Реферат по теме выпускной работы
Содержание
- Введение
- 1. Постановка задачи
- 2. Актуальность темы
- 3. Анализ существующих способов получения качественных поверхностей в деталях типа валов и гильз
- 4.Экономичность механической обработки
- Выводы
- Список источников
Введение
В настоящее время требования к качеству поверхностей значительно повысились, что связано с особыми требованиями эксплуатации изделия. Это вызвано значительным шагом вперед всех технологий обработки – появились высокоточные станки и усовершенствовались инструменты. Также немаловажным является факт существования альтернативных вариантов обработок. Например, если по каким-то причинам невозможно выполнить шлифование, пластическое деформирование, а поверхность должна быть достаточно точной, то возможно использование многократного тонкого точения.
1. Постановка задачи
Целью данной работы является анализ вариантов достижения требуемой шероховатости при различных способах механической обработки, сравнение результатов, а также определение их влияния на физико-механические свойства поверхностного слоя из конструкционных материалов при их обработке.
Объект исследования – технология финишной обработки ответственных поверхностей детей типа тел вращения (валов и гильз) из конструкционных материалов.
Предмет исследования – процессы, происходящие в поверхностном слое материала при механическом воздействии на него, и обоснование выбора рационального способа обработки по критерию минимальной себестоимости.
2. Актуальность темы
В данной работе предполагается рассмотрение возможных вариантов финишной обработки деталей типа тел вращения из конструкционных материалов (на примере легированных сталей). На основе полученных результатов планируется выявление способа, обеспечивающего минимальную себестоимость обработки, при соблюдению требований по точности и качеству обработки.
3. Анализ существующих способов получения качественных поверхностей
в деталях типа валов и гильз
Тонкое точение и растачивание
Этот метод точения широко применяют в авиационной, тракторной и автомобильный промышленностях при обработке цилиндрических и конических поверхностей (наружных и внутренних), а также торцовых поверхностей, уступов и др. Точность размеров деталей соответствует 2-му, и иногда и 1-му классу точности. Более высокая точность получается при обработке цветных металлов, так как при обработке сталей и чугунов на точности сказывается износ резца по задней поверхности. Тонкое растачивание, в особенности цветных металлов, по точности и чистоте поверхности превосходит развертывание и не уступает шлифованию [1].
К станкам для тонкого точения предъявляют следующие требования:
- Повышенные числа оборотов шпинделя (2000 – 6000 об/ми);
- Малые подачи (0,01 – 0,2 мм/об);
- Высокая точность вращения шпинделя (радиальное биение – не более 0,005 мм), высокая точность и большая жесткость всех элементов станка;
- Отсутствие вибраций при больших числах оборотов шпинделя.
В качестве режущего инструмента для тонкого точения применяют:
- Резцы с пластинками твердого сплава марок ВК2 и ВК3М для тонкого обтачивания и растачивания чугуна; Т30К4 и Т60К6 для тонкого точения и растачивания стали, легких сплавов и цветных металлов.
- Алмазные резцы – для тонкого точения и растачивания легких сплавов, цветных металлов и неметаллических материалов [4].
Алмазные резцы значительно долговечнее твердосплавных резцов. Они позволяют работать сотни часов без переточки и переналадки и тем самым обрабатывать большое количество одинаковых деталей с соблюдением точности размеров, достигающей 2-го и даже 1-го класса и чистоты по-верхности 8 – 11 квалитетов.
Поверхностное пластическое деформирование
Сущность процесса заключается в следующем. При изготовлении деталей машин применяют поверхностное пластическое деформирование (ППД) – обработка давлением, при которой пластически деформируется только поверхностный слой материала детали. Различают статическое, ударное, вибрационное и ультразвуковое ППД. Возможен вариант ППД в рабочей среде. В качестве рабочей среды используется жидкость (гидравлическое ППД) или сжатый воздух (пневматическое ППД); в качестве рабочих тел – ролики, шарики, дробь и т.д. ППД может выполняться одновременно несколькими методами обработки (совмещенное ППД) или последовательно также несколькими методами (комбинированное ППД). Цель обработки – образование определенной макро- и (или) микрогеометрической формы (поверхностно пластическое формообразование), уменьшение параметра шероховатости поверхности (сглаживание), изменение размеров заготовки до допустимых (калибрующее ППД), изменение структуры материала без его полной рекристаллизации (поверхностный наклеп), создание определенного напряженного состояния (напряженный поверхностный наклеп) и упрочнение поверхностным наклепом [2].
При обработке деталей все перечисленные выше изменения происходят в поверхностном слое. Основные из них определяют метод обработки: накатывание (упрочняющее, сглаживающее, калибрующее, формообразующее); поверхностные дорнование и редуцирование, обработка дробью, дробеабразивная обработка, галтовка, вибрационная ударная обработка, центробежная обработка, обработка механической щеткой, чеканка, выглаживание.
Обкатывание и раскатывание поверхностей
Обработка осуществляется роликами и шариками, оказывающими давление на поверхность обрабатываемой детали. При определенном (рабочем) усилии в зоне контакта деформирующих элементов и детали интенсивность напряжений превышает предел текучести, в результате чего происходит пластическая деформация микронеровностей, изменяются физико-механические свойства и структура поверхностного слоя. Объемная деформация детали обычно незначительна.
Сочетанием вращательного и поступательного перемещений детали и деформирующих элементов методами обкатывания, раскатывания обрабатывают плоские, цилиндрические, переходные поверхности, фасонные поверхности и канавки (рис. 1, а – е).
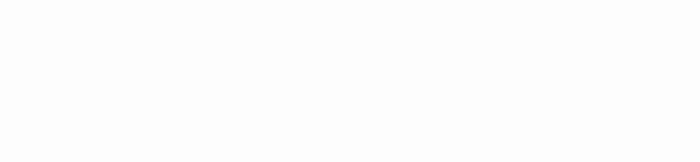
Рис. 1. Схемы процесса обкатывания: а – роликом с продольной подачей; б – роликом с поперечной подачей; в – фасонным роликом с поперечной подачей; г – торцовой поверхности шариком; д – роликами поверхности шлицев; е – плоской поверхности роликом.
(Анимамация, объем – 55,3 Кб, состоит из 7 кадров, 5 повторений, задержка кадров 1 секунда)
Сочетанием вращательного и поступательного перемещений детали и де-формирующих элементов методами обкатывания, раскатывания обрабаты-вают плоские, цилиндрические, переходные поверхности, фасонные поверхности и канавки (рис. 1, а – е).
Теперь перейдем от самого процесса обработки к точности. Изменение размера поверхности при обкатывании и раскатывании связано со смятием микронеровностей и пластической объемной деформацией детали. Таким образом, точность обработанной детали будет зависеть от ее конструкции и конструкции инструмента, режимов обработки, а также от точности размеров, формы и качества поверхности детали, полученных при обработке на предшествующем переходе.
Наиболее целесообразно обкатыванием и раскатыванием обрабатывать исходные поверхности 7 – 11 квалитетов инструментами жесткого копирующего типа и поверхности 5 – 7 квалитетов ударным инструментом.
Основополагающим критерием для нас является шероховатость поверх-ности, поэтому следующий этап будет посвящен именно ей. При ППД практически достигаются параметры шероховатости обрабатываемой поверхности Ra=0,2 – 0,8 мкм при исходных значениях этих параметров 0,8 – 6,3 мкм. Степень уменьшения шероховатости поверхности зависит от материала, рабочего усилия или натяга, подачи, исходной шероховатости, конструкции инструмента и т.д. [2].
Одним из факторов, влияющим на процесс ППД, являются усилия обкатывания и раскатывания поверхностей. Ниже приведена номограмма их определения (рис. 2) [2].
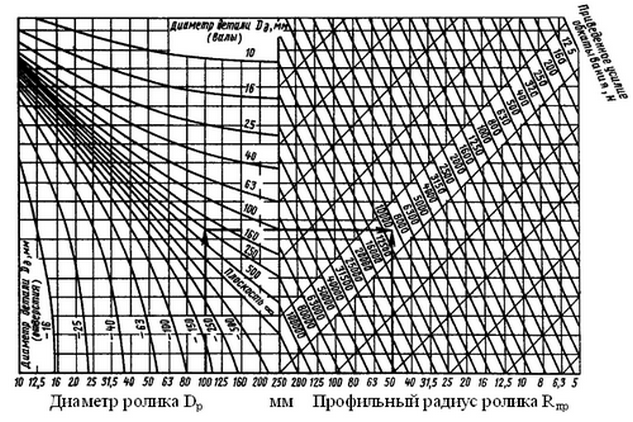
Рис. 2. Нанограмма для определения усилия обкатывания и расскатывание поверхностей в зависимости от размеров детали и ролика. Например, при обработке вала диаметром D=250 мм роликом диаметром Dр=100 мм с профильным радиусом Rпр=50 мм усилие обкатывания Р=9000 Н.
Алмазное выглаживание
Еще одной разновидностью ППД является алмазное выглаживание. Сущность процесса заключается в том, что при выглаживании поверхностей инструмент (алмаз, смонтированный в державке) прижимается с определенной силой к обрабатываемой поверхности. В процессе выглаживания поверхностей в месте контакта деформируемого элемента и обрабатываемой детали возникают значительные контактные напряжения и при определенном усилии происходит пластическая деформация поверхностного слоя, в результате чего снимаются микронеровности и изменяются физико-механические свойства поверхностного слоя. Выглаживанием могут обрабатываться наружные и внутренние поверхности вращения, а также торцовые поверхности.
При правильно подобранных режимах выглаживания микронеровности могут быть уменьшены в несколько раз (Ra=0,1 – 0,005 мкм), микротвердость увеличивается на 50 – 60% , т.е. глубина наклепанного слоя может составлять до 400 мкм. Как следствие детали обладают высокой износостойкостью и усталостной прочностью [2].
Но помимо положительных характеристик имеются и негативная – за счет смятия исходных микронеровностей размер детали может несколько уменьшиться. В связи с этим целесообразно на предшествующем переходе обеспечить точность размеров на 20 – 30% выше заданной для окончательно обработанной детали.
Центробежная обработка поверхностным пластическим деформированием
В инструментах центробежной обработки деформирующие элементы (шарики или ролики) размещают в радиальных пазах диска. При работе элементы могут смещаться в радиальном направлении. Диск с элементами вращается с высокой скоростью. Они при этом наносят многочисленные удары по поверхности детали, пластически деформируя ее, после чего отскакивают обратно. В результате этого шероховатость поверхности повышается до Ra=0,1 – 0,04 мкм при исходном значении Ra=0,8 – 3,2 мкм. Твердость поверхности увеличивается на 30 – 80% при глубине наклепанного слоя 0,3 – 3 мм [5].
Центробежно-ударную обработку применяют при изготовлении деталей из цветных металлов и сплавов, чугуна и стали и твердостью до HRC 58 – 64. Таким способом возможна обработка наружных и внутренних поверхностей, а также места сопряжения поверхностей и прерывистые поверхности.
Накатывание рифлений и клем
Накатывание рифлений проводят цилиндрическими роликами, свободно установленными на осях в специальных державках. Обработку выполняют на токарных, револьверных станках и автоматах как один из переходов обработки или как самостоятельную операцию на специальных станках. Рифления на плоских поверхностях накатывают на строгальных, долбежных и строгальных станках. Накатываемые рифления могут быть прямыми и сетчатыми (ГОСТ 21474 – 75). Шаг рифлений выбирают из рядов: прямых – 0,5; 0,6; 0,8; 1,0; 1,2; 1,6; сетчатых – 0,5; 0,6; 0,8; 1,0; 1,2; 1,6; 2,0.
В результате накатывания происходит увеличение наружного диаметра детали на величину 0,5 – 1,0 шага рифлений.
Необходимый профиль рифлений получают за пять – десять последовательных проходов. Число проходов зависит от материала детали, шага и связанной с ним глубины рифлений.
Схемы клеймения деталей методом накатывания показаны на рис. 3, а – г. Накатывание по схеме, приведенной на рис. 3, б, осуществляется при перекатывании роликовой каретки с заготовкой. Каретка возвращается в исходное положение пружиной. Возможно накатывание клейм на резьбонакатных станках с плоскими и круглыми плашками и на других станках, удобных для накатывания по кинематике рабочих движений [2].

Рис. 3. Схемы клеймения деталей накатыванием: а и б – плоских деталей на поперечно-строгальном и горизонтально-фрезерном станках, в и г – цилиндрических деталей на токарном и горизонтально-фрезерном станках, 1 – деталь, 2 – накатный ролик, 3 – опорные ролики, 4 – каретка.
Калибрование отверстий
Калибрование (деформирующее протягивание, дорнование) – чистовая операция обработки отверстий деталей машин пластическим деформированием. Эту операцию выполняют перемещение с натягом деформирующего инструмента. При l/d<7, где l – длина отверстия и d – его диаметр, детали обкатываются методом прошивания (рис. 4, а и б), а при l/d>7 – методом протягивания (рис. 4, в – д). Глухие отверстия обрабатывают при возвратно-поступательном движении оправки (рис. 4, д). Различают обработку со сжатием (рис. 4, в) и с растяжением (рис. 4, г). Наиболее часто обработку ведут со сжатием.
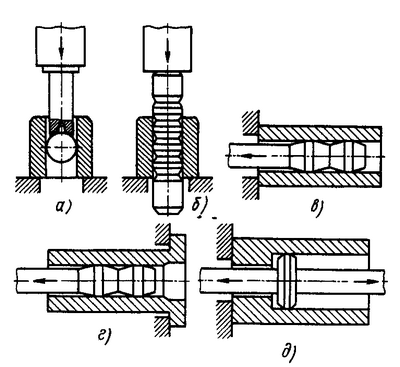
Рис. 4. Схемы обработки отверстий: а и б – прошиванием с помощью шарика и оправки; в – со сжатием детали; г – с растяжением детали; д – при возвратно-поступательном ходе оправки.
Инструментом для обработки при калибровании служат оправки или шарики. Обработка шариками не обеспечивает оптимальных условий деформации – элементы имеют малую размерную стойкость. Однако шарики применяют в промышленности ввиду простоты процесса обработки и возможности его автоматизации.
Материал деформирующих элементов (твердый сплав ВК15, ВК15М) обеспечивает высокую износостойкость инструмента и высокую изгибную прочность. При малых нагрузках на инструмент можно применять сплав ВК8.
Шероховатость поверхности зависит от предшествующей точности обра-ботки. При обработке отверстий в толстостенных деталях после переходов растачивания или развертывания (исходный параметр Ra=6,3 – 1,6 мкм) получают поверхности с Ra=0,8 – 0,1 мкм, если материал деталей сталь, Ra=0,4 – 0,1 мкм при обработке деталей из бронзы и Ra=1,6 – 0,4 мкм при обработке деталей из чугуна. Шероховатость поверхностей тонкостенных деталей в 2 – 4 раза выше.
Шлифование
Шлифованием называют абразивную обработку, при которой инструмент совершает только вращательное движение, которое является главным движением резания, а заготовка – любое движение.
Шлифование – один из прогрессивных и универсальных методов окончательной обработки различных поверхностей деталей машин, к которым предъявляются высокие требования по точности размеров, геометрической формы и качеству обработки.
Круглое шлифование периферией и торцом круга
Круглое шлифование периферией и торцом круга предназначено для обработки деталей типа тел вращения и является основным способом, обеспечивающим высокую точность. Оно может осуществляться с установкой детали в невращающихся центрах и в кулачковом или цанговом патроне вращающегося шпинделя станка [7].
Круглое шлифование можно осуществлять как периферией круга (в основном), так и его торцом; при этом в качестве режущей части используют наружную и торцовую поверхность щлифовального круга.
Применяют следующие основные операции круглого шлифования: обдирочное, предварительное, окончательное (чистовое), тонкое и выглаживание.
Внутреннее шлифование
Способом внутреннего шлифования обрабатывают цилиндрические, конические и профильные отверстия.
При внутреннем шлифовании в патроне и бесцентровом шлифовании подача осуществляется вследствие вращения детали со скоростью vд. При внутреннем шлифование крупногабаритных деталей деталь неподвижна, а шпиндель шлифовального круга совершает вращение вокруг оси обрабатываемого отверстия.
Бесцентровое шлифование
При бесцентровом шлифовании деталь не закрепляют в центрах или в патроне, а базируют по обрабатываемой или ранее обработанной поверхности.
Деталь получает вращение от ведущего круга, окружная скорость которого в 60 – 100 раз меньше, чем скорость шлифовального круга.
Профильное шлифование
Шлифование поверхностей , образующая которых является кривой или ломаной линией, называют профильным шлифованием.
Зубошлифование
Наибольшее применение в машиностроении получили зубчатые колеса из закаленных сталей с твердостью рабочих поверхностей HRC 48 – 60, которые выполняют 4 – 7-ой степени точности в зависимости от условий работы. Шлифование зубьев может осуществляться методом копирования или обкатывания.
Скоростное, обдирочное и глубинное шлифование
Скоростное, обдирочное и глубинное шлифование интенсифицирует процесс и позволяют повысить производительность обработки, снизить трудоемкость и стоимость операции.
Скоростное шлифование является наиболее известным высокопроизводительным методом абразивной обработки. Этот метод можно производить разными способами [3]:
- Шлифование с повышенной скоростью вращения круга без изменения других составляющих режима шлифования. В этом случае будут обеспечены низкие параметры шероховатости поверхности шлифуемой детали и повышенная стойкость круга, что уменьшит число правок, скорость изнашивания кругов и вспомогательное время. Процесс шлифования происходит при меньших силах.
- Шлифование с повышенной скоростью вращения круга при одновременном пропорциональном увеличении частоты вращения детали или продольной или окружной скорости стола (в зависимости от типа станка, на котором производится обработка) без увеличения поперечных подач. В этом случае производительность обработки повышается при снижении машинного времени пропорционально увеличению скорости вращения и стойкости круга. Шероховатость поверхности и силы шлифования будут теми же, что и до повышения скорости вращения круга.
- Шлифование с повышенной скоростью вращения круга при одновременном пропорциональном увеличении частоты вращения детали и скорости перемещения стола (на плоскошлифовальных станках) и увеличении поперечных подач круга. При этом резко возрастает производительность шлифования, но уменьшается стойкость круга, увеличивается шероховатость поверхности.
Недостатки скоростного шлифования: возрастает мощность шлифования; увеличивается выделение теплоты, что может привести к появлению прижогов. Прижогов можно избежать путем повышения скорости обрабатываемой детали и совершенствования составов и способов подвода смазочно-охлаждающих технологических средств.
Обдирочное шлифование
Обдирочное шлифование, обеспечивающее значительные съемы обрабатываемого материала, находит все более широкое применение в машиностроении. Оно предназначено для удаления с заготовок слоя после литья, ковки, штамповки, прокатки, сварки [7].
Обдирочное шлифование осуществляют периферией круга, имеющей гладкий и фасонный профиль, и торцом шлифовального круга. В последнем случае чаще всего используют сегментные или прерывистые круги.
При обдирочном шлифовании производительность шлифования повышается до 6 раз и снимается значительный припуск (до 7 мм на сторону).
Глубинное шлифование
Глубинное шлифование является разновидностью обдирочного шлифования. Однако, в ряде случаев, глубинное шлифование по достигаемому качеству обрабатываемой поверхности может являться чистовым.
Глубинное шлифование применяют для профильного шлифования, в том числе широкими кругами, для шлифования стружечных канавок на сверлах, гребенок, пазов; при шлифовании резьб, зубьев и червяков и деталей топливной аппаратуры и при алмазной обработке твердосплавных режущих инструментов.
4. Экономичность механической обработки
При выборе экономичных режимов обработки необходимо учитывать технические характеристики металлорежущих станков. В качестве ограничений при выборе экономичных режимов резания можно рассматривать следующие характеристики станков:
- Максимальную подачу;
- Максимальную частоту вращения шпинделя;
- Максимальную мощность привода;
- Максимально допустимую силу резания;
- Пределы подачи (или скорости), обеспечивающие необходимую шероховатость обработанной поверхности;
- Ступени скоростей и подач.
Себестоимость обработки детали складывается из нескольких статей. Для простоты рассмотрим обработку одним инструментом [6].
- Непроизводительные затраты С, приходящиеся на одну деталь, включают стоимость закрепления и снятия одной детали, стоимость простоя оборудования.
- Стоимость машинного времени обработки С2.
- Стоимость времени на смену инструмента С3.
- Стоимость инструмента, отнесенная к одной детали С4.
- Стоимость материала С5.
Себестоимость детали может быть снижена путем сокращения времени закрепления и снятия детали, времени простоя и времени смены инструмента. Для этого могут быть использованы как технические так и организационные методы. Совершенствование материала инструмента и заточки повышает стойкость инструмента, уменьшает количество смен инструмента и стоимость заточки, приходящуюся на одну деталь, тем самым снижая себестоимость детали. Износ режущего инструмента может быть снижен путем изменения свойств обрабатываемого материала. Увеличение скорости резания может иметь обратное влияние на себестоимость детали, так как она уменьшает стойкость инструмента.
Производительность обработки обратно пропорциональна времени обработки и зависит от режимов резания и стойкости инструмента.
Факторы, снижающие себестоимость деталей и увеличивающие производительность обработки, увеличивают и прибыль в единицу времени.
Выводы
Таким образом, можно подытожить, что при выборе способа финишной обработки, помимо основных критериев (шероховатости, точности обработки), немаловажными являются такие понятия как себестоимость и производительность обработки. На базе анализа соответствующих величин должно приниматься оптимальное решение.
Список источников
- Тонкое точение. [Электронный ресурс]. – Режим доступа: http://machinetools.aggress.ru....
- Справочник технолога-машиностроителя. Т 2 / Под ред. А.Г. Косиловой и Р.К. Мещерякова. – 4-е изд., перераб. и доп. – М.: Машиностроение, 1985. – 496 с.
- Кащук В.А., Верещагин А.Б. Справочник шлифовщика. – М.: Машиностроение, 1988. – 480 с.
- Бруштейн Б.Е., Дементьев В.И. Токарное дело. Учебник для проф.-техн. училищ. Изд. 6-е, переработ. И доп. М., «Высшая школа», 1967 г. – 448 с.
- Браславский В.М. Технология обкатки крупных деталей роликами, 1987 г. – 159с.
- Армарего И.Дж.А., Браун P.Х. Обработка металлов резанием. Пер. с англ. В.А.Пастунова. М.: Машиностроение, 1977. – 325с.
- Наерман М.С. Справочник молодого шлифовщика. – М.: Высш. шк., 1985. – 207 с., ил. – (Профтехобразование).