Реферат за темою випускної роботи
Зміст
- Вступ
- 1. Постановка завдання
- 2. Актуальність теми
- 3. Аналіз існуючих способів отримання якісних поверхонь в деталях типу валів і гільз
- 4.Экономічність механічної обробки
- Висновки
- Перелік посилань
Вступ
Нині вимоги до якості поверхонь значно підвищилися, що пов'язано з особливими вимогами експлуатації виробу. Це викликано значним кроком вперед усіх технологій обробки – з'явилися високоточні верстати і удосконалилися інструменти. Також важливим є факт існування альтернативних варіантів обробок. Наприклад, якщо з якихось причин неможливо виконати шліфування, пластичну деформацію, а поверхня має бути досить точною, то можливе використання багатократного тонкого точіння.
1. Постановка завдання
Метою цієї роботи є аналіз варіантів досягнення необхідної шорсткості при різних способах механічної обробки, порівняння результатів, а також визначення їх впливу на физико-механичні властивості поверхневого шару з конструкційних матеріалів при їх обробці.
Об'єкт дослідження – технологія фінішної обробки відповідальних поверхонь дітей типу тіл обертання (валів і гільз) з конструкційних матеріалів.
Предмет дослідження – процеси, що відбуваються в поверхневому шарі матеріалу при механічній дії на нього, і обгрунтування вибору раціонального способу обробки за критерієм мінімальної собівартості.
2. Актуальність теми
У цій роботі передбачається розгляд можливих варіантів фінішної обробки деталей типу тіл обертання з конструкційних матеріалів (на прикладі легованих сталей). На основі отриманих результатів планується виявлення способу, що забезпечує мінімальну собівартість обробки, при дотриманні вимог по точності і якості обробки.
3. Аналіз існуючих способів отримання якісних поверхонь
в деталях типу валів і гільз
Тонке точіння і розточування
Цей метод точіння широко застосовують в авіаційній, тракторній і автомобільній промисловостях при обробці циліндричних і конічних поверхонь (зовнішніх і внутрішніх), а також торцевих поверхонь, уступів та ін. Точність розмірів деталей відповідає 2-у, а іноді і 1-у класу точності. Вищою точність виходить при обробці кольорових металів, оскільки при обробці сталей і чавунів на точності позначається знос різця по задній поверхні. Тонке розточування, особливо кольорових металів, по точності і чистоті поверхні перевершує розгортання і не поступається шліфуванню [1].
До верстатів для тонкого точіння пред'являють наступні вимоги:
- Підвищені числа оборотів шпинделя (2000 – 6000 об/хв);
- Малі подачі (0,01 – 0,2 мм/об);
- Висока точність обертання шпинделя (радіальне биття – не більше 0,005 мм), висока точність і велика жорсткість усіх елементів верстата;
- Відсутність вібрацій при великих оборотах шпинделя.
В якості різального інструменту для тонкого точіння застосовують:
- Різці з пластинками твердого сплаву марок ВК2 і ВК3М для тонкого обточування і розточування чавуну; Т30К4 і Т60К6 для тонкого точіння і розточування сталі, легких сплавів і кольорових металів.
- Алмазні різці – для тонкого точіння і розточування легких сплавів, кольорових металів і неметалічних матеріалів [4].
Алмазні різці значно довговічніші за твердосплавні різці. Вони дозволяють працювати сотні годин без переточування та переналадки і тим самим обробляти велику кількість однакових деталей з дотриманням точності розмірів, що досягає 2-го і навіть 1-го класу і чистоти поверхні 8 – 11 квалітетів.
Поверхневе пластичне деформування
Суть процесу полягає в наступному. При виготовленні деталей машин застосовують поверхневу пластичну деформацію (ППД) – обробка тиском, при якій пластично деформується тільки поверхневий шар матеріалу деталі. Розрізняють статичне, ударне, вібраційне і ультразвукове ППД. Можливий варіант ППД в робочому середовищі. В якості робочого середовища використовується рідина (гідравлічне ППД) або стисле повітря (пневматичне ППД); в якості робочих тіл – ролики, кульки, дріб і так далі ППД може виконуватися одночасно декількома методами обробки (поєднане ППД) або послідовно також декількома методами (комбіноване ППД). Мета обробки – отримання певної макро- і (чи) мікрогеометричної форми (поверхневе пластичне формоутворення), зменшення параметра шорсткості поверхні (згладжування), зміна розмірів заготовки до допустимих (калібруюче ППД), зміна структури матеріалу без його повної рекристалізації (поверхневе наклепання), створення певного напруженого стану (напружене поверхневе наклепання) і зміцнення поверхневим наклепом [2].
При обробці деталей усі перелічені вище зміни відбуваються в поверхневому шарі. Основні з них визначають метод обробки: накочення (що зміцнює, згладжує, калібрує, формоутворює); поверхневі дорновання і редукування, обробка дробом, дробеабразивная обробка, галтовка, вібраційна ударна обробка, відцентрова обробка, обробка механічною щіткою, карбування, випрасовування.
Обкочування і розкочування поверхонь
Обробка здійснюється роликами і кульками, що чинять тиск на поверхню оброблюваної деталі. При певному (робочому) зусиллі в зоні контакту деформуючих елементів і деталі інтенсивність напруги перевищує межу текучості, внаслідок чого відбувається пластична деформація мікронерівностей, змінюються физико-механічні властивості і структура поверхневого шару. Об'ємна деформація деталі зазвичай незначна.
Поєднанням обертального і поступального переміщень деталі і деформуючих елементів методами обкатування, розкатування обробляють плоскі, циліндричні, перехідні поверхні, фасонні поверхні і канавки (мал. 1, а – е).
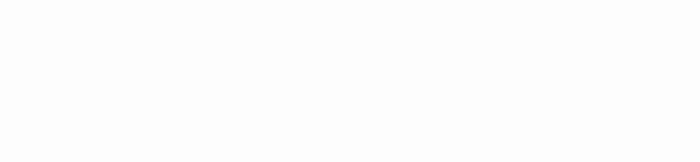
Рис. 1. Схеми процесу обкатування : а – роликом з повздовжньою подачею; б – роликом з поперечною подачею; в – фасонним роликом з поперечною подачею; г – торцевої поверхні кулькою; д – роликами поверхні шліців; е – плоскій поверхні роликом.
(Анімація, обсяг – 55,3 Кб, складається з 7 кадрів, 5 повторень, затримка кадрів 1 секунда)
Тепер перейдемо від самого процесу обробки до точності. Зміна розміру поверхні при обкатуванні і розкочуванні пов'язана зі зминаннєм мікронерівностей і пластичною об'ємною деформацією деталі. Таким чином, точність обробленої деталі залежатиме від її конструкції і конструкції інструменту, режимів обробки, а також від точності розмірів, форми і якості поверхні деталі, отриманих при обробці на попередньому переході.
Найдоцільніше обкатуванням і розкочуванням обробляти вихідні поверхні 7 – 11 квалитетів інструментами жорсткого копіюючого типу і поверхні 5 – 7 квалитетов ударним інструментом.
Основним критерієм для нас є шорсткість поверхні, тому наступний етап буде присвячений саме їй. При ППД практично досягаються параметри шорсткості оброблюваної поверхні Ra=0,2 – 0,8 мкм при початкових значеннях цих параметрів 0,8 – 6,3 мкм. Міра зменшення шорсткості поверхні залежить від матеріалу, робочого зусилля або натягу, подачі, початкової шорсткості, конструкції інструменту і так далі [2].
Одним з чинників, що впливає на процес ППД, є зусилля обкатування і розкочування поверхонь. Нижче приведена номограма їх визначення (мал. 2) [2].
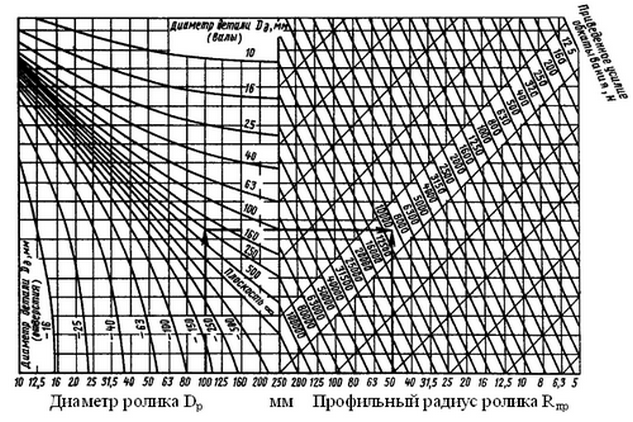
Рис. 2. Нанограма для визначення зусилля обкатування і розскатування поверхонь залежно від розмірів деталі і ролика. Наприклад, при обробки валу діаметром D=250 мм роликом діаметром Dр=100 мм з профільним радіусом Rпр=50 мм зусилля обкатування Р=9000 Н.
Алмазне випрасовування
Ще одним різновидом ППД є алмазне випрасовування. Суть процесу полягає в тому, що при випрасовуванні поверхонь інструмент (алмаз, змонтований в державці) притискається з певною силою до оброблюваної поверхні. В процесі випрасовування поверхонь в місці контакту елементу, що деформується, і оброблюваної деталі виникає значна контактна напруга і при певному зусиллі відбувається пластична деформація поверхневого шару, внаслідок чого знімаються мікронерівності і змінюються физико-механические властивості поверхневого шару. Випрасовуванням можуть оброблятися зовнішні і внутрішні поверхні обертання, а також торцеві поверхні.
При правильно підібраних режимах випрасовування мікронерівності можуть бути зменшені у декілька разів (Ra=0,1 – 0,005 мкм), мікротвердість збільшується на 5 – 60%, тобто глибина наклепаного шару може складати до 400 мкм. Як наслідок деталі мають високу зносостійкість і втомну міцність [2].
Але окрім позитивних характеристик є і негативна – за рахунок зминання початкових мікронерівностей розмір деталі може дещо зменшитися. У зв'язку з цим доцільно на попередньому переході забезпечити точність розмірів на 20 – 30% вище заданої для остаточно обробленої деталі.
Відцентрова обробка поверхневим пластичним деформуванням
У інструментах відцентрової обробки деформуючі елементи (кульки або ролики) розміщують в радіальних пазах диска. При роботі елементи можуть зміщуватися в радіальному напрямі. Диск з елементами обертається з високою швидкістю. Вони при цьому завдають численних ударів по поверхні деталі, пластично деформуючи її, після чого відскакують назад. В результаті цього шорсткість поверхні зменшується до Ra=0,1 – 0,04 мкм при початковому значенні Ra=0,8 – 3,2 мкм. Твердість поверхні збільшується на 30 – 80% при глибині наклепаного шару 0,3 – 3 мм [5].
Відцентрово-ударну обробку застосовують при виготовленні деталей з кольорових металів і сплавів, чавуну і сталі і твердістю до HRC 58 – 64. У такий спосіб можлива обробка зовнішніх і внутрішніх поверхонь, а також місця сполучення поверхонь і переривчасті поверхні.
Накочення рифлень і клем
Накочення рифлень проводять циліндричними роликами, вільно встановленими на осях в спеціальних державках. Обробку виконують на токарних, револьверних верстатах і автоматах як один з переходів обробки або як самостійну операцію на спеціальних верстатах. Рифлення на плоских поверхнях накочують на строгальных, довбальних і строгальных верстатах. Накочувані рифлення можуть бути прямими і сітчастими (ГОСТ 21474 – 75). Крок рифлень вибирають з лав: прямих – 0,5; 0,6; 0,8; 1,0; 1,2; 1,6; сітчастих – 0,5; 0,6; 0,8; 1,0; 1,2; 1,6; 2,0.
В результаті накочення відбувається збільшення зовнішнього діаметру деталі на величину 0,5 – 1,0 кроку рифлень.
Необхідний профіль рифлень отримують за п'ять – десять послідовних проходів. Число проходів залежить від матеріалу деталі, кроку і пов'язаної з ним глибини рифлень.
Схеми таврування деталей методом накочення показані на мал. 3, а – г. Накочення за схемою, приведеною на мал. 3, б, здійснюється при перекочуванні роликової каретки із заготівлею. Каретка повертається в початкове положення пружиною. Можливе накочення клейм на різьбоканатних верстатах з плоскими і круглими плашками і на інших верстатах, зручних для накочення по кінематиці робочих рухів [2].

Рис. 3. Схеми таврування деталей накоченням : а і б – плоских деталей на поперечно-стругальному і горизонтально-фрезерному верстатах, в і г – циліндричних деталей на токарному і горизонтально-фрезерному верстатах, 1 – деталь, 2 – накатний ролик, 3 – опорні ролики, 4 – каретка.
Калібрування отворів
Калібрування (деформуюче простягання, дорновання) – чистова операція обробки отворів деталей машин пластичною деформацією. Цю операцію виконують переміщення з натягом деформуючого інструменту. При l/ d<7, де l – довжина отвору і d - його діаметр, деталі обкатуються методом прошивки (мал. 4, а і б), а при l/ d>7 – методом простягання (мал. 4, в – д). Глухі отвори обробляють при зворотно-поступальному русі оправки (мал. 4, д). Розрізняють обробку із стискуванням (мал. 4, в) і з розтягуванням (мал. 4, г). Найчастіше обробку ведуть із стисканням.
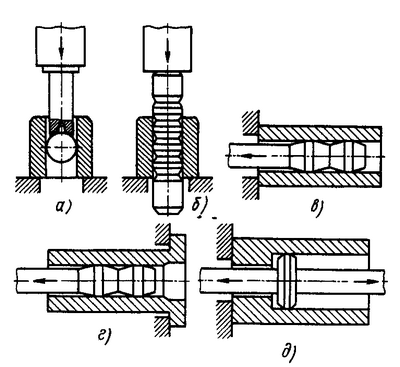
Рис. 4. Схеми обробки отворів : а і б – прошивкою за допомогою кульки і оправки; в – із стискуванням деталі; г – з розтягуванням деталі; д – при зворотно-поступальному ході оправляння.
Інструментом для обробки при калібруванні служать оправки або кульки. Обробка кульками не забезпечує оптимальних умов деформації – елементи мають малу розмірну стійкість. Проте кульки застосовують в промисловості зважаючи на простоту процесу обробки і можливості його автоматизації.
Матеріал деформуючих елементів (твердий сплав ВК15, ВК15М) забезпечує високу зносостійкість інструменту і високу вигинисту міцність. При малих навантаженнях на інструмент можна застосовувати сплав ВК8.
Шорсткість поверхні залежить від попередньої точності обробки. При обробці отворів в товстостінних деталях після переходів розточування або розгортання (початковий параметр Ra=6,3 – 1,6 мкм) отримують поверхні з Ra=0,8 – 0,1 мкм, якщо матеріал деталей сталь, Ra=0,4 – 0,1 мкм при обробці деталей з бронзи і Ra=1,6 – 0,4 мкм при обробці деталей з чавуну. Шорсткість поверхонь тонкостінних деталей в 2 – 4 рази вище.
Шліфування
Шліфуванням називають абразивну обробку, при якій інструмент здійснює тільки обертальний рух, який є головним рухом різання, а заготівля – будь-який рух.
Шліфування – один з прогресивних і універсальних методів остаточної обробки різних поверхонь деталей машин, до яких пред'являються високі вимоги по точності розмірів, геометричної форми і якості обробки.
Кругле шліфування периферією і торцем круга
Кругле шліфування периферією і торцем круга призначене для обробки деталей типу тіл обертання і являється основним способом, що забезпечує високу точність. Воно може здійснюватися з установкою деталі в необертальних центрах і в кулачковому або цанговому патроні шпинделя верстата, що обертається [7].
Кругле шліфування можна здійснювати як периферією круга (в основному), так і його торцем; при цьому в якості різальної частини використовують зовнішню і торцеву поверхню щлифовального круга.
Застосовують наступні основні операції круглого шліфування : обдирне, попереднє, остаточне (чистове), тонке і вигладжування.
Внутрішнє шліфування
Способом внутрішнього шліфування обробляють циліндричні, конічні і профільні отвори.
При внутрішньому шліфуванні в патроні і безцентровому шліфуванні подача здійснюється внаслідок обертання деталі із швидкістю vд. При внутрішньому шліфування великогабаритних деталей деталь нерухома, а шпиндель шліфувального круга здійснює обертання навколо осі оброблюваного отвору.
Безцентрове шліфування
При безцентровому шліфуванні деталь не закріплюють в центрах або в патроні, а базують по оброблюваній або раніше обробленій поверхні.
Деталь отримує обертання від провідного круга, окружна швидкість якого в 60 – 100 разів менша, ніж швидкість шліфувального круга.
Профільне шліфування
Шліфування поверхонь, твірна яких є кривою або ламаною лінією, називають профільним шліфуванням.
Зубошліфування
Найбільше застосування в машинобудуванні отримали зубчасті колеса із загартованих сталей з твердістю робочих поверхонь HRC 48 – 60, які виконують 4 – 7-ої мірі точності залежно від умов роботи. Шліфування зубів може здійснюватися методом копіювання або обкатування.
Швидкісне, обдирне і глибинне шліфування
Швидкісне, обдирне і глибинне шліфування інтенсифікує процес і дозволяють підвищити продуктивність обробки, понизити трудомісткість і вартість операції.
Швидкісне шліфування є найбільш відомим високопродуктивним методом абразивної обробки. Цей метод можна робити різними способами [3]:
- Шліфування з підвищеною швидкістю обертання круга без зміни інших складових режиму шліфування. В цьому випадку будуть забезпечені низькі параметри шорсткості поверхні шліфованої деталі і підвищена стійкість круга, що понизить число правок, швидкість зношування кругів і допоміжний час. Процес шліфування відбувається при менших силах.
- Шліфування з підвищеною швидкістю обертання круга при одночасному пропорційному збільшенні частоти обертання деталі або подовжньої або окружної швидкості столу (залежно від типу верстата, на якому здійснюється обробка) без збільшення поперечних подач. В цьому випадку продуктивність обробки підвищується при зниженні машинного часу пропорційно збільшенню швидкості обертання і стійкості круга. Шорсткість поверхні і сили шліфування будуть тими ж, що і до підвищення швидкості обертання круга.
- Шліфування з підвищеною швидкістю обертання круга при одночасному пропорційному збільшенні частоти обертання деталі і швидкості переміщення столу (на плоскошліфувальних верстатах) і збільшенні поперечних подач круга. При цьому різко зростає продуктивність шліфування, але зменшується стійкість круга, збільшується шорсткість поверхні.
Недоліки швидкісного шліфування : зростає потужність шліфування; збільшується виділення теплоти, що може привести до появи прижогів. Прижогів можна уникнути шляхом підвищення швидкості оброблюваної деталі і вдосконалення складів і способів підведення технологічних засобів, що мастильний-охолоджують.
Обдирне шліфування
Обдирне шліфування, що забезпечує значні знімання оброблюваного матеріалу, знаходить усе більш широке застосування в машинобудуванні. Воно призначене для видалення із заготовок шару після литва, кування, штампування, плющення, зварювання [7].
Обдирне шліфування здійснюють периферією круга, що має гладкий і фасонний профіль, і торцем шліфувального круга. У останньому випадку найчастіше використовують сегментні або переривчасті круги.
При обдирному шліфуванні продуктивність шліфування підвищується до 6 разів і знімається значний припуск (до 7 мм на сторону).
Глибинне шліфування
Глибинне шліфування є різновидом обдирного шліфування. Проте, у ряді випадків, глибинне шліфування по якості оброблюваної поверхні, що досягається, може бути чистовим.
Глибинне шліфування застосовують для профільного шліфування, у тому числі широкими кругами, для шліфування стружкових канавок на свердлах, гребінок, пазів; при шліфуванні резьб, зубів і черв'яків і деталей паливної апаратури і при алмазній обробці твердосплавних різальних інструментів.
4. Економічність механічної обробки
При виборі економічних режимів обробки необхідно враховувати технічні характеристики металорізальних верстатів. В якості обмежень при виборі економічних режимів різання можна розглядати наступні характеристики верстатів:
- Максимальну подачу;
- Максимальну частоту обертання шпинделя;
- Максимальну потужність приводу;
- Максимально допустиму силу різання;
- Межі подачі (чи швидкості), що забезпечують необхідну шорсткість обробленої поверхні;
- Ступені швидкостей і подач.
Собівартість обробки деталі складається з декількох статей [6]. Для простоти розглянемо обробку одним інструментом:
- Непродуктивні витрати С1, що доводяться на одну деталь, включають вартість закріплення і зняття однієї деталі, вартість простою устаткування.
- Вартість машинного часу обробки С2.
- Вартість часу на зміну інструменту С3.
- Вартість інструменту, віднесена до однієї деталі С4.
- Вартість матеріалу С5.
Собівартість деталі може бути понижена шляхом скорочення часу закріплення і зняття деталі, часу простою і часу зміни інструменту. Для цього можуть бути використані як технічні так і організаційні методи. Вдосконалення матеріалу інструменту і заточування підвищує стійкість інструменту, зменшує кількість змін інструменту і вартість заточування, що доводиться на одну деталь, тим самим знижуючи собівартість деталі. Знос різального інструменту може бути знижений шляхом зміни властивостей оброблюваного матеріалу. Збільшення швидкості різання може мати зворотний вплив на собівартість деталі, оскільки вона зменшує стійкість інструменту.
Продуктивність обробки зворотньо пропорційна до часу обробки і залежить від режимів різання і стійкості інструменту.
Чинники, що знижують собівартість деталей і збільшують продуктивність обробки, збільшують і прибуток в одиницю часу.
Висновки
Таким чином, можна підсумувати, що при виборі способу фінішної обробки, окрім основних критеріїв (шорсткості, точність обробки), важливими є такі поняття як собівартість і продуктивність обробки. На базі аналізу відповідних величин повинно прийматися оптимальне рішення.
Перелік посилань:
- Тонкое точение. [Электронный ресурс]. – Режим доступа: http://machinetools.aggress.ru....
- Справочник технолога-машиностроителя. Т 2 / Под ред. А.Г. Косиловой и Р.К. Мещерякова. – 4-е изд., перераб. и доп. – М.: Машиностроение, 1985. – 496 с.
- Кащук В.А., Верещагин А.Б. Справочник шлифовщика. – М.: Машиностроение, 1988. – 480 с.
- Бруштейн Б.Е., Дементьев В.И. Токарное дело. Учебник для проф.-техн. училищ. Изд. 6-е, переработ. И доп. М., «Высшая школа», 1967 г. – 448 с.
- Браславский В.М. Технология обкатки крупных деталей роликами, 1987 г. – 159с.
- Армарего И.Дж.А., Браун P.Х. Обработка металлов резанием. Пер. с англ. В.А.Пастунова. М.: Машиностроение, 1977. – 325с.
- Наерман М.С. Справочник молодого шлифовщика. – М.: Высш. шк., 1985. – 207 с., ил. – (Профтехобразование).