Abstract
Content
- Introduction
- 1. Task statement
- 2. Theme actuality
- 3. The analysis of existing methods for producing high quality surfaces in shaft and sleeves type details
- 4. Machining economy
- Conclusions
- Literature
Introduction
Now requirements to quality of surfaces have considerably risen that is linked with special requirements of product usage. It is caused by a considerable step forward of all techniques of machining – high-precision machine tools had appeared and instruments were improved. Also the important fact is that alternative variants of handlings exist. For example, if for any reasons it is impossible to execute grind, plastic deformation, and the surface should be exact enough, multiple thin turning usage is possible.
1. Task statement
The purpose of the this abstract is the analysis of variants of reaching a demanded roughness at various machining ways, comparison of results, and also definition of their influence on physical and mechanical properties of a constructional materials blanket at their handling.
Object of research – technique of critical details surfaces finish machining of bodies of revolution (shafts and sleeves) type from constructional materials.
Subject of research – the processes occurring in a material blanket at mechanical effect on it, and a choice justification of a rational mode of handling by criterion of the minimum cost price.
2. Theme actuality
In this abstract consideration of possible variants of a critical parts surfaces finish machining of revolution type bodies from constructional materials (on an example of the doped steels) is supposed. On the basis of the received results detection of the mode ensuring the minimum cost price of handling is planned, while respecting requirements on exactitude and quality of machining.
3. The analysis of existing methods for producing high quality surfaces
in shaft and sleeves type details
Delicate turning and a boring work
This turning method is widely applied in aviation, tractor and automobile industries at machining of cylindrical and conic surfaces (external and internal), and also end surfaces, ledges, etc. Exactitude of details sizes corresponds to 2nd, and sometimes to 1st accuracy class [1].
Surface plastic deformation
The essence of process consists in the following. At manufacture of machine parts surface plastic deformation (SPD) is applied – processing by pressure at which only the blanket of a detail material is plastically deformed [2].
Surfaces running and reeling out
Processing is carried out with rollers and balls putting pressure upon a surface of a part. Volumetric deformation of a part is usually insignificant.
Combining rotational and translational motions of a part and deforming elements by using running and reeling out methods, flat, cylindrical, transitive surfaces, contours and grooves are processed (fig. 1, а – е).
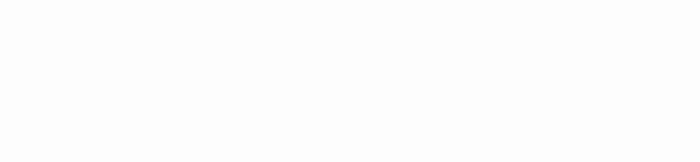
Scheme of the running process: a – with a help of a roller with a longitudinal feeding; b – with a help of a roller with cross-section feeding; c – with a help of a shaped roller with cross-section feeding; d – of a end surface with a help of a ball; e – surface of the slots with a help of rollers; f – a flat surface with a help of a roller.
(Animation, volume – 55,3 kb, 7 frames, 5 cycle repeat, 1 second)
One of the factors influencing SPD process is a force of surfaces running and reeling out. The nomogram of their calculation is showed below (fig. 2) [2].
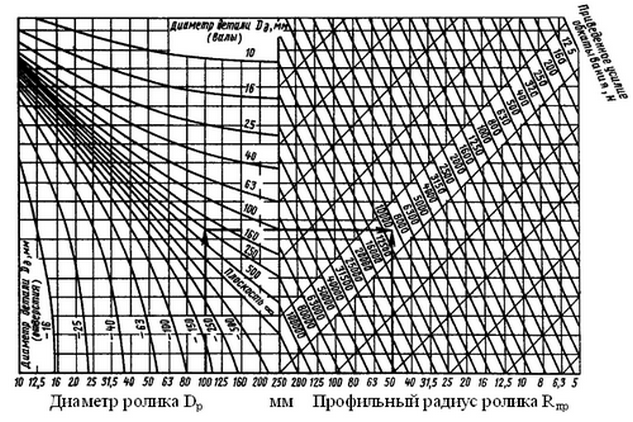
Fig. 2. Nomogram for calculating force of surfaces running and reeling out depending on the sizes of a part and a roller. For example, at processing of the shaft in diameter of D=250 mm with a help of a roller in diameter of Dr=100 mm with of Rcs=50 mm running force is Р=9000 Н.
Diamond smoothing
The essence of process is that at surfaces smoothing the tool (the diamond mounted in holder) nestles with certain force on a processed surface. External and internal surfaces of rotation, and also end surfaces can be processed with smoothing.
At correctly picked smoothing modes microroughnesses can be reduced several times (Ra=0,1 – 0,005 micron), microhardness increases by 5 – 60 %, i.e. depth of the riveted layer can constitute to 400 microns. As consequence a partpossess high wear resistance and fatigue durability [2].
Centrifugal processing by superficial plastic deformation
In tools of centrifugal processing (balls or rollers) deforming elements are placed in radial grooves of a disk. At processing elements can be displaced in a radial direction. The disk with elements rotates with high speed. They thus strike numerous blows to a detail surface, plastically deforming it and then jump aside back. As a result of it the surface roughness raises to Ra=0,1 – 0,04 micron compared with the initial value Ra=0,8 – 3,2 micron. Hardness of a surface increases by 30 – 80 % at depth of the riveted layer of 0,3 – 3 mm. [5]
Rolling of corrugations and stamps
A corrugations rolling is carried out by the cylindrical rollers freely mounted on shafts in special holders. As a result of a rolling there is an increase in outside diameter of a part on the value of 0,5 – 1,0 steps of corrugations.
Necessary profile of corrugations is received for five – ten consecutive passes. The number of passes depends on a material of a part, a step and the corrugations depth linked with it.
Schemes of a parts stamping by a rolling method are displayed on fig. 3. Rolling by the scheme displayed on fig. 3, is carried out at rolling the roller carriage with preform [2].

Fig. 3. Schemes of a parts stamping by rolling: a and b – flat parts on cross-planing and horizontal–milling machines, c and d – cylindrical parts on turning and horizontal-milling machines, 1 – a part, 2 – knurled roller, 3 – support rollers, 4 – the carriage.
Calibration of holes
A calibration (a deforming drawing, mandrelling) – finishing operation of machining holes in mechanisms parts by plastic deformation. This operation is carried out by moving a deforming instrument with tension. At l/d <7 where l – length of a hole and d – its diameter, parts are run in by a suturing method (fig. 4, a and b), and at l/d> 7 – a pulling method (fig. 4, c – d). Blind holes are processed by reciprocation of mandrel (fig. 4, e). There are processing with compression (fig. 4, c) and with stretching (fig. 4, d). Most frequently processing is carried out with compression.
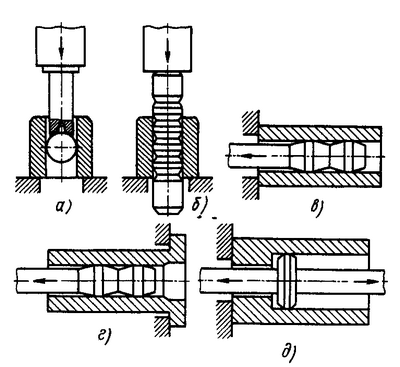
Fig. 4. Scheme of holes handling: a and b – suturing using a ball and mandrel; c – with detail compression; d – with a detail tension; e – at a reciprocation of a mandrel.
Grinding
Grinding – one of progressive and multiple-purpose methods of final processing of various parts surfaces for mechanisms which meet high demands on exactitude of the sizes, geometrical shape and quality of machining.
Round grinding by periphery and end face of a disk
Round grinding by periphery and end face of a disk is intended for processing parts such as bodies of revolution and is the basic way of ensuring high accuracy. It can be carried out with part installation in unrotative centers and in a jaw or a draw-in chuck of a gyrating spindle of the machine.
Internal grinding
With a help of internal grinding cylindrical, conical and cross-sectional holes are processed [7].
At internal grinding in a cartridge and centerless grinding feeding is carried out through rotation of a part with a speed Vp. At internal grind of large-sized parts the part is motionless, and the grinding wheel spindle makes rotation round an axis of a processed hole.
Centerless grind
At centerless grind a part isn’t fixed in the centers or in a cartridge, and is placed on processed or previously processed surface.
The part receives rotation from the leading disk which circumferential speed is in 60 – 100 times less, than a speed of a disk.
Cross-sectional grinding
Grinding of the surfaces, which generatrix is a curve or a polygonal line, is called cross-sectional grinding.
Gear grinding
The greatest application in machine industry was received by tooth gears from tempered steels with hardness of working surfaces HRC 48 – 60 which are produced with 4th – 7th degree of accuracy depending on working conditions. Grinding of tooth can be carried out with a method of copying or running [7].
4. Machining economy
At a choice of economic conditions of processing it is necessary to consider technical characteristics of metal-cutting machines [6].
The cost price of a part processing sums up from several expenditures. For simplicity we will look through processing by one instrument.
- Non-production expenditures C, on a one part, include cost of fixing and removal of one part, equipment downtime cost.
- Cost of a machining time С2.
- Cost of time for instrument change C3.
- Cost of the instrument which has been attributed to one part С4.
- Cost of material С5.
The part cost price can be lowered by abbreviation of a part fixing and removal time, down time and time needed to change the instrument. Both technical and organizational methods can be used for this purpose.
Productivity of machining inversely proportional to a machining time and also depends on conditions of cutting and durability of the instrument.
The factors reducing the cost price of parts and increasing productivity of machining also augment profit per unit of time.
Conclusions
Thus, it is possible to sum up that at a choice of a finish machining way, besides the basic criteria (roughnesses, exactitude of machining), such concepts as the cost price and productivity of machining are important. On the basis of the corresponding values analysis the optimum decision must be made.
Literature
- Тонкое точение. [Электронный ресурс]. – Режим доступа: http://machinetools.aggress.ru....
- Справочник технолога-машиностроителя. Т 2 / Под ред. А.Г. Косиловой и Р.К. Мещерякова. – 4-е изд., перераб. и доп. – М.: Машиностроение, 1985. 496 с.
- Кащук В.А., Верещагин А.Б. Справочник шлифовщика. &ndash М.: Машиностроение, 1988. – 480 с.
- Бруштейн Б.Е., Дементьев В.И. Токарное дело. Учебник для проф.-техн. училищ. Изд. 6-е, переработ. И доп. М., «Высшая школа», 1967 г. – 448 с.
- Браславский В.М. Технология обкатки крупных деталей роликами, 1987 г. – 159с.
- Армарего И.Дж.А., Браун P.Х. Обработка металлов резанием. Пер. с англ. В.А.Пастунова. М.: Машиностроение, 1977. – 325с.
- Наерман М.С. Справочник молодого шлифовщика. – М.: Высш. шк., 1985. – 207 с., ил. – (Профтехобразование).