Реферат по теме выпускной работы
Содержание
- Введение
- 1. Актуальность темы
- 2. Цель и задачи исследований
- 3. Результаты исследований
- 3.1 Анализ конвейерной линии с промежуточными бункерами как объекта автоматического управления
- 3.2 Разработка способа и математической модели автоматического управления конвейерной линии с промежуточными бункерами
- 3.3 Разработка структурной схемы системы автоматического управления конвейерными линиями с промежуточными бункерами
- Выводы
- Перечень ссылок
Введение
Процесс конвейерного транспорта шахты – это технологический процесс перемещения горной массы, материалов, а в некоторых случаях и людей с помощью конвейеров по горным выработкам. На шахтах для конвейерного транспорта в основном применяются конвейерные линии с ленточными конвейерами. Современные подземные конвейерные линии характеризуются значительной протяженностью (десятки километров) и разветвленностью транспортных магистралей, изменяющих со временем свои параметры: длину, топологию и т.п. Конвейерная линия по своему технологическому назначению является транспортным объектом, обслуживающим очистной забой. Для шахтных конвейерных линий характерны возмущения на входе объекта управления (дискретный характер забойных грузопотоков и их переменная интенсивность в периоды непрерывных поступлений), внутренние возмущения объекта управления (экстренные и аварийные остановы конвейеров линии), возмущения на выходе объекта управления, связанные с ограниченной пропускной способностью сопряженных транспортных звеньев (приемного бункера, рельсового транспорта, грузового подъема) либо с нарушением нормального режима их работы.
Одним из способов повышения эффективности конвейерного транспорта на угольных предприятиях является
1. Актуальность темы
Развитие автоматизации шахтных конвейерных линий на протяжении длительного периода определялось необходимостью снижения трудоемкости управления и повышения безопасности эксплуатации конвейерного транспорта. В связи с этим широкое распространение получило автоматизированное управление конвейерной линией, техническая сущность которого заключается в централизации управления процессами пуска-останова конвейеров, а также в обеспечении автоматической защиты от развития аварии при возникновении аварийных ситуаций.
Потенциальные возможности автоматизированного управления исчерпаны не полностью. Продолжают оставаться актуальными следующие задачи: снижение трудоемкости обслуживания автоматизированных конвейерных линий, вероятности отказов в работе линии и времени простоев линии в результате отказа за счет улучшения параметров надежности и ремонтопригодности аппаратуры и технических средств автоматизации, а также развития информационных свойств аппаратуры автоматизации, позволяющих сократить время поиска причины и места отказа; повышение безопасности эксплуатации за счет совершенствования существующих технических средств и создания средств автоматизации нового функционального назначения.
2. Цель и задачи исследования
Цель работы – повышение эффективности работы конвейерной линии с промежуточными бункерами путем обоснования способа и алгоритма управления, на основе которых разработка системы автоматического управления.
Для достижения поставленной цели нужно решить следующие задачи:
1. Анализ конвейерной линии с промежуточными бункерами как объекта автоматического управления.
2. Разработка способа и математической модели автоматического управления конвейерной линии с промежуточными бункерами.
3. Исследование на ЭВМ математической модели системы автоматического управления конвейерной линии с промежуточными бункерами.
4. Разработка схемотехнических решений по системе автоматического управления конвейерной линии с промежуточными бункерами.
3. Результаты исследований
3.1 Анализ конвейерной линии с промежуточными бункерами как объекта автоматического управления
Как объект автоматического управления в магистерской работе рассматривается конвейерная линия с промежуточными бункерами. На рисунке 1 представлен фрагмент конвейерной линии с промежуточным бункером.
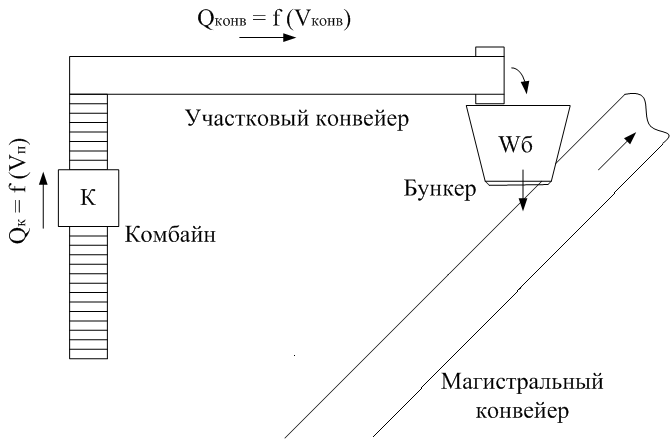
Рисунок
1 – Технологическая схема конвейерной линии с промежуточным
бункером
(анимация: количество слайдов – 13; задержка между слайдами
– 1,5 с; количество циклов повторения – 5; размер
анимации – 153Кб)
Технологические паузы в работе выемочных комбайнов, в том числе при аварийной остановке лавы, и периодическое изменение их скорости перемещения вдоль линии очистного забоя являются причиной неравномерности или отсутствия грузопотоков, которые также отражаются на загрузке конвейера. При этом характерна значительная недогрузка магистральных конвейеров, продолжительная работа в режиме холостого хода. Это отрицательно сказывается на технико-экономических показателях использования конвейеров, т.к. они большую часть времени своей работы имеют существенную (в 2...4 раза) недозагрузку, приводят к повышению удельных расходов электроэнергии.
В настоящее время на угольных предприятиях для повышения эффективности конвейерного транспорта применяются угольные аккумулирующие бункеры.
В качестве базового, в работе был принят механизированный бункер с нереверсивным донным конвейером представленный на рисунке 2.
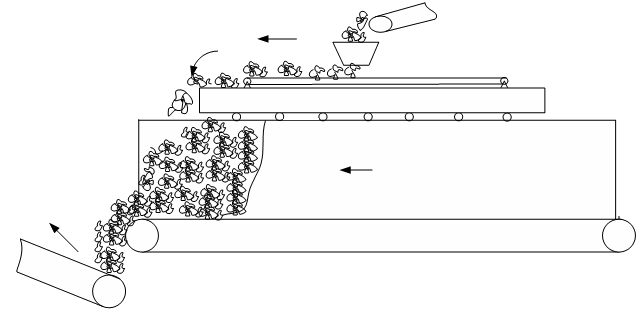
Рисунок
2 – Механизированный бункер с нереверсивным донным конвейером
При эксплуатации механизированных бункеров с нереверсивным донным конвейером груз подают в бункер по заднему откосу отсыпанного в нем массива горной массы, перемещаемому вдоль всего бункера, с использованием загрузочного механизма (плужкового сбрасывателя или распределительного конвейера). Выдачу груза производят от переднего откоса этого массива, стационарно размещенного в голове бункера с помощью разгрузочного механизма (нереверсивного донного конвейера). Операции загрузки и разгрузки бункера, таким образом, производятся на расстоянии и в различное время двумя самостоятельными механизмами. Операция формирования равномерного грузопотока при этом, по существу, свелась к формированию равномерного массива горной массы в бункере, выполняемому одновременно с его загрузкой. Эти особенности механизированных бункеров с нереверсивным донным конвейером определяют их хорошую приспособленность к автоматизации при эксплуатации как в режиме аккумулирования груза, так и в режиме сглаживания неравномерностей грузопотоков.
В результате анализа конвейерной линии как объекта автоматического управления нами формулируются следующие требования к системе автоматического управления конвейерной линией с промежуточными бункерами:
1. Обеспечение централизованного автоматического управления и контроля конвейерной линией с промежуточными бункерами.
2. Регулирование скорости комбайна и участкового конвейера в зависимости от работы транспортной цепочки.
3. В случае аварии на магистральном конвейере включать загрузочный конвейер бункера и снижать скорость участкового конвейера и производительность комбайна.
4. Равномерная загрузка бункера, применение уровнемеров для контроля уровня заполнения бункеров позволит заблаговременно определить время прекращения подачи грузопотока в бункер.
5. Автоматическое отключение загрузочного конвейера бункера при достижении верхнего уровня загрузки.
6. Автоматическое отключение комбайна и участкового конвейера спустя несколько минут после загрузки бункера.
7. Включение конвейера, разгружающего бункер на при включении магистрального конвейера после аварии.
8. Включение участкового конвейера и комбайна на скорости V1 при включении магистрального конвейера.
9. Выключение конвейера, разгружающего бункер, после опорожнения емкости и работа бункера в транзитном режиме.
3.2 Разработка способа и математической модели автоматического управления конвейерной линии с промежуточными бункерами
Прежде всего, необходимо отметить, что формулировка задача системы
автоматического управления конвейерной линией как повышение фактической
производительности линии до максимально возможной нельзя считать
приемлемой. Это обусловлено тем, что конвейерная линия по своему
технологическому назначению является транспортным объектом,
обслуживающим очистной забой и, следовательно, вопрос о величине
фактической производительности данного объекта имеет реальный смысл
только в сопоставлении с интенсивностью забойного грузопотока. Без
связи с забойным грузопотоком задача максимальной производительности
конвейерной линии недостаточно конкретна. Задача системы
автоматического управления конвейерной линии заключается в том, чтобы
предельно снизить ограничивающее влияние режимов работы конвейерной
линии на производительность очистного забоя, т. е. задача управления
вытекает из той вспомогательной обслуживающей технологической роли,
которую играет конвейерная линия по отношению к забою. Ограничивающее
влияние режимов работы конвейерной линии на производительность
добычного участка проявляется исключительно в виде простоев лавы из-за
остановки конвейерного транспорта [1].
Критерий автоматического управления конвейерными линиями целесообразно
формулировать в следующем виде: минимальное
время простоев
добычных участков по причине
отказов конвейерной линии или отказов на выходе конвейерной
линии
.
Автоматическое управление по критерию минимальное
время
простоев добычных участков по причине отказов конвейерной линии или
отказов на выходе конвейерной линии
может быть достигнуто
путем применения способов, позволяющих использовать аккумулирующую
способность участков ленты конвейерной линии или промежуточных
бункеров, не полностью загруженных в периоды непрерывных реализаций
забойного грузопотока при работе конвейеров в нормальном режиме на
номинальной скорости. Способы следующие:
1. Регулирование скорости ленты каждого принимающего груз конвейера на основании информации, формируемой в пределах измерительного интервала, от смежного подающего конвейера. Параметры регулирования каждого принимающего груз конвейера определяются системой автоматического слежения за состоянием грузопотока на конвейерной линии.
2. Синхронизация моментов пуска (останова) конвейера с моментами поступления (прекращения поступления) груза на его ленту. Способ позволяет уменьшить среднюю скорость продвижения груза к точке отказа за счет отключения линии в интервалах отсутствия забойного грузопотока, а следовательно частично или полностью использовать аккумулирующую способность свободных участков конвейерной ленты. Однако этот способ при коротких интервалах отсутствия грузопотока и при нерегулируемых процессах пуска-останова приводит к частым пускам конвейеров, что ухудшают тепловой режим работы двигателей и связаны с дополнительными динамическими нагрузками в ленте и приводе.
Степень использования аккумулирующей способности ленты зависит от фактического состояния загрузки части линии, находящейся между забоем и точкой отказа, т. е. в зоне отказа. Принципиально использование аккумулирующей способности ленты возможно, если на линии, находящейся в зоне отказа, имеется (в данный момент) свободный участок ленты в головной части хотя бы одного конвейера.
Для реализации этих способов необходима информация о фактическом расположении груза по длине каждого конвейера линии. Если система управления не располагает никакой информацией о состоянии загрузки линии, то в этом случае возможен лишь пуск против грузопотока либо одновременный пуск. Способ одновременного пуска позволяет максимально сократить время пуска линии и довести его до величины, определяемой продолжительностью разгона одного (наиболее тяжелого) конвейера. Пуск конвейеров линии осуществляется при данном способе с одинаковой интенсивностью, заданной программой разгона.
3. Регулирование загрузки-разгрузки аккумулирующего бункера. Способ позволяет в случае отказа на сборном конвейере (часть конвейерной линии после бункера) осуществлять загрузку бункера в течение некоторого времени, определяемого емкостью бункера и количеством груза, находящегося в надбункерной части конвейерной линии. Тем самым предотвращается остановка работы добычного участка [1].
В результате анализа указанных способов в работе разработан новый способ автоматического управления конвейерной линии с промежуточными бункерами, который может быть достигнут путем осуществления трех возможных ситуаций:
1. Нормальный режим работы участка. Комбайн работает с номинальной скоростью подачи Vнк и производительностью Qнк , конвейер также работает при номинальной скорости Vнкон с номинальной производительностью Qнкон , бункер работает в транзитном режиме, то есть Wб = 0.
2. Аварийный режим (авария на магистральном конвейере и его останов). В этом случае возможным является увеличение цикла работы участка на время заполнения бункера tбзап. С помощью координирующего устройства бункер переводится в аккумулирующий режим, скорость подачи комбайна снижается до V1к и соответственно производительность до Q1к, скорость конвейера снижается до V1кон, производительность до Q1кон. До тех пор пока бункер не заполнится полностью (Wб = 1). Тогда диспетчер с помощью координирующего устройства отключает комбайн, выключает груженный конвейер, до тех пор пока поломка не будет устранена.
3. Послеаварийный режим работы участка. Бункер открывается на выдачу груза на магистральный конвейер, включается конвейер на скорости V1кон и одновременно включается комбайн со скоростью подачи V1к и производительностью Q1к. Участок работает на этих скоростях до тех пор, пока Wб = 0, затем переводим участковый конвейер и комбайн на номинальную скорость Vнкон и Vнк соответственно.
Для реализации способа автоматического управления конвейерными линиями с промежуточными бункерами было разработано устройство управления бункером УУБ. Структурная схема устройства УУБ представлена на рисунке 3.
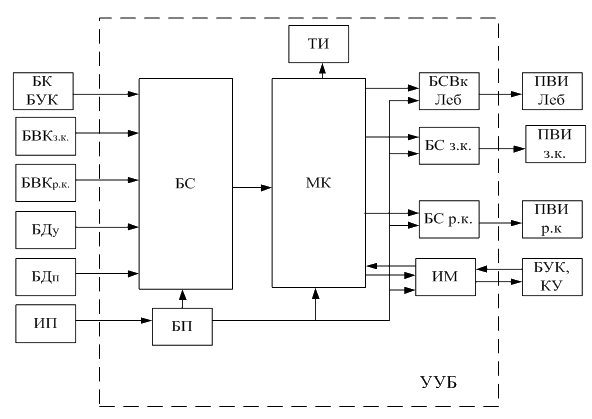
Рисунок
3 – Структурная схема устройства управления бункером
На схеме пунктиром выделены разрабатываемые блоки.
На рисунке 3 обозначено: БК БУК – блок-контакты блока управления конвейером; БВК з.к. – Блок включения-выключения загрузочного конвейера; БВК р.к. – Блок включения-выключения разгрузочного конвейера; БД у – Блок датчиков уровня; БД п – Блок путевых датчиков; ИП – Источник питания; БС – Блок согласования дискретных сигналов с микроконтроллером; БП – Блок питания; МК – Микроконтроллер; БСВК Леб – Блок согласования с пускателем лебедки; БС з.к. – Блок согласования с пускателем загрузочного конвейера; БС р.к. – Блок согласования с пускателем разгрузочного конвейера; ИМ – Интерфейсный модуль; БУК – Блок управления конвейером; КУ – Координирующее устройство конвейерного транспорта; ТИ – Табло индикации.
Ведущим элементом устройства является микроконтроллер МК, который выполняет функции обработки информации, получаемой от датчиков уровня, путевых датчиков, формирования выходных сигналов, управляющих сигналов и сигналов индикации. К блоку микроконтроллера через блок согласования дискретных сигналов подключаются такие блоки и датчики: блок-контакты блока управления конвейером БК БУК; блок включения-выключения загрузочного конвейера БВК з.к.; блок включения-выключения разгрузочного конвейера БВК р.к.; блок датчиков уровня БД у; блок путевых датчиков БД п.
Табло индикации ТИ включает светодиодные индикаторы, сигнализирующие о режимах работы промежуточного бункера.
Блок питания БП предназначен для питания искроопасным напряжением внутренней схемы устройства и искробезопасным – цепей датчиков [2].
Эффективность реализации задачи регулируемый конвейер – промежуточный бункер выполняется за счет увеличения времени работы добычного участка. Как известно, время заполнения бункера при номинальной скорости подачи комбайна Vнк и номинальной скорости Vнкон и производительности Qнкон конвейера определяется из соотношения:
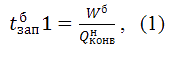
где Wб – объем бункера, равный 300 т; Qнкон – номинальная производительность конвейера.
После того, как с помощью координирующего устройства бункер переводится в аккумулирующий режим, скорость подачи комбайна снижается до V1к и соответственно производительность до Q1к, скорость конвейера снижается до V1кон, производительность до Q1кон. Время заполнения бункера станет равным:
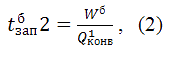
где Wб – объем бункера; Q1кон – минимальная производительность конвейера.
Входными данными является бункер, вместительностью 300 тонн, очистной комбайн с регулируемой скоростью подачи КДК-500, участковый конвейер 1ЛТ80У (Vнкон = 2,5 м/с, Qнкон = 10,3 т/мин, V1кон = 1,6 м/с, Q1кон = 7 т/мин, угол наклона β = 0o, двигатель ВРП225М4Р мощностью 1×55 кВт, L = 500) [3]. Результат расчета времени заполнения бункера в зависимости от производительности конвейера и комбайна приведен на рисунке 4.
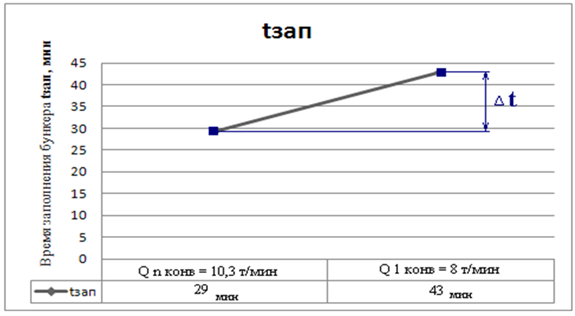
Рисунок
4 – Время заполнения бункера в зависимости
от скорости конвейера
На графике показано ∆t – время заполнения бункера при снижении производительности комбайна и конвейера. Если еще учесть дополнительное время tзагр.конв. необходимое для загрузки всей длины конвейера, то время работы добычного участка увеличится на:
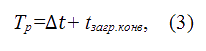
При осуществлении пуска груженного конвейера выполняется проверка применимости всех составных частей ленточного конвейера. Необходим ряд проверочных расчетов ленточного конвейера в период его пуска с грузом.
Период пуска конвейера можно разделить на две фазы: трогание и разгон. Фаза трогания характеризуется постепенным вовлечением в движение элементов ленты. В начальный момент фазы трогания, предшествующий движению конвейерной ленты, усилие прикладываемое к ленте, но еще не превысившее общее сопротивление движению ленты по роликам, отклоняет роликоопоры по направлению движения, что вызывает возникновение изгибающего момента в месте установки роликоопоры на став конвейера и возможность продольного смещения последнего [4].
В предпусковом периоде на роликоопору действует сила от веса ленты с грузом:
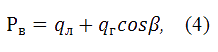
В начальный момент трогания к роликоопорам, несущим груженную ветвь, прикладывается момент трения равный сопротивлению движению конвейерной ленты с грузом относительно оси ролика:
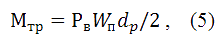
где dp – диаметр ролика, м; Wп – коэффициент сопротивления при пуске (Wп = 0,06–0,09), и момент, действующий на 7-ю роликоопору от тягового усилия привода.
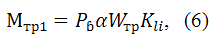
где Рɓ – окружное усилие на приводном барабане, Н; а – расстояние от точки приложения силы до оси ролика, а = dp/2, м; Wтр – коэффициент трения ленты о роликоопору; Kli – коэффициент, учитывающий расстояние от 7-ой роликоопоры до приводного барабана, м [4].
До тех пор, пока выполняется условие Мтр > Мтр1 лента не движется, и усилие прикладываемое к ленте от двигателя отклоняет роликоопору. По мере роста окружного усилия на приводном барабане в движение включаются следующие элементы конвейерной ленты, которые, в свою очередь, последовательно воздействуют на роликоопоры. Волна движения идет не только по ленте, но и по ставу, причем скорость движения пусковой волны (толчка) по ставу значительно превышает скорость распространения волны в ленте, так как жесткость става значительно больше жесткости ленты. Рассмотрим изгибную деформацию стойки роликоопоры в начальный момент трогания. Тяговое усилие, приложенное к ленте в точке ее контакта с роликом, отделяющей неподвижный участок тягового органа от движущегося, должно перетянуть через ролик провисшую ленту с грузом. При этом роликоопора изгибается под воздействием сил, вызванных провисшей за роликоопорой лентой с транспортируемым материалом Рн.пр.
Представляющее интерес отклонение роликоопоры происходит в случае, когда ролик еще не вращается, а волна деформации уже начала растягивать ленту за роликоопорой. При этом принимаем следующие допущения: сила сопротивления движению ленты описывается законом сухого трения; пробуксовка ленты на барабане отсутствует; ролик не вращается пока Рɓ ˂ Рн.пр , а отклонение верхней точки роликоопоры ∆Х равно участку ленты за роликоопорой ∆l, вовлеченному в движение до момента t срыва ленты с ролика, а значит и начала вращения ролика.
Таким образом, сила, изгибающая роликоопору в начальный момент трогания:

где cosβ – угол наклона конвейера (cosβ = 0o); W'тр – коэффициент трения при трогании. Кроме того, во время запуска конвейера нагруженным для исключения пробуксовки должно выполняться условие:
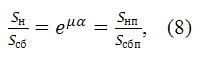
где Sн, Sсб – усилия в набегающей и сбегающей с приводного барабана ветвях ленты соответственно; Sнп, Sсбп – усилия в набегающей и сбегающей с приводного барабана ветвях ленты при пуске конвейера соответственно; μ, α – коэффициент трения ленты о поверхность приводного барабана и угол обхвата лентой этого барабана соответственно [5].
Так как Sнп ˃ Sн, в соответствии с условием (8), и Sсбп должно быть больше Sсб. Следовательно для пуска ленточного конвейера без пробуксовки в течение времени пуска tп натяжное устройство должно создавать повышенное натяжение ленты, обеспечивающее в сбегающей ветви усилие Sсбп. Поэтому в тяжелых конвейерах обычно применяются автоматические натяжные устройства. А для остальных конвейеров руководящими техническими материалами [6] при пуске груженого конвейера расчет натяжного усилия натяжного устройства рекомендуется выполнять с использованием повышающего коэффициента – К = 1,2; 1,5 (соответственно для положительных и отрицательных значений температуры окружающей среды). Использование повышающего коэффициента приводит к тому, что тяговая лента конвейера и большинство элементов его конструкции, включая привод, весь период эксплуатации конвейера будут работать с нагрузкой соответствующей пусковому режиму. То есть на 20% и 50% больше требующейся при работе в установившемся режиме, которая приводит к ощутимому снижению срока службы ленты и повышению удельных энергозатрат на транспортирование.
В проектировочных расчетах усилие [6] Sнп определяется по формуле:

где Wгп, Wпп – сопротивления движению ленты на груженой и порожней ветвях соответственно, a – ускорение движения ленты за время tп ее разгона при пуске конвейера; qг, qл – линейные нагрузки от сил тяжести транспортируемого груза и ленты соответственно; L – длина конвейера; K1 – коэффициент учета инерции вращающихся масс роликов и барабанов; g – ускорение свободного падения. Статические сопротивления движению ленты, подсчитанные по коэффициенту wn = Kmw (где w – коэффициент сопротивления движению при установившемся движении ленты; Km – коэффициент увеличения сопротивления движению при трогании ленты с места), достигают своих максимумов Wгп, Wпп только в момент трогания ленты, а затем в течение времени tп снижаются до постоянных значений, рассчитанных по коэффициенту w, так как они не зависят от величины пускового ускорения ленты [6].
Первое слагаемое формулы (9) – Sсбп = KSсб (где Кп – коэффициент повышения предварительного натяжения ленты при пуске груженого конвейера, характеризующий дополнительную нагруженность ленты и других элементов), для исключения пробуксовки приводного барабана должно реагировать не только на повышение сопротивления движению при трогании ленты с места, но и на возникающее при ее разгоне дополнительное динамическое усилие, описываемое четвертым слагаемым формулы (9). С целью получения зависимости для вычисления Кп рассмотрим условие пуска груженого ленточного конвейера без пробуксовки приводного барабана:

где Рп = (Sнп – KSсб) – тяговое усилие на приводном барабане во время пуска; kзс = 1,1-1,2 – коэффициент запаса сцепления [6]. Отсюда можно получить:

В нормативах [3] принято, что Кп = К = 1,2; 1,5. Результаты численных расчетов по формуле (11) для конвейера производительностью 480 т/ч, перемещающего уголь со скоростью 1,6 м/с на расстоянии 500 м, в графическом виде представлены на рисунке 5. Из них при минимизации критерия дополнительной пусковой нагруженности конвейера представляется возможным выбрать время разгона tп и расчетный коэффициент Кп, соответствующие техническим параметрам конвейера.
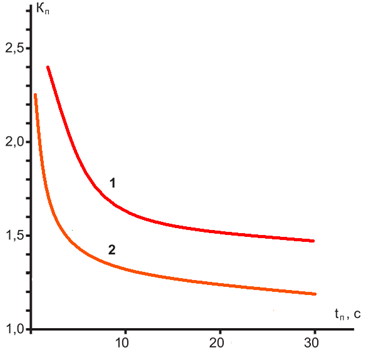
Рисунок
5 – Графики зависимости коэффициента Кп от времени пуска tп
груженого конвейера 1ЛТ80У: 1 – при β =
0° и
К=1,5; 2 –
при β = 0° и К = 1,2
С помощью полученного коэффициента Кп можно определить необходимое для пуска груженого конвейера усилие в натяжном устройстве, используя известные зависимости [5] и заменяя в них нормативный повышающий коэффициент К на Кп. Реализация принятого по графику (рис 5.) времени пуска tп возможна путем применения в электрической цепи привода конвейера передовых элементов – частотных преобразователей.
Проведенные исследования позволяют в компенсирующих автоматических натяжных устройствах в зависимости от времени пуска, технических параметров конвейера, угла наклона трассы и температурных условий окружающей среды принимать более точные значения необходимого натяжения ленты натяжным устройством в течение времени пуска груженого ленточного конвейера
В конвейерах, где угол наклона трассы β = 0° (из графика видно), коэффициент Кп несколько выше нормативных значений К, что в данном случае положительно отразится на надежности передачи тягового усилия приводным барабаном ленточного конвейера в период его пуска с грузом.
Кроме того, полученные значения коэффициента Кп и соответствующего ему времени пуска tп позволяют скорректировать расчет силы Sнп по формуле (8), что будет способствовать повышению качества проверочных расчетов ленточного конвейера в период его пуска с грузом [5].
Далее был проведен ряд расчетов для реализации пуска груженого конвейера в послеаварийном режиме необходимых для построения математической модели в приложении Simulink пакета MATLAB [7]. Модель привода ленточного конвейера набрана из стандартных блоков пакета MATLAB и приведена на рисунке 6. Исходя из моделирования переходных процессов было установлено, что пуск конвейера 1ЛТ80У загруженным в послеаварийный период на скорости V1кон осуществлен успешно.
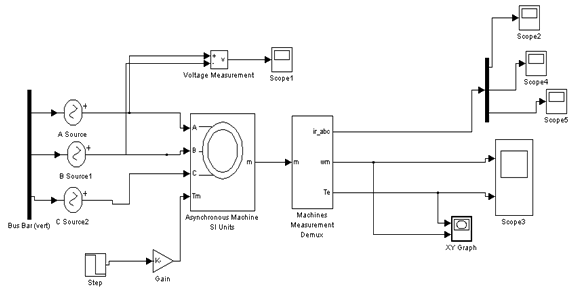
Рисунок
6 – Модель привода ленточного конвейера 1ЛТ80У
3.3 Разработка структурной схемы системы автоматического управления конвейерными линиями с промежуточными бункерами
На основании проведенных исследований была разработана структурная схема системы автоматического управления конвейерными линиями с промежуточными бункерами на базе комплекса САУКЛ, комплекса технических средств управления очистными комбайнами КС 500Ч, и разработанного устройства управления бункером УУБ, представленная на рисунке 7. На рисунке 7 обозначено: координирующее устройство конвейерного транспорта; БИУком – блок исполнительных устройств комбайна; БД1–n – блок датчиков; БУ – блок управления комбайном; БУК1-БУКn – блок управления конвейером № 1…n; БД1-БДn – блок датчиков бункера № 1…n; БДт1-БДтn – блок датчиков конвейера № 1…n; УРС1-УРСn – устройство регулирования скорости; ПЧ1-ПЧn – преобразователь частоты; ПУ САУКЛ – пульт управления САУКЛ; ИБП – источник бесперебойного питания; АЛС – адаптер линии связи; АПУ – адаптер пульта управления; УУБ1-УУБn – устройство управления бункером № 1…n.
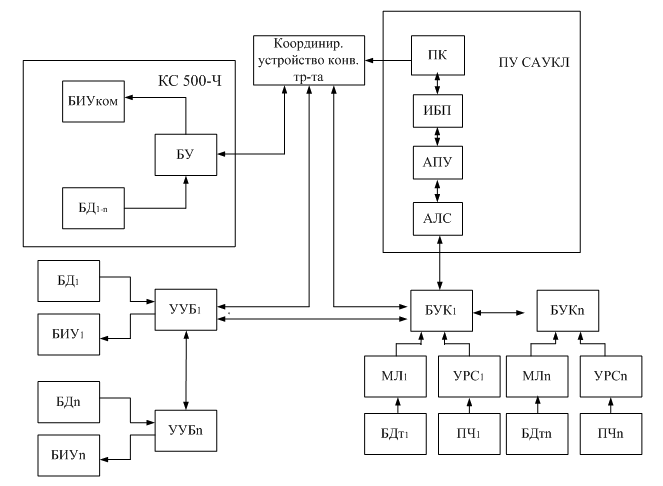
Рисунок
7 – Структурная схема системы автоматического управления
конвейерными линиями с промежуточными бункерами
Выводы
Для повышения эффективности работы добычного участка разработана структурная схема, устройство управления бункером и предложен способ автоматического управления конвейерными линиями с промежуточными бункерами с использованием современной микропроцессорной техники, координирующего устройства. Установлено, что эффективность данной системы автоматического управления достигается путем увеличения времени цикла работы участка на время Tр = ∆t + tзагр.конв. Осуществлен пуск груженного конвейера в послеаварийном режиме на скорости V1кон.
Реализация предлагаемой структурной схемы системы автоматического управления конвейерными линиями с промежуточными бункерами позволит в рабочем режиме регулировать скорость подачи комбайна и скорость конвейера, в аварийном режиме использовать аккумулирующую способность линии, в послеаварийном режиме осуществлять пуск груженого конвейера, обеспечивать не только функции блокировок и телемеханического управления, но и сбор и обработку информации от сопутствующего оборудования, передачу ее на поверхность для последующего мониторинаг работы участка.
При написании данного реферата магистерская работа еще не завершена. Окончательное завершение: декабрь 2012 года. Полный текст работы и материалы по теме могут быть получены у автора или его руководителя после указанной даты.
Перечень ссылок
- Гливанский А.А. Методы управления шахтным подземным конвейерным транспортом. Средства и аппаратура горной автоматики для угольных предприятий, Труды института № 29 / А.А. Гливанский, И.П. Коновалова, В.М. Ротенберг, Е.К. Травкин – Москва, 1978.
- Чиженко И.М. Справочник по преобразовательной технике / Под ред. И.М. Чиженко – Киев: Техника, 1978. – 447 с.
- Шахмейстер Л.Г. Теория и расчет ленточных конвейеров / Л.Г. Шахмейстер, В.Г. Дмитриев – М.: Машиностроение, 1987 – 256 с.
- Ефименко Л.И. Определение нагрузок на конвейерный став от воздействия тягового усилия / Л.И. Ефименко, М.П. Тиханский
- Рачков Е.В. Совершенствование системы пуска ленточного конвейера с грузом. Речной транспорт / Е.В. Рачков – 2011. – № 5 (53). – с. 63
- Дьячков В.К. Основные требования к проектированию ленточных конвейеров общего назначения. РТМ 24.093.04-80 / В.К. Дьячков, Н.А. Смирнова – М.: ЦНИИТЭтяжмаш, 1980.
- Черных И.В. Моделирование электротехнических устройств в MATLAB. SimPowerSystems и Simulink / И.В. Черных – М.: ДМК Пресс, 2007. – 288 с., ил. (Серия «Проектирование»).
- Штокман И.Г. Проектирование и конструирование транспортных машин и комплексов / И.Г. Штокман – М.: Недра, 1986. – 392 с.