Abstract
Contents
- Introduction
- 1. Theme urgency
- 2. The purpose and objectives of the master's work
- 3. Automatic control system for ventilation in a blind drifts
- Conclusion
- References
Introduction
At present the work in coal-mine is impossible without forced ventilation. Termination of ventilation leads to a cessation of mine or processing facility mine and found people on the surface, to stop the operation of all machinery and equipment.
The state of the mine atmosphere depends on the possibility of mining operations, the normal functioning of the equipment and the safety of the miners and mine personnel.
The coal industry is characterized by heavy, harmful and dangerous conditions, and is the subject of high-risk labor.
Blind drifts are considered to be one of the most dangerous grooves. Because of the difficulty of ventilation in the grooves there is the possibility of accumulation of dangerous concentrations of methane, which can lead to disaster. According to statistics Makeevsky Sience Research Institute in the mines of Ukraine for more than 50 % methane-air explosions and coal dust were recorded precisely in blind drifts [1].
In general, in recent years, the quantity of explosions and accidents at mines declined, but the level of risk is still very high, it indicates a low efficiency of the systems aerogas control. Therefore, the development and improvement of methods and means of control, diagnosis and management of the state of the mine atmosphere is an important task and requires the solution.
1. Theme urgency
The problem of control, diagnosis and management of state aerogas developing section follows the development of the deep levels of the mine hazards release, discharge and accumulation of methane, and, consequently, gas contamination of grooves. Therefore, the relevance of developing a system of automatic control, diagnosis and management of state aerogas developing section of particular importance.
To solve all these problems is possible with an integrated automation system for monitoring the presence of methane, as well as the vibroacoustic diagnosis of the rock mass and provide the automatic control ventilation and removing the gas in blind drift.
Safety of mining operations is impossible to achieve without sufficient air and the normal state of aerogas in the mine atmosphere.
2. The purpose and objectives of the master's work
The purpose of master's work is to increase mine safety by creating a system of automatic control of the aerogas state in the atmosphere, management of ventilation and removing the gas in blind drift.
Objectives of master's work are:
3. Automatic control system for ventilation in a blind drifts
Condition of formation methane-air mixture in environment in coal mines, dangerous on gas, are probabilistic in nature and depend on the amount of methane emitted from the rock mass and transported rock. The formation of an explosive concentration varies widely.
Therefore, a continuous control of the mine atmosphere and the timely adoption of measures to eliminate sparks in a potentially hazardous gas release and possible arcing locations [2].
The amount of methane in the grooves of Gt is defined

where q(Θ,xt) – absolute gas emission per unit length as a function of the length of blind drifts and the duration of gas contamination, m3/m∙с;
хt – length of the blind drifts production;
Qp – clean air to the production of blind drifts [3].
In the figure 1 distribution curves of the distribution of methane concentration on the length of blind drift production for varying lengths gas contamination.
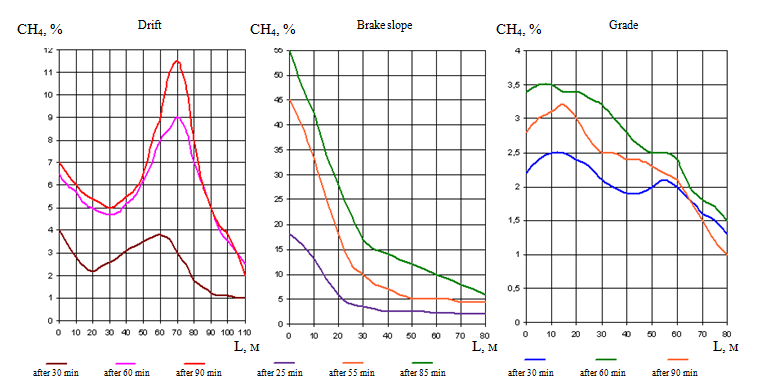
Figure 1 – Curves of the distribution of methane concentration on the length of blind drift production for varying lengths gas contamination.
The figure 2 shows a schematic diagram of a system of safe operations in the development of the blind drifts.
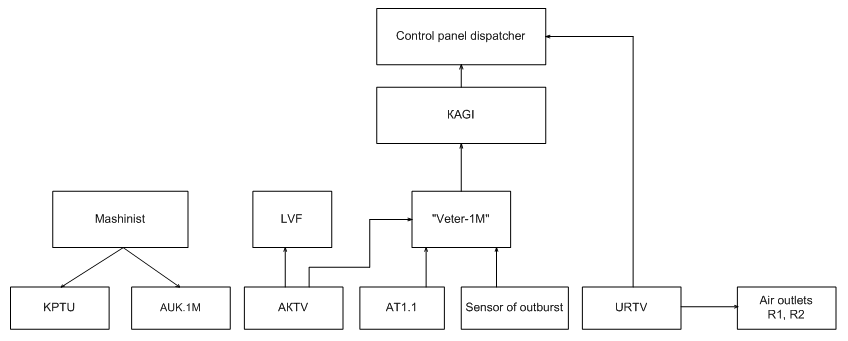
Figure 2 – Schematic diagram of a system of safe operations in the development of the blind drifts
In the figure 2 use the following notation:
KPTU – a set of management and diagnostic technique for drifting a uniform;
AUK.1M – automatic control of conveyor apparatus;
LVF – local ventilation fan;
AKTV – control equipment ventilation of blind drifts;
AT1.1 – methane analyzer;
"Veter-1M" – remote control and signaling devices;
KAGI – set information aerogas;
URTV – designed device of the removing the gas in blind drift.
The process of ventilation is carried out automatically with the help of equipment AKTV. All necessary signals are fed to the system console mining dispatcher. In the case of hazardous and emergency dispatcher decides to manage the process of ventilation [4].
Turn off the equipment in case of exceeding the permissible concentration of methane in the atmosphere of blind drifts production by methane analyzer AT1.1 [5-7]. The machinist controls the penetration KPTU and AUK.1M.
The LCD display device URTV displays information about the concentration of methane and gas contamination in blind drift. Signal from the device URTV affects the actuator that opens and closes the air outlet dampers.
Dampers are opened and closed by means of hydraulic jacks.
The figure 3 shows the process of removing the gas in blind drift using a device URTV.
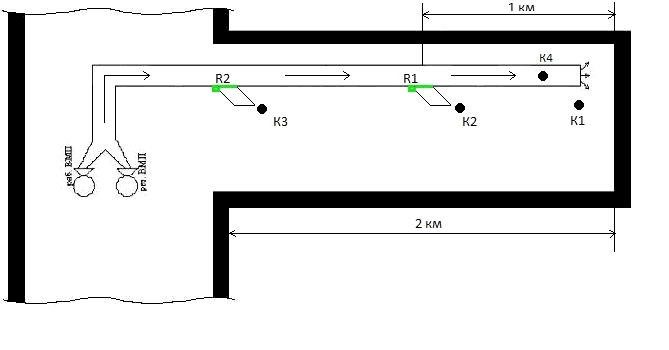
Figure 3
– The process of removing the gas in blind drift using a
device URTV
(animation: 7 frames, 7 cycles of repeating, 65 kilobytes)
In the figure 3 uses the following notation:
К1, К2, К3 – sensors of methane;
К4 – air speed sensor;
R1, R2 – dampers that open the air outlet.
The length of the blind drift adopted 2 km.
The sensor methane K1 is set at the end of blind drift, the sensor is installed in the middle of methane K2 groove, before an air outlet 1, which opens damper R1. The sensor methane R3 is set to end before an air outlet 2, which opens damper R2.
Air speed sensor is usually installed in K4 10–15 meters before the end of the air outlet.
Flow diagram of the control algorithm of blind drift degassing device (URTV) is shown in the figure 4.
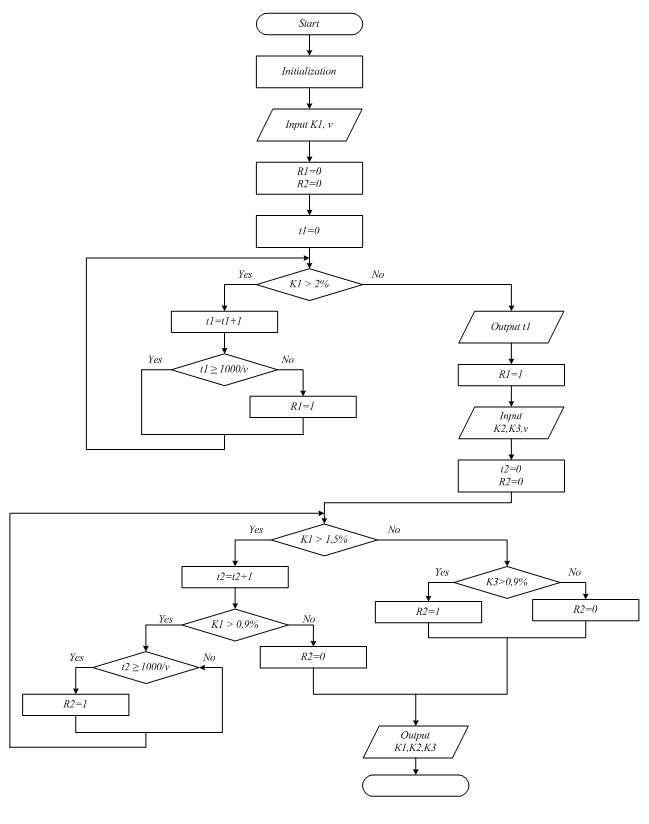
Figure 4 – Flow diagram of the control algorithm of blind drift degassing device (URTV)
The figure 5 shows a schematic diagram of the device URTV.
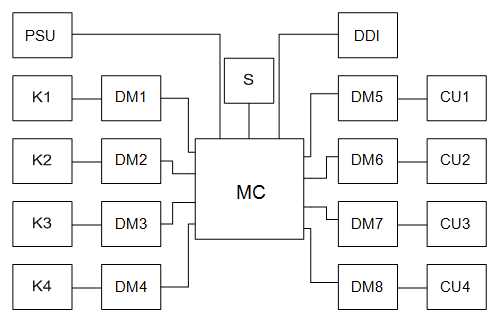
Figure 5 – Schematic diagram of the device URTV
К1, К2, К3 – methane monitoring sensors;
К4 – air speed sensor
DM1-4 – a device matching for analog sensors;
DM5-8 – a device matching for discrete sensors;
S – reset button;
CU1-4 – the control unit (relay and the hydraulic jack);
MC – the microcontroller;
DDI – the display device information;
PSU – power supply unit.
Power supply PSU used to power the microcontroller MC.
With control of sensor methane K1, ..., K3 through matching device DM1, ..., DM3 receive information about the concentration of methane in various areas of grooves, then this information on a particular algorithm is processed in the microcontroller MC and a DM4, ..., DM8 control signals are issued to the CU1, ..., CU4 for closing or opening dampers air outlet.
S button is necessary to reset the device to its original state in case of software or other errors.
DDI is used to display the methane concentration in the formulation.
Air speed sensor K4 with matching device US4 used to determine the time approaches for the methane cloud air outlet damper.
The devices are used to harmonize DM-intrinsically safe electrical isolation.
Conclusion
For the coal industry, with its particularly severe conditions of increased safety is the most urgent task. This task is achieved by improving technology and the organization of mining, mechanization of production processes, the use of objective control of the rock mass, the equipment and the environment [2].
The developed system for automatic degassing of blind drifts increases the efficiency of ventilation and removing the gas, controls and prevents dangerous concentrations of methane, provides safe mining at the mine.
Notice. At the time of writing this essay master's work is not yet complete. The final completion – December 2012. Full text of the work and materials on the subject may be obtained from the author or his head after that date.
References
- Шевцов Н.Р. Взрывозащита горных выработок / Н.Р. Шевцов. – Донецк: ДонНТУ, 2002. – 280 с.
- Курносов В.Г. Научные основы автоматизации в угольной промышленности: опыт и перспективы развития: монография / В.Г. Курносов, В.И. Силаев // Международный институт независимых педагогических исследований МИНПИ-ЮНЕСКО, ОАО «Автоматгормаш им. В.А. Антипова». – Донецк: изд-во «Вебер» (Донецкое отделение), 2009. – 422 с.
- Местер И.М. Особенности опасных по газу тупиковых выработок как объектов управления при автоматизации процесса разгазирования / И.М. Местер // Уголь Украины. – 1998. – №2–3. – С. 55–59.
- Азбель М.Д. О метрологическом обеспечении аэрогазового контроля в угольных шахтах / М.Д. Азбель [Электронный ресурс]. – Режим доступа: http://elibrary.ru.
- Филин А.Э. О средствах тестирования систем и оборудования аэрогазового и пылевого контроля / А.Э. Филин [Электронный ресурс]. – Режим доступа: http://elibrary.ru.
- Тахо-Годи А.З. Результаты исследований эффективности способа снижения интенсивности выделения метана на участках шахт, опасных по газовому фактору / А.З. Тахо-Годи [Электронный ресурс]. – Режим доступа: http://rae.ru.
- Пашковский П.С. Комплексное решение проблем вентиляции шахт в нормальных и аварийных условиях / П.С. Пашковский, Н.М. Кравченко, М.В. Кравченко [Электронный ресурс]. – Режим доступа: http://www.nbuv.gov.ua.