Реферат по темі випускної роботи
Зміст
- Вступ
- 1. Актуальність теми
- 2. Мета та завдання дослідження
- 3. Структура та особливості роботи ГТД ТВ3–117
- 4. Особливості синтезу композиційних технологій для ремонту та відновлення лопаток ГТД
- 4.1 Класифікація лопаток
- 4.2 Види пошкодження лопаток
- 4.3 Існуючі технології ремонту та відновлення лопаток ГТД
- Висновки
- Список джерел
Вступ
В сучасному машинобудуванні в умовах гострої конкуренції на українському та світовому ринках особливу актуальність для двигунобудівних підприємств має проблема випуску конкурентно спроможної продукції. При цьому необхідно враховувати якість своєї продукції, стислі терміни і вартість виробу[1].
Однією з найважливіших завдань вдосконалення авіаційних двигунів є підвищення їх надійності та ресурсу.
Надійність газотурбінних двигунів в значній мірі залежить від надійності роботи лопаток компресора і турбіни, оскільки вони є найбільш навантаженими деталями. Лопатки піддаються дії статичних, динамічних та циклічних навантажень, крім того, лопатки турбіни відчувають циклічні, термічні напруги, вони працюють в умовах агресивного газового середовища при високій температурі та піддаються газовій корозії [2]. Лопатки ГТД мають складну просторову геометрію і виготовляються з важко-деформівних матеріалів: жароміцних, титанових і алюмінієвих сплавів. До них пред'являються підвищені вимоги, такі як: за структурою металу, його хімічного складу, механічних властивостей, геометричних розмірів, виключення дефектів (закови, простріли, перепал, прижоги та т.д.) [1].
1. Актуальність теми
Тому збільшення працездатності лопаток газотурбінного двигуна, які при дії знакозмінних навантажень та відцентрових сил, є актуальною проблемою сучасності, яка може вирішуватися комплексної обробкою на останні операції технологічного процесу. Підвищення експлуатаційних характеристик на етапі їх виробництва є розробка та впровадження прогресивних фінішних технологій, які забезпечують значний внесок в якість виготовлення виробу, а отже, і у підвищення його ресурсу та надійності [3].
Газотурбінні двигуни виходять з експлуатації після закінчення ресурсу працездатності лопаток. Бувають випадки коли пошкодження лопаток незначні, тоді необхідно їх відновлювати. В основному відновному ремонту підлягають лопатки у яких пошкоджена передня кромка.
Складність відновлювального ремонту пошкоджених лопаток в тому, що розташування, розмір і форма сколів в кожному конкретному випадки унікальна. Тому, кожен випадок відновлювального ремонту лопатки вимагає індивідуального підходу.
В даній роботі запропоновано спосіб підвищення якості відновлювального ремонту лопаток, ГТД ТВ3–117, на основі спеціальних композиційних технологій, які базуються на композиції основних особливостей та принципів синтезу комбінованих (гібридних), макро-, мікро-, і нанотехнологій, функціонально-орієнтованих технологій. Ці технології відносяться до нового класу організаційно-технологічних форм технологій. На базі цих технологій забезпечується якісно нова сукупність властивостей виробів [4]. Також будуть розглянуті методи ремонту та відновлення лопаток, класифікація лопаток, розроблений прогресивний технологічний процес відновлення та ремонту лопаток та спроектовано пристосування для нанесення вакуумного іонно-плазмового покриття.
Наукова цінність роботи
Наукова цінність полягає у встановленні закономірностей між операціями і створення раціональної структури технологічного процесу ремонту та відновлення лопаток ГТД ТВ3–117.
Практичне значення роботи
Практичне значення полягає в тому, що при підвищенні якості лопаток ГТД, підвищується їх довговічність, зносостійкість та збільшується їх термін експлуатації.
2. Мета та завдання дослідження
На підставі вищесказаного поставлена мета роботи:
Підвищення якості ремонту та відновлення лопаток газотурбінного двигуна ТВ3–117, за рахунок удосконалення технологічного забезпечення синтезу композиційних технологій.
На підставі поставленої мети, визначено основні задачі роботи:
- Провести аналіз сучасного стану технологічного забезпечення процесів ремонту та відновлення лопаток газотурбінного двигуна ТВ3–117, на підставі синтезу композиційних технологій;
- Дослідити можливості підвищення довговічності лопаток ГТД ТВ3–117 шляхом нанесення вакуумних іонно-плазмових покриттів;
- Розробити прогресивний технологічний процес ремонту та відновлення лопаток ГТД ТВ3–117;
- Спроектувати пристосування для нанесення вакуумного іонно-плазмового покриття;
- Виконати експерименти з дослідження властивостей зносостійкого вакуумного іонно-плазмового покриття;
- Розробити рекомендації щодо вдосконалення технологічного забезпечення процесів ремонту та відновлення лопаток ГТД ТВ3–117.
Наукова новизна:
- Встановити зв'язок закономірності між операціями структури композиційного технологічного процесу для ремонту та відновлення лопаток ГТД ТВ3–117;
- Розробити раціональну структуру технологічного процесу для нанесення вакуумних іонно-плазмових покриттів.
Об'єкт дослідження:
Композиційний технологічний процес ремонту та відновлення лопаток ГТД
Предмет дослідження:
Встановлення зв'язку закономірності між операціями технологічного процесу ремонту та відновлення лопаток ГТД
3. Структура та особливості роботи ГТД ТВ3–117
Розглянуто двигун ТВ3–117 (рис. 1), який був створений на якісно новому рівні ніж газотурбінні двигуни (ГТД) другого покоління. При його впровадженні вперше в СРСР були освоєні такі прогресивні технологічні процеси, як електронно-променеве зварювання і холодна вальцювання лопаток компресора, які згодом ввели в конструкції всіх без винятку вітчизняних ГТД. У порівнянні зі своїм попередником ТВ2–117, двигун має більшу на 30% злітну потужність при менших габаритах та масі [5]. Принцип дії такого двигуна – стиснуте атмосферне повітря з компресора поступає в камеру згорання, туди ж подається паливо, яке, згораючи, утворює велику кількість продуктів згоряння під високим тиском. Потім в газовій турбіні енергія газоподібних продуктів згорання перетворюється в механічну роботу за рахунок обертання струменем газу лопаток, частина якої витрачається на стиснення повітря в компресорі. Інша частина роботи передається на привід агрегату.Робота, затрачена цим агрегатом, є корисною роботою ГТД. [11].
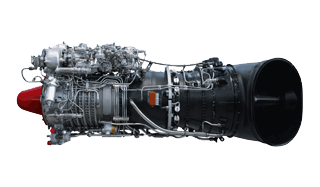
Рисунок 1 – Газотурбінний турбовальний двигун ТВ3–117
Розробка турбовального двигуна ТВ3–117 для вертольота Ми–24 (рис.2) почалась в ОКБ ім. В.Я. Климова під керівництвом С.П. Ізотова у 1965 році. Вперше у вітчизняному двигунобудуванні було вирішено застосувати на двигуні титановий ротор компресора, зварений з окремих дисків електронно-променевим зварюванням, робочі та направляючі лопатки компресора з титанового сплаву, отримані методом холодного вальцювання, малогабаритні контактні графітові ущільнення масляних порожнин. У порівнянні з ТВ2–117 новий двигун вийшов потужнішим на 30% при менших габаритах і масі. У 1972 році він пройшов державні випробування. В цьому ж році почалося його серійне виробництво на Запорізькому заводі Моторобудівник
[6].
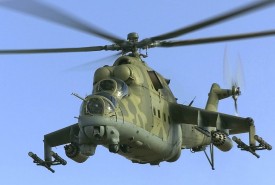
Рисунок 2 – Транспортно-бойовий вертоліт МИ–24
ТВ3–117 складається з 12-ступеневого осьового компресора з регульованим вхідним направляючим апаратом та направляючого апаратаму з 4 ступенів, кільцевої камери згоряння, двоступеневої турбіни компресора та двоступеневої вільної турбіни. Встановлено пилозахисний пристрій [6]. У системі регулювання використані електронні блоки. Двигун працює на авіаційному керосині марок Т–1, ТС–1, РТ. Масляна система використовує синтетичне масло Б–3В.
Двигун ТВ3–117 є одним з кращих в світі по економічності у своєму класі, що було досягнуто високим ККД агрегатів (компресора – 86%, турбіни компресора – 91%, вільної турбіни – 94%). Він успішно експлуатується як в морських, арктичних, так і в тропічних кліматичних умовах [6].
За ступенем досконалості ТВ3–117 відноситься до третього покоління двигунів по світовій класифікації. При його розробці були застосовані раціональні прийоми конструювання, нові технологічні процеси, велика увага приділялася зменшенню металоємності. Найважливішими нововведеннями, запровадженими при створенні ТВ3–117, були [7]:
- застосування регульованих напрямних апаратів перших чотирьох ступенів та вхідного направляючого апарату, що дозволило добре узгодити роботу окремих ступенів та отримати високий ККД (максимальне значення 86%) і високий запас стійкості (майже 22%);
- виготовлення робочих лопаток компресора методом холодного вальцювання, а лопаток напрямних апаратів – методом протягування. Метод вальцювання лопаток дозволив відмовитися від трудомісткого фрезерування профільної частини, що застосовувався раніше в двигунобудування. Метод фрезерування не дозволяв виготовляти тонкі профілі, тому доводилося штучно збільшувати їх товщину, а, отже, збільшувати хорду, що призводило до погіршення параметрів та збільшення довжини компресора. З впровадженням методу вальцювання допуск на виготовлення лопатки зменшився більш ніж удвічі, значно підвищилась стабільність параметрів компресора. Так, якщо для двигунів другого покоління розкид в ККД компресорів становив 5 ... 6%, то у ТВ3–117 він знизився до 2,5 ... 3%. Згодом метод вальцювання був впроваджений на всіх без винятку радянських газотурбінних двигунах;
- застосування валків робочих лопаток турбін з лабіринтовими гребінцями на полицях та металокерамічними вставками, що забезпечило високі ККД турбіни компресора – 91% (розрахунковий – 90%) та силової турбіни – 93,4% (розрахунковий – 90%);
- використання в кріпленні робочих лопаток турбін двухзубого замку замість зазвичай застосовувалися три- або четирехзубих, що дозволило відмовитися від кріпильних фланців та деталей, підвищити жорсткість конструкції і зменшити її масу;
- застосування в турбінах суцільнолитих соплових апаратів, що забезпечило високу жорсткість конструкції, високий коефіцієнт використання металу і мінімальну масу, скоротилася в порівнянні з розбірної конструкцією майже на 25%;
- впровадження камери згоряння кільцевого типу, в якій теплонапруженість перевищувала рекомендовані значення, що дозволило скоротити довжину камери та всього двигуна;
- розміщення паливного колектора всередині камери згоряння, що дало виграш в його масі в порівнянні з конструкцією двигуна типу ТВ2–117 майже на 40%;
- застосування контактних графітових ущільнень, скоротили витоку повітря майже вдвічі;
- широке використання титану, з якого виконано близько 50% деталей та вузлів (корпус та барабан компресора, корпуси турбін, корпус та дифузор камери згоряння, передня опора компресора, кронштейни тощо), що дозволило значно зменшити масу двигуна;
- впровадження точного (прецизійного) лиття, що забезпечило істотний виграш в коефіцієнті використання металу;
- застосування електроннопроменевої та автоматичної зварки, що дозволили значно зменшити масу двигуна і забезпечили високу жорсткість конструкції і високу надійність з'єднань.
Двигун ТВ3–117 може використовуватися крім вертольотів на різних суднах водного транспорту, в якості приводу електрогенераторів та компресорів нефтегазоперекачівающіх станцій. У реактивному варіанті (без модуля вільної турбіни) двигун може застосовуватися для сушіння струменем вихлопних газів приміщень для худоби, будуючихся будівель, здування снігу та льоду на шосейних та залізних дорогах, аеродромах [8].
4. Особливості синтезу композиційних технологій для ремонту та відновлення лопаток ГТД
Композиційна технологія це спеціальна технологія, що базується на композиції принципів та особливостей синтезу різних варіантів технологій, яка дозволяє управляти властивостями виробу і забезпечувати підвищення параметрів його якості за напрямами складу композиції варіантів технологій. У цій технології кількість напрямів підвищення якості виробів визначається числом варіантів технологій, що входять до складу композиційної технології. Зв'язки між етапами проектування в цих технологіях виконуються ітераційні та рекурентні [4].
4.1 Класифікація лопаток
В газотурбінному двигуні ТВ3–117 розрізняють робочі, спрямляючі та поворотні лопатки компресора і турбіни. Крім того, в компресорі є направляючі лопатки та вхідні напрямні лопатки, а в турбіні – соплові лопатки та охолоджувальні [12].
Конструктивні та технологічні особливості робочих лопаток (рис. 3) надають принциповий вплив на газодинамічні характеристики двигунів і стійкість (надійність) їх роботи. Характеристики міцності робочих лопаток також надають принциповий вплив на характеристики надійності, тому що обрив робочих лопаток може привести до нелокалізованого руйнування двигуна та катастрофи. Нелокалізовані відмови через обрив лопаток відносяться до такого типу відмов, за якими двигун повинен задовольняти міжнародним нормам: відірвані частини лопатки (-ок) повинні залишатися всередині корпусу двигуна. Однак необхідно враховувати, що обриви лопаток можуть ініціювати інші важкі відмови: руйнування диска, пожежу та ін. Робочі лопатки турбін працюють при високих температурах, відчувають великі статичні, вібраційні та температурні напруги. Вони піддаються одночасно корозії та ерозії дії газів. Враховуючи важкі умови праці робочих лопаток та їх роль у двигуні (надійність і ресурс лопаток турбін зазвичай визначає надійність і ресурс двигуна), до конструктивних форм робочих лопаток, до способу їх кріплення в диску, до їх матеріалів, технології виготовлення та контролю в експлуатації пред'являють особливо жорсткі вимоги [13].
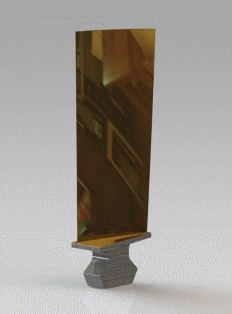
Рисунок 3 – Модель робочої лопатки, розроблена в SolidWorks
Лопатки осьового компресора спрямляючі (рис.4) – нерухомі або поворотні профільовані лопатки, розташовані за робочим колесом ступені осьового компресора та випрямляють (повністю або частково) закручений потік повітря, що виходить з робочого колеса. Лопатки осьового компресора спрямляючі є основним елементом спрямляючого апарату осьового компресора. Нерухомі лопатки кріпляться або безпосередньо до корпусу осьового компресора, або до зовнішнього кільцевого бандажа, який в свою чергу кріпиться до корпусу компресора, або до обох (зовнішньому та внутрішньому) бандажів [14].
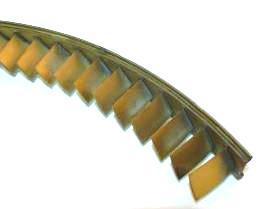
Рисунок 4 – Спрямляючі лопатки на бандажі
Лопатки осьового компресора поворотні (мал. 5) – рухливі лопатки, які можна повертати і цим самим змінювати кут їх установки при роботі двигуна на землі та в польоті. Вони призначені для регулювання компресора на нерозрахованих режимах його роботи головним чином з метою підвищення ККД компресора та забезпечення стійкості його роботи. Поворотні лопатки напрямних апаратів широко застосовуються в одновальних осьових компресорах авіаційних газотурбінних двигунів для полегшення запуску та розгону ротора двигуна, а також для забезпечення стійкості його роботи на рівноважних, але на нерозрахованих режимах. В багатоступеневому осьовому компресорі немає необхідності повертати лопатки напрямних апаратів усіх ступенів. Оскільки режими роботи середніх ступенів мало відхиляються від розрахункового, у багатьох випадках достатньо обмежитися поворотом лопаток напрямних апаратів лише першої та останньої ступені компресора. В деяких випадках відомого ефекту в регулюванні осьового компресора можна домогтися застосуванням лопаток компресора поворотних тільки одного напрямного апарату, розташованого на вході в компресор. Це пояснюється тим, що саме в першому ступені найчастіше виникає помпаж. Лопатки компресора поворотні спрямляючого та направляючого апаратів осьового компресора забезпечуються пристроями для одночасного їх повороту на заданий кут. Поворот лопаток відповідно до режиму роботи двигуна може здійснюватися автоматичним регулятором, пов'язаним з важелем, керуючим одночасним поворотом лопаток. Лопатки компресора поворотні знайшли також застосування у відцентрових компресорах авіаційних газотурбінних та поршневих двигунів [15].
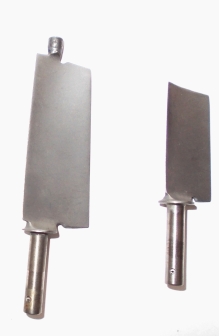
a                   б
Рисунок 5 – Поворотні лопатки: а – двухопорна; б – консольна.
Соплові лопатки турбіни на відміну від робочих не відчувають дії відцентрових сил, тому опір повзучості в даному випадку не так важливо. Проте в минулому ці лопатки зрідка ламалися від появи тріщин або вигину, що виникали внаслідок надмірних температурних градієнтів відразу ж після запуску двигуна [16]. В даний час зазвичай проводять лабораторні випробування на одиночних пластинках такого ж профілю, що і соплові лопатки, і отримують таким чином необхідні дані для проектування. Слід зазначити також, що на додаток до температурних напруг соплові лопатки відчувають ще згинальні напруження.
Однак у зв'язку з тим, що лопатки зазвичай встановлюються в кільці вони можуть бути зроблені досить міцними при допустимих розмірах. Соплові лопатки зазвичай виготовляються методами прецизійного лиття із застосуванням воскових моделей. Тому виливки профілів можуть бути отримані з високим ступенем точності. В одному з малих газотурбінних двигунів соплові лопатки виконані порожніми з листа німоник 75
шляхом вигину його в аеродинамічний профіль та зварювання отриманих лопаток по вихідній кромці. Охолоджувальне повітря з компресора пропускається через ці порожнисті лопатки, завдяки чому можна застосовувати високі температури на вході в турбіну [16].
4.2 Види пошкодження лопаток
В експлуатації крім силових факторів, що визначаються конфігурацією лопаток і дією зовнішніх сил (статичних, газодинамічних та вібраційних), на лопатки діє ряд інших факторів, пов'язаних з особливостями впливу середовища, в якому експлуатується двигун: потрапляння сторонніх предметів, корозія, зміна температури, ерозія, знос, фреттинг-корозія і т.д. [13].
Силові чинники, за винятком вібраційних і, в якійсь мірі, циклічних, досить точно прогнозуються та враховуються на стадії проектування, інші чинники складно передбачувані.
Найбільше число несправностей компресорів пов'язано з попаданням в двигун сторонніх предметів і спричинених ними механічних пошкоджень.
Деякі характерні види механічних ушкоджень (забоїн, вм'ятина, погнутість) і геометричні характеристики пошкоджень кромок та кінцевих частин робочих лопаток наведені на рис. 6.
Також можливі забоїни власне на центральній частині пера робочих лопаток. Ці забоїни характеризуються глибиною і діаметром, взаємним розташуванням, а також тим, є, чи ні, випинання в їх зоні матеріалу із зворотного боку пера лопатки [13].
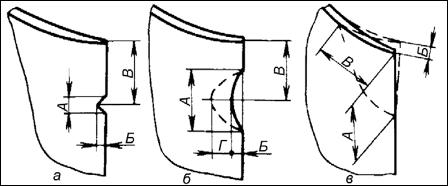
Рисунок 6 – Види пошкоджень кромок, верхівок (кінцевих частин) лопаток та їх характеристики [13].
(а – забоїн: (характерні розміри) А – довжина забоїни; Б – глибина забоїни, вимірювана по хорді профілю; В – відстань від периферійного торця лопатки до середини забоїни.
б – вм'ятина: А – довжина вм'ятини, яка вимірюється вздовж вхідний кромки лопатки; Б – максимальна глибина вм'ятини (вимірюється в площині профілю пера лопатки перпендикулярно вхідний кромці); В – відстань від периферійного торця лопатки до середини вм'ятини (вимірюється уздовж вхідний кромки лопатки); Г – максимальна ширина вм'ятини (вимірюється по поверхні профільної частини з боку спинки або корита перпендикулярно вхідний кромці лопатки).
в – погнутість: А – величина відігнутої частині профілю лопатки, яка вимірюється вздовж вхідний (вихідний) кромки; Б – величина відхилення вершини кута лопатки; В – величина відігнутої частині профілю лопатки, яка вимірюється по периферійної кромці лопатки)
Найбільша пошкоджуваність в експлуатації лопаток компресора припадає на 1 ступінь [17] (близько 21%), 72% ушкоджень – на вхідну кромку та 17% – на вихідну (до 90% лопаток має лише одне пошкодження), частіше пошкоджується верхня половина пера лопатки.
Пошкодження лопаток в експлуатації носять випадковий характер як по виду ушкоджень, так і за розподілом ушкоджень по перу лопатки.
Викривлення розрахункової геометрії пошкоджених лопаток викликає розбалансування ротора та підвищення рівня вібрацій двигуна, а також може стати причиною появи нових резонансних режимів та автоколивань лопаток. Найбільш небезпечні ізгібние коливання по першим формам (рис. 7) [13].
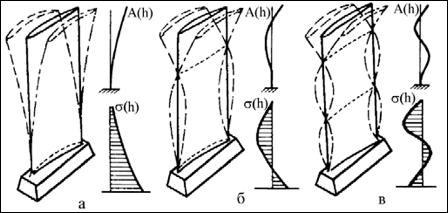
Рисунок 7 – Форми згинальних коливань робочих лопаток та характер розподілу амплітуд переміщень А(h) та напруг сигма(h) [18]: а – перша (1X1), б – друга (2X1), в – третя (3X1) форма.
Дефекти робочих лопаток розподіляються наступним чином: 29% – конструктивні, 17% – технологічні (виробничі); 11% – експлуатаційні; 43% – поєднання конструктивних, технологічних та експлуатаційних.
Можливі також несправності елементів допоміжних систем компресорів, таких як противообледенительна та протівопомпажна системи, які, в кінцевому підсумку, можуть призвезти до ушкоджень робочих лопаток.
Пошкоджуваність та надійна робота робочих лопаток турбін в значній мірі залежить і від роботи всіх елементів гарячої частини двигуна. Збільшення ресурсу та підвищення робочих параметрів в турбінах ГТД супроводжується інтенсифікацією процесів пошкодження робочих лопаток під дією статичних та вібраційних навантажень, високих температур, циклічних навантажень, що викликаються дією силових факторів, термічних напружень, корозійного та ерозійного впливу газового потоку [13].
Більшість руйнувань робочих лопаток турбін, як і робочих лопаток компресорів, має втомний характер і пов'язане зі змінними напругами, що виникають при коливаннях за нижчими формами (які можуть викликатися в тому числі пульсаційним горінням палива в камері згоряння). При коливаннях по першій вигинистої форми можливі також розтріскування та втомні руйнування хвостовиків лопаток.
Згідно [17] втомні руйнування лопаток турбін складають до 33%, руйнування від малоцикловой втоми – близько 9%, руйнування від поєднання малоцикловой втоми, вібраційних напружень – близько 42% та руйнування, пов'язані з вичерпанням тривалої міцності – 16%.
Таким чином, в загальному випадку, причинами руйнування лопаток турбін можуть бути [13]:
- зниження межі витривалості через утворення мікротріщин в поверхневому шарі, пошкодженому нерегламентованої механічною обробкою;
- підвищення амплітуди вібраційних напружень через раззазорювання бандажних полиць внаслідок зносу площадок контакту;
- невідповідність натягу по бандажнім полкам технічним умовам при збірці;
- перегрів за нерівномірного температурного поля перед турбіною;
- порушення умов експлуатації;
- недостатня ефективність системи охолодження;
- підвищення амплітуди вібраційних напружень внаслідок зміни умов збудження (прогар лопаток соплових апаратів, закоксованість паливних форсунок та т.п.);
- нерівномірність розподілу навантаження по зубцям хвостовика;
- неоптимальні режими різання профілю хвостовика;
- недосконалість процесів штампування, термообробки або лиття лопаток і т. д.
Руйнування лопаток турбін з технологічних причин складають [17] близько 25%, по недосконалості конструкції близько 23%, інші 52% припадають на несприятливе поєднання конструктивних та технологічних факторів.
При аналізі пошкоджуваності робочих лопаток турбін з причини термічної втоми та вироблення способів її зниження в загальному випадку слід враховувати [13]:
- при одному і тому ж градієнті температур кромок та середній частині лопатки напруги в кромках завжди більше, ніж в середній частині;
- при запуску двигуна в кромках виникають напруги стиснення, здатні, в деяких випадках, викликати втрату їх стійкості;
- при зупинці двигуна на кромках виникають напруги розтягання тим більші, чим вище режим, з якого відбувається вимикання;
- при значному градієнті температур виникаючі температурні напруги можуть перевищити межу пружності і при багаторазовому повторенні здатні викликати руйнування (утворення тріщини) по типу малоцикловой втоми;
- величину напружень можна знизити шляхом зниження градієнта температур за рахунок більш плавного наростання подачі палива при запуску, охолодження двигуна на зниженому режимі перед його вимиканням, а також низкою конструктивних заходів (плівкове охолодження кромок, теплова ізоляція кромок від газового потоку, застосування пустотілих неохолоджуваних лопаток).
В залежності від вибору матеріалу та покриттів циклічна довговічність може підвищитися до 10 разів завдяки більш високій пластичності матеріалу.
Зазвичай вартість матеріалу та маса лопатки збільшуються при застосуванні матеріалів з підвищеною пластичністю.
На відміну від порівняно нескладних способів збільшення довговічності на встановлених режимах для підвищення опору малоцикловой втоми лопаток потрібні фундаментальні зміни, а саме: заміна матеріалу, підбір відповідного покриття, схеми охолодження та конфігурації деталі [13].
Проте слід враховувати, що зміни, необхідні для підвищення циклічної довговічності робочих лопаток можуть вплинути на іншу частину роторної системи.
Наприклад, зміна матеріалу, що приводить до збільшення маси лопатки, зажадає змін в конструкції диска, щоб компенсувати збільшені відцентрові навантаження і т.п.
4.3 Існуючі технології ремонту та відновлення лопаток ГТД
В сучасності існує безліч технологій з ремонту й відновлення лопаток ГТД. Розвиток науки та техніки в швидкому темпі, розкриває перед нами безліч технологій, які спрямовані на зменшення собівартості та збільшення якості ремонту і відновлення лопаток ГТД.
Технологія ремонту та відновлення лопаток ГТД складається з етапів:
- вхідний контроль;
- металургійне дослідження;
- зняття зовнішнього та внутрішнього жаростійкого покриття;
- наплавлення;
- термообробка;
- підготовка під нанесення покриття;
- нанесення покриття на внутрішню порожнину;
- нанесення покриття на проточну частину пера лопатки;
- вихідний контроль.
Розглянемо деякі методи наплавлення:
Електронно-променеве наплавлення.
Останні нововведення в ремонті та відновленні лопаток ГТД застосовується електронно-променеве наплавлення. Технологія та обладнання призначені для нанесення в вакуумі градієнтних порошкових покриттів значної товщини (до 15 мм) з метою підвищення поверхневої міцності, опору зносу, корозійної стійкості, термостійкості і модифікації інших фізичних, хімічних і механічних властивостей поверхневих шарів матеріалів та виробів з них.
Електронно-променеве наплавлення (ЕПН-технологія багатофункціональних покриттів на деталі та вироби порошковими матеріалами в вакуумі є принципово новою технологією порошкової металургії, реалізованої в електронному пучку безпосередньо на деталі. ЕПН технологія – це технологія XXI століття, вона не має аналогів в Росії і за кордоном. Під впливом електронного променя і відповідної подачі порошкової суміші на поверхні деталі реалізуються процеси порошкової металургії в режимі жидкофазного спікання з повним збереженням складу, дисперсності та властивостей заданої порошкової композиції. Завдяки високій щільності потужності в промені (10,4 – 10,5 вт/куб.см ), можливості оперативного управління енергетичними характеристиками променя та малому обсягом розплавленої ванни (10 – 20 мм3), з'являється можливість управляти цими процесами, змінюючи відповідним чином не тільки інтегральну температуру ванни, а й швидкість її нагрівання та охолодження. ЕПН-технологія дозволяє використовувати самі різні порошкові композиції, включаючи ультрадисперсні. Все це робить цю технологію універсальної як в плані різноманіття функціональних властивостей порошкових покриттів, так і в плані нанесення покриттів будь-якої товщини, включаючи шарові та градієнтні, на деталі з будь-яких металів, сплавів та будь-якої геометрії [21].
Плазмова наплавка-напилення.
В даний час серед методів порошкової плазмової наплавки найбільше поширення має спосіб, при якому використовується стисла пряма дуга, що горить між електродом та виробом. У той же час за кордоном найбільш активно використовується метод порошкової плазмової наплавки, що отримав назву РTА – процес (plasma transferred arc). При цьому методі діють одночасно основна дуга (палаюча між електродом та виробом) і непряма або пілотна дуга (палаюча всередині плазмотрона між електродом та плазмообразуючим соплом). У зв'язку з тим, що процес нанесення покриттів тільки непрямої плазмової дугою називається плазмовим напиленням, нова технологія отримала назву плазмова наплавка-напилення.
Таким чином, процес плазмового наплавлення-напилення – це метод нанесення порошкових покриттів товщиною 0,5 – 4,0 мм з гнучким регулюванням введення тепла в порошок та виріб плазмотроном з двома дугами – основної та пілотної.
Оскільки покриття наносяться методом плазмового напилення обмежені товщиною близько 1 мм, за межами якої проявляється тенденція до відшарування (внаслідок високих внутрішніх напружень), а покриття, що наносяться плазмової наплавкой традиційним способом з використанням лише основної дуги пов'язані з великим проплавленням основного металу та його перемішуванням з присадним матеріалом (відповідно, з відсутністю необхідних властивостей покриття в першому наплавленном шарі), то дана технологія плазмової наплавки-напилення відноситься до гібридних процесів, що поєднує позитивні характеристики процесів наплавлення та напилення [20].
Якість нанесених покриттів методом плазмового напилення залежить від великого числа вхідних параметрів. При цьому в даний момент не існує кількісних неруйнівних методів контролю якості плазмових напилених покриттів. Тому отримання беспорістих покриттів з максимальними адгезійними властивостями за рахунок використання другого джерела тепла – основної дуги, дозволило значно підвищити якість та експлуатаційні характеристики покриттів.
Процес плазмової наплавки-напилення (РТА-процес) забезпечує використання пілотної (непрямої) дуги для розплавлення присадочного порошку і основної дуги (переносимої) для підтримки необхідної температури частинок порошку оточеної на деталі. При цьому збільшення часу перебування частинок порошку при високій температурі сприяє максимальному зчепленню та ущільненню часток з мінімальним перегрівом поверхні деталі. Оптимізація основних характеристик процесу (струмів основної та пілотної дуги, відстані до вироби, швидкості подачі порошку і швидкості переміщення плазмотрона) виявило мінімальну чутливість до швидкості подачі порошку і в певних межах до швидкості переміщення плазмотрона.
При аналізі мікроструктури самофлюсуючих покриттів, нанесених методом плазмового наплавлення-напилення, було відзначено отримання литої структури (на відміну від шаруватої структури, типової для процесів плазмового напилення), а також відсутність пористості (близько 0,3%). Мікротвердість покриття склала HV 800. Зона термічного впливу зафіксована близько 0,5 мм, в той час як при плазмовій наплавці вона складає близько 3 – 4 мм [20].
Імпульсно-лазерне наплавлення.
Розроблена технологія відновлення зношених лопаток методом імпульсної лазерної наплавки дозволяє в значній мірі усунути недоліки, притаманні існуючій технології ремонту лопаток методом електродугової наплавки (рис. 8) і отримати значний економічний ефект за рахунок зниження трудомісткості ремонту та підвищення ресурсу роботи лопаток:
- Значно знизити обсяг виконання механічної обробки лопаток після наплавлення, так як припуски на подальшу після наплавлення механічну обробку не перевищують 100 мкм та практично перебуває в геометричному полі допуску після наплавлення.
Рисунок 8 – Методи відновлення лопаток електродугового наплавлення й імпульсної лазерної наплавки, відповідно [22]
- Усунути технологічні операції термообробки перед наплавкой і після наплавки лопаток, так як зони термічного впливу знаходяться на рівні сотні мікрон.
- Формує в наплавленому шарі дрібнодисперсні структури, що забезпечують підвищену зносостійкість поверхневого шару лопатки до рівня нових та вище.
- Дозволяє розширити зони ремонту лопаток внаслідок мінімальних зон термічного впливу, в порівнянні з електродугової наплавкою з 1/3 по висоті до 100%, тобто до зони кріплення лопатки.
Технологія імпульсної лазерної наплавки відкриває нові потенційні можливості при ремонті лопаток і дозволяє:
- Усунути трудомісткі технологічні операції зняття та установки лопаток з диска вала турбіни для відправки їх на ремонтний завод, тобто проводити ремонт безпосередньо на газоперекачувальній станції.
- Створити мобільний комплекс для ремонту лопаток, що дозволяє проводити ремонт лопаток безпосередньо на газоперекачувальній станції.
Технологію імпульсної лазерної наплавки можна застосовувати для відновлення зношених лопаток авіаційних турбін, атомних, теплових та гідроелектростанцій [22].
В ході виконання магістерської роботи буде використаний метод вакуумного іонно-плазмового нанесення покриття, в лабораторіях кафедри технологія машинобудування на установці Булат-6
(рис. 9).
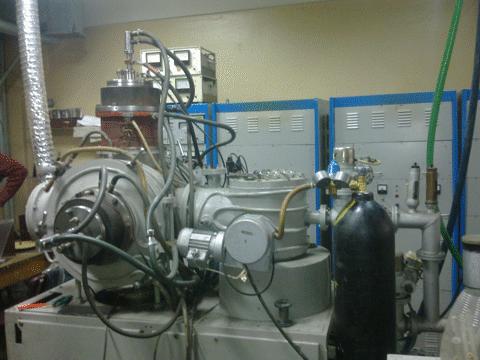
Рисунок 9 – Установка для нанесення вакуумного іонно-плазмового покриття Булат-6
Зміцнення здійснюється за рахунок нанесення зносостійких покриттів вакуумно-дуговим методом КІБ без іонного пучка, або з асистуванням високоенергетичним (20 – 150 кэВ) іонним пучком, а також за рахунок поліенергетіческой імплантації металевими іонами з енергією до 150 кеВ. Покращення декоративних властивостей здійснюється за рахунок нанесення декоративних покриттів.
Одне з найбільш ефективних напрямків удосконалення технології синтезу багатофункціональних покриттів пов'язано з розробкою технологій отримання багатошарових-композиційних покриттів з нано метричною товщиною кожного з шарів на основі одинарних, подвійних і потрійних сполук тугоплавких металів IY - YI груп Періодичної системи елементів (карбіди, нітриди, бориди , оксиди та їх суміші). Товщина кожного шару таких покриттів може становити декількох нанометрів, що дозволяє не тільки гранично зменшити кількість різних дефектів, але й реалізувати теоретичну
міцність матеріалу покриття. Використання виробів з подібними покриттями дозволяє ефективно вирішити цілий ряд завдань для широкої гами проблем машинобудування. Зокрема, стосовно до одного з найбільш масових виробів – різального інструменту, що підвищує продуктивність різних технологічних операцій різання, зростання точності і якості обробки, зниження витрати дорогих інструментальних матеріалів, можливість реалізації екологічно безпечного різання без застосування СОТС. [23].
Приклад лопаток ГТД після нанесення вакуумного іонно-плазмового покриття.
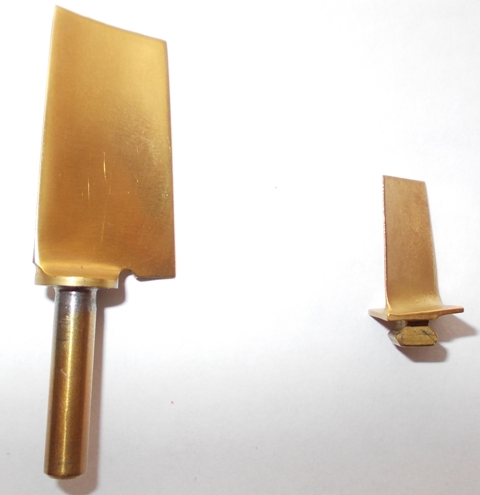
Рисунок 10 – Поворотна та робоча лопатка з нанесенням вакуумного іонно-плазмового напилення
Висновки
В даній роботі був проведений аналіз сучасного стану питання, ремонту та відновлення лопаток газотурбінного двигуна ТВ3–117. Розглянуто існуючі методи ремонту і відновлення лопаток ГТД, переглянуті особливості роботи і конструкція ГТД ТВ3–117, так само проаналізовано види пошкодження лопаток компресора та лопаток турбіни.
Існує безліч технологій відновлювального ремонту лопаток ГТД, які мають свої переваги і недоліки. Але наука розвивається, тому необхідно застосовувати більш прогресивні технології, які дозволять знизити собівартість та підвищити надійність, довговічність і зносостійкість лопаток ГТД. Такими технологіями є композиційні технології, які базуються на композиції основних особливостей та принципів синтезу комбінованих та функціонально-орієнтованих технологій.
При написанні даного реферату магістерська робота ще не закінчена. Остаточне завершення: грудень 2012 р. Повний текст роботи та матеріали по темі можуть бути отримані у автора або його керівника після зазначеної дати.
Список джерел
- Казаков Роман Александрович ОАО
НПО Сатурн
УГ Мет, Конструкторско-технологическое бюро перспективного развития, г. Рыбинск,Изготовление лопатки ВНА компрессора ГТД изотермической штамповкой
. - Крымов В.В., Елисеев Ю.С., Зудин К.И.
Производство газотурбинных двигателей
/ Под ред. В.В. Крымова. М.: Машиностроение / Машиностроение – Полет, 2002. – 376 с., ил. - Технологическое обеспечение эксплутационных характеристик деталей ГТД: монография / Лопатки компрессора и вентилятора / [Богуслаев В.А., Муравченко Ф.М., Жеманюк П.Д. и др.]. – Запорожье: ОАО
Мотор Сич
, 2003. – 396 с. - А.Н. Михайлов, Е.А. Михайлов, Д.А. Михайлов
Основы синтеза композиционных технологий машиностроения
. - Михаил Саркисов, Александр Саркисов, Данила Изотов
Жизнь семейства ТВ3–117
, ГУПЗавод им. В.Я. Климова
. - Богуслаев В.А.
Двигатель для воздушных трасс будущего
// Двигатель. – 2000. – №2 – 4. - Петр Изотов, Данила Изотов
Семейство ТВ3–117
, ГУПЗавод им. В.Я. Климова
. - Авиационная энциклопедия
Уголок неба
[электронный ресурс]. – Режим доступа: http://www.airwar.ru/... - Каталог мирового вооружения [электронный ресурс]. – Режим доступа: http://www.worldweapon.ru/...
- Сошин В.М.
Электронный ресурс предназначен для студентов 2-го курса специальности 130300, изучяющих конструкцию двигателя ТВ2–117 по дисциплине
, г. Самара, 2007 г.Авиационная техника
- Свободная энциклопедия
Википедия
[электронный ресурс]. – Режим доступа: http://www.ru.wikipedia.org/... - Авиасловарь [электронный ресурс]. – Режим доступа: http://www.aviaslovar.ru/...
Рабочие лопатки авиационных ГТД. Часть 1. Эксплутационная повреждаемость рабочих лопаток
, Московский государственный университет гражданской авиации.- Летная школа
Капитан Нестеров
[электронный ресурс]. – Режим доступа: http://www.flyingschool.ru/... - Справочник
АвиаПОРТ
[электронный ресурс]. – Режим доступа: http://www.aviaport.ru/... - Устройство автомобиля [электронный ресурс]. – Режим доступа: http://www.astra-world.ru/...
- Петухов А.Н.
Сопротивление усталости деталей ГТД
. – М: Машиностроение, 1993. – 240 с. - Лозицкий Л.П. и др.
Конструкция и прочность авиационных деталей
. – М: Воздушный транспорт, 1992. – 535 с. - В.А. Богуслаев, А.Я. Качан, В.Ф. Мозговой
Финишные технологии обработки деталей ГТД
- Научно-производственная фирма
Плазмацентр
[электронный ресурс]. – Режим доступа: http://www.plasmacentre.ru/... - Солдатов Анатолий Николаевич
Электронно-лучевая наплавка износостойких покрытий
. - Вятское машиностроительное предприятие
Лазерная техника и технологии
[электронный ресурс]. – Режим доступа: http://www.techlaser.kirov.ru/... - Научно-производственное предприятие
Булат
[электронный ресурс]. – Режим доступа: http://www.bulatsteel.ru/...