Реферат за темою випускної роботи
Зміст
- Вступ
- 1. Актуальність, мета и задачі дослідження
- 2. Технологічні особливості мартенівського виробництва сталі
- 3. Технологічні особливості електросталеплавильного виробництва
- 4. Порівняльний аналіз питомих викидів забруднюючих речовин мартенівського і електросталеплавильного виробництва
- 5. Оцінка кількісного та якісного складу викидів забруднюючих речовин при різних режимах роботи електросталеплавильних печей
- 6. Аналіз можливих методів очищення газів, що відходять електросталеплавильного виробництва
- 7. Розрахунок розсіювання викидів забруднюючих речовин в атмосферному повітрі для мартенівського цеху ПрАТ
Донецьксталь
-МЗ - 8. Дослідження рівня забруднення атмосферного повітря в районі розташування мартенівського сталеплавильного цеху за даними спостереження прилеглих стаціонарних постів контролю
- Висновки
- Список джерел
Вступ
До числа найбільш актуальних проблем міста Донецька належить забруднення атмосферного повітря, яке є причиною виникнення великої кількості різних захворювань у жителів міста. Негативний вплив на стан атмосферного повітря справляють промислові підприємства, в число яких входять підприємства металургії.
Одним з провідних підприємств, що спеціалізуються на випуску високоякісної сталі, є ПрАТ Донецьксталь
– металургійний завод. Випуск сталі на даному підприємстві здійснюється у фізично та морально застарілих мартенівських печах, які не обладнані системами газоочистки. Внаслідок цього при роботі мартенівських печей в атмосферне повітря надходить велика кількість забруднюючих речовин. За величиною валових викидів ПрАТ Донецьксталь
-МЗ довгі роки займає одне з перших місць серед підприємств міста Донецька. На рисунку 1 наведена діаграма викидів забруднюючих речовин в цілому по м. Донецьку і мартенівським цехом ПрАТ Донецьксталь-МЗ
[1].
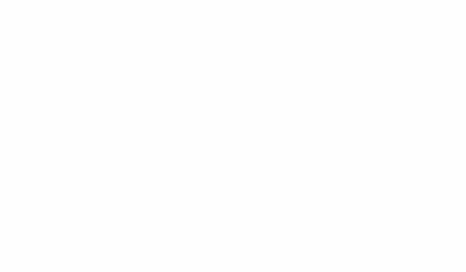
Рисунок 1 – Потужність викидів забруднюючих речовин
Аналіз даних діаграми показує, що мартенівський цех ПрАТ Донецьксталь
-МЗ робить істотний внесок у забруднення атмосферного повітря пилом (потужність викидів становить 33% від загальноміського показника) і оксидами азоту (потужність викидів становить 40%).
Слід зазначити, що дані речовини є пріоритетними забруднювачами для м. Донецька, зокрема, за величиною екологічного ризику оксиди азоту займають друге місце серед забруднюючих речовин, а пил – четверте (величини екологічного ризику для даних речовин становлять відповідно 3,96*10-3 і 2,28*10-4).
Таким чином, виробництво сталі в застарілих мартенівських печах, що працюють без пилогазоочисних установок, має сильний негативний вплив на стан атмосферного повітря, і тим самим сприяє зростанню рівня захворюваності населення. Одним з можливих способів зниження техногенного навантаження на атмосферне повітря міста є заміна мартенівського способу виробництва сталі на електросталеплавильний, що дозволить суттєво зменшити викиди забруднюючих речовин.
1. Актуальність, мета та задачі дослідження
В даний час в м. Донецьку на підприємстві ПрАТ Донецьксталь
-металургійний завод реалізується програма по заміні мартенівського виробництва сталі на електросталеплавильний. Виплавка сталі на даному підприємстві буде проводитися в сучасній електросталеплавильній печі.
Внаслідок зміни типу печі та технології виплавки сталі відбудеться значна кількісна та якісна зміна складу викидів забруднюючих речовин підприємства. Зокрема, істотно знизяться викиди пилу та оксидів азоту, які є пріоритетними забруднювачами для міста. У той же час, при роботі електросталеплавильних печей в атмосферне повітря надходять такі забруднюючі речовини, як ціаніди, фториди, діоксини та фурани. Таким чином, вплив мартенівського і електросталеплавильного виробництва на стан атмосферного повітря істотно відрізняється.
Метою магістерської роботи є порівняльний аналіз впливу мартенівського і електросталеплавильного виробництва на стан атмосферного повітря.
Задачи исследования:
- аналіз технологічних особливостей мартенівського і електросталеплавильного виробництв;
- оцінка кількісного та якісного складу викидів забруднюючих речовин при різних режимах роботи мартенівських і електросталеплавильних печей;
- аналіз можливих методів очищення газів, що відходять, для даних виробництв;
- розрахунок розсіювання викидів забруднюючих речовин в атмосферному повітрі та визначення зони впливу сталеплавильних цехів;
- дослідження рівня забруднення атмосферного повітря в районі розташування мартенівського сталеплавильного цеху за даними спостереження прилеглих стаціонарних постів контролю;
- розрахунок вкладу мартенівського виробництва у формування фонових концентрацій забруднюючих речовин в атмосферному повітрі;
- визначення залежності концентрацій забруднюючих речовин в атмосферному повітрі в зоні впливу мартенівського цеху від його потужності викидів;
- розрахунок потужності викидів забруднюючих речовин від електросталеплавильного цеху;
- розрахунок екологічних ризиків.
2. Технологічні особливості мартенівського виробництва сталі
Мартенівська піч представляє собою полум'яну регенеративну піч для переробки чавуну і сталевого брухту в сталь заданого хімічного складу та якості.
Мартенівська піч складається з наступних основних частин (рисунок 2): робочого простору (подина, передня і задня стінки, звід), де здійснюється плавка; головок (правої і лівої), що складаються з власне головок і вертикальних каналів для подачі палива і повітря в робочий простір і відведення з нього продуктів згоряння; шлаковиків (повітряних і газових) – для осадження та накопичення пилу і частинок шлаку, що випадають з продуктів згоряння, які проходять через них; регенераторів (повітряних і газових) – для підігріву газу і повітря, що надходять в піч теплом продуктів згоряння, які виходять з робочого простору; кнурів (каналів) для повітря, газу та продуктів згоряння; системи перекидних клапанів, призначених для зміни напрямку подачі в піч палива і повітря та відводу з робочого простору продуктів згоряння; котла-утилізатора; димової труби. Робочий простір і головки печі розташовані вище робочого майданчика цеху і умовно називаються верхньою будовою печі. Інші частини знаходяться під робочим майданчиком і називаються нижньою будовою [2].
Мартенівська піч має симетричну будову: права і ліва її сторони щодо вертикальної осі однакові по пристрою.
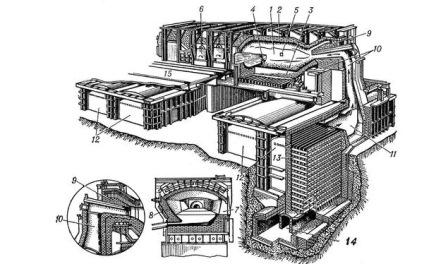
1 – робочий простір; 2 – звід, 3 – подина, 4 – сталевипускний отвір; 5 – отвір для спуску шлаку; 6 – завалочні вікна; 7 – передня стінка, 8 – задня стінка; 9 – головки; 10 – вертикальні канали; 11 – шлаковик; 12 – регенератори: 13 – насадка регенераторів; 14 – борови; 15 – робочий майданчик
Рисунок 2.1 – Устрій мартенівської печі
У мартенівському процесі виплавки стали розрізняють такі періоди: заправка печі, завалення і прогрівання шихти, заливка рідкого або завалення твердого чавуну, плавлення, кипіння, розкислення і легування, випуск.
Заправка печі необхідна для підтримки в робочому стані всіх елементів кладки плавильного простору. Заправка печі полягає в тому, що після випуску з печі металу і шлаку подину ретельно оглядають і, якщо потрібно, виправляють відмічені нерівності.
Завалка шихти здійснюється машиною завалення. Всі тверді шихтові матеріали подаються до печі в спеціальних коробах – мульдах). Для додаткового підігріву всього сталевого брухту перед заливкою в піч чавуну проводять прогрівання шихти, після чого відбувається заливка рідкого або завалення твердого чавуну.
Період плавлення починається відразу після закінчення заливки (завалки) чавуну і триває 1-5 год. У піч в цей період подається максимальна кількість палива, ванна продувається киснем. В процесі заливки чавуну і в перший момент плавлення відбувається інтенсивне утворення шлаку, до складу якого входять оксиди заліза, кальцію, кремнію, марганцю, фосфору, а також руйнуються вогнетриви кладки печі, флюси і домішки, що вносяться шихтою. Товстий шар шлаку, що утворився, ускладнює передачу тепла від факела до металу. У зв'язку з цим в першій половині плавлення з печі видаляють (шляхом спуску в шлакові чаші) деяку кількість шлаку [3].
Хімічний склад металевої ванни в момент повного розплавлення помітно відрізняється від складу, який сталь повинна мати перед випуском плавки; температура металу відносно невисока. Тому головне призначення наступних періодів плавки, які мають назву доведення
, полягає в тому, щоб забезпечити необхідний нагрів металу, доведення його до заданого хімічного складу.
У зв'язку з цим період кипіння – найбільш відповідальний період мартенівської плавки. Головною реакцією цього періоду є реакція окислення розчиненого в рідкому металі вуглецю. Утворені в результаті цієї реакції бульбашки оксиду вуглецю вириваються на поверхню металу, пробивають шар шлаку і, виходячи на його поверхню, створюють враження кипіння ванни.
Період кипіння умовно поділяють на 2 частини – період рудного кипіння, коли в піч вводять добавки руди (кисень), вапна, флюсів, і період чистого кипіння, коли окислення розчиненого в металі вуглецю продовжується без яких-небудь добавок, за рахунок розчиненого в шлаку і металі кисню. В період чистого кипіння відбувається остаточне доведення металу до необхідних температури і хімічного складу.
Розкислювання і легування – завершальний період плавки, основне призначення якого полягає в зниженні вмісту кисню в металі і доведенні складу металу до заданого за змістом всіх елементів, включаючи легуючі. Розкислюючі і легуючі добавки залежно від виплавлюваної марки стали вводять або в піч, або в сталеплавильний ківш під час випуску металу [4].
Для випуску металу з печі з боку задньої стінки пробивають або пропалюють струменем газоподібного кисню стале випускний отвір; метал по жолобу стікає у встановлений під ним сталерозливний ківш. З ковша метал розливають до ізложниць або на установках безперервного розливання сталі.
Головним достоїнством мартенівського процесу є можливість його проведення за будь витраті чавуну, а також можливість переробки як рідкого, так і твердого чавуну. Іншою перевагою мартенівських печей є високий вихід сталі, який складає 90-96% металевої завалювання. До переваг мартенівського виробництва сталі також відноситься використання первинної енергії (тепла газоподібного та рідкого палива).
Недоліками мартенівського виробництва є:
- низька продуктивність;
- великі труднощі в синхронізації плавки сталі в мартенівської печі і розливання сталі на машини безперервного лиття заготовок;
- велика витрата вогнетривких матеріалів і палива;
- необхідність ручної праці при ремонтах печей;
- важкі умови праці;
- велика тривалість процесу плавки.
З цих причин мартенівський процес неухильно витісняють киснево-конвертерний і електросталеплавильний.
3. Технологічні особливості електросталеплавильного виробництва
Електросталеплавильне виробництво – виробництво сталі в електричних (головним чином дугових) печах. Дозволяє отримувати сталі широкого сортаменту (від рядових до високоякісних) при масі плавки від декількох десятків кілограм до 200 т і вище. Електросталеплавильне виробництво має суттєві переваги перед іншими способами одержання сталі, і його питома вага у світовому виробництві сталі безперервно зростає.
Виплавку стали даним способом здійснюють в дуговій сталеплавильній печі (рисунок 3). Розрізняють сталеплавильні печі постійного і змінного струму [5].
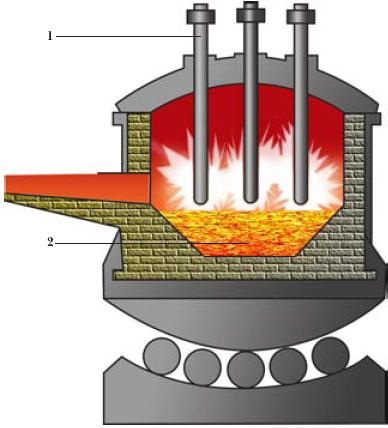
1 – електроди, 2 – метал
Рисунок 3.1 – Дугова електросталеплавильна піч
Дугова піч складається з робочого простору (фактично печі) з електродами і струмопідведенням, а також пристроїв, що забезпечують нахил печі, утримання та переміщення електродів і завантаження шихти.
Плавку стали ведуть в робочому просторі, обмеженому зверху куполоподібним склепінням, знизу сферичним подом і з боків стінами.
Плавка сталі в дугових сталеплавильних печах, після огляду печі та ремонту постраждалих ділянок футеровки (заправка), починається з завалки шихти. Шихту в печі завантажують зверху за допомогою завантажувальної бадді (кошика). Для запобігання подини від ударів великими шматками шихти на дно бадді завантажують дрібний лом. Для раннього шлакоутворення в завалку вводять вапно у кількості 2-3% від маси металевої шихти.
Після закінчення завалювання в піч опускають електроди, включають високовольтний вимикач і починають період плавлення. Під дією високої температури дуг шихта під електродами плавиться, рідкий метал стікає вниз, накопичуючись в центральній частині подини. У міру збільшення кількості рідкого металу електроди піднімаються. Плавлення ведуть при максимальній потужності пічного трансформатора. Під час плавлення відбувається окислювання складових шихти, формується шлак, відбувається часткове видалення в шлак фосфору і сірки. Окислення домішок здійснюється за рахунок кисню повітря, окалини та іржі, внесених металевої шихтою [6].
За час плавлення повністю окислюється кремній, 40 – 60 % марганцю, частково окислюється вуглець і залізо. Шлак близько к кінцю періоду плавлення має приблизно наступний склад, %: 35-40 CaO; 15-25 SiO2; 8-15 FeO; 5-10 MnO; 3-7 Al2O3; 0,2 P2O5. Тривалість періоду плавки визначається потужністю трансформатора і становить від 1 години.
Окислювальний період починається з того, що з печі зливають 65-75 % шлаку, що утворився в період плавлення. Злив шлаку виробляють для того, щоб видалити з печі фосфор, який перейшов в шлак.
Присадку руди протягом окислювального періоду здійснюють для інтенсивного кипіння ванни – окислюється вуглець, реагуючи з оксидами заліза руди з виділенням великої кількості бульбашок СО. При цьому відбувається дегазація металу та його перемішування, що прискорює процеси дефосфорації і нагріву. При кипінні разом з бульбашками СО з металу також видаляються водень і азот.
Після формування шлаку в ванні протягом усього окислювального періоду ведуть продувку киснем. Піч для зливу шлаку в протягом даного періоду нахилена в бік робочого вікна. Під впливом газів шлак спінюється, рівень його підвищується, і він стікає в жужільну чашу через поріг робочого вікна.
Шлак наприкінці окислювального періоду має приблизно наступний склад, %: 35-50 CaO; 10-20 SiO2; 4-12 MnO; 6-15 MgO; 3-7 Al2O3; 6-30 FeO; 2-6 Fe2O3; 0,5 P2O5.
Окислювальний період закінчується тоді, коли вуглець окислюється до нижньої межі його змісту в виплавленій марці стали, а вміст фосфору знижено до 0,015 %. Повне скачування окисного шлаку необхідно, щоб фосфор, який міститься в ньому, не перейшов назад в метал під час відновного періоду [7].
4. Порівняльний аналіз питомих викидів забруднюючих речовин мартенівського і електросталеплавильного виробництва
Кількісний і якісний склад викидів забруднюючих речовин при проведенні процесу виплавки стали залежить від технології виплавки сталі і від ємності печі. У таблиці 1 наведена порівняльна характеристика питомих викидів забруднюючих речовин для мартенівських печей, що діють на ПрАТ Донецьксталь
-МЗ (однованні печі ємністю 100 т, в яких не застосовується продування киснем), і для електросталеплавильної печі ємністю 150 т, яка буде встановлена замість мартенівських [8].
Таблица 4.1 – Потужність викидів забруднюючих речовин під час проведення мартенівського та електросталеплавильного процесу
Назва забруднюючої речовини | Питомі викиди забруднюючих речовин, кг / т сталі | |
мартенівське виробництво | електросталеплавильне виробництво | |
1 організовані викиди | ||
Пил | 11,33 | 9,40 |
Оксиди азоту | – | 0,27 |
Оксид вуглецю | – | 1,35 |
Діоксид сірки | – | 0,0016 |
Ціаніди | – | 0,0284 |
Фториди | – | 0,00056 |
2 Неорганізовані викиди | ||
Пил | 6,516-7,575 | 0,68-1,38 |
Оксиди азоту | 0,5 | – |
Оксид вуглецю | 4,084-0,499 | – |
Діоксид сірки | 0,0204 | – |
3 Викиди важких металів, г / т сталі | ||
Кадмій | 0,80 | 0,52 |
Свинець | 35,30 | 12,90 |
Мідь | 1,53 | 2,70 |
Ртуть | – | 0,012 |
Нікель | 0,33 | 0,48 |
Цинк | 52,10 | 176,50 |
Аналіз даних таблиці показує, що питомі викиди пилу, оксидів азоту, діоксиду сірки, кадмію і свинцю мають більші значення для мартенівського виробництва, а питомі викиди міді, нікелю та цинку більші при електросталеплавильному виробництві. Також слід зазначити, що у викидах електросталеплавильного виробництва присутні такі токсиканти, як ртуть, ціаніди і фториди, нехарактерні для мартенівського виробництва.
5. Оцінка кількісного та якісного складу викидів забруднюючих речовин при різних режимах роботи електросталеплавильних печей
У зв'язку зі складними фізико-хімічними процесами, що відбуваються під час виплавки сталі, цей процес супроводжується інтенсивним утворенням газів, в яких містяться оксиди вуглецю, оксиди азоту, оксид сірки, пил, а також невелика кількість ціанідів, сірчистого ангідриду і фторидів. Концентрація даних забруднюючих речовин у відхідних газах залежить від періоду плавки, способу її інтенсифікації та різко змінюється в межах однієї плавки.
На рисунку 4 наведені дані про вміст ціаністих сполук (крива 1), оксидів азоту (крива 2), оксиду вуглецю (ІІ) (крива 3), а також пилу (крива 4) у газах, що відходять, при нормальних умовах для роботи печі ДСП-100. Загальний час циклу такій печі складає 2 години 15 хвилин, а середній обсяг газів, що відходять – 8000 м3/год [9].
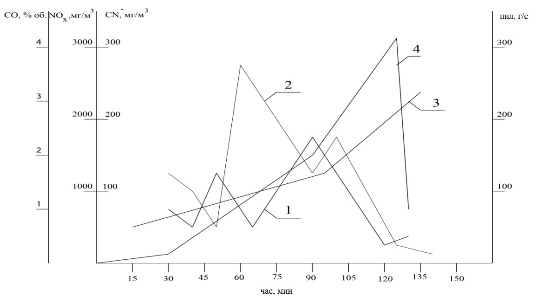
Рисунок 5.1 – Залежність викидів забруднюючих речовин від часу роботи електропечі для одного циклу
На підставі представлених даних в програмі ЕОЛ + був проведений розрахунок розсіювання викидів забруднюючих речовин для печі ДСП-100 в 4 точках: 50 хв., 60 хв. (максимум для концентрації діоксиду азоту), 90 хв. (максимум для концентрації ціаністих сполук), 125 хв. (максимум пиловиділення).
В результаті проведення даного розрахунку були визначені концентрації аналізованих забруднюючих речовин в атмосферному повітрі та їх концентрації на межі санітарно-захисної зони, яка становить 1000 м.
Як показали розрахунки, максимальні значення для всіх розглянутих речовин спостерігаються на відстані 1100 м від джерела і тому практично збігаються зі значеннями концентрацій на межі СЗЗ.
Аналіз результатів розрахунку показав, що концентрації NO2 і HCN досягають найбільших значень (0,430 і 0,023 ГДК відповідно) при розсіюванні викидів, які утворюються під час плавлення, коли температура максимальна. Для оксиду вуглецю та пилу спостерігається зростання концентрації забруднюючих речовин протягом процесу. При цьому, якщо для СО в кінці процесу концентрація на СЗЗ становить 0,12 ГДК, то для пилу перевищує нормативні в 3,62 рази..
Таким чином, при визначенні концентрації забруднюючих речовин в атмосферному повітрі більш доцільно використовувати не середні значення потужності викидів, а їх пікові значення.
6 Аналіз можливих методів очищення газів, що відходять електросталеплавильного виробництва
Газ, що виділяється з електросталеплавильної печі, має такий хімічний склад,% (об'ємн): СО < 68; СО2 < 30; О2 < 21; N2 30-79. Концентрація пилу становить 50-60 г/м3, він складається з оксидів заліза, кремнію, алюмінію, марганцю, кальцію. Температура газу на виході з печі складає близько 1600 °С.
Внаслідок наявності в газі вибухонебезпечного оксиду вуглецю (СО), перед направленням на очистку оксид вуглецю допалюють в спеціальному пристрої.
Гази, що відходять, очищають в сухому пластинчастому електрофільтрі або в тканинному рукавні фільтри, оскільки серед поширених сухих способів очищення промислових газів від пилу найбільша ефективність уловлювання тонкодисперсних частинок (до 5 мкм) досягається практично тільки при використанні рукавних фільтрів і електрофільтрів.
Провідний стан в даний час займають рукавні фільтри. При збільшенні коефіцієнта пиловловлення від 98 до 99 % вартість електрофільтрів значно зростає (приблизно на 20%), в той час як вартість рукавних фільтрів і обсяг споживаної ними енергії зі збільшенням ефективності пиловловлення не змінюються, що робить їх найбільш привабливими з точки зору експлуатації.
Установки пиловловлення із застосуванням електрофільтрів характеризуються меншим енергоспоживанням, але для їх спорудження потрібні значні капітальні витрати. При цьому, електрофільтри чутливі до параметрів газів, що очищаються, при їх коливанні може знижуватися ефективність апаратів.
Електрофільтри застосовуються при температурах газів до 300-400 ?С і є найбільш економічними при обсягах газів більше 500 тис. м3 / год. У той же час, фахівці не рекомендують застосовувати електрофільтри при необхідності отримання запиленості газу на виході менше 500-100 мг/м3. Ступінь очистки газів в електрофільтрах досягає 98 %. При використанні електрофільтрів пред'являються достатньо високі вимоги безпеки, оскільки велика ймовірність ураження працівників електрострумом у разі недотримання вимог охорони праці при їх експлуатації. Тому рукавні фільтри мають певну перевагу перед електрофільтрами.
При використанні рукавних фільтрів забезпечується залишкова запиленість нижче 5-10 мг/м3 незалежно від властивостей пилу; робота проводиться в широкому діапазоні очищуваного газу. Ступінь очищення становить 99 % і більше, особливо пилу з високим електричним опором, уловлювання якого в електрофільтрах відбувається недостатньо повно. Витрата енергії становить 2-2,5 кВт / год на 1000 м3 газів, що очищаються. Низькі капітальні витрати і помірні експлуатаційні витрати – ще одна перевага таких пристроїв. Застосування синтетичних тканин як фільтрувальних матеріалів для фільтрів дозволяє використовувати їх при температурах вище 140 ?С. При цьому, такі тканини довговічніші в порівнянні з натуральними вовняними і бавовняними тканинами.
Особливий інтерес представляють рукавні фільтри з імпульсною продувкою. Вони застосовуються для очищення газів обсягом 500 тис. м3 і більше і температурах близько 150 ?С з використанням синтетичних фільтрувальних матеріалів, що забезпечує високий ступінь очищення при значних питомих навантаженнях (46 м3/кВ*м*хв). Іншими перевагами таких фільтрів є відсутність рухомих частин, простота обслуговування, надійність дії і тривалий термін служби рукавів (до 20-24 місяців) [10].
7 Розрахунок розсіювання викидів забруднюючих речовин в атмосферному повітрі для мартенівського цеху ПрАТ Донецьксталь
-МЗ
На основі даних інвентаризації джерел викидів ПрАТ Донецьксталь
-МЗ в програмі ЕОЛ+ був проведений розрахунок розсіювання викидів забруднюючих речовин мартенівського цеху підприємства. Отримані результати показали, що на границі санітарно-захисної зони підприємства спостерігаються такі концентрації забруднюючих речовин, в долях ГДК:
- Оксид заліза (в перерахунку на залізо) – 0,15;
- Оксид кадмію (у перерахунку на кадмій) – 0,025;
- Марганець та його сполуки (у перерахунку на діоксид марганцю) – 1,03;
- Оксид міді (в перерахунку на мідь) – 0,0058;
- Нікель металевий – 0,0041;
- Свинець та його сполуки (у перерахунку на свинець) – 3,34;
- Хром шестивалентний (в перерахунку на триоксид хрому) – 0,039;
- Цинк та його сполуки (у перерахунку на цинк) – 0,0099;
- Діоксид азоту – 3,33;
- Діоксид сірки – 0,12;
- Оксид вуглецю – 0,41;
- Пил неорганічний – 0,22.
Таким чином, можна зробити висновок? що на границі СЗЗ підприємства порушуються нормативи ГДК для марганцю та його сполук (у перерахунку на діоксид марганцю), свинцю та його сполук (у перерахунку на свинець), а також для діоксид у сірки.
8 Дослідження рівня забруднення атмосферного повітря в районі розташування мартенівського сталеплавильного цеху за даними спостереження прилеглих стаціонарних постів контролю
У зоні впливу ПрАТ Донецьксталь
-МЗ розташовано пост спостереження і контролю атмосферного повітря № 4. На даному пості аналізується концентрація таких забруднюючих речовин як пил, діоксид сірки, оксид вуглецю, діоксид азоту. На рисунку 5 представлена динаміка рівня забруднення атмосферного повітря за останні 11 років за даними спостереження поста № 4.
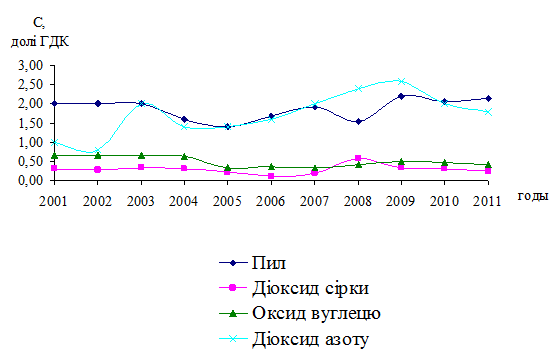
Рисунок 8.1 – Динаміка зміни концентрації забруднюючих речовин на пості спостереження № 4
Аналіз графіка дозволяє зробити висновок про те, що протягом всього аналізованого періоду спостереження на даному пості концентрація оксиду вуглецю і діоксиду сірки в атмосферному повітрі не перевищувала нормативів ГДК, в той час як по пилу та діоксиду азоту спостерігалися значні перевищення ГДК. Концентрації даних речовин досягла максимуму в 2009 році і склала 2,2 ГДК для пилу і 2,6 ГДК для діоксиду азоту.
Висновки
Мартенівський цех ПрАТ Донецьксталь
-МЗ робить істотний вплив на стан атмосферного повітря міста, зокрема, викиди пилу даного цеху складають 33% від загальноміського показника, а діоксиду азоту – 40%. Саме по цим речовинам спостерігається значне перевищення нормативів ГДК на пості спостереження і контролю атмосферного повітря, розташованого в зоні впливу підприємства.
Значні обсяги викидів забруднюючих речовин даними цехом обумовлені тим, що виплавка сталі в ньому виробляється в фізично і морально застарілих мартенівських печах, які не обладнані пилогазоочисними установками.
Але в даний час на підприємстві реалізується програма по заміні мартенівського виробництва сталі на електросталеплавильний. Для електросталеплавильного виробництва характерні значно менші питомі викиди таких забруднюючих речовин, як пил, діоксид азоту, діоксид сірки, кадмій і свинець. Також слід зазначити, що електросталеплавильний цех буде обладнаний сучасними пилоочисного установками – рукавними фільтрами, ефективність очищення яких становить 99%.
Таким чином, заміна мартенівського способу виробництва сталі на електросталеплавильний дозволить істотно знизити викиди забруднюючих речовин і зменшити техногенне навантаження на атмосферне повітря міста.
Список источников
- Звіт про стан навколишнього природного середовища в м. Донецьк у 2006 році. – Донецьк, 2003. – 152 с.
- Доклад о состоянии окружающей природной среды города Донецка в 2004 – 2005 годах. – Донецк, 2006. – 72 с.
- Брыгинец Н.Г., Батманов А. И. Защита воздушного и водного бассейнов от выбросов металлургических заводов. – М.: Металлургия, 1980. – 48 с.
- Газоочистные установки и аппараты в металлургическом производстве. Ученик для вузов. – М.: Металургія, 1990. – 400 с.
- Збірник показників емісії (питомих викидів) забруднюючих речовин в атмосферне повітря різними виробництвами, т.1. – Донецьк: Український науковий центр технічної екології, 2004. – 184 с.
- Программа охраны и оздоровления атмосферного воздуха города Донецка. [Электронный ресурс] – Режим доступа: http://doneco.org.ua.
- ОНД-86. Госкомгидромет. Методика расчёта концентраций в атмосферном воздухе вредных веществ, содержащихся в выбросах предприятий. – М., 1987. – 82 с.
- Науково-технічний розвиток Донецької області у сфері охорони навколишнього середовища, екологічної безпеки та відтворення природних ресурсів на період до 2020 року [Електронний ресурс] / Донецьк. – Режим доступу: http://doneco.org.ua.
- Пылегазовые выбросы предприятий черной металлургии. Андоньев С.М., Зайцев Ю.С., Филипьев О.В. – Харьков: Металлургия, 1998. – 247 с.
- Бирман Ю.А, Вурдова Н.Г. Инженерная защита окружающей среды. – М.: АСВ, 2002. – 296 с.