Реферат за темою випускної роботи
Зміст
- Вступ
- 1. Актуальність теми
- 2. Мета і задачі дослідженнь
- 3. Результати досліджень
- 3.1 Аналіз конвеєрної лінії з проміжними бункерами як об’єкта автоматичного управління
- 3.2 Розробка способу і математичної моделі автоматичного управління конвеєрною лінією з проміжними бункерами
- 3.3 Розробка структурної схеми системи автоматичного управління конвеєрними лініями з проміжними бункерами
- Висновки
- Перелік посилань
Вступ
Процес конвеєрного транспорту шахти – це технологічний процес переміщення гірської маси, матеріалів, а в деяких випадках і людей за допомогою конвеєрів по гірських виробках. На шахтах для конвеєрного транспорту в основному застосовуються конвеєрні лінії зі стрічковими конвеєрами. Сучасні підземні конвеєрні лінії характеризуються значною довжиною (десятки кілометрів) і розгалуженістю транспортних магістралей, та змінюють з часом свої параметри: довжину, топологію і т.п. Конвеєрна лінія за своїм технологічним призначенням є транспортним об’єктом, обслуговуючим очисний забій. Для шахтних конвеєрних ліній характерні перепади характеристик на вході об’єкта управління (дискретний характер забійних вантажопотоків і їх мінлива інтенсивність в періоди безперервних надходжень), внутрішні обурення об’єкта управління (екстрені і аварійні зупинки конвеєрів лінії), перепади характеристик на виході об’єкта управління, пов’язані з обмеженою пропускною здатністю сполучених транспортних ланок (приймального бункера, рейкового транспорту, вантажного підйому) або з порушенням нормального режиму їх роботи.
Одним із способів підвищення ефективності конвеєрного транспорту на вугільних підприємствах є застосування систем автоматизації.
1. Актуальність теми
Розвиток автоматизації шахтних конвеєрних ліній протягом тривалого періоду визначався необхідністю зниження трудоємності управління та підвищення безпеки експлуатації конвеєрного транспорту. У зв’язку з цим широкого поширення набуло автоматизоване управління конвеєрної лінією, технічна сутність якого полягає в централізації управління процесами пуску-зупинки конвеєрів, а також у забезпеченні автоматичного захисту від розвитку аварії при виникненні аварійних ситуацій.
Потенційні можливості автоматизованого управління вичерпані не повністю. Продовжують залишатися актуальними такі завдання: зниження трудомісткості обслуговування автоматизованих конвеєрних ліній, ймовірності відмов у роботі лінії і часу простоїв лінії в результаті відмови за рахунок поліпшення параметрів надійності і ремонтопридатності апаратури і технічних засобів автоматизації, а також розвитку інформаційних властивостей апаратури автоматизації, що дозволяють скоротити час пошуку причини і місця відмови; підвищення безпеки експлуатації за рахунок вдосконалення існуючих технічних засобів і створення засобів автоматизації нового функціонального призначення.
2. Мета і задачі дослідженнь
Мета роботи – підвищення ефективності роботи
конвеєрної лінії з проміжними бункерами шляхом обгрунтування способу і
алгоритму управління, на основі яких розробка системи автоматичного
управління.
Для досягнення поставленої мети потрібно вирішити наступні задачі:
1. Аналіз конвеєрної лінії з проміжними бункерами як об’єкта автоматичного управління.
2. Розробка способу і математичної моделі автоматичного управління конвеєрної лінії з проміжними бункерами.
3. Дослідження на ЕОМ математичної моделі системи автоматичного управління конвеєрної лінії з проміжними бункерами.
4. Розробка схемотехнічних рішень по системі автоматичного управління конвеєрної лінії з проміжними бункерами.
3. Результати досліджень
3.1 Аналіз конвеєрної лінії з проміжними бункерами як об’єкта автоматичного управління
Як об’єкт автоматичного управління в магістерській роботі розглядається конвеєрна лінія з проміжними бункерами. На рисунку 1 представлений фрагмент конвеєрної лінії з проміжним бункером.
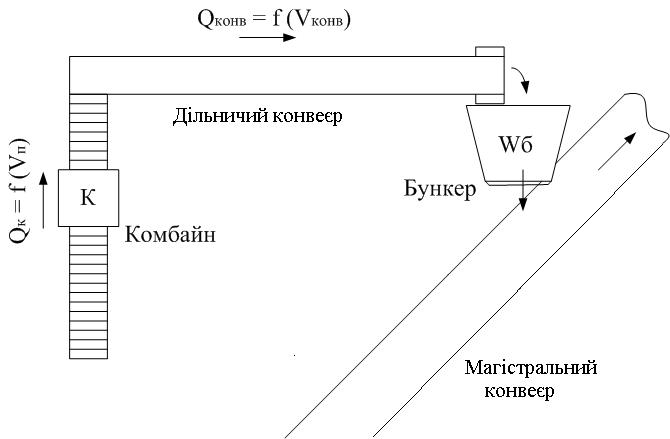
Рисунок
1 – Технологічна схема конвеєрної лінії з проміжним бункером
(анімація: кількість слайдів – 13; затримка між слайдами
– 1,5 с;
кількість циклів повторення – 5; розмір анімації –
153Кб)
Технологічні паузи в роботі видобувних комбайнів, у тому числі при аварійній зупинці лави, і періодична зміна їх швидкості переміщення вздовж лінії очисного вибою є причиною нерівномірності або відсутності вантажопотоків, які також відображаються на завантаженні конвеєра. При цьому характерна значне недовантаження магістральних конвеєрів, тривала робота в режимі холостого ходу. Це негативно позначається на техніко-економічних показниках використання конвеєрів, так як вони більшу частину часу своєї роботи мають значне (в 2...4 рази) недозавантаження, призводять до підвищення питомих витрат електроенергії.
В даний час на вугільних підприємствах для підвищення ефективності конвеєрного транспорту застосовуються вугільні акумулюючі бункери.
В якості базового, в роботі був прийнятий механізований бункер з нереверсивним донним конвеєром представлений на рисунку 2.
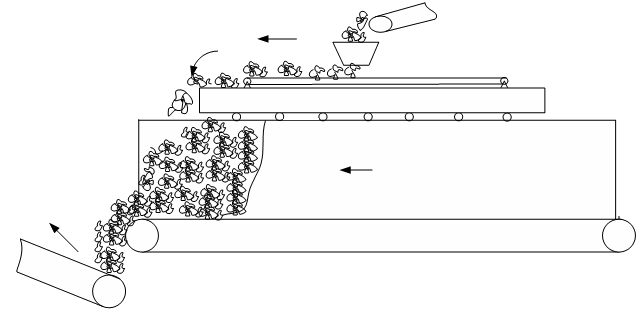
Рисунок
2 – Механізований бункер з нереверсивним донним конвеєром
При експлуатації механізованих бункерів з нереверсивним (донним конвеєром вантаж подають в бункер по задньому схилу відсипаного в ньому масиву гірської маси, переміщуваному уздовж всього бункера, з використанням завантажувального механізму (плужкового скидача або розподільчого конвеєра). Видачу вантажу виробляють від переднього схилу цього масиву, стаціонарно розміщеного в голові бункера за допомогою розвантажувального механізму (нереверсивного донного конвеєра). Операції завантаження і розвантаження бункера, таким чином, виробляються на відстані і в різний час двома самостійними механізмами. Операція формування рівномірного вантажопотоку при цьому, по суті, звелася до формування рівномірного масиву гірської маси в бункері, що виконується одночасно з його завантаженням. Ці особливості механізованих бункерів з нереверсивним донним конвеєром визначають їх добру пристосованість до автоматизації при експлуатації як в режимі акумулювання вантажу, так і в режимі згладжування нерівномірностей вантажопотоків.
В результаті аналізу конвеєрної лінії як об’єкта автоматичного управління ми формулюємо наступні вимоги до системи автоматичного управління конвеєрної лінією з проміжними бункерами:
1. Забезпечення централізованого автоматичного управління та контролю конвеєрної лінії з проміжними бункерами.
2. Регулювання швидкості комбайна і дільничного конвеєра в залежності від роботи транспортного ланцюжка.
3. У випадку аварії на магістральному конвеєрі включати завантажувальний конвеєр бункера і знижувати швидкість дільничого конвеєра і продуктивність комбайна.
4. Рівномірне завантаження бункера, застосування рівнемірів для контролю рівня заповнення бункера дозволить завчасно визначити час припинення подачі вантажопотоку в бункер.
5. Автоматичне відключення завантажувального конвеєра бункера при досягненні верхнього рівня завантаження.
6. Автоматичне відключення комбайна і дільничого конвеєра через кілька хвилин після завантаження бункера.
7. Включення конвеєра, що розвантажує бункер при включенні магістрального конвейєра після аварії.
8. Включення дільничного конвеєра і комбайна на швидкості V1 при включенні магістрального конвеєра.
9. Вимкнення конвеєра, що розвантажує бункер, після випорожнення ємності і робота бункера в транзитному режимі.
3.2 Розробка способу і математичної моделі автоматичного управління конвеєрною лінією з проміжними бункерами
Перш за все, необхідно зазначити, що формулювання задачі системи автоматичного управління конвеєрною лінією як підвищення фактичної продуктивності лінії до максимально можливої можна вважати прийнятною. Це обумовлено тим, що конвеєрна лінія за своїм технологічним призначенням є транспортним об’єктом, обслуговуючим очисний забій і, отже, питання про величину фактичної продуктивності даного об’єкта має реальний сенс лише в зіставленні з інтенсивністю забійного вантажопотоку. Без зв’язку з забійним вантажопотоком задача максимальної продуктивності конвеєрної лінії недостатньо конкретна. Задача системи автоматичного управління конвеєрною лініею полягає в тому, щоб гранично знизити обмежуваний вплив режимів роботи конвеєрної лінії на продуктивність очисного забою, тобто задача управління випливає з тієї допоміжної обслуговуючої технологічної ролі, яку відіграє конвеєрна лінія по відношенню до забою. Обмежуючий вплив режимів роботи конвеєрної лінії на продуктивність видобувних ділянок проявляється виключно у вигляді простоїв лави через зупинку конвеєрного транспорту [1].
Критерій автоматичного управління конвеєрними лініями доцільно
формулювати в наступному вигляді: мінімальний
час простоїв
видобувних дільнянок через відмови конвеєрної лінії або відмови на
виході
конвеєрної лінії
.
Автоматичне
управління за критерієм мінімальний
час простоїв видобувних
ділянок через відмови конвеєрної лінії або відмови на виході конвеєрної
лінії
може бути досягнуто шляхом
застосування способів, що
дозволяють використовувати акумулюючу здатність ділянок стрічки
конвеєрної лінії або проміжних бункерів, не повністю завантажених в
періоди безперервних реалізацій забійного вантажопотоку при роботі
конвеєрів в нормальному режимі на номінальній швидкості. Способи
наступні:
1. Регулювання швидкості стрічки кожного приймаючого вантаж конвеєра на підставі інформації, що формується в межах вимірювального інтервалу, від суміжного конвеєра. Параметри регулювання кожного приймаючого вантаж конвеєра визначаються системою автоматичного спостереження за станом вантажопотоку на конвеєрної лінії.
2. Синхронізація моментів пуску (зупинки) конвеєра з моментами надходження (припинення надходження) вантажу на його стрічку. Спосіб дозволяє зменшити середню швидкість просування вантажу до точки відмови за рахунок відключення лінії в інтервалах відсутності забійного вантажопотоку, а отже частково або повністю використовувати акумулюючу здатність вільних ділянок конвеєрної стрічки. Однак цей спосіб при коротких інтервалах відсутності вантажопотоку і при нерегульованих процесах пуску-зупинки призводить до частих пусків конвеєрів, що погіршують тепловий режим роботи двигунів і пов’язані з додатковими динамічними навантаженнями в стрічці і приводі. Ступінь використання акумулюючої здатності стрічки залежить від фактичного стану завантаження частини лінії, що знаходиться між забоєм і точкою відмови, тобто в зоні відмови. Принципово використання акумулюючої здатності стрічки можливо, якщо на лінії, що знаходиться в зоні відмови, є (у даний момент) вільна ділянка стрічки в головній частині хоча б одного конвеєра. Для реалізації цих способів необхідна інформація про фактичне розташування вантажу по довжині кожного конвеєра лінії. Якщо система управління не має в своєму розпорядженні ніякої інформацією про стан завантаження лінії, то в цьому випадку можливий лише пуск проти вантажопотоку або одночасний пуск. Спосіб одночасного пуску дозволяє максимально скоротити час пуску лінії і довести його до величини, яка визначається тривалістю розгону одного (найбільш важкого) конвеєра. Пуск конвеєрів лінії здійснюється при даному способі з однаковою інтенсивністю, заданою програмою розгону.
3. Регулювання завантаження-розвантаження акумулюючого бункера. Спосіб дозволяє в разі відмови на збірному конвеєрі (частина конвеєрної лінії після бункера) здійснювати завантаження бункера протягом деякого часу, що визначається місткістю бункера і кількістю вантажу, що знаходиться в надбункерній частини конвеєрної лінії. Тим самим запобігається зупинка роботи добувних ділянок [1].
В результаті аналізу зазначених способів в роботі розроблено новий спосіб автоматичного управління конвеєрною лінією з проміжними бункерами, який може бути досягнутий шляхом здійснення трьох можливих ситуацій:
1. Нормальний режим роботи ділянки. Комбайн працює з номінальною швидкістю подачі Vнк і продуктивністю Qнк, конвеєр також працює при номінальній швидкості Vнкон з номінальною продуктивністю Qнкон, бункер працює в транзитному режимі, тобто Wб = 0.
2. Аварійний режим (аварія на магістральному конвеєрі і його зупинка). В цьому випадку можливим є збільшення циклу роботи дільниці на час заповнення бункера tбзап. За допомогою координуючого пристрою бункер переводиться в акумулюючий режим, швидкість подачі комбайна знижується до V1к і відповідно продуктивність до Q1к, швидкість конвеєра знижується до V1кон, продуктивність до Q1кон. До тих пір поки бункер не заповниться повністю (Wб = 1). Тоді диспетчер за допомогою координуючого пристрою вимикає комбайн, вимикає завантажений конвеєр, до тих пір поки поломка не буде усунена або не включиться магістральний конвеєр.
3. Післяаварійний режим роботи ділянки. Бункер відкривається на видачу вантажу на магістральний конвеєр, включається дільничий конвеєр на швидкості V1кон і одночасно включається комбайн зі швидкістю подачі V1к і продуктивністю Q1к. Ділянка працює на цих швидкостях до тих пір, поки Wб = 0, потім переводимо дільничний конвеєр і комбайн на номінальну швидкість Vнкон і Vнк відповідно.
Для реалізації способу автоматичного управління конвеєрними лініями з проміжними бункерами було розроблено пристрій управління бункером УУБ. Структурна схема пристрою УУБ представлена на рисунку 3.
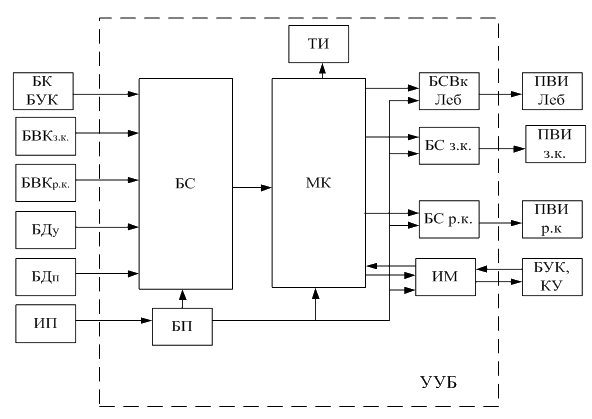
Рисунок
3 – Структурна схема пристрою управління бункером
На схемі пунктиром виділені блоки, які було розроблено.
На рисунку 3 позначено: БК БУК – блок-контакти блоку управління конвеєром; БВК з.к. – Блок включення-виключення завантажувального конвеєра; БВК р.к. – Блок включення-виключення розвантажувального конвейєра; БД у – Блок датчиків рівня; БД п – Блок шляхових датчиків; ІП – Джерело живлення; БС – Блок узгодження дискретних сигналів з микроконтроллером; БП – Блок живлення; МК – Мікроконтролер; БСВК Леб – Блок узгодження з пускачем лебідки; БС з.к. – Блок узгодження з пускачем завантажувального конвеєра; БС р.к. – Блок узгодження з пускачем розвантажувального конвейєра; ІМ – Інтерфейсний модуль; БУК – Блок управління конвеєром; КУ – Координуючий пристрій конвеєрного транспорту; ТИ – Табло індикації.
Провідним елементом пристрою є мікроконтроллер МК, який виконує функції обробки інформації, що отримується від датчиків рівня, шляхових датчиків, формування вихідних сигналів, сигналів управління і сигналів індикації. До блоку мікроконтролера через блок узгодження дискретних сигналів підключаються такі блоки і датчики: блок-контакти блоку управління конвеєром БК БУК; блок включення-виключення завантажувального конвеєра БВК з.к.; блок включення-виключення розвантажувального конвейєра БВК р.к.; блок датчиків рівня БД у; блок колійних датчиків БД п.
Табло індикації ТІ включає світлодіодні індикатори, що сигналізують про режими роботи проміжного аккумулюючого бункера.
Блок живлення БП призначений для живлення іскронебезпечною напругою внутрішньої схеми пристрою та іскробезпечною – ланцюгів датчиків [2].
Ефективність реалізації задачі регульований конвеєр – проміжний бункер виконується за рахунок збільшення часу роботи добувних ділянок. Як відомо, час заповнення бункера при номінальній швидкості подачі комбайна Vнк і номінальній швидкості Vнкон і продуктивності Qнкон конвеєра визначається зі співвідношення:
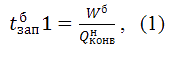
де Wб – обсяг бункера, рівний 300 т, Qнкон – номінальна продуктивність конвеєра.
Після того, як за допомогою координуючого пристрою бункер переводиться в акумулюючий режим, швидкість подачі комбайна знижується до V1к і відповідно продуктивність до Q1к, швидкість конвеєра знижується до V1кон, продуктивність до Q1кон. Час заповнення бункера стане рівним:
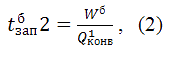
де Wб – обсяг бункера, Q1кон – мінімальна продуктивність конвеєра.
Вхідними даними є бункер, місткістю 300 тонн, видобувний комбайн з регульованою швидкістю подачі КДК-500, дільничний конвеєр 1ЛТ80У (Vнкон = 2,5 м/с, Qнкон = 10,3 т/хв, V1кон = 1,6 м/с, Q1кон = 7 т/хв, кут нахилу β = 0o, двигун ВРП225М4Р потужністю 1×55 кВт, L = 500) [3]. Результат розрахунку часу заповнення бункера в залежності від продуктивності конвеєра і комбайна наведено на рисунку 4.
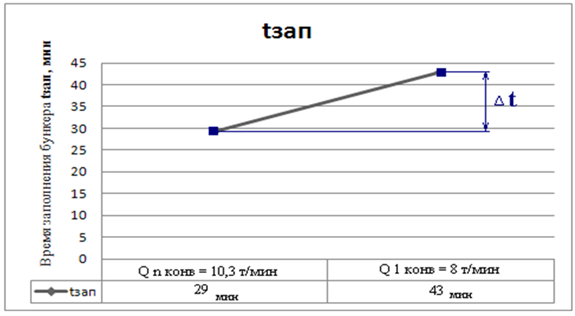
Рисунок
4 – Час заповнення бункера в залежності від швидкості конвеєра
На графіку показано Δt – час заповнення бункера при зниженні продуктивності комбайна і швидкості конвеєра. Якщо ще врахувати додатковий час tзагр.конв. необхідний для завантаження всієї довжини конвеєра, то час роботи добувних ділянок збільшиться на:
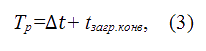
При здійсненні пуску завантаженого конвеєра виконується перевірка застосовності всіх складових частин стрічкового конвеєра. Необхідний ряд перевірочних розрахунків стрічкового конвеєра в період його пуску з вантажем.
Період пуску конвеєра можна розділити на дві фази: зрушення і розгін. Фаза зрушення характеризується поступовим залученням в рух елементів стрічки. В початковий момент фази зрушення, що передує руху конвеєрної стрічки, зусилля що прикладається до стрічки, але ще не перевищило загальний опір руху стрічки по роликам, відхиляє ролікоопори у напрямку руху, що викликає виникнення згинального моменту в місці установки роликоопори на ставши конвеєра і можливість поздовжнього зміщення останнього [4].
У передпусковий період на роликоопор діє сила від ваги стрічки з вантажем:
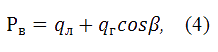
У початковий момент зрушення до роликоопор, що несуть завантажену гілку, прикладається момент тертя рівний опору руху конвеєрної стрічки з вантажем щодо осі ролика:
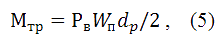
де dp – діаметр ролика, м; Wп – коефіцієнт опору при пуску (WH = 0,06-0,09), і момент, що діє на 7-у роликоопору від тягового зусилля приводу.
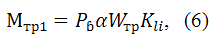
де Рɓ – окружне зусилля на приводному барабані, Н; а – відстань від точки прикладання сили до осі ролика, а = dp/2, м; Wтр – коефіцієнт тертя стрічки по роликоопорі; Kli – коефіцієнт, що враховує відстань від сьомої роликоопори до приводного барабана, м.
До тих пір, поки виконується умова Мтр > Мтр1 стрічка не рухається, і зусилля, що прикладається до стрічки від двигуна відхиляє роликоопору. По мірі зростання окружного зусилля на приводному барабані в рух включаються такі елементи конвеєрної ленти, які, в свою чергу, послідовно впливають на роликоопори. Хвиля руху йде не тільки по стрічці, але і по ставу, причому швидкість руху пусковий хвилі (поштовху) по ставу значно перевищує швидкість поширення хвилі в стрічці, так як жорсткість става значно більше жорсткості стрічки.
Розглянемо згинальну деформацію стійки роликоопори в початковий момент зрушення. Тягове зусилля, прикладене до стрічки в точці її контакту з роликом, що відокремлює нерухому ділянку тягового органу від рухомого, повинно перетягнути через ролик провислу стрічку з вантажем. При цьому роликоопора вигинається під впливом сил, викликаних провислою за роликоопору стрічкою з матеріалом, що транспортується Рн.пр.
Відхилення роликоопори відбувається у випадку, коли ролик ще не обертається, а хвиля деформації вже почала розтягувати стрічку за роликоопори. При цьому приймаємо наступні допущення: сила опору руху стрічки описується законом сухого тертя; пробуксовка стрічки на барабані відсутня; ролик не обертається поки Рɓ ˂ Рн.пр, а відхилення верхньої точки роликоопори ΔХ одно ділянці стрічки за роликоопори Δl, залученому в рух до моменту t зриву стрічки з ролика, а значить і початку обертання ролика.
Таким чином, сила, яка згинає роликоопору в початковий момент зрушення:

де cosβ – кут нахилу конвеєра (cosβ = 0o); W'тр – коефіцієнт тертя при зрушенні.
Крім того, під час запуску конвеєра навантаженим для виключення пробуксовки повинна виконуватися умова:
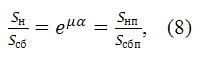
де Sн, Sсб – зусилля в набігаючий і збігаючий з приводного барабана гілках стрічки відповідно; Sнп, Sсбп – зусилля в набігаючий і збігаючий з приводного барабана гілках стрічки при пуску конвеєра відповідно; μ, α – коефіцієнт тертя стрічки об поверхню приводного барабана та кут обхвату стрічкою цього барабана відповідно [5].
Так як Sнп ˃ Sн, відповідно до умовою (8), і Sсбп повинно бути більше Sсб. Отже для пуску стрічкового конвеєра без пробуксовки протягом часу пуску tп натяжний пристрій повинен створювати підвищений натяг стрічки, що забезпечує в збігаючий гілки зусилля Sсбп. Тому у важких конвеєрах зазвичай застосовуються автоматичні натяжні пристрої. А для решти конвеєрів керівними технічними матеріалами [6] при пуску навантаженого конвеєра розрахунок натяжного зусилля натяжного пристрою рекомендується виконувати з використанням підвищувального коефіцієнта – К = 1,2; 1,5 (відповідно для позитивних і негативних значень температури навколишнього середовища). Використання підвищувального коефіцієнта призводить до того, що тягова стрічка конвеєра і більшість елементів його конструкції, включаючи привід, весь період експлуатації конвеєра будуть працювати з навантаженням, що відповідає пусковому режиму. Тобто на 20% і 50% більше вимагається при роботі в усталеному режимі, що призводить до відчутного зниження терміну служби стрічки і підвищення питомих енерговитрат на транспортування.
В проектувальних розрахунках зусилля [6] Sнп визначається за формулою:

де Wгп, Wпп – опір руху стрічки на навантаженій і порожнії гілках відповідно; a – прискорення руху стрічки за час tп її розгону при пуску конвеєра; qг, qл – лінійні навантаження від сил тяжіння вантажу, що транспортується й стрічки відповідно; L – довжина конвеєра; K1 – коефіцієнт обліку інерції обертових мас роликів і барабанів; g – прискорення вільного падіння. Статичні опору руху стрічки, підраховані за коефіцієнтом wn = Kmw (де w – коефіцієнт опору руху при стабільному русі стрічки; Km – коефіцієнт збільшення опору руху при зрушенні стрічки з місця), досягають своїх максимумів Wгп, Wпп тільки в момент зрушення стрічки, а потім протягом часу tп знижуються до постійних значень, розрахованих за коефіцієнтом w, так як вони не залежать від величини пускового прискорення стрічки [6].
Перший доданок формули (9) – Sсбп = KSсб (де Кп – коефіцієнт підвищення попереднього натягу стрічки при пуску навантаженого конвеєра, що характеризує додаткову навантаженість стрічки та інших елементів), для виключення пробуксовки приводного барабана має реагувати не лише на підвищення опору руху при рушанні стрічки з місця, а й на що виникає при її розгоні додаткове динамічне зусилля, що описується четвертим доданком формули (9).
З метою отримання залежності для обчислення Кп розглянемо умову пуску навантаженого стрічкового конвеєра без пробуксовки приводного барабану:

де Рп = (Sнп – KSсб) – тягове зусилля на приводному барабані під час пуску; kзс = 1,1–1,2 – коефіцієнт запасу зчеплення [6]. Звідси можна отримати:

У нормативах [3] прийнято, що Кп = К = 1,2; 1,5.
Результати чисельних розрахунків за формулою (11) для конвеєра продуктивністю 480 т/год, що переміщує вугілля зі швидкістю 1,6 м/с на відстань 500 м, в графічному вигляді представлені на рисунку 5. З них при мінімізації критерію додаткової пускової навантаженості конвеєра представляється можливим вибрати час розгону tп і розрахунковий коефіцієнт Кп, відповідні технічним параметрам конвеєра.
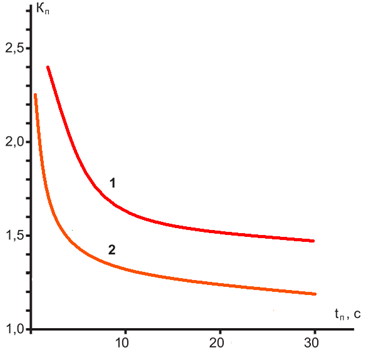
Рисунок
5 – Графіки залежності коефіцієнта Кп від часу пуску tп
навантаженого конвеєра 1ЛТ80У: 1 - при β =
0°
і К = 1,5;
2 - при β = 0° і К = 1,2
За допомогою отриманого коефіцієнта Кп можна визначити необхідне для пуску навантаженого конвеєра зусилля в натяжному пристрої, використовуючи відомі залежності [5] і замінюючи в них нормативний підвищувальний коефіцієнт К на Кп. Реалізація прийнятого за графіком (рис 5.) Часу пуску tп можлива шляхом застосування в електричному ланцюзі приводу конвеєра передових елементів – частотних перетворювачів.
Проведені дослідження дозволяють в компенсуючих автоматичних натяжних пристроях в залежності від часу пуску, технічних параметрів конвеєра, кута нахилу траси і температурних умов навколишнього середовища приймати більш точні значення необхідного натягу стрічки натяжним пристроєм протягом часу пуску навантаженого стрічкового конвеєра
У конвеєрах, де кут нахилу траси β = 0° (з графіка видно), коефіцієнт Кп трохи вище нормативних значень К, що в даному випадку позитивно позначиться на надійності передачі тягового зусилля приводним барабаном стрічкового конвеєра в період його пуску з вантажем.
Крім того, отримані значення коефіцієнта Кп і відповідного йому часу пуску tп дозволяють скорегувати розрахунок сили Sнп за формулою (8), що сприятиме підвищенню якості перевірочних розрахунків стрічкового конвеєра в період його пуску з вантажем [5].
Далі був проведений ряд досліджень і розрахунків пуску навантаженого конвеєра в післяаварійному режимі для побудови математичної моделі в додатку Simulink пакета MATLAB [7]. Модель приводу стрічкового конвеєра набрана із стандартних блоків пакета MATLAB і приведена на рисунку 6. Виходячи з моделювання перехідних процесів було встановлено, що пуск конвеєра 1ЛТ80У завантаженим в післяаварійний період на швидкості V1кон здійснено успішно.
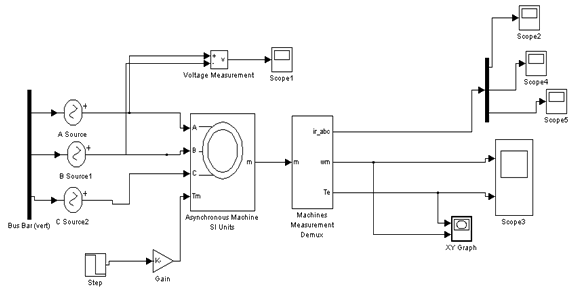
Рисунок
6 – Модель приводу стрічкового конвеєра 1ЛТ80У
3.3 Розробка структурної схеми системи автоматичного управління конвеєрними лініями з проміжними бункерами
На підставі проведених досліджень була розроблена структурна схема автоматичного управління конвеєрними лініями з проміжними бункерами на базі комплексу САУКЛ, комплексу технічних засобів управління очисними комбайнами КС 500Ч, і розробленого пристрою управління бункером УУБ, представлена на рисунку 7. На рисунку 7 позначено: координуючий пристрій конвеєрного транспорту; БИУком – блок виконавчих пристроїв комбайна; БД1-n – блок датчиків; БУ – блок управління комбайном; БУК1-БУКn – блок управління конвеєром № 1 ... n; БД1-БДn – блок датчиків бункера № 1 ... n; БДт1-БДтn – блок датчиків конвеєра № 1 ... n; УРС1-УРСn – пристрій регулювання швидкості; ПЧ1-ПЧn – перетворювач частоти; ПУ САУКЛ – пульт управління САУКЛ; ИБП – джерело безперебійного живлення; АЛС – адаптер лінії зв’язку; АПУ – адаптер пульта управління; УУБ1-УУБn – пристрій управління бункером № 1 ... n.
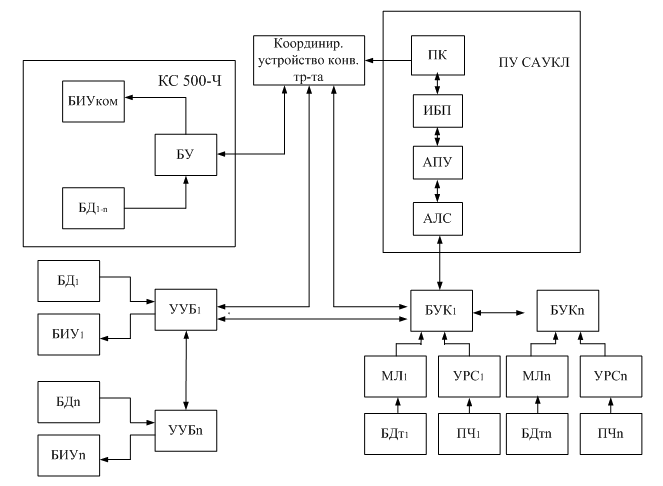
Рисунок
7 – Структурна схема автоматичного управління конвеєрними
лініями з проміжними бункерами
Висновки
Для підвищення ефективності роботи добувних ділянок розроблена структурна схема, пристрій управління бункером і запропонований спосіб автоматичного управління конвеєрними лініями з проміжними бункерами з використанням сучасної мікропроцесорної техніки, координуючого пристрою.
Встановлено, що ефективність даної системи автоматичного управління досягається шляхом збільшення часу циклу роботи дільниці на час Tр = Δt + tзагр.конв. Здійснено пуск завантаженого конвеєра в післяаварійному режимі на швидкості V1кон.
Реалізація запропонованої структурної схеми системи автоматичного управління конвеєрними лініями з проміжними бункерами дозволить в робочому режимі регулювати швидкість подачі комбайна і швидкість конвеєра, в аварійному режимі використовувати акумулюючу здатність лінії, в післяаварійному режимі здійснювати пуск навантаженого конвеєра, забезпечувати не тільки функції блокувань і телемеханічного управління, але та збір і обробку інформації від супутнього обладнання, передачу її на поверхню для подальшого моніторінга роботи ділянки.
При написанні даного реферату кваліфікаційна робота магістра ще не завершена. Дата остаточного завершення роботи: грудень 2012 Повний текст і матеріали по темі роботи можуть бути отримані у автора або наукового керівника після зазначеної дати.
Перелік посилань
- Гливанский А.А. Методы управления шахтным подземным конвейерным транспортом. Средства и аппаратура горной автоматики для угольных предприятий, Труды института № 29 / А.А. Гливанский, И.П. Коновалова, В.М. Ротенберг, Е.К. Травкин – Москва, 1978.
- Чиженко И.М. Справочник по преобразовательной технике / Под ред. И.М. Чиженко – Киев: Техника, 1978. – 447 с.
- Шахмейстер Л.Г. Теория и расчет ленточных конвейеров / Л.Г. Шахмейстер, В.Г. Дмитриев – М.: Машиностроение, 1987 – 256 с.
- Ефименко Л.И. Определение нагрузок на конвейерный став от воздействия тягового усилия / Л.И. Ефименко, М.П. Тиханский
- Рачков Е.В. Совершенствование системы пуска ленточного конвейера с грузом. Речной транспорт / Е.В. Рачков – 2011. – № 5 (53). – с. 63
- Дьячков В.К. Основные требования к проектированию ленточных конвейеров общего назначения. РТМ 24.093.04-80 / В.К. Дьячков, Н.А. Смирнова – М.: ЦНИИТЭтяжмаш, 1980.
- Черных И.В. Моделирование электротехнических устройств в MATLAB. SimPowerSystems и Simulink / И.В. Черных – М.: ДМК Пресс, 2007. – 288 с., ил. (Серия «Проектирование»).
- Штокман И.Г. Проектирование и конструирование транспортных машин и комплексов / И.Г. Штокман – М.: Недра, 1986. – 392 с.