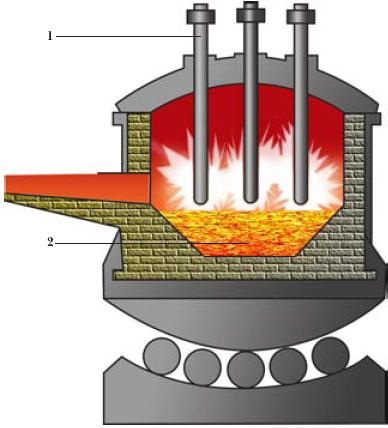
1 – electrodes, 2 – metal
Figure 3.1 – Electric arc furnace
Arc furnace consists of a workspace (actually the oven) with the electrodes and current leads and devices, providing the slope of the stove, holding and moving the electrodes and the loading of the charge.
Melting of steel are in the workspace, limited above a domed vault, spherical hearth bottom and sides of the walls.
Melting of steel in electric arc furnaces, ovens, after inspection and repair of the affected areas of the lining (filling), begins with the filling mixture. Charge in the furnace is charged from the top with boot tub (basket). To protect the hearth from the blows large chunks of the charge on the bottom of the tub is charged a small crowbar. For early slag formation in the filling of lime injected 2-3% by weight of the metal charge.
After the end of filling is lowered into the furnace electrodes include a high voltage switch and start the melting period. Under the influence of high temperature arc charge under the electrode melts, the liquid metal flows downward, accumulating in the central part of the hearth. As the number of liquid metal electrodes are raised. Melting is carried out at a maximum power of the furnace transformer. During melting, oxidation components of the charge, the slag is formed, there is a partial removal of the slag phosphorus and sulfur. The oxidation of the impurities at the expense of atmospheric oxygen, scale and rust, made of metal charge [6].
During melting completely oxidized silicon, 40-60% of manganese, partially oxidized carbon and iron. The slag at the end of the period of melting is approximately the following composition,%: 35-40 CaO; 15-25 SiO2; 8-15 FeO; 5-10 MnO; 3-7 Al2O3; 0,2 P2O5.The duration of the heat capacity is determined by the transformer is 1 hour.
Oxidative period begins with the fact that poured out of the oven 65-75% of the slag formed during the melting. Draining the slag produced in order to remove from the oven converted to slag phosphorus.
Additive ore during the oxidation period is carried out for intensive boiling bath – oxidized carbon reacts with oxides of iron ore a large amount of CO bubbles. Thus there is a metal degassing and mixing, which speeds up the process of heating and dephosphorization. When boiling, with bubbles of CO from the metal and removes hydrogen and nitrogen.
After the formation of slag in the bath zhidkopodvizhnogo during the oxidation period are purged with oxygen. Furnace slag to drain during this period is tilted toward the working window. Under the influence of gas foamed slag, its level rises, and it drains into the slag bowl over the threshold of the working window.
The slag at the end of the oxidation period is approximately the following composition,%: 35-50 CaO; 10-20 SiO2; 4-12 MnO; 6-15 MgO; 3-7 Al2O3; 6-30 FeO; 2-6 Fe2O3; 0,5 P2O5.
Oxidative period ends when the carbon is oxidized to the lower limit of its content in the smelted steel grade, and the phosphorus content is reduced to 0.015%. Download the complete oxidation of slag is necessary that it contained phosphorus is not passed back to the metal during the recovery period [7].
4 Calculation of the dispersion of pollutants in the air for the open-hearth shop PrJSC Donetsk stall
-MZ
Based on the inventory of emission sources PrJSC Donetsk stall
-MZ in the program EOL + was calculated dispersion of emissions of open-hearth shop of the enterprise. The results showed that at the boundary of the sanitary protection zone of the plant are observed following the concentration of pollutants in the fractions of MPC:
- Iron oxide (in terms of iron) – 0,15;
- Cadmium oxide (based on cadmium) – 0,025;
- Manganese and its compounds (based on manganese dioxide) – 1,03;
- Copper oxide (based on copper) – 0,0058;
- Nickel metal – 0,0041;
- Lead and its compounds (in terms of lead) – 3,34;
- Hexavalent chromium (in terms of chromium trioxide) – 0,039;
- Zinc and compounds (in terms of zinc – 0,0099;
- Nitrogen dioxide – 3,33;
- Sulfur dioxide – 0,12;
- Carbon dioxide – 0,41;
- Inorganic dust – 0,22.
Thus, it can be concluded that the company violated the SPZ boundary limit values for manganese and its compounds (based on manganese dioxide), lead and its compounds (in terms of lead), and for nitrogen dioxide.
5 Investigation of the level of air pollution in the area of the open-hearth steel plant according to the observations of nearby stationary control posts
In the zone of influence PrJSC Donetsk stall
-MH is located a monitoring and control of air number 4. In this post, analyzes the concentration of such pollutants as dust, sulfur dioxide, carbon monoxide, nitrogen dioxide.
Analysis the period under review in this post, observing the concentration of carbon monoxide and sulfur dioxide in the atmosphere does not exceed the limit values, while the dust and nitrogen dioxide observed a significant excess of MPC. The concentrations of these substances peaked in 2009 and amounted to 2.2 MAC for dust and 2.6 MAC for nitrogen dioxide.
Findings
Open-hearth shop PrJSC Donetsk stall
-MZ "has a significant impact on the air of the city, in particular, the dust emissions of the plant make up 33% of the citywide rate, and nitrogen dioxide – 40%. For these substances there is a significant excess of limit values for fasting supervision and control of air, which is located in the zone of influence of the enterprise.
Significant amounts of pollutants according to shop due to the fact that the production of steel in it is a physically and morally obsolete open-hearth furnaces, which are not equipped with dust filters settings.
But now the company implemented a program to replace the open-hearth steel production by electric arc. For electric production is characterized by significantly lower specific emissions of pollutants such as dust, nitrogen dioxide, sulfur dioxide, cadmium and lead. It should also be noted that the arc-shop will be equipped with modern facilities pyleochistnymi – bag filters, cleaning efficiency which is 99%.
Thus, the replacement of open-hearth method of steel production by electric arc will significantly reduce pollutant emissions and to reduce human impacts on the atmosphere of the city.
List of sources
- Звіт про стан навколишнього природного середовища в м. Донецьк у 2006 році. – Донецьк, 2003. – 152 с.
- Доклад о состоянии окружающей природной среды города Донецка в 2004 – 2005 годах. – Донецк, 2006. – 72 с.
- Брыгинец Н.Г., Батманов А. И. Защита воздушного и водного бассейнов от выбросов металлургических заводов. – М.: Металлургия, 1980. – 48 с.
- Газоочистные установки и аппараты в металлургическом производстве. Ученик для вузов. – М.: Металургія, 1990. – 400 с.
- Збірник показників емісії (питомих викидів) забруднюючих речовин в атмосферне повітря різними виробництвами, т.1. – Донецьк: Український науковий центр технічної екології, 2004. – 184 с.
- Программа охраны и оздоровления атмосферного воздуха города Донецка. [Электронный ресурс] – Режим доступа: http://doneco.org.ua.
- ОНД-86. Госкомгидромет. Методика расчёта концентраций в атмосферном воздухе вредных веществ, содержащихся в выбросах предприятий. – М., 1987. – 82 с.
- Науково-технічний розвиток Донецької області у сфері охорони навколишнього середовища, екологічної безпеки та відтворення природних ресурсів на період до 2020 року [Електронний ресурс] / Донецьк. – Режим доступу: http://doneco.org.ua.
- Пылегазовые выбросы предприятий черной металлургии. Андоньев С.М., Зайцев Ю.С., Филипьев О.В. – Харьков: Металлургия, 1998. – 247 с.
- Бирман Ю.А, Вурдова Н.Г. Инженерная защита окружающей среды. – М.: АСВ, 2002. – 296 с.