Abstract
Content
- Introduction
- 1. Overview of inert additives
- 2. The main directions of inert additives
- 3. Removal of surface deffekts
- 4. The operating principle of inert additives
- 5. Accounting for the viscosity of raw materials
- 6.Uvelichenie performance
- 7. Additives oblegchabschie processing of polymers
- Findings
- List of sources
Introduction
With the introduction of inert additives on the stage of granulation mixture is more homogeneous, the producer of raw materials is well aware of the peculiarities of each particular brand and are able to choose the most suitable product. On the other hand, when administered at the stage of granulation can not take into account the peculiarities of processing equipment, modes that are selected for processing, etc. This leads to the fact that some manufacturers of additives is redundant (that is, in principle, does not impair the processability, but also affects the price), but not enough for some. Typically, manufacturers of raw materials enter the minimum number of inert additives, so as not to unduly increase the price, and recommend to introduce an additional amount of inert additives during processing if necessary.
1. Overview of inert additives
There are two main methods for the introduction of inert additives in the feed. The first - the manufacturer of the polymer enters the inert additive in the granulation step after the synthesis of the polymer and the second - the introduction of additives directly to the processing of raw materials in the product. Both methods have their advantages and disadvantages. The second way - the introduction of in-process in the product - is more flexible because allows to take into account features of the equipment and operation modes, and use different brands of raw materials, simply by changing the dosage of an inert additive. However, this method is the complexity. The effectiveness of inert additives is highly dependent on the quality of their mixing with the basic raw material. Inert additives are introduced into a very small amount (0.04-0.05%, or 400-500 ppm), and in order to achieve high-quality mixed with recyclable material must be used masterbatches. Materials on the market contain from 2 to 5% of an inert additive. Since fluoroelastomers are not compatible with polyethylene, they form a discontinuous phase in a matrix of polyethylene. The smaller the particle size, the higher the efficiency of masterbatches. In any case, for optimal particle size should not exceed 2 mcm.
2. The main directions of inert additives
Inert additives used to improve the following performance parameters: 1. Removal of surface defects and anomalies arising from the excess viscosity and shear stress. Two. Preventing the formation of deposits and sludge in the shaping tool. Three. The increase in productivity. 4. Reducing the number of helico. Five. Facilitating the processing of carbonaceous materials. Initially, inert additives have been developed to facilitate the processing of polyethylene, so much of the data obtained in the investigation of this application. However, in addition to the production of such films are inert additives used in the extrusion of pipes, profiles and fibers, blown molding and injection molding. Furthermore, the inert additives used and the processing of HDPE (HDPE), linear metallocene polyethylene, polypropylene, plastomers (polyolefin plastomers), thermoplastic elastomers, polystyrene and its copolymers, polyamide, polyacrylates, etc[1].
3. Removal of surface deffekts
Until now, the mechanism of this phenomenon is the subject of discussion. However, we note two main causes of this phenomenon. The first - due to the difference of the coefficient of internal friction of the polymer and the coefficient of friction material on a metal snap-flow velocity in the middle of the melt flow near the wall, and vary greatly. Once the material leaves the gap, the rate begin to level off, and in the boundary layer having large shear stresses causing rupture of the melt at this point. This effect is enhanced by intense cooling of the cold air as cooling down the melt elasticity. Usually the result of this phenomenon can be seen on the outer surface of the film. On the inner surface of microscopic appear very rarely, on machines with internal cooling sleeve with strong blowing cold air. The second - an anomaly of viscosity (slip-stick phenomenon), which developed in the near-wall layers, which is the cause of the defects on the surface of the extrudate (unstable flow), disruption of the jet and slug flow. The mechanism of these phenomena is the sharp increase in High-strain under high velocity and shear stress in the near-wall layers. For certain values ??of flow velocity and in High-strain in the outer layers of a wall and the outer layer separation occurs in the form of a ring (ie, resulting stress becomes greater than the strength of the adhesive interaction between the polymer - metal). At the exit of the die ring is the outer layer relaxes (ie, rotated in a vertical plane), resulting in a distortion in the form of "Christmas trees" and other violations of the film surface. In the limit, with an increase in pressure or shear rate above the critical value, the near-wall layers is the failure of the jet at which the melt flows relative to the outer layer, rather than the capillary walls. Increased shear flow of cork attached to the character of the sharply increased costs. Cork can be realized within and without disruption of the jet due to slip in the outer layer of the polymer with low viscosity that is observed when administered in low-viscosity material components. Both theories operate on the concept of critical shear stress (or critical shear rate). The introduction of inert additives significantly delays the process of reaching this critical value[1].
4 The principle of inert additives.
Profile distribution of the velocity of the melt of carbon mass in the slit gap of die depends on the presence of additives. (Fig. 1)

Figure 1 - Distribution of the velocity of the melt mass of carbon: A - in the absence of additives, B - in the presence of an inert additive
The quality of mixing additives with the carbon mass - a very important factor, the smaller the particle additive, the greater their number reaches the surface of the head of a unit of time. With the passage of melt through the head of the particles of inert material gradually reach the surface of the head, and, eventually, form a sliding layer. It should be noted that the introduction of inert additives may be fluctuations in performance due to the uneven surface of the coating head at an early stage. After some time, which is called the air-conditioning (usually 15-20 minutes), the process is stabilized, surface defects disappear, the load on the shaft is greatly reduced. The particles of inert material is gradually taken away from the surface of the head of the melt material. Various abrasive substance in carbon mass (pigments, antiblokingi, etc.) accelerate this process. Thus, there is an equilibrium point between the deposition of inert material on the surface of the head of the melt and its entrainment. The process conditions (temperature, velocity, and other additives) affect the ratio of the rate of entrainment and deposition of additives, and therefore a change in conditions must be adjusted and the content of inert material[2].
5. Accounting for the viscosity of raw materials
Inert additives should be chosen taking into account the viscosity of the processed polymer. Most supplements on the market, designed for a linear LDPE with MFI = 2.1 g/10 min. or just below, and bimodal HDPE with broad molecular weight distribution.
The viscosity of raw materials depends on the molecular - mass composition, and many chemical properties. Type and number of functional groups can also affect the performance of inert additives. According to some literature data, possible interaction with the addition of acid groups oxides and hydroxides on the surface of the head, improves adhesion. At the same time, other research groups have reported a lack of effectiveness of additives depending on the content of functional groups, while others report a negative impact on the property. Apparently, it depends on the compatibility of specific additives to the material specific die and can not be accounted for in advance. Consequently, experimental studies are needed in each case.[1]
Experimental studies have shown that one of the factors influencing the effectiveness of inert additives is the gradient of shear stress. At high shear rates has a melt flow is quite sharp (see Figure 1). The gradient of the stress strongly promotes the inert additives to the walls of the channel. However, if the shear rate is very high, it starts an anomaly of viscosity, which prevents the addition of a uniform coating of the channel walls. Thus, the optimal speed when air conditioning is the maximum, but does not cause the formation of "herringbone". Shear stress is inversely proportional to the temperature-dependent, ie You can change the flow regime as the speed increases, and by lowering the temperature, which leads to an increase in shear stress and may contribute to more effective deposition of inert additives on the channel walls. In Fig. 3 shows that the air conditioning polypropylene is faster at lower temperatures, as at this point, the shear stress is close to critical.
Therefore, one should note the importance of careful selection and control of temperature, which is usually neglected. An example is the relationship shown in Fig. 2.
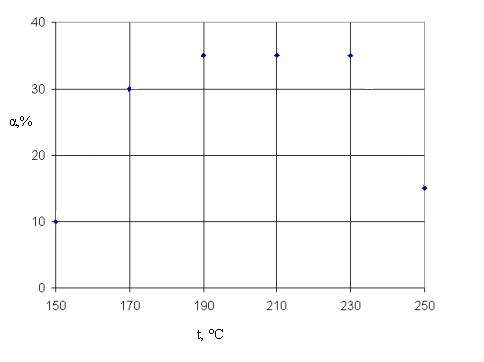
Figure 2 – Dependence of pressure drop C,% In the spinneret, depending on the temperature t,°C of material.
Preventing the formation of carbon deposits on the shaping tool.
Another important advantage of the use of inert additives is a significant reduction in soot forming on the surface. It should be noted that soot is formed not only at the exit slit of the melt gap head, which leads to the formation of bands on the film, but inside the extrusion head, the screw channels, which leads to decreased productivity, increased gage, the formation of a large number of helico, etc. etc. The deposits are typically low molecular weight components of the scorched mass of carbon and residues of pigments, fillers and additives (sliding, antistatic agents) with low thermal stability. Removal of sediment on the surface, and form-building tool in the channels is due to the formation on the metal layer of an inert additive that prevents the buildup of carbon mass, reduces the residence time of material and, consequently, the thermal degradation. In addition, inert additives have a cleaning effect, displacing the black dots on the screw head and at an early stage. Out of a large number of black pixels after the introduction of inert additives can last from minutes to hours, depending on the contamination of the extruder and the concentration of additives and process parameters (temperature, pressure, velocity). Therefore, in order to save time and material equipment before using additives must be cleaned with special concentrates or mechanically.
.6. The increase in productivity.
Increased productivity is one of the determining factors in minimizing costs and reducing production costs. To increase the productivity can be attributed not only to yield the final product, but also reduce the time for cleaning and maintenance of equipment, reducing the number of marriages, etc. The use of inert additives facilitates the process of polymer melt flow in narrow channels, significantly reduces the pressure in the head and the load on the shaft. In Fig. 3 presents data on the pressure in the head compared to mixtures. The comparison was made at the same temperature and performance[3].
Figure 3 - The pressure in the spinneret for mixtures with different contents of polyethylene>
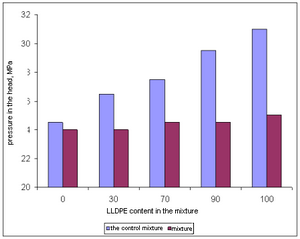
Figure 3 - The pressure in the spinneret for mixtures with different contents of polyethylene
7. Additives to facilitate the processing of polymers.
Addition of 1 - masterbatch containing fluoroelastomer in the matrix of linear polyethylene. Designed specifically for the extrusion of linear polyethylene of high density polyethylene. Increases the transparency of the films and the performance of the process.
Addition of 2 - Represents the variance in a transparent heat-resistant polyorganosiloxane polystyrene. Designed specifically for sheet extrusion polystyrene. Improves performance and stability of the process and allows to obtain shiny, glossy product with less unevenness.
Addition of 3 - represents a variance of fluoroelastomer in polypropylene. Designed specifically for extrusion of pipes and profiles made of polypropylene. Allows you to increase the productivity of the process and improve the surface quality of products made of polypropylene[1].
Findings
In accordance with the theory of the destruction of one of the main parameters affecting the strength properties of the material is the amount of microdefects on the surface of the product. The use of fluoroelastomers allows to obtain films with improved physical and mechanical properties, as decreases the amount of surface defects due to the reduction of shear stress on the output of the polymer forming the head.
List of sources
- Доступно о полимерах [Электронный ресурс]. Режим доступа:http://www.plastichelper.ru/
- Аналитический портал химической промышленности. [Электронный ресурс]. Режим доступа:http://newchemistry.ru
- Клинков А.С., Беляев П.С., Скуратов В.К., Соколов М.В., Однолько В.Г.. -Тамбов : Изд-во Тамб. гос. техн. ун-та, 2010., - 100 с.