Реферат за темою випускної роботи
Зміст
- Вступ
- 1. Загальні відомості про інертні добавки
- 2. Основні напрямки застосування інертних добавок
- 3. Усунення поверхневих дефектів
- 4. Принцип дії інертних добавок
- 5. Облік в'язкості сировини
- 6. Збільшення продуктивності
- 7. Добавки полегшуючі переробку полімерів
- Висновки
- Перелік посилань
Вступ
При введенні інертних добавок на стадії грануляції змішання виходить більш однорідним, виробник сировини добре знає особливості кожної конкретної марки, і в змозі підібрати найбільш відповідний продукт. З іншого боку, при введенні на стадії грануляції неможливо врахувати особливості переробного обладнання, режимів, які будуть обрані для переробки і т.д. Це призводить до того, що для деяких виробників кількість добавки є надлишковим (що, в принципі, не погіршує нафтових, але впливає на ціну), а для деяких недостатнім. Зазвичай виробники сировини вводять мінімально необхідну кількість інертних добавок, щоб не збільшувати невиправдано ціну, і рекомендують вводити додаткову кількість інертних добавок в процесі переробки при необхідності.
1. Загальні відомості про інертні добавки
Існують два основні методи введення інертних добавок в сировині. Перший - виробник полімеру вводить інертну добавку на стадії грануляції полімеру після синтезу і другий - введення добавок безпосередньо при переробці сировини в продукт. Обидва методи мають свої переваги і недоліки. Другий шлях - введення на стадії переробки у виріб - більш гнучкий, тому що дозволяє враховувати особливості устаткування і режимів, а також використовувати різні марки сировини, просто змінюючи дозування інертної добавки. Але й при цьому методі є складнощі. Ефективність інертних добавок дуже сильно залежить від якості їх змішання з базовим сировиною. Інертні добавки вводяться в дуже невеликій кількості (0,04-0,05% або 400-500 ppm) і для того, щоб досягти якісного змішання з переробляється необхідно використовувати суперконцентрати. Представлені на ринку матеріали містять від 2 до 5% інертної добавки. Так як фтореластомери не сумісні з поліетиленом, вони утворюють дисперсну фазу в матриці поліетилену. Чим менше розмір часток, тим вище ефективність суперконцентрати. У будь-якому випадку для оптимальної роботи розмір часток не повинен перевищувати 2 мкм.
2. Основні напрямки застосування інертних добавок
Інертні добавки використовуються для поліпшення наступних параметрів виробничого процесу: 1. Усунення поверхневих дефектів, що виникають внаслідок аномалії в'язкості і надлишкових зсувних напруг. 2. Попередження утворення відкладень і нагару на формотворне інструменті. 3. Збільшення продуктивності. 4. Зниження кількості гелик. 5. Полегшення переробки вуглецевих матеріалів. Спочатку інертні добавки розроблялися для полегшення переробки поліетилену, тому більша частина даних отримана при дослідженні цієї області застосування. Однак, крім виробництва таких плівок інертні добавки використовуються при екструзії труб, профілів і волокон, при екструзійно-роздувне формування та лиття під тиском. Більш того, інертні добавки застосовуються і при переробці ПЕВЩ (ПНД), металлоценового лінійного поліетилену, поліпропілену, пластомеров (polyolefin plastomers), термопластичних еластомерів, полістиролу та його кополімерів, поліаміду, поліакрилатів і т.д.[1].
3. Усунення поверхневих дефектів
До сих пір механізм виникнення цього явища є предметом обговорення. Тим не менш, можна відзначити дві основні причини виникнення такого явища. Перше - внаслідок різниці коефіцієнта внутрішнього тертя полімеру і коефіцієнта тертя матеріалу по металевій оснащенні швидкості течії в середині потоку розплаву і біля стінки розрізняються дуже сильно. Як тільки матеріал виходить з зазору, швидкості починають вирівнюватися, і в пристінному шарі виникають великі зсувні напруги, що викликають розрив розплаву в цьому місці. Цей ефект посилюється при інтенсивному охолодженні розплаву холодним повітрям, тому що при охолодженні знижується еластичність розплаву. Зазвичай результат цього явища видно на зовнішній поверхні плівки. Мікророзриви на внутрішній поверхні проявляються дуже рідко, на машинах з внутрішнім охолодженням рукава при сильному охолодженні охолодженим повітрям. Друге - це аномалія в'язкості (slip-stick phenomenon), що розвинулася в пристінних шарах, яка є причиною виникнення дефектів на поверхні екструдату (нестійке перебіг), зриву струменя і пробкового течії. Механізм цих явищ полягає в різкому зростанні високоеластіческой деформації під дією високих швидкості і напруження зсуву в пристінних шарах. При певних значеннях швидкості течії і високоеластіческой деформації в зовнішньому і пристінному шарах настає відрив зовнішнього шару у вигляді кільця (тобто виникають напруги стають більше міцності адгезійного взаємодії полімер - метал). На виході з головки екструдера це кільце зовнішнього шару релаксує, (тобто повертається у вертикальній площині), в результаті чого утворюється спотворення в формі «ялинки» та інші порушення поверхні плівки. У межі, зі збільшенням тиску або швидкості зсуву вище критичного, в пристінних шарах відбувається зрив струменя, при якому розплав тече щодо зовнішнього шару, а не стінок капіляра. Збільшені швидкості зсуву надають течією корковий характер з різко збільшеними витратами. Коркове течія може бути реалізовано і без зриву струменя за рахунок ковзання в зовнішньому шарі полімеру з низькою в'язкістю, що спостерігається при введенні в сировині низьков'язких компонентів. Обидві теорії оперують поняттям критичної напруги зсуву (або критичної швидкості зсуву). Введення інертних добавок суттєво затримує процес досягнення цієї критичної величини[1].
4 Принцип дії інертних добавок
Профіль розподілу швидкості руху розплаву вуглецевої маси в щілинному зазорі фільєри істотно залежить від наявності добавки. (Рис. 1)

Рисунок 1 - Розподіл швидкості руху розплаву вуглецевої маси: А - при відсутності добавки, Б - при наявності інертної добвкі
5 Облік в'язкості сировини
Інертні добавки слід вибирати і з урахуванням в'язкості переробляється полімеру. Більшість добавок, представлених на ринку, розроблені для лінійного ПЕНЩ з ПТР = 1-2 г/10 хв. або трохи нижче і бімодального ПЕВЩ з широким молекулярно масовим розподілом.
В'язкість сировини залежить від молекулярно - масового складу і багатьох хімічних властивостей. Тип і кількість функціональних груп також можуть впливати на експлуатаційні якості інертних добавок. За деякими літературними даними можлива взаємодія кислотних груп добавки з оксидами і гідроксидами на поверхні головки, що покращує адгезію. У той же час, інші дослідницькі групи повідомляють про відсутність залежності ефективності добавки від змісту функціональних груп, а треті повідомляють про негативний вплив на властивості. Мабуть, це залежить від сумісності конкретної добавки з матеріалом конкретної фільєри, і не може бути враховано заздалегідь. Отже, необхідні експериментальні дослідження в кожному випадку[1].
Експериментальні дослідження показали, що одним з факторів, що впливає на ефективність інертних добавок є градієнт зсувних напруг. При великих швидкостях зсуву профіль течії розплаву досить гострий (див. рис 1). Градієнт напруг сильно сприяє просуванню інертної добавки до стінок каналу. Однак, якщо швидкість зсуву дуже висока, то починається аномалія в'язкості, що перешкоджає однорідному покриттю добавкою стінок каналу. Таким чином, оптимальною швидкістю при кондиціонуванні є максимальна, але не викликає утворення «ялинки». Зсувні напруги обернено пропорційно залежать від температури, тобто змінити режим течії можна як збільшенням швидкості, так і шляхом зниження температури, що призводить до збільшення зсувних напруг, і може сприяти більш ефективному осадженню інертної добавки на стінках каналу. На рис. 3 видно, що кондиціювання поліпропілену відбувається швидше при більш низькій температурі, тому що в цій точці напруга зсуву близький до критичного. Тому, слід зазначити важливість ретельного вибору та контролю температури, яким зазвичай нехтують. Прикладом може служити залежність, представлена ??на рис. 2.
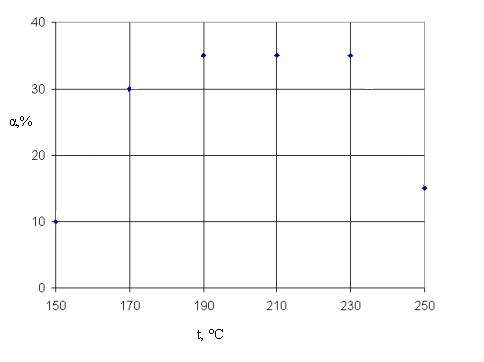
Рисунок 2 - Залежність зниження тиску?,% В філь'єрі в залежності від температури t, ° C сировини.
6. Збільшення продуктивності
Збільшення продуктивності є одним з визначальних чинників у мінімізації витрат і зниження собівартості продукції. До збільшення продуктивності можна віднести не тільки вихід готового продукту, але і скорочення часу на очищення і обслуговування устаткування, зниження кількості браку і т.д. Застосування інертних добавок полегшує процес течії розплаву полімеру у вузьких каналах, значно знижує тиск у головці і навантаження на валу.[3]
На рис. 3 представлені дані про тиск у головці для порівнюваних сумішей. Порівняння проводилося при однаковій температурі і продуктивності.
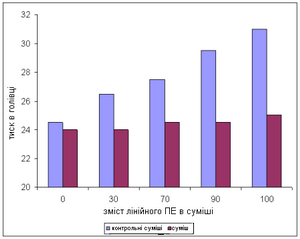
Рисунок 3 - Тиск в філь'єрі для сумішей з різним вмістом поліетилену
7. Добавки полегшуючі переробку полімерів
Добавка 1 - суперконцентрати, що містить фтореластомер в матриці лінійного поліетилену. Розроблений спеціально для екструзії лінійного поліетилену і високомолекулярного поліетилену низького тиску. Підвищує прозорість плівок і продуктивність процесу.
Добавка 2 - Являє собою дисперсію поліорганосілоксанов в прозорому термостійкому полістиролі. Розроблений спеціально для листової екструзії полістиролу. Підвищує продуктивність і стабільність процесу і дозволяє отримувати блискучі, глянсові вироби з меншою разнотолщинностью.
Добавка 3 - Являє собою дисперсію фтореластомера в поліпропілені. Розроблений спеціально для екструзії труб та профілів з поліпропілену. Дозволяє підвищити продуктивність процесу і поліпшити якість поверхні виробів з поліпропілену[1].
Висновки
Відповідно до теорії руйнування одним з основних параметрів, які впливають на міцнісні характеристики матеріалу, є кількість мікродефектів на поверхні виробу. Застосування фтореластомеров дозволяє отримувати плівки з покращеними фізико-механічними характеристиками, так як зменшується кількість поверхневих дефектів внаслідок зниження зсувних напруг на виході полімеру з формуючої головки.
Перелік посилань
- Доступно о полимерах [Электронный ресурс].Режим доступа:http://www.plastichelper.ru/
- Аналитический портал химической промышленности. [Электронный ресурс].Режим доступа:http://newchemistry.ru
- Клинков А.С., Беляев П.С., Скуратов В.К., Соколов М.В., Однолько В.Г. -Тамбов : Изд-во Тамб. гос. техн. ун-та, 2010., - 100 с.